What is Scheduled Maintenance?
Scheduled maintenance refers to maintenance tasks that are assigned to a technician with a given deadline. It includes inspections, servicing, adjustments, and planned shutdowns. The tasks can be performed as one-off jobs or at regular intervals.
Scheduled maintenance aims to minimize equipment failure, maintenance backlogs, and reactive maintenance. It also allows for better resource allocation. For instance, changing the bearing on a conveyor belt every 30 days to prevent its snapping is an example of scheduled maintenance. Another example is scheduling the repair of a motor after noticing a problem.
The easiest way to create work orders, assign scheduled maintenance, and track progress is by using mobile-first CMMS software.
The Difference Between Scheduled Maintenance and Planned Maintenance
Scheduled maintenance is often confused with planned or preventive maintenance.
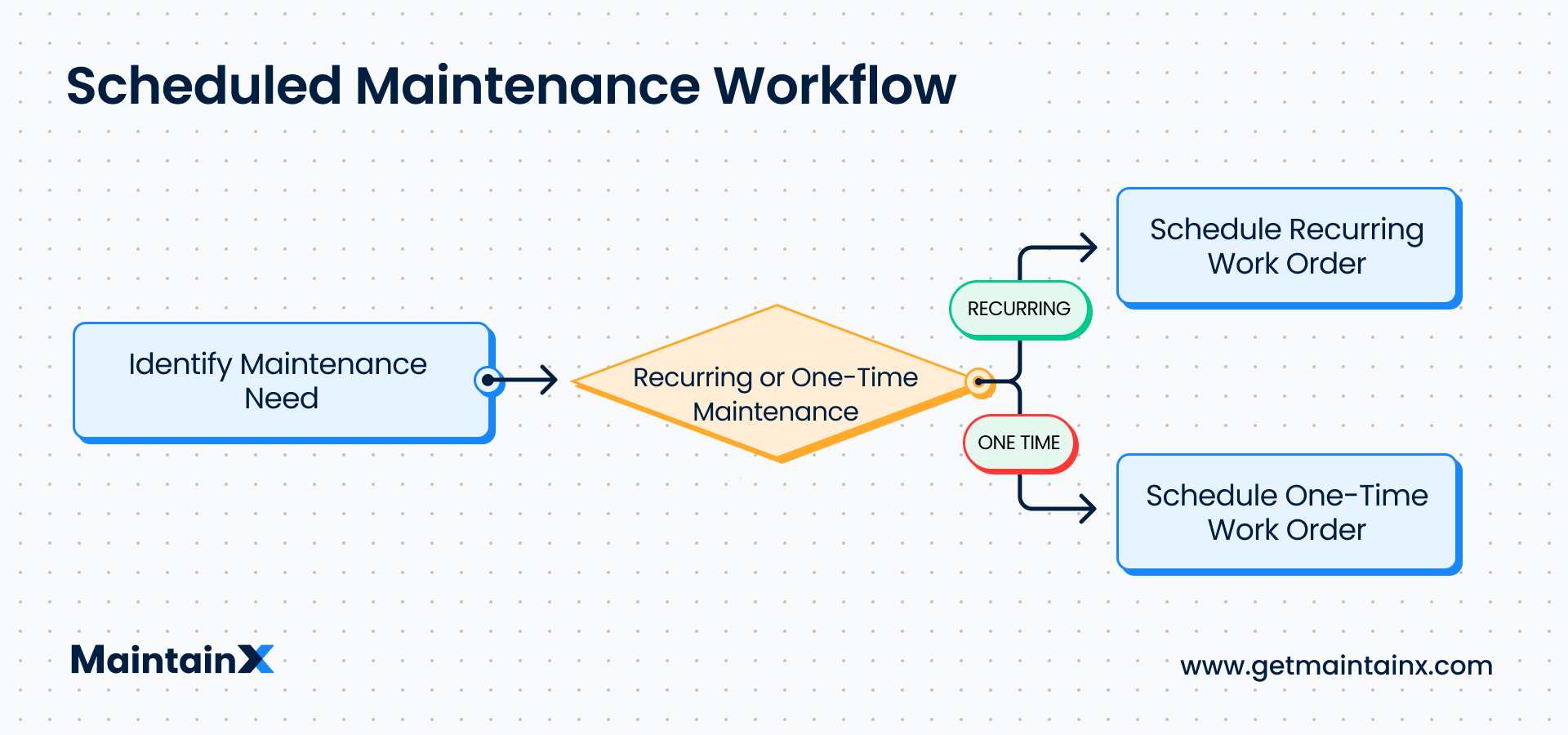
Scheduled Maintenance
This maintenance plan refers to deciding when maintenance tasks will be completed and by whom. Unlike planned maintenance, scheduled maintenance work doesn’t require complex work and equipment behavior forecasting. A task falls into this category when an issue has been identified, assigned to a technician, and given a deadline for completion. It can either be part of a comprehensive planned maintenance strategy or a simple workflow on its own.
Planned Maintenance
This plan involves anticipating equipment needs and implementing strategic systems for completing future maintenance actions. This process includes identifying a task, organizing materials and workflows, prioritizing work orders, and implementing procedures to analyze the ongoing effectiveness of completed tasks. Planned maintenance includes correction-based (CBM), predictive, and preventive maintenance.
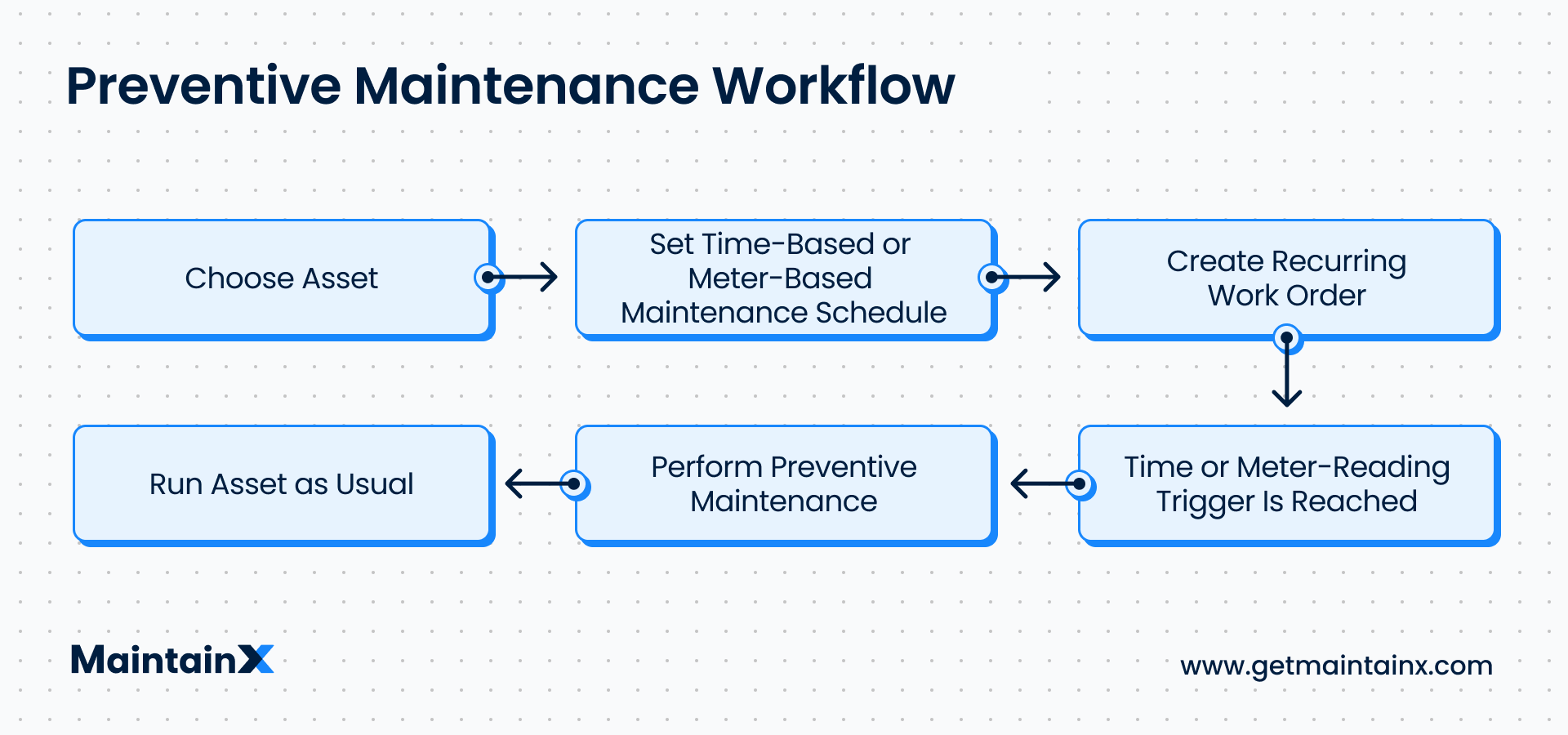
How Important is Scheduled Maintenance?
Although scheduled maintenance is a simplistic form of preventive maintenance, the practice is still valuable. It ensures that every piece of equipment will continue working as designed to reduce unplanned downtime and maintain maximum value. Depending on the asset condition and manufacturer specifications, consistent maintenance schedules can add years to asset lifespans. Furthermore, minimum recommended maintenance instructions keep asset warranties active.
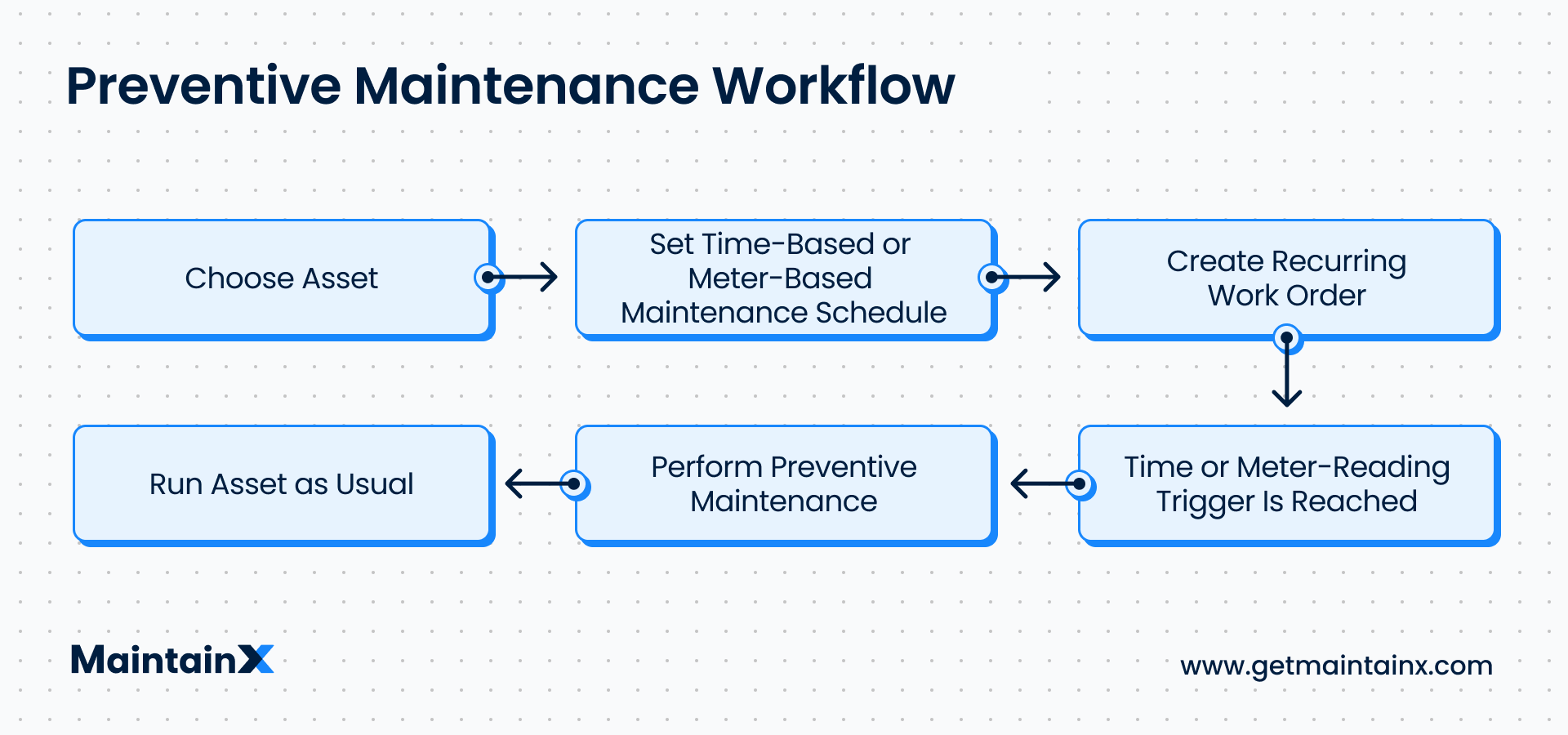
If you intend to sell off an asset as salvage or acquire a new one, performing routine maintenance will help retain its resale value. For this reason, it’s always advisable to document time-based maintenance and equipment servicing. Most obviously, the type of maintenance is a useful tool for asset diagnostics. Your maintenance team may rely on you to schedule maintenance to ensure assets function as they should and resolve any issues before a breakdown occurs.
What is Factory Scheduled Maintenance?
Factory scheduled maintenance is a form of time-based maintenance. This plan focuses on checking for signs of problems while doing maintenance procedures to improve performance. Also known as 30/60/90K maintenance in the automotive world, the term refers to vehicles undergoing owner’s manual procedures every 30,000 miles. However, all types of machinery come with recommended maintenance schedules that ensure optimal functioning.
Many companies avoid factory-scheduled maintenance to save money. However, doing so proves costly in the long run. As previously mentioned, failing to follow recommended maintenance schedules can null warranties. You may also suffer unexpected equipment breakdowns leading to expensive downtimes.
What is Scheduled Maintenance Critical Percent (SMCP)?
Scheduled maintenance critical percent (SMCP) is a tool companies used to organize recurring planned maintenance tasks and prioritize overdue maintenance tasks. The tool calculates how late your maintenance tasks are in relation to their frequency of occurrence. Tasks with higher percentages are given priority.
So, why is SMCP needed? Ideally, it’s performed on the manufacturer’s recommended scheduled day, and everything works out perfectly. However, as any seasoned technician will agree, things don’t always work out as planned on paper.
How to Calculate SMCP
SMCP is calculated by adding the number of days scheduled maintenance is late to the number of days in a maintenance cycle. Divide your result by the number of days in the maintenance cycle and multiply that number by 100 to arrive at a percentage.

SCMP Formula:
SMCP = (# of Days Late + # of Days in PM Cycle) / (# of Days in PM Cycle) * 100
Example:
Two scheduled maintenance tasks on the same system are overdue. The first task, typically completed every 30 days, is 3 days overdue. The second task, performed every 90 days, is five days late. The question is: Which task should your maintenance team tackle first?
Task 1: (3+30) ÷ 30 x 100 = 110%
Task 2: (5+90) ÷ 90 x 100 = 105%
According to SMCP, Task 1 has the higher percentage, therefore, you should prioritize it.
The Benefits of Tracking SMCP
Calculating SMCP benefits organizations in three ways:
- Improves Maintenance Scheduling: SMCP lets you know which tasks to prioritize for improved effectiveness.
- Reduces Cases of Reactive Maintenance: The formula also allows you to identify assets more prone to failure and take care of them. You can clear your backlog in order of priority.
- Makes Audits Easier: Missed maintenance schedules can cause trouble with audits and compliance. Tracking your SMCP enables you to highlight urgent tasks and take care of them before they cause problems. It also helps to identify the root cause of overdue tasks for addressing.
Finally, SMCP helps reduce unnecessary downtime and maintenance costs. It is a foundational maintenance metric that can help to elevate your maintenance strategies.
How to Write Scheduled Maintenance Messages
The key to a well-run program is clear and timely communication between facilities managers, maintenance technicians, and key stakeholders. Here are a few tips on how to write work order announcements that get read, understood, and remembered:
- Understand Task Impact: The scope of the impact of the maintenance task will inform your strategy. Which service lines and how many users will be affected? How long will the task last? Put yourself in the user’s shoes and think about how the interruptions will affect them.
- Give Sufficient Notice: Don’t ambush users with news of a scheduled maintenance task. Inform everyone early enough and give constant reminders until the day of the task. See an example of a reminder below.
- Use Effective Communication Channels: For company communications, emails are the most effective. For other users, you can rely on social media posts and in-app banners.
- Include Necessary Details: There’s no need to list all of the details, but inform your users which team is doing the maintenance, the channels through which their concerns and questions will be addressed, and alternative ways to access your services if there are any.
When writing maintenance messages, provide a human touch. Robotic-sounding messages tend to be ignored.
Implement a CMMS for Scheduled Maintenance
A robust scheduled maintenance management program can help companies prioritize maintenance tasks, minimize equipment failure, and reduce maintenance backlogs while allowing for better resource allocation. It will also reduce the need for costly reactive maintenance repairs.
Scheduled Maintenance FAQS
How Often Should Scheduled Maintenance be Conducted?
The frequency of scheduled maintenance varies based on equipment type, manufacturer recommendations, usage patterns, environmental conditions, and industry standards. Timeframes can range from daily, weekly, monthly, quarterly, to annually.
What Are the Benefits of Following a Scheduled Maintenance Plan?
Benefits of scheduled maintenance processes include increased equipment reliability, improved safety, reduced risk of unexpected breakdowns, enhanced efficiency and uptime prolonged asset lifespan, and better cost management by avoiding major repairs.
How Can I Implement an Effective Scheduled Maintenance Program?
Implementing an effective program involves creating a detailed schedule, tracking maintenance activities, adhering to manufacturer guidelines, training staff, documenting procedures, and leveraging maintenance management software.
See MaintainX in action