Proactive maintenance is a maintenance strategy that aims to identify and fix the reasons for equipment failure before it happens. The goal of proactive maintenance is to increase asset reliability and reduce the risk of downtime.
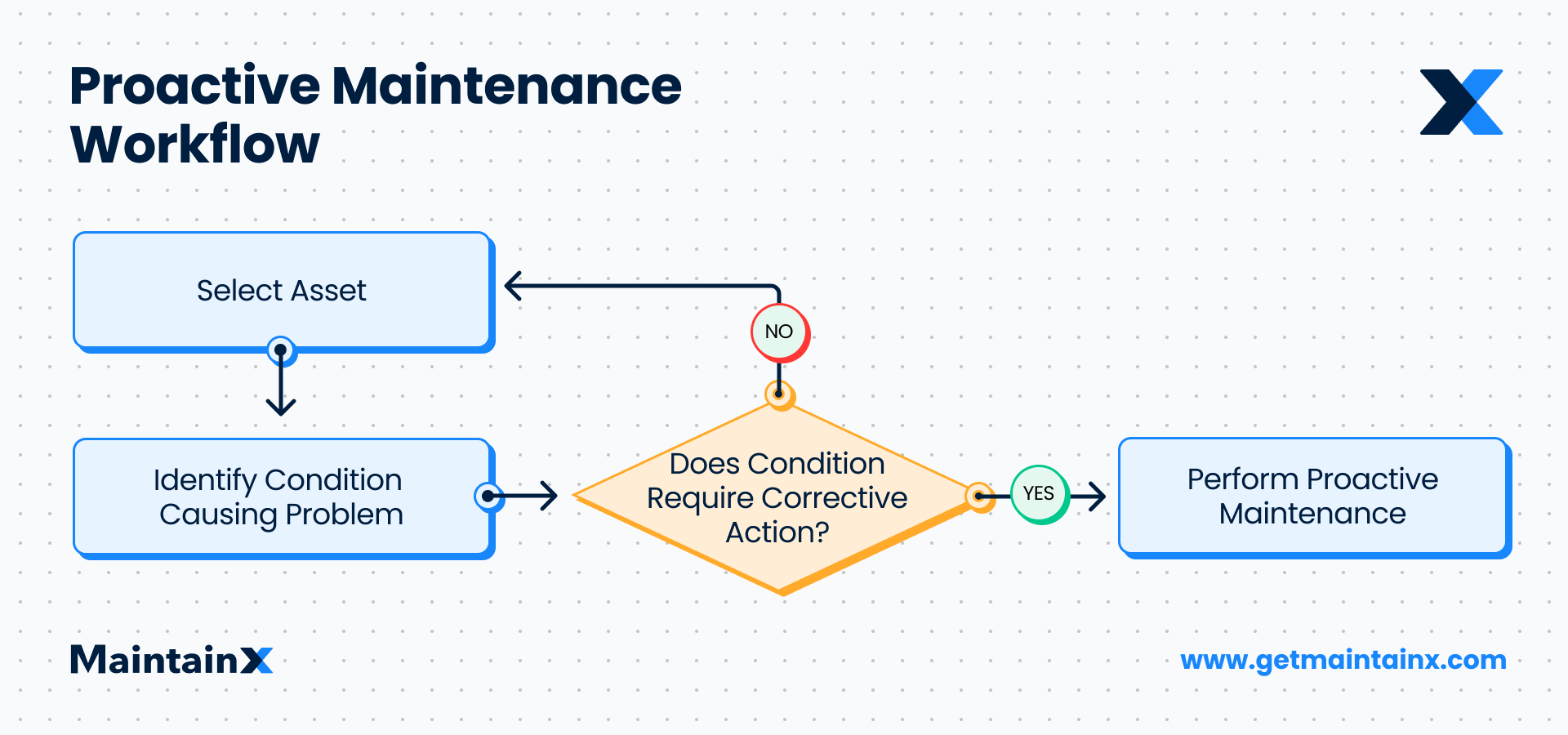
Wear and tear is a normal part of equipment lifecycles. However, a solid proactive maintenance strategy can extend the lifespan of assets and improve performance. Proactive maintenance reduces maintenance and operational costs by addressing hidden operational inefficiencies. Equipment operating in good condition uses less energy than machines near the point of breakdown. Wear and tear negatively impact output as well.
Contrary to run-to-failure (RTF) maintenance, in which maintenance is performed after an asset breaks down, proactive maintenance addresses potential issues in advance. For most organizations, a smart balance between proactive and reactive maintenance exists.
Types of Proactive Maintenance
There are a few types of proactive maintenance.
Preventive Maintenance (PM)

Preventive maintenance aims to prevent failures and unplanned downtime. PM requires maintenance technicians to regularly perform maintenance work before a piece of equipment breaks down. Defining intervals by which to schedule maintenance is either based on usage (e.g., every 1000 hours of runtime) or on calendar time (e.g., every month).
Condition-Based Maintenance (CBM)
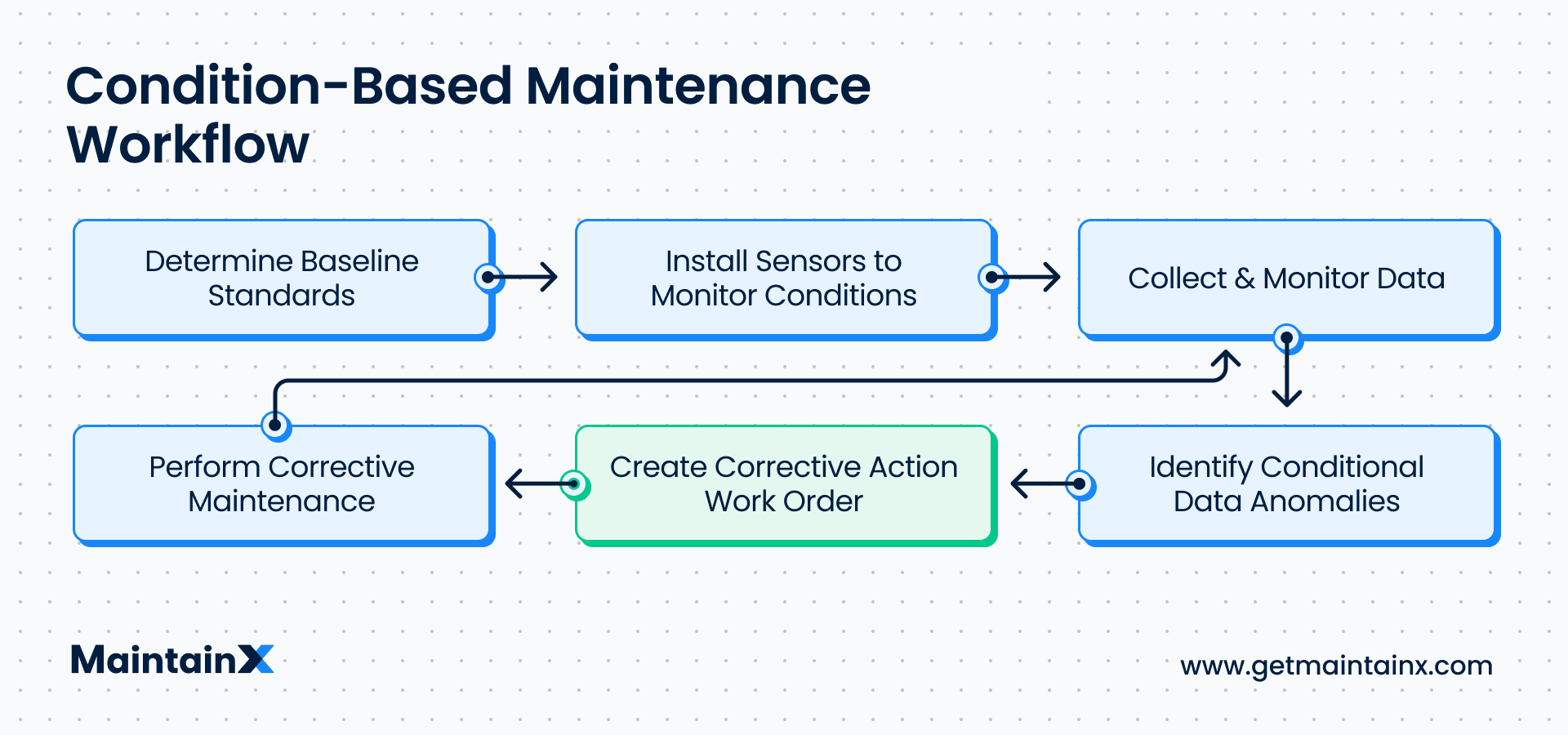
In a condition-based maintenance approach, performance and condition metrics are monitored in real time. This allows maintenance managers to schedule maintenance work before a problem occurs.
Scheduled (Periodic) Maintenance
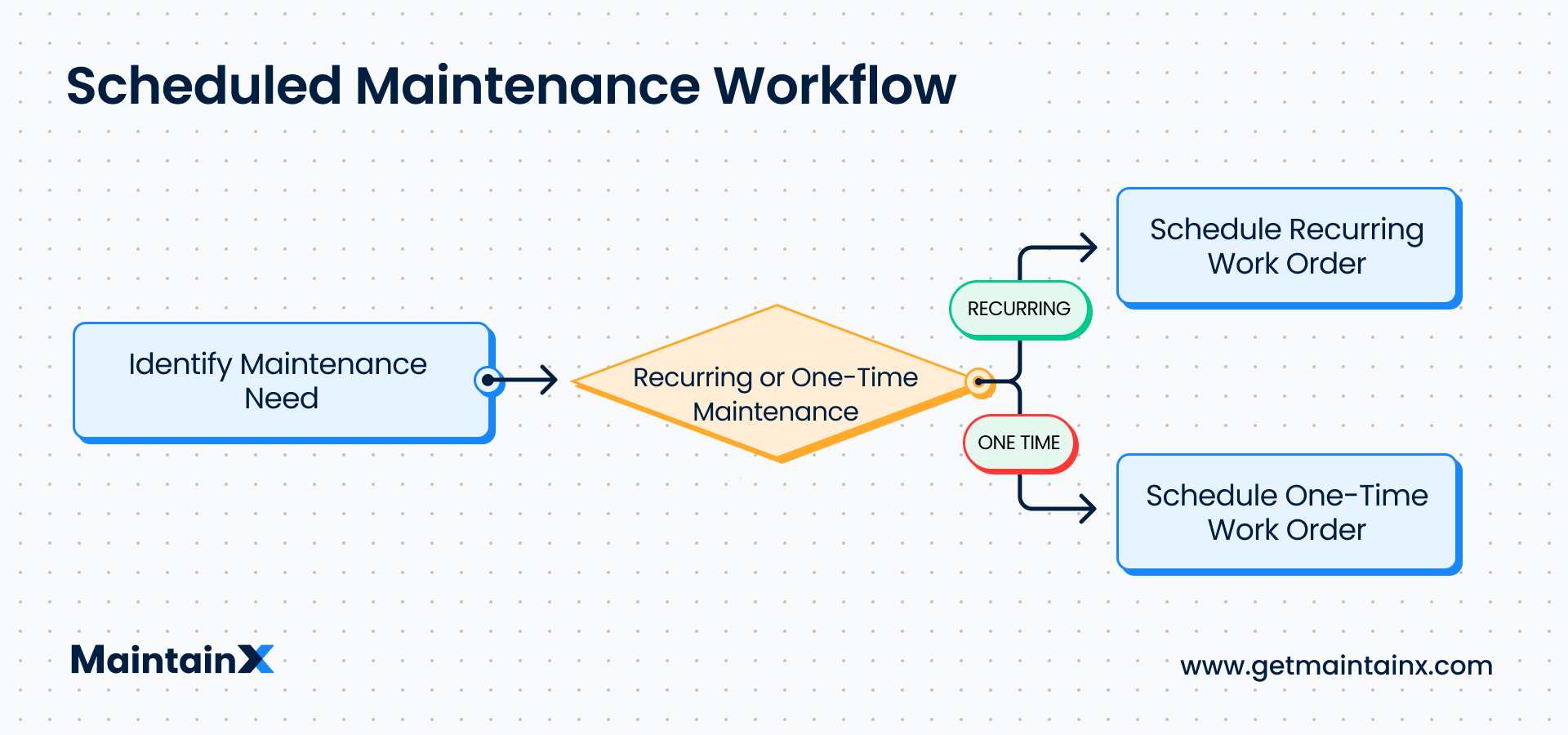
Scheduled maintenance, also known as periodic or time-based maintenance, is an approach in which maintenance work is scheduled in advance, at set intervals. To do this, manufacturer guidelines and the facility’s historical data are used.
Many organizations use a combination of these maintenance strategies for different assets or systems.
Examples of Proactive Maintenance
Examples of proactive maintenance include:
- Checking Pipes for Signs of Corrosion, Thinning, or Cracks: Regularly inspecting pipes for corrosion is a cornerstone in enhancing their lifespan, maintaining optimal functionality, and preventing failures.
- Lubricating Machines at Regular Intervals: Machines with rotating components need regular lubrication to avoid surface-to-surface friction. Make sure you’re storing lubricants properly to prevent contamination.
- Checking the Tread Depth of Car Tires: Worn-out car tires dramatically decrease the safety and performance of a vehicle. Monitoring the tread depth of car tires is another example of proactive maintenance. For this, most tires come with an integrated wear bar indicator.
5 Tips to Transition from Reactive to Proactive Maintenance
Reactive maintenance may seem like a good idea at first, given that it’s so easy to implement—just fix it when it breaks, right? However, bills for outsourced emergency maintenance tasks can quickly add up and unexpected downtime is inefficient.
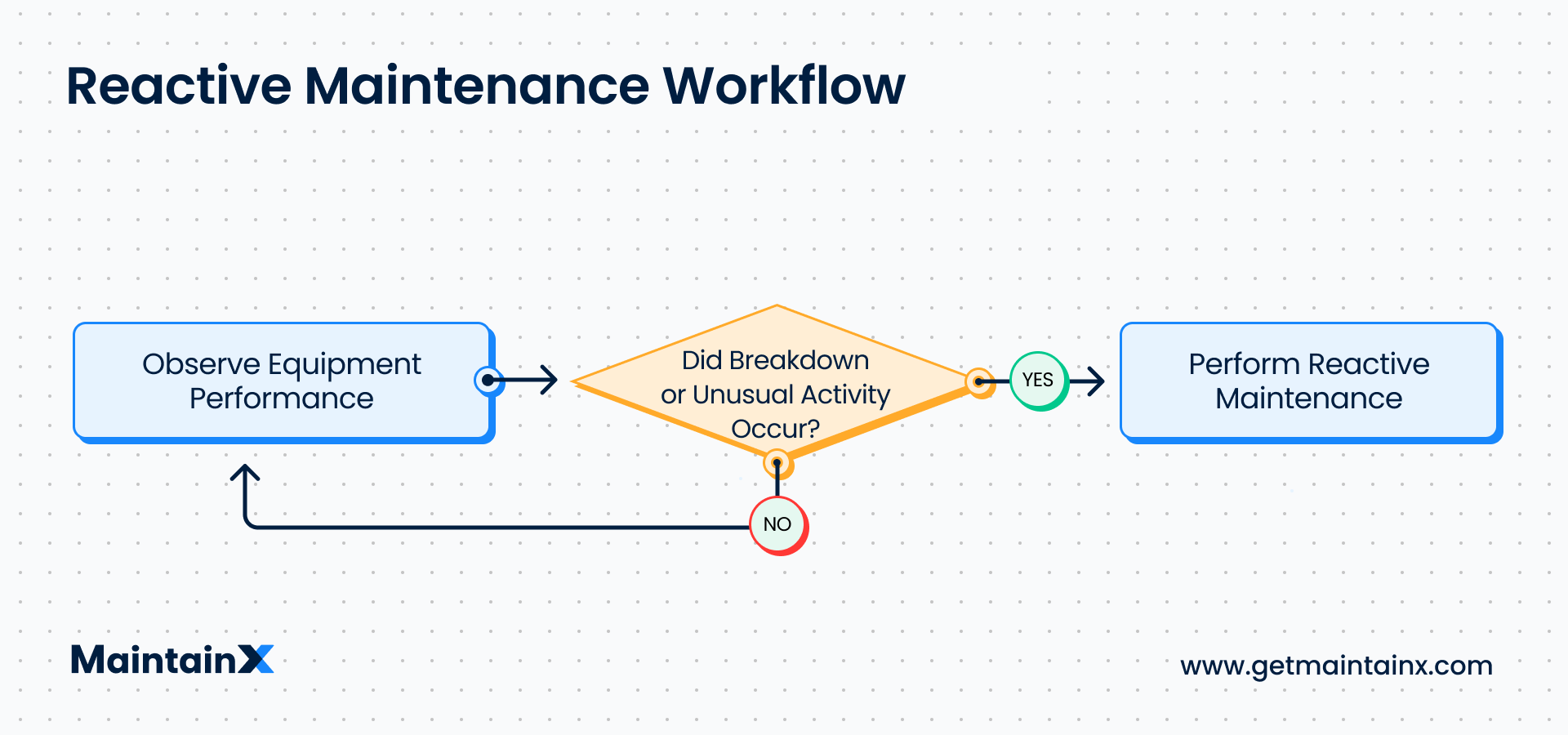
Proactive maintenance is a strategy that is more cost effective in the long run when implemented correctly. To transition smoothly from reactive to proactive maintenance:
1. Start with Your Most Critical Assets
Critical equipment is equipment that is vital to a facility’s functioning and productivity. It’s a great starting point for your proactive maintenance program, as it will yield the highest ROI. Even small changes in how you manage your most critical machinery can have a big impact on your operations and extend the “useful life” of assets.
2. Make Maintenance an Essential Part of Your Business
Maintenance should be one of your highest priorities. Invest in training both maintenance technicians and machine operators.
3. Plan and Schedule Maintenance Activities in Advance
Planned maintenance goes a long way to prevent failure. Additionally, scheduling maintenance work in advance helps ensure that you have the manpower and inventory to perform them.
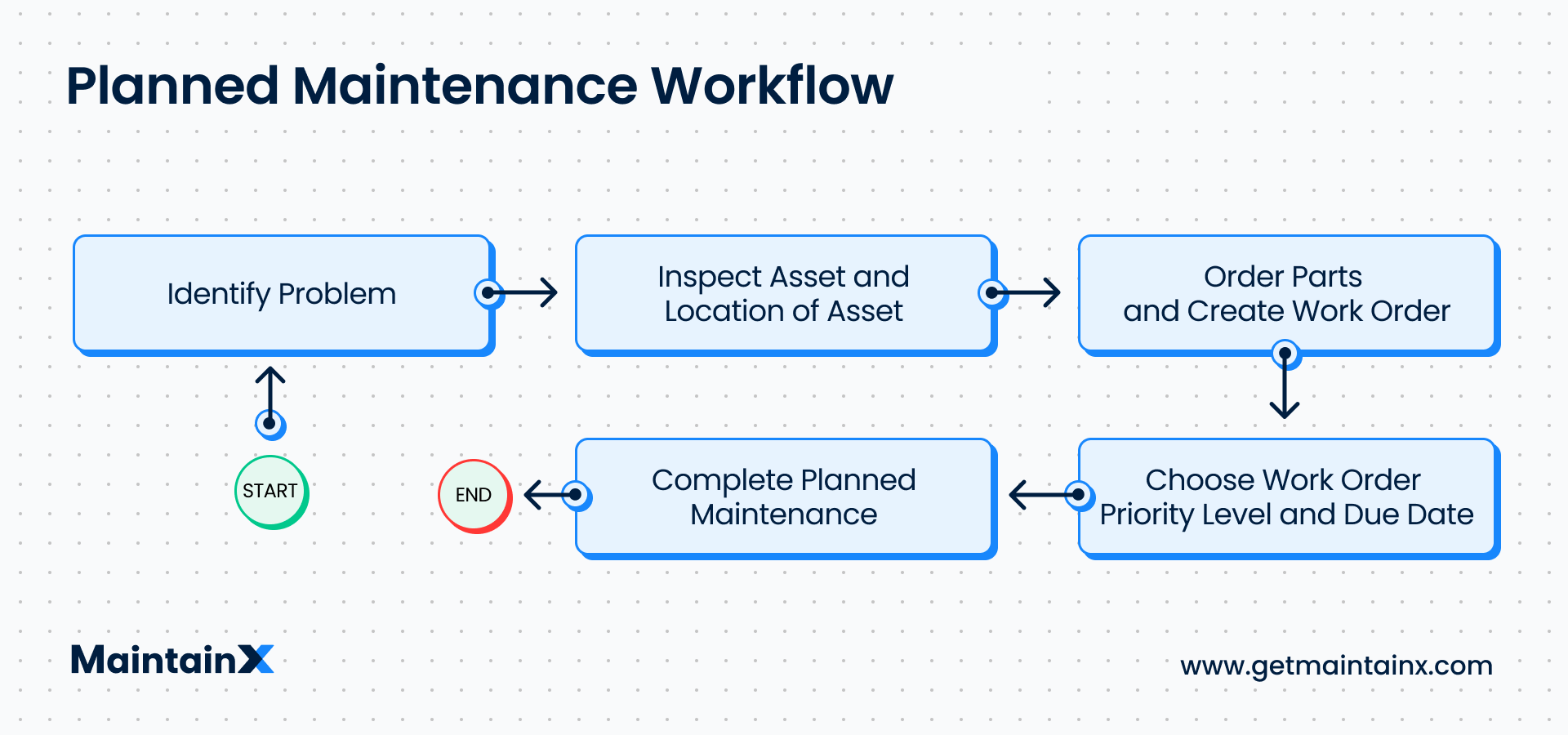
4. Track and Analyze Performance and Failure Data
Having sufficient data on hand will help you identify failure patterns, as well as predict and prevent future problems.
5. Look at the Reasons Why Equipment Fails
Every maintenance manager deals with asset failures, which cannot always be prevented. However, an in-depth analysis of the reasons why equipment fails can greatly help reduce the risk of breakdowns.
Common Causes of Asset Failure and How to Eliminate It
There are many possible causes of equipment failure. A robust proactive maintenance program will help you identify a cause and find a solution before a breakdown occurs. Common causes of asset failure include:
1. Low-Quality Materials
It’s always best to buy spare parts and materials from trusted vendors and stick to manufacturer recommendations. High-quality materials may be more expensive up-front, but the higher price typically comes with a high ROI (return on investment) and leads to an increase in asset maintainability and uptime.
2. Maintenance Staff Errors
Sometimes, the work of different maintenance technicians can differ in terms of quality. Make sure all standard operating procedures (SOPs) are as detailed and up-to-date as possible so technicians can follow them without errors. Invest in staff training if necessary.
3. Machine Operator Errors
Machine operators can make mistakes using equipment, which can lead to equipment deterioration and failure. Again, having detailed SOPs and adequate training procedures in place will help eliminate these errors.
4. Assets Nearing the End-of-Life Cycles
Assets that are approaching the end of their lifespan may underperform and need to be fixed more often than usual. Sometimes it makes more sense to replace them before their complete failure rather than suffer increased maintenance costs or potential losses associated with downtime.
5. Skipped or Delayed Periodic Maintenance
If the maintenance team is overwhelmed and needs to skip periodic maintenance activities to fix more urgent issues, this increases the risk of machine failures. Implement a solid periodic maintenance schedule and adhere to it.
6. Unusual Increases in Production Output
During a busy season, equipment is more prone to wear and tear. Shorten periodic maintenance intervals or implement a condition-based maintenance program to prevent failure.
Proactive Maintenance vs. Preventive Maintenance
Finally, there is often confusion between the terms “proactive maintenance” and “preventive maintenance.” The phrases are used interchangeably, despite different meanings.
Proactive maintenance strives to identify and eliminate the root causes of asset failure. For example, say you notice that a given piece of equipment fails more often when Team A is on shift, compared to Team B. This could indicate that Team A needs additional training. Providing them with new resources and knowledge could result in fewer mishaps, thus reducing maintenance costs.
Alternatively, preventive maintenance aims to service equipment based on pre-set maintenance schedules. For example, a maintenance team may replace filters every 6 months or lubricate rotating parts every week per manufacturer guidelines.
For these reasons, most organizations choose to use a combination of both strategies.
Get MaintainX for Your Proactive Maintenance
Constantly reacting to equipment malfunctions is a clear indication of organizational dysfunction. Maintenance departments can improve equipment reliability, reduce unplanned downtime, and keep costs low by implementing proactive maintenance plans that fix small problems before they become costlier larger ones.
See MaintainX in action