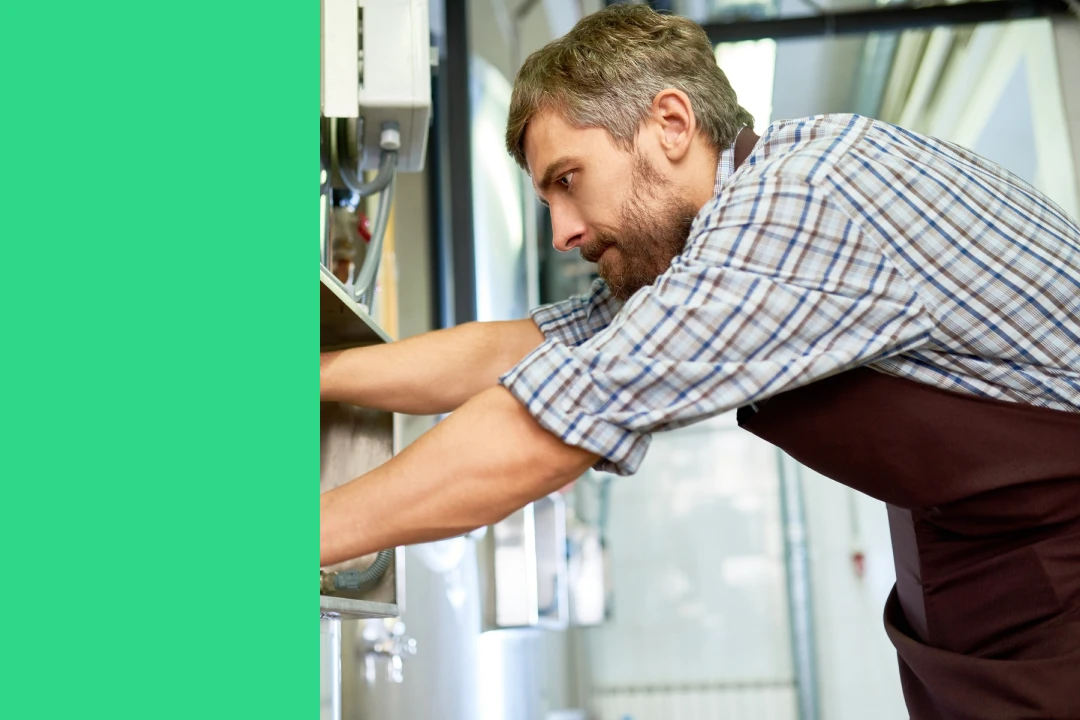
Maintenance departments across industries share one goal: keeping assets operational. Understanding the difference between repair and maintenance directly impacts your bottom line.
When equipment fails, consequences extend beyond repair costs. According to Siemens' The True Cost of Downtime 2024 report, unplanned downtime costs the world's 500 largest companies $1.4 trillion annually—11% of their revenues. In automotive manufacturing, each hour of downtime costs $2.3 million.
Maintenance preserves functionality through planned activities, while repairs restore functionality after failures. This distinction determines whether your operation runs proactively or reactively, influencing equipment lifespan, reliability, capital improvements, and budgets.
For maintenance professionals, recognizing this difference enables better resource allocation and strategic planning with fewer emergency situations. Understanding when to maintain versus repair helps teams balance costs against operational needs while maximizing uptime.
Key Takeaways
- Repairs and maintenance represent fundamentally different approaches to asset management—one reactive, one proactive.
- The cost difference between repairs and maintenance goes far beyond direct expenses, with unplanned downtime costing major manufacturers up to $2.3 million per hour in some industries.
- Organizations should aim for an 80/20 ratio of preventive maintenance to reactive repairs for optimal cost-effectiveness and reliability.
- Effective maintenance strategies reduce unplanned downtime, extend equipment life, and provide significant cost savings by preventing expensive emergency repairs.
- Modern CMMS solutions like MaintainX help organizations shift from reactive to proactive strategies through better scheduling, tracking, communication, and data analysis.
What's the difference between repair and maintenance?
Repair and maintenance represent fundamentally different approaches to equipment management. Repairs fix broken capital assets, while maintenance prevents breakdowns from occurring.
Repair: Actions taken to restore functionality after equipment failure. Repairs are reactive measures that address problems after they occur.
Maintenance: Activities performed to preserve functionality and prevent failures. Maintenance is proactive work that extends asset lifespan and prevents unplanned downtime.
The cost implications of repairs versus maintenance extend beyond the immediate expense of parts and labor. When equipment fails unexpectedly, companies face:
- Emergency repair premiums
- Production losses during downtime
- Potential safety incidents
- Depreciation over time
- Decreased equipment lifespan
- Overtime labor costs
The most effective maintenance strategies focus on prevention rather than reaction, with maintenance experts recommending an 80/20 ratio of preventive maintenance to reactive repairs for optimal cost-effectiveness and reliability.
What are repairs?
Repairs are actions taken to restore equipment functionality after a failure or when equipment breakdowns occur. According to the MaintainX 2024 State of Industrial Maintenance Report, 41% of respondents cited asset deterioration as a primary driver of costly unplanned downtime.
When equipment fails, repairs become necessary to return assets to operational status. Unlike other maintenance operations, repairs are reactive measures that address problems after they've occurred rather than preventing them.
Types of repairs
Corrective repairs: Issues identified during inspections or regular operation before complete failure occurs. While still reactive, corrective repairs are planned responses to discovered problems, such as replacing a bearing showing signs of wear or fixing a misaligned conveyor belt in a manufacturing plant.
Emergency repairs: Urgent fixes for sudden, complete or prevent equipment failures that stop production. Examples include repairing a broken hydraulic line on excavation equipment, replacing a blown motor in an HVAC system, or fixing a failed pump in an oil and gas facility. Emergency repairs typically incur premium costs and cause significant operational disruption.
Deferred repairs: Postponed repairs for non-critical issues where immediate attention to urgent repairs isn't required. Examples include postponing the repair of secondary equipment in a food processing plant during peak production season or delaying cosmetic fixes to retail facility fixtures until after holiday shopping periods.
Common repair activities
Common repair activities across industrial settings include:
- Replacing failed components or parts
- Rebuilding damaged mechanical assemblies
- Addressing electrical system failures
- Fixing structural damage to equipment
- Repairing leaks in hydraulic or pneumatic systems
- Restoring equipment after safety shutdowns
- Troubleshooting and resolving control system malfunctions
- Correcting alignment issues post-failure
- Restoring equipment after environmental damage
- Repairing damaged power transmission components
Unlike maintenance activities that aim to preserve functionality, these repair tasks focus on returning equipment to working condition after a failure has already occurred.
What is maintenance?
Maintenance refers to the systematic care and upkeep of assets to preserve their functionality, performance, and safety throughout their operational lifespan. Proper maintenance extends equipment life, ensures reliable performance, and prevents costly unplanned downtime.
Types of maintenance
Preventive maintenance: Scheduled, routine activities performed while equipment is still functioning properly to prevent failures. Preventive maintenance includes regular inspections, lubrication, cleaning, and component replacements based on time intervals or usage metrics. For example, scheduling quarterly HVAC system maintenance in manufacturing facilities or performing regular oil changes on fleet vehicles.
Predictive maintenance: Data-driven approach using condition-monitoring technologies to determine when maintenance is actually needed. This includes vibration analysis, thermal imaging, and oil analysis to detect potential failures before they occur. Examples include monitoring bearing vibration patterns in industrial equipment or tracking energy consumption trends in refrigeration systems.
Corrective maintenance: Addresses identified issues before they cause equipment failure. While reactive in nature, corrective maintenance differs from repairs as it targets minor problems discovered during inspections before they lead to breakdowns or major repairs. This includes tightening loose connections or replacing worn belts discovered during routine checks.
Reliability-centered maintenance: Strategic approach that analyzes each asset's functions, potential failures, and consequences to determine the most appropriate maintenance strategy. This might include implementing condition monitoring for critical equipment while using time-based maintenance for less critical assets.
Common maintenance activities
Common maintenance activities focus on preserving equipment functionality and preventing failures. These activities typically include:
- Inspecting equipment for signs of wear or damage
- Lubricating moving parts to reduce friction
- Cleaning components and surrounding areas
- Replacing filters and fluids on schedule
- Calibrating instruments and controls
- Tightening loose fasteners and connections
- Testing safety systems and controls
- Documenting equipment condition and performance
- Adjusting components for optimal performance
- Conducting predictive tests (vibration, thermal, electrical)
These proactive maintenance activities form the foundation of a successful asset management program, helping organizations maximize equipment reliability while minimizing unexpected failures and the costly repairs they necessitate.
Repair and maintenance expense examples
Repair and maintenance expenses vary widely depending on the equipment type, industry, and whether the repair and maintenance work is performed internally or externally. Understanding these costs helps maintenance departments allocate resources effectively.
Personnel costs
Maintenance and repair work requires various skilled professionals:
- Maintenance technicians: Handle routine maintenance tasks and basic repairs, typically as internal staff members with hourly rates ranging from $30-$40 depending on experience and location.
- Specialized engineers: Address complex equipment issues requiring deeper technical knowledge. Mechanical, electrical, and automation engineers command higher rates, whether employed internally or contracted.
- Trade specialists: Include electricians for electrical systems, HVAC technicians for climate control equipment, hydraulic specialists for fluid power systems, and controls technicians for automation systems. These specialists often have certification requirements and specialized tools.
- Reliability professionals: Focus on analyzing maintenance data, implementing predictive techniques, and optimizing maintenance programs to reduce repair costs.
Internal vs. external resources
Evaluating the total cost of repairs must account for both the direct expenses incurred (labor, parts, equipment) and indirect costs (production losses, quality impacts, delivery delays). For critical equipment, these indirect costs often significantly exceed the direct repair expenses, reinforcing the value of preventive maintenance strategies.
Organizations face critical strategic decisions when allocating maintenance responsibilities between their in-house teams and outside specialists.
- Internal maintenance teams:
- Lower hourly rates compared to contractors
- Greater familiarity with facility equipment
- Faster response times for emergency repairs
- Consistent availability for scheduled maintenance
- Require investment in training, tools, and management
- External contractors:
- Provide specialized expertise not available internally
- Supply specialized equipment without capital investment
- Offer scalable workforce for large projects or fast turnarounds
- May provide manufacturer-certified service for warranty compliance
- Typically charge premium rates (often 1.5-3x the cost of internal labor)
How to decrease your maintenance, repair, and operations (MRO) expenses
Reducing MRO expenses requires a strategic shift from reactive repairs to proactive maintenance. Organizations that successfully minimize these costs focus on prevention rather than reaction.
Proactive maintenance strategies
Implement preventive maintenance programs: Develop systematic maintenance schedules based on manufacturer recommendations, equipment usage patterns, and historical data. Routine inspections catch issues before they cause failures, reducing emergency repair costs.
Invest in staff training: Well-trained maintenance technicians identify potential problems earlier, perform maintenance tasks more effectively, and make fewer errors. Regular training on equipment, procedures, and safety reduces both repair frequency and severity.
Utilize CMMS software: Computerized Maintenance Management Systems track asset history, automate work orders, manage inventory, and analyze maintenance data. This technology eliminates inefficiencies, prevents missed maintenance, and provides valuable insights into equipment performance and maintenance costs.
Adopt condition monitoring: Implement technologies that track equipment health in real time, including vibration analysis, thermal imaging, and oil analysis. These tools detect deterioration patterns before they lead to failures, allowing for planned interventions rather than emergency repairs.
Standardize equipment and parts: Reduce inventory costs and technician training requirements by standardizing equipment models and parts where possible. This approach streamlines maintenance processes and enables bulk purchasing discounts.
Cost benefits of prevention vs. reaction
The financial case for preventive maintenance is compelling when comparing total costs:
Preventive maintenance costs:
- Scheduled labor hours at standard rates
- Planned parts replacement at normal pricing
- Minimal production disruption during scheduled downtime
- Predictable budget allocation
Reactive repair costs:
- Emergency labor rates (often 1.5-2x standard rates)
- Rush-ordered parts at premium prices
- Production losses during unplanned downtime
- Quality issues from hasty repairs
- Potential safety incidents due to equipment failure
Maintenance experts recommend an 80/20 ratio—80% of resources dedicated to preventive activities and 20% to reactive repairs. Organizations that achieve this balance typically see significant reductions in total MRO expenses while improving equipment reliability, extending asset lifespan, and enhancing operational efficiency.
Simplify preventive maintenance with MaintainX
MaintainX enables maintenance teams to create, assign, and track preventive maintenance tasks through an intuitive interface accessible on any device. The platform's built-in work order system ensures nothing falls through the cracks, while digital checklists replace unreliable paper processes.
With MaintainX, organizations typically achieve:
- 32% reduction in unplanned downtime
- 30% savings on monthly maintenance costs
- 39% improvement in overall equipment effectiveness
- 53% improvement in work order completion rates
- 49% increase in planned maintenance percentage
The platform also facilitates real-time communication between technicians and managers through built-in messaging, allowing teams to solve problems faster. Advanced reporting features provide visibility into maintenance metrics, helping organizations identify patterns and make data-driven decisions.
FAQs on maintenance and repairs
What is considered repair vs. maintenance?
Maintenance refers to routine, scheduled activities performed to preserve asset functionality and prevent breakdowns. This includes inspections, cleaning, lubrication, and other minor repairs and adjustments that extend equipment life. Maintenance is proactive and planned.
Repairs are reactive responses to equipment that has already failed or broken down. While repairs restore functionality, they address problems after they occur rather than preventing them. Repairs typically happen unexpectedly and often result in unplanned downtime.
What is an example of a repair cost vs. a maintenance cost?
Repair cost example: Emergency replacement of a failed pump motor in a manufacturing line, costing $5,000 for the part, $2,000 in rushed shipping, $3,000 in emergency labor rates, plus $60,000 in lost production during the 8-hour downtime ($7,500/hour).
Maintenance cost example: Scheduled quarterly inspection and lubrication of the same pump motor during planned downtime, costing $200 in labor and $50 in lubricants, with no production loss since the maintenance work is performed during off-hours.
What are the 3 types of repairs?
- Corrective repairs: Planned responses to issues identified during inspections before complete failure occurs. For example, replacing a bearing showing signs of wear detected during a routine inspection.
- Emergency repairs: Urgent fixes for sudden, complete failures that stop production. These unplanned repairs often require immediate attention, such as repairing a broken hydraulic line on excavation equipment or replacing a blown HVAC motor.
- Deferred repairs: Non-critical issues where the repair is postponed to a more convenient time. For example, postponing cosmetic fixes to retail fixtures until after holiday shopping periods or delaying secondary equipment repairs until scheduled downtime.
What are the 4 types of maintenance?
- Preventive maintenance: Scheduled, routine activities performed while equipment is still functioning to prevent failures. Examples include regular inspections, lubrication, cleaning, and component replacements based on time intervals or usage metrics.
- Predictive maintenance: Data-driven approach using condition monitoring technologies to determine when maintenance is actually needed. This includes vibration analysis, thermal imaging, and oil analysis to detect potential failures before they occur.
- Corrective maintenance: Addresses identified issues before they cause equipment failure. While reactive in nature, it targets minor problems discovered during inspections before they lead to breakdowns.
- Reliability-centered maintenance: Strategic approach that analyzes each asset's functions, potential failures, and consequences to determine the most appropriate maintenance strategy for different equipment types and criticality levels.
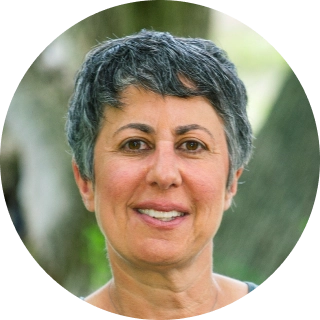
Caroline Eisner is a writer and editor with experience across the profit and nonprofit sectors, government, education, and financial organizations. She has held leadership positions in K16 institutions and has led large-scale digital projects, interactive websites, and a business writing consultancy.