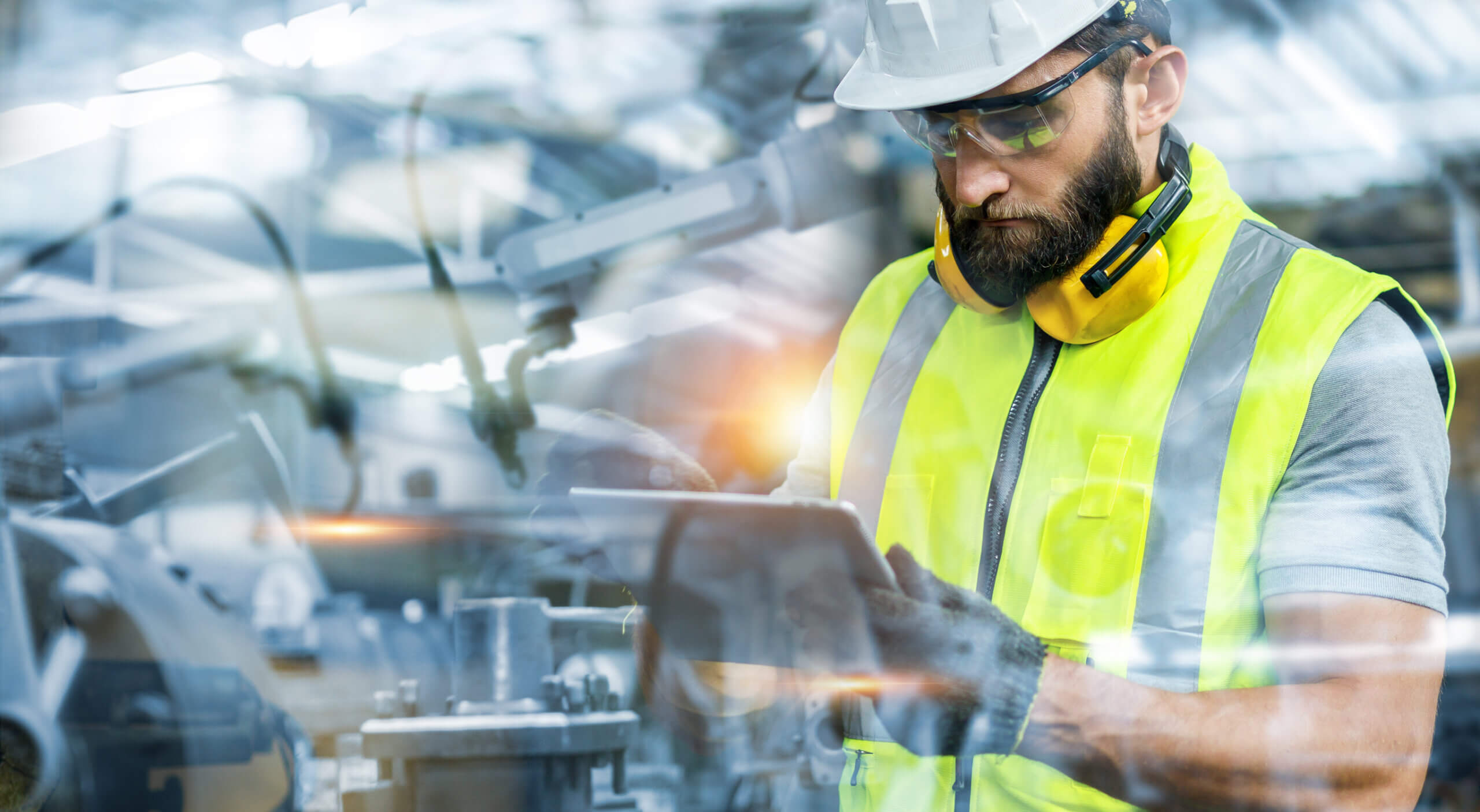
Preventive maintenance is a proactive approach that ensures equipment and machinery are in good condition, reducing the likelihood of unexpected breakdowns and costly repairs. PM is a type of regular maintenance that involves scheduled inspections, cleaning, lubrication, and replacing worn-out parts to keep the equipment functioning optimally. In addition to these benefits, preventive maintenance can also improve the overall performance of equipment. By ensuring that equipment is properly lubricated and adjusted, it can run more efficiently, reducing energy consumption and improving productivity.
Preventive Maintenance Is Proactive
Preventive maintenance (PM) is a proactive approach to maintenance that aims to keep an asset in good working order by fixing issues before failures occur. In addition, the practice reduces unplanned downtimes by scheduling maintenance at regular intervals. When performed consistently, PM can help organizations minimize expenses associated with unplanned downtimes, reduce maintenance costs, and enhance reliability.
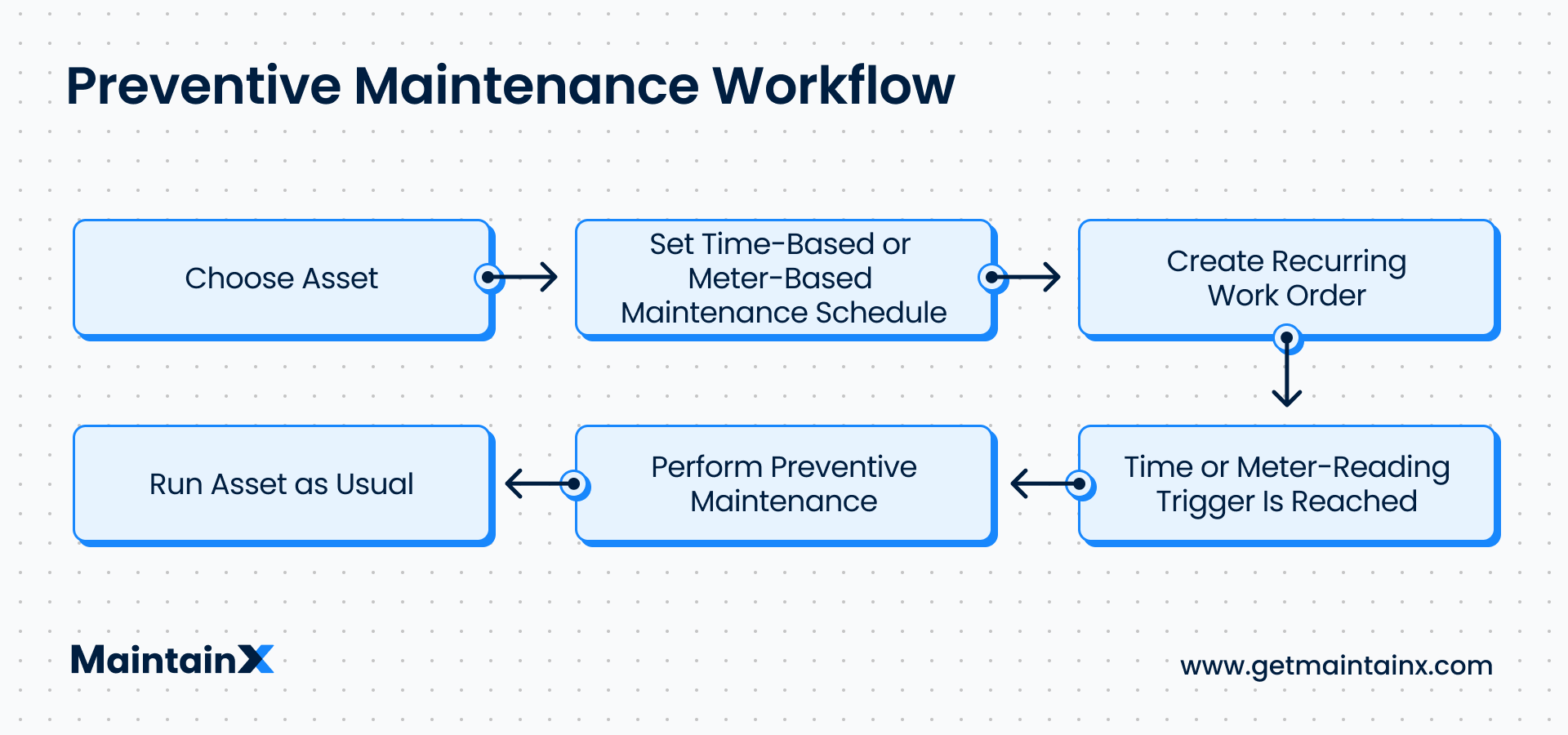
The U.S. Department of Energy estimates that PM can save facilities up to 18 percent more in maintenance costs than reactive maintenance alone. This article will review the different types of preventive maintenance and what you need to include in your PM program.
PM tasks are performed regularly to reduce the likelihood of equipment malfunctioning or complete failure. They are performed throughout an asset’s normal operating conditions. Operational and maintenance managers schedule PM tasks according to manufacturer recommendations, average asset life cycles, or historical behavior patterns.
“… [planned] maintenance programs have been shown to lead to a tenfold increase in ROI, a 25%-30% reduction in maintenance costs, a 70%-75% decrease of breakdowns and a 35%-45% reduction in downtime.”
Forbes
6 Simple Reasons to Use Preventive Maintenance
As a manufacturer, the best facilities management plan keeps your equipment running optimally. Preventive maintenance benefits include the following:
1. Reduced Downtime
Company leaders cannot afford to overlook the impact of equipment downtime and disruptions on organization profitability. Unexpected equipment downtime forces maintenance personnel to divert their focus from preventive maintenance activities to reactive maintenance. Unfortunately, reactive maintenance is often more expensive than preventative maintenance. Unplanned maintenance can mean waiting for parts or outside maintenance technicians.
2. Enhanced Safety
The more often assets are checked, the less likely dangerous problems occur. Following preventive maintenance schedules reduces the risk of unexpected breakdowns, health hazards, and liability lawsuits. Regular preventive maintenance can also improve safety by identifying potential hazards before they become a risk. For example, regular inspection of electrical equipment can help identify frayed wires or damaged insulation, which can be dangerous if left unaddressed.
3. Longer Equipment Lifespan
PM schedules ensure business assets are running according to manufacturer and consumer guidelines. As poorly performing parts are updated, assets perform at a steady level of productivity throughout the year. This reduces the frequency of capital expenditures needed to purchase new equipment. There’s a lot to be said for preventive maintenance plans to increase the useful life of your equipment.
4. Increased Productivity and Efficiency
As reported by Deloitte, inadequate maintenance strategies can reduce an organization’s production capacity by 20 percent. Modern preventive maintenance solutions allow operational managers to digitize essential equipment details, assign recurring maintenance work orders, and review asset history from the convenience of their mobile devices. Equipment uptime is a key factor in enabling workforce productivity and efficiency.
5. Reduced Costs
Reactive maintenance downtime contributes to costly repairs. Using equipment to the point of failure may cost 10X more than performing periodic maintenance. Sometimes, internal employees can accomplish those repairs quickly. Asset management plans should aim for 80% preventive maintenance and 20% reactive or corrective maintenance.
Other times, organizations must wait on outsourced professionals to get the job done. Companies that adopt PM experience fewer breakdowns, which translates to greater output. According to Jones Lang LaSalle’s “Determining the Value of Preventive Maintenance,” a telecommunications company experienced a 545 percent ROI when implementing a preventive maintenance plan. Moving away from run-to-failure maintenance plans to schedule preventive maintenance increases cost savings.
The best maintenance teams optimize equipment reliability so much so that their organizations make significantly more money than they spend on maintenance-related expenses.
6. Less Energy Consumption
Poorly maintained electrical assets often consume more energy than those operating under normal conditions. PM allows energy-robbing issues to be addressed quickly, resulting in smaller utility bills. The more energy your business saves, the higher your profits will be.
Track Preventive Maintenance with Key Performance Indicators (KPIs)
Key performance indicators and metrics provide insights into the effectiveness of maintenance teams and systems operations.
Maintenance KPIs are measurements that link the effectiveness of organizational processes with specific maintenance goals. O&M managers use maintenance KPIs to measure, analyze, evaluate, and improve processes to enhance asset reliability.
Good maintenance KPIs act as quantifiable benchmarks that correlate with broader company goals. For example, an organization wanting to cut costs may set a KPI to minimize maintenance costs by 10 percent. Of course, no two maintenance departments are exactly alike. Additionally, best practices can vary widely by industry, sector, and location.
Maintenance KPIs can measure:
- Efficiency
- Asset downtime
- Asset performance
- Inventory management
- Maintenance task management
- Maintenance spending and costs
- Workplace safety and compliance
Put simply, organizations use maintenance KPIs to measure the performance of maintenance technicians, operational systems, and processes.
“Companies know where they want to go. They want to be more agile, quicker to react, and more effective. They want to deliver great customer experiences, take advantage of new technologies to cut costs, improve quality and transparency, and build value.”
McKinsey
Reduce Asset Deterioration → Reduce Downtime → Reduce Costs
Look under the hood of any organization, and the primary goal of its preventive maintenance program is the same:
Preventive Maintenance (PM) is planned maintenance that increases the longevity of company assets, equipment, and infrastructure. Also known as preventative maintenance, PM includes adjustments, cleaning, lubrication, repairs, and replacements. Put simply, any kind of maintenance that isn’t a reaction to “Oh crap, when (or how) did that happen?” is preventive maintenance.
Types of Preventive Maintenance
A maintenance task must possess three components to be considered preventive maintenance:
- It’s systematic
- It’s performed routinely
- It’s aimed at reducing or minimizing equipment failures
These characteristics define the scope of all preventive maintenance tasks. Regardless of the industry, running a successful preventive maintenance program involves several moving parts. Operational managers must catalog assets, adopt organizational calendars, assign work orders, and hold team members accountable to ensure PM procedures don’t backlog. However, you might be surprised to learn there isn’t just one type of PM method. New technologies have created new ways to predict equipment breakdown with unparalleled accuracy in recent years.
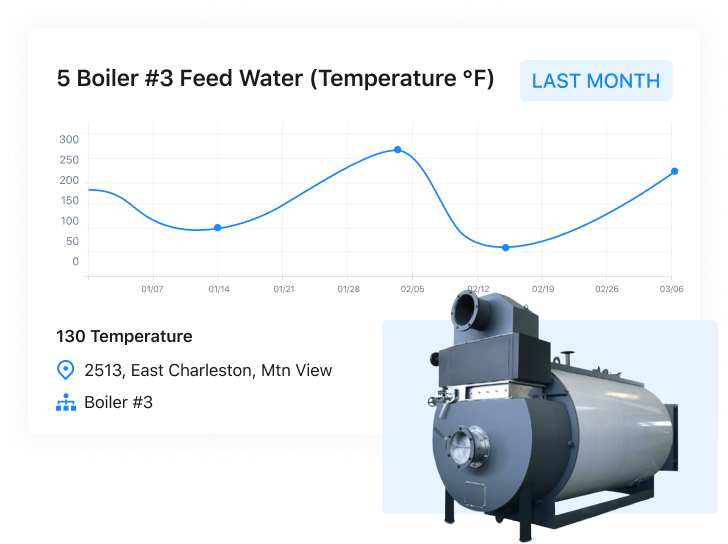
Meter-Based Maintenance
Meter-based maintenance, also known as performance-based maintenance, is slightly more complex than periodic maintenance. This preventive maintenance method is performed when a meter reading indicates that an asset should be serviced. Common variables of measurement include, but are not limited to, hours used, miles driven, parts produced, and pressure generated. Essentially, all meter readings are based on time-based triggers. Consequently, meters must be regularly monitored to ensure equipment is maintained. Sometimes the asset will have a built-in meter, while other times, the machine will require separate components for measurement.
Examples of Meter-Based Maintenance:
- Conveyor belt machines with maximum run times
- Changing the oil of a motor every 15,000 miles
Periodic Maintenance
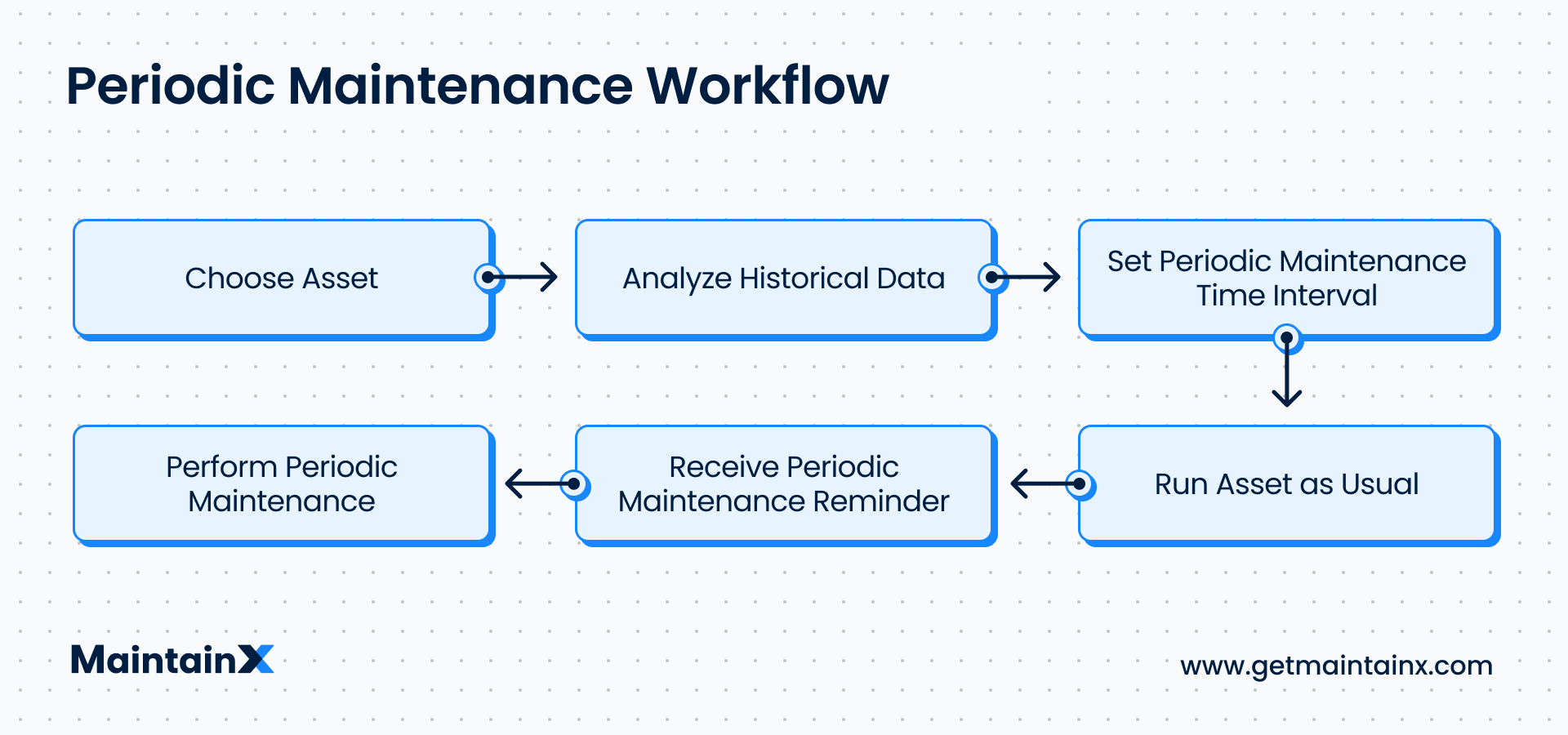
Periodic maintenance, or time-based maintenance, is performed on assets at scheduled intervals throughout the calendar year. It could be done annually, quarterly, monthly, or weekly. The easiest way to determine how often to update asset parts is to check the manufacturer’s guidelines. Each piece of equipment comes with specific maintenance recommendations designed to extend lifespans.
Examples of Periodic Maintenance
- Cleaning corrosion
- Changing lubricating oils and filter components
Predictive Maintenance
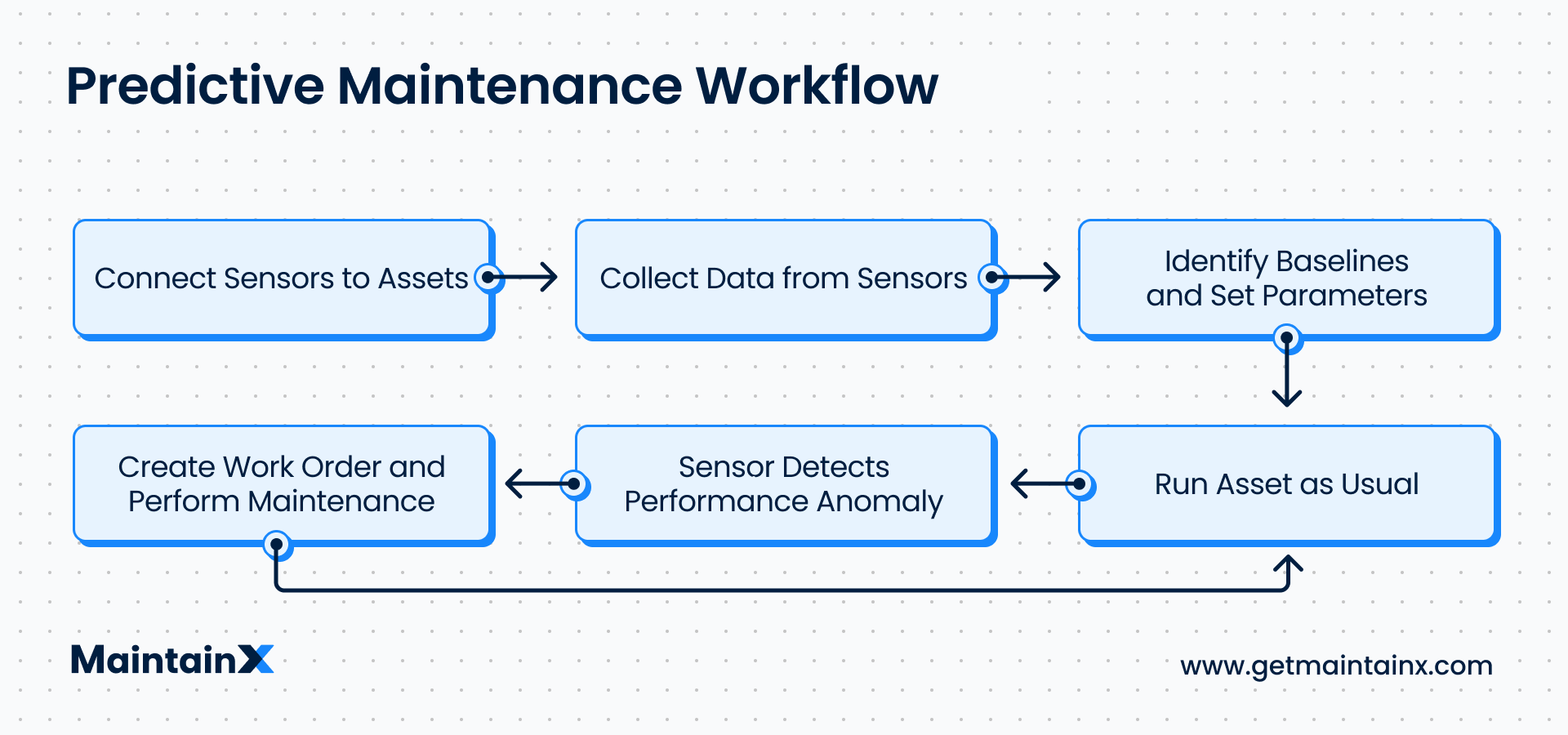
Predictive Maintenance (PdM) is the “just right” solution for not overdoing it or underdoing it with PM. This advanced maintenance method monitors the condition of assets using sensor devices. Once a sensor detects an abnormality, a work order is automatically generated within a CMMS and assigned to a technician.
Predictive maintenance programs can save organizations time, staffing, and money in the long run. However, emerging technology isn’t a good fit for all teams. Ideal candidates will already have a high level of PM organization in place to set up initial PdM baselines. If your team is still in reactive maintenance mode most of the time or isn’t willing to make a sizable investment, we recommend sticking with time-based and meter-based PM.
Examples of Predictive Maintenance
- Thermal sensors installed on equipment provide automated alerts when vents are in danger of overheating.
- Vibration meters attached to centrifugal pump motors to identify abnormal spikes in acceleration.
Prescriptive Maintenance
Similar to predictive maintenance, prescriptive maintenance (RxM) makes data-based decisions. However, this equipment monitoring method takes efficiency even further with machine learning software. The smart software analyzes equipment conditions over time, assesses operational risks, and makes specialized recommendations that outperform generic manufacturer guidelines. As a result, rxM allows maintenance teams to track variable operating conditions up to the time of failure. The technology behind the advancement is called “prescriptive analytics” and was created to hypothesize potential outcomes that could lead to equipment stops.
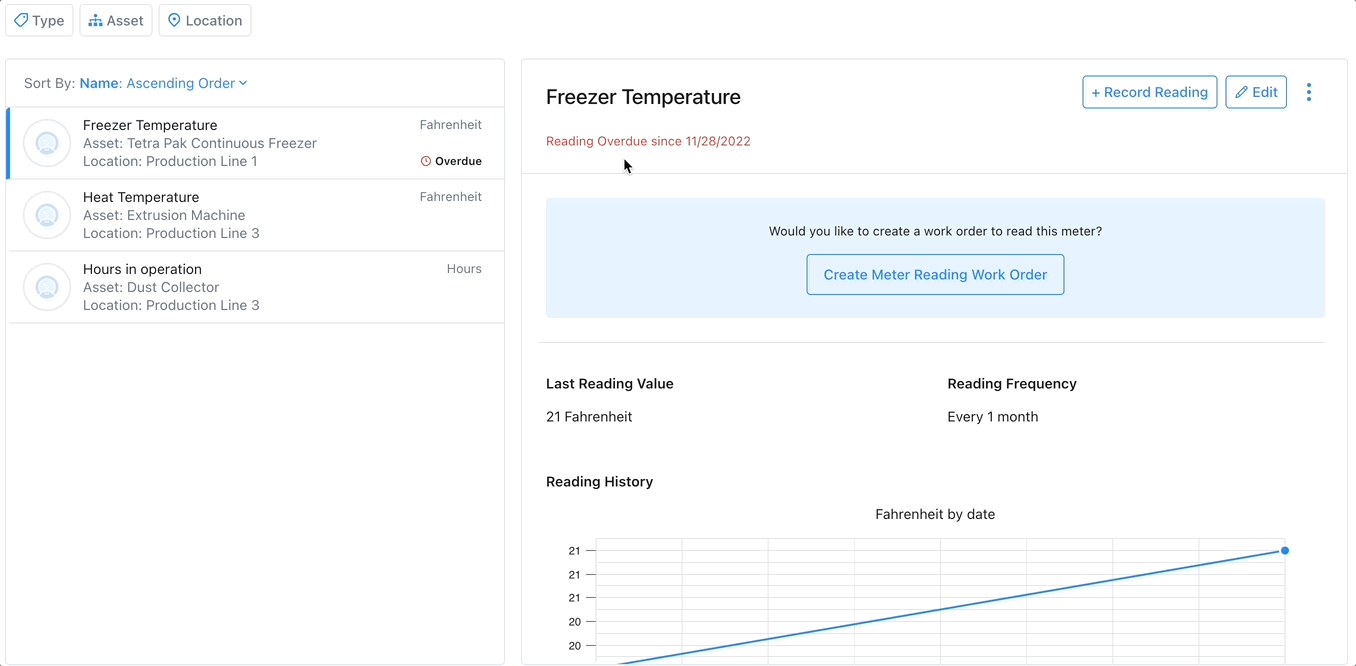
Examples of Prescriptive Maintenance:
• During thunderstorms, which can raise the barometric pressure, AI can trigger you to adjust the pressure in a processing tank.
• If your production line gearbox is due for a monthly PM, AI can determine the likelihood of a failure
Preventive maintenance checklists help organizations reduce unplanned downtimes, increase asset reliability, minimize maintenance costs, and improve operations. While initially launching a preventive maintenance program may seem complicated, it’s simple if you effectively plan for it.
Focus on scheduling PM for your most critical assets to keep your new maintenance program affordable, manageable, and effective.
Which Type of Preventive Maintenance Is Best for Your Organization?
The answer depends on your company size, existing PM systems, and budget. However, most organizations would benefit from a mixture of predictive and meter-based maintenance because of their proven overall efficiency and low entry cost.
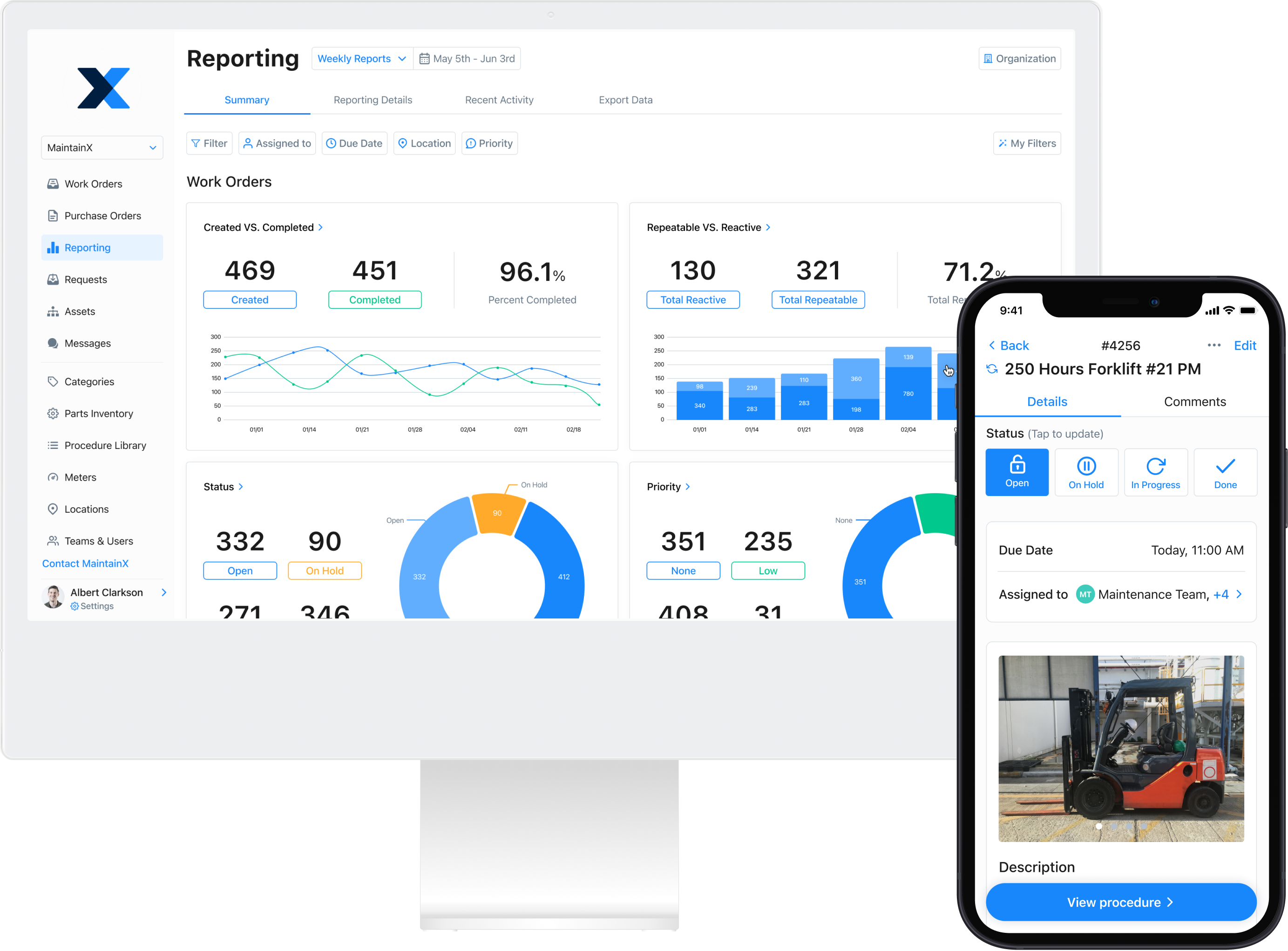
Seriously, You Need a CMMS for PM
Computerized maintenance management systems (CMMS) organize O&M tasks, including planning, scheduling, and tracking work orders. Preventive maintenance software, like MaintainX’s CMMS, also can maintain asset historical records, manage inventory, and monitor spending trends. Most effective PM programs have one thing in common: a CMMS that the entire team feels comfortable using. Maintenance planners can create, implement, and track recurring work orders via user-friendly dashboards.
MaintainX helps teams create work orders, track asset history, and enhance accountability with digital audit trails.
FAQs
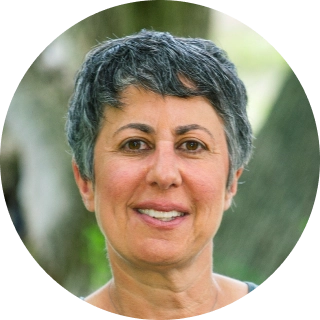
Caroline Eisner is a writer and editor with experience across the profit and nonprofit sectors, government, education, and financial organizations. She has held leadership positions in K16 institutions and has led large-scale digital projects, interactive websites, and a business writing consultancy.