The threat of downtime is an ever-present danger that can impact production and be very costly. In fact, Senseye’s whitepaper, The True Cost of Downtime, found that the annual cost of downtime averages $129 million per facility.
One way to ensure you keep your assets in good order? Paying attention to FMECA.
FMECA (Failure Mode, Effects, and Criticality Analysis) helps identify potential failures in your systems and is an extension of the FMEA (Failure Mode and Effects Analysis). FMECA also factors in criticality analysis, which is a systematic approach to applying a criticality rating to equipment and assets based on potential risks.
In this article, you’ll learn what FMECA is and how to plan, track, and optimize maintenance at your facility.
What is FMECA?
FMECA is a risk assessment methodology in which you determine failure modes, assess their level of risk to your equipment or system, and rate the failure based on that level of risk. The U.S. military invented this FMECA analysis technique in the ‘40s and continues to use it even today under the MIL STD-1629A. It is predominantly used in space and military applications, but manufacturers can practically use it in almost any industry.
FMECA is a valuable technique for several different functions. First, teams apply FMECA when performing failure detection and criticality analysis on systems to improve their performance. In addition, FMECA typically provides input for Maintainability Analysis and Logistics Support Analysis, both of which rely on FMECA data.
FMECA and predictive maintenance
With Industry 4.0, many industries are adopting predictive maintenance strategies for their equipment. They use FMECA to prioritize failure modes and identify mechanical system and subsystem issues.
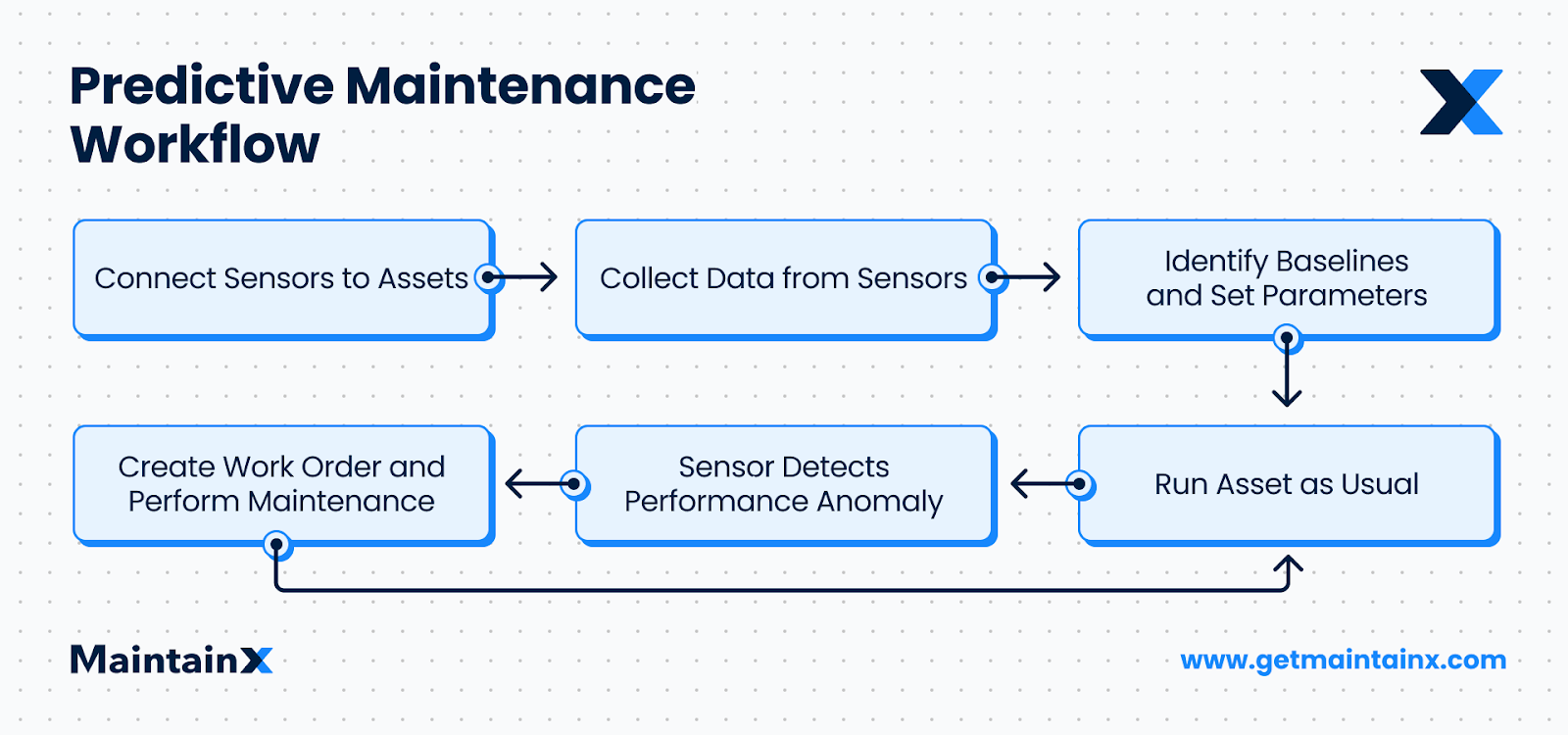
Once you have a list of failure modes in order of priority, you can implement preventive strategies to mitigate those risks. Of course, the process isn’t foolproof—it doesn’t guarantee zero failures. Some level of failure risk will persist, and you or your team will make mistakes at some point, but FMECA helps minimize the probability and costs of failure for the business.
FMECA vs. FMEA
FMECA is used instead of FMEA when a more detailed and numbers-based method is needed to determine the risk of potential failures. The FMECA process also involves completing an FMEA process worksheet, followed by a Criticality Worksheet to determine criticality. In contrast,r FMEA focuses on qualitative information where you explore what-if scenarios. It assesses the failure modes and their effects and relies on a multi-functional team to set Severity and Occurrence using guidelines.
FMEA becomes FMECA with the addition of critical analysis, allowing the FMEA team to identify critical failure points and determine the probability of failure. FMECA goes a step further and assesses the criticality of failure modes and ranks them based on priority (or level of criticality).
When you have component data, using FMECA makes more sense because it lets you focus on the criticality of failure modes. However, if component data is unavailable, use FMEA.
Why is FMECA performed?
As we’ve discussed, FMECA helps you identify potential failures in your systems so you can get ahead of them. Let’s explore a few more reasons why FMECA matters.
Strengthening reliability and safety
By performing FMECA, you can identify potential failure modes and their effects on your equipment and systems. With this knowledge, you can take proactive measures to prevent these failures and mitigate their negative effects. As a result, you’ll improve reliability and be able to address potential safety hazards before they can lead to accidents.
Prioritizing maintenance efforts
Dealing with limited resources means maintenance teams often have to decide how to prioritize maintenance work. FMECA provides you with a clear understanding of which components or systems are most critical and most likely to fail. This approach means that you can modify your maintenance planning to focus on these specific areas. By prioritizing maintenance activities based on criticality and failure risk, you can ensure you make the most of your maintenance resources, reduce the likelihood of system failures, and improve overall efficiency.
Ensuring compliance with industry standards
Many industries have stringent safety and reliability standards that organizations must adhere to, and FMECA is often a key component of these compliance efforts. Conducting a thorough FMECA ensures that you can document and address potential failure modes and their effects. This system not only helps you avoid penalties and legal issues, but also demonstrates a commitment to high safety and reliability standards, which can enhance your organization's reputation and trustworthiness.
How to run an FMECA
Plan, organize, and prepare
Begin by defining the scope of the FMECA, which includes identifying the system or process you want to analyze and its boundaries. Gather all relevant data, such as design documents, historical failure data, and operational procedures. You should also assemble your core team here. Ensure that they have experience with the system under analysis, and work with them to determine your FMECA approach. This step should include clearly deciding the specific methods and tools to be used during the FMECA process.
Complete a system breakdown
Consider each system you want to analyze and break it down into smaller, manageable subsystems and components. Taking this approach helps you perform more detailed analyses. Use visual aids such as block diagrams, flowcharts, or hierarchical charts to represent each system's structure. This way, you’ll get easy insight into the interactions between different parts of the system. You’ll also be able to ensure you don’t miss any details, and consider all potential failure modes.
Identify possible failure modes & effects
For each subsystem and component, identify all potential failure modes. Think about all the ways in which a component can fail to perform its intended function. Document the potential effects of each failure mode on the system, including both immediate and secondary impacts.
Determine causes of failures
Once you’ve determined the potential failures, go one step further to identify the underlying causes of each. Failure causes can include: design flaws, material defects, manufacturing errors, environmental conditions, or human factors. Understanding the root causes helps you develop effective mitigation strategies and corrective actions.
Assign severity & occurrence ratings
Next, rate the severity of each failure mode's effects on the system using a predefined scale. Use a numerical scale (say from 1 to 10) to keep things easy to understand. After rating, assess the probability of occurrence for each failure mode based on historical data, expert judgment, or statistical analysis.
Identify detection and prevention controls
Before creating any new workflows to address potential failures, identify existing controls and procedures that can detect or prevent each failure mode from occurring. Detection methods may include inspections, testing, or monitoring systems, while prevention controls could involve design changes, redundancy, or protective measures. Document these controls to evaluate their effectiveness in managing the identified risks.
Assign detection ratings
Assign a detection rating to each failure mode based on the effectiveness of the identified detection controls. Use a predefined scale to rate the likelihood that a failure will be detected before it causes a system impact. Lower detection ratings indicate higher confidence in the controls' ability to catch failures early.
Calculate the Risk Priority Numbers (RPN)
Calculate the Risk Priority Number (RPN) for each failure mode by multiplying its severity, occurrence, and detection ratings. The RPN provides a quantitative measure of risk, with higher values indicating greater risk. Use the RPNs to prioritize failure modes for corrective actions and resource allocation.
Create prioritized plans to address failure modes
Develop and implement action plans to address the highest-priority failure modes based on their RPNs. These plans may include design modifications, process improvements, additional controls, or preventive maintenance strategies. Document the plans and track their implementation to ensure that the identified risks are effectively mitigated and that the system's reliability and safety are enhanced.
How MaintainX supports FMECA
Say you’re done coming up with a list of critical items you need to work on to minimize the effects of failure. How do you execute these actions effectively?
A computerized maintenance management system (CMMS) like MaintainX ensures you have complete control. Use MaintainX to:
Schedule maintenance: Once you’ve identified potential failure modes, you’ll need to take concrete steps to prevent them and mitigate their effects. MaintainX enables robust maintenance management, from creating to assigning and monitoring work orders. You’ll be able to schedule work orders in advance, complete with checklists and digital SOPs to ensure technicians know exactly how to complete the necessary work. With MaintainX’s native mobile app, real-time notifications ensure no technician ever misses a maintenance task. This also means that you can track work orders from start to completion, communicate with staff right from the shop floor, and provide real-time feedback.
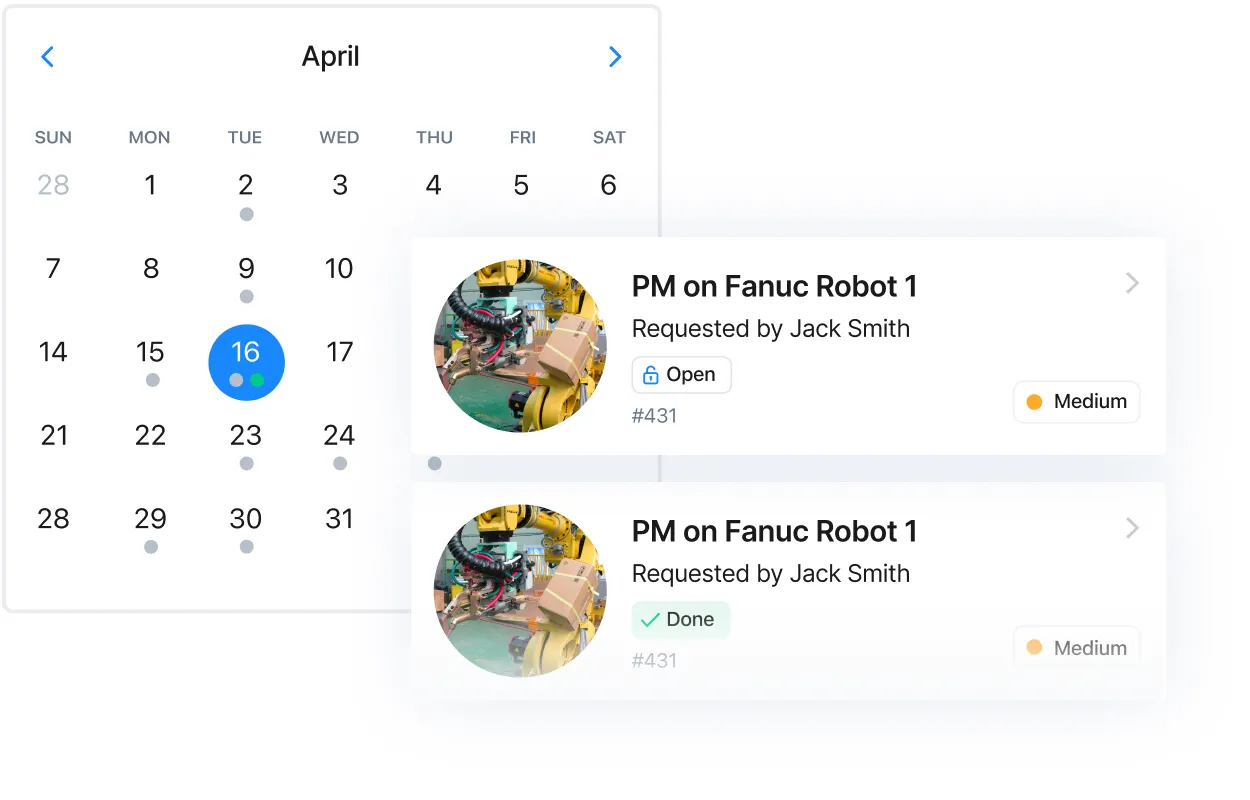
Track asset performance: Stay on top of your asset performance and identify imminent or potential failures with MaintainX’s asset management features. Use meters and readings to track assets over time and gain insight into their performance. Get an instant view of historical asset performance data by scanning barcodes and QR codes to pull up the right assets in the field.
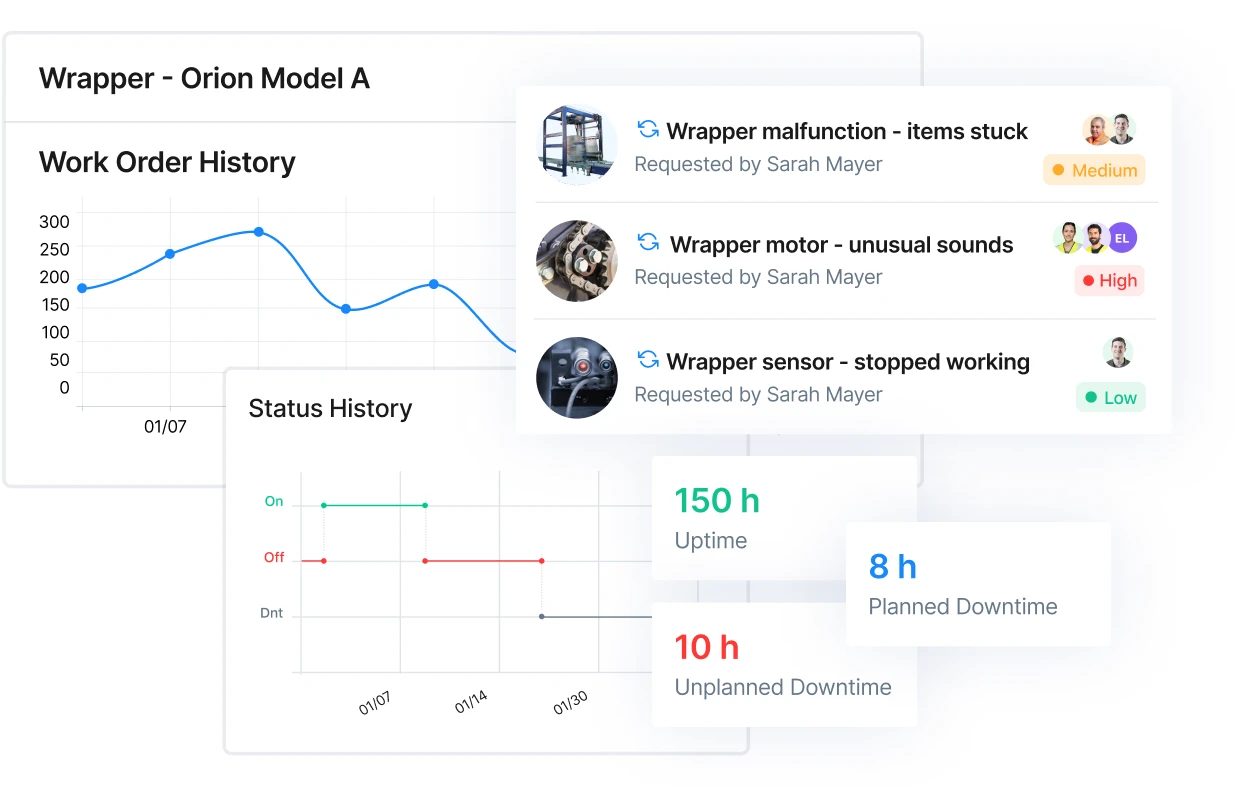
Analyze failure data: Tracking asset performance and collecting failure data is only one component of the process. To make data-driven decisions about mitigating the effects of failure modes, you’ll need real insight. MaintainX’s robust reporting module enables you to analyze your data. With custom dashboards and visualizations, you’ll be able to identify trends and assess the criticality of different failure modes.
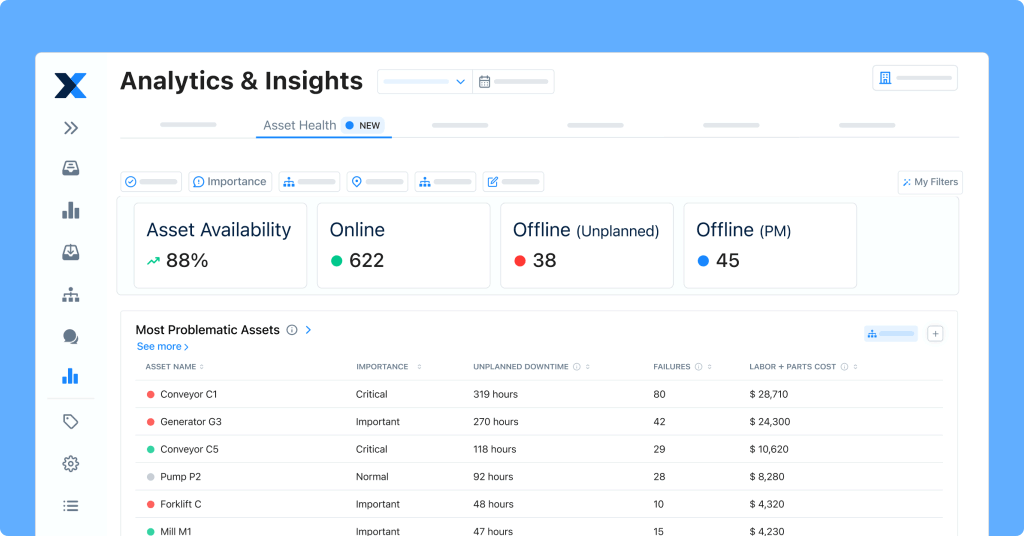
Ensure availability of necessary parts: Mitigate the effects of failures and maintain system reliability by never running out of crucial parts. MaintainX helps you spend less on emergency parts shipping, avoid stockouts, and reduce storage costs by using data to ensure you order only what you need.
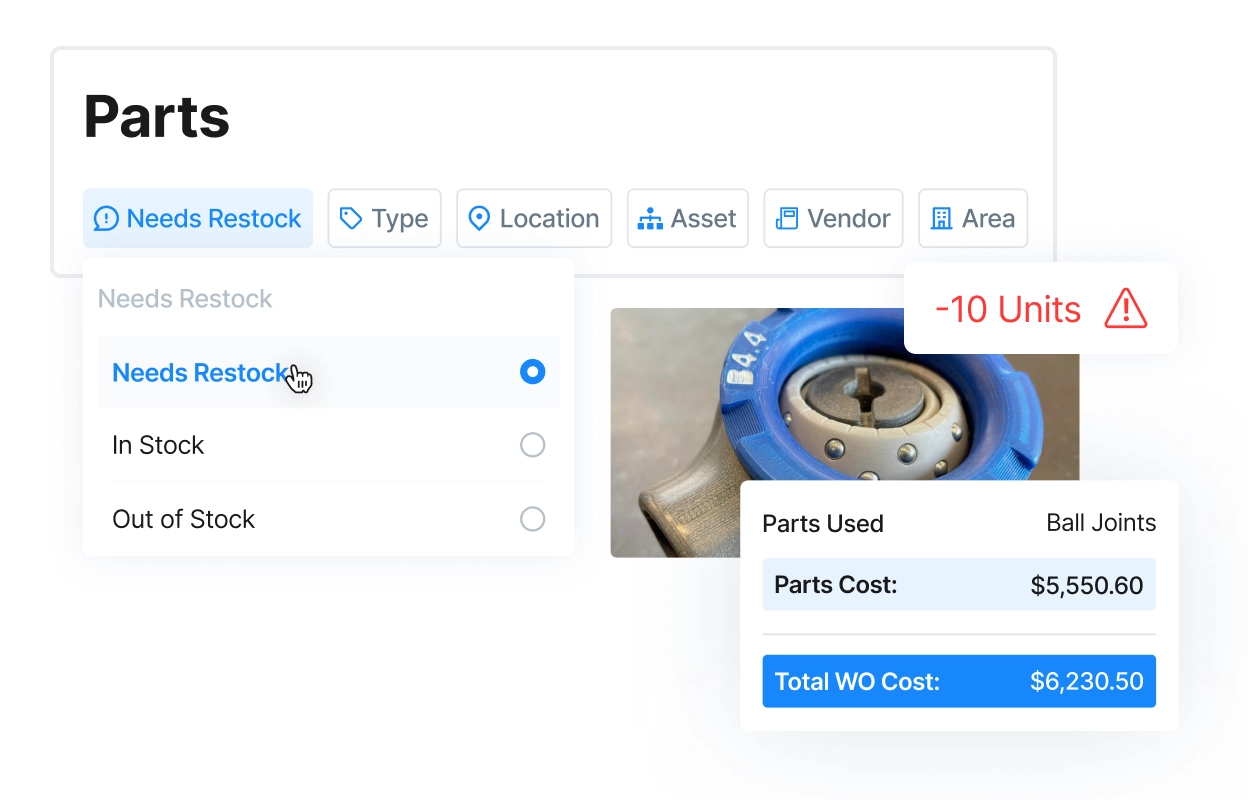
Everything you do in MaintainX lives on the cloud, making it accessible from anywhere. In addition, MaintainX automatically creates an audit trail for all actions, saving you and the team plenty of time.
FMECA FAQs
Variations of the FMECA process exist, which adapt the standard FMECA methodology to different stages of the product lifecycle. Examples include Design FMECA (DFMECA) and Process FMECA (PFMECA). DFMECA focuses on identifying potential failures in the design phase, while PFMECA analyzes failures related to manufacturing and assembly processes.
FMECA prioritizes failure modes by calculating a Risk Priority Number (RPN) for each identified failure mode, with higher numbers denoting increased risk.
To calculate Risk Priority Number (RPN) in FMECA, multiply three ratings: the severity of the failure mode's impact, the likelihood of its occurrence, and the effectiveness of existing detection controls. The formula is RPN = Severity × Occurrence × Detection, with each rating typically assigned on a scale from 1 to 10, where higher numbers indicate greater risk.
Industries that commonly use FMECA for risk assessment include aerospace, automotive, medical devices, electronics, and manufacturing.
To create an FMECA worksheet, start by listing all subsystems and components in a table format. For each component, document potential failure modes, their effects, causes, and current controls, then assign severity, occurrence, and detection ratings. Include columns for calculating the RPN and space for noting recommended actions and their status to facilitate comprehensive analysis and follow-up.
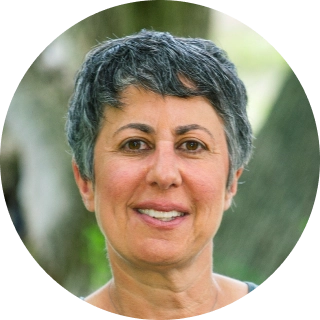
Caroline Eisner
Caroline Eisner is a writer and editor with experience across the profit and nonprofit sectors, government, education, and financial organizations. She has held leadership positions in K16 institutions and has led large-scale digital projects, interactive websites, and a business writing consultancy.
See MaintainX in action