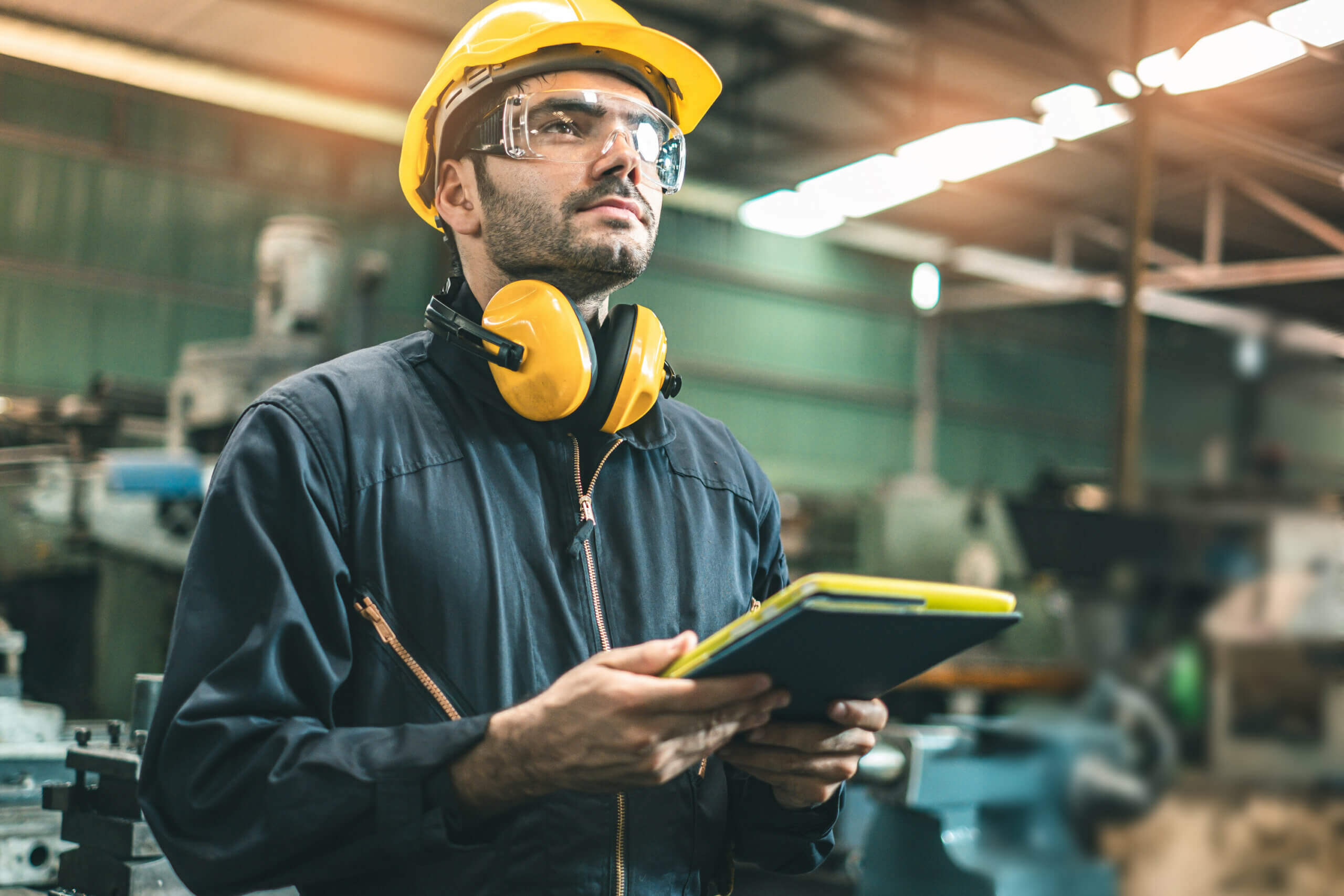
Asset tracking is a powerful tool for businesses of all sizes. Asset inventory management is a combination of asset management and inventory management.
It requires the perpetual balancing of several moving parts, including the development of standard operating procedures, customer retention, and predictable profit margins. Of course, the larger the company, the more assets it likely requires to meet its goals. And the more important asset inventory management becomes to scaling your efforts.
In maintenance management circles, asset tracking means monitoring and recording the movement of any assets or resources used to maintain a system. It includes tracking the location, condition, and maintenance history of individual assets or resources and their associated costs, such as repair and replacement costs. Equipment tracking is essential for ensuring efficient and effective use of resources and preventing unnecessary equipment downtime due to mismanagement or negligence.
In this post, we take a closer look at the ins and outs of asset inventory management, already complicated by labor and supply-chain shortages. However, after reading, you may even feel—dare we say—excited to begin cataloging assets!
How Asset Tracking Increases Profits
The prospect of inputting, tracking, and analyzing data for hundreds, if not thousands, of pieces of equipment can feel overwhelming! Especially for hands-on managers who remain involved in day-to-day operations. With that said, taking the time to develop failproof asset inventory management systems can be invaluable.
When your team members can identify what you have, where it’s located, and how much it’s worth (within seconds), they’re poised to make better decisions autonomously. Let’s begin by dissecting the basic concepts involved by answering the following question.
Additionally, by tracking key performance indicators, such as utilization, cycle times, and downtime, equipment tracking can help identify exactly where you can improve maintenance.
Not to mention, asset tracking can save you money by ensuring you have the right parts available when maintenance is needed.
“The emergence of a new generation of data processing, analysis, and visualization tools is starting to help organizations get maintenance planning under control, and take their operations to the efficient frontier.”
McKinsey
What Is Asset Tracking?
According to the Corporate Finance Institute, assets are items that generate “positive economic benefits for organizations.”
Put simply, assets are resources that help organizations meet their production and service objectives. Without assets, you wouldn’t have a business; you would have groups of people standing around with nothing to do!
Assets fall into several categories, including operating, non-operating, physical, intangible, current, and non-current assets. Examples of assets include vehicles, machinery, furniture, computer equipment, intellectual property, and even digital formats such as webinars.
Asset inventory management concerns itself with ensuring departments have access to up-to-date inventories of company assets. Thus, an asset inventory management system helps streamline asset inventory management. It’s a combination of hardware and software technologies as well as processes that oversee the monitoring and maintenance of organizational assets and inventories.
“Asset management and tracking solutions are increasingly critical to achieving greater operational efficiencies in the current market scenario of rapid digitalization in manufacturing environments and office spaces.”
Mordor
Benefits of Asset Tracking
Effective asset-tracking systems make it easy to track the movement of objects across organizational departments. Among other benefits, prioritizing asset inventory management helps streamline supply chains.
Asset management is a core aspect of risk reduction and value creation. Government institutions, non-profit organizations, large companies, and small and medium enterprises (SMEs) need to maintain consistent records of possessions.
Benefits
- Maintain Central Asset Repositories: Storing data in one place makes it easier to generate reports for maintenance scheduling decisions, claim warranties, and apply for asset insurance/financing services.
- Keep Tabs on Asset Whereabouts: Asset management is crucial to tracking the physical location of your assets. The right software allows you to see where assets are located, how they are being used, and if any changes have been made to them recently. You also can track equipment through its lifecycle to optimize its maintenance, upgrade, and disposal timelines.
- Monitor Idle Time: Tracking the utilization of key assets is essential to evaluating team productivity. Asset management systems make it easier to calculate and develop strategies to reduce idle time.
- Evaluate Asset Performance: Understanding the capabilities of your assets is crucial to gaining maximum value from them. Furthermore, you can identify the risks associated with the use of the assets to find ways to reduce them.
- Asset Maintenance: Lastly, facility asset management allows you to develop an effective proactive maintenance strategy to keep your assets in good working condition. You also can track asset maintenance history to make informed maintenance decisions. You will be able to avoid problems associated with under or over-maintenance.
- Improve Safety: Asset tracking can help reduce the risk of accidents or equipment breakdowns by ensuring assets are regularly maintained and operating safely. And during an emergency, a manager can assign work order procedures from the spot of the breakdown. This eliminates the time needed to get back to the office to assign a team.
- Increase Cost Savings: Tracking equipment maintenance history and scheduling preventive maintenance helps reduce the need for emergency repairs and increase asset lifespan. In addition, CMMS asset tracking analytics can also help identify cost-saving opportunities, increase equipment reliability, and reduce lifecycle costs.
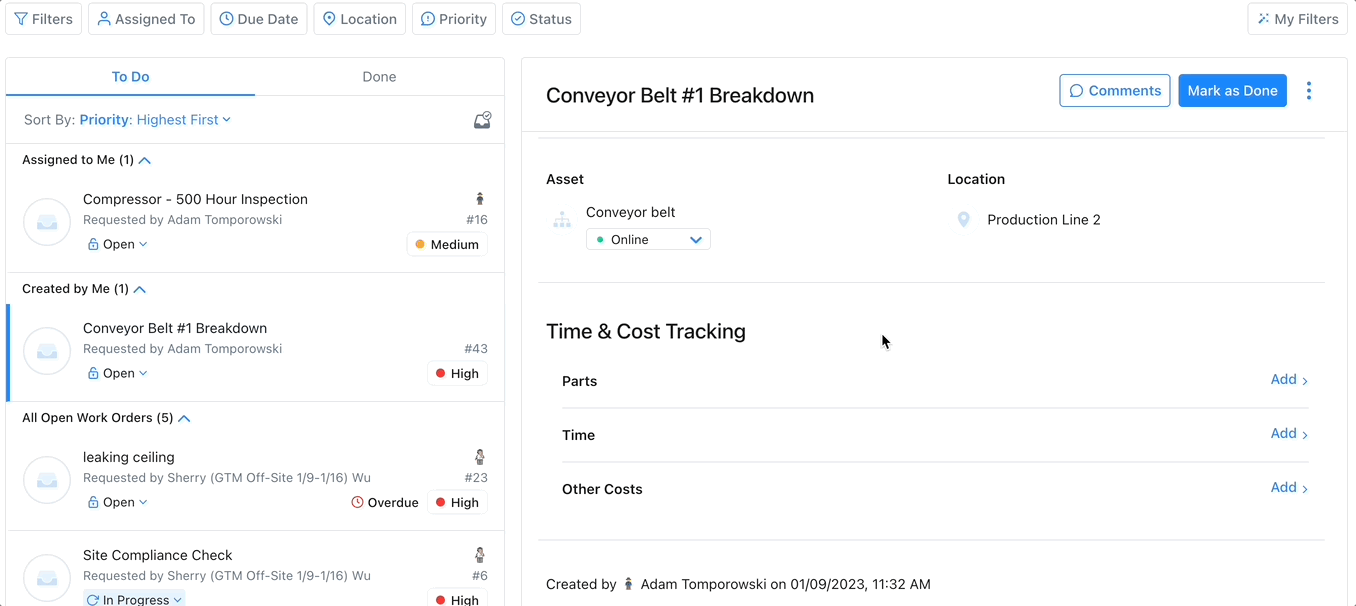
Track Assets with a CMMS
Enhances Maintenance Scheduling: Asset tracking software can monitor an asset’s condition over time, providing information to use to create and optimize preventive maintenance schedules and help avoid emergency maintenance, costly repairs, or expensive replacements.
Improves Budgeting: Asset tracking via advanced reporting and key performance indicators can improve budgeting in several ways. Asset tracking can help managers calculate the useful life of an asset. This enables managers to budget for maintenance and replacement costs accurately.
Increases Efficiency: Asset tracking increases efficiency by providing real-time visibility into the use and location of their assets. This increases productivity by ensuring assets are online when needed.
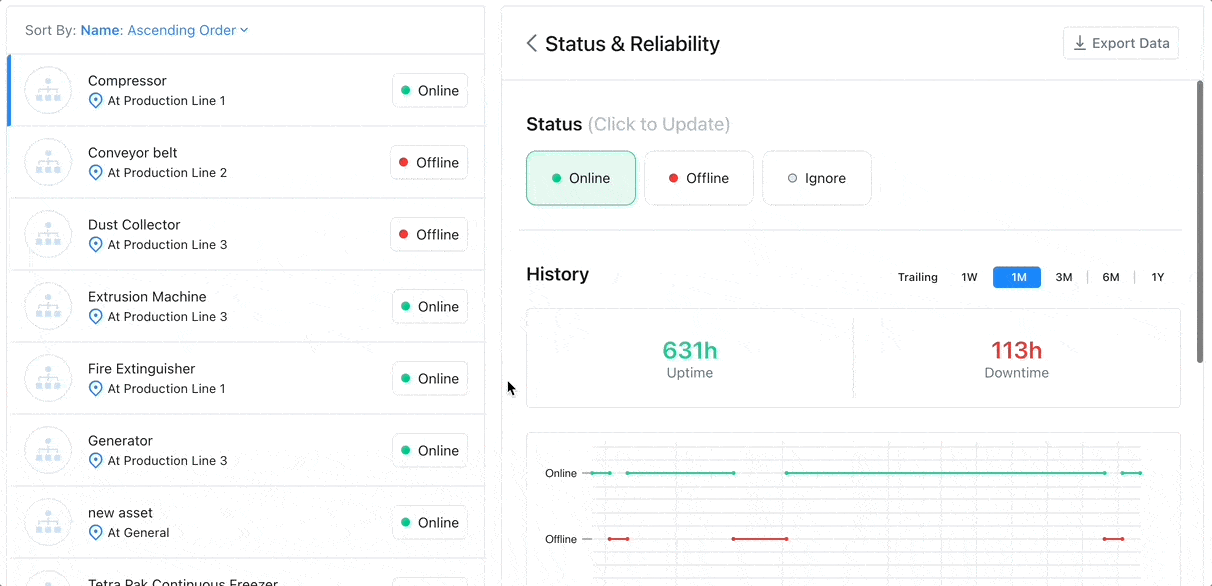
8 Factors to Help You Choose the Best CMMS for Asset Tracking
- Cost: Consider the total cost of the CMMS software, including any additional fees for features, such as asset tracking.
- Ease of Use: Ensure that the CMMS is easy to navigate and use for both technicians, managers, and leadership.
- Scalability: Choose a system that can easily scale up or down with your company as your needs change.
- Automation: Look for a CMMS that can automate tasks such as generating work orders and scheduling maintenance.
- Reporting Features and Advanced Analytics: Ensure that the CMMS offers extensive reporting analytics capabilities to track and monitor equipment performance.
- Security: Check that the CMMS has adequate security measures to protect your equipment data.
- Integration: Ensure that the CMMS easily integrates with other software and systems. Think about your accounting, enterprise asset management (EAM) software, and enterprise resource planning (ERP) systems.
- Support: Check the availability and quality of customer support and technical assistance.
Choose MaintainX for All Your Asset Tracking
At the end of the day, the primary goal of any business is to make a profit. For this reason, looking for opportunities to reduce unnecessary expenses is integral to improving operations. MaintainX features a robust inventory management system, real-time KPI metrics reporting, global procedures, and work order management.
MaintainX streamlines process improvement by providing management with a centralized platform for digitizing, assigning, and managing standard operating procedures. It also facilitates team messaging, enhanced reporting transparency, and automated preventive maintenance scheduling.
We recommend using a CMMS like MaintainX. You can schedule recurring work orders, implement digital SOP checklists, and demonstrate cost avoidance with advanced reporting charts. Check out MaintainX on desktop or mobile app to track your company’s assets and save on costs.
FAQs
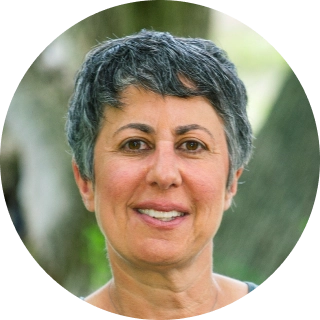
Caroline Eisner is a writer and editor with experience across the profit and nonprofit sectors, government, education, and financial organizations. She has held leadership positions in K16 institutions and has led large-scale digital projects, interactive websites, and a business writing consultancy.