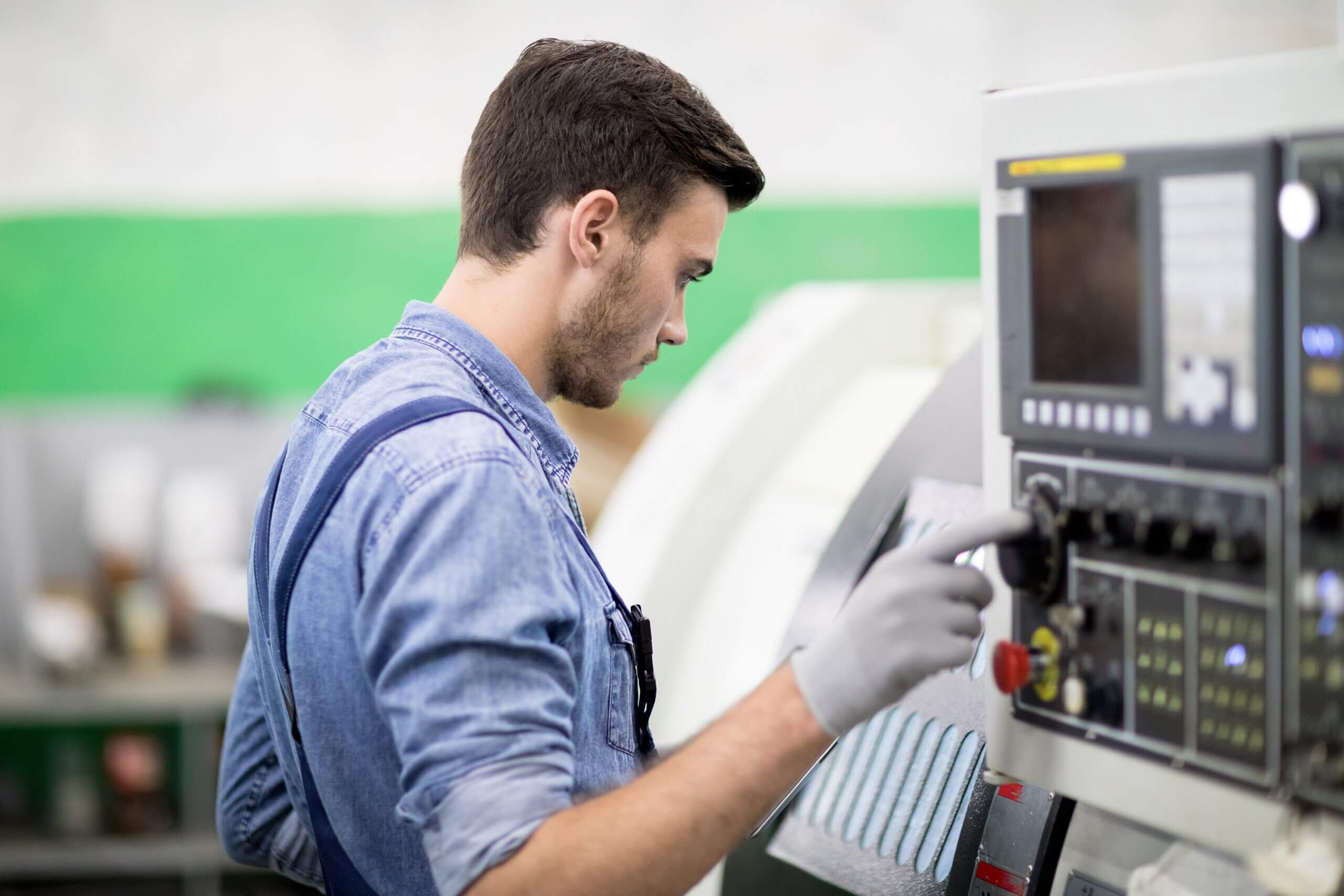
If you want to improve asset reliability while keeping maintenance costs down, you need preventive maintenance.
Preventive maintenance (PM) is a proactive approach to maintenance that aims to keep an asset in good working order by fixing issues before failures occur. The practice reduces unplanned downtimes by scheduling maintenance at regular intervals.
When performed consistently, PM can help organizations minimize expenses associated with unplanned downtimes, reduce maintenance costs, and enhance reliability.
The U.S. Department of Energy estimates that PM can save facilities up to 18 percent more in maintenance costs than reactive maintenance alone. This article will review the different types of preventive maintenance and what you need to include in your PM program.
What Is Included in Preventive Maintenance?
Preventive maintenance minimizes equipment downtime, improves asset lifespans, and lowers maintenance costs. It’s a simple, direct, and systematic way to improve asset reliability.
The most common preventive maintenance tasks include:
- Inspections
- Cleaning
- Lubrication
- Adjustments
- Repairs
- Parts replacement
PM tasks are performed on a regular basis to reduce the likelihood of failure. They are performed throughout an asset’s normal operating conditions. Operational and maintenance managers schedule PM tasks according to manufacturer recommendations, average asset life cycles, or historical behavior patterns.
Resources commonly needed to complete PM tasks include sensor devices, wrenches, drills, scissors lifts, and lockout tagout devices, among others.
Preventive Maintenance and CMMS
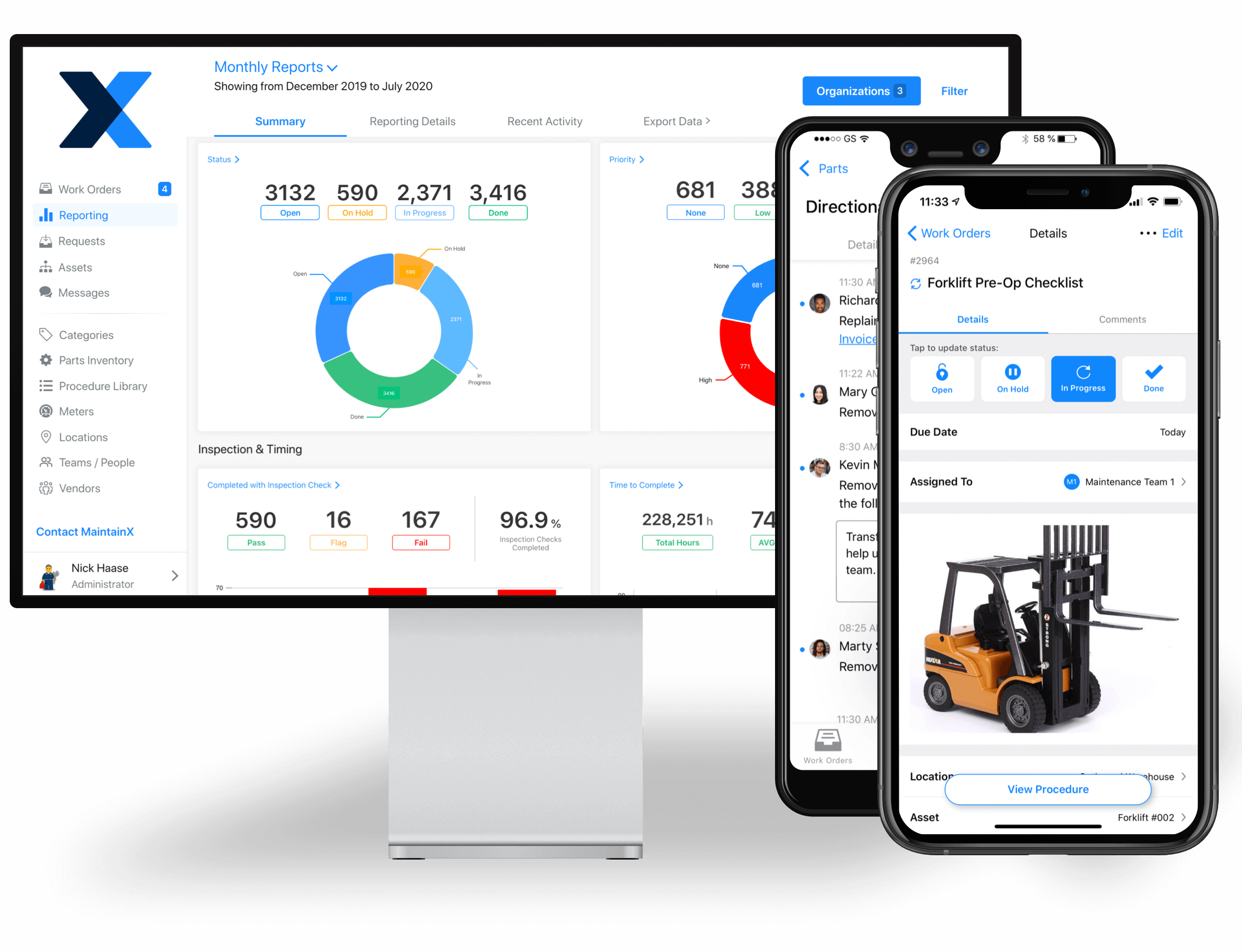
Computerized maintenance management systems (CMMS) organize O&M tasks, including planning, scheduling, and tracking work orders. CMMS also can maintain asset historical records, manage inventory, and monitor spending trends.
Though 39 percent of facilities still rely on paper records for maintenance management, there are many benefits to adopting and integrating CMMS. A cloud-based CMMS provides remote access, real-time maintenance data, automatic work order tracking, and built-in inventory tracking.
The software also improves communication between maintenance managers and technicians by enabling the sharing of real-time updates and maintenance reports. Managers wishing to maximize CMMS can a) adopt a mobile CMMS that workers can keep in their pockets and b) empower team members to become more autonomous in using the technology.
Types of Preventive Maintenance (PM)
Preventive maintenance tasks aim to reduce unplanned downtimes. Maintenance tasks usually are categorized into four broad categories. They include:
- Periodic Maintenance: This type of maintenance includes preventive maintenance tasks performed at scheduled intervals. They can be performed weekly, monthly, quarterly, or annually. For example, you can change your engine oil every three months. Equipment manuals usually contain the recommended maintenance schedules for an asset. Periodic maintenance also is referred to as time-based maintenance.
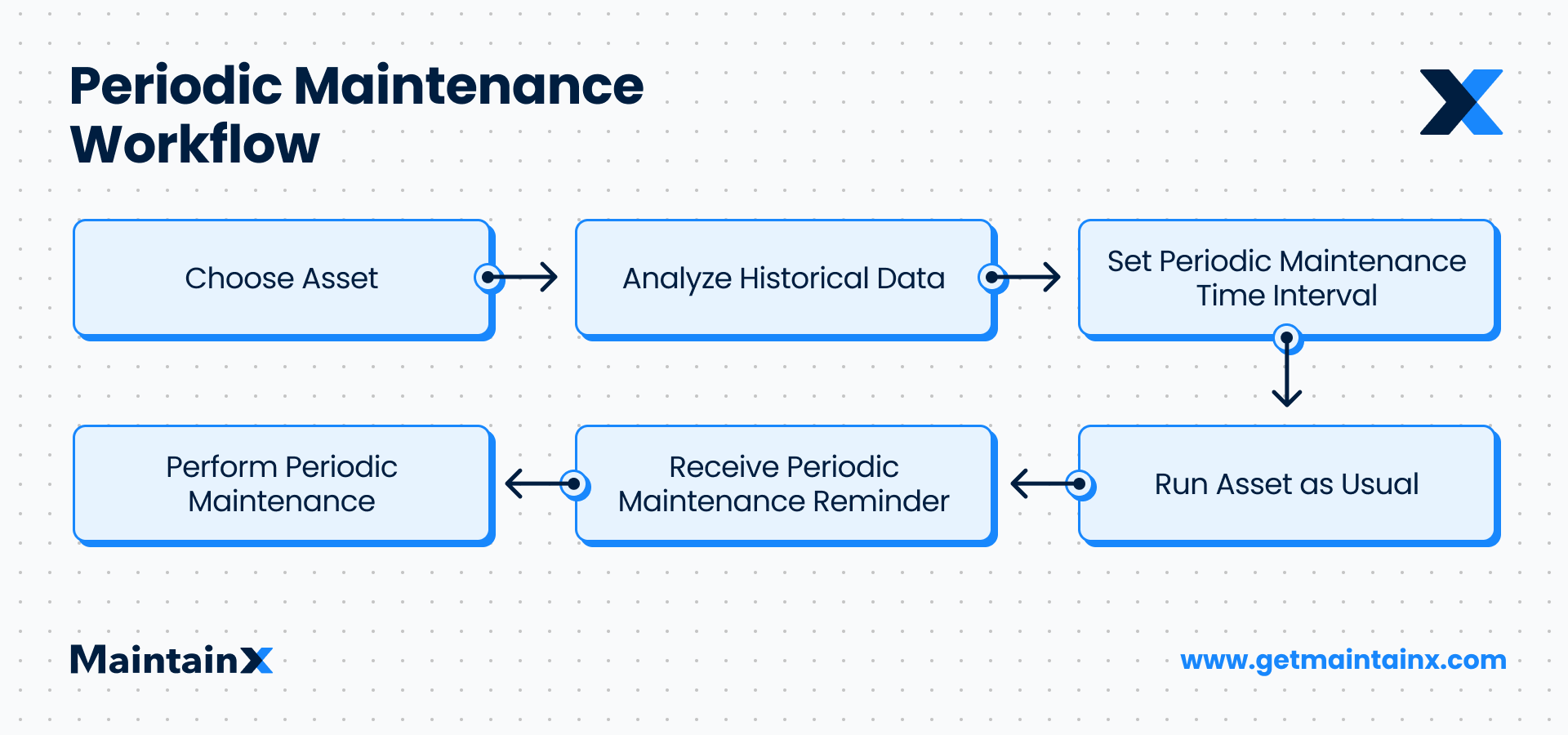
- Meter-Based Maintenance: Also known as performance-based maintenance, this maintenance scheduling is based on equipment usage variables. Such assets usually have meters or counters to measure usage milestones. An example of meter-based maintenance is changing the engine oil every 3,000 miles.
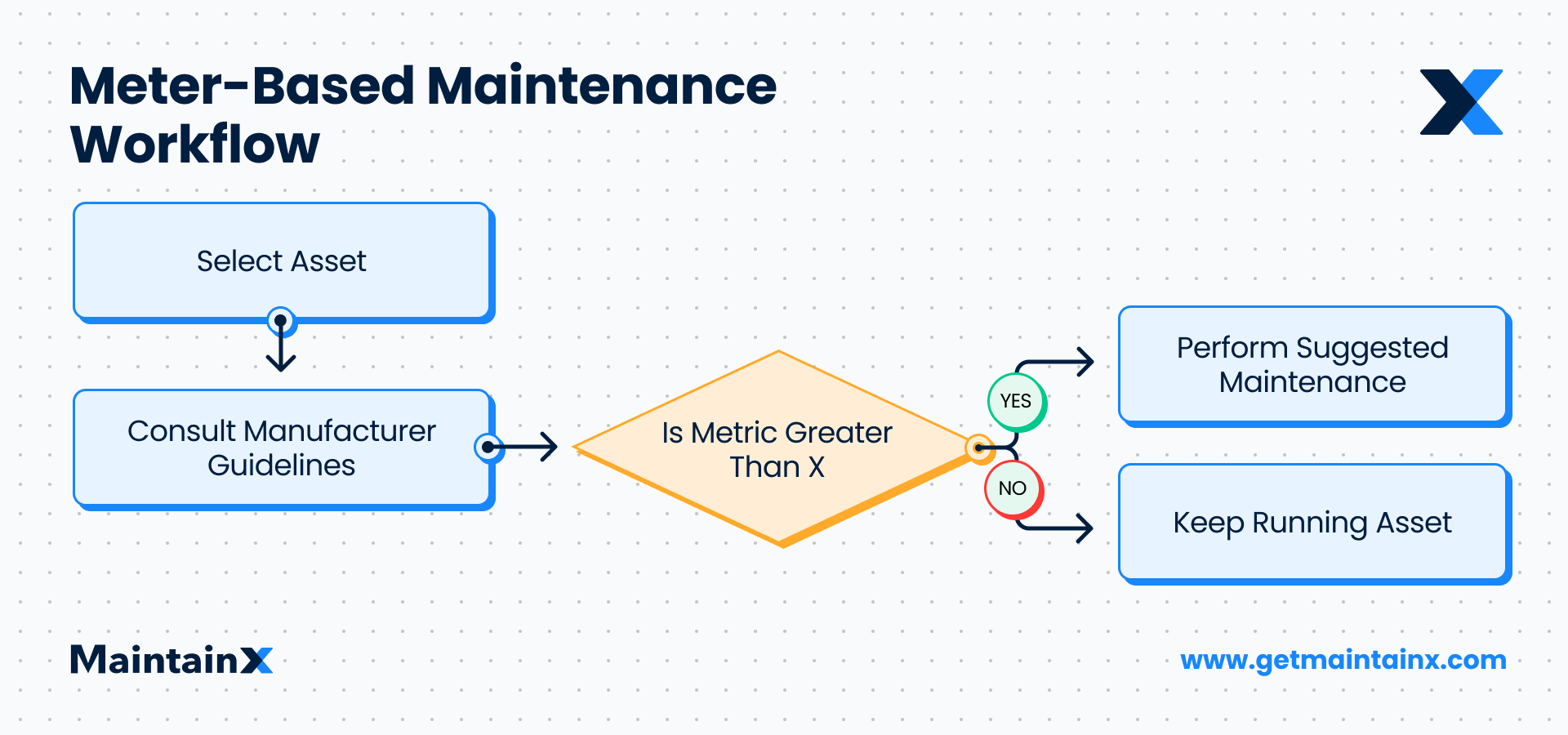
- Predictive Maintenance (PdM): PdM is an advanced form of PM that uses sensor devices and data analysis tools to predict the optimal time when assets should receive maintenance to prevent failure. The goal of PdM is to perform maintenance just before failure occurs to eliminate the risk of under- or over-maintenance. An example of PdM is using vibrational analysis on high-rotating machinery to detect imbalance, misalignment, or bearing wear. Maintenance is then performed when there’s a fluctuation in machine vibrations.
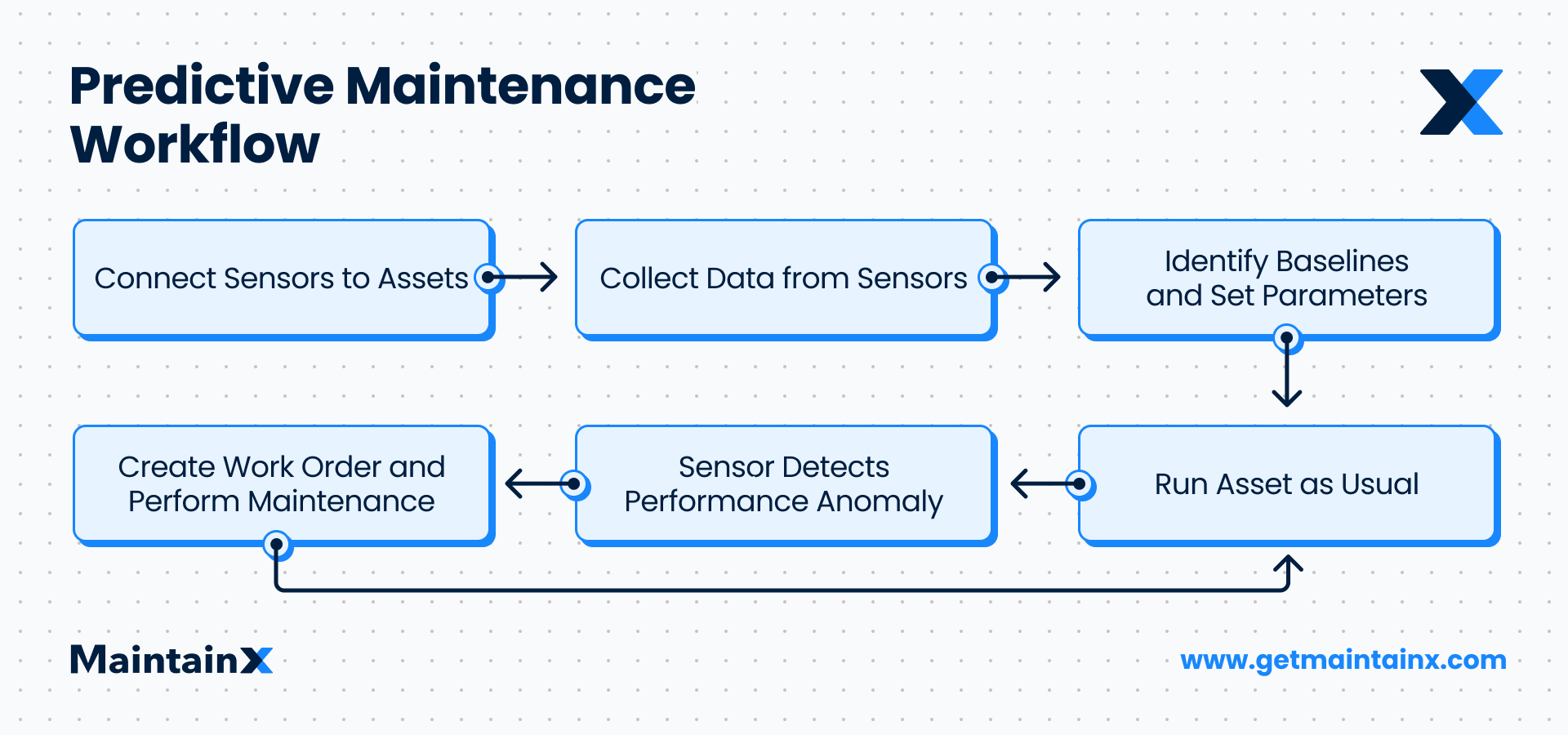
- Prescriptive Maintenance: Prescriptive maintenance is similar to PdM as they both rely on data to make maintenance decisions. However, with prescriptive maintenance, machine learning software gathers and analyzes equipment conditions to recommend specific maintenance actions. This helps to minimize operational risks. For example, sensors or other artificial intelligence (AI) software will recommend adjusting the barometric pressure in a processing tank in the event of a thunderstorm to avoid high pressure in the tank.
Examples of Preventive Maintenance
Almost every industry and organization runs a preventive maintenance program. Real-life examples of preventive maintenance include:
1. Lubricating Moving Parts
Friction can cause a machine to break down and disrupt production. The heat generated from the friction can also result in a fire. Because machines are constantly running, there are high chances of friction. Regularly lubricating the moving parts of the machine can help to reduce friction and unplanned breakdowns.
2. Changing HVAC Filters
With time, HVAC filters become clogged and can result in the entire system breaking down. Repairing or replacing broken-down HVAC systems is more costly than simply replacing the filters every six months.
3. Refrigerator Maintenance
If you operate a restaurant, then a walk-in refrigerator is a critical asset to your business. You can’t afford to have it breaking down. Preventive maintenance activities on the refrigerator include checking the door seals for any leaks, defrosting built-up ice, draining the drip pan, and cleaning the condenser coils regularly.
Automate Preventive Maintenance with MaintainX
Regardless of your organization’s size, a preventive maintenance plan is key to achieving both short-term and long-term maintenance goals. CMMS can help you get the best out of your facility’s PM program.
With MaintainX, you don’t have to sacrifice features for simplicity—you can:
- Create reactive and preventive maintenance work orders.
- Assign recurring work orders to both teams and individuals.
- Monitor progress by maintenance category, priority level, downtime, etc.
- Analyze maintenance costs for greater efficiency and savings.
- Hold text conversations with team members in real time.
Anyone with a smartphone can download the app and get started with our basic plan, which includes unlimited work orders, right away.
FAQs
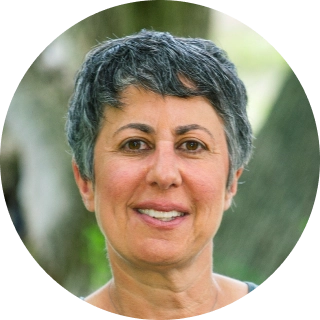
Caroline Eisner is a writer and editor with experience across the profit and nonprofit sectors, government, education, and financial organizations. She has held leadership positions in K16 institutions and has led large-scale digital projects, interactive websites, and a business writing consultancy.