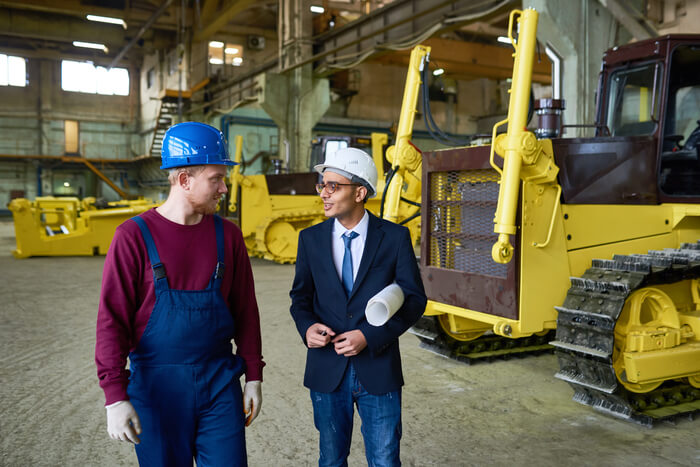
On the surface, it’s easy to fall in love with the concept of reliability-centered maintenance (RCM). It offers what every organization craves: optimization.
RCM is a complete maintenance framework designed to support operational managers in making the most cost-effective, efficient, and strategic maintenance decisions. When properly executed, the strategy extends equipment lifespans, decreases downtime, and reduces inefficient O&M spending patterns.
Motivated by the promise of dramatic department improvements—one study suggests a 70 percent reduction in workloads (page 313) when combined with preventive maintenance (PM)—many of these organizations spent hundreds of thousands of dollars building complex programs supported by sophisticated technologies.
Industry experts promised executives that their investments in costly vibration analysis, infrared, and sound-level measurement technologies would soon deliver ROI. Unfortunately, most of these programs failed.
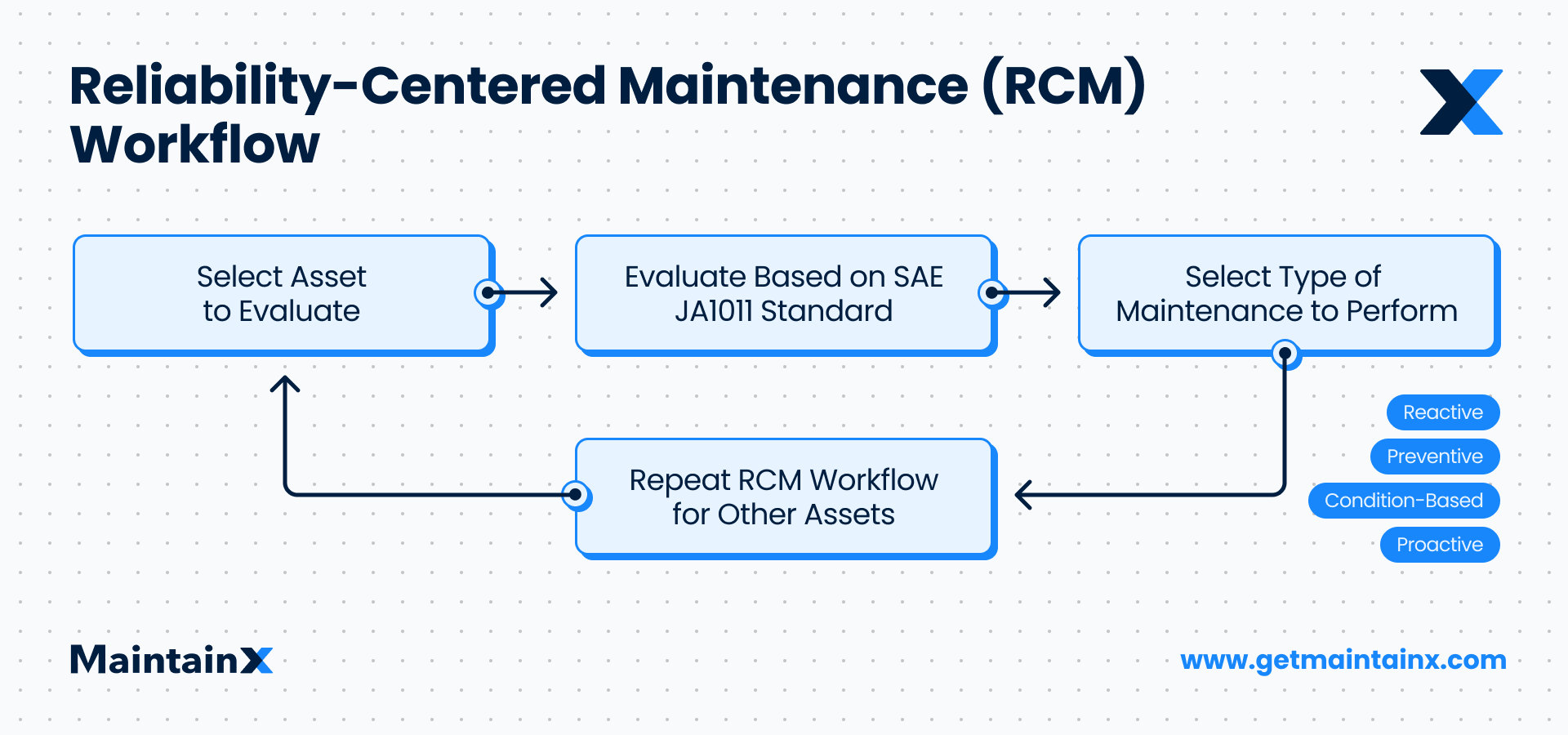
The Surprising Reasons 70% of Reliability-Centered Maintenance Programs Fail
ReliabilityWeb reports that more than 70 percent of RCM programs fail to generate their projected cost savings and/or asset productivity results. Why? Additional research suggests that only 5 percent of organizations implement RCM programs with the right systems in place.
Do the repeated failed attempts mean the strategy is overrated?
Not necessarily. In fact, when appropriately used, RCM is an excellent way to control O&M costs, improve equipment performance, and ensure reliability. So, what’s going wrong in so many program implementations? Surprisingly, it’s often only one or two missing pieces that cause entire initiatives to fall short.
In this article, we’ll highlight four steps to consider before implementing a reliability-centered maintenance program. These points address the most frequent reasons organizations fail to meet their RCM goals. Though you’ll likely still face organization-specific challenges, we hope these tips will better prepare you to hit the ground running.
How Reliability-Centered Maintenance Programs Work
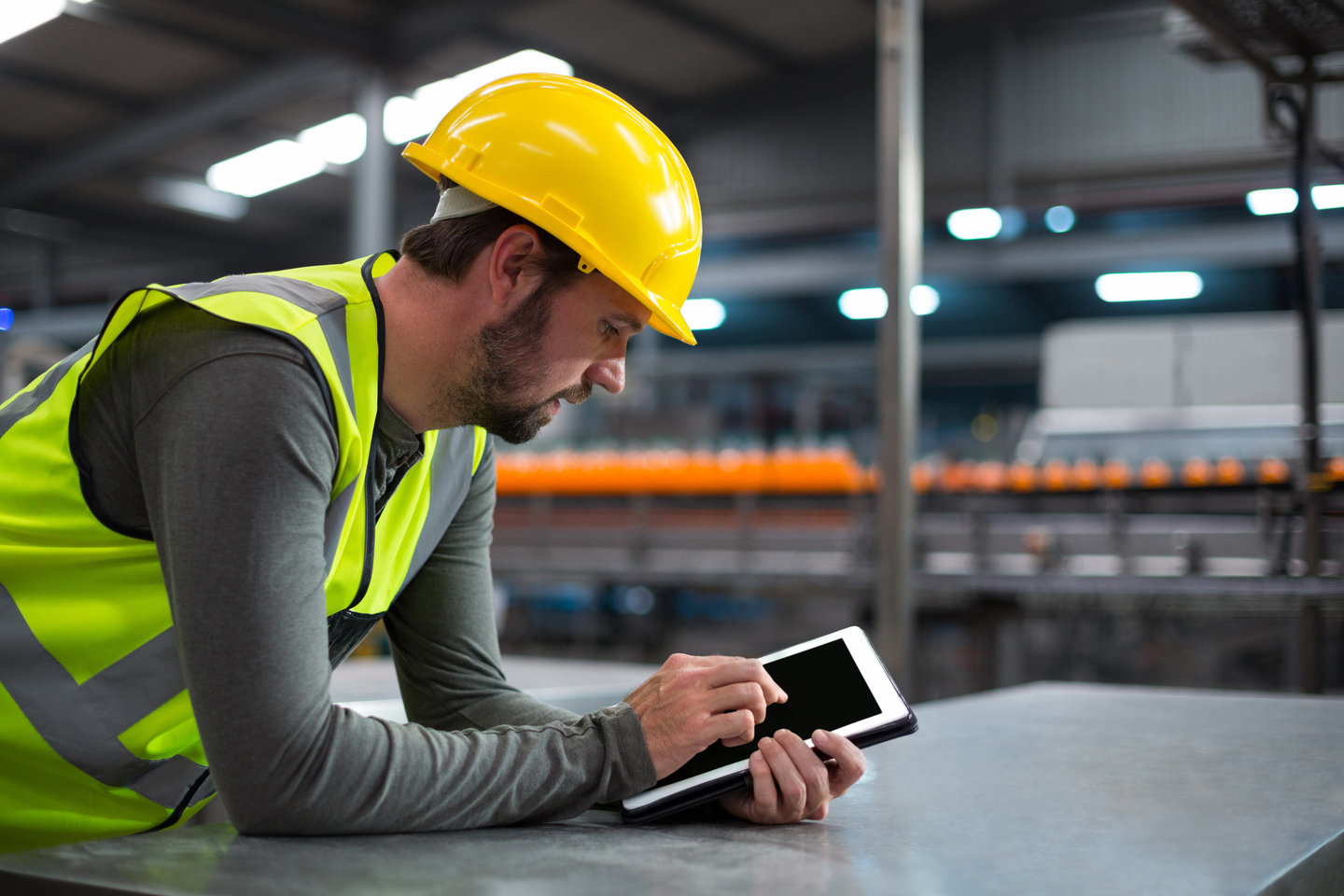
Before we dive in, let’s briefly review how RCM works. Reliability-centered maintenance programs are designed to prevent organizations from making the following common O&M mistakes:
- Wasting manpower on unnecessary preventive maintenance (PM) tasks,
- Wasting capital on expensive unplanned repair fees, and
- Failing to replace assets past their optimal Useful Life.
RCM reduces these inefficiencies by recognizing that not all facility assets hold tangible value distinct from safety, process, and financial vantage points.
As such, top-performing facilities divide their maintenance efforts into less than 10 percent reactive maintenance, 25 to 35 percent preventive maintenance, and 45 to 55 percent predictive maintenance (PdM) on average.
Matching each asset with an ideal maintenance schedule, and setting up the technology to help maintenance planners do so, is only the beginning of reliability-centered maintenance. Management also must invest consistently in the following four steps to achieve consistent progress over time.
4 Steps for Running a Successful Reliability-Centered Maintenance Program
1. Create the Culture
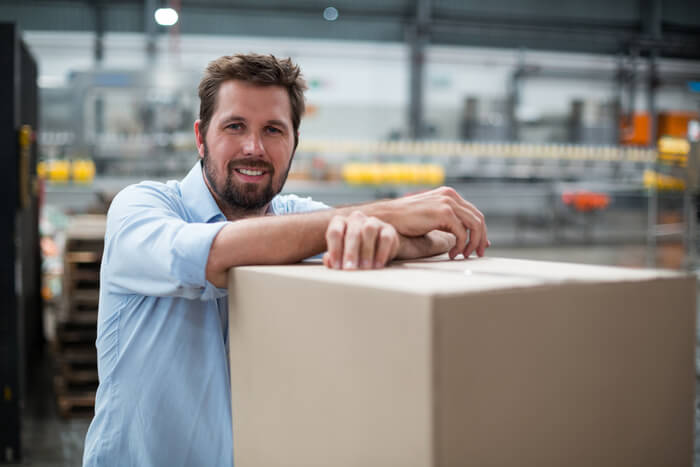
When faced with any kind of organizational problem, how often does it turn out that improving workplace culture is the key to resolution? Time after time, businesses large and small find that an improved company culture can cure many ills. Such is the case with reliability-centered maintenance. Before implementing any new standard operating procedures (SOPs) and investing in a complete maintenance department rehaul, build a culture that supports your efforts.
According to a LinkedIn survey conducted by Terrence O’Hanlon, director of the Reliability Leadership Foundation, cultural resistance to RCM is the program’s number one reason for failure. A whopping 48 percent of the survey’s 376 respondents cited culture as the culprit. Unfortunately, O’Hanlon’s findings are consistent with the results of several studies over the years. RCM initiatives often lack understanding and, thus, support from cost-conscious company leaders.
This “lack of executive sponsorship” from the top-down causes program leaders to sometimes skip necessary RCM framework steps, like consulting with the right industry experts, making new hires, or installing recommended technologies. Additionally, many RCM failure statistics are based on plants using antiquated paper work order systems and failing to prepare adequate systems for data analysis. If your organization’s leadership isn’t entirely on board, consider running a pilot program to prove RCM’s potential value.
Work with leadership to set test parameters for specific pieces of equipment on preventive maintenance plans. Then, invest in a computerized maintenance management system (CMMS) like MaintainX to begin identifying O&M patterns to decrease labor costs, enhance scheduling efficiency, and increase reliability. As you prove ROI with simple data-based improvements over time, executives will likely become more open to hearing about the precise data revelations only predictive maintenance (PdM) technologies can provide.
2. Tighten Existing Maintenance Systems
Would you build a solid house on a shaky foundation? Nope.
Similarly, don’t expect to successfully implement RCM if your facility includes a mishmash of thrown-together operations and procedures. Before adding another layer of operational complexity, make sure your existing systems and processes are clear, documented, and efficient.
Work with maintenance technicians, machine operators, and leadership to develop standard operating procedures (SOPs) for task consistency. The two other most significant improvements an organization can make before delving into RCM are 1) tightening existing PM systems and 2) maximizing CMMS value.
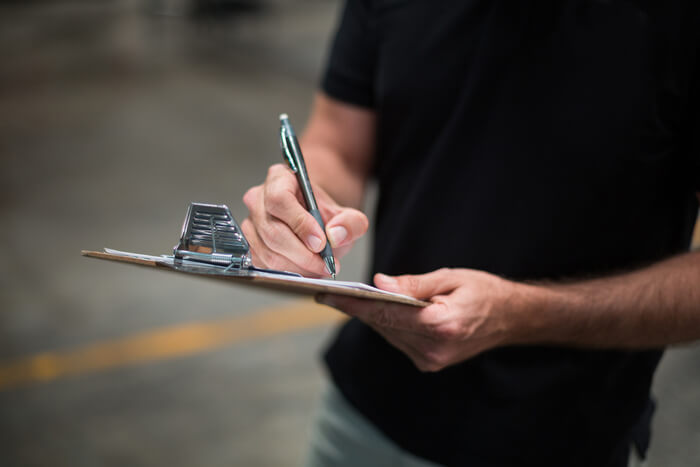
Studies show approximately 70 percent of North American manufacturers fail to do enough preventive maintenance. The tried-and-true maintenance strategy is the building block for RCM. As the saying goes, “walk before you run.”
Additionally, while many industrial organizations have a CMMS, less than 20 percent of them use the software to its fullest capabilities on average. Gaining familiarity with advanced reporting metrics and using data to pivot maintenance decisions will lead to a more successful implementation of RCM. The bottom line: RCM isn’t a magic beanstalk for maintenance woes. Master the basics before adding additional layers of complexity with RCM.
3. Optimize RCM Program Efforts
Obviously, it’s unrealistic to expect any kind of transformational change overnight. All meaningful progress takes time and effort—operations and maintenance initiatives are no exception. Thorough root cause analysis and consistent optimization are crucial elements of RCM program success. Without analyzing the root cause of all failures, those failures are sure to repeat.
Staying ahead of the maintenance curve consistently requires knowing which assets are likely to fail and when. One of the keys to proper optimization is finding the “sweet spot” on the return curve for investing in your assets.
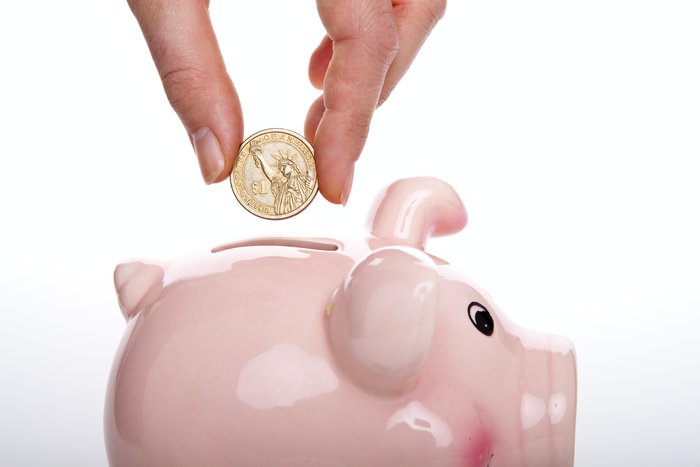
The dollars spent early in the optimization process will yield a higher return than those spent later on, but that doesn’t mean you should stop early in the curve. As long as all subsequent dollars invested in RCM initiatives continue to provide a positive return, these efforts will be worthwhile.
Eventually, you will enjoy an ROI for your consistent efforts with RCM. At this point, it’s important to assess the status of your program more vigorously. Are there other optimizations to find within the system, or is it time to simply sustain the plan that is now in place? Put simply, an RCM system should never be thought of as “done.” Rather, it’s an organic process of continually evaluating program objectives, fine-tuning maintenance strategies, and addressing bottlenecks.
4. Manage Asset Lifecycle Costs
Beyond increasing reliability via efficient maintenance scheduling, one of the primary objectives of RCM is meeting equipment Useful Life projections. Useful Life is an estimate of the average number of years an asset can be used before depreciating in value. In other words, equipment owners calculate the figure to answer the question: when does it no longer make financial sense to continue maintaining this piece of equipment?”
Maximizing facility investments means neither replacing aging equipment too soon nor too late. The older a tangible asset becomes, the more maintenance it will require to remain in working condition.Though straightforward in concept, determining the sweet spot of asset profitability is an individualized process. Actual equipment Useful Life may vary based on several factors, including installation practices, equipment usage behaviors, facility environment, and maintenance standards. The starting point to determine Useful Life is to compare the manufacturer’s specifications against IRS Publication 946, Appendix B:
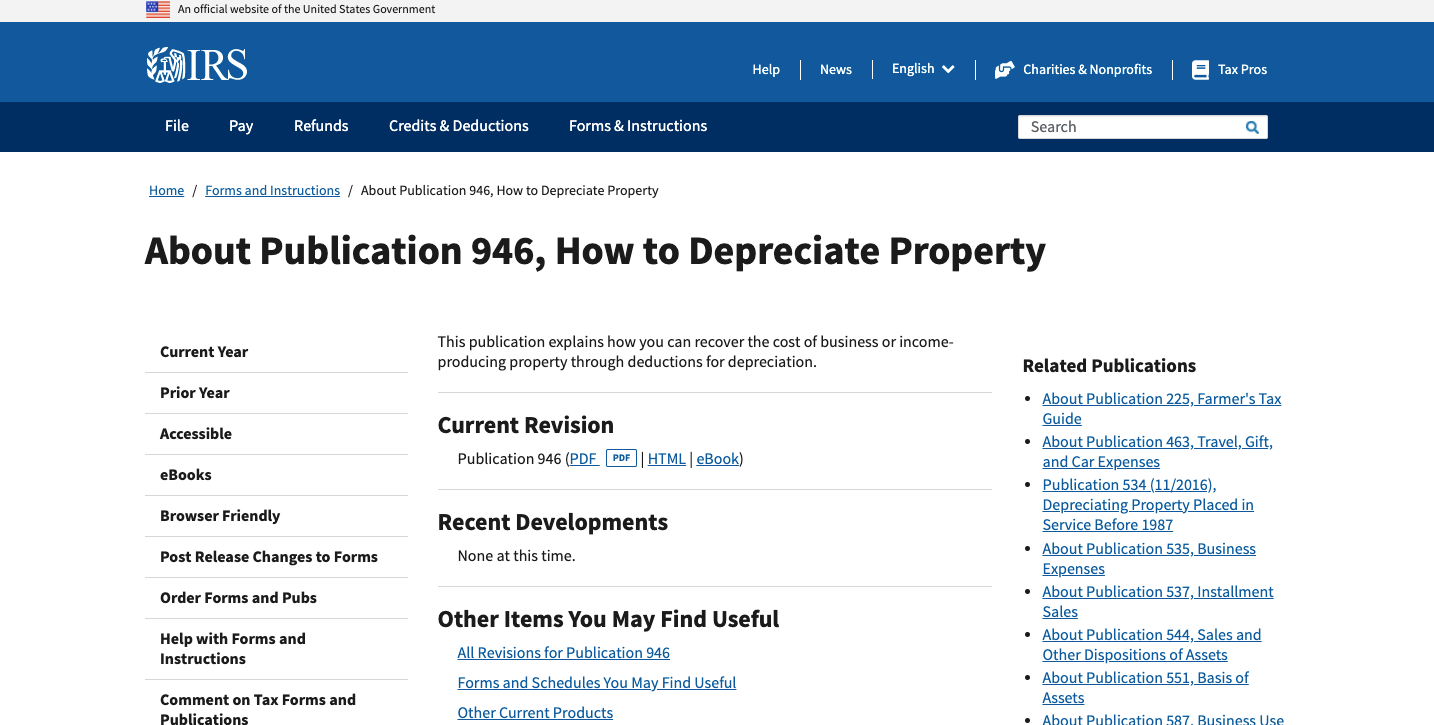
The document provides averages for the most commonly used pieces of equipment. Facilities engaging RCM programs should take calculations a step further by analyzing everything from early design standards to equipment precision alignment and balancing.
RCM consultant Doug Plucknette writes that maintaining useful life standards requires consistently following strict protocols:
“The Reactive Domain is the place where we once again ruin the Reliability and Useful Life of the new asset being installed. With the failure being ‘unexpected,’ we put new parts on order at a premium price and then pressure the people installing it to get the equipment running as soon as possible. At a time when we, again, should be paying close attention to the precision maintenance/installation standards we leave the tools in the drawer, slap it together and make it run.”
Put simply, stringently following SOPs for root cause analysis following critical equipment breakdowns ensures maximum longevity and manages costs. But knowing what you should be doing isn’t enough—put foolproof systems in place to ensure team members consistently follow Useful Life-extension protocols.
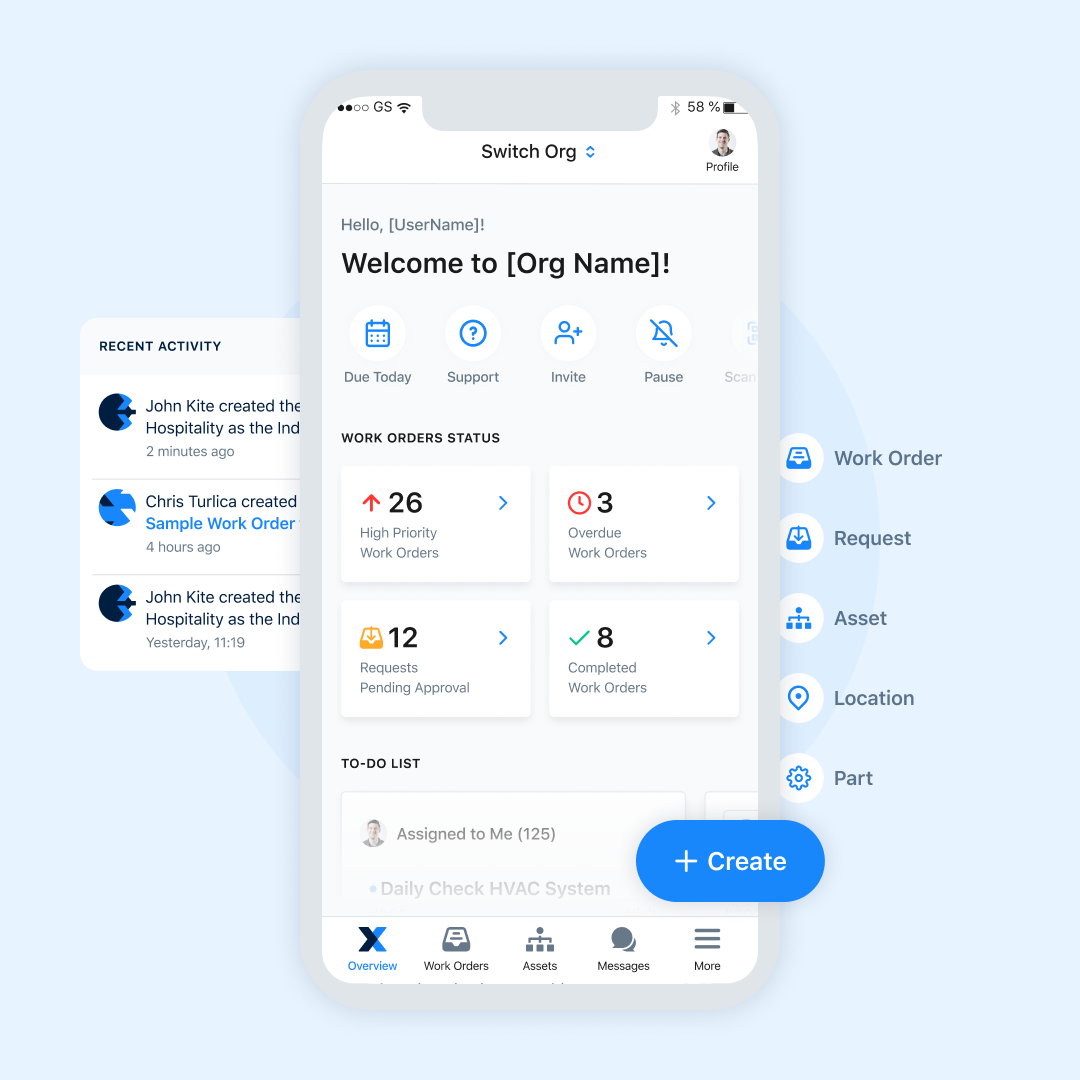
Reliability-Centered Maintenance Program Success
Reliability-centered maintenance programs offer extraordinary benefits to organizations that put in the time, effort, and resources to get it right. Beyond simple cost savings, other potential gains include enhanced safety and eliminating unnecessary work that can lead to machine downtime. With so much at stake, organizations wishing to implement RCM need to jump in with both feet—half-hearted attempts are destined to fail. Lean on the steps offered in this article as a starting point, and you’ll dramatically improve your odds of reaching a positive outcome.
FAQs
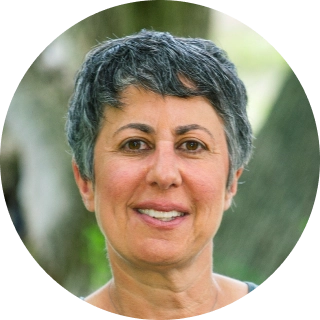
Caroline Eisner is a writer and editor with experience across the profit and nonprofit sectors, government, education, and financial organizations. She has held leadership positions in K16 institutions and has led large-scale digital projects, interactive websites, and a business writing consultancy.