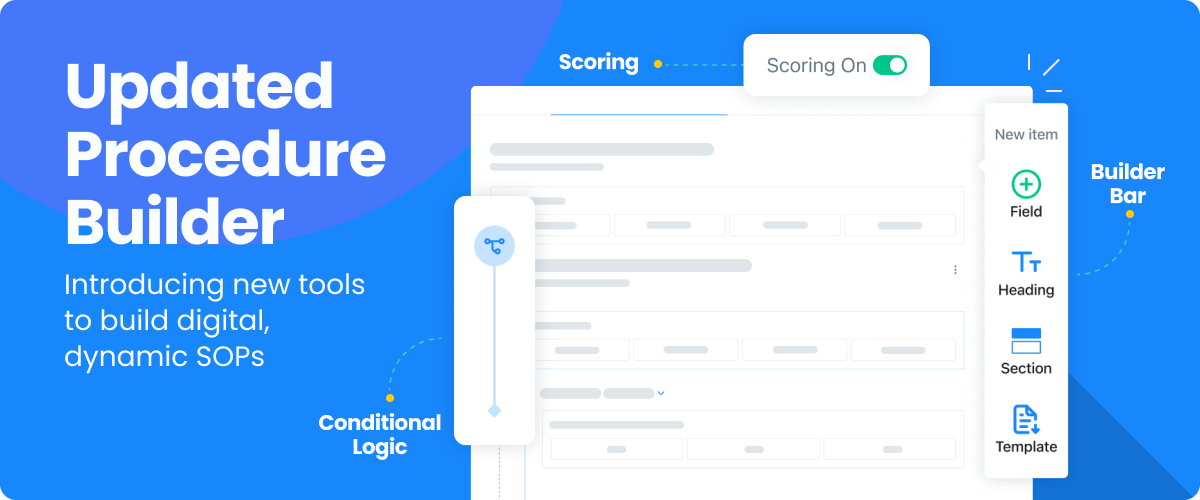
Meeting production goals, safety standards, and customer expectations amid today’s labor shortage is no easy task. Not only is it harder than ever to recruit and retain talent, but as more workers approach retirement age, companies risk losing the technical and institutional knowledge needed to keep their operations safe, productive, and efficient. Maintenance teams looking to combat resource shortages and organizational brain drain are implementing SOPs across more of their processes.
Unfortunately, when “data collection is manual, using pen and paper or basic spreadsheets, the process is prone to errors and inaccuracies” (McKinsey). Furthermore, when maintenance managers struggle to ensure their SOPs are used properly, it becomes all too easy to write off CMMS as yet another contributor to decreased tool time.
If you want your team to actually use your SOPs, you need to first digitize them and then make them flexible enough to suit any situation and easy enough for every technician to follow. For those of you already using our CMMS, we’re excited to introduce three new Procedure features to help you:
- Minimize technician errors by adding headers and sections to forms, marking required fields, and previewing SOPs before publishing.
- Simplify complex procedures and boost efficiency by applying if-then logic to your Procedures, with no separate software required.
- Drive continuous improvement by including Procedure Scores to identify SOPs that fall short of your quality, operational, and safety standards.
Streamline SOPs with Updated Procedure Builder
In the last few years, MaintainX customers have created over 80,000 unique SOPs to help workers navigate nearly every part of their days, from Lockout Tagout to preventive maintenance best practices to site compliance assessments. As we talked to our customers, we found that some organizations had over 100 fields in their paper-based SOPs. With such long forms, it can be hard for users to navigate procedures. And, worse, it may become tempting for teams to pencil-whip inspections, skipping critical tasks.
Our updated Procedure Builder will help guide your team through even the most complex SOPs. You can mark fields as required so workers never miss a step. If you have a long SOP, you can add headings and sections to better organize information for your team to keep them on track. And, finally, you can even nest a Procedure within a Procedure. Not only does this save you time having to copy steps from another Procedure, but it makes the Procedure much easier for your team to follow.
In addition, you can preview a Procedure before publishing it. Previewing ensures that the procedure flows optimally before you assign it. Once you attach a Procedure to a Work Order, the MaintainX mobile app guides users through each step, helping your team perform the right task at the right time, every time. By giving employees a streamlined, guided SOP experience, you can boost SOP completion rates and reduce the frequency of human error in your operations.
Simplify Complex SOPs with Conditional Logic Fields (Beta)
Whether teams are performing maintenance troubleshooting, completing a permit to work, or conducting safety inspections, their actions will vary depending on the condition of the facilities and equipment. With most legacy Work Order solutions, you can only create static checklists and attach flowchart diagrams to Work Orders (and hope your team can decipher them). Building digital forms with branching logic typically requires purchasing form builders or inspection software to guide teams through each scenario.
Today, we are excited to announce that MaintainX customers can now access Conditional Logic Fields in beta. These fields let you apply if-then logic to Procedures, so available fields change dynamically based on user input. Instead of having to interpret static diagrams or printed instructions, users will see only the checklists, instructions, and tasks relevant to them.
For example, let’s say you want technicians to request a hot work permit if they see that a piece of equipment needs welding or electrical work. If a hot work permit is necessary, then technicians would check for fire extinguisher availability, lack of flammable liquids, and more before performing any welding or electrical work. If a hot work permit is not necessary, then none of those steps need to be performed.
By incorporating conditional logic into your Procedures, you can save time for your team and ensure they follow the right process in the right situation, no matter what the situation.
Improve Safety, Quality, and Efficiency with Procedure Scores
Many organizations use pass/fail criteria on SOP inspections to flag issues needing immediate corrective action. In addition to fixing urgent issues, however, managers often need to know not just if the work was completed, but if it was performed well. In other words, were your organization’s standards for safety, quality, and cleanliness met?
With our new Procedure Scores, you can evaluate any process, such as a compliance audit, safety inspection, or site assessment, against your organizational and regulatory standards. You can adjust how the total Procedure Score is calculated based on your organization’s priorities and goals. Once you attach scored Procedures to Work Orders, you will begin seeing which inspections, locations, and tasks consistently receive low scores. This makes it much easier to pinpoint improvements to reduce risk and improve quality.
For example, let’s say your organization conducts monthly site audits to ensure your facilities are efficient, safe, and compliant with OSHA requirements. Without scored Procedures, a technician may complete all the steps in an SOP, but it doesn’t indicate if the procedure was done well. However, with scoring, if wet floors have been an issue for you in the past, now you can add weight to factors that ensure floors are dry and not a safety hazard.
In addition, by honing in on low-scoring Procedures, you can quickly pinpoint risk factors in your organization to get valuable insights to drive continuous improvements for safety, efficiency, and quality.
Turbocharge Your SOPs with MaintainX
At MaintainX, we believe that managing standard operating procedures shouldn’t be a burden. That’s why we’re proud to make our new Procedure features available to existing customers on every plan at no additional cost.
If you are an existing customer who wants to get beta access to Conditional Logic Fields, please contact your account representative. If you are not yet a MaintainX customer but want to see how you can turbocharge your SOPs, get in touch for a live walkthrough from one of our product experts!
FAQs
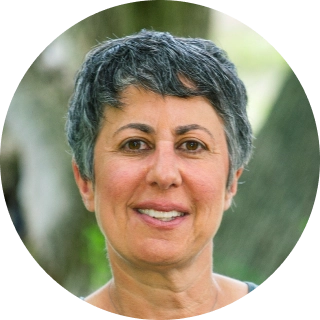
Caroline Eisner is a writer and editor with experience across the profit and nonprofit sectors, government, education, and financial organizations. She has held leadership positions in K16 institutions and has led large-scale digital projects, interactive websites, and a business writing consultancy.