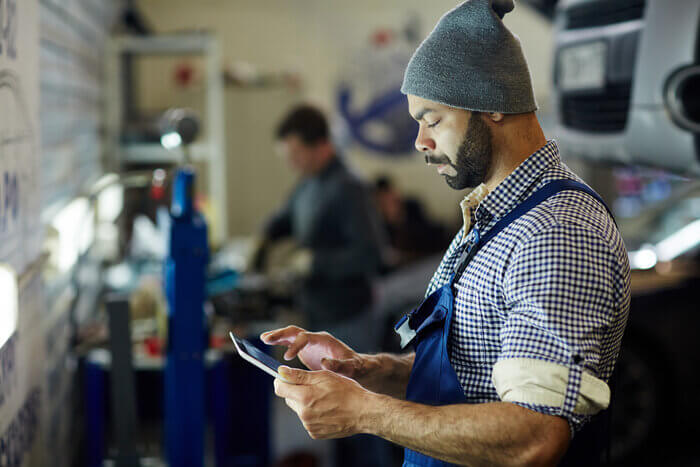
Imagine a maintenance team scrambling to complete tasks without clear instructions. It could mean delays, confusion, and costly mistakes. This is what can happen when dealing with ineffective work orders. However, an effective work order does the opposite. It gives you clarity, streamlines operations, and ensures that tasks are completed correctly the first time.
Effective work orders begin with proper creation, which depends on having a connected system that provides real-time data and easy access to information. Before digital solutions became common, many maintenance teams struggled with outdated processes like manually printing hundreds of paper work orders each week. A well-structured computerized maintenance management system (CMMS) simplifies the creation process, saves time, and reduces costs. Automatic work order triggers, preventive maintenance scheduling, and customizable templates ensure maintenance teams that every work order contains all the necessary details for effective and efficient execution.
Where work order creation fits into the work order process
Creating effective work orders is one of many steps in the work order process, and having a clear set of steps from start to finish is essential. This is where standard operating procedures (SOPs) come in. SOPs help streamline work order creation, letting you capture every detail accurately. Work order creation isn’t an isolated task. It connects every part of the maintenance workflow. From identifying a need to carrying out essential repairs, work orders bridge the gap between seeing the problem and resolving it. When looking at the process as a whole, the work order life cycle typically follows these steps:
- Generate a work request
- Create the work order
- Perform the repair or maintenance task
- Close the work order
- Review the process
Each step in this process is crucial but starts with an initial event or need that prompts action. These events, known as triggers, set the entire work order process in motion.
Common triggers for work order creation
Work orders don’t just appear out of thin air. Specific events or needs within your operation—called triggers—set them in motion. These triggers signal that something needs attention, whether it’s regular maintenance or an emergency maintenance repair. For example, the results of a routine equipment inspection might reveal wear and tear, triggering a work order for preventive maintenance. Similarly, when an HVAC system fails, a work order is generated to fix the issue immediately before air-quality problems escalate. Scheduled preventive maintenance is another common trigger, ensuring critical equipment stays in top condition.
Automated triggers simplify work order creation
Manually generating work orders whenever something needs attention is inefficient and can cause delays. Automated triggers generate work orders as soon as the system detects certain conditions. For example, a sensor might monitor the oil pressure in a machine and automatically generate a work order if the pressure falls outside the safe range. A CMMS like MaintainX can also help schedule recurring tasks, like monthly fire alarm inspections, to generate work orders without manual intervention. These automated triggers help ensure that your team stays current with maintenance tasks without relying on manual inputs.
IoT sensors for real-time monitoring
IoT (Internet of Things) sensors continuously monitor equipment conditions during operation. These sensors detect when a machine's performance crosses a specific threshold, such as overheating or increased vibrations. Once the system notices these changes, it notifies the work order management software to automatically generate a request to address the issue before it leads to equipment failure. This real-time monitoring lets technicians take preventive action early, reducing the risk of major breakdowns and costly repairs.
Meter readings for predictive maintenance
Meter readings help predict when equipment will need servicing based on usage data. This proactive servicing is called predictive maintenance, which helps significantly reduce unplanned downtime and extends the lifespan of critical assets. By monitoring factors such as operating hours or mileage, digital systems like MaintainX can generate preventive maintenance work orders before equipment breaks down.
Inspection-based triggers
Scheduled inspections play a vital role in generating work orders. After performing an inspection, the technician can immediately enter a maintenance request into the work order management software for any necessary repairs or adjustments. For example, during a routine HVAC inspection, if the technician notices a buildup of debris in the system's filters, they can trigger a work order to replace or clean the filters before it becomes a problem. By addressing small issues early on, you can prevent more expensive issues in the future.
How to create effective work orders
There's more to creating a solid work order than just writing down a task. A good work order shows all the important details that help get the job done right the first time. Clear instructions, assigning the right team members, and setting the correct priority help every qualified technician do the job properly and without delays.
What to include in a work order
A well-made work order contains all the important details for completing your task. The key pieces of a work order include:
- Task description: Clearly describe the task at hand, such as "sump pump switch replacement" or "lubricate conveyor belts." A detailed task description helps the assigned maintenance technician understand what they need to do and reduces confusion.
- Assigned personnel: Specify the team member or maintenance crew responsible for completing the task. The maintenance manager assigns tasks based on the availability of qualified workers so they can designate resources properly.
- Equipment or asset information: Include the asset's identification number, location, and other important details. This information helps the maintenance department track equipment history and maintenance schedules more closely, supporting smooth workflows.
- Priority level: Indicate how urgent the task is, from low-priority routine maintenance tasks to high-priority emergency repairs. Indicating the priority level helps maintenance departments manage tasks better and keep the equipment running smoothly.
- Expected completion date: Set due dates for finishing jobs so that work orders are closed on time. This helps prevent delays in the overall maintenance strategy.
- Step-by-step instructions: Provide specific steps for completing a job. For example, "Turn off the power, remove the filter, and replace it with a new one." This information keeps task execution consistent and improves efficiency for the maintenance team.
- Necessary tools or materials: List the tools, parts, and equipment needed to perform the task. These could be items such as air filters, safety gloves, or wrenches. This prevents delays by making sure maintenance teams have everything they need before starting the job.
- Safety procedures: Include any required safety precautions, such as wearing protective gloves or verifying proper ventilation. Safety procedures help avoid potentially harmful incidents while performing work, protecting both technicians and equipment.
This information helps the maintenance team complete tasks efficiently and accurately. It also reduces the chance of delays or miscommunication.
What to consider when creating a work order
When creating maintenance requests, it’s important to consider several factors so you know that your team will complete tasks properly. The work order should clearly outline details such as the task's urgency, necessary tools, and safety precautions. This helps technicians understand exactly what’s needed and prevents any confusion so that workers carry out each task efficiently and safely.
- Priority level: Identify the urgency of the task.
- Resources: Consider the tools, materials, and personnel needed.
- Timeframe: Set a realistic deadline for completion.
- Potential risks: Include safety precautions and potential challenges.
- Task dependencies: Confirm that related tasks are handled beforehand.
These elements will help you assign work effectively and reduce downtime.
How to create a work order system
When you try to manage a large volume of maintenance tasks without a clear work order system in place, critical tasks might slip through the cracks and the workload can pile up. A well-organized work order system helps prevent that by managing maintenance tasks efficiently. It lets you easily generate, track, and complete work orders consistently, keeping everything on schedule. To build an effective work order system, follow these steps:
Standardize procedures for service requests and work order creation
Clear, step-by-step processes eliminate confusion and avoid errors. This includes defining how to submit requests, outlining necessary approvals, and making all the information required for each work order uniform. With a consistent work order management process, maintenance managers and teams can respond more quickly, and management can easily track the progress of maintenance tasks each step of the way.
Make sure relevant data is easily accessible
Maintenance teams rely on accurate, up-to-date information about company assets and equipment to make informed decisions about what needs fixing, as well as when and how to approach the issue. By centralizing key information, technicians can avoid delays caused by missing or outdated details. This information might include standard operating procedures (SOPs), equipment manuals, or maintenance histories. MaintainX helps centralize all relevant data so technicians and managers have the necessary information.
Automate work order creation with IoT triggers and preventive maintenance schedules
IoT sensors, alongside preventive maintenance schedules, enable you to automatically generate work orders when certain conditions are met. For example, equipment reaching a preset usage limit or showing signs of wear can trigger a work order without manual intervention. This helps keep recurring tasks and critical repairs running on time, reducing unexpected breakdowns, keeping equipment running as it should, and creating a safer work environment for everyone.
Use real-time data to plan and prioritize work orders
By analyzing equipment performance, operational metrics, and upcoming maintenance schedules, teams can adjust priorities and refine their maintenance strategy based on current conditions. Real-time data also helps you monitor parts inventory to have the right components in stock for quick repairs, avoiding delays. With this approach, you can be confident that urgent repairs will be addressed quickly while still keeping routine maintenance tasks on track.
By using a data-driven strategy, you’ll streamline workflows for maintenance technicians, reduce downtime, and create a safer work environment by keeping equipment properly maintained, which prompts timely issue resolution.
Improve how you create and manage work orders with MaintainX
Creating and managing work orders is faster and more efficient with MaintainX. Our array of tools streamlines the entire work order process, empowering your team to respond quickly and effectively. Automated features reduce manual effort while helping to ensure work order accuracy. This helps teams stay organized and better able to focus on completing tasks.
- Automated triggers: IoT sensors and meters automatically generate work orders when specific conditions are met, ensuring timely maintenance and repairs.
- Preventive maintenance schedules: Set up recurring work orders to handle routine tasks before equipment fails.
- Customizable templates: Pre-built templates make it easy to standardize recurring work orders, saving time and reducing errors.
- Real-time data: Access up-to-date information to plan and prioritize work orders for efficient resource use and timely task completion.
- Mobile access: The MaintainX mobile app allows you to create and manage work orders from any location. This helps your team stay connected and productive.
MaintainX puts you in control. From automated triggers to real-time data-driven decision-making, we make it easier to stay ahead of maintenance tasks and keep your operation running smoothly.
How to Create Work Order FAQs
What are the different types of work orders?
Work orders fall into several categories, each serving a specific purpose. Some of the most common work order types include:
- Preventive maintenance work order: Regularly scheduled tasks that help keep equipment running smoothly and prevent unexpected breakdowns.
- Corrective maintenance work order: Issued when equipment malfunctions and requires immediate repairs.
- Inspection work orders: Generated to assess equipment condition and identify any potential issues.
- Emergency work orders: Created for urgent repairs that need to be addressed immediately to avoid significant downtime or safety risks.
What is an example of a work order?
A typical work order might be created for a preventive maintenance task such as replacing a part. For example, a work order might lay out the inspection and replacement of air filters in an HVAC system. This would include information such as the task description, assigned technician, materials needed, and an expected completion date. This level of detail helps the maintenance team complete tasks quickly while meeting safety and quality standards.
How does a CMMS help me create work orders?
A computerized maintenance management system (CMMS) makes work order creation easier by automating many parts of the process. With a CMMS like MaintainX, you can set up automated triggers based on equipment conditions. Customizable templates make repeatable tasks easier and more consistent, and assigning work orders to the appropriate personnel is effortless. CMMS also provides real-time data so that work orders are accurate and swiftly completed while keeping a full maintenance history of all relevant activities for future reference.
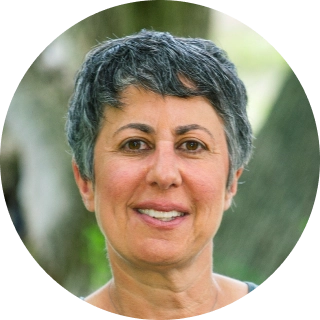
Caroline Eisner is a writer and editor with experience across the profit and nonprofit sectors, government, education, and financial organizations. She has held leadership positions in K16 institutions and has led large-scale digital projects, interactive websites, and a business writing consultancy.