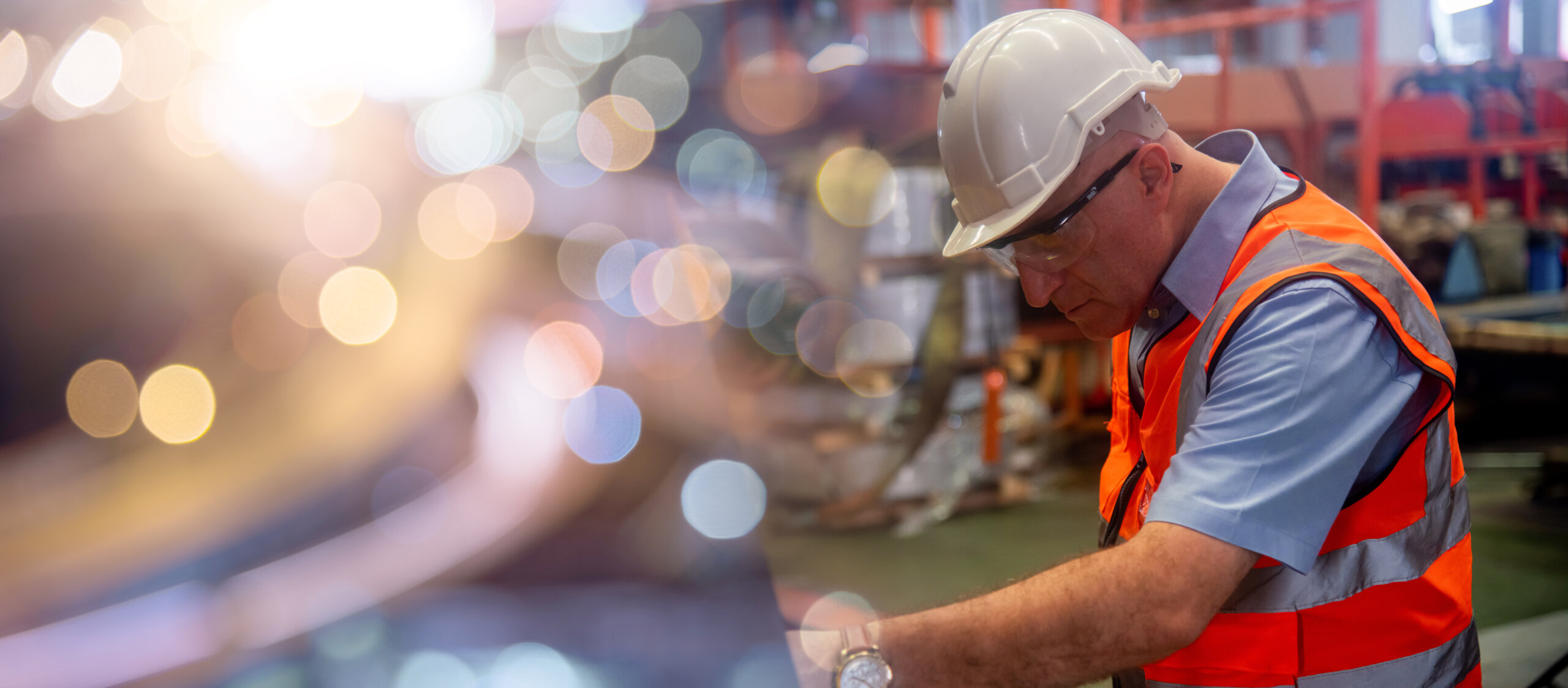
Kata is a Japanese word that refers to a structured way of doing things. The term originates from the Japanese martial arts concept of continuous improvement and gradual mastery.
The concept of Kata is used in various martial arts, from traditional Okinawan martial arts like Karate to more modern forms such as Judo. A Karate Kata, for example, is a specified series of moves. A person carries out the moves transitioning from one posture to the next while attempting to maintain perfect form.
It’s understandable if you’re wondering just how this definition of Kata applies to maintenance. After all, a dojo in Okinawa probably seems a world away from a manufacturing floor.
However, it wasn’t until Toyota adopted the methodology as part of its lean manufacturing system that the concept, “Toyota Kata,” became popular. Nowadays, Kata is a powerful maintenance concept, especially when applied to a lean strategy. Let’s explore how.
“Digital technologies and lean principles are intersecting in what is commonly termed “digital lean” –which can be a powerful combination of timeless lean principles and constantly evolving digital technologies to decrease waste and variability in processes.”
Deloitte
Types of Kata
There are two main types of Kata: Improvement Kata and Coaching Kata. Going off the names alone, you might assume Improvement Kata is the more important concept. But the two types work hand in hand.
Improvement Kata
Improvement Kata is a process to help challenge and grow your outlook. It is a 4-step process that helps teams identify their improvement goals and develop strategies to reach them. Questions in the process can include:
Where are you spending too much maintenance time?
Do you really need to revamp your preventive maintenance strategies?
Is your planned downtime optimal?
4-Steps of Improvement Kata
The Improvement Kata mindset helps you through 4 steps:
- Understand or set your target conditions or goals
- Understand your current conditions
- Establish the next target condition
- Conduct experiments and test ideas for the next challenge
Coaching Kata
Coaching Kata is a process by which workers learn how to adopt the Improvement Kata process. Beyond knowing the 4-step process, Coaching Kata helps people apply the tools. With five key questions, you can apply a more systematic approach to problem solving:
- What is the target condition or challenge?
- What is the actual condition now?
- Are any obstacles preventing you from reaching the target condition? What are they? Which one are you addressing right now?
- What is your next step?
- When can we go and see what we have learned from taking that step?
“Lean organizations seek to identify and eliminate activity. This systematic analysis of processes and value streams to reduce waste, variability, and inflexibility boosts performance in cost control, product quality, customer satisfaction, and employee engagement—often simultaneously.”
McKinsey
How Can Kata Help You Go Lean?
Going lean is a good idea for many reasons. In addition to the potential of reducing downtime and increasing your bottom line, running a lean maintenance strategy can help you become more efficient overall.
Here are ways the Kata methodology can help you implement lean manufacturing processes. Kata will help:
Reduce Risk
Adopting a lean maintenance strategy often involves significant changes to your current operations. The goal is to strip your maintenance operations of any processes that aren’t necessary. This is easier said than done, and figuring out what to cut back on can be challenging.
Using Kata as a tool can help ensure you make the right choices. A systematic approach, with gradual changes, means you’re not taking any big swings out of nowhere. This reduces the risk of sudden dysfunction in your process. Improvement Kata uses a model called PDCA (Plan-Do-Check-Act). As the name suggests, PDCA involves a cycle of making plans about what to change, making the changes, checking the effect, and either keeping the plans because they work or adjusting them to make sure they work.
The PDCA cycle helps you test out ideas while mitigating risk. Instead of, say, switching overnight from a weekly maintenance schedule to a monthly one, you can make incremental changes to first test out your new schedule, watching for any potential consequences and making adjustments as needed.
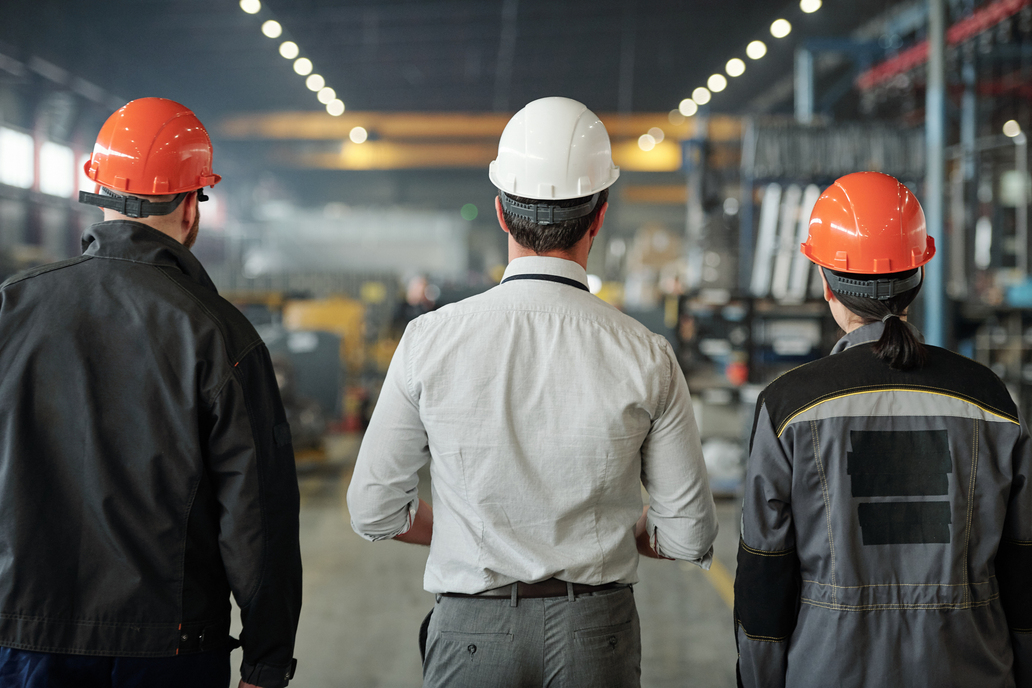
Increase Employee Confidence
Making the changes required from transitioning to a lean strategy can be challenging for workers. Nobody wants to be responsible for executing a change that puts an asset out of commission.
Let’s consider this example to go back to the word’s origins. Imagine a karateka, or karate practitioner, faced with two styles of karate training. One involves a gradual improvement process, taking the time to master a new Kata before moving on. Another involves “Kumite,” or sparring against an opponent. In real life, training will likely involve some mix of the two.
The same goes for maintenance. At some point, you have to roll up your sleeves and get your hands dirty. That said, workers, especially those new to the field, benefit from a gradual approach. Because this reduces the potential consequences of failure, employees should also be less afraid of making a mistake. This lean transition will impact your lean strategy positively as employees are more confident and willing to take the necessary actions.
Support Lean Workflows and Procedures
A Lean Six Sigma approach can help your company make more accurate predictions about your workflows and procedures (SOPs). The approach focuses on getting to the root causes of problems through a five-phase process. This process involves
- defining
- measuring
- analyzing
- improving
- controlling
Kata is all about creating habits through steady effort. Thus, it goes hand-in-hand with Six Sigma tools to create a lean manufacturing and maintenance culture.
Go Lean with MaintainX
If you’re thinking about applying Kata principles to your operations, be systematic in your approach. A well-designed CMMS will give you various tools to execute this. MaintainX, for example, provides templates to create lean standard operating procedures, communicate plans via in-app messaging, maintain accurate asset and parts inventories, and get you real-time metrics (KPIs) of your teams’ maintenance and manufacturing performance.
The best CMMS is designed to make it easy to centralize and disseminate maintenance and repair information and can easily be used as a lean management tool.
Using a CMMS like MaintainX helps streamline process improvement by providing a centralized platform to digitize, assign, and manage standard operating procedures.
FAQs
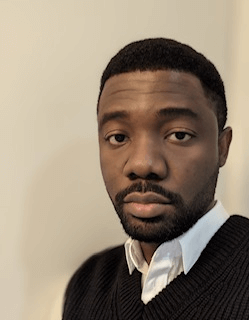
Lekan Olanrewaju is a content writer with years of experience in media and content creation. He has held positions at various media organizations, working with and leading teams at print magazines, digital publications, and television productions.