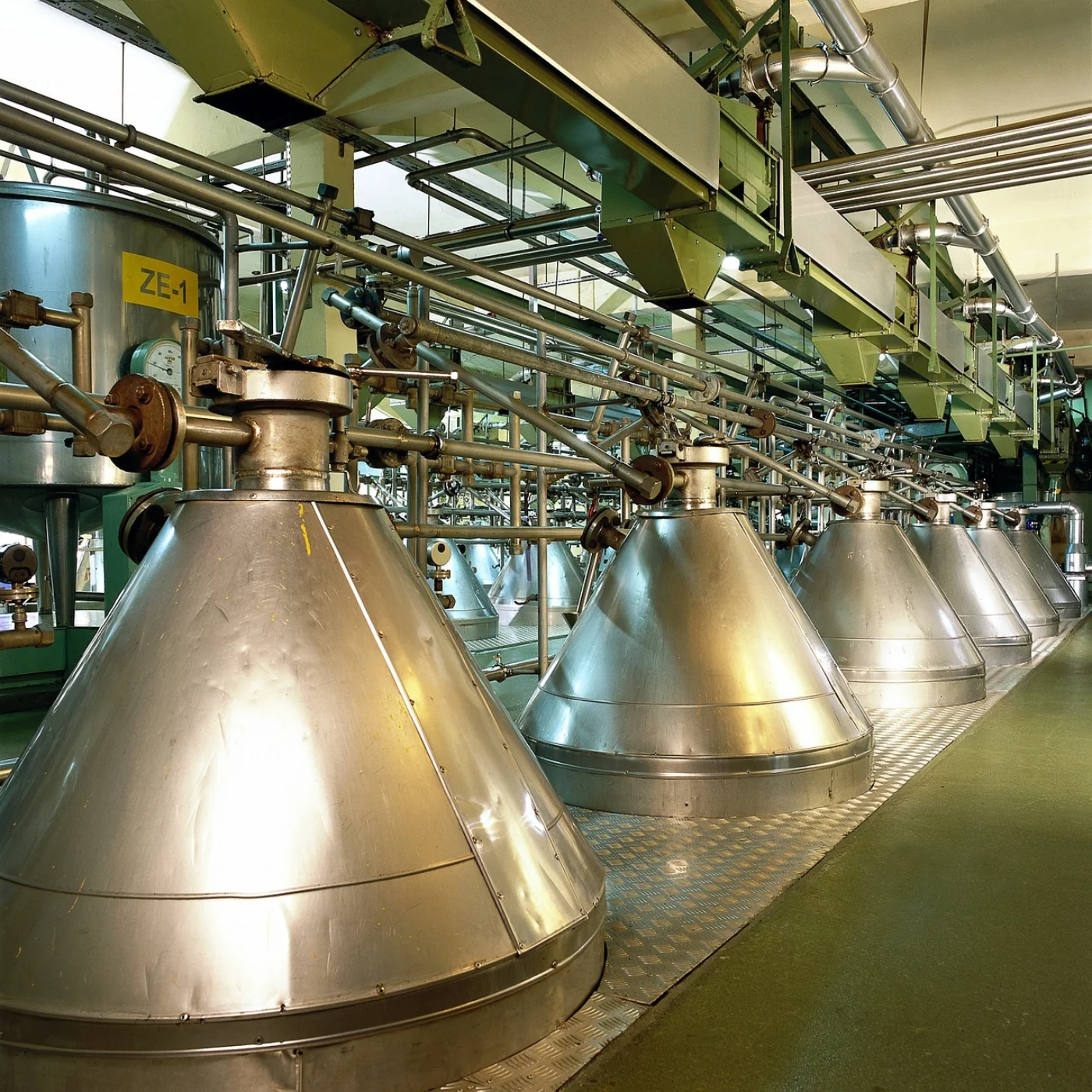
Standard operating procedures (SOPs) vary across industries, but one universal goal remains consistent: achieving optimal production efficiency. In today's manufacturing process, maximizing output while minimizing resource consumption separates industry leaders from those struggling to survive.
Facilities operating at peak efficiency deliver higher quality control, maintain stronger profit margins, and respond more effectively to market demands. This article outlines nine proven strategies to support production efficiency, identify inefficiencies, implement practical solutions, and measure tangible improvements in your production processes.
Key takeaways
- Production efficiency occurs when a facility creates maximum output with minimum resource input, directly impacting profitability and competitiveness.
- Track critical KPIs, including OEE, throughput, capacity utilization, downtime, yield rate, and scrap rate, to identify improvement opportunities.
- Challenge established workflows, workspace layouts, and technologies to overcome "this is how we've always done it" thinking.
- Implement preventive maintenance to significantly reduce costly downtime and equipment failures.
- Standardize processes, optimize supply chains, and invest in employee training to create sustainable efficiency improvements.
- Data analysis provides the foundation for continuous improvement cycles and accountability.
What is production efficiency, and why does it matter?
Production efficiency represents a manufacturing state where operations produce maximum output with minimum resource input. It occurs when a facility creates the highest possible volume of high quality products without wasting labor, materials, time, or capital.
At its core, production efficiency means getting the most value from every resource invested in your production process: equipment, personnel, raw materials, energy, and space.
Manufacturing organizations must pursue production efficiency as a competitive necessity rather than an optional goal. Businesses that use manufacturing software to master this discipline gain significant advantages:
- Reduced costs: Efficient production minimizes waste in materials, labor hours, and energy consumption. Lower production costs translate directly to higher profit margins or more competitive pricing.
- Improved consistency and quality: Standardized, efficient processes lead to consistent product quality, which reduces defect rates, rework, and customer complaints while building brand reputation.
- Reduced waste: Efficient production naturally minimizes waste generation through optimized material usage and process design. This creates environmental benefits while reducing disposal costs.
- Increased output: Efficiency improvements often unlock additional production capacity without requiring new equipment investments. Facilities can meet growing demand without proportional cost increases.
- Enhanced worker safety: Well-designed, efficient processes typically eliminate hazardous workarounds and reduce operator fatigue, creating safer working environments.
- Faster delivery times: Streamlined production reduces manufacturing lead times, allowing faster customer delivery and improved responsiveness to market changes.
Achieving production efficiency requires systematic analysis of your entire operation. The next section outlines the key metrics that help measure and track your progress toward optimal production efficiency in manufacturing itself.
How to measure production efficiency
Measuring production and improving manufacturing efficiency often requires tracking specific key performance indicators (KPIs) that quantify your manufacturing performance. These metrics provide objective data to identify improvement opportunities and verify the results of efficiency initiatives.
Overall equipment effectiveness (OEE)
OEE measures the percentage of planned production time that is truly productive. It combines availability, key performance indicators, and quality into a single metric that reveals hidden capacity in your operations.
Formula: Availability × Performance × Quality
World-class manufacturers achieve OEE scores of 85% or higher, while average facilities typically hover around 60%. An OEE below 60% indicates significant improvement opportunities.
Throughput
Throughput measures the average number of units your production line creates in a specific timeframe. This foundational metric of manufacturing productivity helps identify bottlenecks and calculate the cost impact of equipment downtime.
For example, if your standard output equals $500,000 worth of products per hour, a 30-minute repair delay costs $250,000 in lost production opportunity.
Benchmark your throughput against historical performance and industry standards to set realistic improvement targets.
Capacity utilization
Capacity utilization calculates the percentage of your maximum production capability currently in use. This metric helps determine if your facility is operating at optimal and productive efficiency levels.
Formula: (Actual Output ÷ Maximum Possible Output) × 100
The average capacity utilization in the US in 2023 was 79.31%. The Corporate Finance Institute suggests that a rate of 85% capacity utilization is optimal, as this provides optimal efficiency while maintaining flexibility for maintenance and unexpected demand fluctuations.
Downtime
Equipment Downtime measures periods when equipment isn't operating during scheduled production time. This includes both planned maintenance and unplanned breakdowns.
The costs associated with these downtimes vary enormously between industries. A 2024 Sieman’s survey showed that every hour of downtime in the Fast Moving Consumer Goods industry costs $36,000; every hour of downtime in the Automotive industry costs $2.3 million.
Yield rate
Yield rate represents the percentage of products that meet quality standards without requiring rework or scrapping. It directly impacts both manufacturing efficiency and profitability.
Formula: (Good Units ÷ Total Units Started) × 100
Yield rates can differ massively from industry to industry, within industries, and even within manufacturing facilities for different goods. For instance, TSMC reports 80-90% yields for 5nm semiconductor chips but only 32% for 100 mm2 chips.
Scrap rate
Scrap rate measures the percentage of materials wasted during production. This metric of production waste affects both material costs and production efficiency.
Formula: (Scrap Weight ÷ Total Material Weight) × 100
Tracking these metrics provides a comprehensive view of your manufacturing production efficiency throughout. The following steps outline specific strategies to improve each of these KPIs and optimize your overall manufacturing performance.
How to increase production efficiency
Improving production efficiency requires questioning established practices. Organizations develop operational habits that may have once worked but no longer serve current needs. Challenging the status quo enables you to streamline processes and identify inefficiencies that remain hidden behind "this is how we've always done it" thinking.
Step 1: Evaluate your workspace and workflows
Your physical workspace directly impacts your plant's production efficiency. Factory layouts should minimize movement of materials, tools, and personnel.
Apply these workspace optimization principles:
- Position workstations to create logical flow paths for materials.
- Keep tools and supplies within arm's reach of operators.
- Eliminate unnecessary movement between process steps.
- Ensure adequate space for equipment maintenance access.
Environmental factors significantly affect both equipment performance and worker productivity:
- Proper lighting reduces errors and worker fatigue.
- Appropriate temperature maintains equipment tolerances and worker comfort.
- Effective ventilation removes contaminants that can damage products or equipment.
- Noise control improves communication and reduces stress.
Step 2: Update technology
Strategic technology investments deliver substantial efficiency improvements:
- IoT/smart sensors monitor equipment performance in real time, detecting abnormalities before failures occur.
- Maintenance automation tools handle repetitive tasks with consistent precision. Start with simple automation for repetitive processes, then expand to more complex operations as ROI is proven.
- Data analytics platforms identify patterns and improvement opportunities invisible to human observation. These tools transform raw production data into actionable insights.
Computerized maintenance management system software centralizes maintenance management, work order tracking, and asset history. MaintainX's CMMS mobile platform provides technicians immediate access to equipment documentation and maintenance procedures in the field.
Step 3: Modernize your maintenance processes
Traditional reactive maintenance—fixing equipment only after failure—falls short in today's competitive environment, costing 3-9x more than preventive approaches while causing unpredictable disruptions.
Modern operations require a balanced maintenance strategy:
- Preventive maintenance based on manufacturer recommendations prevents failures before they occur, reducing downtime and extending asset life.
- Predictive maintenance uses condition monitoring to identify potential failures, enabling repairs during scheduled downtimes.
- Reactive maintenance remains appropriate for non-critical equipment where replacement costs less than prevention but should be minimized.
This balanced approach improves efficiency while maintaining flexibility to address unexpected issues through:
- Automating maintenance assignments and follow-up
- Creating digital procedures accessible via mobile devices
- Tracking KPIs to identify recurring issues
- Establishing clear emergency repair protocols
Organizations shifting from primarily reactive to preventive maintenance typically reduce costs while improving equipment reliability and production consistency.
Step 4: Identify production bottlenecks
Bottlenecks limit your entire operation's output regardless of other improvements. Identify bottlenecks by:
- Mapping your complete production process
- Measuring cycle times at each production stage
- Identifying where work accumulates or waits
- Analyzing equipment downtime patterns
Once identified, address bottlenecks through additional equipment, process redesign, or resource reallocation before focusing on other efficiency improvements.
Step 5: Find and eliminate wastefulness
Lean manufacturing principles identify and reduce eight types of waste represented by the acronym DOWNTIME: Defects, Overproduction, Waiting, Non-utilized talent, Transportation, Inventory, Motion, and Excess processing.
Implement waste reduction through:
- Value stream mapping to visualize waste
- 5S workplace organization (Sort, Set in order, Shine, Standardize, Sustain)
- Material recovery and recycling programs
- Production leveling to prevent overproduction
- Use of EAM to understand your asset lifecycle
Step 6: Optimize your supply chain
Supply chain inefficiencies directly impact production performance. Material shortages, delivery delays, and quality inconsistencies from suppliers can halt production lines and create costly downtime, while excess inventory ties up capital and warehouse space. Optimize through:
- Vendor management:
- Establish performance metrics for suppliers.
- Develop contingency plans for critical materials.
- Create transparent communication channels.
- Inventory optimization:
- Determine optimal inventory levels based on lead times and demand variability.
- Implement cycle counting procedures.
- Consider just-in-time or just-in-case strategies based on your risk profile.
Step 7: Organize and standardize your processes
Standardization creates consistency across shifts and operators:
- Document best practices for all critical procedures.
- Create visual work instructions accessible at workstations.
- Implement error-proofing mechanisms (poka-yoke).
- Establish regular process audits.
Standardized processes provide the foundation for all other improvement initiatives. They reduce variability in product quality, decrease training time for new employees, and enable meaningful performance comparisons between shifts or facilities.
When processes are standardized, problems become immediately visible, allowing faster identification and resolution of issues. Additionally, standardization creates a stable baseline from which continuous improvement activities can be measured and validated.
Step 8: Update employee training processes
Employee knowledge and skills directly impact production efficiency. Untrained or poorly trained workers make more mistakes, work more slowly, and struggle to identify and resolve issues, leading to increased downtime and quality problems. Effective training programs:
- Implement structured onboarding for consistent baseline knowledge.
- Develop cross-training programs to increase workforce flexibility.
- Provide ongoing training as processes and technologies evolve.
- Create skill matrices to identify training needs.
Cross-trained employees can adapt to production demands, covering absences and shifting to bottleneck areas as needed, which minimizes disruptions and maintains productivity even during staffing challenges.
Step 9: Track and analyze data for continuous improvement
Data-driven decision-making establishes accountability and identifies improvement opportunities:
- Implement real-time production monitoring systems.
- Create visual management boards showing current performance.
- Establish regular review meetings focused on KPIs.
- Set improvement targets with clear ownership.
Continuous improvement requires measuring results, adjusting approaches, improving efficiency, and repeating the cycle with new targets.
Improve Production Efficiency with MaintainX
Boosting organizational production efficiency is an ongoing process. Don’t underestimate the value of making small tweaks to production waste management, employee training, and bottlenecked production lines.
Sometimes, the smallest, strategic, operational changes yield the biggest returns. With that said, the quickest way to increase production efficiency is by enforcing standard operating procedures using mobile CMMS.
MaintainX allows manufacturing managers to create online libraries of SOPs, assign work orders, and manage assets from one centralized dashboard. The app also allows workers to conveniently access quality control checklists, safety audits, and PMs from their tablets and smartphones.
The result? A digitized audit trail that proves compliance, alongside a powerhouse of data that can improve production efficiency. Oh, and the app also boasts a team messaging feature that our customers love using!
FAQs on How to Improve Production Efficiency
What steps can you take to improve production efficiency?
- Evaluate workspace layouts and environmental conditions.
- Update technology with IoT sensors, CMMS, and automation tools.
- Implement preventive maintenance programs.
- Identify and eliminate production bottlenecks.
- Apply lean principles to reduce waste.
- Optimize supply chain and inventory management.
- Standardize processes across operations.
- Develop comprehensive employee training programs.
- Establish data tracking and continuous improvement systems.
How can you measure production efficiency?
- Overall equipment effectiveness (OEE)
- Throughput rates
- Capacity utilization percentage
- Equipment downtime
- Yield rates
- Scrap rates
- Maintenance response times
- Labor productivity
- Energy efficiency
What tools help increase production efficiency?
MaintainX CMMS offers essential features for maximum efficiency and improvement:
- Mobile work order management
- Preventive maintenance scheduling
- Asset management with performance tracking
- Digital procedure libraries
- Real-time team messaging
- Inventory management
- Inspection checklists and audits
- Analytics and reporting dashboards
- Automated notifications and escalations
These tools provide the foundation for data-driven decisions, standardized processes, and proactive maintenance—all critical elements of more efficient production processes and operations.
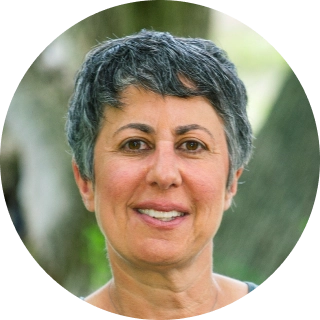
Caroline Eisner is a writer and editor with experience across the profit and nonprofit sectors, government, education, and financial organizations. She has held leadership positions in K16 institutions and has led large-scale digital projects, interactive websites, and a business writing consultancy.