Cycle time is an efficiency metric for manufacturers to help track the efficiency of production and maintenance tasks. A case study reveals that a business’s pretax profit improved by 2% to 13% due to an in-depth understanding of cycle time.
Other metrics like throughput and lead time also monitor efficiency but are technically different from cycle time. This post explains cycle time, how to calculate it, how it differs from other similar metrics, and what to keep in mind when reducing cycle time in production processes. It also explains how a CMMS can minimize cycle time.
What Is Cycle Time (CT)?
Cycle time is the average time required to produce one unit, beginning when you start the first manufacturing task until it’s ready to ship. CT includes both value-added and non-value-added time.
You can apply the concept of cycle time to almost every business task. For example, you can monitor the cycle time needed for a product to pass through a specific manufacturing operation instead of considering the time required to produce one unit. By applying this metric across your company, you can set efficiency initiatives that will lead to continuous improvement.
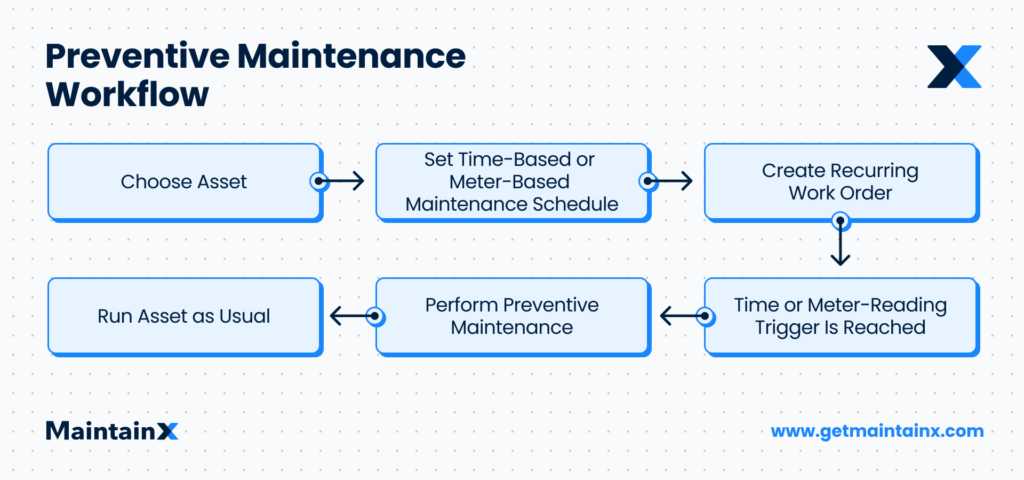
You can also use cycle time to optimize your maintenance schedule. For example, here are the four tasks necessary to calculate preventive maintenance (PM) cycle time:
- Create a PM schedule
- Record equipment meter readings
- Update scheduled PM work orders
- Update PM status to complete
The more efficiently you and your team perform these tasks, the lower the maintenance CT. The lower, the better, so long as quality and safety are never at risk.
Keep in mind all the ways project management can implement lean manufacturing methodologies, such as kanban and six sigma, to increase production rates, product delivery, and net production time.
“Manufacturing cycle time is the interval needed to convert raw materials into finished goods. A detailed analysis of this time period can result in a significant reduction in the amount of time needed to convert a customer order into a finished product, which can represent a significant competitive advantage.”
Accounting Tools
How to Calculate Cycle Time?
You can calculate cycle time by dividing the total time it takes to produce a certain number of units by the number of units produced:
Cycle Time (CT) = Time to Produce Units / Number of Units Produced
For example, if your machine assembles 120 units in 8 hours, the CT is 4 minutes (or 0.067 hours) per unit:
0.067 hours = 8 hours / 120 units
This calculation slightly differs when you produce products in batches. When the CT remains unchanged regardless of the batch size, calculate the per-batch cycle time for the entire batch instead of a single unit.
For example, say your oven can fit 20 cookies and takes 20 minutes to bake them. In this case, the CT for the batch is 20 minutes. The CT remains unchanged even if you bake just one cookie because you’ll need the same period of time (20 minutes) to bake 20 cookies.
Cycle Time vs. Throughput Time, Lead Time, or Takt Time
Manufacturers use various metrics like cycle time, throughput time, lead time, and takt time to measure their productivity. These terms have conceptual similarities, but they’re technically different.
Cycle Time vs. Throughput Time
The difference between these two metrics is subtle. Throughput time measures the time it takes for a product to be manufactured entirely. Therefore, when calculating throughput time, you must include the time necessary for loading and unloading raw materials, inspection time, and any inefficiencies or bottlenecks in your manufacturing process.
Calculate throughput time by dividing inventory (the number of units included in the entire production process) by the entire amount of time the inventory units spend in production.
Throughput Time = Inventory / Time in Production
On the other hand, CT measures the time it takes for a product to pass through one operation. Therefore, when you measure CT for the entire process, it will equal the throughput time. This means CT can be lower than or equal to throughput time but never higher.
Cycle Time vs. Lead Time
Lead time is the time between receiving a customer’s order and order fulfillment. Once you receive an order, you add the order to your production backlog. Then, the ordered units become part of your WIP inventory. After you complete production, you still need to package and ship it to your customer. This is when your lead time calculation stops.
Time spent on other actions to the point where you’ve fulfilled the order is also added to your lead time. This means your lead time can never be more than your cycle or throughput time.
Cycle Time vs. Takt Time
Takt (German for pulse) time is the time you spend producing one unit to meet your current customer demand. To calculate takt time:
Takt time = Total Production Hours / Customer Demand
[Note: Total production hours exclude break time and meal time]
Takt time is generally interpreted in the context of CT. You can meet customer demands within deadlines only if your takt time is more than your CT. Tracking takt time helps optimize production according to customer demand—you won’t end up under or overproducing inventory if you carefully monitor takt time.
What to Keep in Mind When Monitoring Cycle Time
Before you start monitoring CT and looking for ways to optimize your processing time, keep the following challenges in mind:
- Supply Chain Problems: Supply chain challenges will disturb your logistics workflow and negatively affect your CT. Before you make any efforts to optimize the cycle time, prepare your supply chain workflow for the change.
- Inefficient Communication: Team members on the shop floor may not have the tools to communicate effectively. The inability to collaborate on the spot makes optimizing the workflow and reducing cycle time difficult.
- Not Having the Right Tools: What happens when a machine goes down? How long does it take to get the emergency maintenance going? The information is passed among several people before it finally reaches a technician who can fix it. However, you can quickly eliminate unplanned downtime with a computerized maintenance management system (CMMS) that keeps all emergency procedures in the cloud and accessible onsite via a mobile device.
You can address these challenges with preparation and a CMMS available on mobile.
How CMMS Helps Reduce Cycle Time
The goal of tracking cycle time is to ensure efficiency, whether you’re tracking it for manufacturing or maintenance.
Keeping your vital assets up and running by implementing a comprehensive maintenance program is critical to achieving production efficiency. It’s simple—the lower the downtime, the lower the cycle time. If an asset requires repair, you want to ensure everyone has the information they need to fix the asset quickly.
That’s where a CMMS like MaintainX helps you implement a maintenance program, monitor maintenance tasks, and issue work orders all from one app. It’s the world’s first CMMS with built-in chat. As a result, technicians can get real-time help when working on maintenance tasks. If that sounds interesting, book a MaintainX tour today.
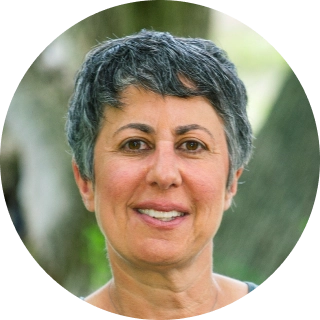
Caroline Eisner
Caroline Eisner is a writer and editor with experience across the profit and nonprofit sectors, government, education, and financial organizations. She has held leadership positions in K16 institutions and has led large-scale digital projects, interactive websites, and a business writing consultancy.
See MaintainX in action