The best time to repair the roof is when the sun is shining, but it's easier said than done in a world with limited resources and time. Deferred maintenance usually starts with minor problems like a squeaky machine or a leaky roof that gets deprioritized, intentionally or unintentionally, due to a lack of resources. And the longer you defer the tasks, the bigger the problem becomes. If left unchecked, deferred maintenance can lead to higher repair costs, increased downtime, disrupted operations, reduced profits and productivity, and greater safety risks.
In this definitive guide to deferred maintenance, we'll walk you through what it is, its impact on facilities, and how you can minimize instances of deferred maintenance and address your growing maintenance backlog.
What is deferred maintenance?
Deferred maintenance refers to maintenance activities (like repairs, upkeep, etc.) that are delayed or postponed because of a lack of available resources like time, workforce, or budget. Think of it as a “to-do” list of overdue maintenance tasks.
A small maintenance backlog is normal and healthy. But, deferred maintenance can quickly get out of hand as problems pile on top of one another. These delays can lead to higher operational costs, faster equipment breakdowns, and increased safety hazards.
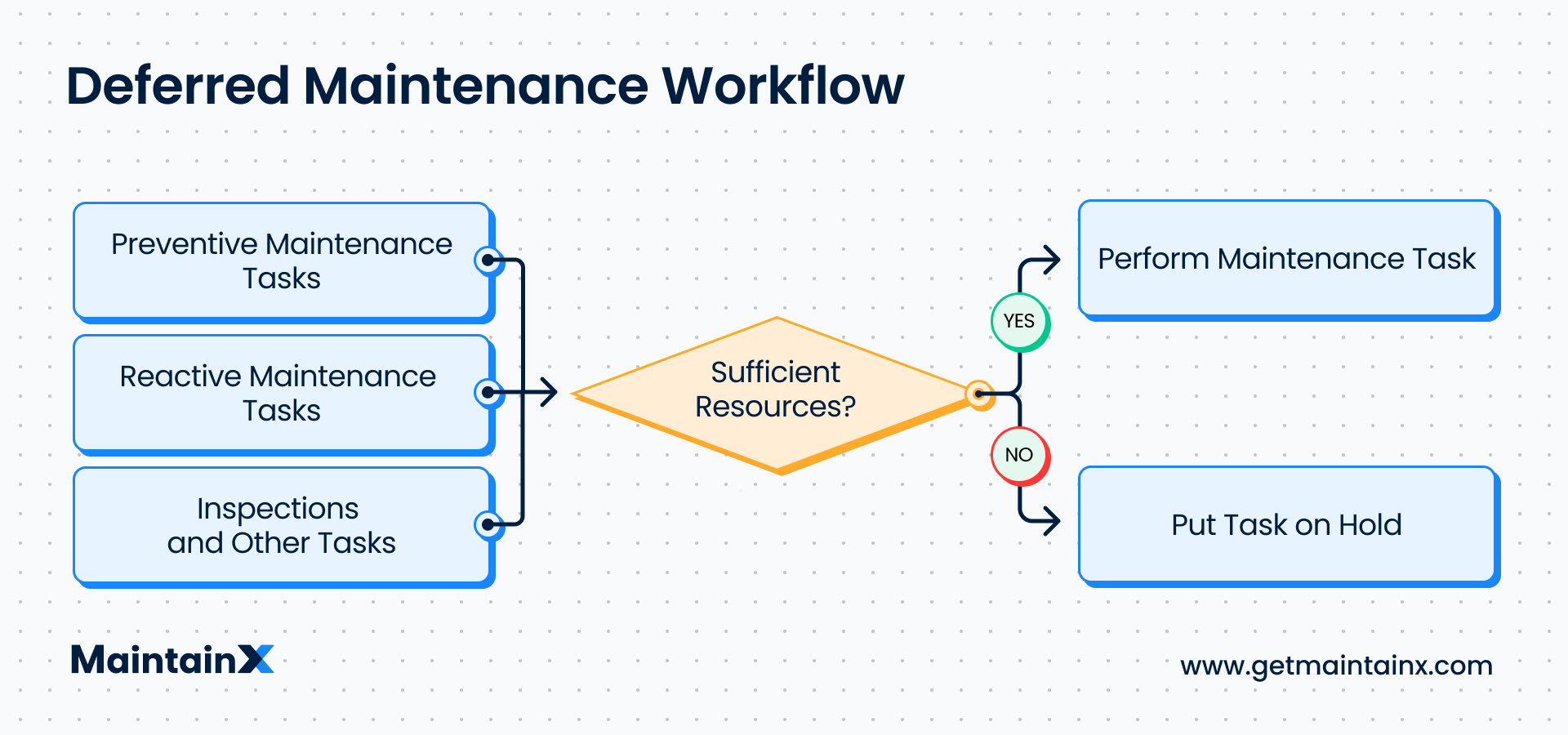
Types of deferred maintenance
Deferred maintenance can be either strategic or involuntary. Make no mistake—both types of deferred maintenance can impact an asset’s longevity, performance, and reliability. The difference is in the intent of the delay and the approach to addressing the backlog.
Strategic deferred maintenance
Strategic deferred maintenance is deliberate. You are making a calculated decision to prioritize more urgent maintenance tasks over lower-priority ones. You might decide to defer maintenance activities to optimize resources, align your maintenance schedule with resource availability, and minimize disruptions to operations. The idea is to defer less critical maintenance tasks while keeping essential systems and assets functional and safe.
Involuntary deferred maintenance
Involuntary deferred maintenance results from resource constraints: budget limitations, emergencies, and a failure to keep up with the maintenance schedule. Most of these factors are typically beyond your control. Even worse, involuntary deferred maintenance can have a snowball effect. Delayed repairs and maintenance tasks turn into bigger problems that cost more to fix and can cause significant disruption.
Common causes of deferred maintenance
There are a few reasons why maintenance teams might choose to defer maintenance tasks. Some of the most common reasons include:
- Budget: Budget constraints often prevent maintenance managers from completing all maintenance tasks. To make the most of available financial resources, you need to make difficult choices. You might need to prioritize tasks with high maintenance criticality and defer less urgent repairs and replacements to later.
- Inefficient decision-making: Suppose your company allows you to request more funding for maintenance when necessary. But how fast does an approval come through when you need it? If management takes weeks to approve funding, the pending tasks could end up in your deferred maintenance backlog.
- Insufficient staffing or lack of skills: Human resources are limited. Sometimes, you may need a larger team to check all the boxes on your maintenance task list. Or, the repairs may be too complex for your in-house maintenance team. Third-party contractors can help, but they’re not always available and may be expensive.
- Prioritization: You might need to schedule maintenance tasks based on budget cycles and long-term plans. Or, you may need to optimize resources to keep machines running and not risk your team’s health and safety. In some cases, you may have to look at the pros and cons of performing maintenance right away versus letting it end up in the backlog. Say you have a big order in production with a tight deadline. Can you afford to stop production to perform maintenance?
- Unforeseen emergencies: Unforeseen events can demand immediate attention and resources. You could end up deferring maintenance tasks if the emergency pushes you to move money from routine maintenance to address an emergency. For example, say a piece of medical equipment critical for patient care malfunctions. Your immediate priority would be patient care and safety. You wouldn’t perform maintenance on a fully functional HVAC system.
- Reliance on corrective maintenance: Corrective maintenance involves performing maintenance on an as-needed basis. Without a proactive maintenance plan, though, you don’t have the data or documentation to help identify the issue causing the breakdown. Of course, it’s also hard to budget for corrective maintenance. You can’t accurately estimate the cost of maintenance needs.
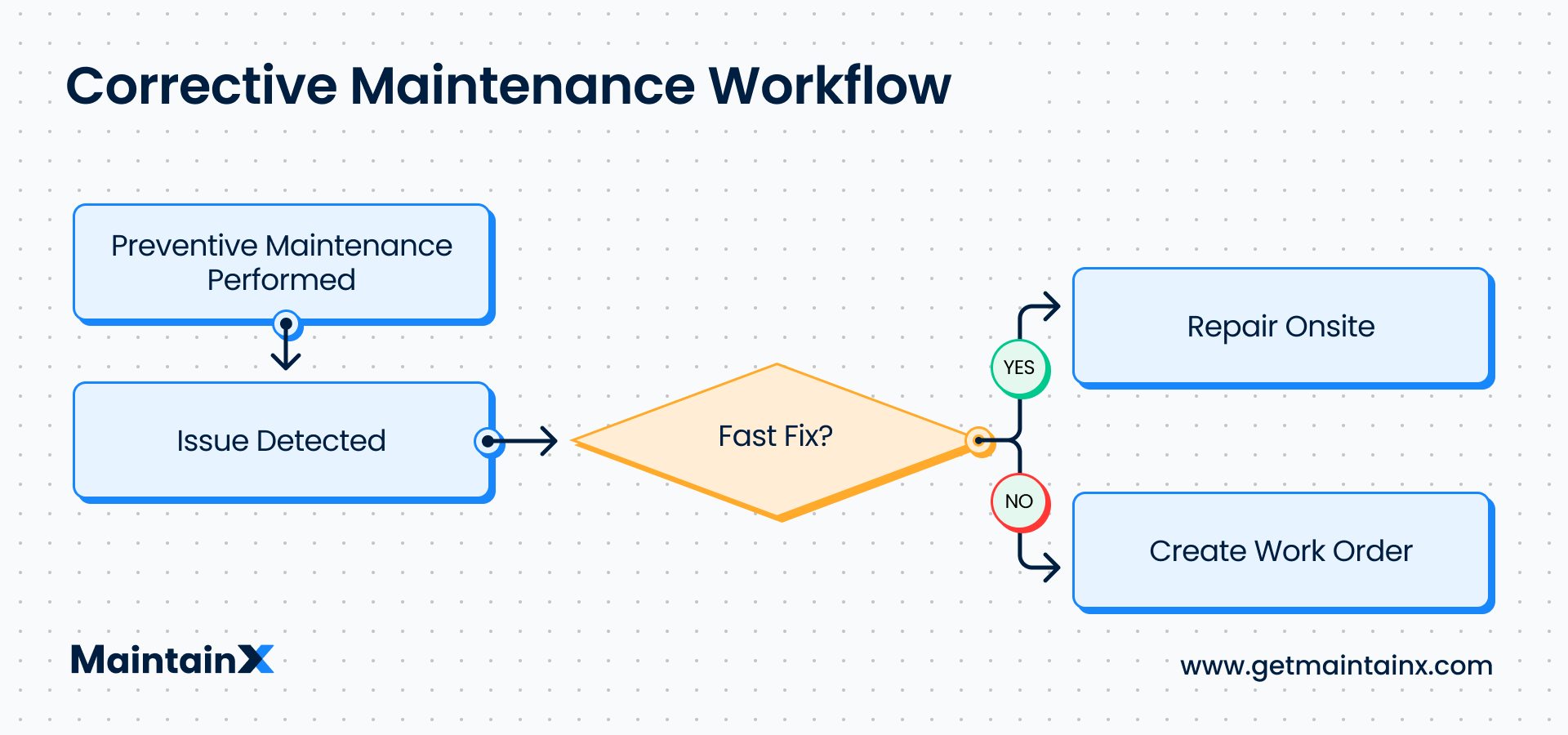
- Lack of maintenance equipment: Companies that don’t monitor parts and tool inventories can end up putting maintenance work orders on hold when they don’t have what they need. This can be an easy fix. If your deferred maintenance stems from frequent parts or tool stockouts, use an inventory management system to alert you when inventory levels dip below your specified threshold.
Signs of deferred maintenance
You can often see the signs of deferred maintenance in assets and across a facility as a whole. Common signs you might find in a facility with a considerable deferred maintenance backlog include:
- Unusual noises or odors: A noise from a machine or a foul odor, such as mildew or mold in old filters, can indicate the need for routine upkeep.
- Wear and tear: Visible signs of equipment deterioration indicate deferred maintenance. Peeled paint, cracked walls, and rusted surfaces can be signs of a growing maintenance backlog.
- Safety hazards: Facilities with a maintenance backlog may have faulty lighting, loose tiles, and blocked emergency exits. These risks can be threats to workers’ safety.
- Expensive repairs: Neglecting maintenance issues for long periods leads to increased repair costs. In some cases, neglecting repairs can translate to complete failure and require you to replace the entire asset.
- Non-compliance notices: Failed inspections or non-compliance fines for safety standards or other industry regulations can indicate a maintenance backlog.
Advantages of deferred maintenance
Short-term deferred maintenance offers two short-term benefits:
- Meeting immediate maintenance needs: Deferring maintenance allows you to focus on urgent maintenance tasks and to wait on low-criticality tasks.
- Saving costs: Deferring maintenance in the short term can save you money at the time. But, you risk paying more for repairs in the long term when you defer maintenance for too long, and problems get worse.
Short-term maintenance offers limited benefits. When possible, keep up with your maintenance schedule. Deferred maintenance almost always costs your company more in the long run.
Disadvantages and risks of deferred maintenance
Deferring maintenance for too long has many disadvantages, including:
- Expensive repairs: Deferring maintenance for too long can worsen minor issues.
- Increased energy consumption: Poorly maintained assets, like HVAC or insulation systems, use more energy and increase your energy bill.
- Reduce asset lifespan: Poor upkeep reduces the useful life of assets. This can result in needing to replace them prematurely, translating to higher long-term costs.
- Safety hazards: Not fixing a broken window or replacing a conveyor belt can pose safety risks for workers on the shop floor.
- Non-compliance: Failing to comply with maintenance requirements and industry regulations can lead to non-compliance fines, penalties, and loss of reputation.
How to decrease deferred maintenance
Deferred maintenance is crucial for a facility manager. But there are ways to manage deferred maintenance so a backlog doesn’t grow too long. Here’s what you can do to decrease deferred maintenance:
Step 1: Audit your maintenance needs
Run a maintenance audit. The audit will identify current problems in your maintenance approach. You can break the audit down by reasons and the return on investment (ROI) of solving each problem.
To decrease deferred maintenance, you need to know what’s causing it. This is where an audit helps.
Do you need more funding for maintenance? Do you need more skilled maintenance personnel? Or do you just need a better regular maintenance plan?
Step 2: Prioritize high-ROI maintenance tasks
Order the tasks in your deferred maintenance task list based on ROI. Compare the cost of not completing the maintenance tasks on your to-do list with the cost of performing maintenance.
For example, the cost of equipment failure due to lack of lubrication is much greater than that of lubricating your equipment. The higher the difference between the cost of performing and not performing a maintenance task, the higher the ROI. Calculate the difference for all tasks in the backlog and prioritize completing tasks with the highest ROI first.
Step 3: Transition to proactive maintenance
Transition to proactive maintenance to prevent the maintenance backlog from growing. Plan your resources, like funding, spare parts, and staffing, to keep up with your preventive maintenance program.

The better the plan, the lower your risk of emergencies. Consider automating your maintenance schedule using a CMMS (computerized maintenance management system) to streamline your maintenance workflow.
Step 4: Adapt and optimize
No preventive maintenance program is perfect. Keep looking to improve your workflow and adjust your program as you go.
If you use a CMMS, monitor work order histories to see if you can optimize resource use maintenance checklists. CMMS gives you an overview of essential data—maintenance history, performance metrics, and even predictive analytics. This visibility can help you make data-driven decisions to optimize your preventive maintenance strategy.
Suppose you’ve installed a thermometer on one of your machines. Technicians collect the data in SOPs stored in your CMMS. The CMMS triggers work orders when the data is out of bounds. These triggers allow you to adjust maintenance frequency and manage resources more effectively.
Examples of deferred maintenance
Deferred maintenance isn’t specific to assets. Delaying maintenance on roof repairs, parking lots, and other parts of a building’s infrastructure also adds to your deferred maintenance task list. Let’s talk about some common examples of deferred maintenance in various industries.
Deferred maintenance in manufacturing plants
Deferred maintenance in manufacturing plants can lead to subpar production quality and increased equipment downtime. Malfunctioning equipment can lead to incorrect alignment and loose components, resulting in quality issues.
Rework and waste are expensive. The loss of reputation can be even more costly.
Suppose you manufacture bearings and have a deferred maintenance problem. Here are the consequences you might face:
- Deviation from tolerances: Deferred maintenance can result in deviations from specified tolerances and dimensions in bearings. Such deviations can lead to inaccurate sizes and shapes of bearings.
- Poor surface finish: Worn-out tooling and inadequate lubrication result in poor surface finish. This can adversely impact the bearings’ functionality and durability.
- Contamination of material: Ignoring required maintenance on filtration systems can lead to material contamination, compromising the integrity of the manufactured units.
Deferred maintenance in real estate
Maintenance backlogs in real estate and property management are apparent in faulty electrical systems, dysfunctional HVAC units, and plumbing issues. These problems can ruin a tenant’s experience and lead to safety hazards.
But that’s not all. Inadequate maintenance is bad for your brand image and bottom line. You’ll also spend more on increased energy use and operational inefficiency, not to mention fines and closures.
For years, the media has reported on the New York City Housing Authority (NYCHA). NYCHA is a “bad landlord” because of its maintenance backlog. Deferred maintenance on NYCHA properties has led to health hazards, like poor heating in the winter and mold exposure.
Deferred maintenance in education
For years, public-sector schools in the U.S. have been asking for more funding to clear their maintenance backlogs. Postponing maintenance and repairs year after year has led to increased safety hazards like water leaks and structural issues.
Consider the Memphis schools, for example. The local funding body had made multiple requests to the district. The district only released partial payments, not enough to maintain schools in their current conditions.
Clear out your maintenance backlog with MaintainX
Things can quickly spiral out of control when maintenance backlogs grow, costing money, time, and resources. With MaintainX, you can automate and streamline your maintenance workflows to reduce the number of delayed maintenance activities. Digitized work orders make planning, tracking, and executing maintenance work easy. And to top it off, MaintainX captures historical maintenance data to help you decide which activities to delay and prioritize.
Are you ready to put a cap on your maintenance backlog? Get started with MaintainX today and experience first-hand how you can reduce deferred maintenance and stay ahead of unplanned downtime!
Deferred maintenance FAQ
A delay in repairing HVAC or air-conditioning is an example of a deferred maintenance item. Similarly, not fixing a leaking roof, peeled paint, and broken windows are also examples of deferred maintenance tasks.
Deferred maintenance poses several risks, including:
- Increased operating costs
- System failures
- Expensive repairs
- Reduced equipment efficiency
- Health and safety risks
- Shorter useful lifecycles of assets
Causes of deferred maintenance can include:
- Staffing shortages
- Emergencies
- Budget constraints
- Not implementing preventive maintenance
- Lack of asset management and spare parts inventory
Deferring maintenance makes sense in some cases. For example, when you’re working on an important order, you can’t pause production to perform routine maintenance. Another case where deferring maintenance makes sense is when you have a limited maintenance budget. You should prioritize high-ROI maintenance tasks and defer the remaining tasks to the next budget cycle.
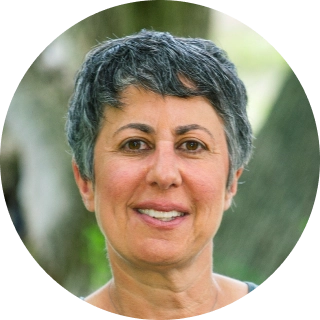
Caroline Eisner
Caroline Eisner is a writer and editor with experience across the profit and nonprofit sectors, government, education, and financial organizations. She has held leadership positions in K16 institutions and has led large-scale digital projects, interactive websites, and a business writing consultancy.
See MaintainX in action