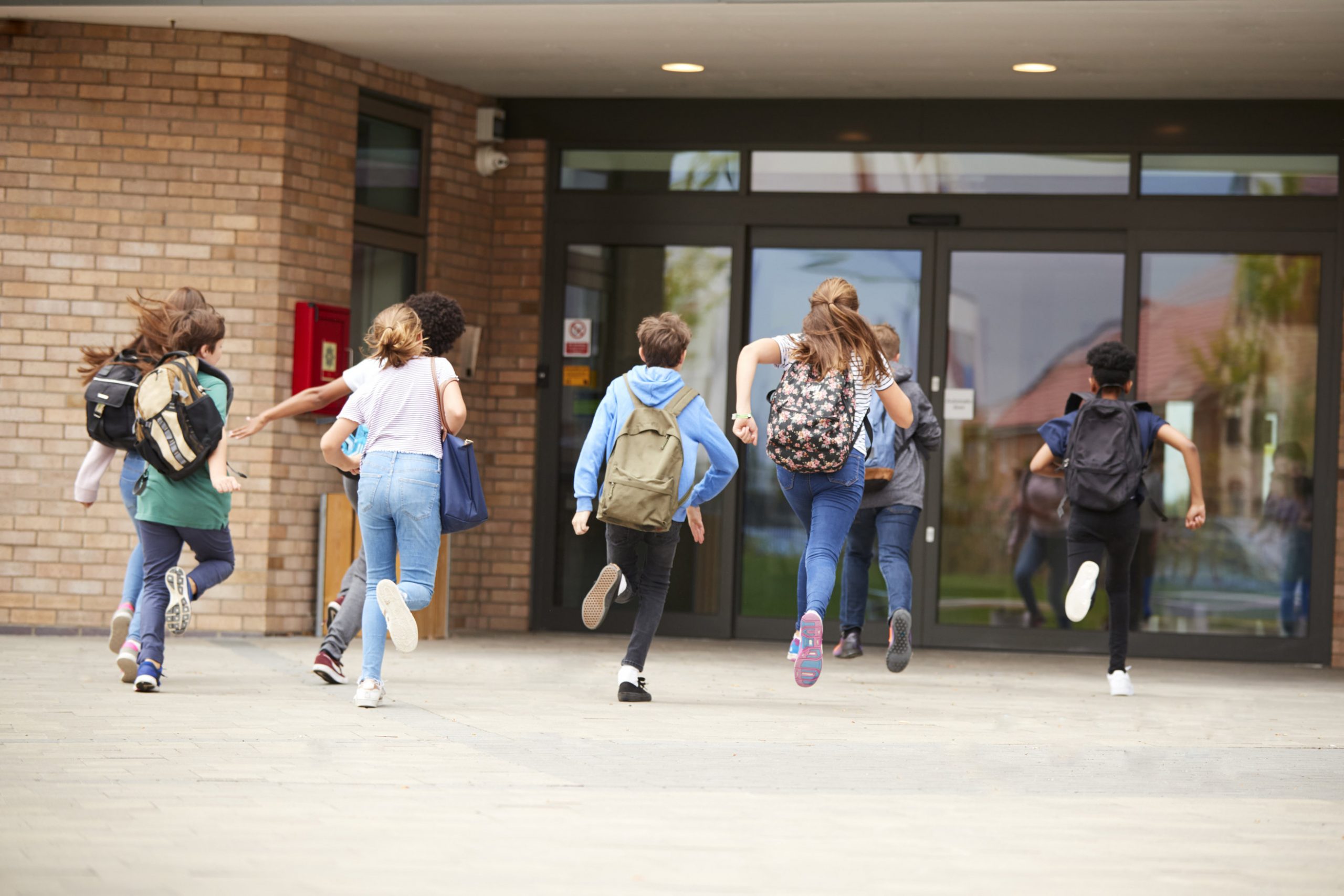
We’ve all heard it by now: work smarter, not harder.
For many campuses, public schools, and school districts, not only is it about working smarter, but it’s also about doing more with less. Education Standard Operating Procedures are about both: being smarter with less. We hear a lot about education funding and reducing costs. Deferred maintenance is often on the long-term list of the planning process.
Campus preventive maintenance activities and tasks mean much more than just fixing broken equipment for the community members. Campus tasks can include reactive maintenance to outdated water fountains to chemical hygiene practices in science labs.
Education Standard Operating Procedures
A well-designed education facility management system built with Standard Operating Procedures for schools includes facility maintenance, reactive maintenance, routine maintenance, preventive maintenance, and predictive maintenance.
A sound facility maintenance plan serves as evidence that school facilities are, and will be, cared for according to quality assurance plans and regulations.
School facility maintenance plans need to focus on campus day-to-day operations and on long-range school management priorities.
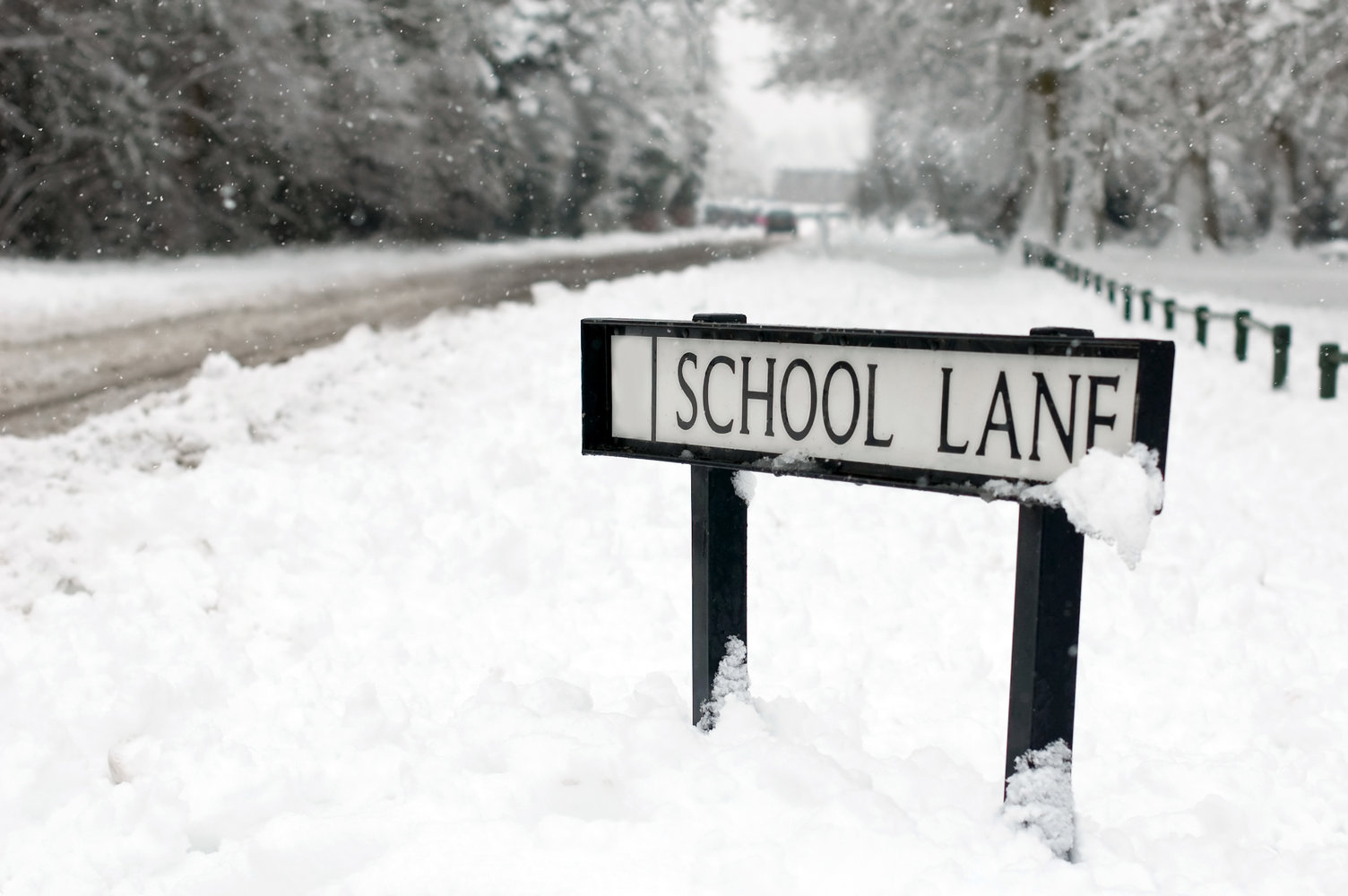
Because there are always routine and unexpected maintenance and repair demands, education organizations should proactively develop and implement plans.
Once online, completed SOPs can be used to create forms and checklists for locations, assets, inspections, and routine safety checks. All the information needed for safety inspections and accreditations is available online.
Time-stamped facility maintenance Standard Operating Procedures create easy audit trails.
Facility management relies on accurate data to make accurate decisions. “Performance” of a mechanical system is about the system operating as designed and providing the maximum benefit for the campus.
Preventive maintenance SOPs and CMMS can manage and evaluate all maintenance on campus and graduate schools.
School facility maintenance is vital to managing an education organization. Standard operating procedures for managing campuses involve maintaining buildings, grounds, and equipment.
SOPs for Buildings, Grounds, and Equipment
Building maintenance includes not only school buildings, but athletic facilities, tool sheds, garages, and other remote sites.
Grounds maintenance includes unpaved surfaces, like the athletic fields, and paved surfaces, like the parking lots. It also includes walkways, sidewalks, and driveways. Grounds also include landscape, water flow, energy use, and even personal safety. In the winter, campus SOPs cover snow plowing for safety and access.
Equipment maintenance includes all vehicle fleets, from lawnmowers to school buses to golf carts.
The National Center for Education Statistics (NCES) publishes the Planning Guide for Maintaining School Facilities. This guide helps school facility managers ensure smooth operations, avoid costly reactive maintenance fixes, and evaluate maintenance efforts with state-of-the-art solutions.
School facility Standard Operating Procedures should include:
- Fleet management
- Building and grounds
- HVAC systems
- Indoor air quality
- Water systems, including safe drinking water
- Foodservice
- Safety and emergency preparedness
- Fire safety
- Recycling
- Sanitation
- Hazardous materials, including asbestos and lead paint
Most of these systems must adhere to federal, state, and local government regulations. These regulations include guidelines set forth by OSHA, fire safety, the United States Department of Education, EPA, AHERA, to name a few.
School facility maintenance teams must follow the rigorous education Standard Operating Procedures set by districts, county, and state authorities about how public monies are granted and spent. This includes quality assurance plans for what gets priority, cost-benefit analysis, and completion procedures, including how and where to purchase materials.
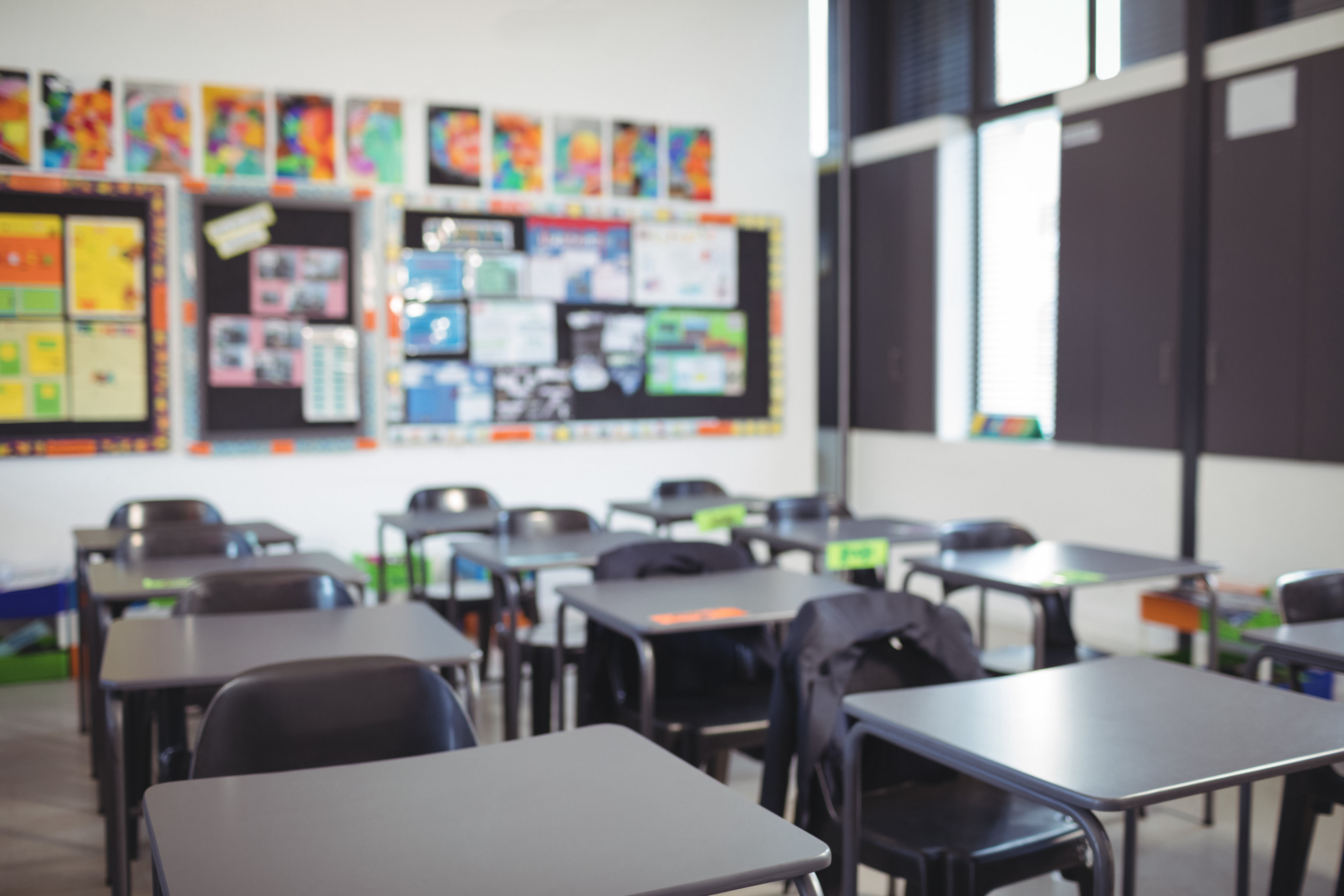
Campus Standard Operating Procedures should:
- Outline processes that are easily followed, accessible, and not “one size fits all” solutions
- Promote best practices and quality assurance guidelines
- Facilitate audits of daily, monthly, and preventive maintenance schedules
- Provide safe environments for teaching and learning
- Manage facility staff and contractors
- Evaluate facility maintenance efforts, implementation, compliance, and completion
Standard Operating Procedures and Audits
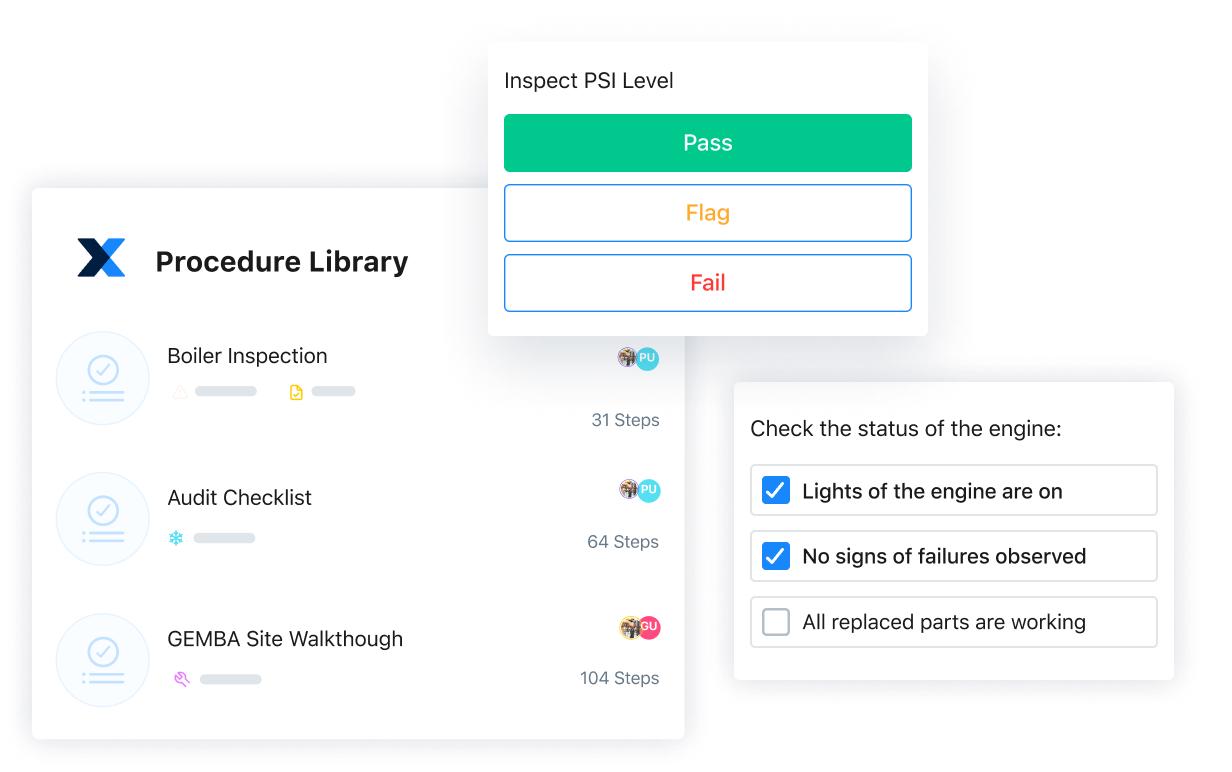
A facility audit is an asset-by-asset inventory of campus buildings, grounds, and equipment. Some information is needed on a day-to-day basis (e.g., fuel requirements and load capacities on a fleet of buses).
Data should be collected and available on all buildings, grounds, and equipment at all sites. Standard Operating Procedures data should include both permanent features (structures) and temporary features (e.g., traffic patterns and snow buildup areas).
Standard Operating Procedures should include information about all of the campus assets, including repair history, specifications for replacement parts, and inspection checks.
CMMS SOP audits can project future maintenance costs of campus facilities.
Asset audits should track SOPs preventive maintenance on building components, furniture, and equipment by age and life cycle. Likewise, reactive maintenance, including vandalism of property, can also be tracked via Standard Operating Procedures and audits.
Facility data also needs to be easily available in case of emergency (e.g., building blueprints may be important when fighting a fire).
Quality management plans that include preventive maintenance SOPs help schools keep track of work requests, create work orders, confirm work completion, and track the cost of parts and labor. CMMS can help manage these work requests and help meet the basic information needs of the district.
When planning preventive maintenance tasks, administrators should consider how to efficiently schedule the work—i.e., during academic breaks or other planned work. Quality plans include preventive maintenance systems that result in fewer reactive emergency events and reduce disruptions to the school schedule.
Manage School Maintenance
MaintainX can help education facility maintenance teams:
Coordinate work. Reduce non-productive time by empowering your facility maintenance and operations teams with job and process information on the go.
Communicate across locations. Through digital SOPs and on-the-spot dashboards, school facility managers can communicate, collaborate, and keep school administrators in the loop to ensure input and corrective actions are available when it matters the most.
Meet regulatory compliance and reporting standards. Digital audit trails streamline complex regulatory procedures while providing unprecedented centralized transparency across campus.
Manage Preventive Maintenance / Asset Management. Improve overall equipment effectiveness (OEE), cut equipment purchases, and reduce downtime with Preventive Maintenance Standard Operating Procedures. With online SOPs and dashboards, teams can access previous work performed to optimize workflows.
Reduce Reactive Maintenance. Via CMMS, problems on campus can be identified efficiently, and solutions can be shared instantly with corrective procedures and actions. With the right information at their fingertips, maintenance workers can make more timely and accurate decisions.
Provide Safety and Training SOPs. CMMS dashboards provide education facility managers with the data and visuals to help improve safety, regulatory, and quality standards across campuses. Managers can collect and analyze data, standardize inspections, send reports, and identify areas in need of improvement. A digital audit trail provides management and leadership with the tools necessary to ensure campus-wide compliance.
Reduce Waste and Repetition. From any computer or hand-held device, SOPs can identify inefficiencies and deploy updates within seconds. MaintainX enables campuses of all sizes to be on the same page at all times to continuously improve operational efficiency.
FAQs
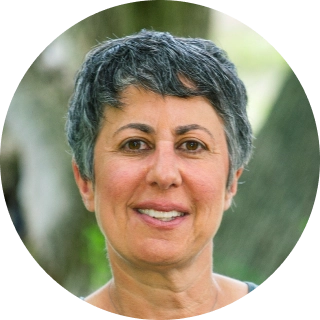
Caroline Eisner is a writer and editor with experience across the profit and nonprofit sectors, government, education, and financial organizations. She has held leadership positions in K16 institutions and has led large-scale digital projects, interactive websites, and a business writing consultancy.