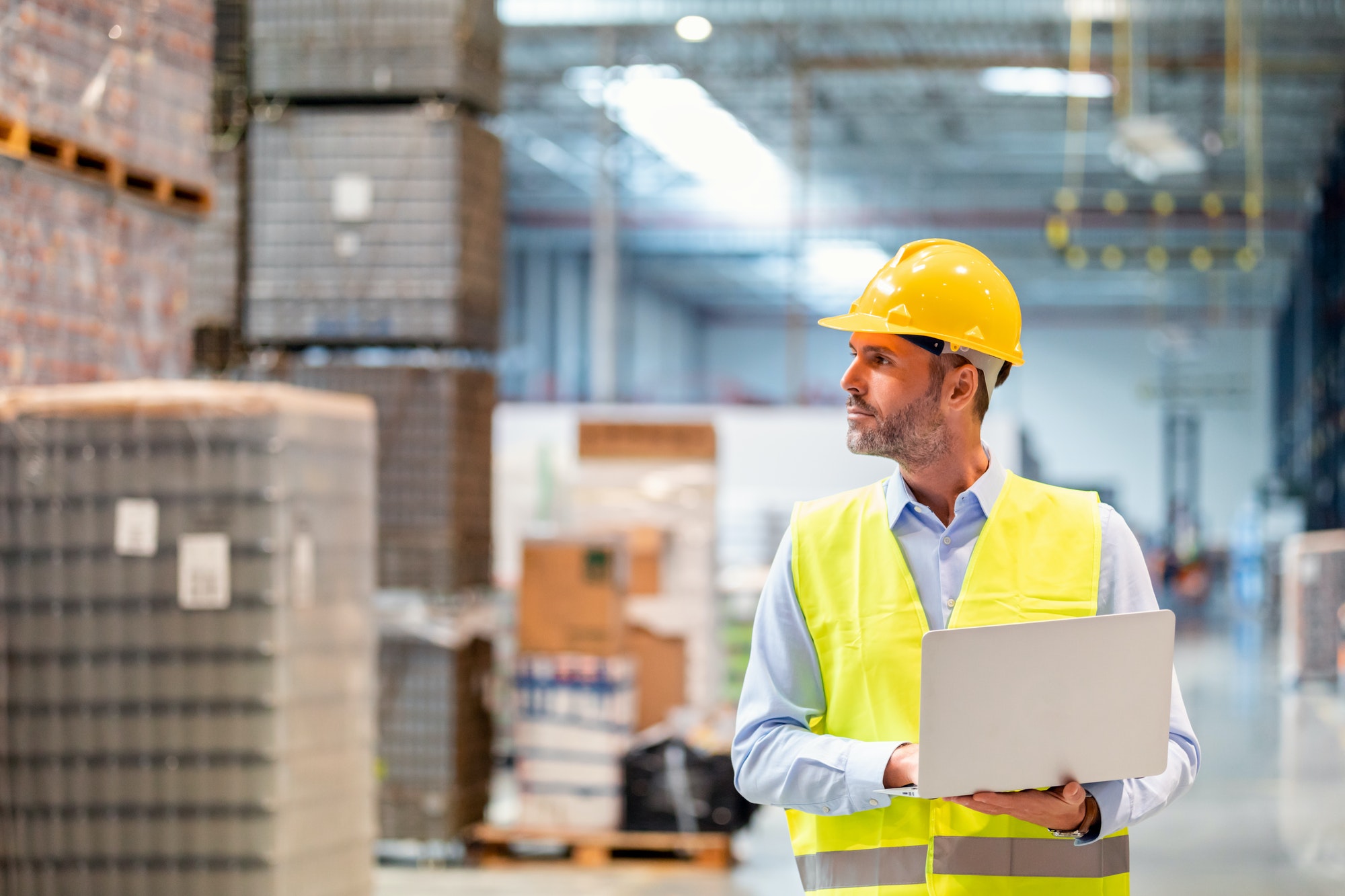
The best manufacturing businesses employ inventory systems and management to track and manage their inventory: from placing purchase orders to tracking points of sale and parts usage. In today’s marketplace, inventory accuracy is crucial.
It’s natural to think of inventory simply as the stock on your warehouse shelves, destined for sale to a customer. However, if we look closer, inventory systems can encompass far more than just the stock levels of your products.
An inventory management system can include three different types of inventory:
- Spare parts inventory,
- Asset inventory, and
- Maintenance parts, materials, and tools.
Items span multiple categories, such as lubrication oil sold to a customer as a product or used during periodic equipment servicing. This post breaks each system down to uncover the repercussions of mismanaging your inventory or ordering management.
More than anything, when it comes down to it, INVENTORY COUNTS!
Learning how to manage each inventory system and the entire procurement system–is the key to a lean and profitable organization.
“Inventory management is the umbrella term for the procedures and processes that affect ordering, receiving, storing, tracking, and accounting for all the goods a business sells.”
Forbes
Inventory Tracking and Control Principles
Finding a balance between keeping enough stock on the shelf but not too much to impact cash flow is a delicate task. This is true for all types of inventory, including stock for sale, assets, and maintenance supplies.
The best supply-chain management lists stock, sets specific reorder points to replenish spent supplies, and organizes inventory effectively.
All companies are familiar with periodic stocktakes. However, some take inventory control a step further and measure the overall efficiency of their demand forecasting, inventory ordering, order fulfillment, and consumption practices.
Inventory turnover measures the number of times a part number or SKU is used in a given period. This ratio indicates inventory “freshness”: whether your company has efficient buying practices and how well your inventory levels are managed. This number is often benchmarked by purchasing and finance teams in large organizations.
Digital warehouse management systems, included as features in the more robust, cloud-based CMMS, provide real-time inventory data.
However, for small businesses, precise inventory management can be challenging without the right tools and systems in place.
“Learning how to manage inventory efficiently is critical to any business . . . . By minimizing lost sales, misplaced stock and excess ordering, accurate inventory management boosts your profits and can even reduce your taxes.”
Forbes
Three Types of Inventory Systems and Management
1. Asset Inventory Management
Asset inventory management covers several critical functions, including centralizing asset repositories, monitoring asset events throughout their life cycles, and evaluating performance.
A sound asset management system can help you:
- better understand idle time and equipment use,
- plan and undertake maintenance, and
- locate your assets using scannable barcode labels or GPS.
Effective asset inventory management systems track the movement of items across organizational departments. Good asset inventory management processes also help you:
- Make informed decisions about your equipment and inventory on hand,
- Effectively maintain equipment so you can manufacture faster and reduce lead times for customers, and
- Maintain an audit trail and identify business improvement opportunities.
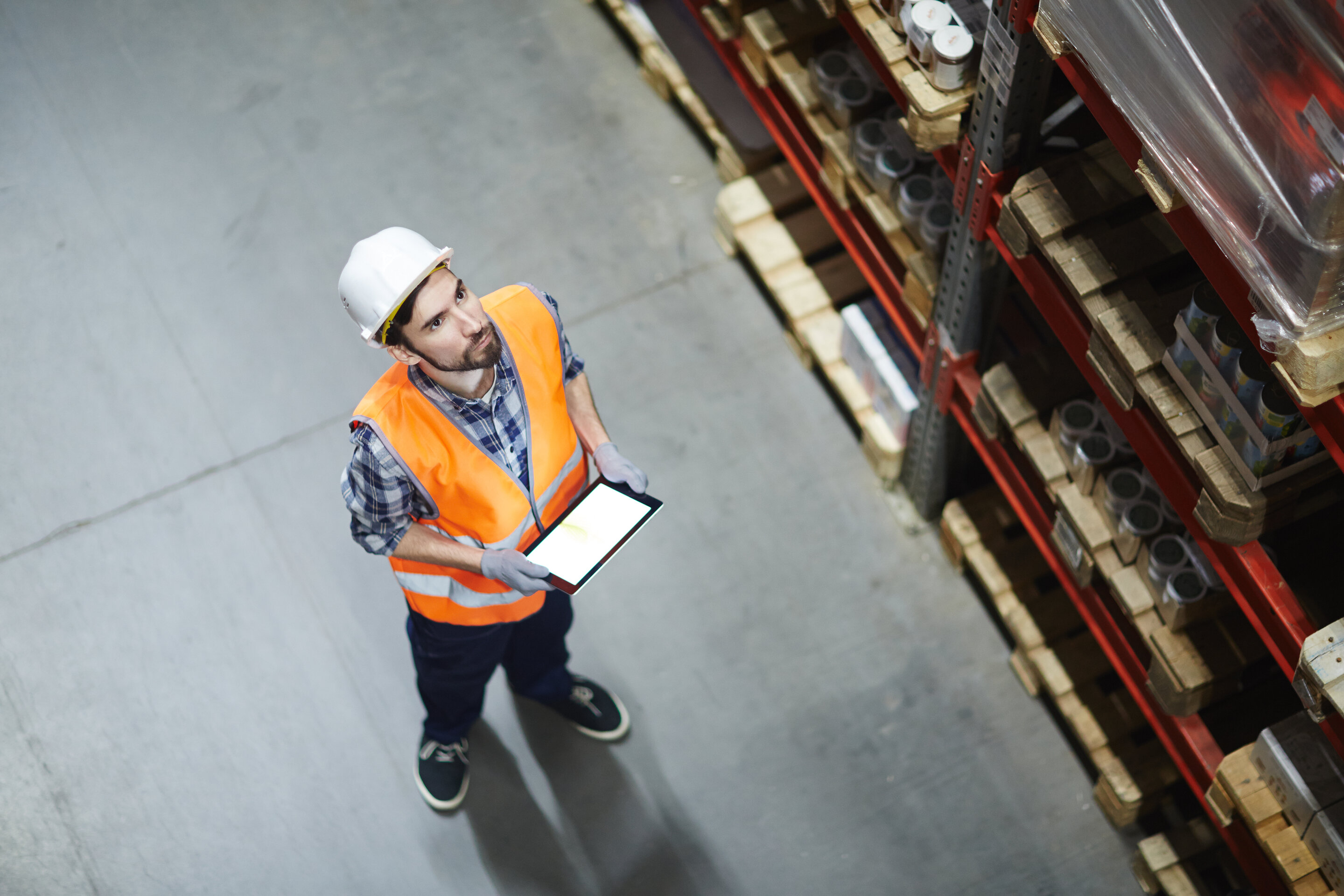
2. Spare Parts Inventory Management Systems
Maintaining adequate levels of spare parts is a balancing act. Finance teams often want to keep inventory levels low to reduce stock-on-hand value. However, not having enough parts on the shelf too often means:
- missed production targets,
- lengthy unplanned downtime,
- expensive freight bills for urgent parts supply, and
- long lead times.
This is where a robust parts inventory management system can deliver value to your business.
Tools and apps to help you manage spare parts inventory can:
- help you develop practical and efficient inventory control procedures,
- manage ordering and receiving lead times, and
- accurately forecast usage.
Such apps ensure your spare parts levels are maintained in a way that works for finance, procurement, production, and warehousing teams.
3. Inventory Systems for Maintenance Parts and Tools
Keeping the correct levels of spare parts and consumables in stock, such as:
- gaskets,
- filters,
- bearings, and
- grease
allows maintenance teams to respond quickly to emergency maintenance.
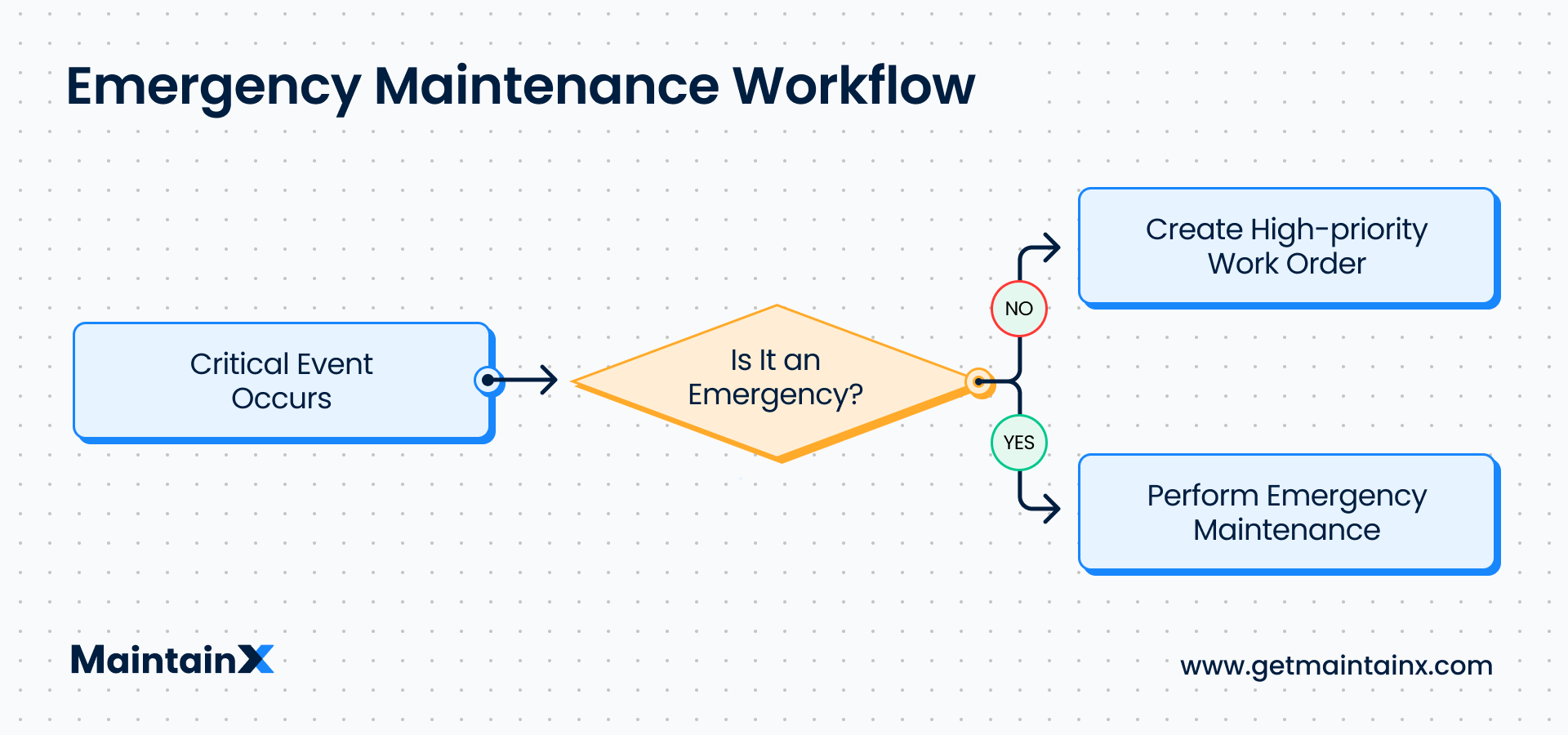
Such systems allow your business to keep equipment running smoothly and help you proactively prevent negative impacts on your production targets.
Maintenance teams aim to ensure the right inventory level is on hand to repair and maintain business assets without going over budget or holding excess stock.
To approach this accurately, we recommend using a CMMS (computerized maintenance management system) to track, manage, and review inventory regularly. A CMMS like MaintainX allows maintenance teams to locate, use, and reorder parts more efficiently, reducing waste and over-ordering.
Plus, good management of parts and materials will help to ensure obsolete parts don’t take up valuable space in your workshop.
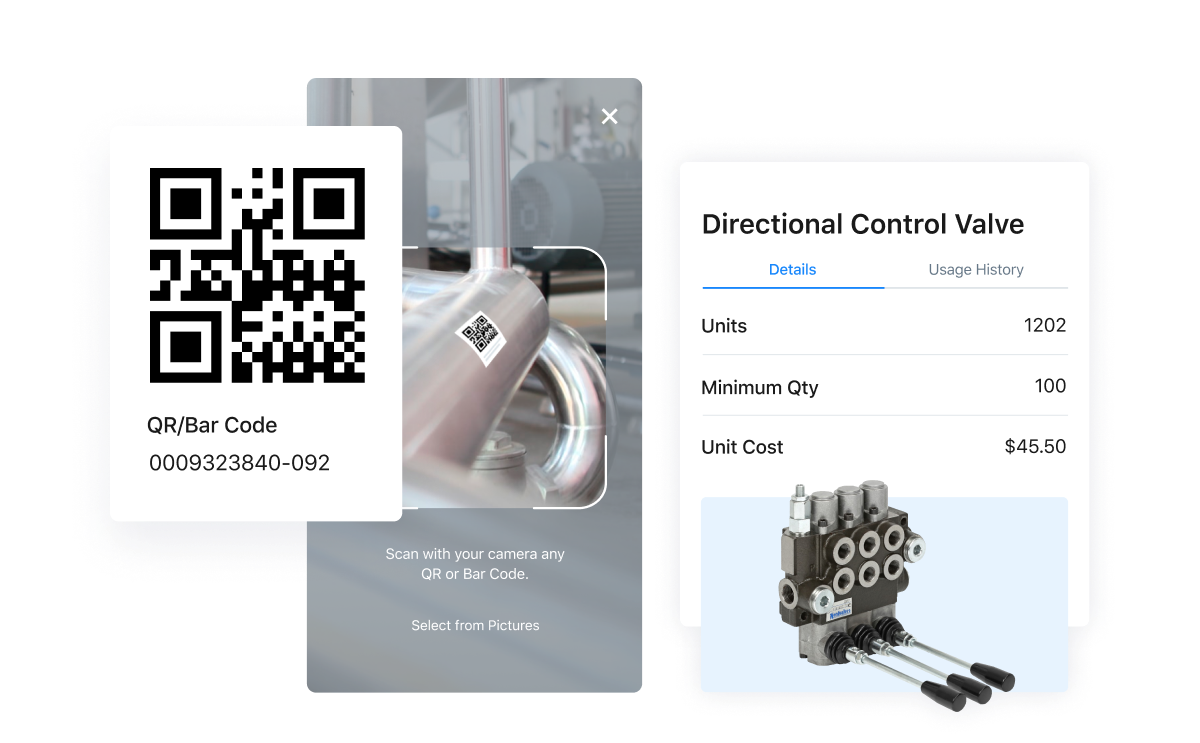
Inventory Management Software
Efficient warehouse management has come a long way since the days of paper-based packing slips and delivery dockets. Even spreadsheets have been superseded with new software that is more stable, available in real-time, and designed to manage inventory at scale.
These days, automated processes that were once confined to eCommerce giants are affordable. As a result, even small manufacturing companies can use CMMS to optimize and streamline their operations cost effectively.
Many enterprise resource planning (ERP) systems manufacturers allow integrations with other software. For example, SAP and Microsoft Dynamics365 can be connected to inventory management apps like MaintainX. In addition, MaintainX offers powerful APIs (application programming interfaces) to connect your current software with our powerful inventory management feature.
Automating your manufacturing and maintenance processes removes time-consuming manual inventory management, reduces human error, and allows manufacturers to monitor inventory in real time.
Inventory management procedures have a substantial impact on profitability. Get all the functionality you need in a single software solution.
Manage All Your Inventory in One Place with MaintainX
Inventory management can be difficult and time-consuming, especially if you use manual paper-based processes or outdated systems that don’t integrate.
Fortunately, MaintainX CMMS offers a user-friendly way to streamline inventory systems and management for both small businesses and large enterprises.
MaintainX helps businesses become more productive by seamlessly integrating their parts inventory with vendors and purchase orders.
FAQs
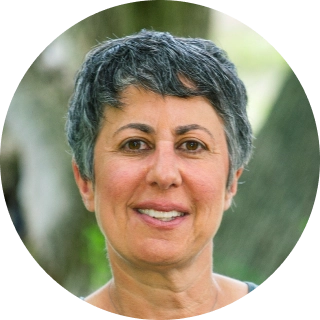
Caroline Eisner is a writer and editor with experience across the profit and nonprofit sectors, government, education, and financial organizations. She has held leadership positions in K16 institutions and has led large-scale digital projects, interactive websites, and a business writing consultancy.