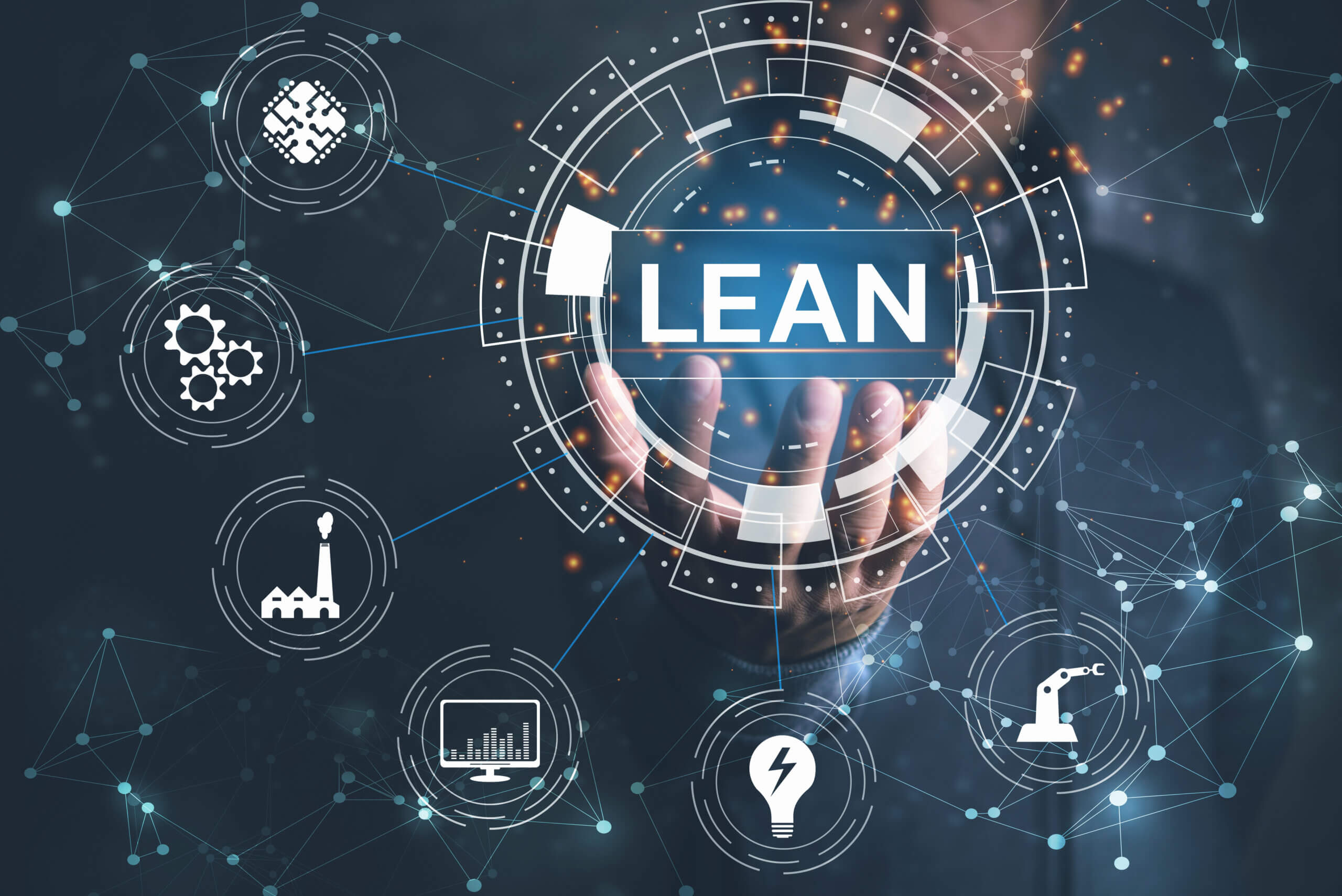
The vast majority of problems in any manufacturing environment come down to a handful of recurring causes. Viewed through the lens of lean methodology, these problems fall into five main categories, often referred to as the 5Ms.
The 5Ms
- Man
- Machine
- Materials
- Methods and
- Measurement.
These categories offer prompts for conducting a detailed analysis of a problem and form the backbone of what is known as the 5M approach. Like many other lean concepts, the 5M approach originated as part of the Toyota Production System.
This powerful problem-solving framework is particularly useful for uncovering issues within complex processes. It provides a system to help you and your team with root cause analysis so you can investigate problems more efficiently.
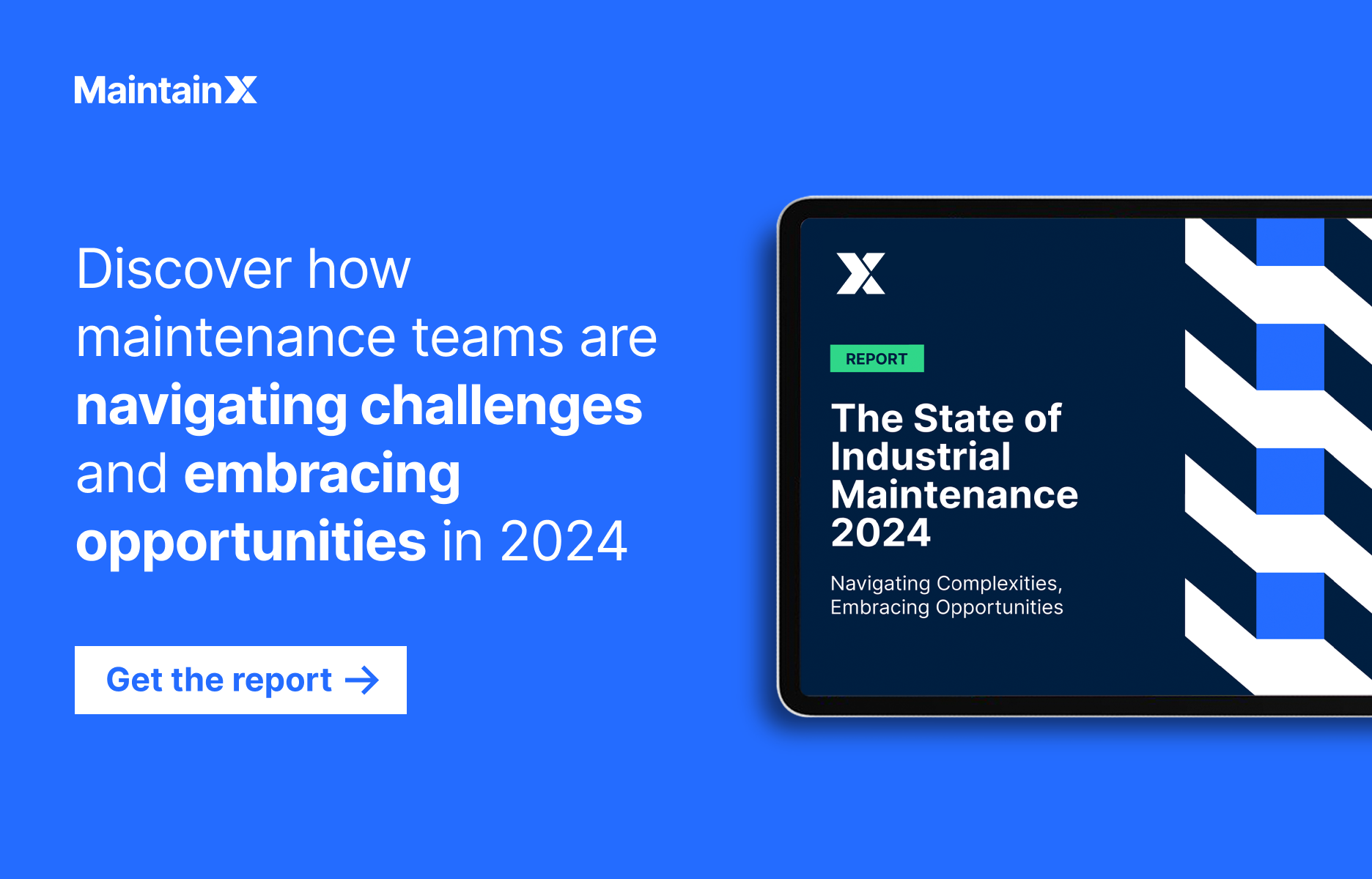
What about Lean 5M+E?
Although the “original” 5M categories cover five specific points, these have been expanded over the years to include additional areas for investigation. One variation uses the addition of “environment” as a potential factor in problem identification. Another variation includes management or money issues. This second variation also includes “Mother Nature” as a prompt for purpose and environmental concerns. Check out both variations below:
Lean 5M+E
- Man (aka Workforce)
- Machine
- Materials
- Methods
- Measurement
- Environment
The 8Ms
- Man (aka Workforce)
- Machine
- Materials
- Methods
- Measurement
- Mother Nature
- Management
- Maintenance
While both are useful, we’ll stick to the core 5Ms and how you can apply them in your company’s problem-solving huddles.
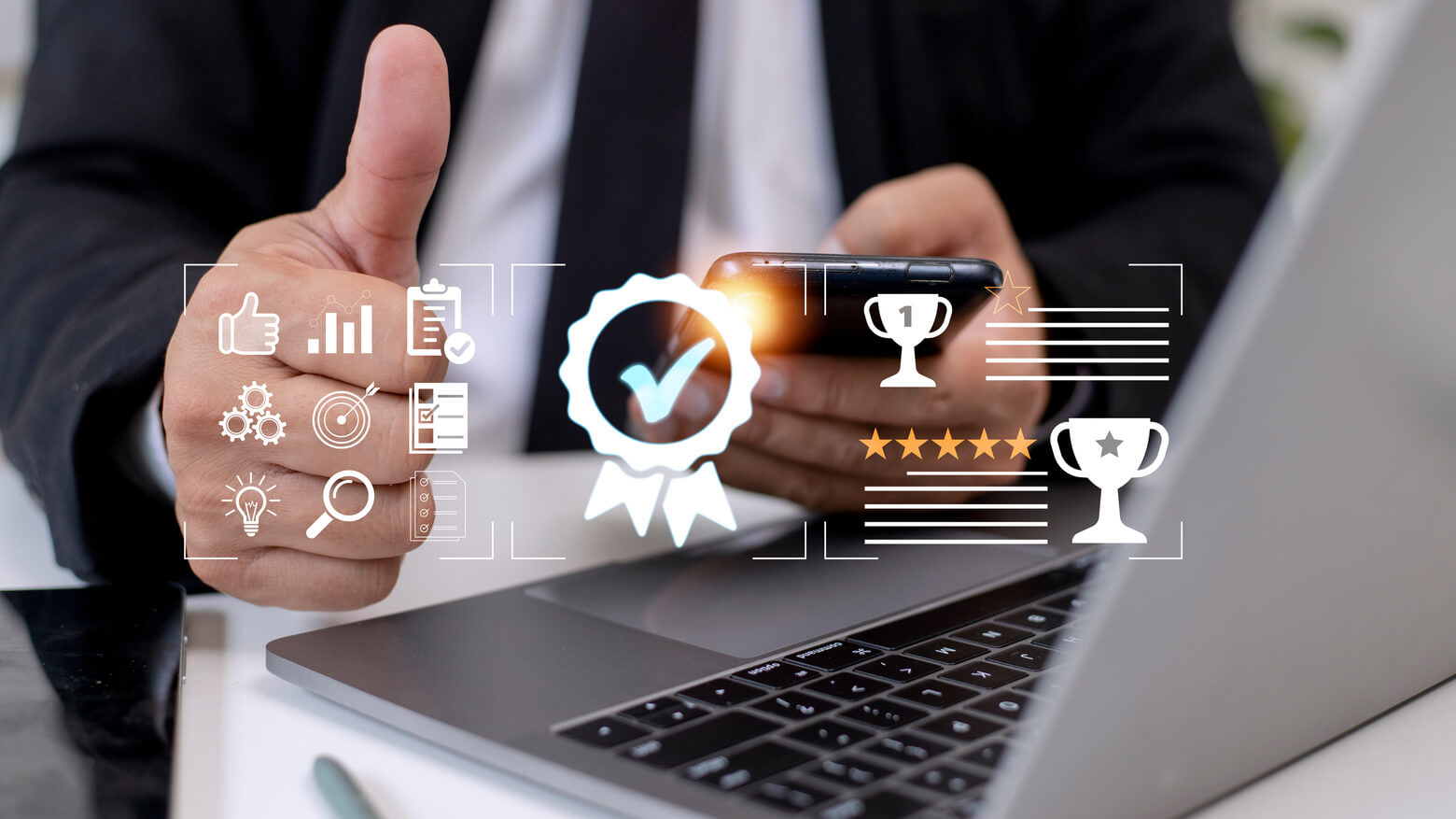
The 5Ms in Detail
For any product-based business, the 5Ms provide a structured way to evaluate problems by concentrating your focus on a specific area. Using this technique to look deeper into the cause of manufacturing problems can help you develop a more precise, more accurate problem statement. This is the basis for all successful root cause analysis exercises.
Let’s take a look at each of the 5Ms in detail and how they can prompt further examination of manufacturing process problems.
Manpower (aka Workforce)
Your team is your most valuable asset, and supervisors must understand their employees’ jobs in intimate detail. Gemba walks can help management teams stay connected to the factory floor, as can regular check-ins to discuss KPIs.
To assess whether your workforce could be a factor in your problem, ask yourself if your team is completing tasks in the expected fashion or does it need additional training. Is staff engagement high? Do employees feel safe and comfortable? Do individuals take pride in their tasks? Is every workstation cleaned via a 5S technique?
Machine
To be truly connected to the day-to-day business processes, supervisors must have a solid working knowledge of each machine and piece of equipment in their area. Knowing when machines are functioning at an optimum level – and when their performance drops – allows early identification of potential problems.
If product quality is an issue, consider whether the plant and equipment in your facility could be at fault. Automation seems like a simple way to boost efficiency, but all machinery still needs someone to oversee its performance. Breakdowns are an obvious culprit for some problems, but other minor machinery performance issues may not be so clear.
Materials
The smooth and precise flow of raw materials is vital when your business adopts a just-in-time production model.
The work zone should only house materials needed for the current task – cluttered workstations and excess materials can contribute to process issues and inefficient workflows. Consider implementing a kanban system to manage consumables and assembly parts like screws and grease.
Methods
Standardized methods, processes, and procedures are crucial to delivering a high-quality finished product to your customers. Using schedules, worksheets, diagrams, and checklists that show order and acceptable quality level for each process will help ensure consistency, no matter who is carrying out the work.
If your methods are letting you down, consider reviewing your standard operating procedures and distributing them in an easily accessible digital format.
Measurement
Tracking the right metrics (and key performance indicators) is the key to understanding whether a process is running smoothly. For example, management should clearly display production schedules, process improvement goals, profitability targets, and acceptable tolerance levels near the work area. This helps ensure everyone know about improvements as they happen.
Inspections, checklists, and audits can provide the necessary measurement tools to track the success of a process and, conversely, reveal problems as they arise.
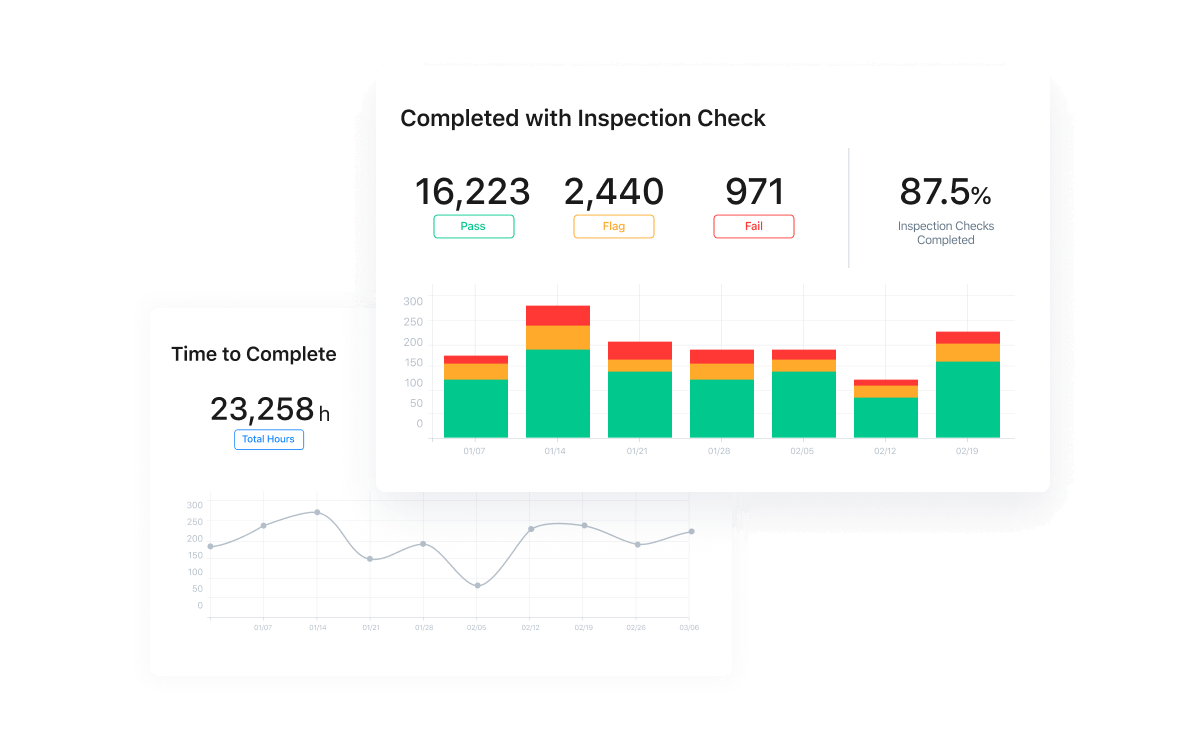
Why You Should Use the 5Ms for Root Cause Analysis
Root cause analysis (RCA) asks teams to shift their attention from the symptom and look more closely at the cause. It typically moves through a few distinct phases:
- Identifying the problem
- Analyzing how and why the problem is occurring
- Working on ways to prevent it from happening in the future.
However, accurately identifying the problem can be tricky with so many overlapping factors at play.
From undiscovered mechanical faults to employees who interpret SOPs differently, it often takes a lot of digging to get to the heart of the issue. Sometimes, several issues may occur simultaneously, adding further complexity. This is where frameworks like 5M can be helpful.
To bring the underlying issues to the fore, teams can use this approach along with several other lean manufacturing methodologies, such as Ishikawa diagrams, the 5 Whys, and cause and effect diagrams, such as fault tree analysis.
The fishbone diagram and the 5 Whys technique can use the 5Ms detailed above–man, machine, materials, methods, and measurement – to prompt brainstorming activities and uncover potential causes of issues.
Optimize Your Lean Business with MaintainX
The continuous improvement mindset that drives the use of these fault-finding techniques dovetails neatly with other lean management techniques.
Six Sigma, for example, is a data-driven approach that minimizes waste and improves business processes by reducing the chance of errors. This focus on data ties in with the final 5M measurement technique. Likewise, Kaizen encourages teams to strive for continuous improvement, and solving root-cause issues using 5M will help improve your operational performance.
At the end of the day, all lean methodologies work together to help to make your business a more productive, efficient, safe, and enjoyable place for all. And adopting the use of a CMMS like MaintainX can help simplify and streamline the entire process of “working towards lean,” helping you to effectively integrate lean techniques, tools, and approaches into your company culture.
FAQs
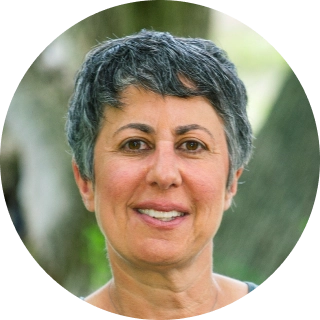
Caroline Eisner is a writer and editor with experience across the profit and nonprofit sectors, government, education, and financial organizations. She has held leadership positions in K16 institutions and has led large-scale digital projects, interactive websites, and a business writing consultancy.