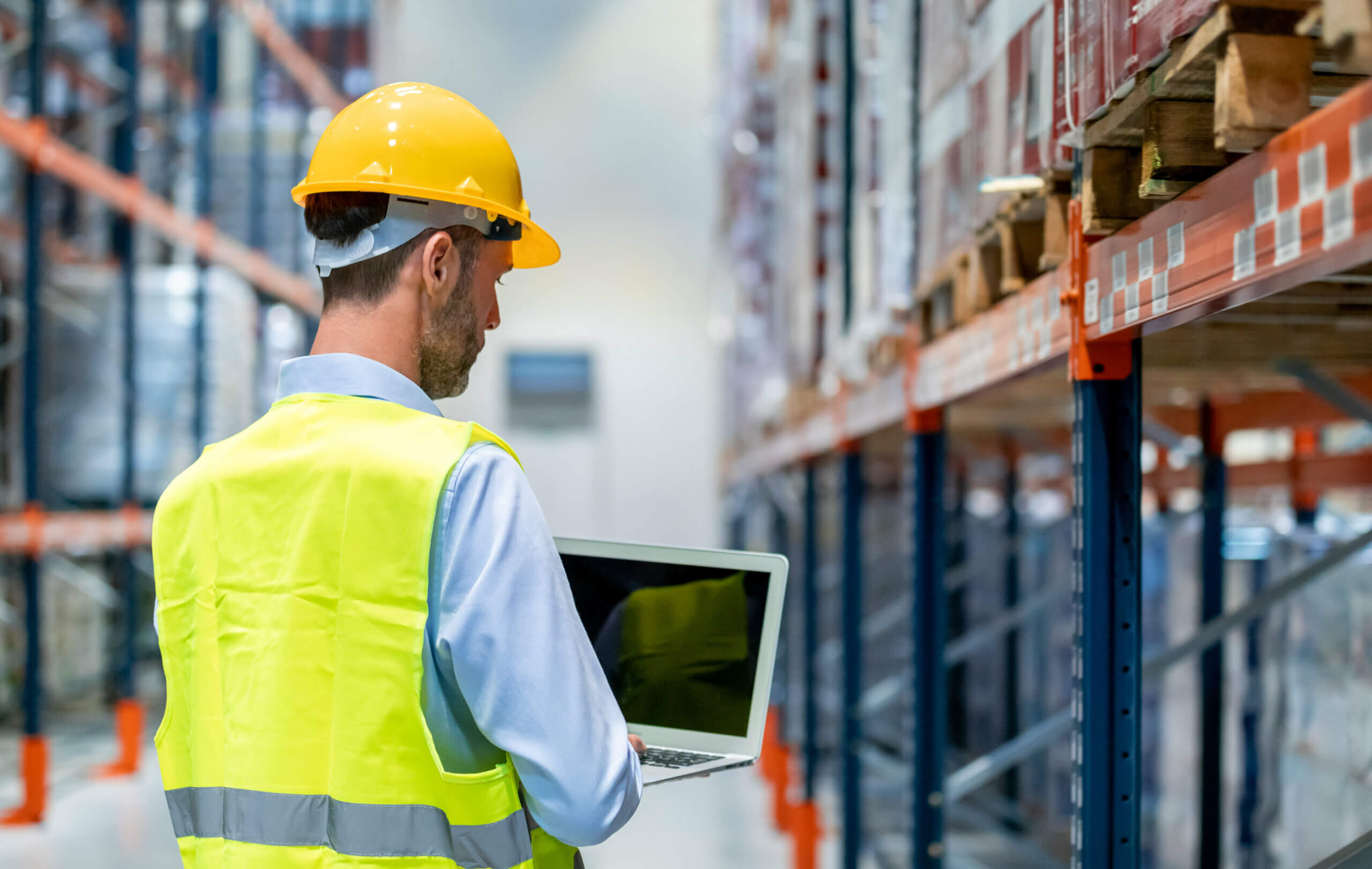
Numbers don’t lie. And in maintenance, KPIs tell you exactly where your team excels and where there's room for improvement. Are your technicians meeting performance goals? Are your assets running at peak efficiency? Maintenance KPIs give you the hard data to answer those questions. Organizations use that information at multiple levels to evaluate their success in reaching targets. In this guide, we’ll break down the essential KPIs your team needs to track in 2025 and how to use them for better decision-making.
What is a maintenance KPI?
Maintenance KPIs are measurements that link the effectiveness of organizational processes with specific maintenance goals. O&M managers use maintenance KPIs to measure, analyze, evaluate, and improve processes to enhance asset reliability.
Maintenance KPIs act as quantifiable benchmarks that correlate with broader company goals. For example, an organization wanting to cut costs may set a KPI to minimize maintenance costs by 10 percent.
Of course, no two maintenance departments are exactly alike. Best practices can vary widely by industry, sector, and location.
Maintenance KPIs can measure:
- Efficiency
- Asset downtime
- Asset performance
- Inventory management
- Maintenance task management
- Maintenance spending and costs
- Workplace safety and compliance
Put simply, organizations use maintenance KPIs to measure the performance of maintenance technicians, operational systems, and processes.
Maintenance Metrics vs. KPIs
Though maintenance pros often use maintenance metrics and KPIs interchangeably, some slight technical differences exist.
Maintenance performance metrics provide insights into the effectiveness of the maintenance team and system operations. Managers can use performance metrics to quantify daily maintenance activities compared to their target numbers.
Alternatively, KPIs technically refer to the target numbers themselves. For example, say your KPI is to minimize average maintenance costs by 5 percent within the next quarter. You can track maintenance performance metrics to monitor the effectiveness of your efforts.
Evaluating metrics like maintenance overtime, planned maintenance percentage (PMP), and overall equipment effectiveness (OEE) can help you reach the KPI.
15 maintenance metrics to benchmark for KPIs
Effective maintenance management relies on tracking the right metrics. Without them, achieving long-term success is a guessing game. Many metrics represent historical data. Others evaluate your current asset situations, and some offer insights into the future performance of equipment and assets. Many data-driven decisions rely on a combination of metrics to formulate an effective plan.
The following sections outline 15 essential metrics to help you set meaningful, data-driven KPIs for your maintenance team.
Mean time between failures (MTBF)
What MTBF measures:
MTBF represents the average time a piece of equipment operates before experiencing a failure. It helps determine asset reliability and predict maintenance needs.
How to calculate MTBF:
MTBF = Total operating time / Number of failures
MTBF = 1,000 / 4 failures = 250 hours
Example:
Let’s say you have a machine that operates for a total of 1,000 hours over the course of a month and experiences 4 failures during that time. To calculate the MTBF:
MTBF = 1,000 hours / 4 failures
MTBF = 250 hours
MTBF KPI benchmark:
A higher MTBF indicates better reliability. While benchmarks can vary, many industries aim for an MTBF of 500 to 2,000 hours, depending on the equipment type and use case.
Mean time to failure (MTTF)
What MTTF measures:
MTTF measures the average time an asset operates before failing beyond repair. It’s a particularly useful metric for non-repairable equipment, like lightbulbs. MTTF differs from MTBF in that MTTF measures the time until total irreparable failure, while MTBF calculates the time between failures that can be fixed.
How to calculate MTTF:
MTTF = Total operating time / Number of failed assets
Example:
Imagine you have a batch of 100 non-repairable light bulbs in operation for a total of 50,000 hours. Over that time, 25 bulbs fail and need to be replaced. To calculate the MTTF:
MTTF = 50,000 hours / 25 failed assets
MTTF = 2,000 hours
MTTF KPI benchmark:
Higher MTTF indicates a longer asset lifespan. Benchmarks vary, but a common target is between 1,000 and 5,000 operating hours, depending on the equipment type and industry standards.
Overall equipment effectiveness (OEE)
What OEE measures:
The overall equipment effectiveness metric evaluates equipment efficiency and productivity by combining three factors: availability, performance, and quality. This maintenance metric gives you a comprehensive view of how well your equipment is running.
How to calculate OEE:
OEE = Availability × Performance × Quality
How to calculate these variables:
- Availability = (Actual operating time / Planned production time)
- Performance = (Actual production rate / Ideal production rate)
- Quality = (Good units produced / Total units produced)
Let’s break this down with a real-world example:
Imagine you have a machine that’s scheduled to run for an 8-hour shift or 480 minutes. However, the machine went down for 60 minutes for repairs. This gives us an actual operating time of 420 minutes.
- Availability = 420 / 480 = 0.875 or 87.5%
Let's say the ideal production rate is 100 units per hour, but the actual production rate was 80 units per hour.
- Performance = 80 / 100 = 0.8 or 80%
Only 540 of the 560 units produced during the 7-hour operation met quality standards and 20 were considered defective.
- Quality = 540 / 560 = 0.964 or 96.4%
When we put this all together, we get the following calculation:
OEE = 0.875 (Availability) × 0.8 (Performance) × 0.964 (Quality)
OEE = 0.674 or 67.4%
OEE KPI benchmark:
An OEE score of 85% or higher is considered world-class. A 60% and 85% score indicate room for improvement, while below 60% suggests significant inefficiencies such as incorrect setups or slow-running equipment.
Planned maintenance percentage (PMP)
What PMP measures:
Planned maintenance percentage tracks how much of your maintenance work is scheduled rather than reactive. A higher PMP indicates a more proactive approach to maintenance, reducing unplanned downtime.
How to calculate planned maintenance percentage:
PMP = (planned maintenance hours / total maintenance hours) × 100
Example:
For instance, your maintenance team worked 300 hours last month. Of those 300 hours, 200 were spent on planned maintenance activities, such as scheduled inspections and preventive repairs.
PMP = (200 / 300) × 100
PMP = 0.6667 × 100
PMP = 66.67%
PMP KPI benchmark:
An ideal PMP benchmark is 85% or higher, meaning a vast majority of your maintenance activities are planned and not reactive.
Reactive maintenance percentage
What reactive maintenance percentage measures:
Reactive maintenance percentage tracks the proportion of maintenance work that is unplanned or done in response to equipment failures. A lower percentage indicates a more proactive approach to maintenance, which can reduce downtime and extend equipment lifespan.
How to calculate reactive maintenance percentage:
Reactive maintenance percentage = (reactive maintenance hours / total maintenance hours) × 100
Example:
For example, revisiting the PMP example, of the 300 hours of total maintenance that month, 100 were spent on reactive maintenance.
Reactive maintenance percentage = (100 / 300) × 100
Reactive maintenance percentage = 33.3%
Reactive maintenance percentage KPI benchmark:
A reactive maintenance percentage below 20% is ideal. Higher values may indicate a need for more robust preventive maintenance strategies or more efficient planning.
Schedule compliance
What schedule compliance measures:
Schedule compliance measures how effectively your maintenance team adheres to the planned maintenance schedule. It tracks the percentage of scheduled maintenance tasks that are completed on time.
How to calculate schedule compliance:
Schedule compliance = (completed scheduled tasks / total scheduled tasks) × 100
Example:
For example, your maintenance team had 120 tasks scheduled for last month. Of those, they completed 108 on time.
Schedule compliance = 108 / 120 x 100
Schedule compliance = 90%
Schedule compliance KPI benchmark:
A 90% or higher schedule compliance benchmark is ideal, indicating that your team completes most maintenance tasks on time. A low score could indicate several issues you need to address, such as ineffective communication between teams or inadequate resource planning.
Remaining asset value (RAV)
What RAV measures:
Remaining asset value measures the current value of an asset compared to its original purchase price. RAV helps determine whether it’s more cost-effective to maintain or replace the asset.
How to calculate remaining asset value:
RAV = (current asset value / original purchase value) × 100
Example:
Suppose you purchased an industrial printer for $20,000; its estimated value is now $8,000. To calculate the RAV:
RAV = (8,000 / 20,000) × 100
RAV = 40%
RAV KPI benchmark:
A lower RAV suggests that the asset is nearing the end of its useful life. A benchmark of 50% or lower typically signals the need to evaluate asset replacement.
Standard maintenance cost per unit (SMCP)
What SMCP measures:
Standard maintenance cost per unit measures the average maintenance cost required to keep each unit of equipment operational. It helps assess the efficiency of your maintenance spending.
How to calculate standard maintenance cost per unit:
SMCP = (total maintenance costs/number of units maintained)
Example:
Let’s say your company spent $50,000 on maintenance last quarter to keep 200 pieces of equipment running efficiently. To calculate SMCP:
SMCP = 50,000 / 200
SMCP = $250 per unit
SMCP KPI benchmark:
A lower SMCP indicates more cost-effective maintenance operations. Benchmarks vary, but tracking trends over time can highlight opportunities to optimize maintenance costs. For example, implement preventive maintenance or use data analytics to help guide decision-making and maximize every dollar you spend.
Work order completion rate
What work order completion rate measures:
Work order completion rate monitors the percentage of work orders completed within a set timeframe. It provides insights into how efficiently your team meets maintenance objectives.
How to calculate work order completion rate:
Work order completion rate = (completed work orders / total work orders) × 100
Example:
Let’s say your team had 150 work orders assigned last month and completed 135. To calculate the Work Order Completion Rate:
Work Order Completion Rate = (135 / 150) × 100
Work Order Completion Rate = 90%
Work order completion rate KPI benchmark:
A 90% or higher rating indicates strong performance. If your score falls below 85%, it may signal inefficiencies in task prioritization or resource allocation.
Maintenance backlog
What maintenance backlog measures:
Maintenance backlog measures the amount of maintenance work that is scheduled but not yet completed. It helps assess your team’s capacity to keep up with scheduled tasks and maintain operational efficiency.
How to calculate maintenance backlog:
Maintenance backlog = (total pending maintenance work / total available maintenance hours) × 100
Example:
Imagine your maintenance team has 500 hours of pending work and 1,000 hours of available maintenance time over the next month. To calculate Maintenance Backlog:
Maintenance Backlog = (500 / 1,000) × 100
Maintenance Backlog = 50%
Maintenance backlog KPI benchmark:
A 2 to 4 week maintenance backlog is considered ideal because it provides enough work to keep your team productive without overwhelming them. A backlog exceeding this range may indicate insufficient resources or inefficient work order management.
Maintenance technician productivity
What maintenance technician productivity measures:
Maintenance technician productivity tracks how efficiently your technicians complete their assigned tasks. It tracks the amount of productive work time versus time lost to delays, errors, or inefficiencies.
How to calculate maintenance technician productivity:
Maintenance technician productivity = (productive maintenance hours / total maintenance hours) × 100
Example:
For instance, your technician worked 160 hours in a month, with 120 hours spent on planned maintenance and 40 hours spent waiting for parts or handling admin tasks. To calculate productivity:
Maintenance Technician Productivity = (120 / 160) × 100
Maintenance Technician Productivity = 75%
Productive maintenance hours refer to the time technicians spend actively working on planned maintenance tasks that directly contribute to the goals of the maintenance operation, as opposed to time spent waiting on parts or administrative work between tasks.
Maintenance technician productivity KPI benchmark:
A productivity rate of 85% or higher is generally considered efficient. If the rate is below 75%, it may indicate bottlenecks or a need for better task management and resource allocation. If your technician is hitting 90% or higher, they're a superstar.
Spare parts turnover ratio
What spare parts turnover ratio measures:
Spare parts turnover ratio represents how often spare parts are used and replaced within a specific time frame. It helps track inventory management efficiency by indicating whether you're using parts efficiently or unnecessarily stockpiling them.
How to calculate spare parts turnover ratio:
spare parts turnover ratio = (cost of spare parts used / average spare parts inventory)
How this works:
- Cost of spare parts used: This is the total monetary value of all the parts consumed within the given period—in this example, a year.
- Average spare parts inventory: This is the average value of the spare parts inventory on hand over the same period.
Example:
For example, if your inventory’s average value is $50,000 and you’ve used $100,000 worth of parts over the year:
Spare parts turnover ratio = ($100,000 / $50,000) = 2
This means your inventory "turned over" twice during the year.
Spare parts turnover ratio KPI benchmark:
An ideal spare parts turnover ratio varies depending on industry and equipment type, but a higher turnover ratio typically indicates better inventory management. A ratio of 2 to 4 is common for many industries, signaling a balance between stocking too many or too few parts.
Equipment downtime
What equipment downtime measures:
Equipment downtime tracks the percentage of time equipment is out of service due to maintenance, repairs, or failures. It’s a critical indicator of operational efficiency and asset reliability.
How to calculate equipment downtime:
Equipment downtime = (total downtime hours / total operating hours) × 100
Example:
Imagine a machine has been out of service for 10 hours during a 200-hour production month. To calculate the equipment downtime percentage:
Equipment Downtime = (10 / 200) × 100
Equipment Downtime = 5%
Equipment downtime KPI benchmark:
A lower equipment downtime percentage is ideal, with many industries aiming for less than 5% downtime. Higher values may signal maintenance inefficiencies or aging equipment that requires more frequent repairs.
Asset utilization
What asset utilization measures:
Asset utilization tracks how efficiently equipment is used compared to its full potential. It shows whether assets are being underused, overworked, or used optimally.
How to calculate asset utilization:
Asset utilization = (actual output / maximum possible output) × 100
Example:
Suppose a manufacturing machine has a maximum production capacity of 1,000 units per month but produced only 750 units last month. To calculate the asset utilization:
Asset Utilization = (750 / 1,000) × 100
Asset Utilization = 75%
What output means:
What counts as output varies depending on the type of asset or industry, but it typically measures the work an asset completes—or is capable of completing—within a given time frame.
Asset utilization KPI benchmark:
An asset utilization rate of 85% to 95% is generally considered optimal. Lower rates may indicate underutilization, while higher rates could suggest overuse, leading to wear and tear.
First pass yield (FPY)
What first pass yield measures:
First-pass yield is a key indicator of quality and process efficiency. It measures the percentage of products or tasks completed correctly the first time around without requiring any rework or corrections.
How to calculate first pass yield:
FPY = (number of units completed without rework / total number of units produced) × 100
Example:
Imagine your team manufactured 1,000 units of a product, and 950 of these passed quality checks without needing rework. To calculate the FPY:
FPY = (950 / 1,000) × 100
FPY = 95%
First pass yield KPI benchmark:
An FPY of 95% or higher is a world-class score. Lower percentages suggest issues with quality control or process inefficiencies that require attention, such as inconsistent processes or substandard materials and components.
How to determine which KPIs to track
We recommend that beginners track no more than five maintenance KPIs at any given time.
Staying “lean and mean” will help prevent data overwhelm and support the kind of incremental improvements that lead to lasting change. So, how do you determine the right KPIs to track?
Ask yourself the following questions:
- What specific changes would most benefit your department?
- What specific outcomes would most benefit organizational goals?
- Which performance metrics could you use to measure progress?
- What management SOPs could you put in place to streamline tracking?
Prioritize the maintenance objectives that most strongly support your organization’s unique goals. To ensure everyone is on the same page, running your proposed KPIs by executive leadership is a good idea.
As previously mentioned, chosen KPIs and maintenance metrics can vary substantially based on industry, location, and other factors. That said, one of the most common KPI-related questions we receive—how to use them effectively—deserves its own section.
How to use maintenance KPIs effectively
Implementing maintenance KPIs is only the first step. The real value lies in using them to drive meaningful improvements. Once you’ve identified which KPIs to track, follow a structured process to make the best use of the insights they provide. Below are key steps to help you get the most out of your maintenance KPIs:
Identify relevant KPIs
The right KPIs can make or break your maintenance strategy. Focus on the ones that align with your maintenance goals and overall business objectives. For example, if reducing equipment downtime is a priority, you might track metrics like mean time between failures (MTBF) and equipment downtime. If cost savings are the goal, focus on maintenance cost per unit (SMCP) or inventory turnover.
Set benchmarks and targets
Clear targets give your team something to aim for. Establish performance benchmarks that reflect industry standards or your company’s goals, providing a baseline to measure progress and identify areas for improvement. For instance, if the industry standard for schedule compliance is 90%, aim to meet or exceed that benchmark and track your progress to ensure your team stays on course.
Collect and analyze data
Data is only as useful as the metrics you track. Use your computerized maintenance management system (CMMS) to gather accurate information for each KPI. Regularly run analyses to uncover inefficiencies and trends. For example, track the number of work orders completed each month to calculate your work order completion rate. Regularly analyze this data to spot trends that point to inefficiencies.
Interpret results
Numbers tell the story, but you need to dig deeper. Look beyond the figures to understand the root causes behind your KPIs. For example, rising equipment downtime might point to aging equipment or inadequate preventive measures.
Take action based on insights
Insights without action are just numbers. Use your KPI analysis to drive concrete improvements. If your analysis shows that your first pass yield is lower than expected, take steps to standardize procedures or improve technician training. Use that data to make adjustments that will directly impact performance.
Communicate results
Sharing is critical to success. Regularly report KPI data to your team and stakeholders to make sure everyone is aligned and working toward the same goals.
Review and adjust KPIs
KPIs should evolve as your business grows. Regularly review your maintenance metrics and adjust them to match shifting business goals or operational realities.
How to track key maintenance metrics automatically with MaintainX
Tracking KPIs doesn’t have to be complicated. MaintainX offers powerful tools to help you track your maintenance KPIs with ease. From customizable dashboards to real-time reporting, our platform ensures you stay on top of your key metrics. Below are some of the critical key performance indicators that MaintainX can help you track:
Work order completion rate
Stay ahead of the game with real-time tracking. With the MaintainX digital work order system, you can track the percentage of work orders completed on time. Our platform lets you monitor work order progress in real-time, helping you stay ahead of deadlines.
Equipment downtime
Keep tabs on equipment downtime. Use MaintainX to identify patterns or recurring issues that lead to operational inefficiencies. Our downtime tracking feature helps you pinpoint problem areas and minimize unplanned outages.
Maintenance costs
It's time to stop guessing and start saving. MaintainX provides detailed cost tracking, allowing you to monitor your maintenance expenses. With real-time reporting, you can optimize spending by comparing actual costs to benchmarks and identifying cost-saving opportunities.
Asset performance and utilization
Get more out of your assets. Monitor their utilization rates and performance with MaintainX’s asset management features. For more advanced metrics like mean time between failures (MTBF) and mean time to repair (MTTR), integrating with IoT sensors or other asset management systems can provide deeper insights to ensure your assets are running efficiently.
Reactive maintenance percentage
Minimize the unexpected. MaintainX's reactive maintenance tracking tools can help you track how much of your maintenance is unplanned. A lower reactive maintenance percentage means more time spent on proactive maintenance activities that avoid unplanned downtime and boost productivity.
Preventive maintenance compliance
Stay ahead of equipment failures. MaintainX's automated reminders and tracking tools ensure that preventive maintenance tasks are completed on schedule. Monitor schedule compliance rates to keep your team on track with planned maintenance activities.
Work order backlog
Stay ahead of the curve. Monitor pending maintenance work with the MaintainX work order backlog feature. This metric helps you identify bottlenecks, prioritize overdue tasks, and complete them efficiently.
Technician productivity
Boost your team’s efficiency. MaintainX helps you track technician productivity by monitoring labor hours and task completion rates. This allows you to spot inefficiencies and direct your resources where they'll do the most good.
It's as easy as it sounds. MaintainX’s dashboards and reports provide an invaluable look into these metrics, helping you make data-driven decisions that boost operational efficiency.
Start down your path toward better performance. MaintainX makes it easy to monitor key performance indicators, streamline operations, and drive real results. Begin optimizing your maintenance processes today with real-time insights and customizable dashboards. Get started with MaintainX now.
Maintenance KPIs FAQs
What are the benefits of tracking maintenance KPIs?
Maintenance KPI tracking gives you valuable insights into the performance of your maintenance operations, revealing opportunities for improvement and pinpointing inefficient processes. This helps make data-driven decisions that reduce downtime, increase asset reliability, and optimize maintenance costs. Most importantly, tracking KPIs helps ensure your team meets its goals, improves overall operational efficiency, and supports long-term planning.
How often should maintenance KPIs be reviewed?
You should review KPIs regularly to confirm that operations are on track. For most companies, a monthly review provides a frequent enough snapshot to spot trends and address issues before they become major problems. You may need to monitor some KPIs weekly or even daily, such as equipment downtime or work order completion rates. Regular reviews ensure that your team can make adjustments quickly, optimize performance, and meet your organization's long-term goals.
How do you use maintenance KPIs to improve decision-making?
Maintenance KPIs provide valuable data to help make informed decisions. For example, by tracking technician productivity, asset utilization, and maintenance costs, you can see where your team excels and where they can improve. This data allows you to make strategic decisions, such as reallocating resources, adjusting maintenance schedules, or investing in preventive maintenance. Regularly analyzing KPIs backs your decisions up with data, helping to improve asset reliability and make the best use of your resources.
What metrics does MaintainX track?
MaintainX monitors a wide range of maintenance metrics to help keep your team on track. Key performance indicators include work order completion rate, equipment downtime, maintenance costs, and preventive maintenance compliance. You can also monitor technician productivity, work order backlog, and reactive maintenance percentage directly within the platform. For more advanced metrics like mean time between failures (MTBF) and mean time to repair (MTTR), MaintainX can integrate with external systems such as IoT sensors to provide deeper insights into asset performance.
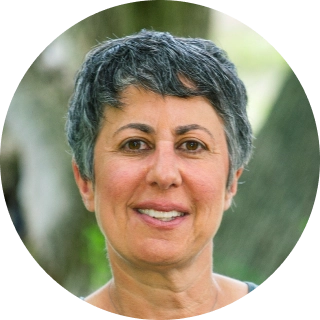
Caroline Eisner is a writer and editor with experience across the profit and nonprofit sectors, government, education, and financial organizations. She has held leadership positions in K16 institutions and has led large-scale digital projects, interactive websites, and a business writing consultancy.