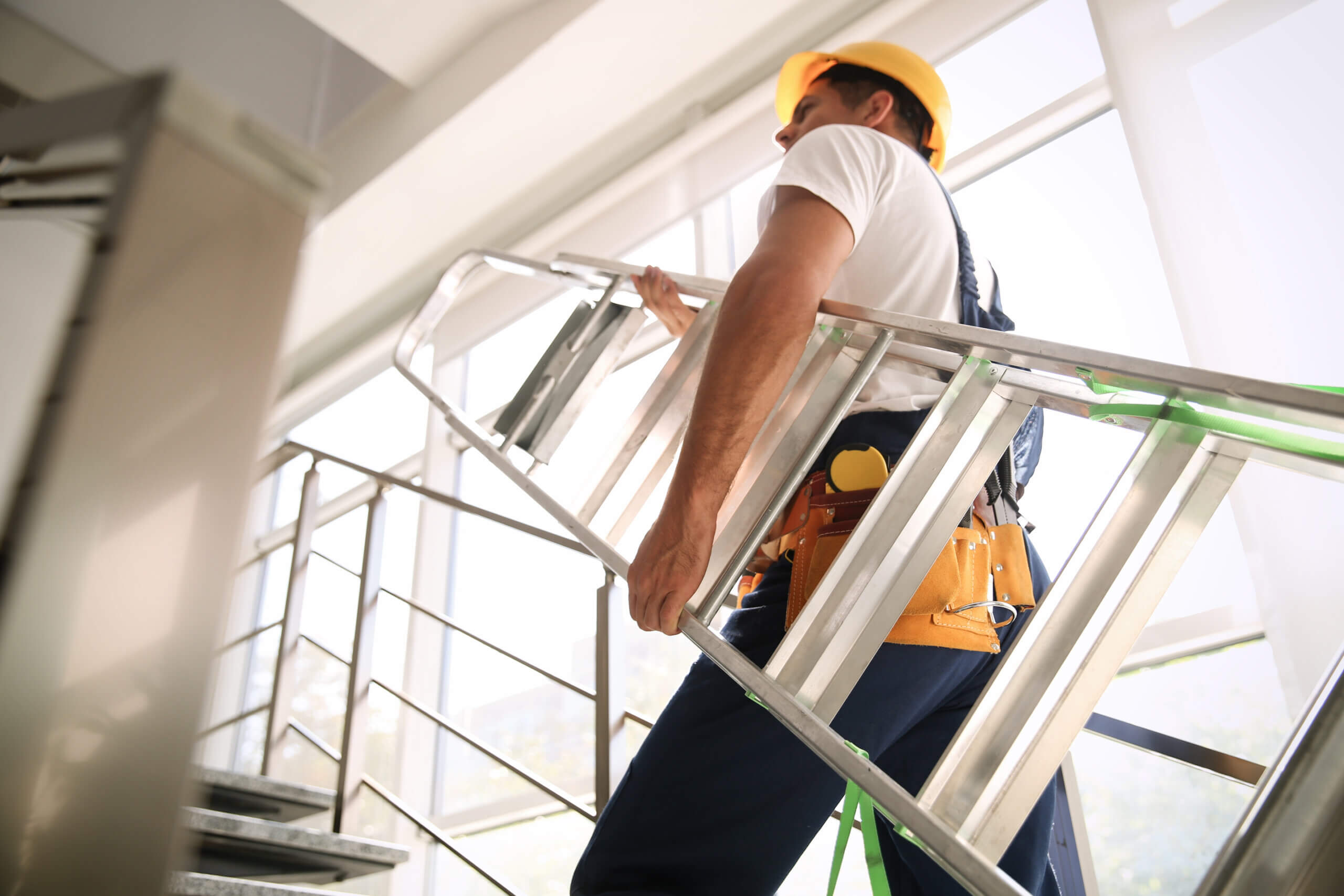
What Is a Building Maintenance Plan?
A building maintenance plan is a way to prioritize goals, maintain assets, schedule work, and monitor progress. A well-executed plan guarantees fewer emergencies, less disruption, and more straightforward repairs across working environments. It also means fewer occupant complaints and happier employees with better control over their workday.
For all this to happen, your building maintenance services team needs to shift its emphasis from reactive maintenance to preventive maintenance.
Reactive Building Maintenance vs. Preventive Building Maintenance
Reactive Maintenance (RM)
Reactive Maintenance addresses problems after they happen. RM falls into two broad categories: corrective maintenance and emergency maintenance.
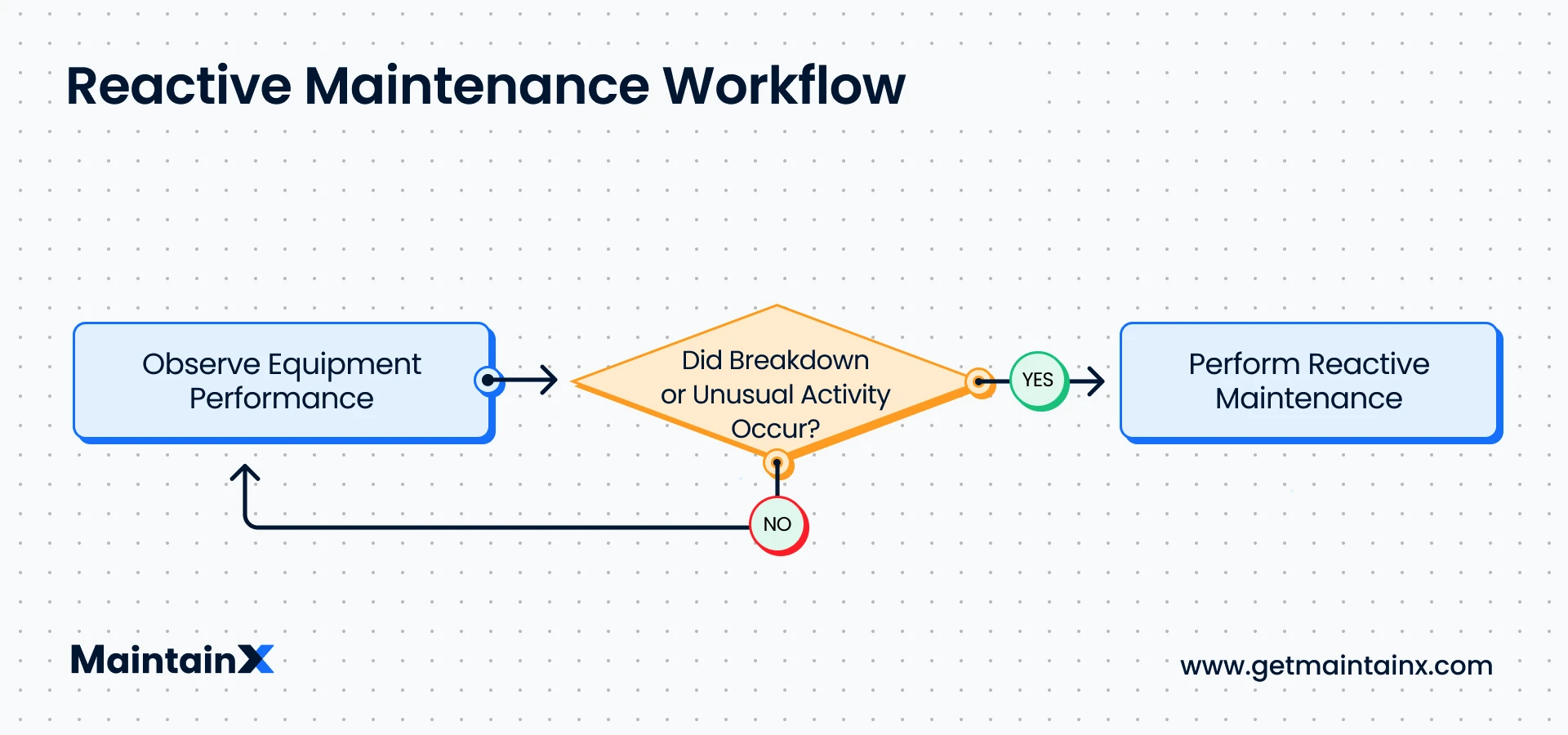
- Corrective Maintenance: Corrective maintenance is fixing something that has already broken, like changing the battery of a malfunctioning thermostat or replacing worn-out rubber washers on a dripping faucet.
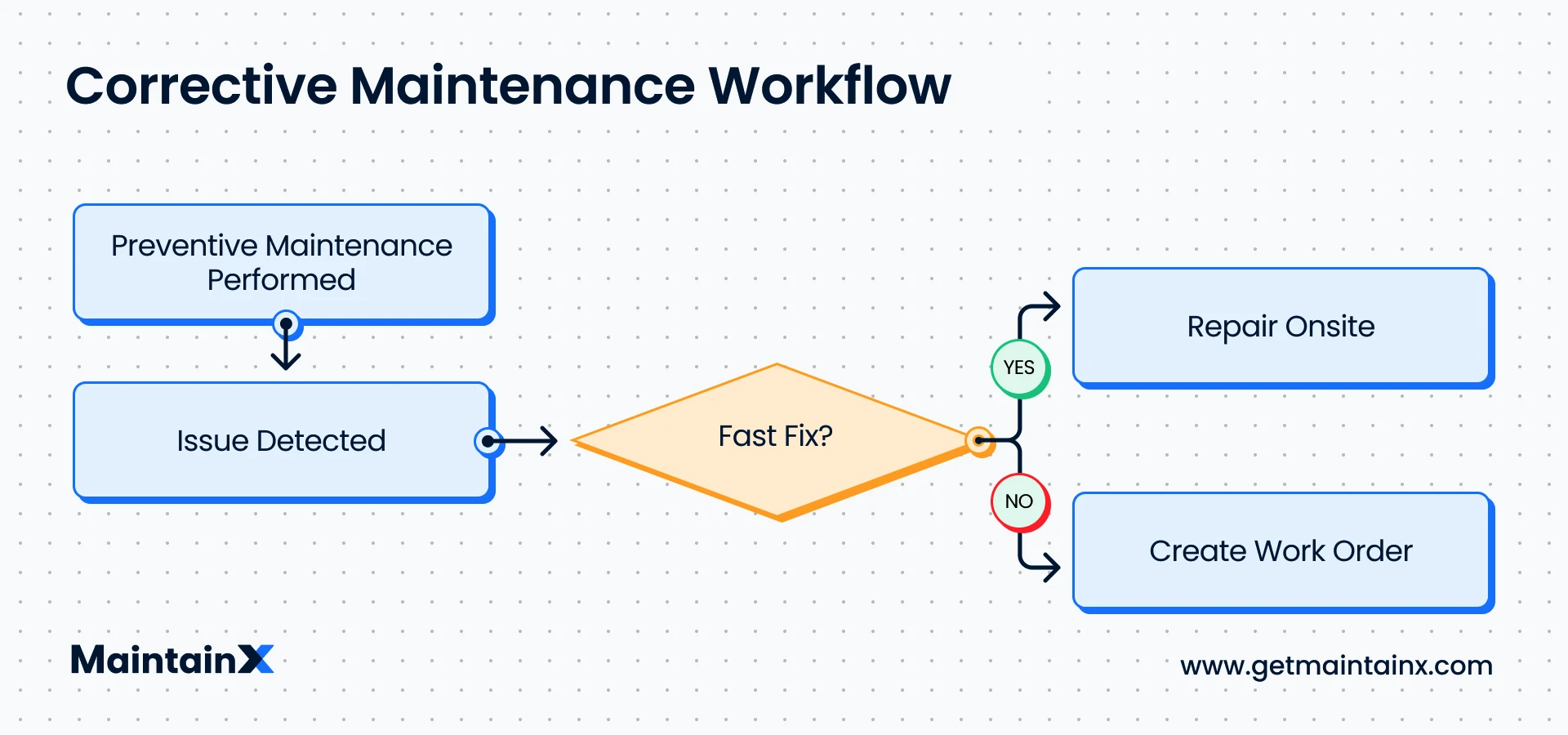
- Emergency Maintenance: Emergency maintenance is the most urgent and costly type of reactive maintenance. Some examples are gas leaks, backed-up sewer lines, no heat in winter, or any maintenance issue that puts people at risk.
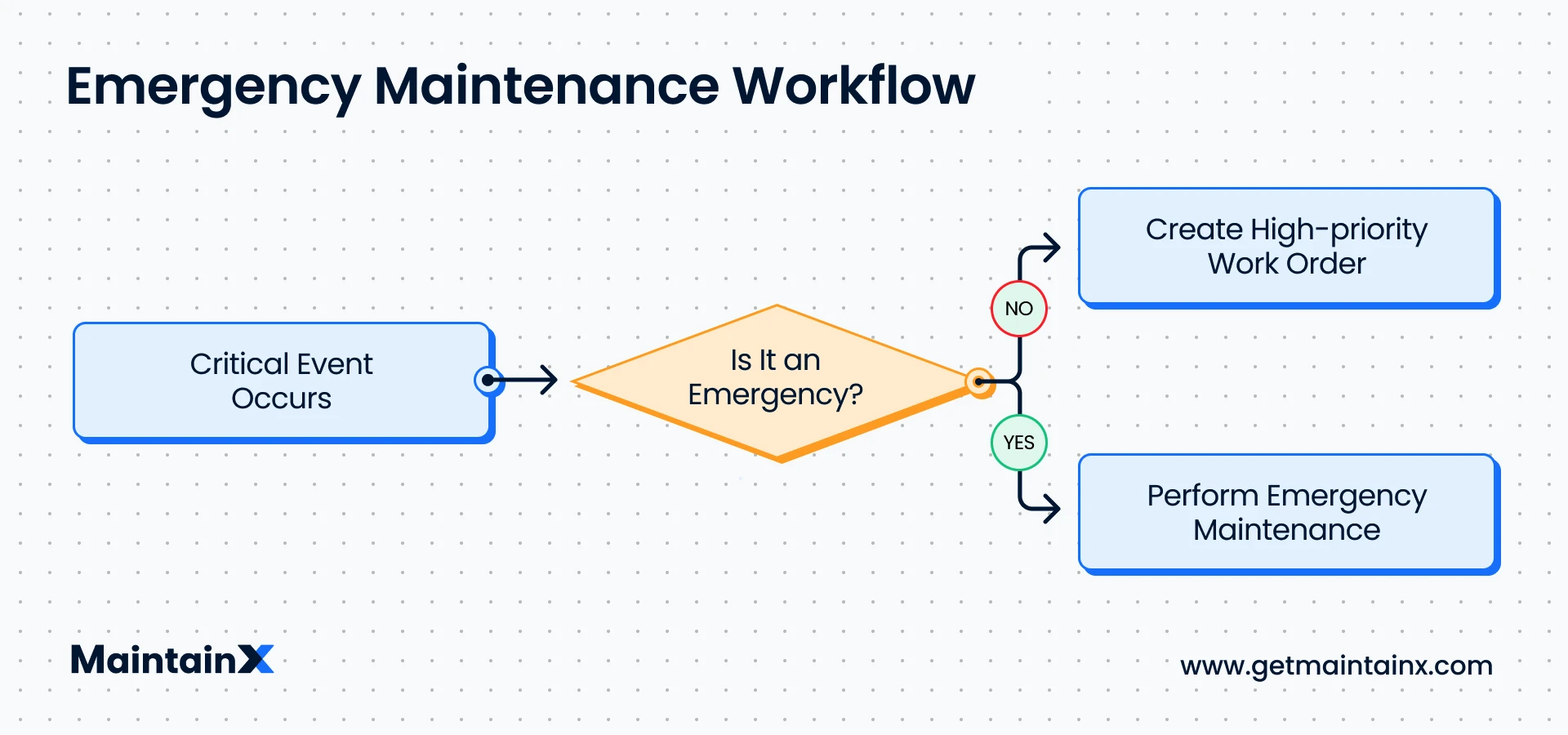
Preventive Maintenance (PM)
Preventive maintenance involves a plan to perform maintenance on building assets that are still working. It is cost-effective and prevents unplanned failures of critical assets, such as broken elevators, water coolers, and overhead lighting. For example, replacing a dirty AC filter with staff labor is considerably less expensive than replacing the entire AC unit when it breaks down because your maintenance team did not regularly replace the filters.
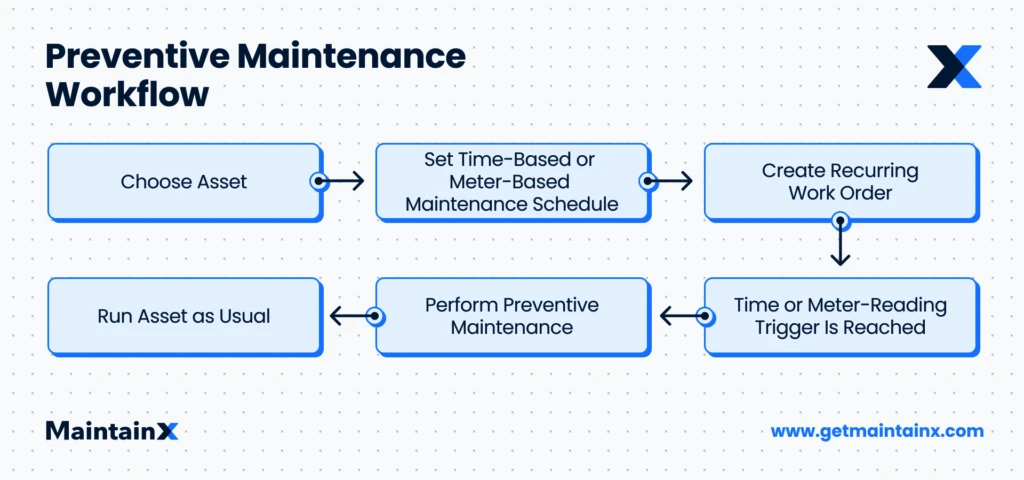
Preventive maintenance is a type of planned maintenance. For example, think about janitorial and cleaning services like disinfecting surfaces and cleaning bathrooms. Or weekly landscaping and general facilities maintenance like indoor window washing and deep cleaning carpets in trafficked areas. Or monthly maintenance, like checking fire alarms, cleaning gutters, scheduling pest control services, and using commercial cleaning services to clean vents and wash outside windows.
Preventive maintenance also allows building managers to monitor energy efficiency and management, negotiate better pricing on non-emergency maintenance, such as janitorial services, and keep a good eye on general building upkeep.
Balancing Reactive Maintenance vs. Preventive Maintenance
The goal of building maintenance is to achieve an optimal balance between RM and PM. Preventive maintenance seeks to reduce the frequency and cost associated with reactive repairs by regularly completing low-cost tasks that don’t take much time. For example, $10 repairs on leaky toilets can save you a boatload of money on your next water bill. Unfortunately, maintenance departments often perform costly and time-consuming repairs because building owners have not followed a preventive maintenance plan.
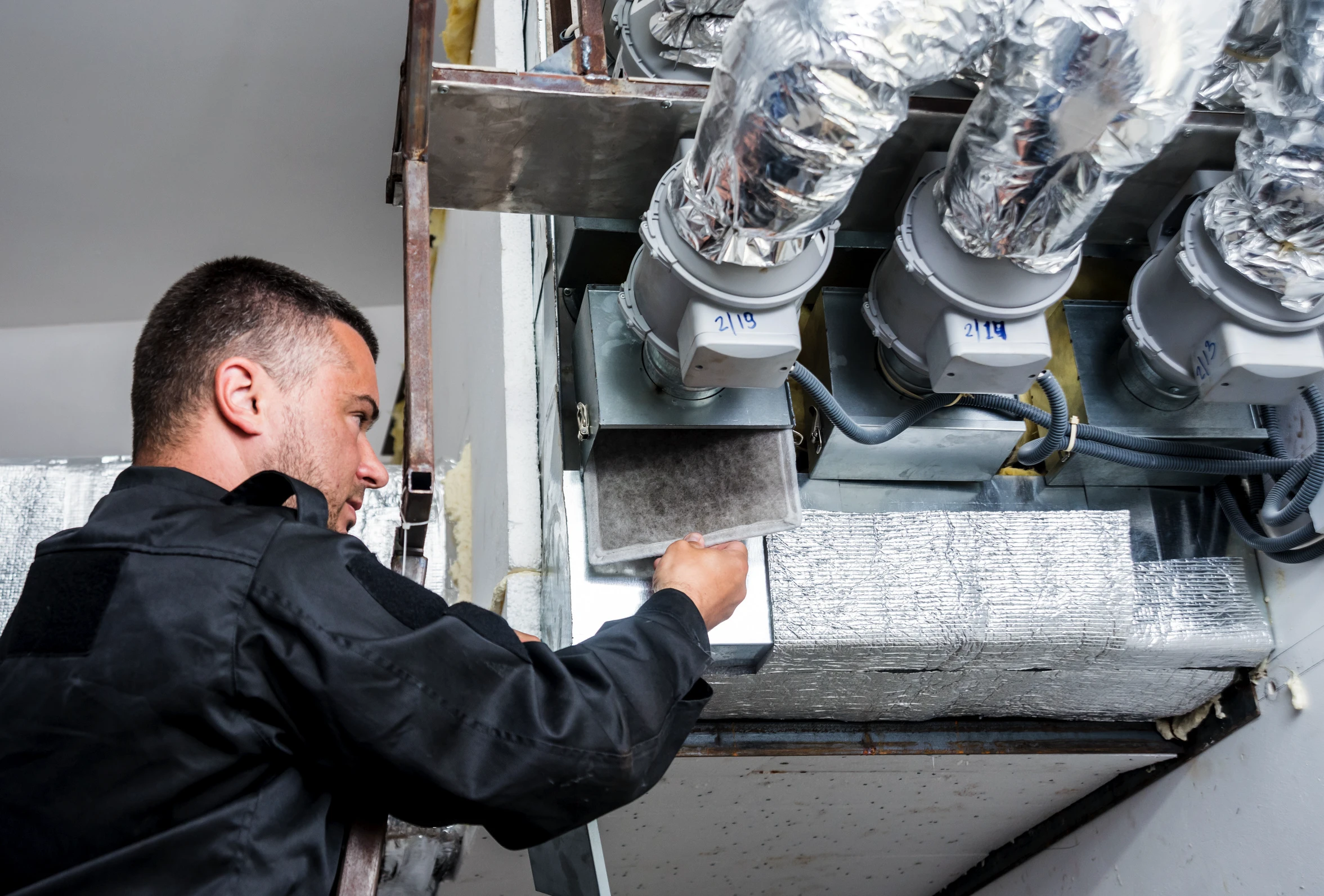
4 Simple Steps to Creating a Preventive Building Maintenance Plan
1. Inventory Your Building’s Assets
You need to decide what equipment to include in your preventive maintenance program. A thorough walkthrough and review of your building’s floor plans will help you log all necessary assets and areas. In addition to common areas, don’t forget to log what you don’t see: electrical systems and HVAC systems, including air conditioning and ventilation, outside drainage, etc.
Record the following data for each building asset:
- Make and model
- Serial number
- Specifications and capabilities
- Unit number
- Category
- Location
- Primary users
- Parts
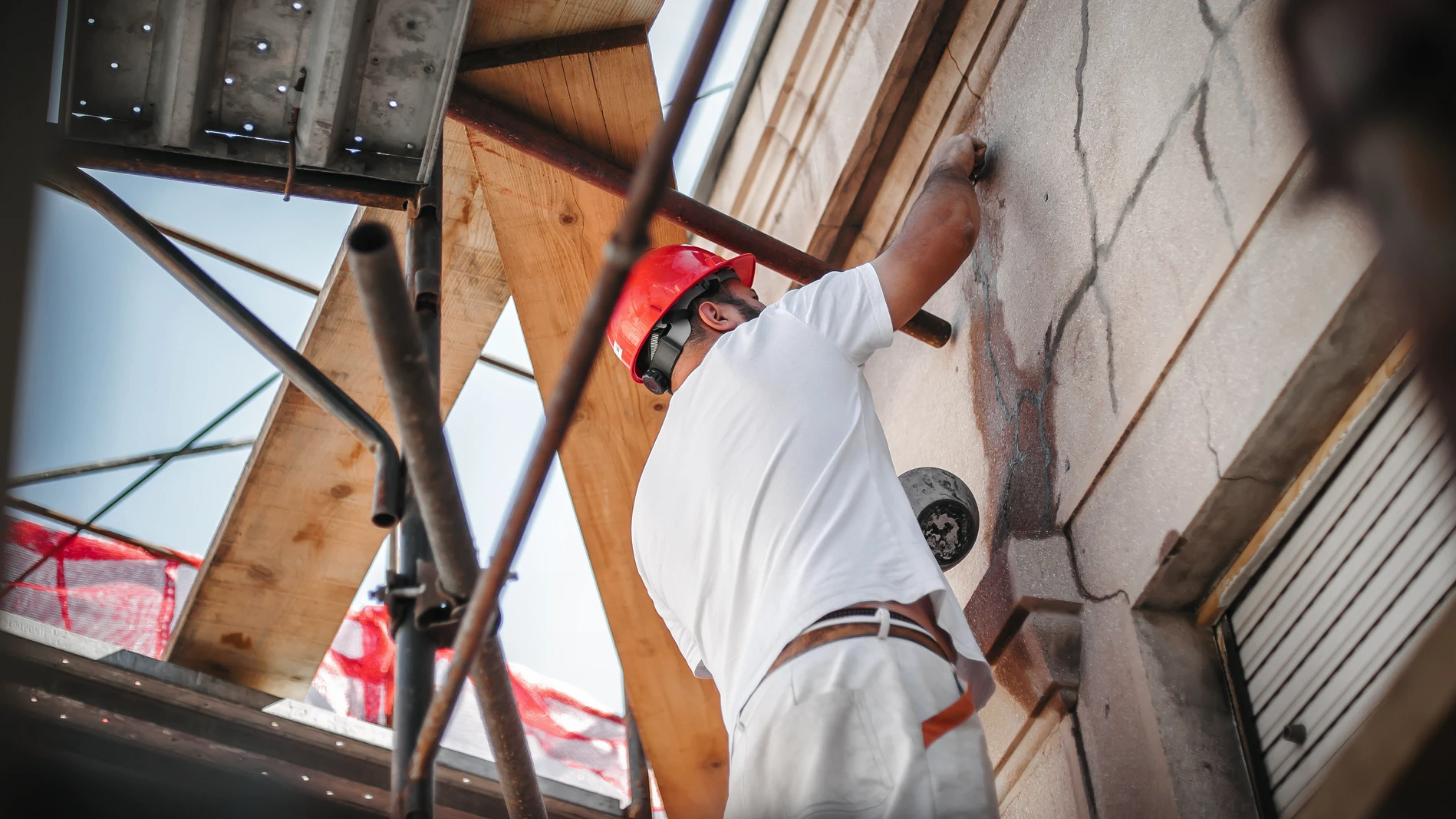
2. Establish Priorities and Maintenance Frequency
Priorities
One way to determine PM priorities is to conduct a criticality analysis. For building maintenance, the following questions will help get you started:
- What is the expected ROI of the equipment?
- Which inexpensive equipment can follow a run-to-failure model?
- What equipment is causing the most disruptions to your department?
By prioritizing the equipment that takes up most of your maintenance team’s time, you can reduce the most time-consuming tasks and find more time for PM work.
Maintenance Frequency
To determine the frequency of your PMs, refer to manufacturer guidelines, speak with experienced maintenance technicians, and review historical maintenance data.
When you need to service equipment after a certain number of hours, such as emergency generators, maintenance software like MaintainX is a game-changer. It will allow you to review past maintenance records to determine the hours an asset has been operating.
“Facility managers can no longer have a reactive maintenance posture . . . . They need to transition to what the industry calls moving from reactive to a ‘planned and preventive’ maintenance posture.”
Forbes
3. Create a Work Order System
A work order system is at the core of any modern maintenance schedule because all maintenance activities require a work order. The following work order process is how a proactive maintenance department would use work order software to organize its maintenance tasks.
Basic Work Order Process for Building Maintenance Plans
- Create Work Orders for All Tasks: To make the right decisions and avoid missed opportunities, create work orders for every task, from routine maintenance to inspections. Of course, you want to gather all the information you can. With historical data at your fingertips, you can easily make maintenance repair vs. replacement decisions and identify cost-saving opportunities.
- Prioritize: Consider how much time a maintenance task will take, where it fits with other priorities, and any operational considerations that could impact scheduling. For example, the maintenance activity may require a planned power outage or special equipment like a boom lift.
- Automate Work Orders for Recurring PMs: You can enter PM frequencies of different PM tasks right into your CMMS. The app will generate a perpetual calendar and automatically issue work orders to technicians on their cell phones and mobile devices the day before each scheduled job. Remember to add maintenance certifications, regulations, and inspections to the list.
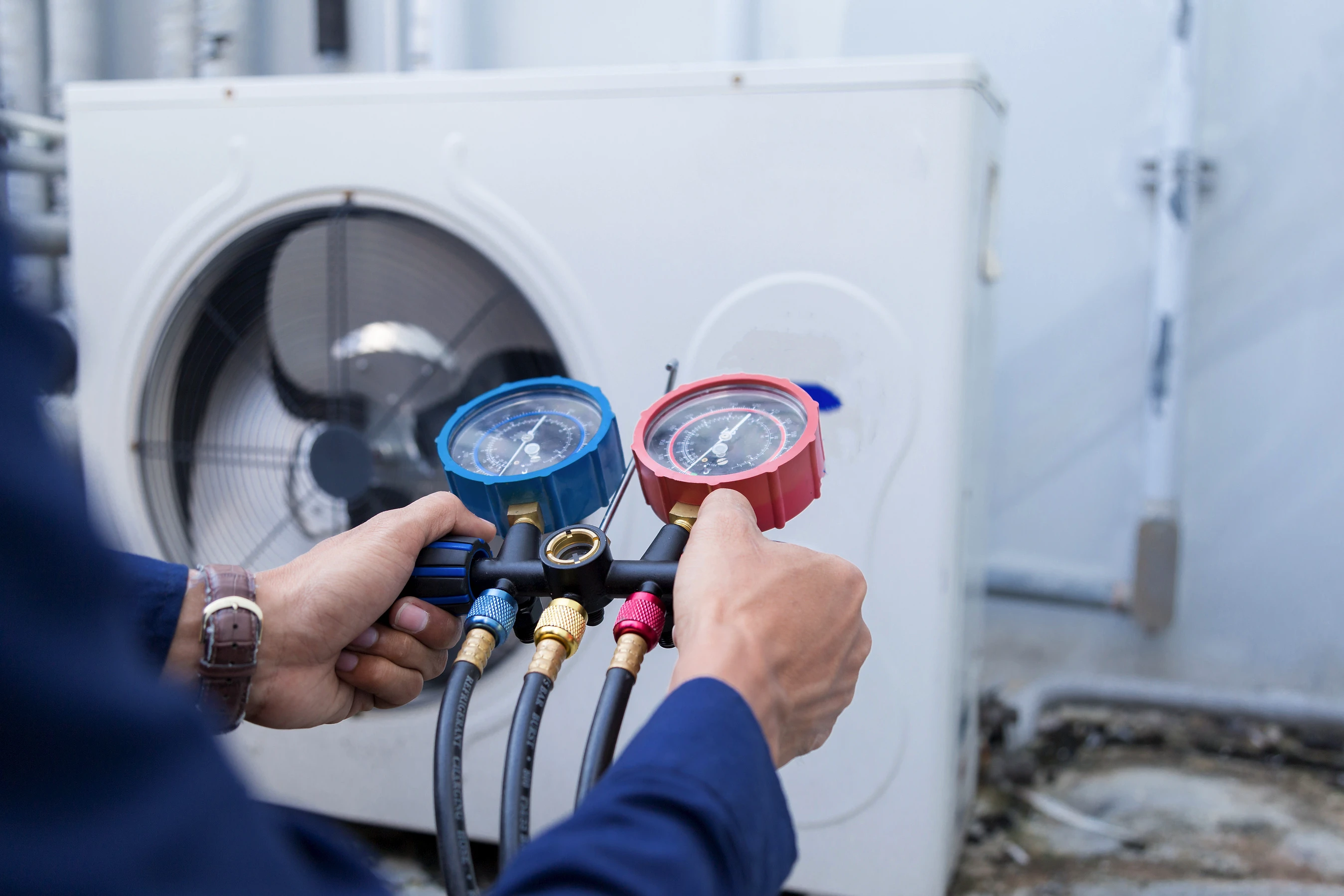
- Include SOPS and Additional PM Procedures on Work Orders: Standard Operating Procedure (SOP) templates help save time and reduce human error by providing a standardized way to follow procedures. You also can automatically include additional preventive maintenance procedures for each piece of equipment on work orders, along with instructions, manuals, and illustrations to help execute the task.
- Review then Repair: Building maintenance workers often want to review equipment and work order history in their CMMS before starting maintenance. This historical information helps technicians diagnose the issue, know where to start, and decide whether to repair or replace it. In addition, once a technician begins the maintenance activity, a mobile CMMS will allow them to check parts availability quickly.
Also, be sure that your maintenance supervisors and team members have the necessary maintenance training to handle the variety of tasks and the range of work orders, from reactive to preventive maintenance.
- Document and Close: When maintenance work is complete, the technician records the completion time. The technician can then upload photos of the repairs and close out the work order. A CMMS with real-time monitoring allows facility managers to monitor all open, in progress, and closed work orders with just one click.
Pro Tip: Frequently communicate with your staff and encourage them to keep one another informed. MaintainX is the only maintenance software in the marketplace that includes instant messaging and group chat functionality.
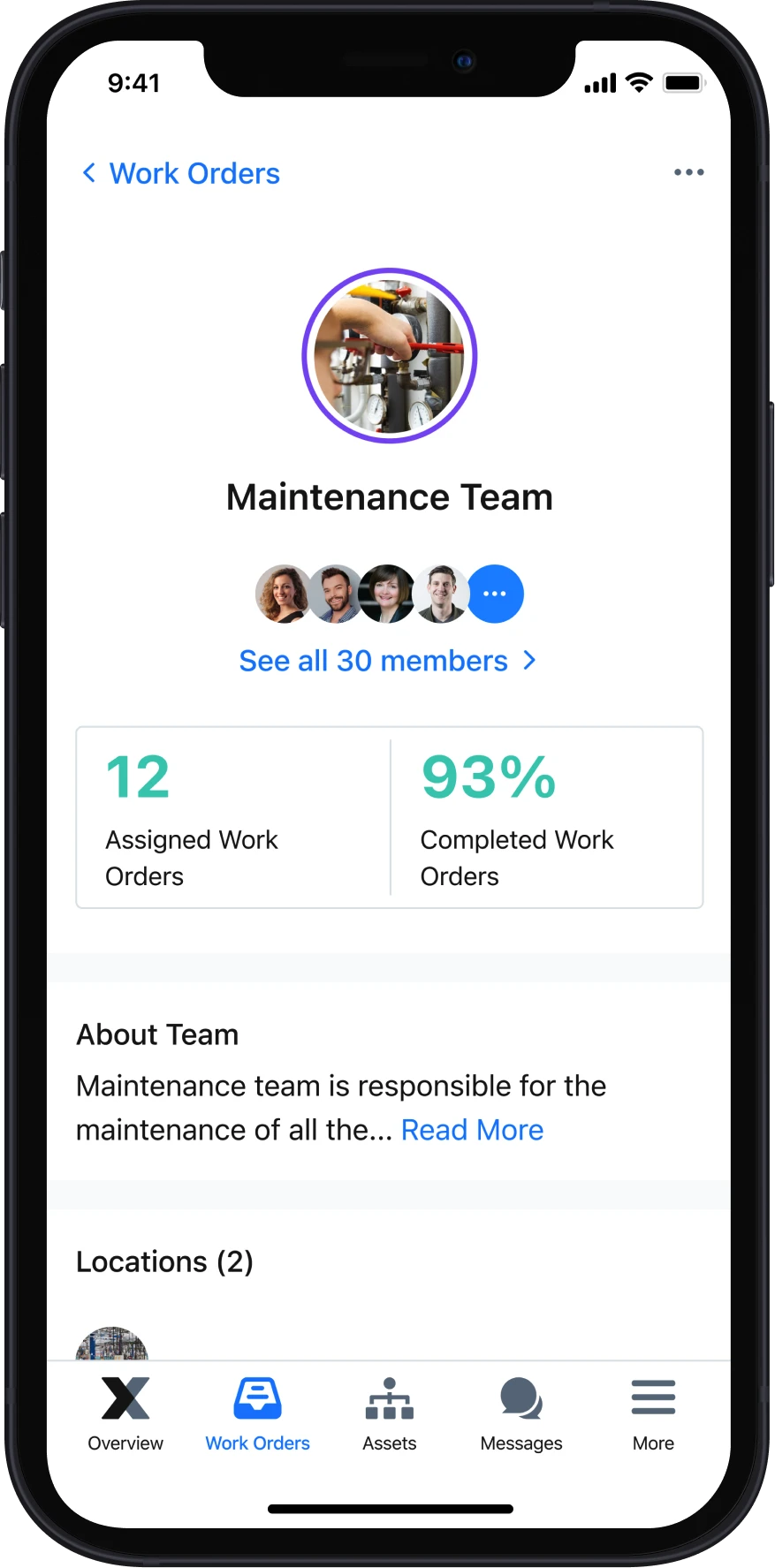
4. Monitor Progress and Adjust Accordingly
The best way to ensure you achieve your goals is to use a Computerized Maintenance Management System (CMMS) to create work orders and checklists, track maintenance progress, and provide data reports on key performance indicators (KPIs).
Your most useful KPIs will be:
Planned Maintenance Percentage (PMP)
PMP compares the number of planned maintenance tasks to the total number of completed tasks. PMP will help you identify opportunities to minimize reactive maintenance to optimize your planned and unplanned work ratio.
To calculate your PMP, divide your total hours spent on planned maintenance activities by your total number of hours spent on all maintenance activities within a given period. Then, multiply the number by 100 to get your PMP percentage.
PMP = (Total Hours of Planned Maintenance / Total Hours of ALL Maintenance) * 100
Mean Time Between Failure (MTBF)
MTBF is the average time between asset breakdowns. You don’t want to do too much or not enough PM. If an asset experiences continual failures, you may need to increase the frequency of PM tasks. Assets that have never experienced a breakdown may still operate without failures.
To calculate MTBF, divide the total uptime of a repairable asset by the number of failures of that asset within a given period to arrive at an hourly measurement.
MTBF = Total Uptime of Repairable Asset / Number of Failures of Asset within Given Time Period
Use a CMMS to Automate Your Building Maintenance Plan
MaintainX is a user-friendly app designed to simplify building systems maintenance. It has all the features you need to streamline your PM efforts and is as easy to use as Facebook.
FAQs
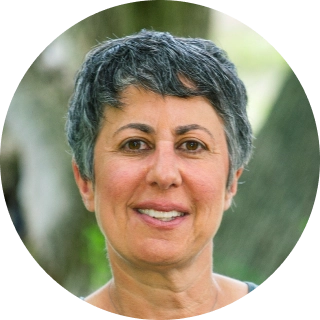
Caroline Eisner is a writer and editor with experience across the profit and nonprofit sectors, government, education, and financial organizations. She has held leadership positions in K16 institutions and has led large-scale digital projects, interactive websites, and a business writing consultancy.