The Japanese have achieved manufacturing excellence by doing simple things consistently well and continuing to improve themselves consistently. Japanese factories aren’t prototypes for a modern factory; they simply focus on basics like preventing machine overload and monitoring systems. They use the lean manufacturing methodology of Kaizen to minimize waste and maximize production.
Kaizen in Manufacturing
Kaizen can help companies become more productive, minimize defects, and encourage innovation. Implementing Kaizen in manufacturing focuses on eliminating waste and improving quality.
For example, CMMS systems with robust Reporting features, like MaintainX, are able to gather and analyze unplanned asset downtime. Once you’ve determined a cause, you can apply an appropriate solution to minimize reactive maintenance.
But what does Kaizen mean?
History of Kaizen
Kaizen comes from the Japanese words “kai” (meaning: change) and “zen” (meaning: good). It refers to focusing on small, continuous, and incremental improvements. The idea came into focus in the US during World War II, as the government enlisted experts to make war-effort industries more productive and efficient. The term was first coined by Toyota, which is why the Kaizen process is also popularly referred to as “the Toyota Way” of manufacturing.
Kaizen Principles
Kaizen relies on these principles to implement improvement:
1. Question old best practices
In the past, things were done a certain way because they worked. As times change, old best practices may need a revamp. Review old best practices to test them for relevance in the current environment.
2. Use data to track performance
If your changes improve a process or workflow, the data should reflect that. Don’t track performance arbitrarily—always look at what the numbers tell you to track the degree of improvement.
3. Be open to change
You often feel the urge to steer clear of change to avoid uncertainty. However, change is central to implementing Kaizen. Keep an open mind, look at a proposed change objectively, and implement the change if it promises improvement, no matter the small steps.
4. Ask for opinions
You would rely on an expert when solving an operational problem. However, you can also consider the opinions of others involved in the process. The more information you have, the closer you get to the truth, and the better position you’re in to come up with an effective solution.
"Kaizen can be a powerful tool for uncovering hidden wastes or waste-generating activities and eliminating them. Kaizen focuses on waste elimination activities that optimize existing processes and that can be accomplished quickly without significant capital investment. This creates a higher likelihood of quick, sustained results."
EPA
How to Implement Kaizen in Your Manufacturing Plant
Now that you know what Kaizen is, let’s talk about how to implement Kaizen on your shop floor. There are two ways to implement Kaizen:
- Daily Kaizen
- Kaizen events
Daily Kaizen
Daily Kaizen is Kaizen in its most authentic form. Workers, supervisors, and managers are encouraged to continually analyze workflows and processes to identify places to improve, such as production lines and supply-chain routes. Any suggested improvements, no matter how small, are encouraged.
The changes you make, however small, may also indirectly influence other parts of the workflow.
Kaizen Events
Kaizen events are brainstorming sessions aimed at improving an existing process. These events are often part of more extensive, long-term program development.
Kaizen events revolve around workers and managers following these steps:
- Looking for places to improve processes and become more efficient
- Brainstorming strategies to improve these processes
- Implementing solutions and quantifying the improvements
- Repeating these steps in a cycle of continual improvement
Kaizen events run for three to five days. They tend to require significant investments of employee time. However, they can help find improvements that daily Kaizen activities can miss.
Examples of Kaizen
Large corporations have relied on the Kaizen philosophy to improve their manufacturing processes. A few examples to inspire you:
Lockheed Martin
Lockheed Martin is an American corporation involved in aerospace, defense, and technology, among other things. It began implementing Kaizen in the 1990s and was incredibly successful:
- Reduced the time required to move parts between receiving and stocking from 30 days to just 4 hours.
- Reduced manufacturing costs by 38% between 1992 and 1997.
- Reduced inventory by 50% and cut delivery time by roughly 50%, from 42 to 21.5 months.
Ford Motor Company
Alan Mulally, an advocate of Lean manufacturing, took over as the CEO of Ford back in 2006, when Ford was on the brink of bankruptcy.
Many were unimpressed by Mulally’s strategy to turn Ford around—his strategy was simply to improve Ford’s efficiency.
Nine years later, Mulally had taken a nearly failed automotive company and made it one of the leading automotive innovators in the US.
How? Kaizen—improving efficiency, one day at a time.
Take the First Step
Getting started can feel daunting, but having the right tools goes a long way. With tools that collect and consolidate data, you’ll be able to identify those small changes that can add up to improved processes and increased maintenance and manufacturing efficiency.
For instance, if you notice that reactive machine maintenance takes too much time, try to identify the reason for the breakdown or the pattern in which it occurs.
Get a CMMS to Integrate Kaizen into Manufacturing
For example, MaintainX Reporting analyzes unplanned asset downtime. Once you’ve determined a cause, apply an appropriate solution to minimize reactive maintenance.
To begin implementing Kaizen to improve maintenance workflows, try MaintainX to digitize your preventive maintenance, standard operating procedures, and key performance indicators.
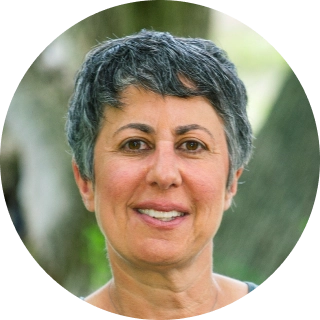
Caroline Eisner
Caroline Eisner is a writer and editor with experience across the profit and nonprofit sectors, government, education, and financial organizations. She has held leadership positions in K16 institutions and has led large-scale digital projects, interactive websites, and a business writing consultancy.
See MaintainX in action