Industrial maintenance is an investment that keeps facilities on track. When machinery breaks down, it’s more than inconvenient—it’s costly. On average, every hour of unplanned downtime costs a facility around $25,000, with larger organizations seeing losses beyond $500,000 per hour. Industrial maintenance professionals step in to save the day—reducing breakdowns, optimizing efficiency, and keeping operations at full speed. They’re the backbones, working behind the scenes to protect both productivity and the bottom line.
Here, we’ll break down the key aspects of industrial maintenance, from job roles and tasks to the best practices for success. Whether you're looking to streamline your maintenance strategies or are considering a career in this field, you'll find actionable insights here on how MaintainX can help you improve your operations and maximize equipment lifespan.
What is industrial maintenance?
Industrial maintenance refers to strategies and practices used to ensure that machinery, equipment, and internal systems in industrial settings operate smoothly and efficiently. By employing preventive, predictive, and reactive maintenance techniques, professionals can reduce unplanned downtime and extend equipment lifespans. This is critical to maintaining operational efficiency in industries like manufacturing, energy production, and construction.
Industrial maintenance today
Modern industrial maintenance encompasses processes intended to minimize asset breakdowns, increase uptime, and improve overall plant reliability. It ensures all plant assets are in good working condition. For this reason, industrial maintenance is sometimes referred to as plant maintenance. Industrial settings that practice this category of maintenance include food processing plants, manufacturing facilities, electricity plants, and more.
Organizations that require industrial maintenance
Any business relying on heavy machinery benefits from industrial maintenance to keep operations smooth and efficient. The following industries, in particular, depend heavily on regular maintenance to maximize uptime and prevent costly downtime:
- Manufacturing: Electronics factories, furniture manufacturers, paint suppliers, or other organizations producing goods for consumers or businesses.
- Food processing: Plants preparing food and beverages, like SanTan Brewing Co.
- Construction: Companies that construct infrastructure or buildings, such as offices, housing, malls, hotels, and hospitals.
- Automobile: Auto parts manufacturers or assembly plants, like Magna International.
- Aviation: Aircraft manufacturers or assembly plants.
- Electricity production: Fossil-fuel or hydroelectric power stations, nuclear power plants, wind turbines, like South East Power.
Industrial facilities always have maintenance staff on board and typically work in teams. Additionally, companies will sometimes hire contractors for specific complex maintenance tasks.
Examples of industrial maintenance & repair tasks
Examples of specific industrial maintenance tasks include:
- Changing lubricants on equipment with rotating parts.
- Detecting and fixing issues in hydraulic or pneumatic systems.
- Doing maintenance work on boilers, heat exchangers, and tanks.
- Assessing complex issues in the case of a breakdown and repairing equipment to minimize downtime.
- Performing mechanical and electrical repairs.
- Troubleshooting equipment that doesn’t perform as expected.
- Inspecting equipment for signs of wear and tear.
- Escalating equipment issues to maintenance supervisors.
- Scheduling future maintenance tasks.
- Managing inventory—spare parts, tools, and materials—for future maintenance work.
Overall, industrial maintenance tasks are varied and complex, requiring a high level of adaptability. Let’s look at additional important skills maintenance workers should have.
Careers in industrial maintenance
Industrial maintenance offers a wide range of rewarding career paths if you enjoy solving problems and working with complex machinery. From hands-on technicians to strategic management roles, industrial maintenance professionals are essential to keeping everything running smoothly in every sector. Let's explore some common job roles in this field and the key skills you need to succeed.
Common industrial maintenance jobs
Industrial maintenance offers a variety of roles, each with its own responsibilities and areas of expertise. Some of the most common jobs in this field include:
Maintenance Manager
Maintenance managers oversee day-to-day maintenance operations and report to upper management. They develop strategic maintenance programs, coordinate scheduling, manage budgets, and ensure compliance with safety regulations and company policies.
Maintenance Supervisor
Maintenance supervisors directly oversee technicians' work and ensure they follow maintenance schedules. They also track key performance indicators (KPIs), such as mean time to repair (MTTR) and schedule compliance, to assess team performance and efficiency.
Maintenance Planner
Maintenance planners ensure technicians have the tools, resources, and parts needed to complete work orders. They also help schedule maintenance tasks and align them with production goals.
Maintenance Mechanic
Maintenance mechanics specialize in troubleshooting, repairing, and maintaining complex industrial machinery. They often perform preventive maintenance and emergency repairs to keep operations running smoothly.
Industrial Engineer
Industrial engineers design efficient systems for maintaining and repairing equipment. While they don’t typically perform hands-on maintenance tasks, they play a critical role in improving processes and developing strategies to minimize downtime.
Key skills for industrial maintenance personnel
Industrial maintenance workers need a broad skill set to manage the variety of tasks required to keep machinery and equipment running efficiently. These skills are critical for anyone looking to build a successful career in industrial maintenance:
Problem-solving
Maintenance work involves identifying and fixing issues. Maintenance employees must be able to identify the best operational solution in the shortest possible time and perform well under pressure. Downtime can be incredibly stressful!
Attention to detail
Technicians should possess a keen eye for detail. This trait is crucial when installing, repairing, and maintaining heavy machinery. An eye for detail is needed to follow manufacturers’ guidelines and standard operating procedures (SOPs) with a high level of precision.
Adaptability
Different pieces of equipment require different maintenance strategies. Maintenance workers must be able to adapt quickly from one SOP to the next. Additionally, SOPs and best practices often change over time, meaning workers must be open to continually improving their skills and knowledge.
Communication skills
Most industrial maintenance work is done in a team setting. Strong communication skills are therefore essential for maintenance personnel. A good CMMS smartphone app with chat functionality can streamline communication within the team. In case of emergency maintenance, for example, it can help maintenance technicians coordinate their efforts without information falling through the cracks.
Physical strength and endurance
Finally, maintenance work is sometimes physically demanding. Technicians may engage in activities that require endurance, stamina, and strength. Common physically demanding maintenance tasks include carrying and assembling heavy machine parts, climbing tall ladders, and working in unusually hot or cold temperatures.
5 strategies used in industrial maintenance
Industries that rely heavily on industrial maintenance include manufacturing, construction, mining, oil and gas, electricity, and automotive. Businesses within these sectors rely on hundreds of expensive, critical pieces of equipment to fulfill customer expectations.
For this reason, running a strategic maintenance program is paramount to sustainable success. A solid plant maintenance plan helps optimize upkeep costs, maximize uptime potential, and increase long-term profitability.
Essentially, industrial maintenance revolves around proactively remedying maintenance issues so important assets won’t fail unexpectedly. Most industrial facilities use a combination of maintenance strategies to meet these goals, including:
Preventive maintenance (PM)
Preventive maintenance involves a proactive approach to equipment upkeep. It requires routine servicing to prevent future failures.
Plant managers schedule periodic maintenance based on machine usage, time-based recommendations, and equipment history. A common example of PM is changing an automobile’s engine oil every 5,000 miles or three months.
Reactive maintenance
Reactive maintenance refers to tasks performed after equipment failure has already occurred. Generally, reactive maintenance assignments fall into two categories: run-to-failure maintenance and emergency maintenance.
Though it may sound odd, plants often allow certain assets to break down before doing maintenance on them. Managers most likely won’t schedule noncritical, inexpensive, and easily replaceable assets for preventative maintenance. For example, run-to-failure maintenance is the ideal maintenance strategy for a light bulb.
Reliability-centered maintenance (RCM)
Reliability-centered maintenance is a proactive maintenance framework that incorporates several techniques to increase uptime, reduce excess spending, and increase efficiency. The process aims to match each asset with the maintenance technique most likely to generate cost-effective uptime. That means both reactive maintenance and preventive maintenance are included in reliability-centered maintenance programs.
An increasingly essential aspect of RCM is predictive maintenance (PdM). PdM technologies like vibration analysis, sound-level measurements, and oil analysis help inform maintenance planning. RCM practitioners can also assess the consequences of equipment failure using exercises like failure modes and effects analysis (FMEA), fault tree analysis (FTA), and more.
Condition-based maintenance (CBM)
Condition-based maintenance is another advanced maintenance framework for performing maintenance based on real-time equipment data. Plant managers monitor moment-to-moment asset conditions using sensor devices designed to detect impending breakdowns.
Similar to RCM, the goal of CBM is to optimize maintenance spending without sacrificing efficiency. A typical application of CBM is to monitor pressure readings on piping systems. For example, food and beverage manufacturers often rely on real-time diagnostics to ensure unexpected pipe bursts never disrupt production lines.
Predictive maintenance (PdM)
Predictive maintenance is a data-driven approach to asset upkeep that aims to prevent failures before they occur. By using real-time data from equipment sensors, such as vibration analysis, temperature readings, and sound-level measurements, predictive maintenance enables teams to identify potential issues early. Common PdM techniques also include oil analysis and infrared thermography, which help maintenance managers plan repairs with precision, minimizing operational disruptions.
Predictive maintenance aims to anticipate equipment failures before they occur, allowing maintenance staff to stay ahead of failures and eliminate unplanned downtime. This method lets teams schedule repairs only when necessary, reducing unnecessary downtime and improving asset reliability.
Industrial maintenance best practices
Effective industrial maintenance is all about staying proactive, organized, and ahead of potential issues. By implementing proven strategies, like preventive and condition-based maintenance, you can extend the life of your equipment. In turn, this helps minimize downtime and improve overall efficiency. Whether you're a manager or technician, following these best practices will help streamline your maintenance processes and keep your facility running like a well-oiled machine.
Use meters for condition monitoring
Condition monitoring involves using sensors, meters, and diagnostic tools to track machinery's performance in real-time. For example, if vibration sensors on a pump detect unusual fluctuations, this could be an early warning sign of misalignment or bearing wear. Promptly aligning or replacing the bearing can prevent the pump from failing entirely, which would lead to significant downtime and costly repairs. By catching these small issues early, maintenance teams can schedule necessary repairs with minimal disruption to operations, preventing unplanned downtime.
Report on and analyze asset health over time
Consistent monitoring and reporting on asset health is key to optimizing equipment performance. By generating regular reports and analyzing historical data, you can identify trends that indicate wear and tear or declining performance. A good example would be a machine's energy consumption gradually increasing over time. This might signal the need for an inspection or the replacement of an electrical part. This information helps maintenance teams make informed decisions and prioritize repairs that extend the life of equipment. Analyzing asset health trends helps stay ahead of breakdowns and minimize long-term maintenance costs.
Provide documentation to ensure safety & compliance
Accurate documentation is essential for maintaining safety standards and complying with industry regulations. By keeping thorough records of maintenance activities, inspections, and repairs, your team can be sure that the equipment is safe to operate and meets regulatory requirements. For instance, documenting routine safety checks on industrial equipment helps prevent accidents by ensuring the equipment runs safely. It also provides proof of compliance during audits. Proper documentation can also identify recurring issues and avoid potential penalties for non-compliance.
Implement preventive maintenance schedules to reduce downtime
Planned preventive maintenance is one of the most effective ways to avoid costly equipment failures. By regularly servicing machines, maintenance teams can extend the lifespan of assets and prevent unexpected downtime. For instance, routine oil changes and filter replacements on vehicles ensure that they remain in top condition. A well-planned preventive maintenance schedule helps prioritize tasks, reduces the chance of emergency repairs, and keeps operations running smoothly without disruption.
Maintain an asset inventory management system
Keeping an accurate asset inventory helps streamline maintenance operations and prevent disruptions. An asset inventory management system does this by helping maintenance teams track the location, condition, and life cycle of critical equipment and parts. For example, a manufacturing plant receives an alert when a production component is running low, letting them know to order replacements in advance. This reduces the risk of production delays due to unavailable stock. Maintaining an up-to-date inventory can help your team improve operational efficiency by making sure they have what they need when they need it.
Enable real-time communication between your maintenance techs and managers
Communication tools, like those available through a computerized maintenance management system (CMMS), keep technicians and managers connected wherever they are. For example, a technician can update a work order from the field to inform the manager of a repair’s status, while the manager can adjust schedules or prioritize tasks as needed. This approach helps minimize downtime by enabling quick responses to changes, preventing delays, and ensuring teams remain in sync.
Use a CMMS for Industrial Maintenance
Maintaining efficiency in today’s fast-paced industrial environment requires more than just traditional maintenance. A CMMS like MaintainX offers a powerful solution to streamline industrial maintenance operations by centralizing maintenance activities, tracking asset performance, and automating routine tasks.
With MaintainX, maintenance managers can easily schedule work orders, track asset health metrics, and ensure timely maintenance with our mobile platform. Our system supports preventive, reactive, and predictive maintenance strategies, allowing you to tailor maintenance based on your specific needs.
For example, use MaintainX to:
- Monitor asset health in real-time and receive alerts when performance drops.
- Automate work order generation based on maintenance schedules or real-time data.
- Track inventory levels and receive notifications when parts or supplies are running low.
- Generate detailed reports on maintenance activities, asset performance, and labor efficiency.
Whether you manage a manufacturing plant, food processing facility, or energy production site, MaintainX empowers your maintenance teams with the tools they need to improve efficiency, reduce costs, and keep everything running. With the convenience of mobile access, your teams can stay connected and in control, no matter where they are.
Ready to check MaintainX out? Book a tour today.
Maintenance FAQs:
What it takes to become an industrial maintenance professional varies from industry to industry. However, most organizations hire for a broad range of skills.
Don’t worry—you don’t need to familiarize yourself with every type of industrial asset–only the critical mechanical systems most frequently relied upon. Plants don’t expect their maintenance workers to know everything about every asset.
Companies frequently outsource certain work orders to third-party contractors. Below are answers to common questions regarding how to become an industrial maintenance professional and what the work entails.
Industrial maintenance workers need a diverse skill set to excel in their roles. Candidates need a solid understanding of electrical and mechanical systems, along with hands-on experience in industrial maintenance technology. A background in mechanical engineering or a related field is also valuable. Familiarity with OSHA regulations is essential for maintaining workplace safety. Additionally, the job demands physical strength for working with heavy equipment, strong troubleshooting skills for addressing mechanical issues, and proficiency in using computers for reporting and record-keeping. Communication and time management skills are equally important to coordinate effectively with teams and ensure the timely completion of tasks.
To qualify as an industrial maintenance engineer, candidates typically need a bachelor’s degree in industrial engineering, mechanical engineering, or a related field. Practical experience in maintaining and repairing industrial equipment is also valuable. Candidates often gain this experience through internships or entry-level positions. Engineers must be skilled in analyzing equipment performance, developing maintenance strategies, and improving the operational efficiency of a variety of equipment. Familiarity with industry standards and safety regulations is also crucial. Additionally, strong problem-solving abilities, proficiency in using maintenance management software, and good communication skills are necessary for coordinating with maintenance staff and management.
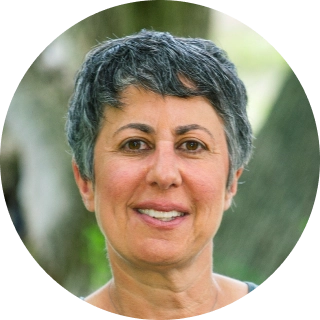
Caroline Eisner
Caroline Eisner is a writer and editor with experience across the profit and nonprofit sectors, government, education, and financial organizations. She has held leadership positions in K16 institutions and has led large-scale digital projects, interactive websites, and a business writing consultancy.
See MaintainX in action