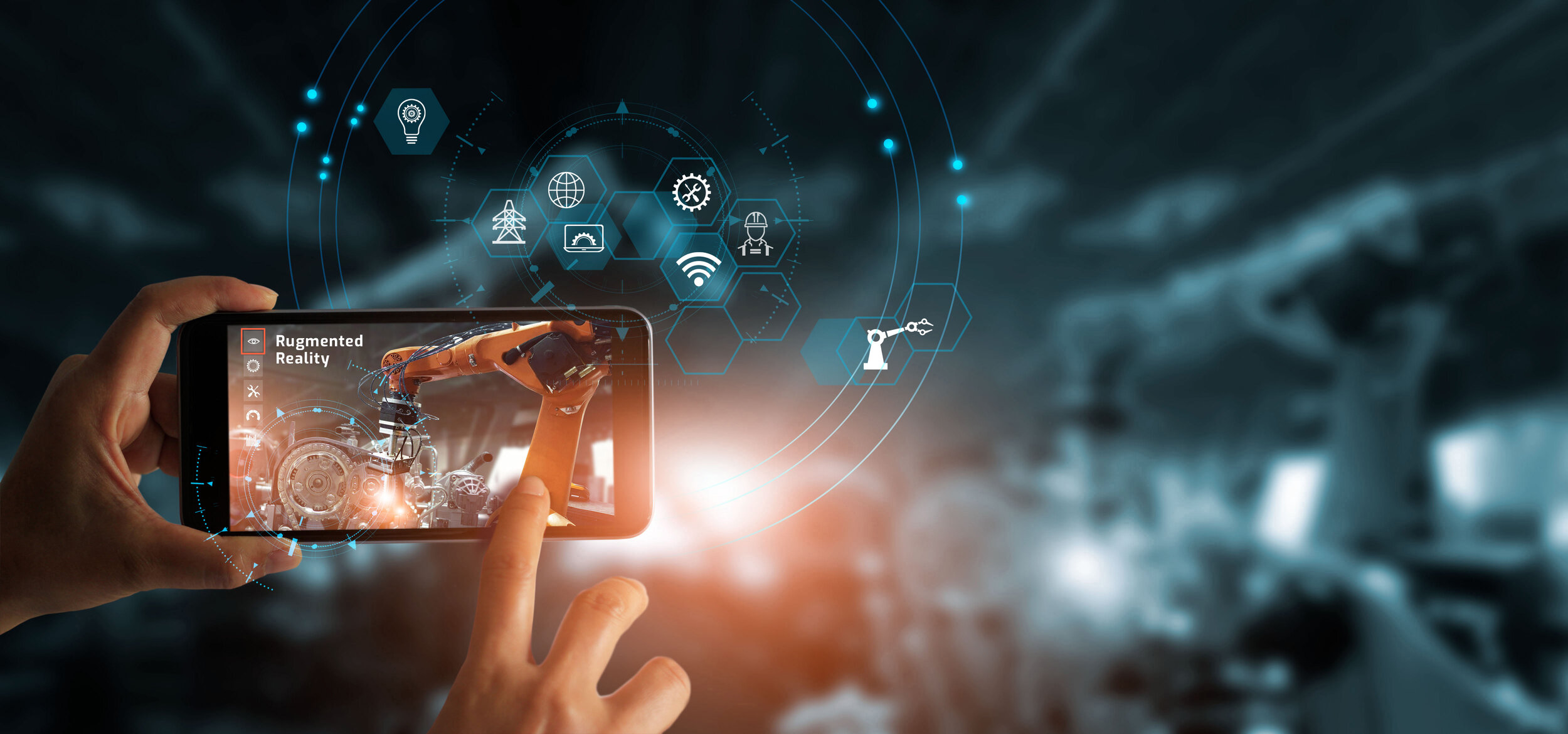
Have you ever wondered who developed the first “official” standard operating procedure (SOP)? You may be surprised to learn the rail industry initially created SOPs to prevent train accidents.
Since then, organizations around the world have adopted SOPs to streamline business processes. The manufacturing, healthcare, property management, and military industries most frequently use them today. However, even small businesses benefit from documenting procedures. Implemented SOPs impact product and service quality, employee safety, and organizational success.
In recent years, several top-performing companies have begun digitizing their SOPs. Why? Because it saves time, increases efficiency, and ensures compliance. This article will reveal how digital SOPs can help automate business processes. We’ll also provide some quick tips for getting started. Here’s a primer on the types of SOPs to begin
What Are SOPs?
Standard Operating Procedures (SOPs) refer to documented, step-by-step instructions for completing given business processes. Operational managers assign workers SOPs to improve workflow efficiency, ensure consistent business performance, and increase regulatory compliance. These documents make it easier for employees to execute routine tasks without error. SOPs are sometimes categorized into two groups: technical and management SOPs.
Technical SOPs outline how workers should complete a given task. They sometimes also describe how to handle possible disruptions should they arise. Technical SOPs vary by department, asset, facility, and business function.
Management SOPs provide guidelines on how managers should develop technical SOPs. They outline who is responsible for reviewing, approving, implementing, and revising SOPs. Additionally, management SOPs summarize the process of auditing technical SOPs for accountability.
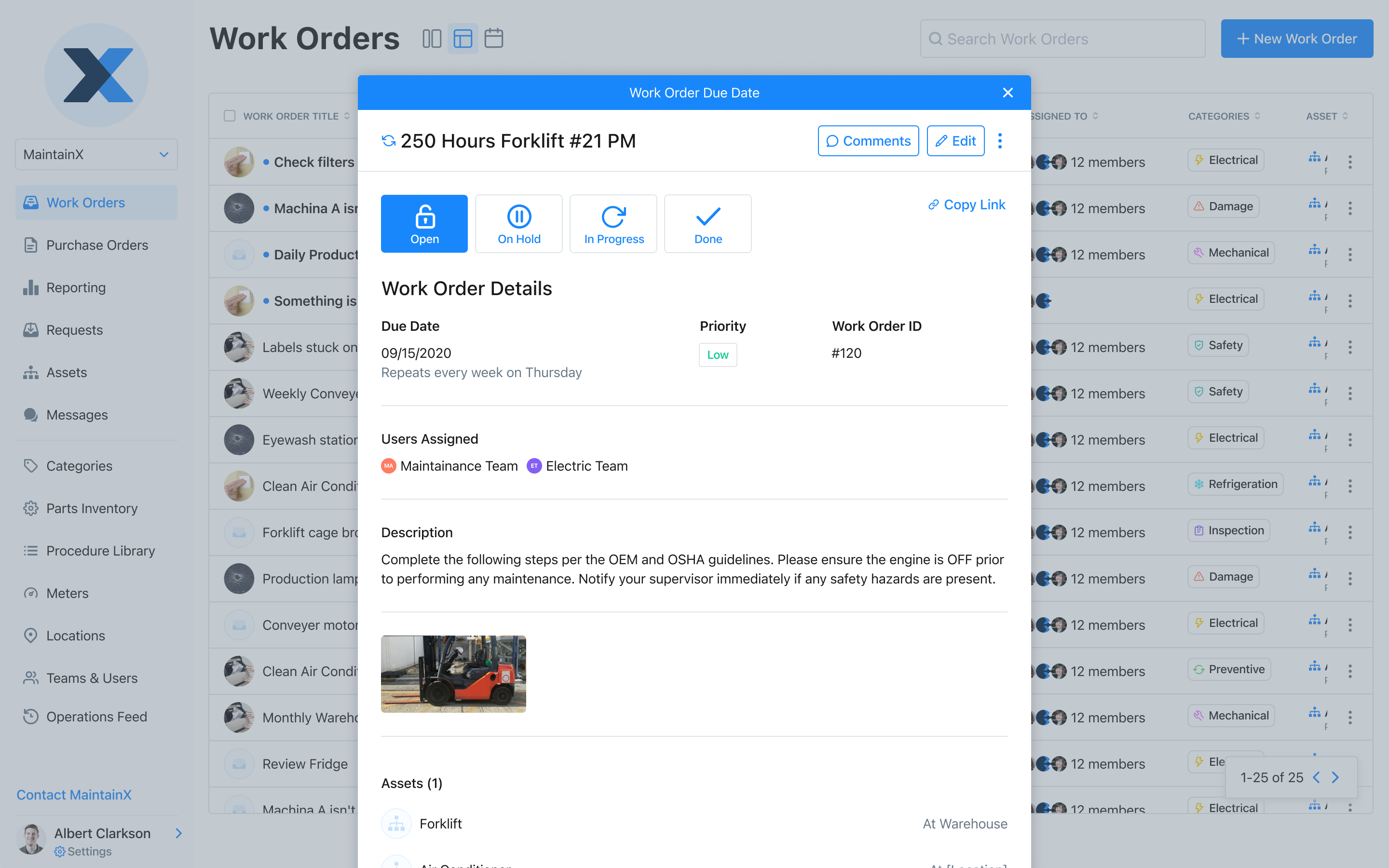
Paper SOPs vs. Digital SOPs
Organizations draft SOPs in both paper and digital formats. While paper SOPs are the most widely used at this time, their inconveniences outweigh their benefits.
Put simply, paper checklists aren’t convenient, economical, or environmentally friendly. It’s not unusual for managers to delay updating paper SOPs because of the time involved in editing, printing, and redistributing them to team members. Another disadvantage to staying analog? Paper procedures often become massive, clunky manuals neglected by busy employees.
According to the Food and Drug Administration, poor content and lack of clarity are some of the main reasons employees don’t properly execute tasks. Organizations that fail to create accessible and straightforward checklists are more likely to experience setbacks caused by human errors.
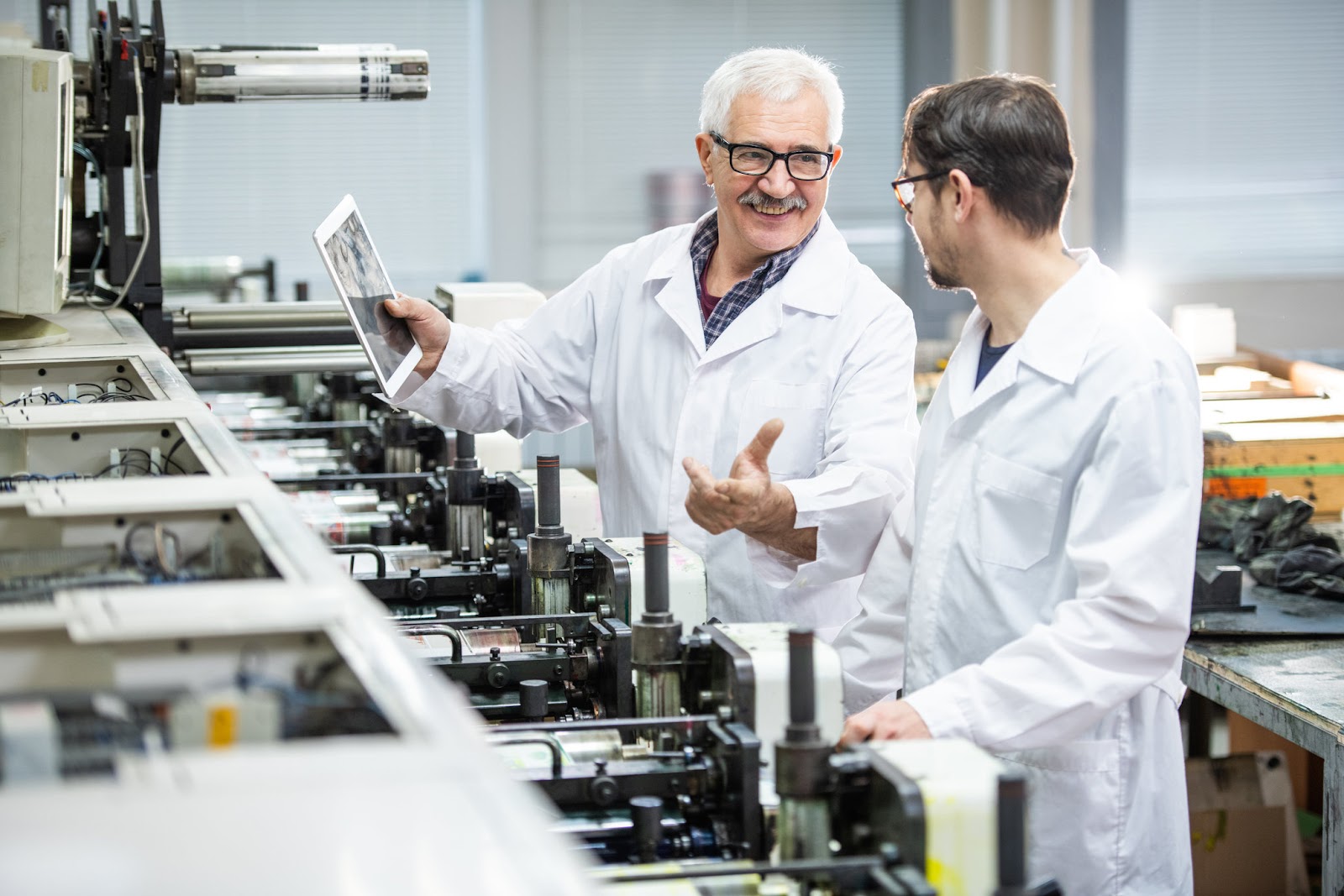
Digital implementation of SOPs solves these problems via:
Audit Trail Accessibility
One of the most significant advantages of digital SOPs is the audit trails they provide. Team leaders can quickly retrieve completed SOP assignments from the cloud. Such data is helpful when evaluating production issues, determining corrective actions, and cooperating with regulatory audits.
Worker Accessibility
Cloud-based software allows team members to access SOPs quickly. This instant availability via smartphone means employees don’t have to struggle to find specific procedures when needed. They also don’t have to wait on paper updates.
Enhanced Confidentiality
Large organizations often struggle to store large volumes of paper SOPs securely. No one wants proprietary processes leaked or stolen. Modern SOP software solves this problem by including security systems requiring authentication for access. It’s easier to prevent a data breach with digital SOPs.
Improved Managerial Oversight
Digital SOPs verify completed tasks for each employee. Software programs like MaintainX even allow workers to upload photographs of completed assignments. These features help management maintain a bird’s eye view.
Streamlined Onboarding
Employee turnover is inevitable. Digital SOPs simplify onboarding new employees, ensuring task continuity without significant disruptions. Managers can also create digital SOPs for new hires to take on standardized tasks.
Simplified Regulatory Compliance
Even small regulatory violations carry stiff non-compliance penalties. Digital SOPs record task completion and provide footprints to show regulatory compliance. For example, an eatery can prove an assigned employee checked its refrigerator temperature daily.
Remote Work Accessibility
Employees and managers can sign off digital SOPs in remote locations. This cuts down on the need to drive down to the office to check off a task. Besides that, managers can send updated versions of SOPs to employee smartphones in real time.
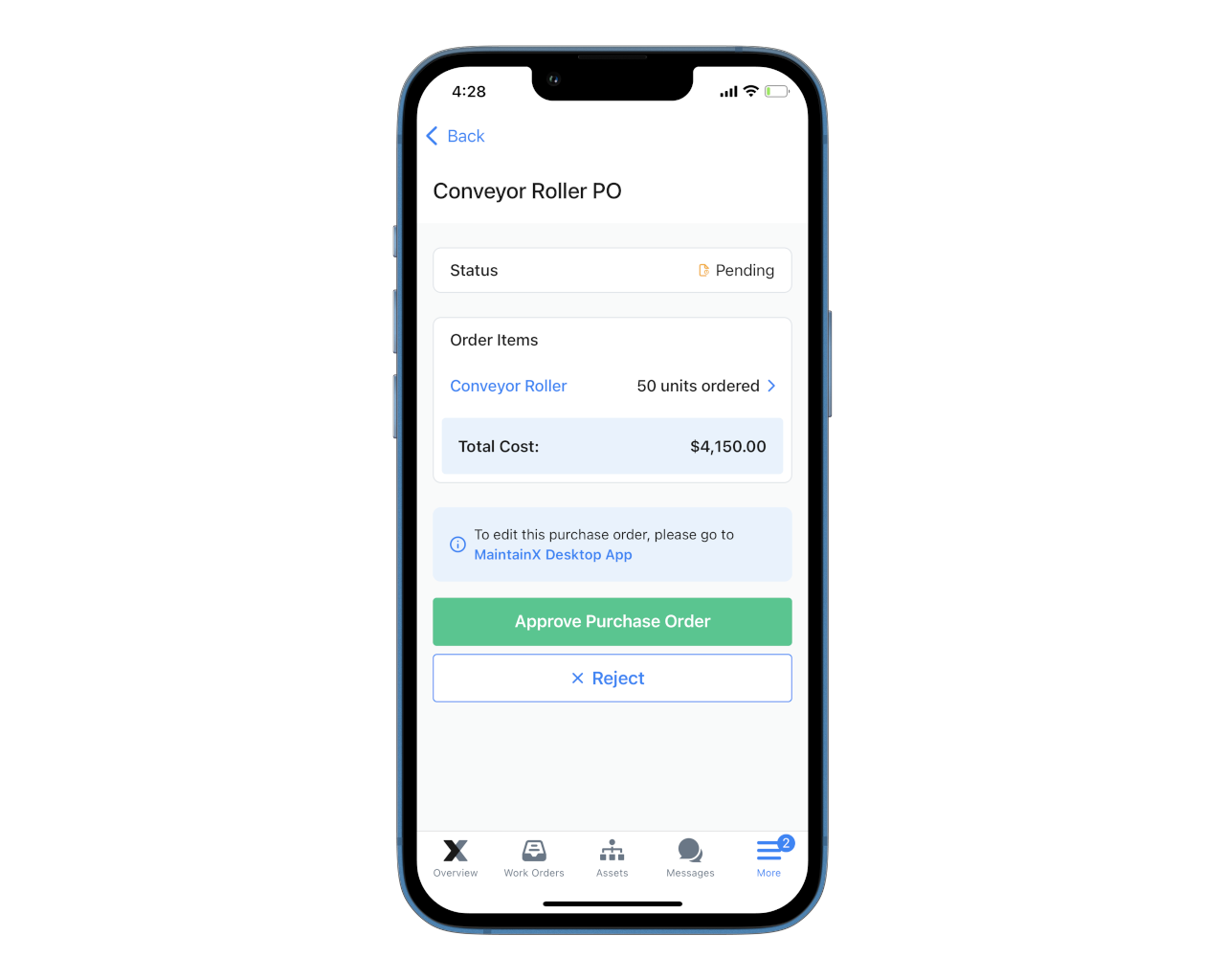
5 Tips to Automate Your Business with Digital SOPs
Evidence suggests organizations need to automate their processes to stay competitive. Automation and SOPs go hand in hand. Why?
Digital SOPs make it easy for employees to reference work instructions, policies, and checklists. Additionally, digitization allows managers to track SOP implementation, quality assurance, and maintenance efforts. Below are five tips to automate your business with SOPs:
1. Use CMMS for SOP Automation
A computerized maintenance management system (CMMS) is a software program for managing organizational assets and streamlining maintenance activities. CMMS helps track asset performance, quality assurance, and compliance audits. Its digital checklists can track processes and work orders to determine how to improve business processes.
While simple SOP software is available, it doesn’t provide the breadth of possibilities afforded by CMMS software. MaintainX is the world’s first CMMS software with instant messaging for desktop and mobile devices. It’s an excellent option for teams looking to combine safety checklists, quality control checklists, maintenance work orders, inventory control, and communication “under one roof.” The best part? Our basic plan is 100 percent free.
2. Automate Repetitive Tasks First
Not sure where to begin? Start by documenting your organization’s most repetitive tasks. Routine, manual tasks provide an easy opportunity for automation to free up time and resources. These tasks may include daily cleaning procedures, routine maintenance tasks, and worker opening/closing processes.
3. Outline Processes with Employee Input
Upon closer look, you may notice that most broad employee assignments contain small steps within them. For this reason, the employees who regularly perform specific procedures should plan out, develop, and write the first draft of the SOP. After all, they are the “subject-matter experts” (SMEs), most familiar with the procedures. The same employee who writes the SOP should then work through the written procedure to make any necessary changes. The writer may need to clarify the text and add graphics to increase clarity and ensure compliance.
Once the initial draft is complete, assign secondary employees and managers to review the SOP. Those familiar with the procedure may notice a missing or complicated step that can be broken into smaller ones. Once in final draft form, organizational leaders can review for quality assurance and make final changes.
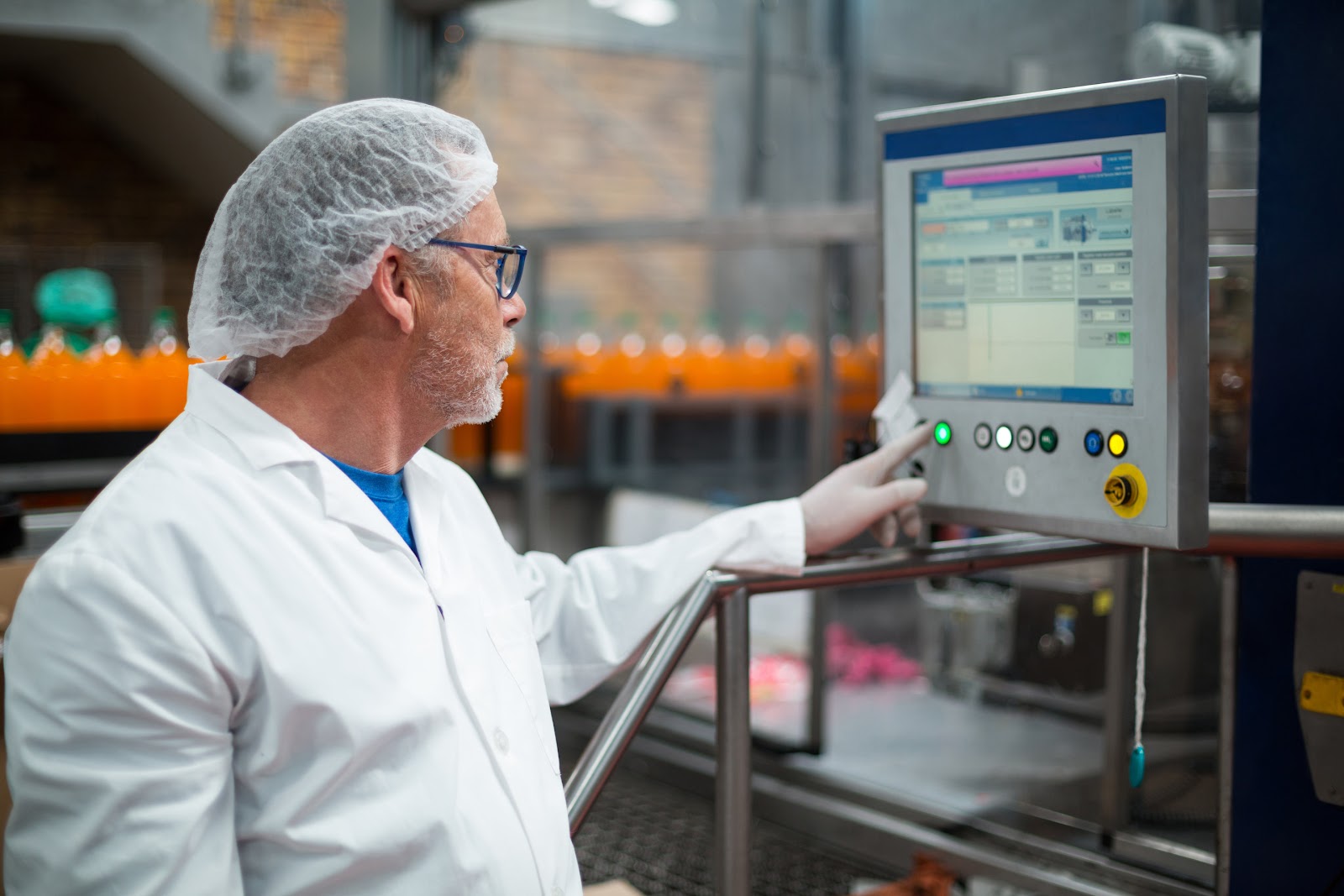
4. Create an SOP Labeling System
Regardless of an organization’s size, uncategorized information can easily fall into “the software black hole.” For example, say you run several McDonald’s franchise restaurants. You may choose to title each digital SOP with a store number followed by a department (e.g., 179-Supervisors). Establishing a consistent SOP-labeling system solves this problem. The organized format becomes a centralized point of reference for every member of the organization.
5. Keep It Simple
An SOP shouldn’t be complicated. The simpler it is, the more effective it will be. Write digital SOPs in simple, straightforward, and actionable language that everyone can understand.
Use consistent vocabulary and avoid lengthy paragraphs better suited as instructional attachments. Of course, long SOPs are sometimes inevitable. But don’t be afraid to create procedural attachments, diagrams, and flow charts for exceptionally complex steps.
Again, a good CMMS software platform will support hierarchical checklists, PDF attachments, and photo uploading to help organize complex SOPs. Finally, always check to make sure your SOP adheres to industry and governmental guidelines.
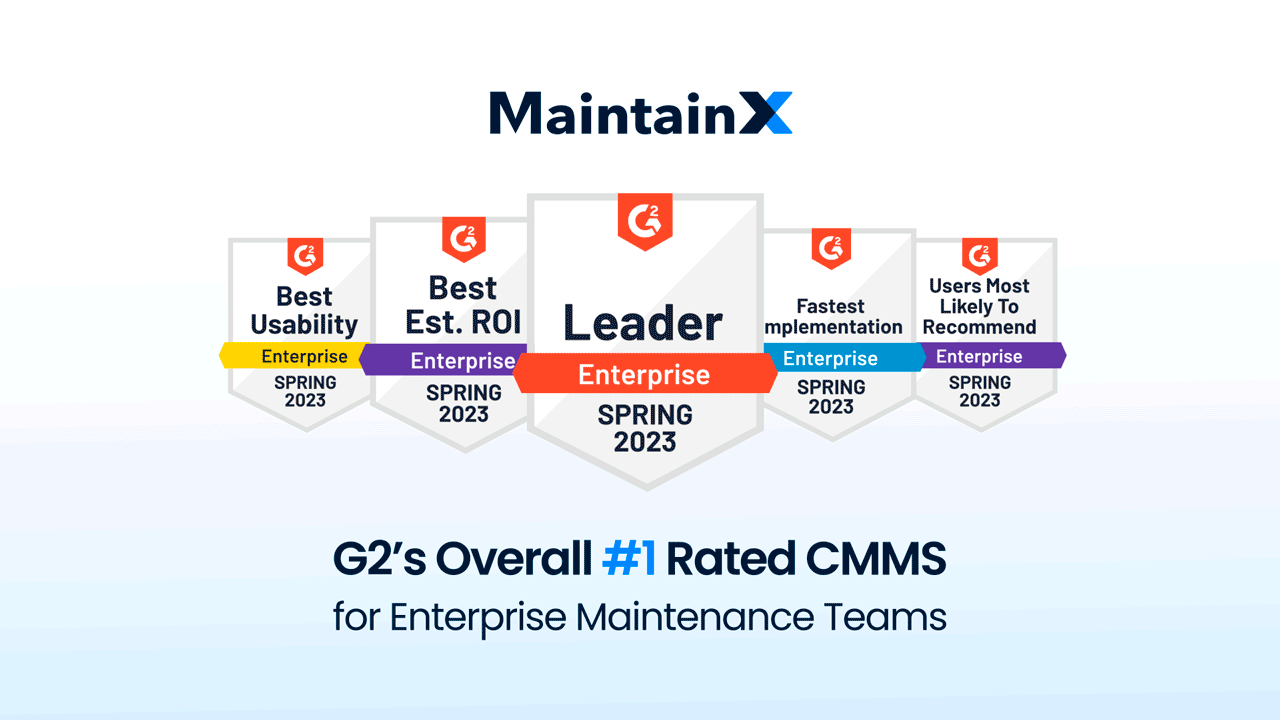
Go Digital with MaintainX
Digital SOPs make life easier for organizations of all types and sizes. They streamline processes, reduce operational costs, and provide real-time updates on task completion. Additionally, those supported by CMMS software provide in-depth analytics that support continuous improvement.
MaintainX’s CMMS platform handles maintenance, operations, safety, and training. We’re also the world’s first provider to include live chat, work order comments, and photo-sharing functionalities within the same digital maintenance platform.
MaintainX is free to download from the app store, and all Premium Features are free for 30 days. Our user-friendly platform includes everything you need to begin creating work orders, communicating with staff, and tracking assets today.
Ready to optimize your business process management system (and reduce downtime)?
FAQs
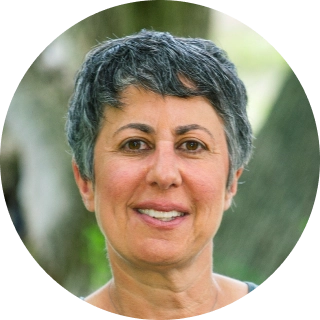
Caroline Eisner is a writer and editor with experience across the profit and nonprofit sectors, government, education, and financial organizations. She has held leadership positions in K16 institutions and has led large-scale digital projects, interactive websites, and a business writing consultancy.