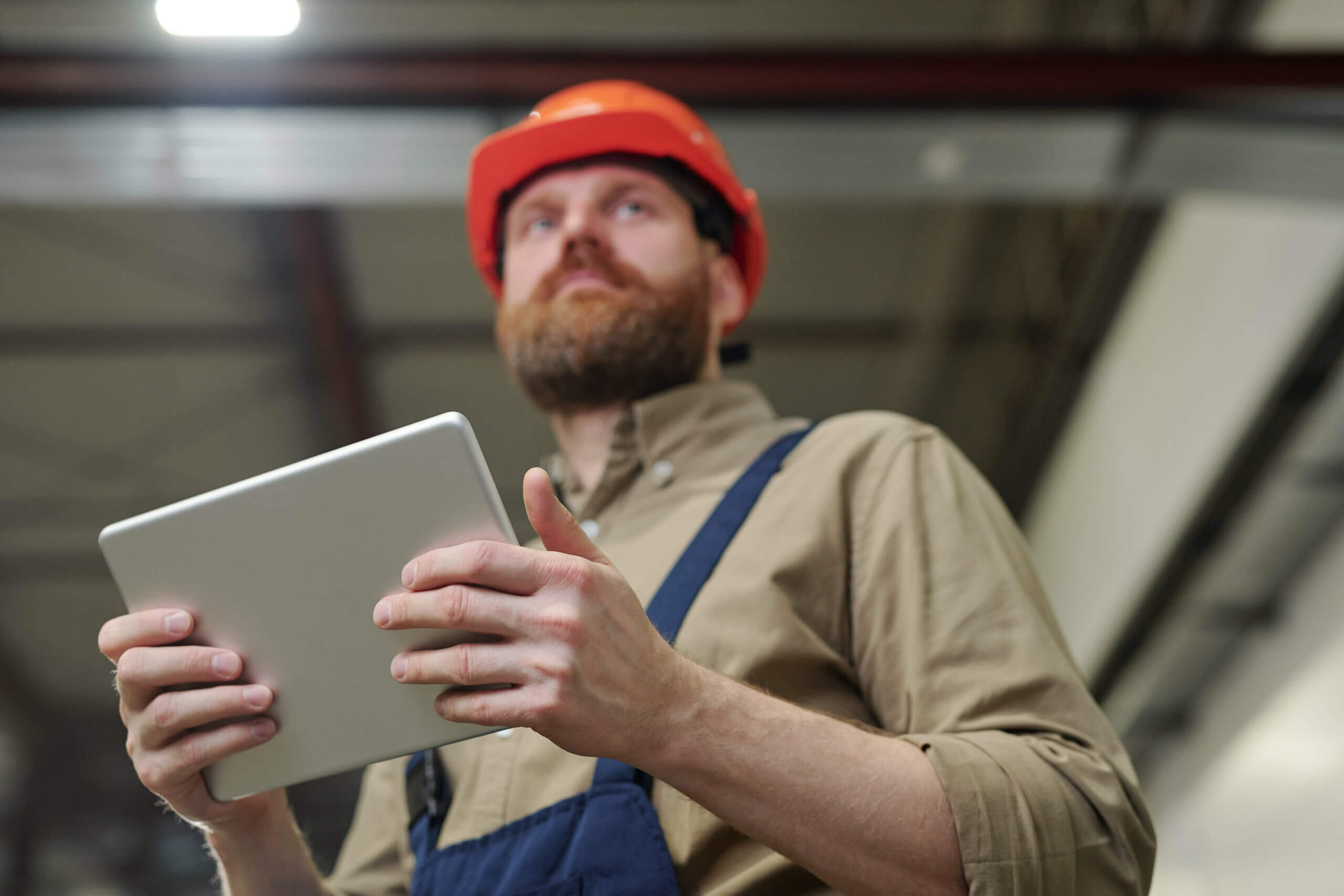
Have you ever wondered how global organizations, facilities, and manufacturers maintain consistency? The answer lies in standard operating procedures (SOPs). SOPs are clear, step-by-step guides that ensure tasks are completed correctly, efficiently, and in compliance with regulations, regardless of who's performing them.
SOPs reduce the risk of errors, accidents, and inconsistent results. And, these days, failure to use them can often negatively impact morale, productivity, and legal compliance. Whether you're a small business aiming for growth or a large organization seeking to streamline operations, SOPs are an essential ingredient for success.
In this blog post, we'll delve into the world of SOPs, explore their benefits, and equip you with the knowledge you need to write effective standard operating procedures people will actually use. Dive in and learn how SOPs can transform your organization!
What is a standard operating procedure (SOP)?
A standard operating procedure is a set of step-by-step instructions or guidelines that explain how to perform a specific task or activity. It’s like a recipe book: it helps people complete work correctly, consistently, and safely every time. A great standard operating procedure removes the guesswork necessary to complete the work at hand, whether in a lab, office, or factory floor.
Overall, the consistent use of SOPs creates a streamlined, cost-effective way to grow a business and its human capital, and lays a foundation for a rock-solid virtual culture for a distributed workforce.
Forbes
Quick SOP example
While the contents of standard operating procedures may vary substantially across industries, the process of managing, using, and updating SOPs is similar. Even though many organizations still use paper checklists, a growing number of companies are streamlining operations with digitized SOPs.
Considering that nearly every worker has a smartphone in their pocket, switching to digital templates is practical. Here's an example of what that looks like:
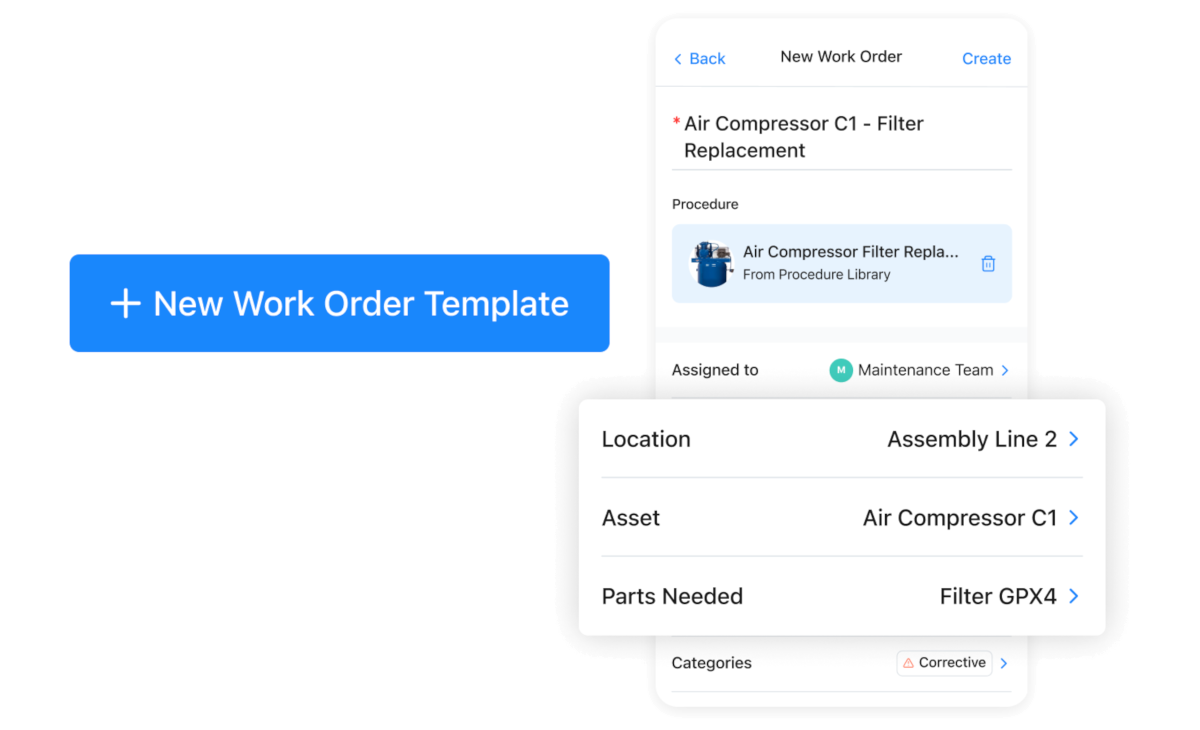
CMMS mobile apps allow operational managers to digitally assign recurring work orders with attached SOPs. Employees can complete checklists, take photographs of unexpected occurrences, and text managers from the convenience of their mobile devices.
The result is increased organizational transparency, compliance, and efficiency. Now let’s dive into some more benefits of using SOPs.
Benefits of standard operating procedures
Businesses of all sizes across all industries can benefit from standard operating procedures. SOPs help streamline business processes, improve employee safety, standardize quality control, maximize efficiencies, and minimize waste.
Without the appropriate procedures in place, companies risk employees performing tasks their own way, potentially compromising safety.
In addition, completed standard operating procedures:
- Prove compliance with organizational and regulatory requirements.
- Reduce miscommunication between employees.
- Detail vital safety instructions and standards.
- Provide checklists for auditing the effectiveness of maintenance plans.
- Streamline workflows and improve efficiencies by minimizing errors.
- Eliminate unproductive steps that decrease production efficiency.
- Serve as a reference to reconstruct operational systems in new settings.
- Improve quality, credibility, and legal defensibility of outputs.
- Track and measure organizational proficiency.
- Streamline onboarding and training of new employees.
- Boost accountability across organizational lines.
Need more reasons to start creating SOPs? Take a look at our post on the advantages of using standard operating procedures.
What should a good SOP include?
A standard operating procedure should include four key elements:
- Purpose: The SOP should clearly define the purpose of the work and its objectives. Describe the problems the SOP will solve, who the SOP is for, and where and how it will be used.
- Procedures: An SOP shouldn’t simply define the tasks that must be completed. It should also illustrate how to complete the tasks with detailed step-by-step guides, and descriptive visuals (where applicable).
- Resources: An SOP should identify and document the necessary resources or tools to complete the work. This could include equipment, software, or specific materials.
- Responsibilities: An SOP should outline who performs the tasks and who to contact if problems arise. It should also outline the person responsible for implementations, reviews, and updates the standard operating procedure.
Four most common SOP formats
While you might envision a single, static document when you hear "Standard Operating Procedure," SOPs are surprisingly diverse and adaptable. They can range from simple checklists to complex multimedia guides incorporating various explanatory tools. Let's explore the four most common SOP formats.
1. Simple checklists
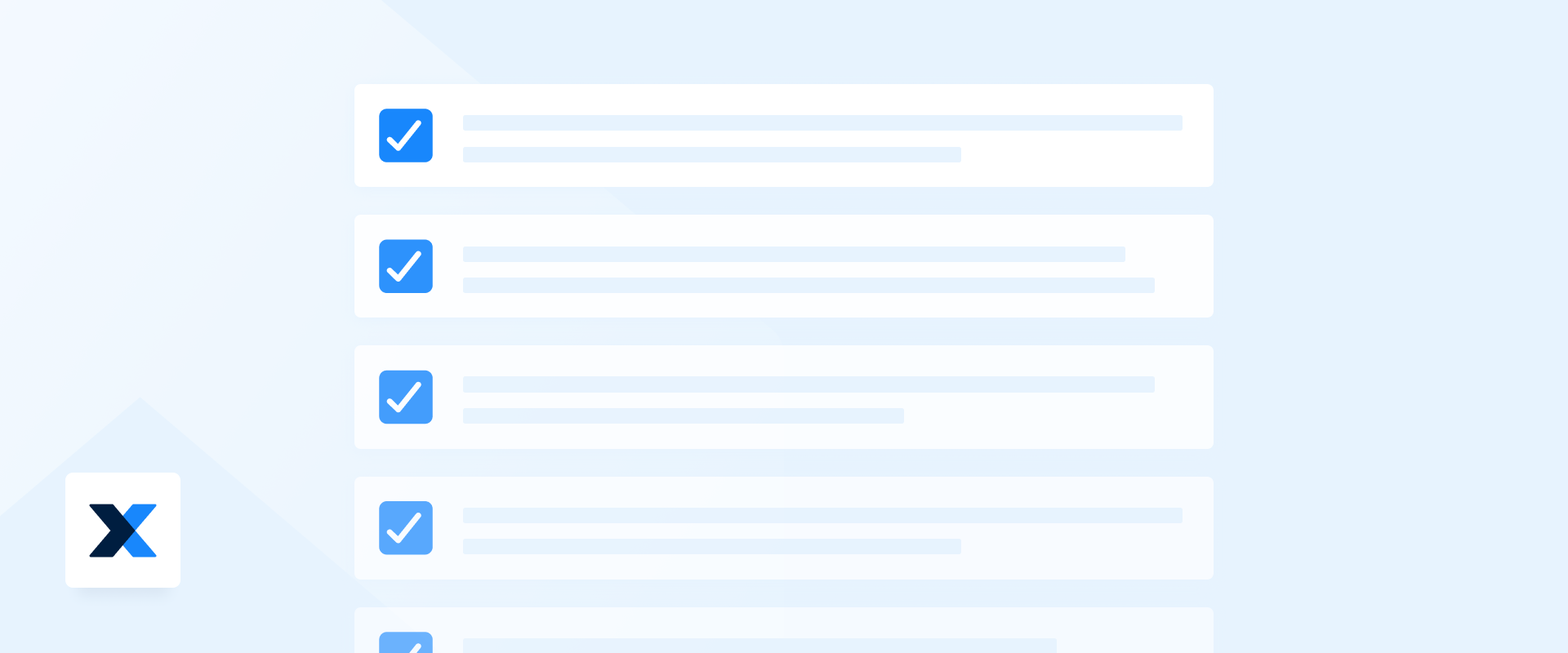
Best for procedures like:
- Clocking in and out
- Turning off factory floor lights
- Parking forklifts in assigned locations
Checklists are a simple and effective tool for creating standard operating procedures (SOPs). Their straightforward format, with clear steps listed in order, promotes clarity and ease of use for even the most complex tasks.
Their simplicity also makes them adaptable. You can easily modify and update checklists as procedures evolve or new information becomes available.
Whether you're onboarding a new employee or navigating a critical safety protocol, checklists provide a reliable and readily accessible guide.FYI: We have thousands of reusable SOP templates in our Global Procedure Library.
2. Step-by-step checklists
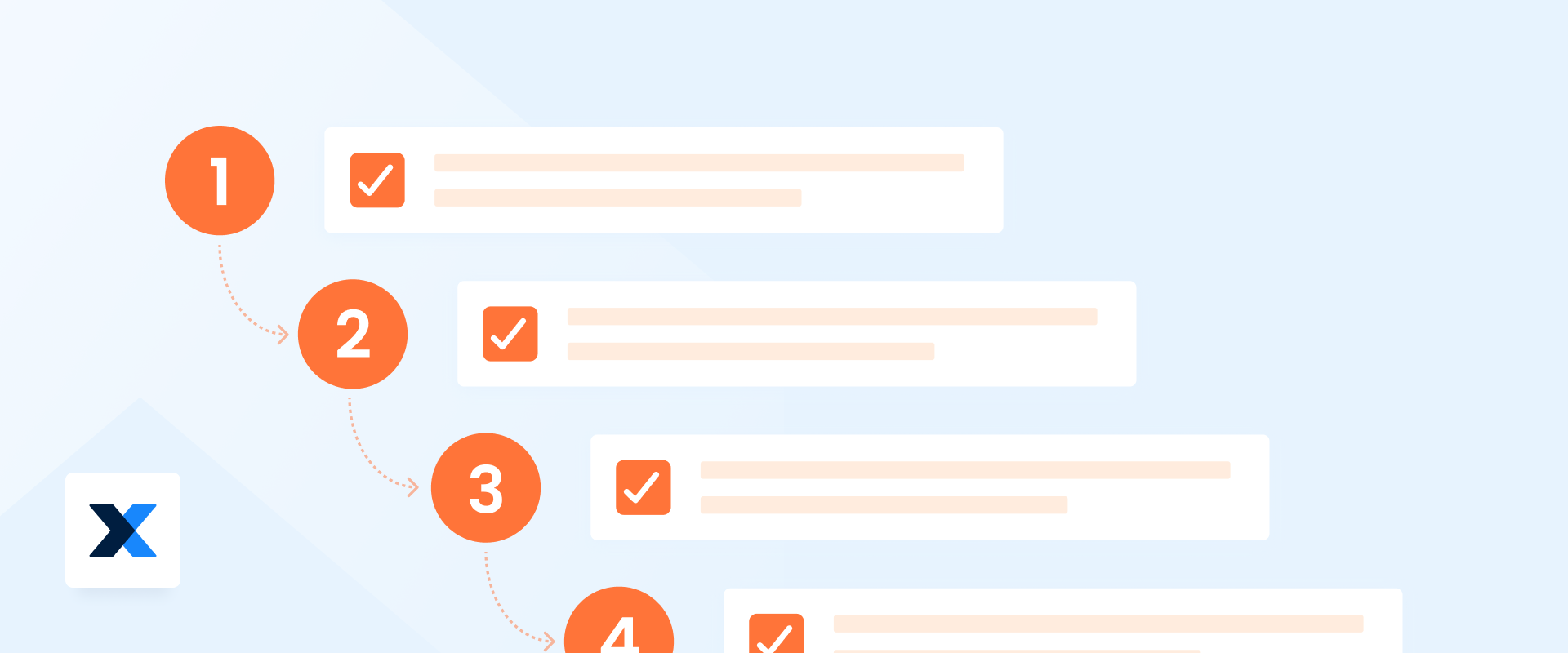
Best for procedures like:
- Daily equipment inspection
- Lubricating equipment
- Changing filters
Step-by-step checklists include bulleted or numbered lists that outline the steps necessary to complete processes. They are checklists without the built-in accountability of a checkbox.
Interestingly, this SOP format is best suited for straightforward tasks requiring little explanation or multiple sub-steps. Examples include setup and cleanup instructions, digital login sequences, and clear instructions for proper equipment use.
3. Hierarchical steps
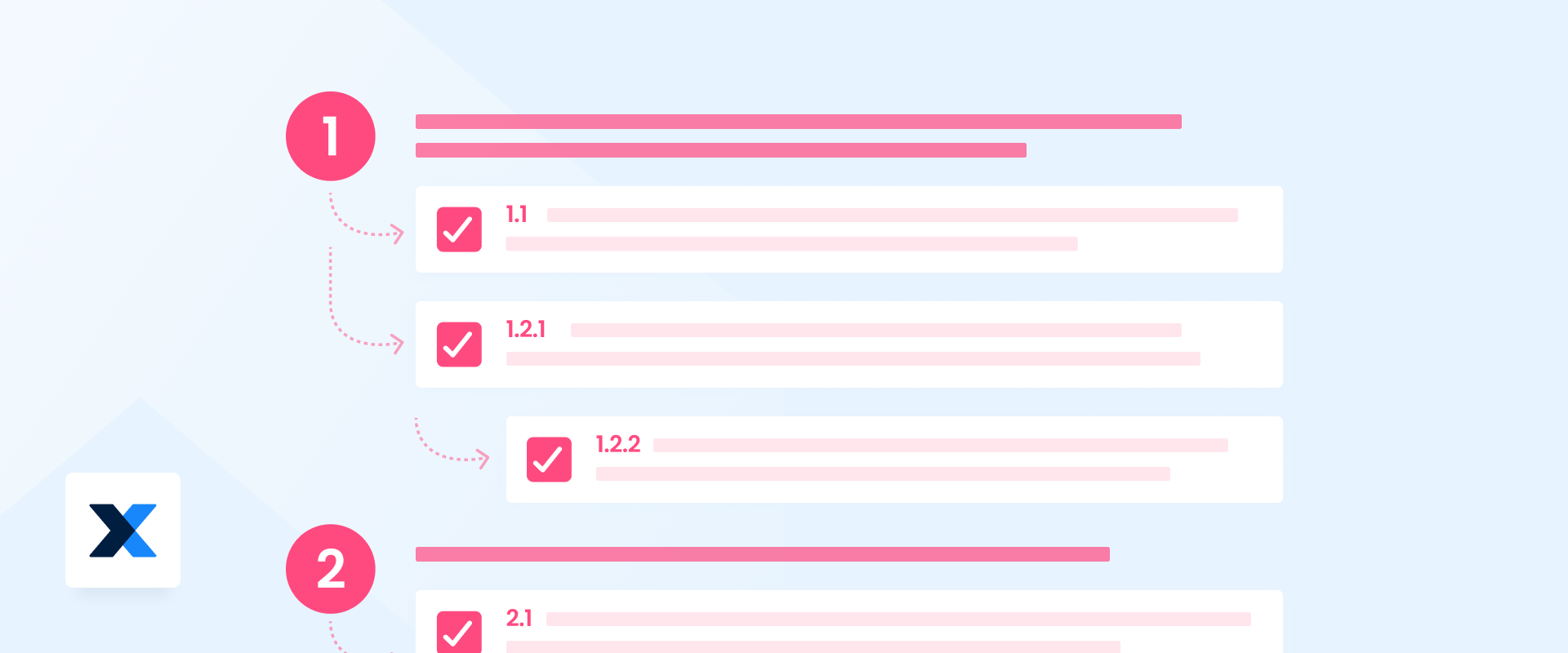
Best for procedures like:
- Overhauling a compressor
- Responding to a major pump failure
- Conducting a hazardous material spill cleanup
A hierarchical format is best suited for standard operating procedures outlining complex tasks with multiple steps and sub-steps. It breaks down complex tasks into bite-sized, digestible pieces of work.
For example, when responding to a major pump failure, the SOP may break down each major step into sub-steps to make it easier for the team to understand the work that needs to be done.
4. Flowchart format

Best for procedures like:
- Troubleshooting a PLC system
- Responding to a gas leak
- Conducting a safety audit
A flowchart format is best suited for standard operating procedures outlining processes with variable outcomes. If a process includes several possible outcomes, use a flowchart format to map out the steps for each state. For example, in the illustration above, the result of the inspection dictates the next step for the employee.
Sample standard operating procedure
Below is an example of a digital SOP created by a MaintainX user. This particular procedure outlines necessary preventive maintenance steps for a factory floor piece of equipment:
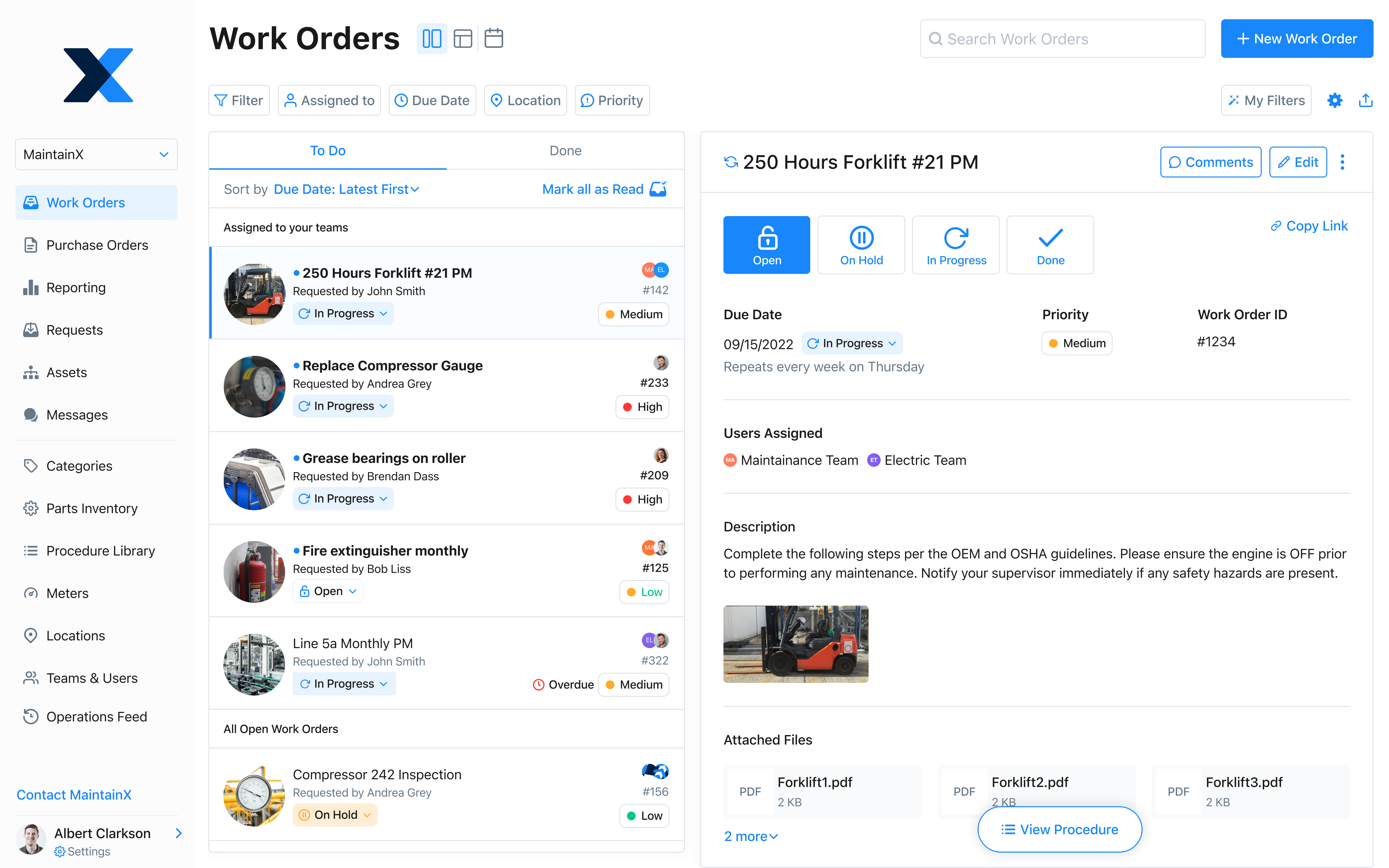
Next, the procedure then gets attached to an automated work order assignment like this:
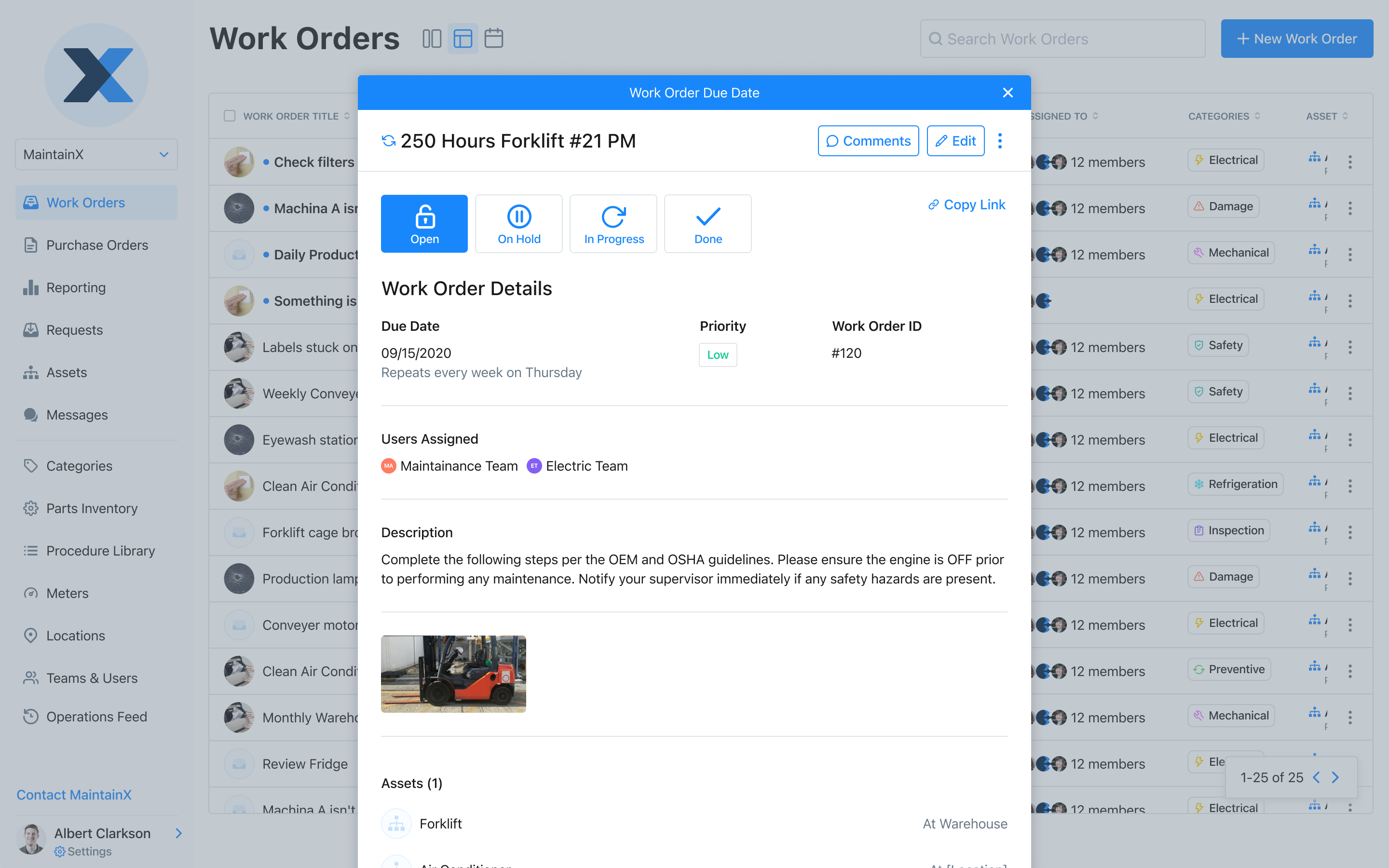
Examples of how businesses use SOPs
From onboarding to customer service, SOPs guide businesses toward ensuring consistency, efficiency, and quality. Across industries, businesses use SOPs for:
- Quality assurance: For example, an industry standard for clean water changes. The new inspection must be performed every other day instead of weekly to maintain high-quality water. The SOP needs to account for this time change and any changes in the clean water standard.
- Task handovers: For instance, a technician is out sick. SOP outlines the detailed steps for someone else to take over their scheduled work orders.
- Quality management systems: A good example is when a manager leaves. The company consults the previous manager's written standard operating procedures to streamline the onboarding process. The new hire quickly assumes the new responsibilities with minimal disruptions to organizational productivity.
- Manufacturing process standardization: For example, a new piece of equipment replaces old equipment, and the preventive maintenance work order is entirely different. A new SOP will clearly outline the new manufacturing process.
- Troubleshooting systems: For instance, a hotel guest notifies the front desk that the room's air conditioning unit is broken. The hospitality worker consults an SOP to quickly resolve the issue.
How to write & implement a great standard operating procedure
Every detail matters in an SOP. You should carefully think through each step required to complete the work and think about the best way to communicate the instructions to the reader.
Step 1: Define the purpose and scope
- Clearly define the purpose of the SOP. What process or task will it cover?
- Determine the scope of the SOP. Which departments, roles, or functions will it affect?
- Identify the process or task to be documented. What problem does it solve? What is the desired outcome?
- Determine the audience. Who will be using this SOP? What level of technical knowledge do they have?
Step 2: Gather information
- Consult with stakeholders and experts to collect detailed information about the process.
- Observe the process in action, if possible, to understand practical aspects.
- Interview subject matter experts. Talk to people who regularly perform the task and gather their insights and best practices.
- Review existing documentation. Look for relevant process flows, checklists, or diagrams.
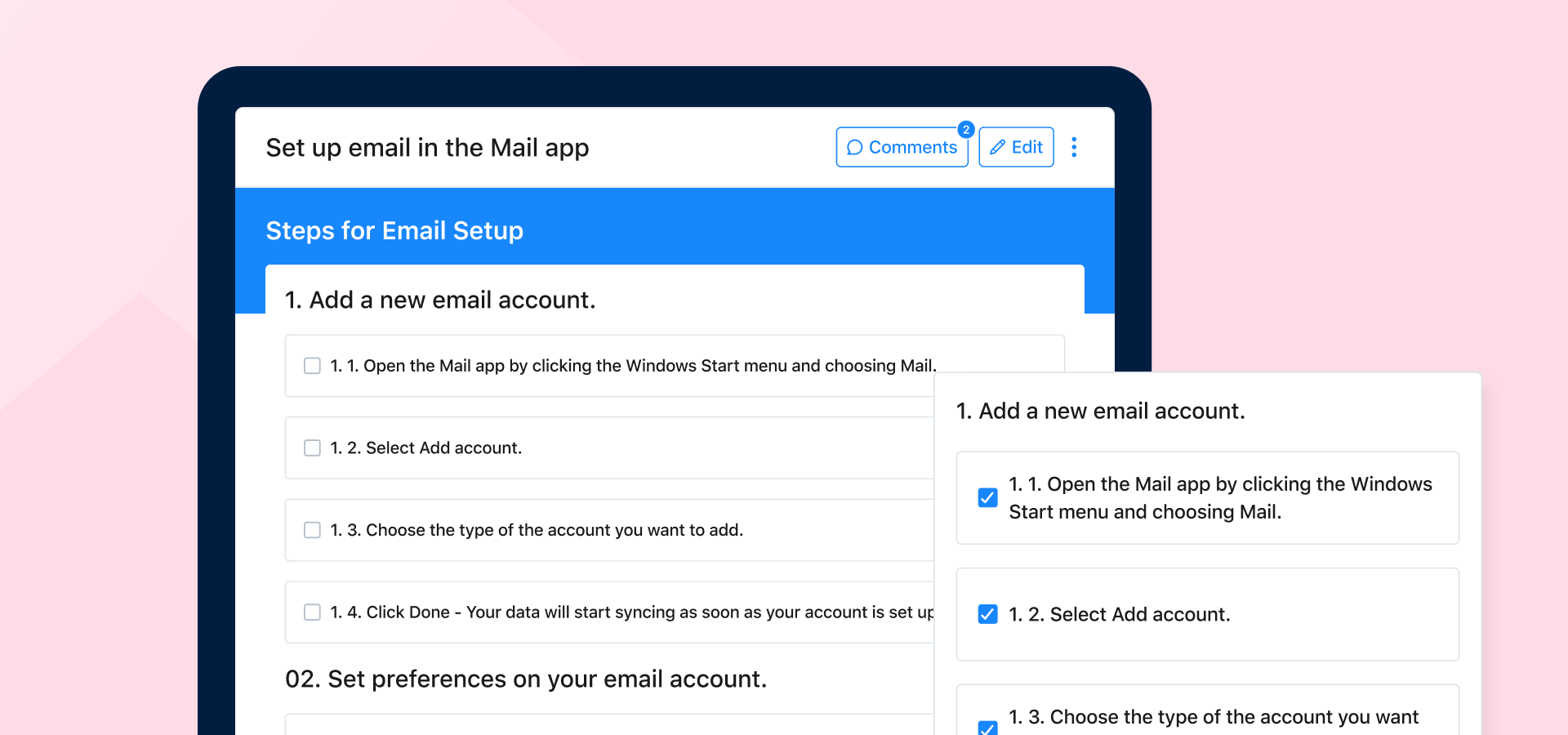
Step 3: Involve the users
At the end of the day, the technicians and operators are the ones who will be using the SOP to complete their work. Don't forget to take their input into consideration when developing standard operating procedures, as they will be closest to the work being completed. By collaborating with the users, you ensure that the SOP reflects the correct steps and ensure that they are comfortable with and bought into the procedure.
Factors to consider include:
- Familiarity with the organization, procedures to be standardized, terminologies, and knowledge level
- Language and comprehension skills
- Level of experience in performing outlined tasks
- Roles and responsibilities if target users are spread across different teams and roles
Identifying target users also helps to assign appropriate tasks and responsibilities in the SOP doc.
Step 4: Write the SOP
Now, write your SOP to include its purpose, procedures, scope, and responsibilities.
Organizations that have developed standard operating procedures in the past can rely on previous templates rather than create new ones. Those developing entirely new SOPs or business processes can choose any of the above formats:
- Start with a clear title and an introduction explaining the purpose of the SOP.
- Name the person or team responsible for completing the procedure.
- List the materials and equipment needed, if applicable.
- Detail the procedure step by step, using clear and concise language.
- Use bullet points or numbered lists for easy readability.
- Incorporate any safety or compliance guidelines relevant to the procedure.
- Include screenshots or images to illustrate complex steps.
- Name the person responsible for signing off on the completed procedure.
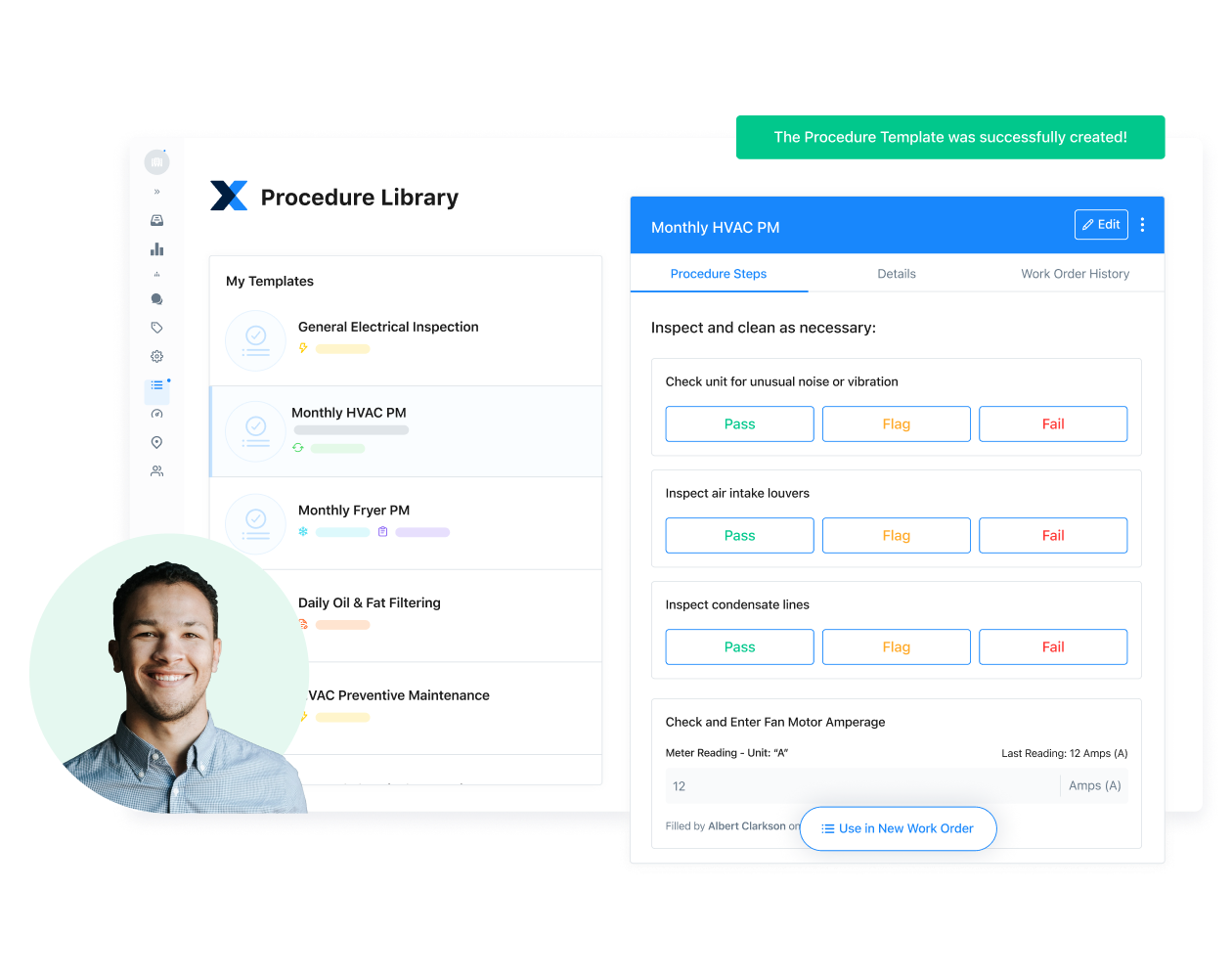
Check out our guide: 8 Tips for Developing Standard Operating Procedures (That Get Used).
Step 5: Review, test, edit
After drafting the SOP, send it to the team members for review. Members should test out the SOP to see if it achieves the desired outcome and to certify language clarity and ease of execution. Incorporate relevant suggestions and edits to improve the final draft.
- Incorporate feedback and make necessary revisions to the SOP.
- Format the document for consistency, including headers, footers, and standardized fonts.
- Include any diagrams, flowcharts, or images that aid in understanding the procedure.
- Obtain necessary approvals from management
The document should only proceed to the final step after all stakeholders accept and approve the SOP.
Step 6: Implement the SOP
Once stakeholders approve the SOP document,
- Distribute the SOP to all relevant parties.
- Train staff on the SOP, ensuring everyone understands their responsibilities.
Step 7: Review and update
- Schedule regular reviews of the SOP to ensure it remains current and effective.
- Update the SOP as processes change or new information becomes available.
- Manage access and distribution to maintain control over the document.
- Ensure that the most current version is easily accessible to all who need it.
Want to streamline SOP creation? Sign up for MaintainX and try our AI SOP Generator today!
Industries using standard operating procedures
Standard operating procedures are crucial across industries for standardizing processes, ensuring quality, maintaining safety, and complying with regulations. Here's how various industries utilize SOPs:
- Healthcare: For patient care, sterilization processes, medication dispensing, and compliance with health regulations.
- Food and Beverage: To manage food safety, quality assurance, and adherence to food handling regulations.
- Manufacturing: For consistent process execution, quality control, and safety measures.
- Chemical Industry: To safely manage chemicals and comply with environmental and safety regulations.
- Energy Sector: To ensure operational safety and efficiency, especially in nuclear, oil, and gas.
- Logistics and Supply Chain: For inventory management, shipping protocols, and service delivery.
- Agriculture: For crop management, equipment use, and food production standards.
- Hospitality: To deliver consistent service quality and manage operational tasks.
- Facility Maintenance: For maintaining buildings and systems, ensuring that maintenance tasks such as inspections, repairs, and preventive maintenance are performed systematically and safely.
- Property Management: To manage tenant relations, building maintenance, lease management, and regulatory compliance.
- Construction: For on-site safety protocols, quality control, and adherence to building codes.
Understanding technical vs. management SOPs
One way to think about developing standard operating procedures is to think of them as either technical SOPs or management SOPs.
On the one hand, technical SOPs detail how to perform and complete a task. They are often in the form of a repeating work order, a preventative maintenance work order, or an inspection.
Conversely, management standard operating procedures outline the processes to define, document, and implement standard operating procedures. It may sound silly, but companies often need management SOPs to manage their large number of technical standard operating procedures! The documents are always helpful for anyone performing a task more than once.
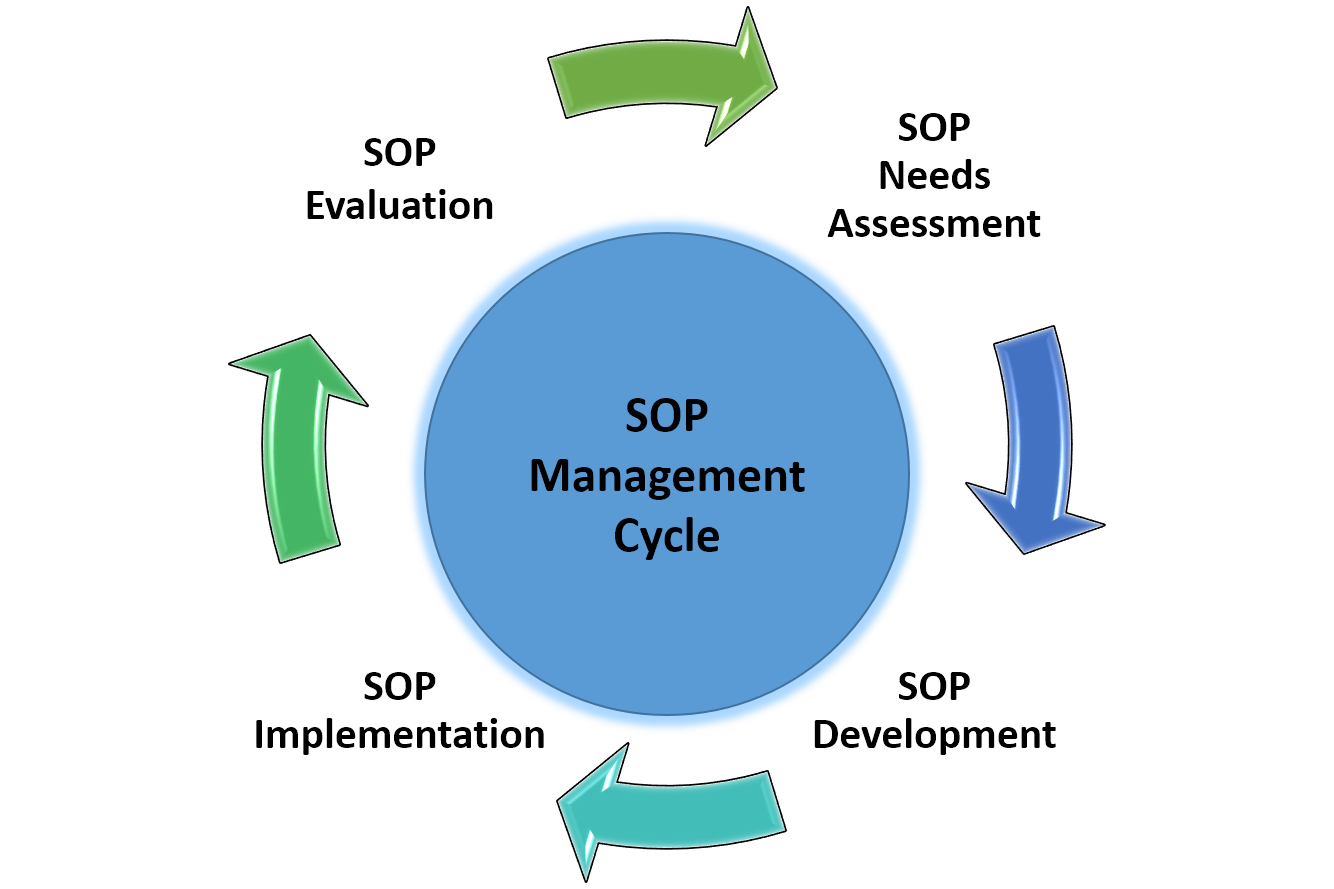
Management SOPs include information about the following:
- How to write SOPs
- Who reviews and approves the SOP
- When the reviewers/approvers revise the SOP and how often
- Who implements and manages the SOP
- Who reviews and revises SOPs as needed
Put simply, standard operating procedures will fail if management doesn't create the process for them to succeed. Whenever procedures, employees, assets, or functions change, update and re-approve SOPs.
Even when procedures don't change, review standard operating procedures regularly. Quality SOP reviews ensure policies and procedures are current, cost-effective, and compliant with changing regulatory standards.
Standard operating procedure (SOP) templates
The content of standard operating procedures depends on your business, strategy, scope, and other variables. While some standard operating procedures are lengthy documents with detailed guidelines for various complex scenarios, others are straightforward checklists.
Regardless, standard operating procedure templates provide a practical starting point to draft SOPs from scratch. Below are links for our most popular MaintainX downloadable free SOP templates. Customize the template of your choice to meet your needs.
1. Manufacturing SOP template
Our free maintenance standard operating procedure template is ideal for jobs that have operational safety inspections, compliance requirements, quality control procedures, production inspections, walkthroughs, and corrective actions.
Download now: Manufacturing Standard Operating Procedure template.
2. Sanitation SOP template
Our free sanitation standard operating procedure template is ideal for professionals who need to stay on top of sanitation protocols in their workplace.
Provide clear headings and enter the effective date, and requirements specific to your workplace, including approved cleaning agents, labeling and storage requirements, priority of operations, corrective action protocols, and more.
Authorizations for the work order are recorded automatically at the bottom of the sheet—just add authorized signatures to finalize.Download now: Sanitation Standard Operating Procedure template here.
3. Warehouse SOP template
Our free warehouse standard operating procedure template is for regular maintenance, operations, inspections, and compliance performed during routine warehouse operations.
From order-form compliance and approvals to receiving procedures to inspection requirements, this template makes the scope of work performed easy to understand by both team members and management.
This template differs from the rest, as specific operational requirements depend on the warehouse's specific function. Depending on the materials and inventory managed, you can include any necessary and specific industry standards.
Download now: Warehouse Standard Operating Procedure template here.
4. Restaurant SOP template
Our downloadable restaurant standard operating procedure template makes building and printing procedures at any location easy.
Complete with everything from hygiene requirements for staff, food safety, inventory management, food preparation, and more, this template will set your restaurant up for success.
Easily edit this template to fit your needs—enter the company name and requirements for each section specific to your restaurant, standard operating rules for authorized approvals, corrective actions, any additional information, and record keeping.
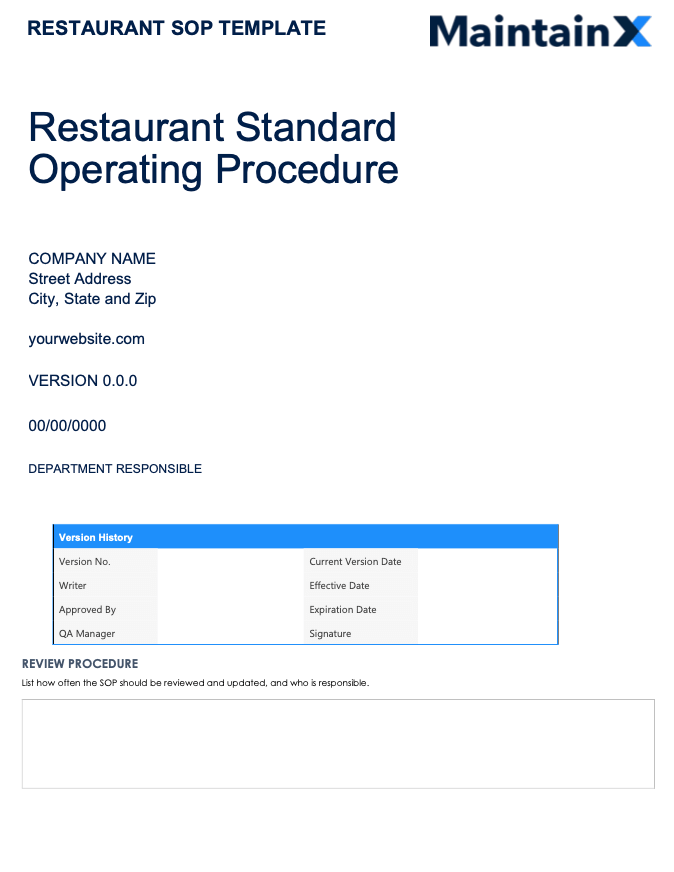
Download now: Restaurant Standard Operating Procedure template here.
Looking for more templates? Check out our Global Procedure Library Today.
Benefits of creating digital standard operating procedures
- Streamlines audits/inspections: Cloud-based checklists provide digital audit trails and are available for inspectors.
- Enhances O&M decision-making: Digital dashboards provide information about job performance, time-on-task, and other insightful metrics.
- Increases efficiency: Processes are uninterrupted and completed on schedule because everyone always has their smartphone in their pockets.
- Improves quality control: Operations are performed correctly, consistently, and quickly because questions get answered on the spot.
- Improves employee skills: Workers are more easily kept up-to-date and trained in new procedures.
- Saves time: Managers don't need to reinvent the wheel when standard operating procedures need to be modified. They can simply make a quick edit from their desktops or phones.
Tracking information, internal controls, and business processes is more manageable when SOPs are digitized using standard operating procedure software. Especially when, for example, suppliers and new outsourcing are involved.
Create better SOPs faster with MaintainX
Everyone in a company is responsible for the quality of its products and services. Most organizations have routine practices in place to ensure the consistent execution of day-to-day business operations and internal processes.
However, the most effective leadership teams go a step further. They take the time to document preferred processes, procedures, and standards so there is no confusion about what to do or how to do it. These standard operating procedures increase performance and improve efficiency.
Now is the time to start if you haven’t yet started digitizing and automating your SOPs. With a digital platform, you can build a roadmap for everyone on your team to follow. This roadmap will help you work smarter, not harder, to achieve your goals faster.
With MaintainX, workers and team members can communicate on SOP progress in real-time via mobile devices. Translation: no more paperwork being filed away and forgotten. MaintainX's AI-powered Procedure Generator allows you to create digital checklists and SOPs in a fraction of the time. All you have to do is share a few details and let our system do the rest. In addition, our Global Procedure Library can help you streamline workflows, communication, and accountability.
Standard operating procedure FAQs
1. What are SOPs?
Standard operating procedures are detailed instructions describing the steps necessary to carry out an operation or task. They are designed to achieve efficiency, quality output, and uniformity of performance while reducing miscommunication and failure to comply with industry regulations. Standard operating procedures are widely used in various industries to ensure that business processes are conducted consistently, reliably, and predictably.
2. Why are SOPs important?
Standard operating procedures are crucial because they provide a structured task framework, ensuring consistency and quality control across an organization's operations. SOPs help maintain compliance with industry and legal standards, reducing the risk of errors and accidents. Additionally, SOPs facilitate training and onboarding by providing clear employee guidelines, enhancing overall productivity and safety of the work environment.
3. What should be included in an SOP?
An effective SOP should include a clear title, purpose, and scope that outline the procedure's intent and applicability. It must detail the necessary steps to perform the task, including equipment, materials, and safety considerations. Additionally, it should specify the roles and responsibilities of the techs involved, define any acronyms, provide contact information, and list any relevant compliance standards or quality control measures that need to be followed.
4. How often should SOPs be reviewed and updated?
Standard operating procedures should be reviewed and updated regularly to ensure they remain relevant and effective. Reviews should take place annually or when significant changes affect the procedures. Regulation updates, technology advancements, or shifts in organizational structure should necessitate reviews.
The industry standards or internal quality assurance policies may also dictate the frequency of review. Documenting each review and update is crucial to maintain a record of changes and ensure ongoing compliance.
5. Who is responsible for developing and maintaining SOPs?
In the manufacturing maintenance industry, the development and maintenance of standard operating procedures are often the responsibility of maintenance managers, engineering teams, or those in charge of operations. These professionals work with health and safety officers to ensure SOPs adhere to legal and industry standards. Involvement from frontline maintenance technicians is also critical to provide insights into these procedures' practical aspects and enforceability.
FAQs
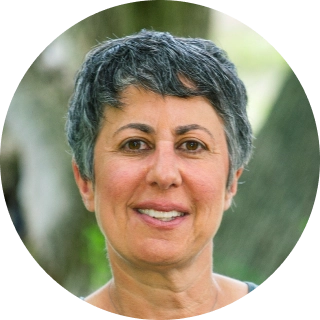
Caroline Eisner is a writer and editor with experience across the profit and nonprofit sectors, government, education, and financial organizations. She has held leadership positions in K16 institutions and has led large-scale digital projects, interactive websites, and a business writing consultancy.