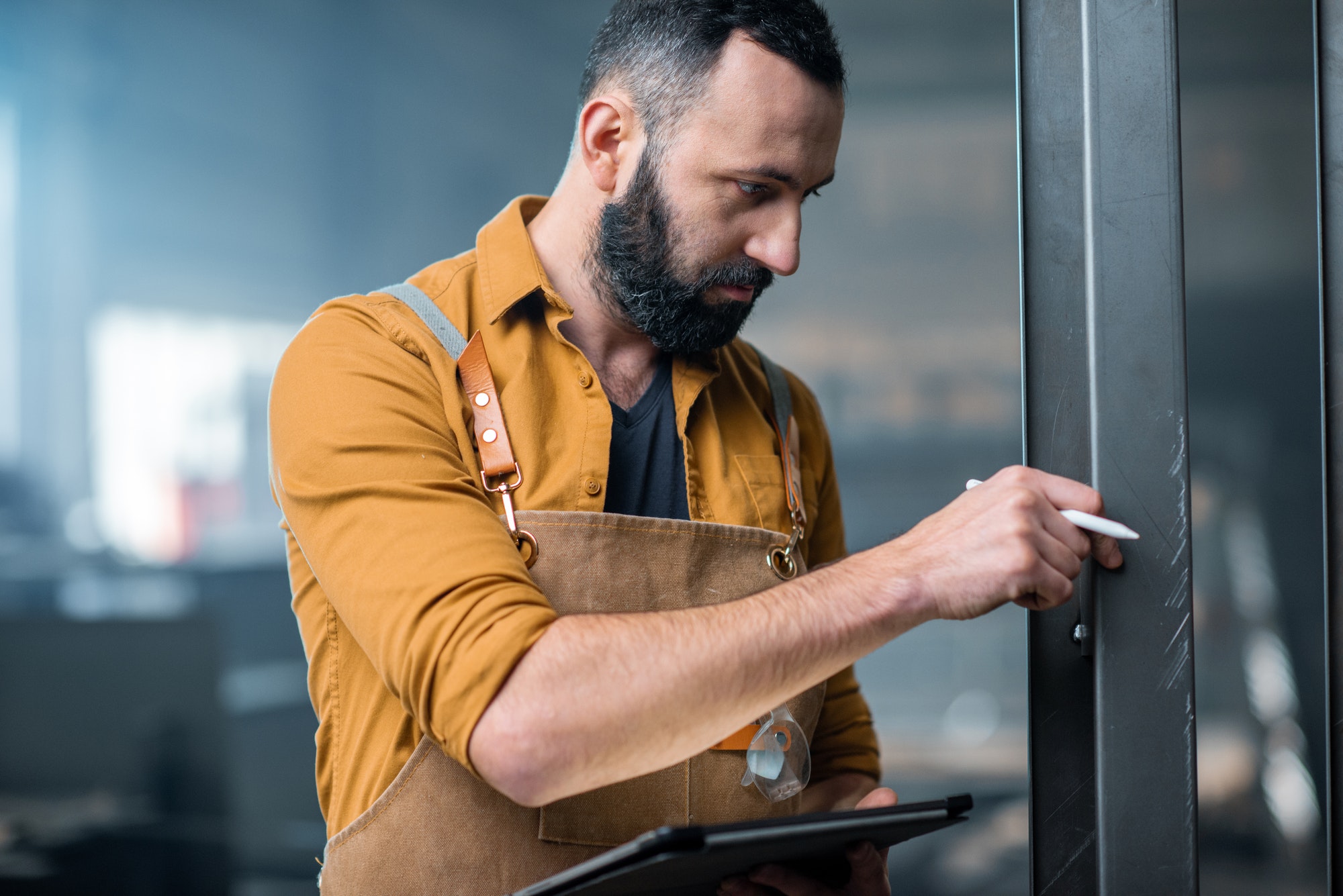
If your plant isn’t running an effective manufacturing standard operating procedures program, this article will motivate you to make the changes you need to improve performance. Here, we’ll discuss the applications, benefits, and importance of manufacturing standard operating procedures.
Strategic SOP programs bolster equipment maintenance, quality assurance, waste management, and supply-chain stability. Repeatable processes can always be made more efficient with SOPs.
What are manufacturing SOPs?
Manufacturing SOPs, or manufacturing standard operating procedures, are detailed instructions that guide workers through specific manufacturing tasks. These step-by-step instructions ensure consistency, quality, and safety when completing repetitive manufacturing processes.
They typically include a list of sequential tasks to be completed and links to relevant documents, forms, or tools. Visual aids like diagrams, flowcharts, or photos are often included as part of the standard operating procedures to clarify further the steps that need to be followed.
Manufacturing SOPs, working in tandem with PM work orders, quality control checklists, and inspection audits, are essential for maintaining efficient and reliable production processes.
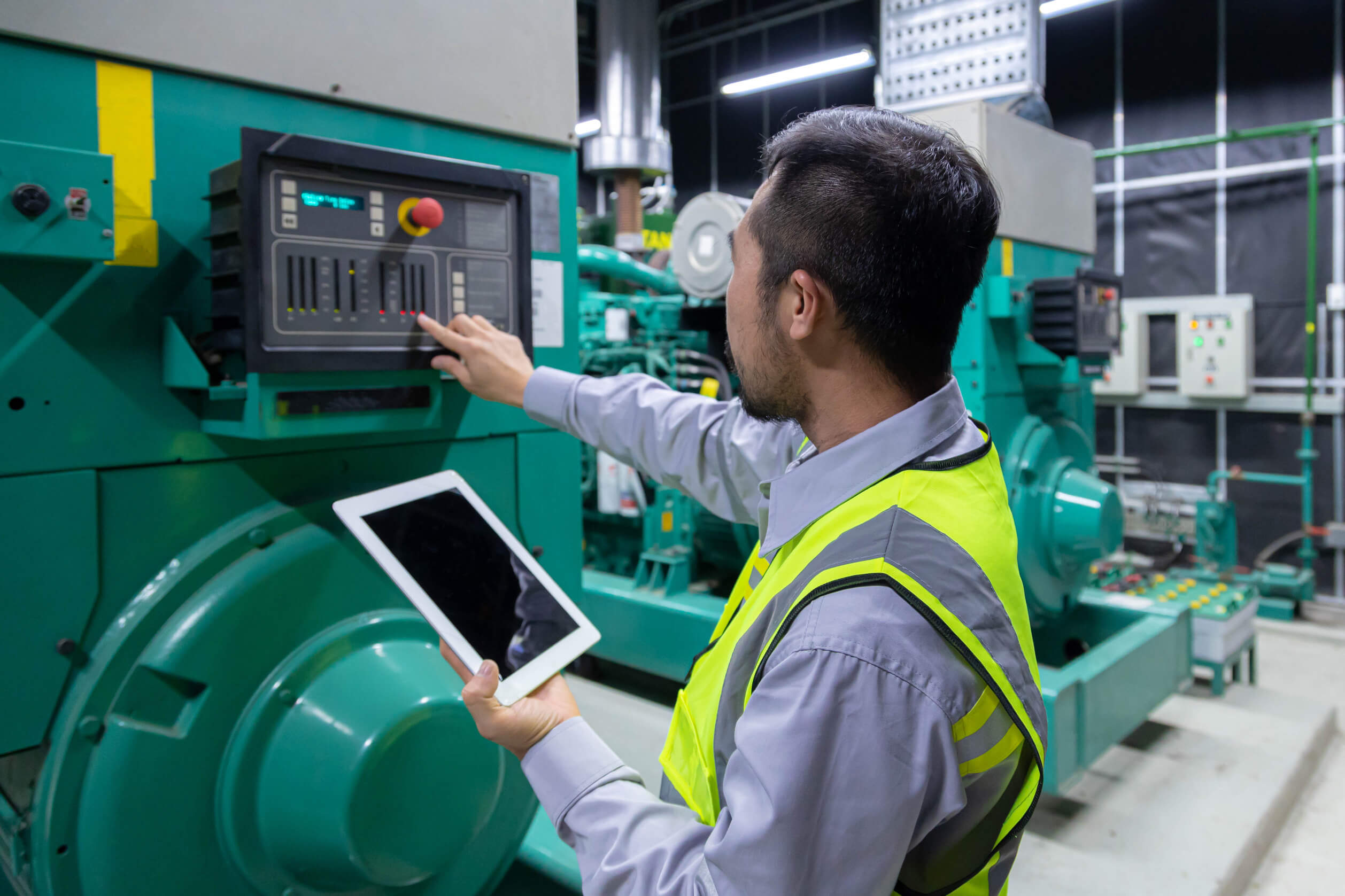
7 benefits of manufacturing standard operating procedures
SOPs are crucial if manufacturing facilities are to achieve uniform performance, production-line efficiency, high-quality production, and regulatory compliance. Here’s a rundown of the benefits you could experience from launching a solid SOP program.
1. Standardized production (time saved)
Manufacturing standard operating procedures (SOPs) ensure all employees complete tasks in precisely the same manner across production lines and facility locations. Generally, this means managers can expect to receive fewer questions about how to implement verbalized work instructions.
Standardized production methods not only thwart confusion but also save management time. Instead of reexplaining how to do something repeatedly, plant managers can refer employees to SOP documentation.
2. Streamlined communication
Manufacturing SOPs enhance communication across all team levels and facilities. When digitized, employees and managers can access real-time updates of ongoing and completed tasks with minimal chances of miscommunication.
Modern computerized maintenance management system (CMMS) apps like MaintainX further enhance communication with digital work order commenting, team messaging, and photo uploading. Such communication improves top-down communication within the organization, streamlines project management, and produces faster problem response times.
Additionally, manufacturing standard operating procedures make it easier for managers to interpret key performance indicators (KPIs). You can't improve what you don't understand. Tracking maintenance and performance metrics is only valuable when you know the specific steps that drive those results. Managers can share meaningful metrics with team members to help explain necessary corrective actions.
3. Improved quality assurance
Producing dependable final products is crucial to maintaining long-term customer relationships. For this reason, managers must build plant systems with acceptable quality standards.
Documenting effective SOPs helps ensure that manufacturing teams meet the International Organization for Standardization (ISO)’s seven ISO 9000 quality management principles for product quality requirements. A robust quality management system is crucial to discouraging cutting corners during production workflows.
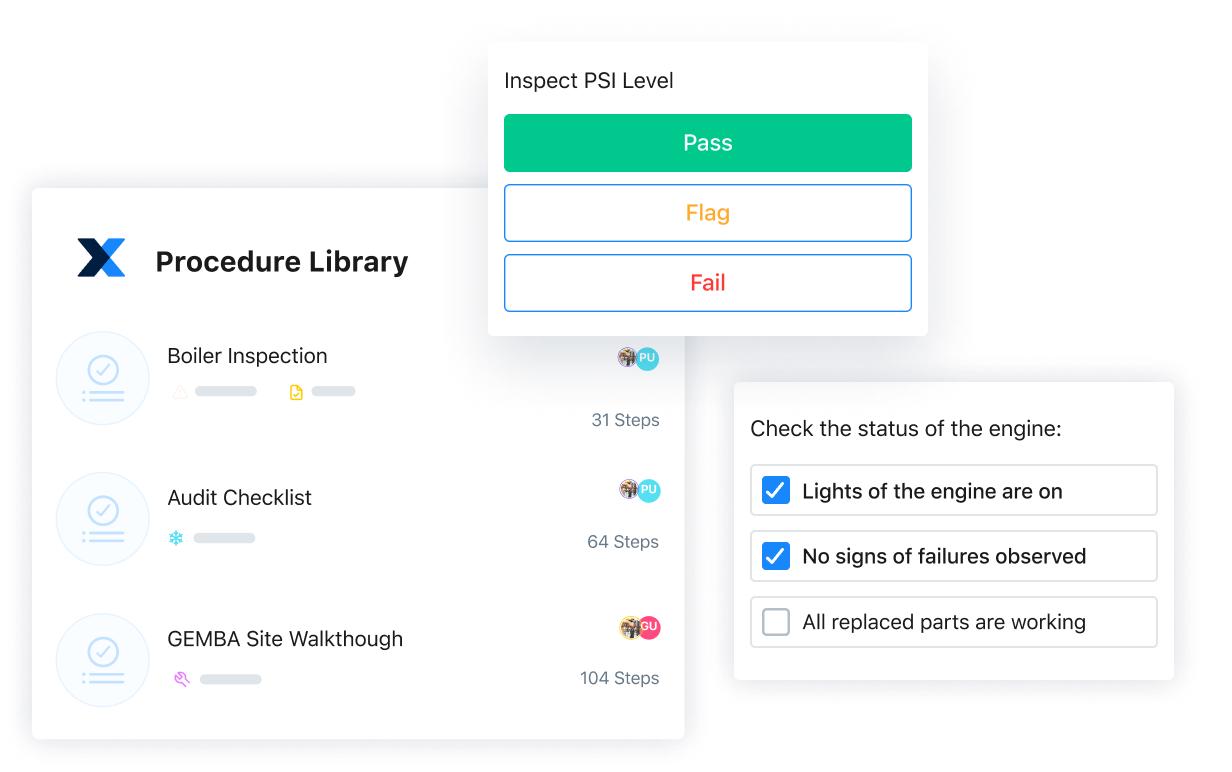
4. Improved regulatory compliance
SOPs also help manufacturing facilities follow best record-keeping practices to ensure they are prepared for regulatory audits. Thorough SOPs support the implementation of safety and compliance standards, which is necessary to pass OSHA safety inspections.
While paper SOP records are better than none at all, SOP software simplifies the process even further with digital audit trails. Manufacturing facilities can safeguard themselves against potential legal actions with digitized reports that demonstrate checklist compliance with time and date automation.
5. Enhanced accountability
In addition to standardizing task completion, SOPs clearly define the roles responsible for completing assignments. Such accountability measures make it easier for plant managers to track performance, improve compliance, and provide direction across the manufacturing floor.
As a result, managers may identify knowledge or skill gaps that necessitate new training programs. Alternatively, management can provide workers with validation that they are doing a good job. Regardless, greater accountability opens the door to providing guidance for continuous improvement.
6. Improved plant efficiency
As mentioned above, consistently seeking ways to improve production efficiency is crucial to plant growth. Exemplary managers continuously evaluate equipment performance patterns, organizational bottlenecks and opportunities for cutting total manufacturing costs.
Established SOPs provide a baseline for measuring progress and making better-informed decisions. Once managers identify frequently made mistakes or extra steps that don’t add value to operational goals, they’re in a powerful position to course correct.
7. Minimized manufacturing waste
Manufacturing facilities should adopt lean manufacturing principles to improve efficiency and eliminate or minimize waste. There are eight different types of manufacturing waste that effective SOPs can help to eliminate or reduce.
They include defects, overproduction, waiting times, under-utilization of talent, transportation waste, inventory waste, overprocessing, and motion waste. Solid SOPs help management better monitor the effectiveness of production lines, pieces of equipment, and employees.
This best practice helps plant leaders confidently tweak business processes based on actual data points rather than hunches. Interested in learning more? Click here to learn why writing standard operating procedures with waste reduction in mind is conducive to success.
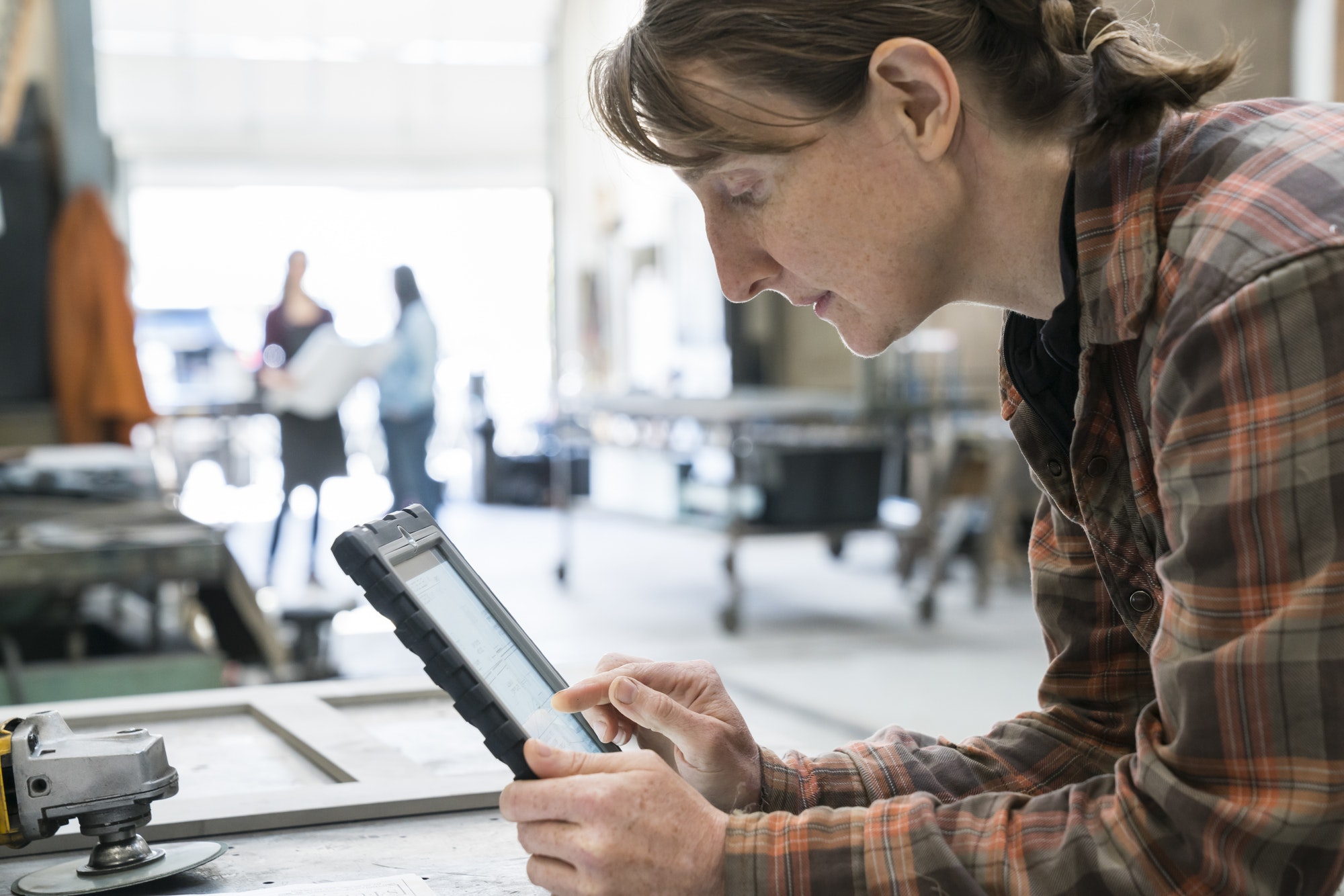
How to write manufacturing SOPs
Here are a few key steps to follow when crafting clear, concise, and comprehensive manufacturing SOPs for your team:
1. Establish objectives
Determine the specific process or task that you want to standardize with the SOP. Are you looking to document production process? Outlines steps for quality assurance? Create guidelines to ensure safety and prevent accidents? Or adhere to industry or government regulations? Clearly defining your objectives will help ensure that your manufacturing SOPs are focused, effective, and easy to follow.
2. Gather necessary data
The next step is to gather all the information you need to write the SOP. This data might include equipment manuals, technical specifications, regulatory guidelines, and safety protocols. Don't forget to tap into the valuable knowledge of your frontline workers—operators, technicians, and supervisors. Their hands-on experience can provide invaluable insights to make your SOPs truly practical and effective.
3. Define process steps
With the necessary data on hand, break down the process into a clear, step-by-step outline. Imagine you are explaining it to a five year old—the goal is to create a logical flow of tasks that’s simple, logical, and easy to follow from start to finish. Each step of the manufacturing sop should be detailed, but not overly complicated.
To streamline this process, consider using tools like an AI-powered procedure generator. It can help you quickly create well structured manufacturing SOPs by just inputting few key details.
4. Prioritize compliance standards
Ensure that you include any relevant safety and compliance requirements, considering industry regulations like OSHA (Occupational Safety and Health Administration) standards and any information specific to your facility.
5. Test and review
Put your SOPs to the test! Have your frontline workers—operators, technicians, and anyone involved in the process—try them out in real-world scenarios. Pay close attention to how they adapt to the instructions and gather their feedback. This hands-on approach will help you uncover any potential issues or areas for improvement, ensuring your final SOPs are practical, effective, and user-friendly.
6. Digitize SOPs with a CMMS
A CMMS streamlines digital SOP creation, storage, access, and updates. Cloud-based storage helps ensure that your team members can access SOPs from anywhere, anytime, while managers can easily update and share new procedures as needed. To make things even easier, choose a CMMS platforms with built-in procedure libraries that give you access to a wealth of industry-standard SOP templates to leverage and adapt to your specific needs.
7. Monitor and update
Monitor the SOP's effectiveness over time and update it as needed. Processes, equipment, and regulations may change, so keeping SOPs current and up-to-date is essential. Regularly solicit feedback from stakeholders to identify any issues or areas for improvement. An outdated SOP can lead to confusion, errors, and compliance risks, so maintaining its relevance is crucial for ongoing success.
Manufacturing SOP templates
Instead of building out your SOPs from scratch, you can use existing SOPs as a baseline from which to begin and simply modify them to suit your needs. MaintainX’s Global Procedure Library houses applicable procedures from various industries and companies, covering different functions. Here are a few:
Procedure for equipment check-in
This SOP outlines the procedures for checking equipment in and out of a lot.
Hazard assessment checklist
Use this to assess your facility for safety hazards
Climate control system preventive maintenance
This procedure inspects all locations and units of the climate control system. This is important to ensure your system is working effectively.
OSHA self-inspection checklist
The OSHA Self Inspection Checklist focuses on providing all necessary practices and responses for safety and health measures. Remove risks and provide a safe working environment for your workers.
SQF fundamentals checklist: Basic level for primary production
The SQF Fundamentals Code checklist assists suppliers in performing internal audits and gap assessments to the SQF Fundamentals for Manufacturing.
Streamline manufacturing operations with MaintainX
MaintainX empowers busy manufacturing teams to streamline their processes, transforming traditional paper-based SOPs into interactive, digitized SOP checklists accessible right from their smartphones. With real-time updates and monitoring, MaintainX helps ensure everyone is on the same page, fostering efficiency and accuracy.
Key Features that enhance your workflow:
AI-enabled procedure generator
Save valuable time by simply uploading existing files or typing out instructions in MaintainX’s AI-powered procedure generator. MaintainX will do the heavy lifting and generate a structured procedure, ready for your review and customization. Think of it like a virtual assistant for creating SOPs.
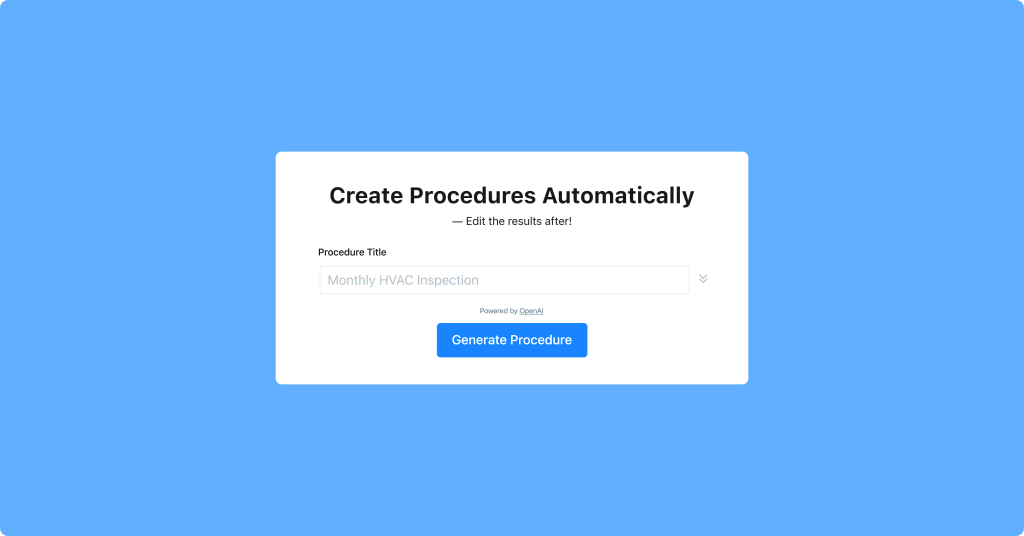
A robust procedure library
Tap into a vast collection of pre-built SOP templates from various industries and customize them to your needs. Instantly enhance your workflow, safety practices, and overall operational efficiency.
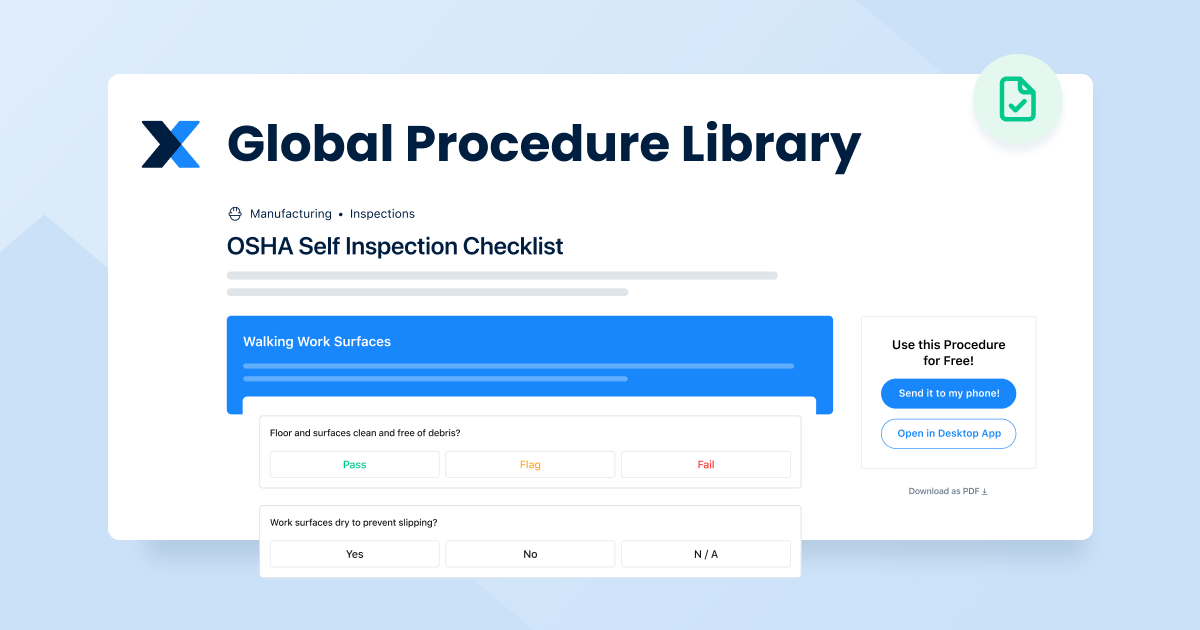
In-depth reporting capabilities
Unlock critical insight into your operations with MaintainX’s robust reporting capabilities. Track critical metrics, pinpoint areas for improvement, and drive operational excellence through data-driven decisions. You can also create custom dashboards to monitor and report on the metrics that matter most to your business.
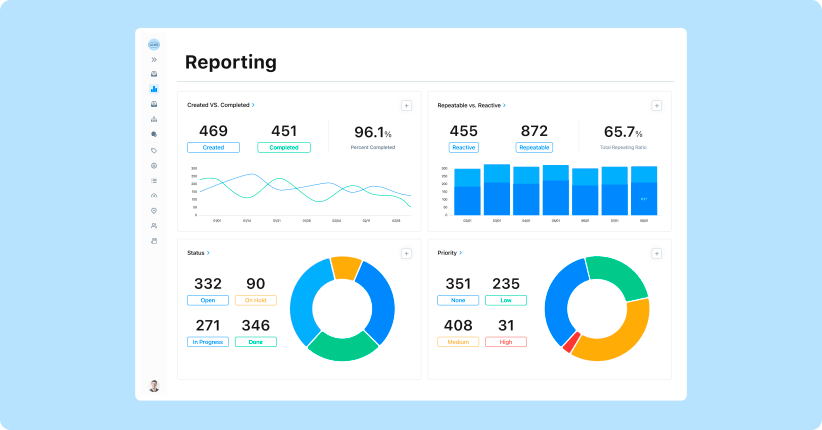
Digital audit trails
Establish a single source of truth for your operations with digital audit trails. Ensure regulatory compliance, identify bottlenecks or errors, and maintain complete transparency and accountability throughout your operations.
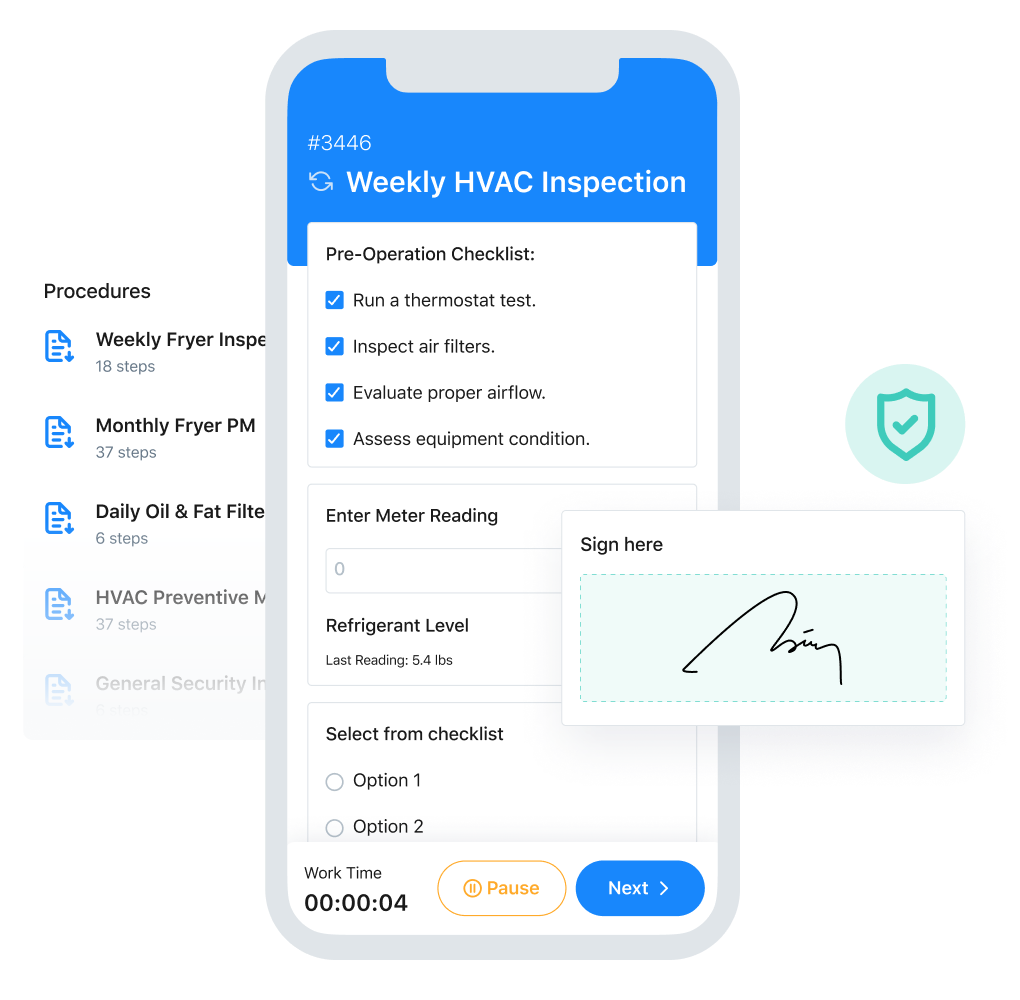
Ready to transform your manufacturing SOPs from cumbersome paperwork into a streamlined, digital powerhouse?
Experience the MaintainX difference today. Get started for free today and discover how our platform can revolutionize your operations, boost efficiency, and empower your team.
Manufacturing SOP FAQs
What are the common manufacturing SOP formats?
Common formats for manufacturing SOPs include narrative-based instructions, checklists, flowcharts, and step-by-step guides. Some SOPs use a combination of these formats to ensure clarity and accessibility for users.
Can a Maintainx SOP template be customized?
You can easily customize MaintainX SOP templates. They are designed to be flexible, allowing you to adjust them to fit your specific processes and organizational needs.
Who is responsible for writing a manufacturing SOP?
Typically, manufacturing SOPs are written by subject matter experts such as experienced managers, supervisors, operators, quality control specialists, or safety officers. They may collaborate with other frontline workers to ensure accuracy and completeness.
How often should manufacturing SOPs be reviewed and updated?
Manufacturing SOPs should be reviewed and updated at least annually or whenever there's a significant change in processes, equipment, regulations, or safety requirements. Regular reviews help ensure that the SOPs remain accurate, effective, and compliant.
FAQs
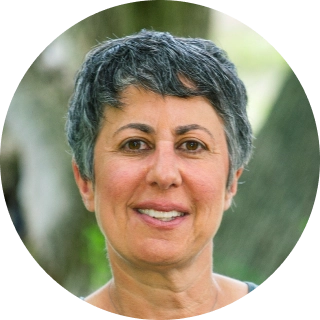
Caroline Eisner is a writer and editor with experience across the profit and nonprofit sectors, government, education, and financial organizations. She has held leadership positions in K16 institutions and has led large-scale digital projects, interactive websites, and a business writing consultancy.