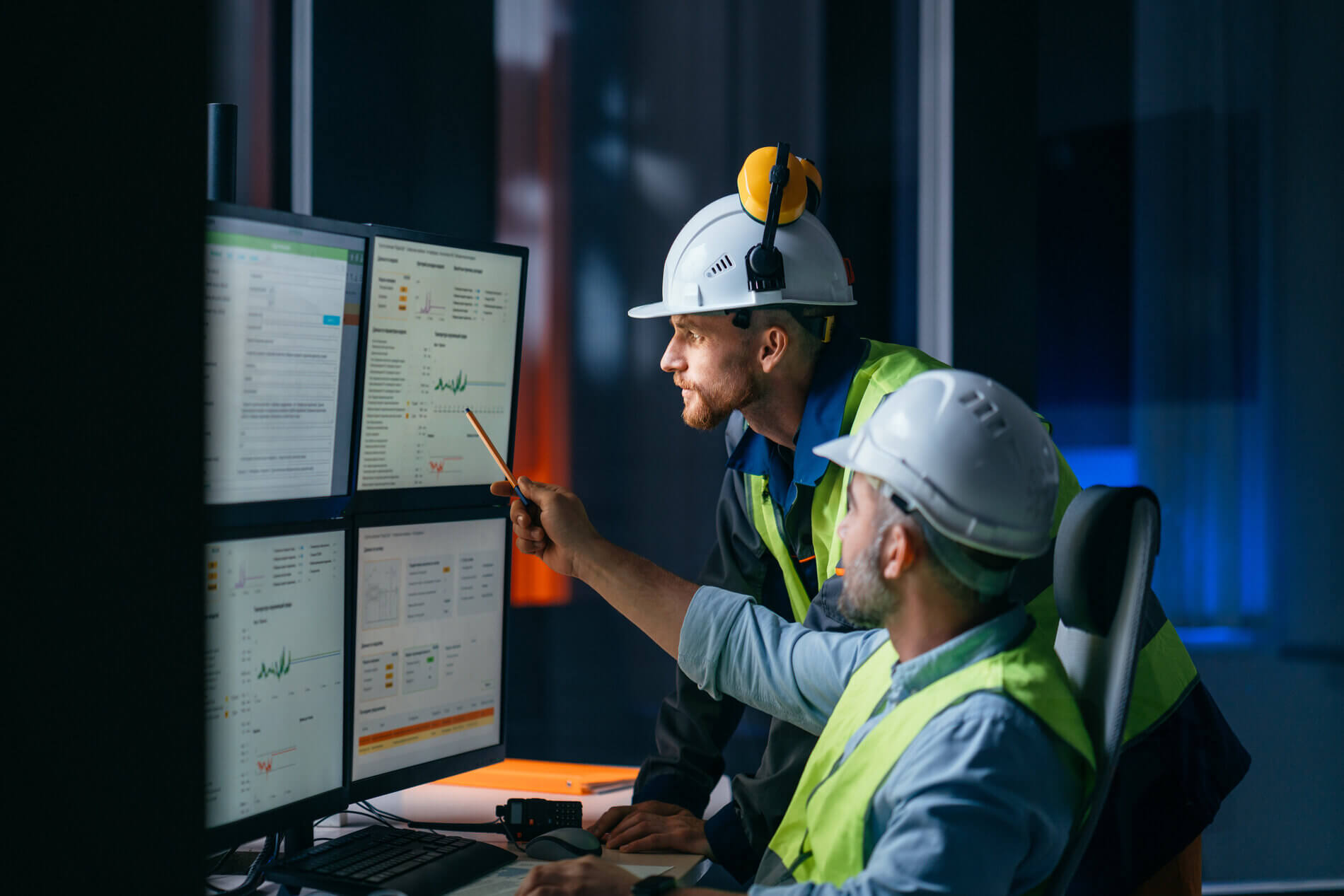
A Unified Namespace (UNS) is a system that assigns a unique identifier to each device, system, and piece of equipment within a manufacturing facility. This identifier, known as a Uniform Resource Identifier (URI), allows for easy communication and integration between these different systems and devices.
A UNS can streamline processes, eliminate bottlenecks, and facilitate automation. Startups and new initiatives in the manufacturing industry with limited resources will find a UNS useful. Especially if they need to optimize processes and make the most of their available time and workforce.
Without a unified namespace, technicians must individually program each system or device to communicate with the others. This can be time consuming and error prone. With a UNS, systems and devices can easily communicate with each other, allowing for automation and efficient data exchange.
Also called a Hub and Spoke model, UNS can improve efficiency and productivity by integrating systems and devices. This Industry 4.0 integration can eliminate bottlenecks.
Digital Revolutions and Data Flow
The main difference in data flow between Industry 3.0 and Industry 4.0 is the level of automation and integration.
Industry 3.0, also known as the Digital Revolution, marked the transition from analog to digital technology in manufacturing and industry. The widespread use of computers, automation, and data exchange characterized this period. On the other hand, Industry 4.0, known as the Fourth Industrial Revolution, uses technology to enhance and optimize manufacturing and industrial processes.
In fact, one key difference is how data is collected, analyzed, and used. In Industry 3.0, humans typically collected and analyzed data. However, in Industry 4.0, advanced technologies like IoT and AI collect and analyze vast amounts of data in real time. In addition, the flow of data in Industry 4.0 is more fluid and interconnected.
“When organizations implement new industrial IoT solutions, they may work fine at first but become less effective as the project or company scales. To scale your industrial IoT implementation, you need a unified namespace—a software solution that acts as a centralized repository of data . . . The solution allows users to collect data from various sources, add context so there’s meaning to it, and transform it to a format that other systems can understand.”
The Industrial Internet of Things (IIoT) uses connected devices and sensors in industrial and manufacturing settings to facilitate data exchange. The UNS is essential for the industrial IoT. Workflow automation facilitates the integration and communication of devices and systems within a manufacturing facility.
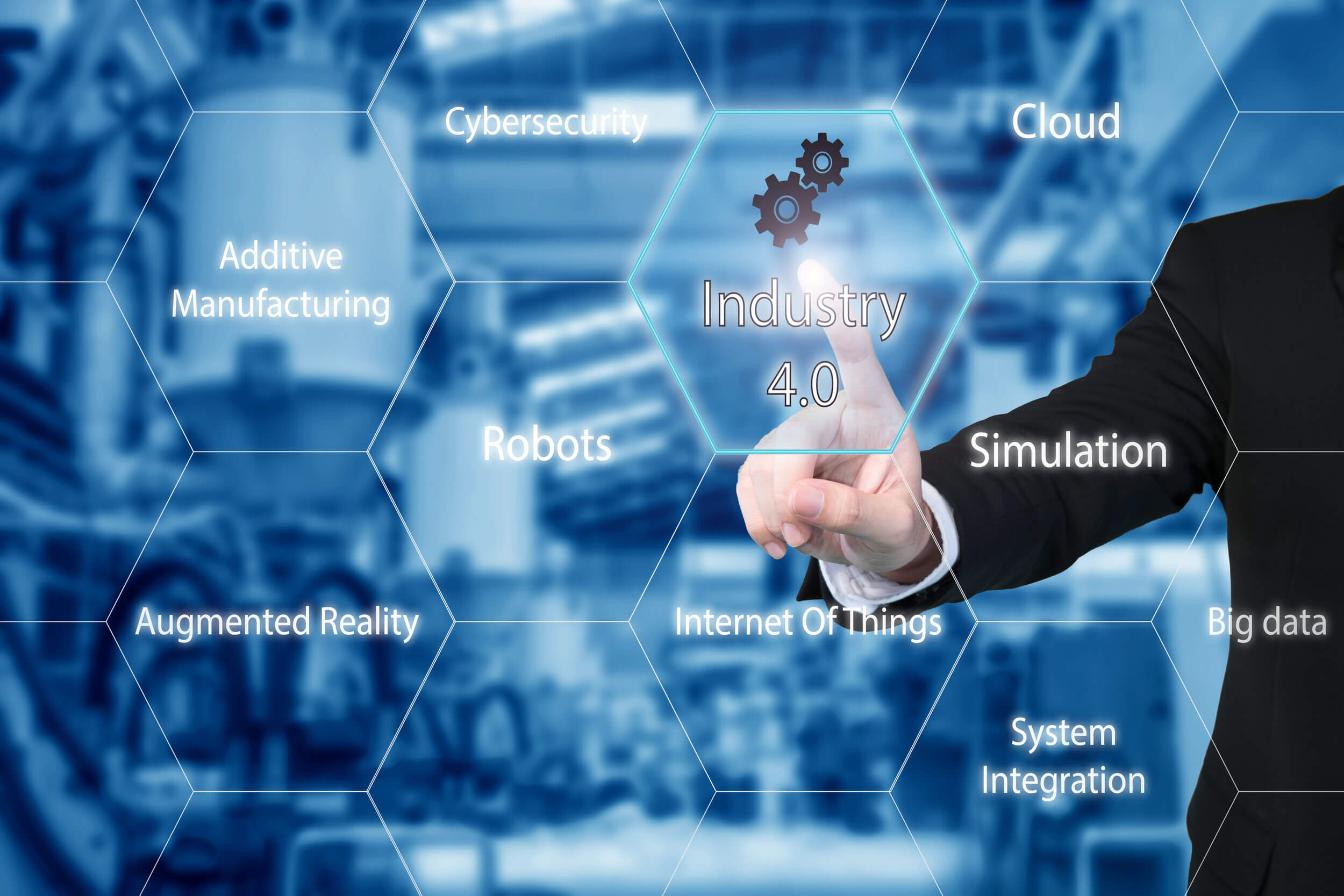
Unified Namespace Key
Data Lake
A data lake is a central repository that allows for storing and managing large amounts of structured and unstructured data. A UNS uses a data lake to store and manage the data from systems and devices within a manufacturing facility. The UNS can identify and retrieve the data for specific tasks or processes. In other words, the data lake is a central repository for storing and managing this data. Walker Reynolds explains that UNS can be the organization data hub based on ISA-95 “Hierarchical Equipment Model.”
Message Broker
A message broker facilitates communication between systems and devices and uses a UNS to improve communication and integration within a manufacturing facility. The UNS’s unique identifiers allow the message broker to route messages and data to the correct systems and devices.
Payload
A payload is the data transmitted between systems and devices as part of a message or request. For example, in the context of a unified namespace, the payload of a message or request contains the data exchanged between different systems and devices within a manufacturing facility. For example, a request to a temperature sensor may include its unique identifier and instructions for accessing data. The sensor uses the identifier to locate the requested data and sends it back in the payload of a response message. The payload allows data exchange between systems and devices using their unique identifiers.
How to Integrate a UNS with a CMMS
To integrate a UNS with a CMMS, follow these steps:
- Determine the current organizational structure and naming conventions used for assets in the CMMS. This will help you understand the organization of an existing system and identify potential conflicts with the unified namespace system.
- Identify the assets to include in the unified namespace system. This may include physical assets such as equipment, buildings, and infrastructure and virtual assets such as software and digital documents.
- Develop a plan for implementing the UNS system. This should include a timeline, necessary resources, and training or communication efforts.
- Implement the UNS by updating the asset names and descriptions in the CMMS to reflect the new naming conventions. You may need to work with IT staff or the vendor of the CMMS to make these changes.
- Test the UNS system to ensure that it functions correctly and that you have appropriately named and organized all assets.
- Communicate the changes to all relevant stakeholders and provide training as needed to ensure that everyone is aware of and able to use the new system.
- Monitor and maintain the unified namespace system on an ongoing basis to ensure that it remains accurate and up-to-date. This may involve periodically reviewing and updating asset names and descriptions as needed.
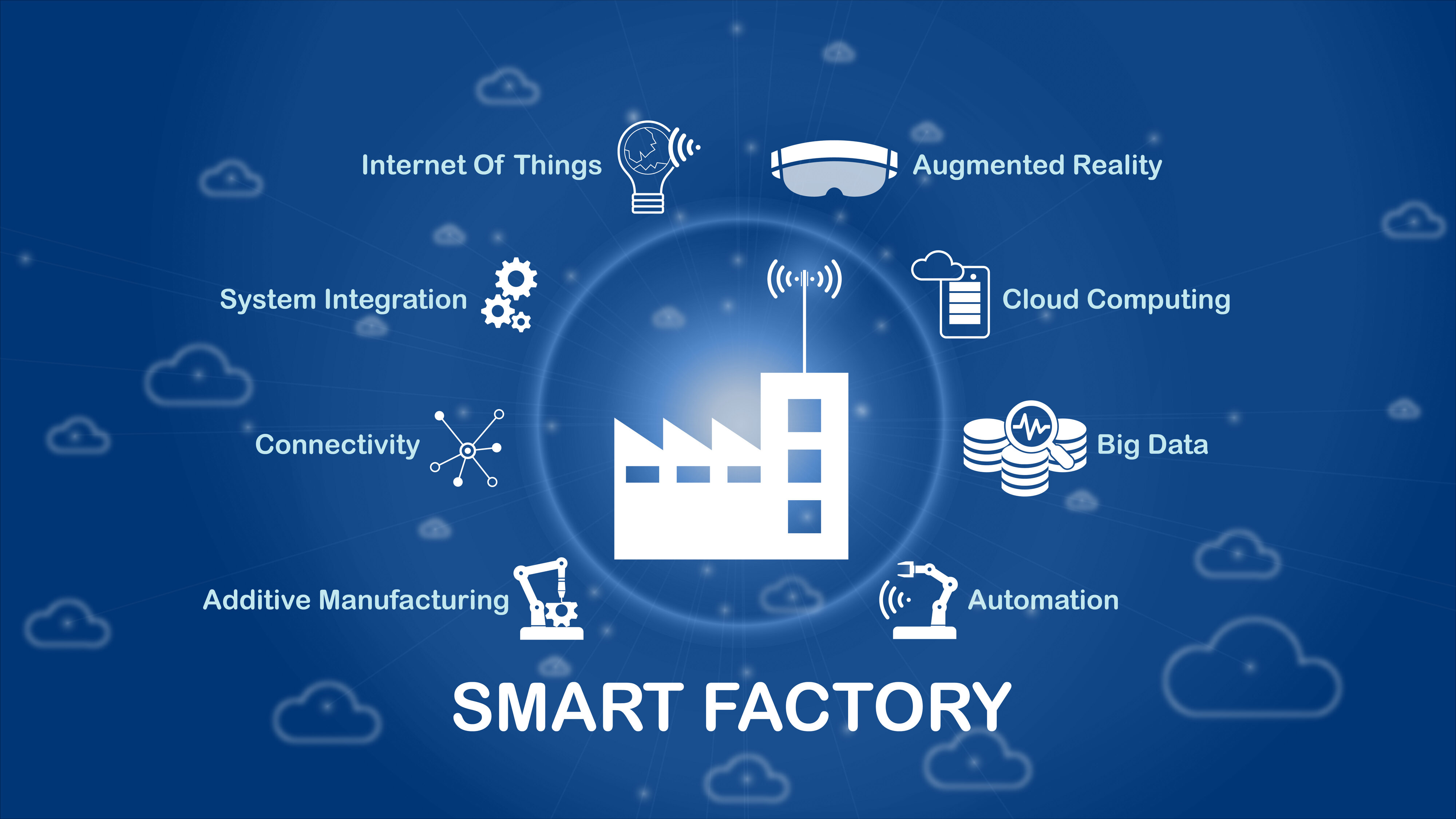
Structure of UNS
The structure of a unified namespace system typically consists of several components, including:
1. Central Hub
This is the main component of the UNS system. The hub is the central point of communication and integration for all devices and systems within the manufacturing facility. The network infrastructure typically includes a database that stores the URIs for each device. It manages the communication and integration of these devices.
2. Connected Devices
For a UNS to be effective, you must connect all the devices and systems within the manufacturing facility to the network. This includes things like sensors, control systems, and production equipment.
3. Communication Channels
Communication channels are the pathways used to exchange data between the different devices and systems within the manufacturing facility. These can include things like cables, wireless networks, and the Internet.
4. Software
This software is used to manage the communication and integration of the various devices and systems within the manufacturing facility or plant floor. This includes the UNS software and any other specialized software that is needed to manage specific devices or systems.
5. Cybersecurity
A UNS involves the exchange of large amounts of data. This makes it essential to have strong cybersecurity measures in place to protect against potential threats.
6. Training
Train employees on how to use the UNS and the various devices and systems connected to it.
Benefits of UNS in Manufacturing Maintenance
A unified namespace can help a manufacturing company in several ways:
- Improved communication and integration. A UNS allows for seamless data exchange between different devices and systems within a manufacturing facility. This helps improve communication and coordination during maintenance activities.
- Increased efficiency. By allowing for the integration of various systems and devices, a UNS can help streamline maintenance processes and reduce the time and resources needed to complete tasks.
- Enhanced decision-making. The UNS allows for collecting and analyzing large amounts of data in real time. This can be used to make informed decisions about maintenance activities and optimize performance.
- Increased predictive maintenance. The UNS can be used to monitor the performance of various systems and devices. This allows for the identification of potential maintenance issues before they occur. In addition, this helps to reduce downtime and improve the overall efficiency of the manufacturing facility.
- Easier Remote monitoring. The UNS allows for the remote monitoring of various systems and devices, which can be useful for maintenance activities performed remotely or remotely supervised.
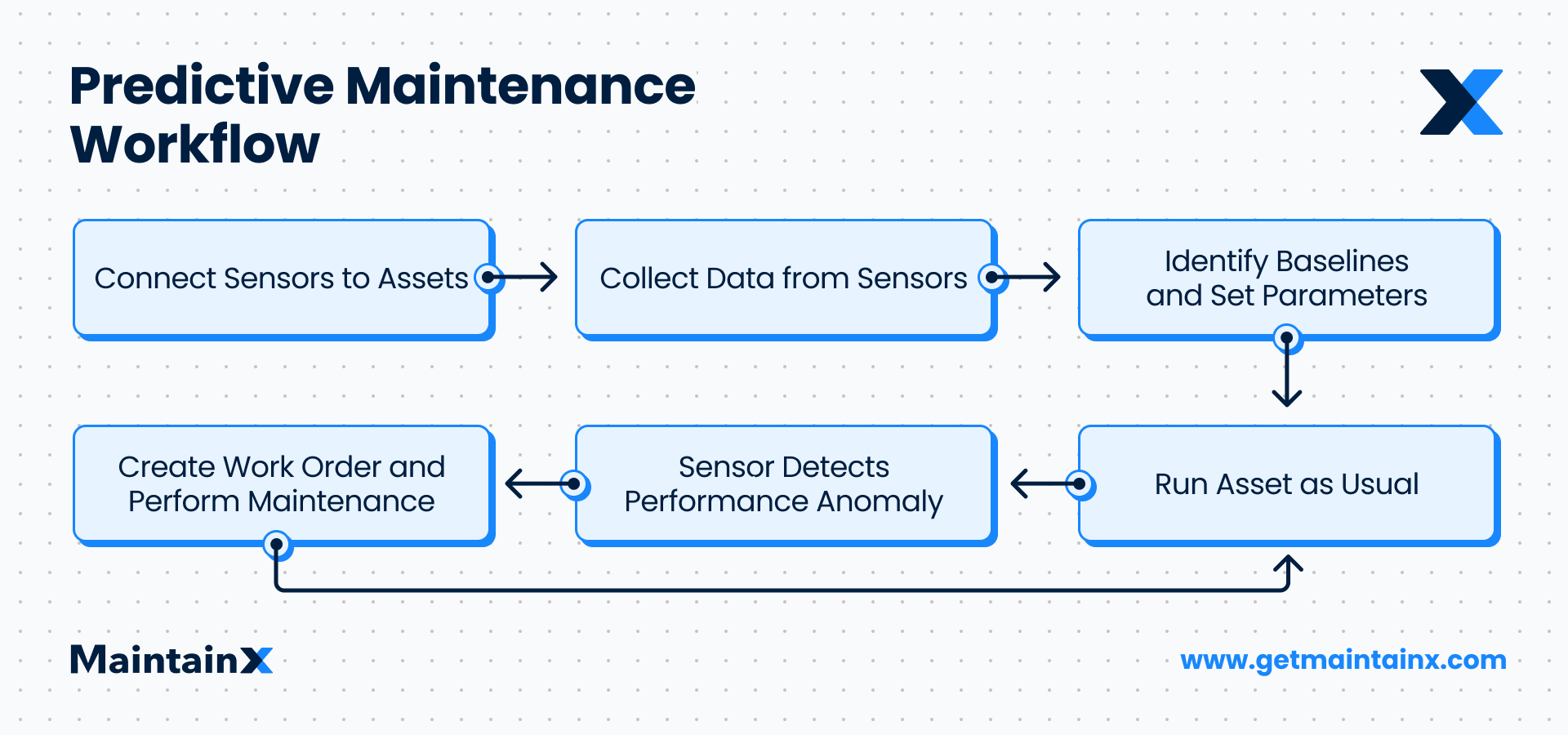
UNS and Improved KPIs
Unquestionably, a UNS can improve KPI tracking and analysis in manufacturing maintenance by automating processes and enabling real-time data collection and analysis. This can help identify trends and patterns in maintenance performance and areas for improvement. Specific KPIs that may be improved include uptime, mean time to repair, and maintenance costs. In addition, integrating a UNS with maintenance processes can improve efficiency and effectiveness, resulting in improved performance on these KPIs.
Overall Equipment Effectiveness (OEE)
OEE is a metric used to measure the efficiency of a manufacturing process. It considers factors such as availability, performance, and quality to calculate the percentage of time that a machine produces good parts at its maximum speed.
For example, if a machine is experiencing frequent downtimes due to maintenance issues, the UNS could be used to track the frequency and duration of these downtimes, as well as the root cause of the issues. In turn, this data can be used to improve the maintenance process and increase the availability of the machine, resulting in an improvement in OEE.
Planned Maintenance Percent (PMP)
A CMMS can help improve PMP by providing a tool for scheduling and tracking planned maintenance activities. This can help ensure maintenance is performed regularly and on schedule, reducing the risk of unplanned downtime.
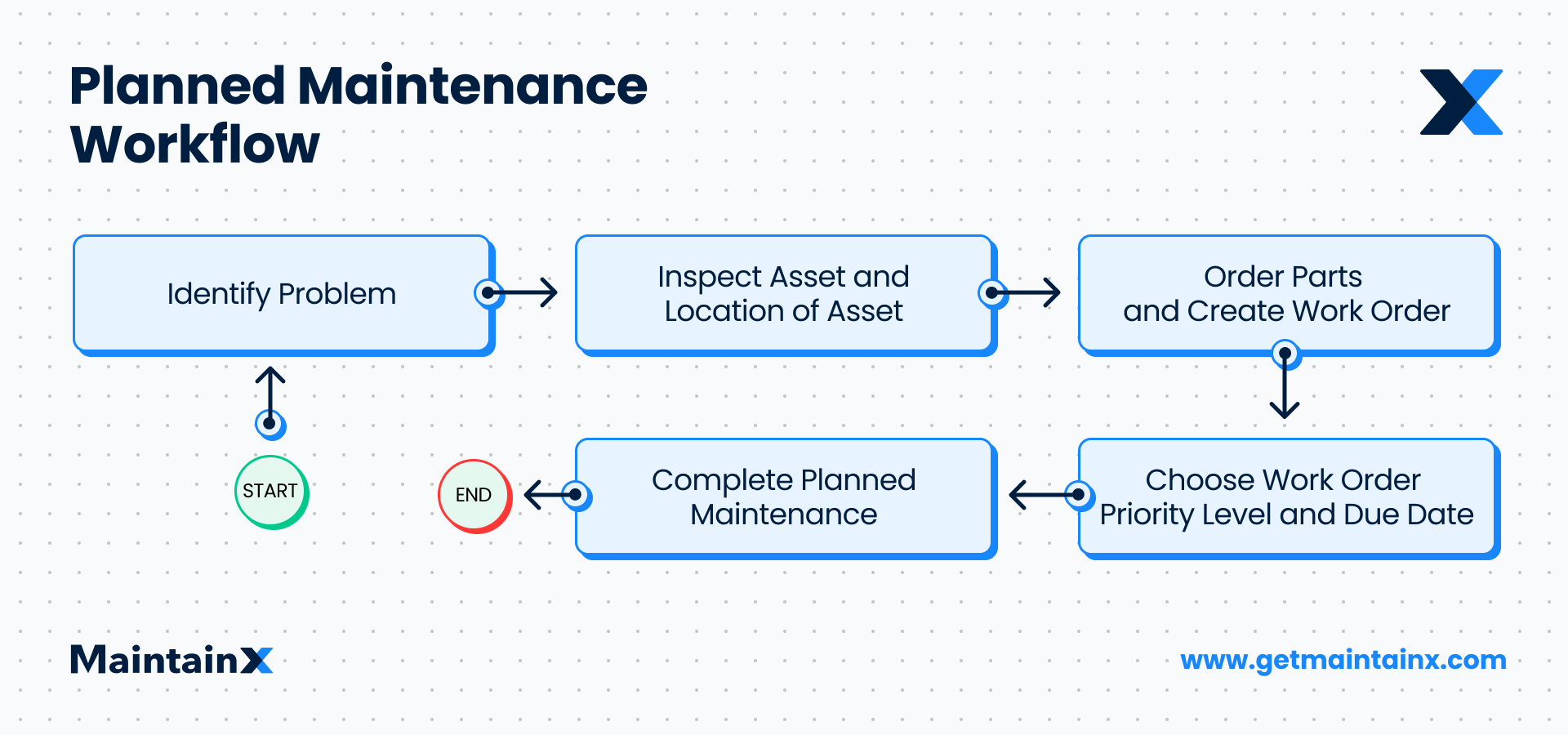
Mean Time Between Failure (MTBF)
A unified namespace system can help improve MTBF and MTTR by enabling quicker and more accurate equipment identification. Furthermore, this can be especially important when it comes to proactive maintenance. This involves identifying equipment at risk of failure and performing maintenance to prevent those failures.
Mean Time Between Failure (MTBF) is a maintenance metric that measures the standard amount of time between expected equipment failures for an asset performing under normal operational usage. Maintenance professionals use MTBF to inform equipment design, optimize preventive maintenance scheduling, and maintain reliability for their most essential pieces of equipment. For example, suppose a specific type of equipment has a higher failure rate than others. In that case, a UNS can help identify all of the equipment of that type and prioritize maintenance for those assets. This can help reduce the frequency of equipment failures and improve MTBF.
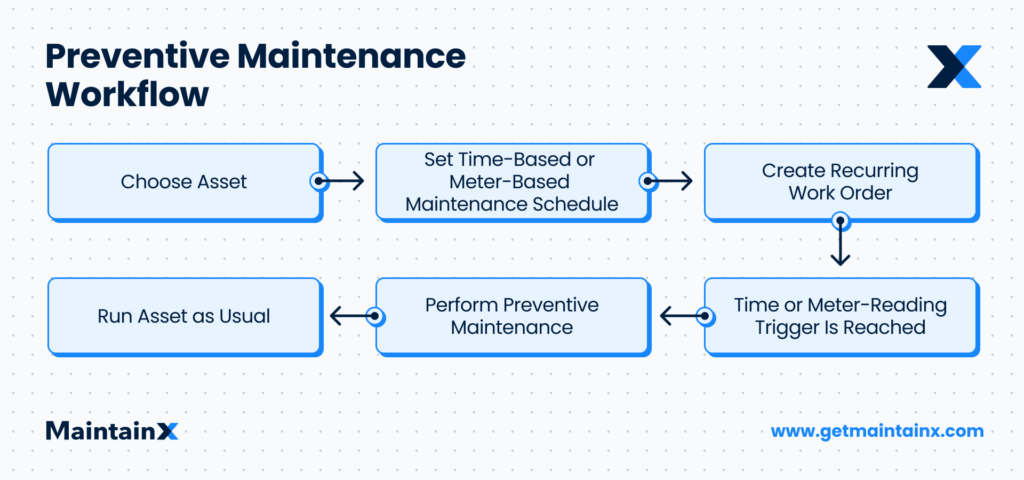
Mean Time to Repair (MTTR)
A unified namespace system can help reduce the risk of equipment failures due to human error, which can help improve MTTR. Mean Time to Repair (MTTR) refers to the average time maintenance teams spend diagnosing, fixing, and recovering failed pieces of equipment. MTTR is a baseline that maintenance departments use to improve asset efficiency, minimize unplanned downtimes, boost bottom lines, and assess equipment value. For example, if different departments or teams use different naming conventions for the same equipment, it can be challenging to accurately track and identify that equipment.
Digital Transformation and UNS
The digital transformation in manufacturing maintenance involves using technology to improve and optimize maintenance processes. This can include using industrial data analytics to identify trends and predict equipment failures, implementing advanced maintenance planning and scheduling systems, and integrating maintenance processes with other systems and processes within the manufacturing facility.
A UNS is an essential component of digital transformation in manufacturing maintenance, as it enables the integration and communication of various systems and devices within the manufacturing facility. In addition, this can facilitate the exchange of data between different systems and devices, allowing for the automation of many processes and the optimization of maintenance activities.
For example, the UNS can integrate a Computerized Maintenance Management System (CMMS) with other systems and devices within the manufacturing facility. This can allow for the automatic collection and analysis of maintenance data, enabling more effective maintenance planning and scheduling.
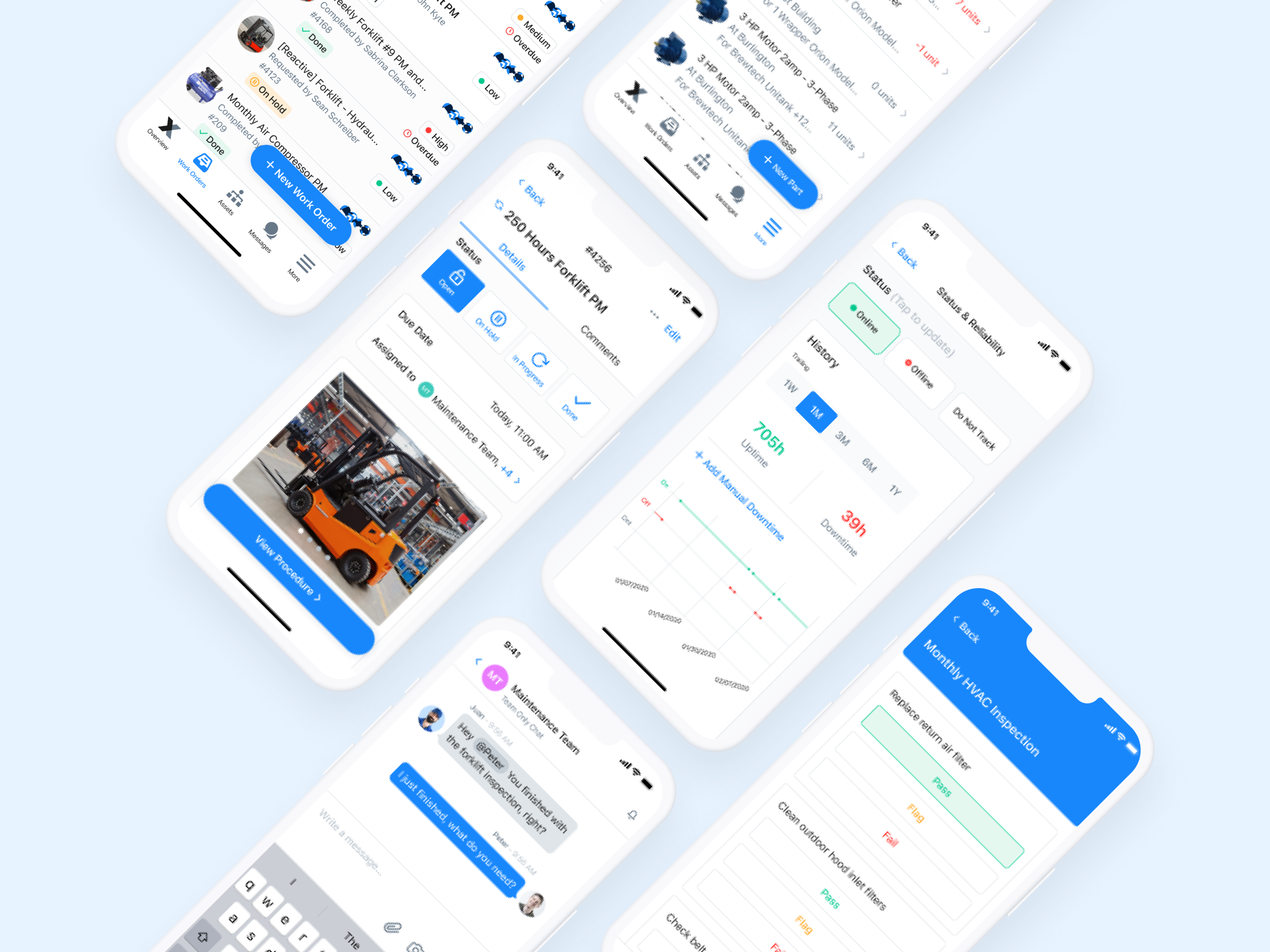
Let MaintainX Run Your UNS
One of the main ways that a CMMS helps with UNS and manufacturing maintenance is by providing a central database for storing and organizing maintenance-related data. This includes things like maintenance schedules, equipment histories, and repair records. In addition, the CMMS can be integrated with the UNS to allow for the seamless exchange of data between different systems and devices within the manufacturing facility.
Integrate UNS with MaintainX API and ERP
Use the MaintainX API to connect with, retrieve, and manage data associated with Work Orders, Work Requests, Assets, and more. An API (Application Programming Interface) is a set of rules for systems to communicate with each other. It allows integration and data exchange between systems. An API with a UNS can facilitate the integration and communication of systems and devices in a manufacturing facility. For example, an API could allow an MES to access and retrieve data from a machine monitoring system using the unique identifiers assigned by the UNS. The API and UNS enable data exchange and process automation in a manufacturing facility.
Likewise, ERP systems (Enterprise Resource Planning) are software platforms that allow companies to manage and integrate various business processes, such as accounting, supply chain management, and production planning, into a single system. With MaintainX, you can integrate your UNS across your company to provide a single data source that all departments can access.
In addition to providing a central database for storing and organizing maintenance data, a CMMS also includes several other features that can help with manufacturing maintenance. These include work order management, inventory control, and asset management. Using a CMMS, a manufacturing company can more effectively plan and manage maintenance activities, improving efficiency and productivity.
FAQs
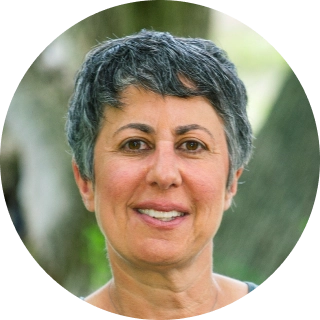
Caroline Eisner is a writer and editor with experience across the profit and nonprofit sectors, government, education, and financial organizations. She has held leadership positions in K16 institutions and has led large-scale digital projects, interactive websites, and a business writing consultancy.