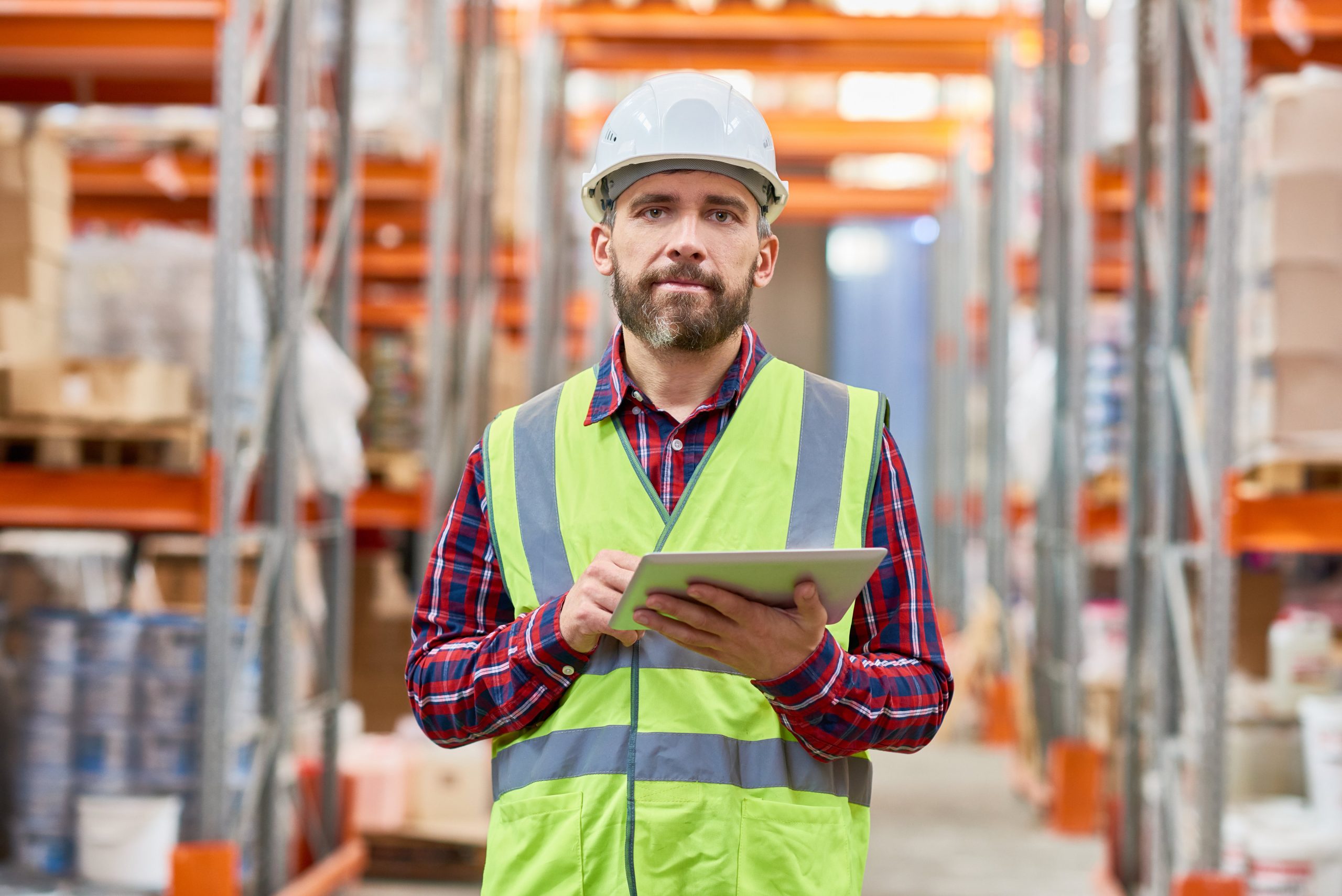
Imagine stepping into a busy kitchen for the first time and being tasked with preparing a complex dish you've never heard of before. How would you start? Now imagine having a detailed recipe that not only lists ingredients but also provides step-by-step instructions, common pitfalls to avoid, and even troubleshooting tips. You’d be able to approach your task without panicking and complete it with confidence. That's the power of a standard operating procedure (SOP).
An SOP is a written document with step-by-step instructions on how to complete an operational task. Organizations of all types use SOPs to achieve efficiency, uniform performance, quality control, and regulatory compliance, especially for critical tasks. Imagine you were actually in that kitchen and the added pressure of preparing that complex meal for a large number of hungry people within a tight deadline. Having that detailed recipe means you don’t need to spend extra time figuring out what to do. Similarly, when critical issues requiring maintenance work arise, time is everything, and SOPs can help your team get to work much faster.
However, reaping the benefits of SOPs requires proper understanding and effective implementation of their formats and types. Using one type of SOP when another is required can mean poorly completed tasks, wasted resources, lost time, and repeated work.
In this article, we’ll review the two types of standard operating procedures (technical and management), how to implement them, and ways to ensure you get the best out of them.
Two types of standard operating procedures: Technical and management
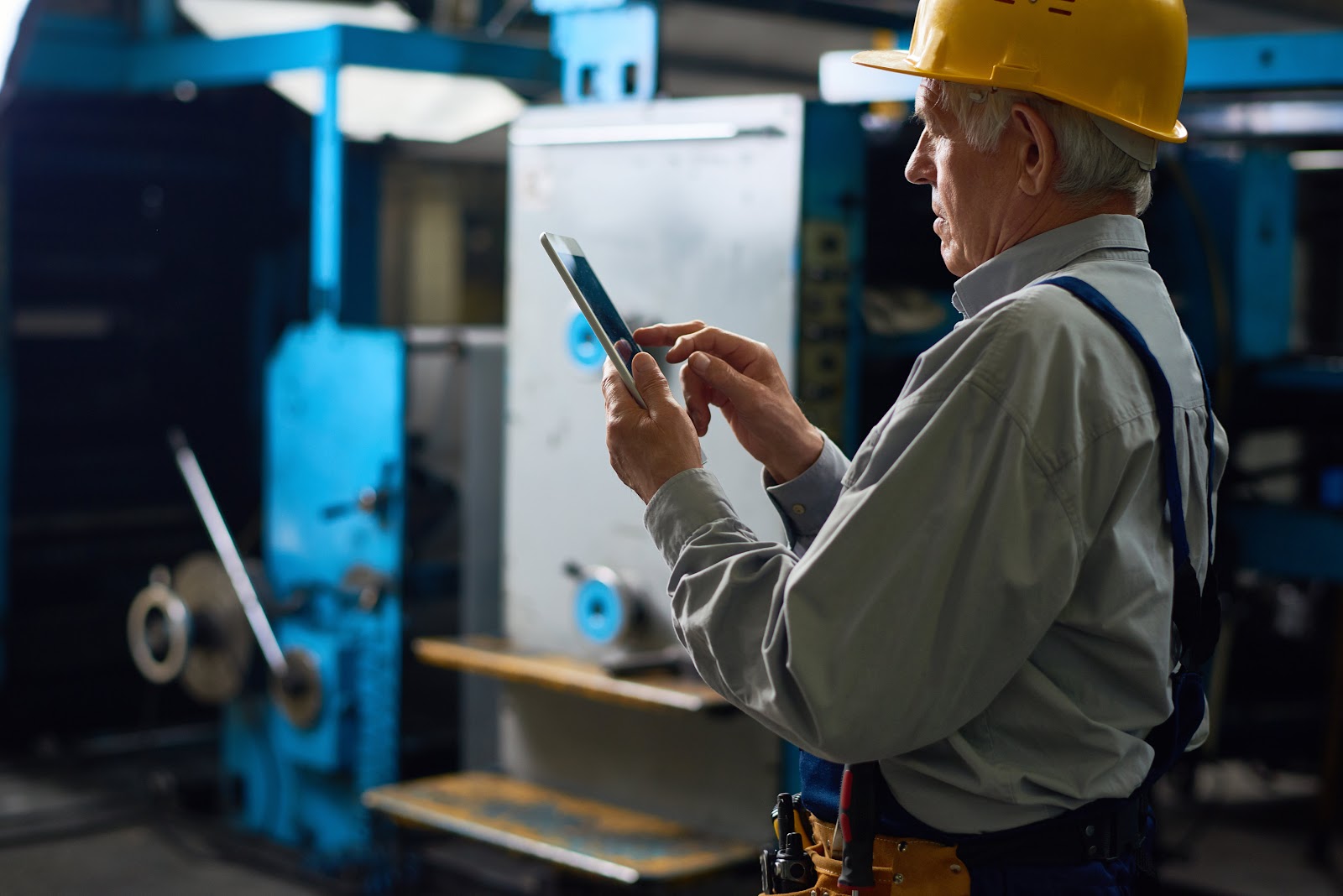
SOPs play roles across all levels of an organization and can involve executives, management, and frontline workers. As such, they can be organized by department, manager, function, and/or asset. However, one useful way to think about SOPs is to categorize them as technical SOPs or management SOPs.
Technical SOPs
Technical SOPs focus mainly on standardizing specific tasks. They break down the process of performing complex technical activities and are crucial in work environments that require precision, accuracy, and adherence to protocol. Many manufacturing and maintenance SOPs fall into this category.
For example, SOPs for operating specific pieces of equipment will guide users through the specifics of setup and installation, operation, maintenance, and troubleshooting.
Technical SOPs are important for:
- Equipment operation
- Maintenance processes
- Technical training
- Troubleshooting
- Safety procedures
Management SOPs
Management SOPs focus on providing a framework for efficient administrative and managerial practices within an organization. These SOPs include steps, guidelines, and best practices for managing organizational operations, like human resources and financial management, ensuring that their work is consistent and effective.
Unlike technical SOPs, management SOPs focus less on technical details, provide more general guidelines, and are more adaptable to different situations.
Management SOPs are useful for:
- Administrative processes
- Human resource management
- Financial management
- Corporate governance
- Project management
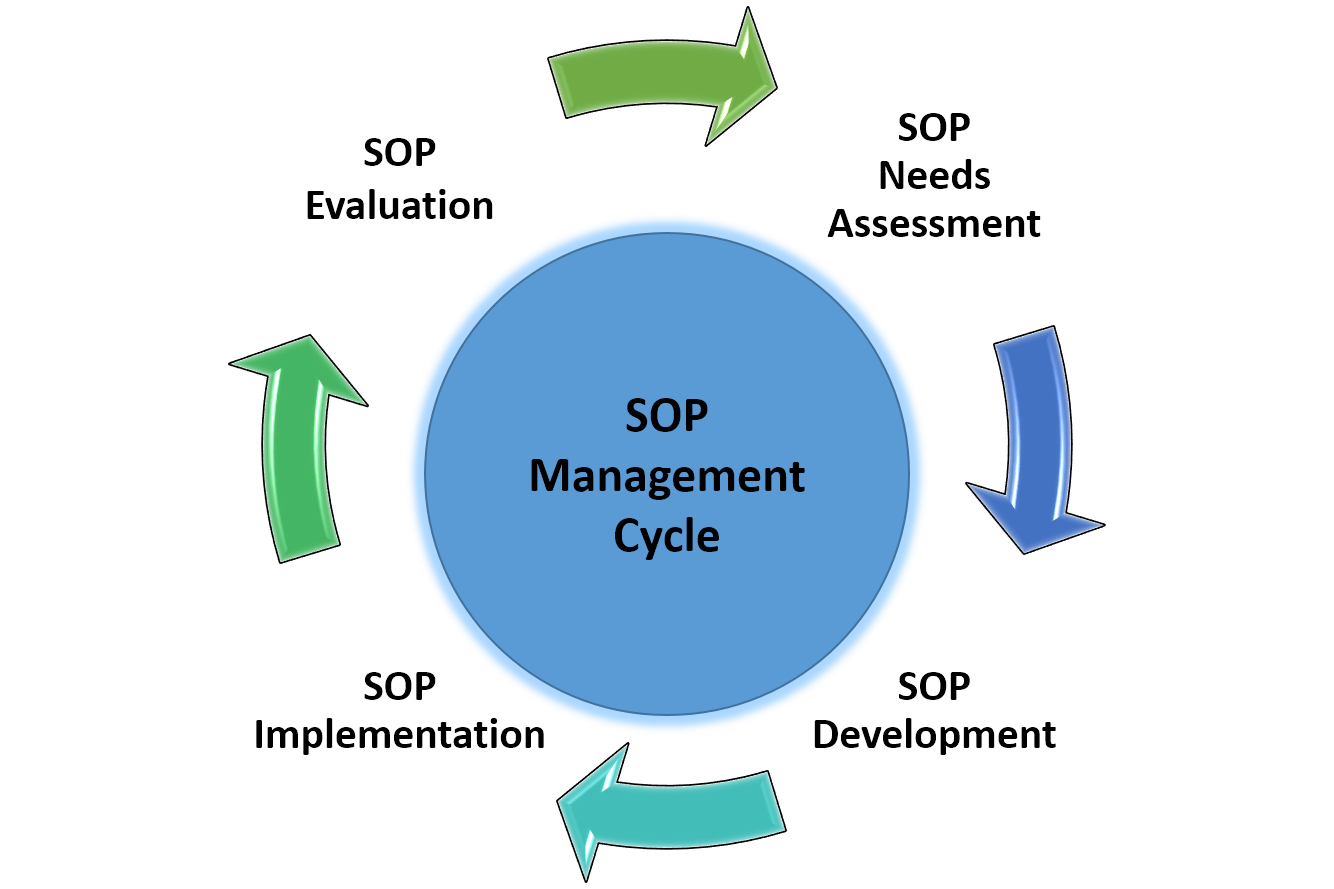
4 common SOP formats
There are different SOP formats that exist, each with its own strengths. The best one for you or your facility really depends on what kind of work you do and how your operations are set up. Here are four common formats you can choose from to make sure your SOPs are as effective as possible.
Step-by-step
This is the most straightforward SOP format. It involves creating a step-by-step guide of the activities required to complete a specific task. It is effective for procedures that require quick references, not too much detail, and don’t involve complex decision-making or multiple outcomes. Examples include simple steps for cleaning or starting up machines.
Flowchart
Flowchart SOPs provide visual representations of the steps involved in carrying out tasks. They typically use shapes connected by arrows which display the flow of the process, and are useful for complex processes that involve multiple decision points and potentially branching paths. The visuals help guide the user through various outcomes based on different decisions. Examples include maintenance workflows like the following:
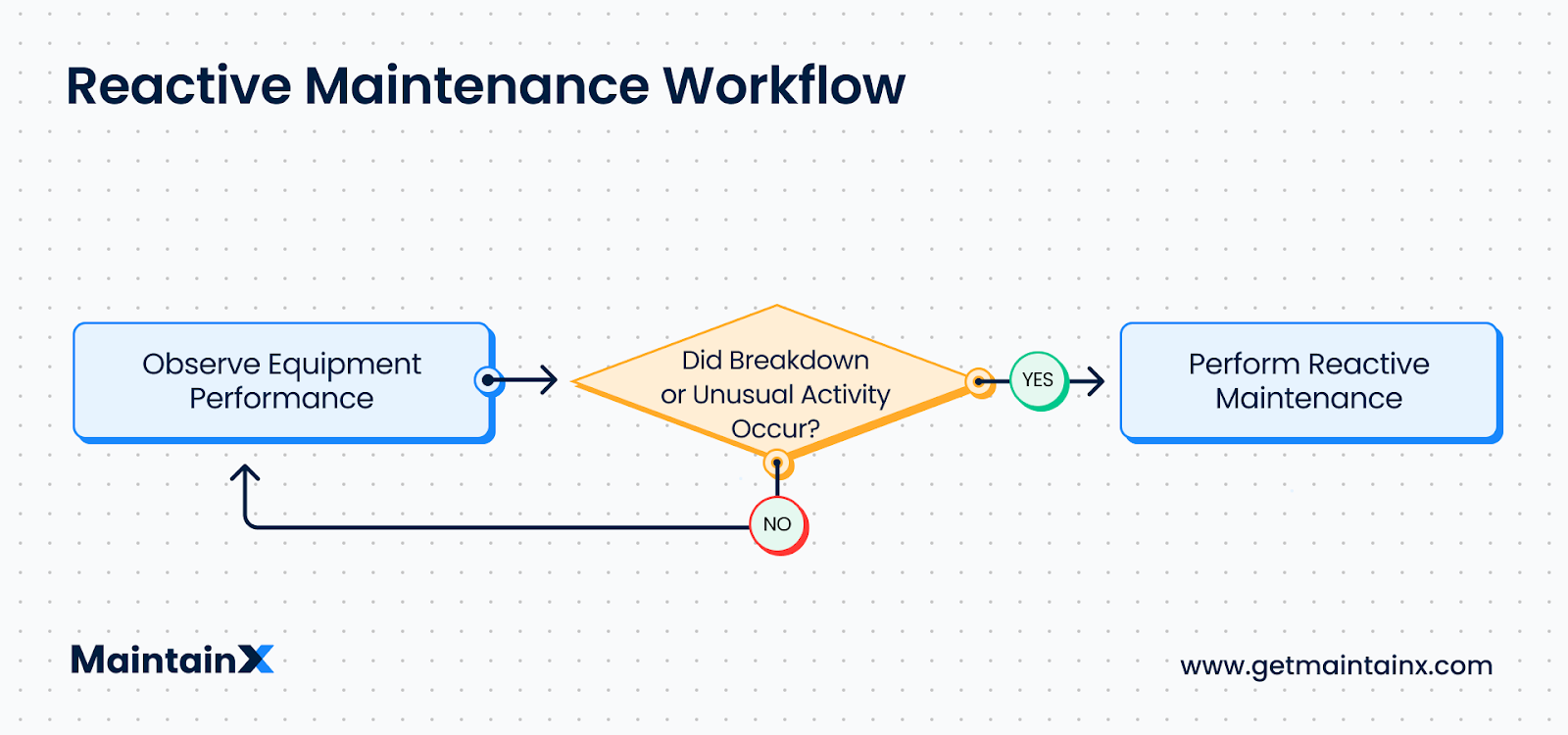
Hierarchical
The hierarchical format expands on the step-by-step approach and details procedures involving multiple layers of steps. This format is useful for tasks that must follow a specific order and include sub-steps, decision points, or conditional actions. Each main step is followed by indented sub-steps that provide further detail or explain conditional action. Examples include troubleshooting a piece of equipment or performing a detailed audit. For example, troubleshooting a computer issue might include:
1) Identify the problem,
1) Check the power supply
2) Verify the cable connections
2) Restart the system
1) Save any open files
2) Close all applications
Checklist
Checklists are SOPs structured as a list of items with accompanying checkboxes. They are similar to the hierarchical SOP and step-by-step formats but provide the added benefit of a checkbox as a visual aid to ensure users remember any outstanding tasks. Software like a computerized maintenance management system (CMMS) can support digital checklists, which streamline your work by allowing you to share real-time updates. In some cases, digital checklists can also create an extra layer of verification. MaintainX, for example, is a CMMS that has the added benefit of digital sign-offs to maintain an audit trail.
Let’s explore digital checklists and SOPs more now.
The benefits of digitized standard operating procedures
Both technical and management SOPs can take multiple forms, regardless of whatever format you choose. Whether using checklists or hierarchical steps, you’ll have to decide whether or not you want to depend on paper workflows or to use digital methods. However, CMMS's ability to digitize your SOPs offers greater flexibility and visibility. Here’s how:
Simplified audits
By using cloud-based checklists, you can ensure that auditors and inspectors have immediate access to up-to-date information from any location. If you’ve ever had to prepare for an audit while depending on paper-based systems, you know how time-consuming and laborious it is to gather binders and files of paper. With digital checklists, you can eliminate that stress while also enhancing the efficiency and accuracy of auditor reviews. Digital accessibility ensures that they can track compliance and spot issues in real time, reducing the likelihood of oversight.
Streamlined workflows
Digitizing SOPs allows all stakeholders to access necessary guidelines and resources seamlessly, minimizing miscommunications or interruptions from confusion. This real-time access reduces the dependency on physical documents and manual updates, leading to a smoother and more reliable workflow. In addition, the standardized processes ensure that all workers follow the same steps and protocols. This consistency enhances the quality of your output and reduces errors, fostering a culture of reliability and excellence.
Quicker employee training and onboarding
Digital SOPs provide a dynamic platform for training employees on new procedures, with interactive elements that can enhance learning and retention. Managers can easily update the SOPs and instantly disseminate the changes, ensuring all employees are up-to-date with the latest practices. In addition, established, effective SOPs can act as training materials to help new employees familiarize themselves with existing workflows.
Enhanced compliance
Digital SOPs can help you ensure that your procedures are always aligned with the latest quality standards and regulatory requirements. You can create automated updates and alerts about new regulatory requirements, ensuring that your team stays in compliance at all times. This process helps maintain standards and mitigates the risk of any legal issues due to non-compliance.
Why do SOPs sometimes fail?
Not surprisingly, one reason technical SOPs sometimes fail is that management hasn’t created a process for them to succeed. Whenever procedures, employees, assets, and/or functions change, managers should update and re-approve SOPs.
In fact, high-quality SOP reviews ensure that policies and procedures are up-to-date, cost-effective, and compliant with new or changing regulations, standards, and quality assurance plans.
Also, when employees change jobs, managers need to train new employees to ensure they meet quality and safety standards. That means the best SOPs should be clear, concise, and easy to follow. In fact, failure to follow a company’s standard operating procedures is a common observation during inspections.
In summary, some reasons SOPs fail are:
- Lack of clarity
- Poor or outdated content
- Lack of training
- Inaccesibility
- Overcomplexity
- Inadequate integration with existing work processes
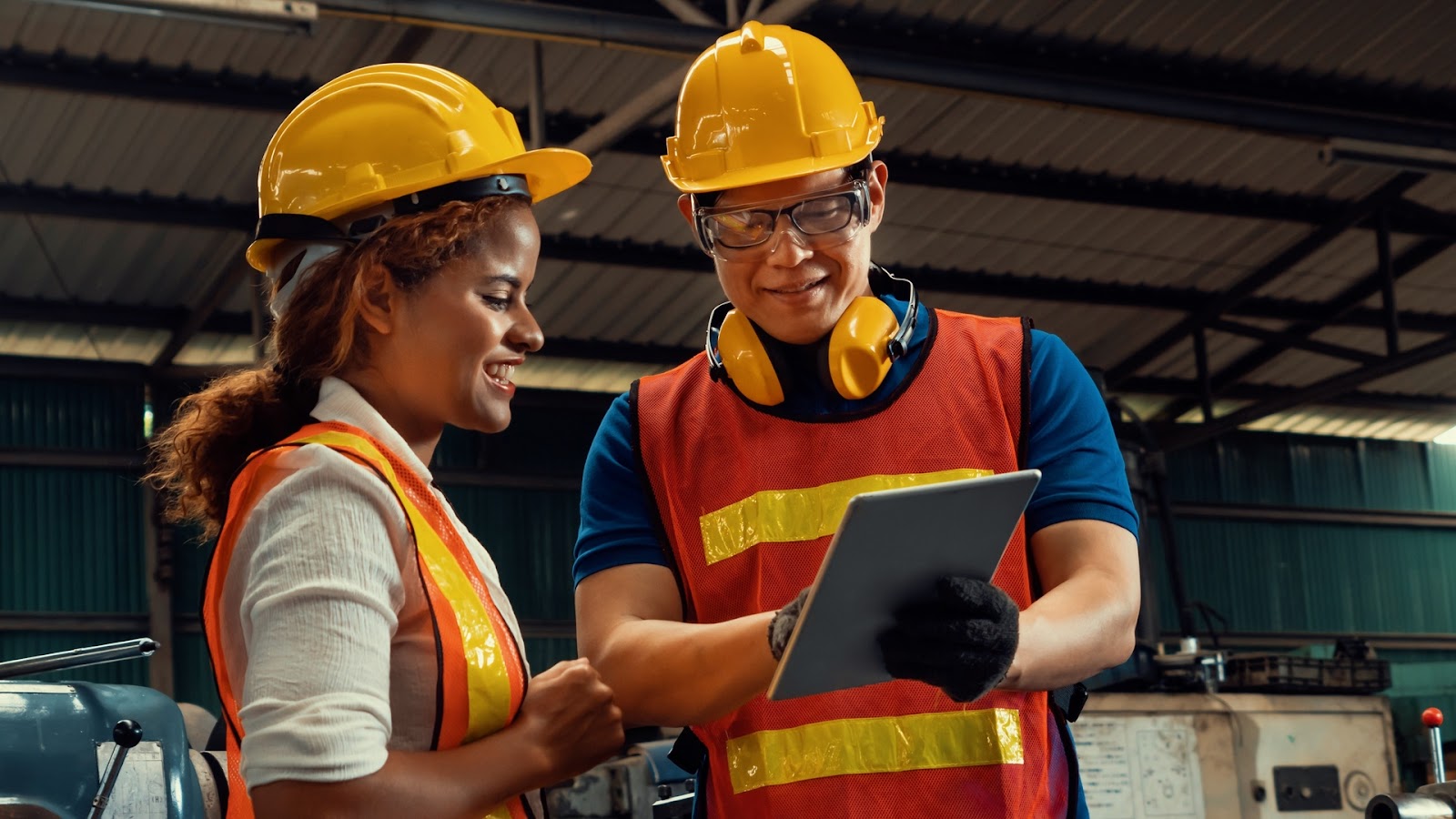
How to enhance SOP compliance
One of the best ways to ensure workers follow SOPs is to explain why they are important. Then, once employees know why an SOP is in place and why they should follow it, success comes down to developing accessible, clear, and user-friendly documents so that they can effectively use them.
According to the Food and Agriculture Organization of the United Nations (FAO), the purpose of a standard operating procedure is to “carry out the operations correctly and always in the same manner.” Most importantly, the FAO says that an “SOP should be available at the place where the work is done.”
This is another reason for you to digitize SOPs: When they’re in the cloud, no one needs to return to the office to retrieve a hardcopy notebook on the shelf. Digital SOPs on a handheld device translate into guidelines, work orders, and checklists that follow wherever you go.
Streamline both types of standard operating procedures with MaintainX
Summing it all up, implementing different types of SOPs through a digital solution such as MaintainX will improve an organization’s metrics and key performance indicators. MaintainX’s cloud-based platform allows companies to operate with the assurance that all processes are available, consistent, and repeatable. With MaintainX, you can:
Streamline your SOP creation
MaintainX enables you to create digital SOPs from scratch or by editing existing SOP templates. In addition, you can quickly and easily review and revise your SOPs and share real-time updates when necessary, all from your mobile device. To make your work even faster, MaintainX contains an AI-powered procedure generator that means you don’t have to write new SOPs from scratch. All you need to do is supply a few key details and let MaintainX generate your SOP for you.
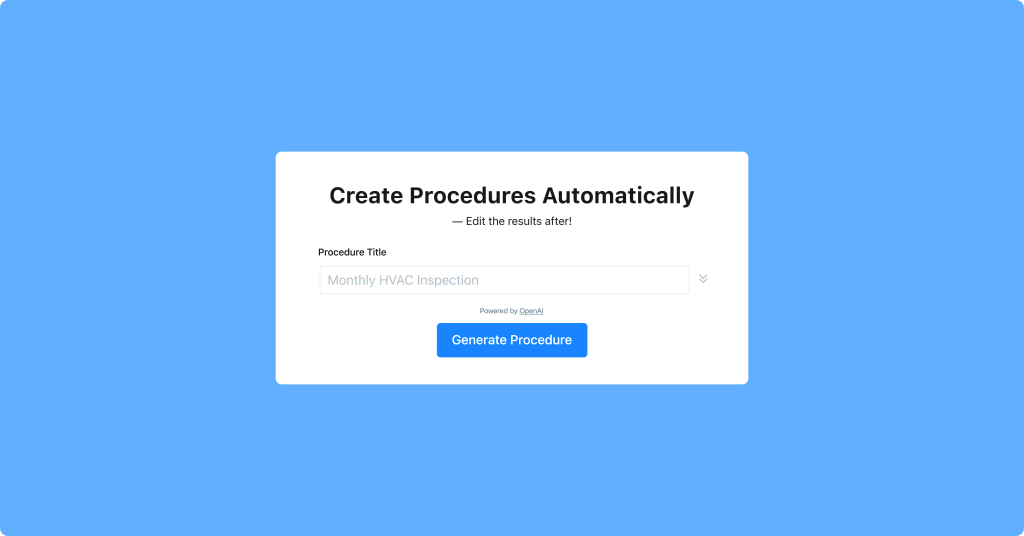
Automate SOP assignments
MaintainX’s work orders module allows you to automate SOP assignments in advance and according to your schedule. MaintainX also enables workload-based scheduling as part of the resource planning module to ensure you assign the right employees to the right tasks. With real-time labor insights, you can assign SOP tasks based on workload and capacity.
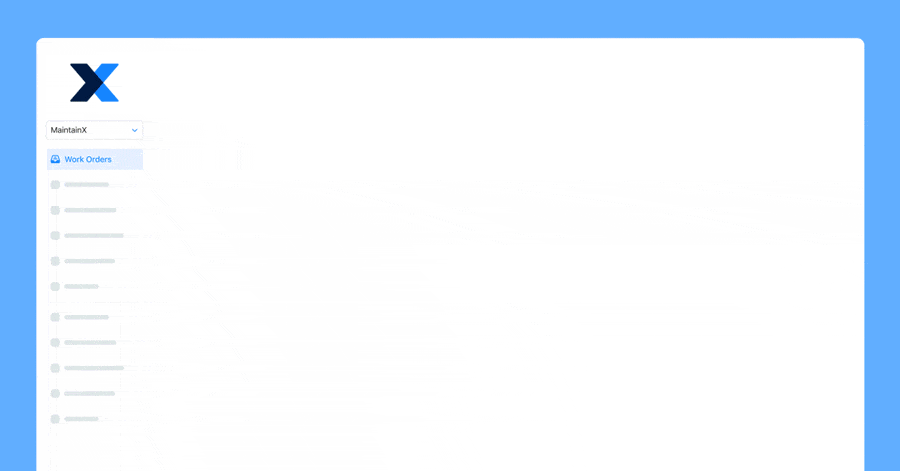
Monitor employee performance of SOPs
With MaintainX’s reporting module, you can monitor the impact of your SOPs by tracking relevant metrics and generating actionable insights. Instead of simply assigning tasks without knowing what difference they’re making, this feature allows you to pull up at-a-glance visualizations of your operational performance. You can also create custom dashboards to save time on administrative reporting, quickly identify areas for improvement, and drive operational excellence.
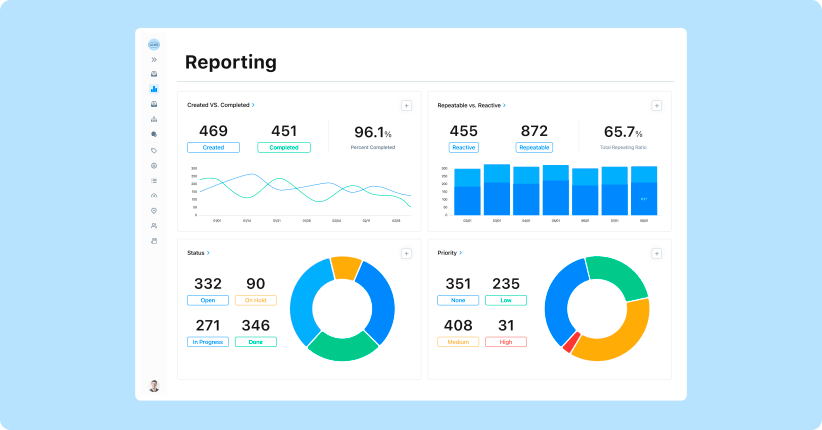
Enhance SOP compliance with e-signatures
For an extra layer of accountability, you can require e-signatures as part of your procedures in MaintainX. Managers can add the e-signature option when assigning work orders and then check to ensure technicians have completed their work satisfactorily before approving.
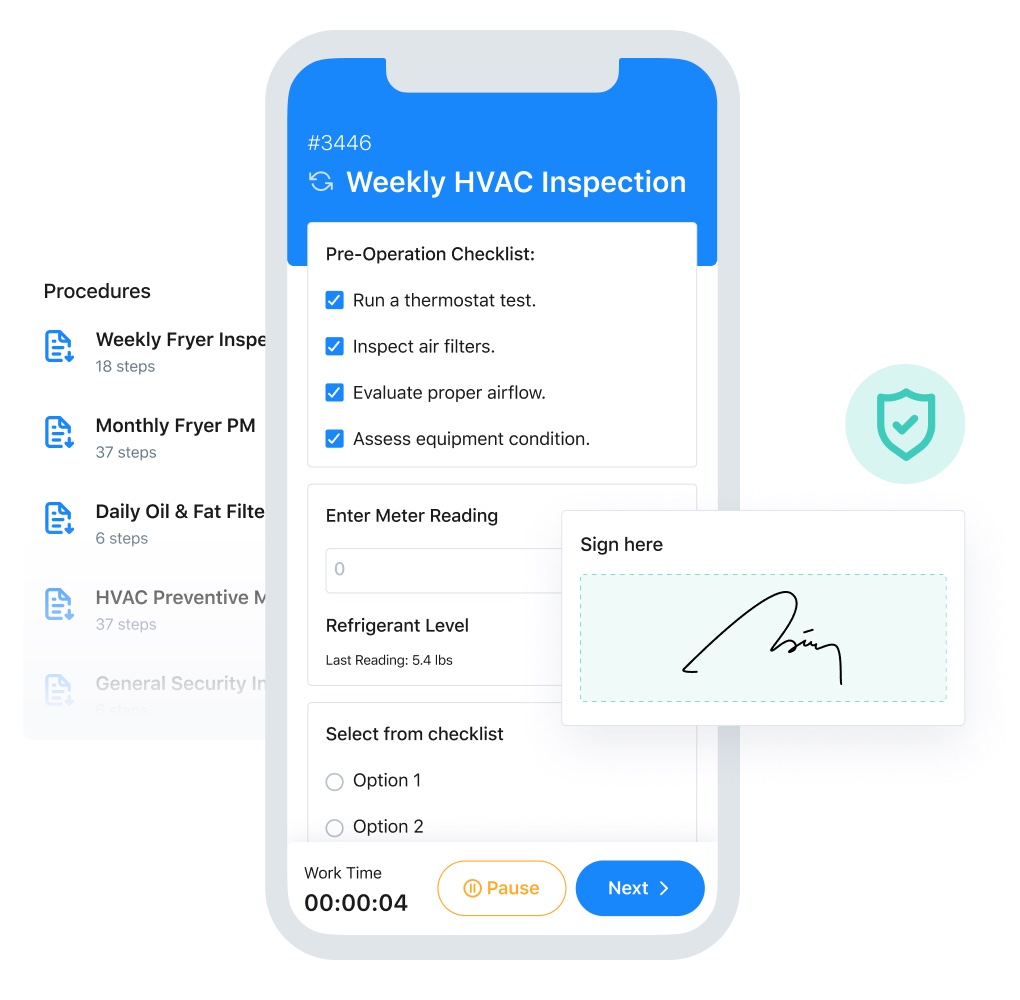
FAQs
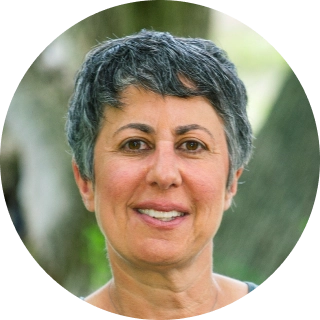
Caroline Eisner is a writer and editor with experience across the profit and nonprofit sectors, government, education, and financial organizations. She has held leadership positions in K16 institutions and has led large-scale digital projects, interactive websites, and a business writing consultancy.