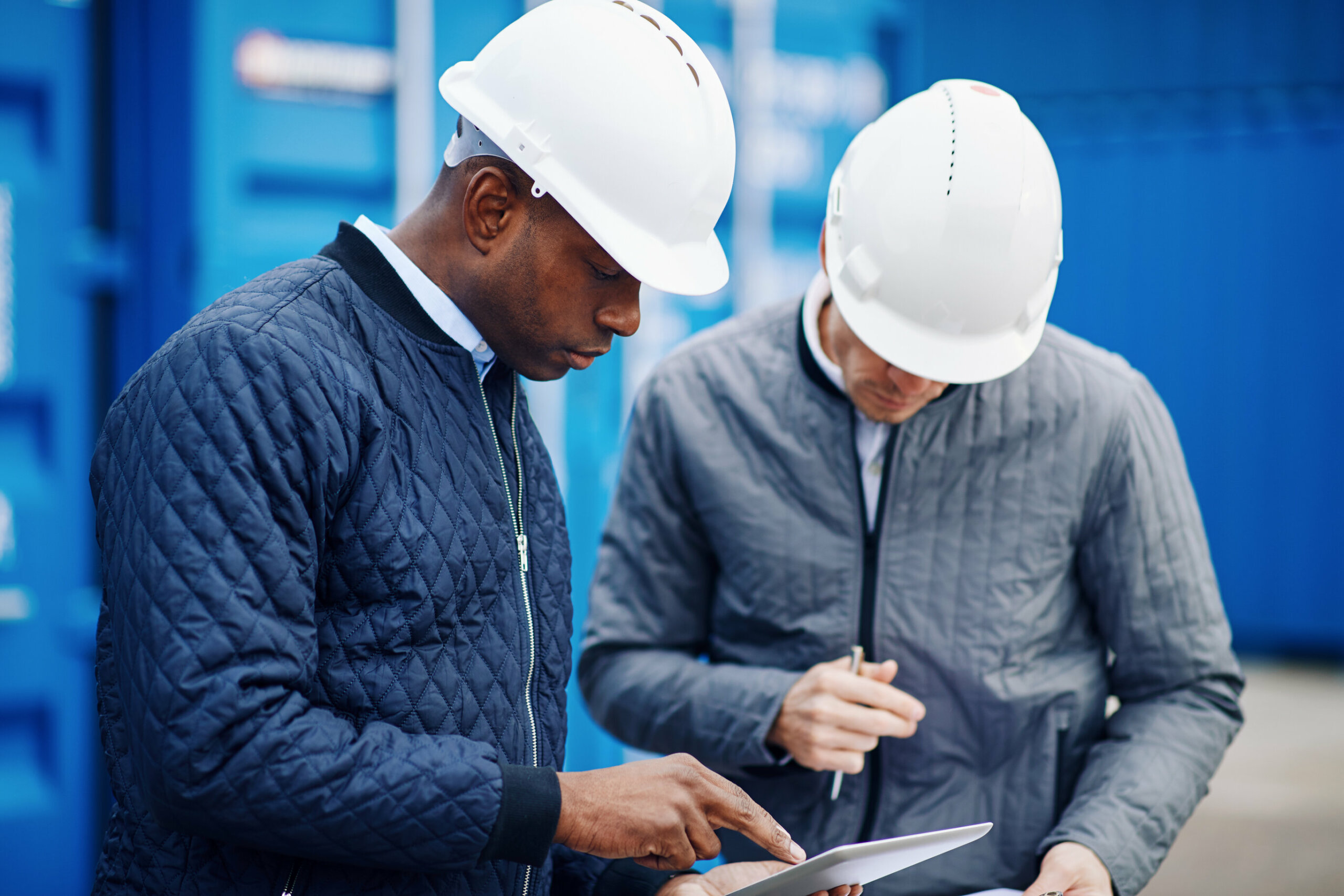
It’s not unusual for operations managers to use the words “process” and “procedure” interchangeably. But when do we use which: process vs. procedure? Or, do they mean the same thing?
Like other terminologies within industry spheres, this debate has likely been the subject of private internal dialogues for ages.
The good news is that the confusion ends today. But, yes, there is a difference between process vs. procedure.
Keep reading to learn how these terms relate to business needs, how workflows help streamline procedures, and how you can automate your processes and procedures for increased efficiency.
The Difference Between Process and Procedure
The primary difference between process and procedure is in terms of depth. Processes are strategic frameworks that guide how work is done. Procedures are detailed, task-specific instructions that dictate how a particular activity or task should be performed within the context of a process. Both are essential in ensuring efficiency, consistency, and quality in business operations.
Another way to think about the difference between process and procedure is this: processes describe the “what,” while procedures answer the “how.” A process outlines the series of steps to follow for a particular goal. A procedure is a specified way of following the steps.
Thus, the most notable difference between the two words is broad information vs. detailed information. Below is an example of how the two terms may function in practice.
“So you’ve developed procedures and processes and connected them to systems that are functioning within your company. Now what? Integrate those systems and leverage technology to automate wherever possible.”
Forbes
What is a "Process"?
ISO 9001:2015 defines a business process as “A set of related or interacting activities, which transform inputs into outputs.” As previously mentioned, processes refer to the general steps needed to achieve a particular outcome.
However, they don’t provide details about how the technician should complete the task. Processes are typically composed of input, procedures, and outcomes.
The number of processes your organization has depends on your type of business, its size, your industry, and your goals. It’s worth emphasizing that there are many types of processes, and some can span various departments.
However, each department will engage in specific processes (or a specific part of a process) unique to its individual goals and objectives.
For example, a company’s marketing department may collect lead information through a landing page form that is automatically relayed to the sales department’s CRM software. Both departments are part of the process of lead generation.
Now, let’s take a closer look at the definition of “procedure.”
What is a "Procedure"?
Procedures refer to detailed instructions on completing specific tasks as part of an overarching process.
Standard operating procedures (SOPs) outline the order of specific steps that technicians need to follow to reach the goal.
A series of procedures combined to produce the desired outcome generates a process. Thus, procedures can be thought of as “the building blocks,” or steps, of processes.
Example of Process vs. Procedure
Steve owns seven McDonald’s franchise locations. Like many franchise owners, Steve was drawn to the franchise business model because it comes with proven processes.
Examples of routine McDonald’s processes include taking customer orders, relaying orders to cooks, and delivering orders when ready. Of course, Steve must put effort (input) into achieving his goal of nurturing steady streams of customers (outcome).
However, Steve doesn’t need to reinvent the wheel. McDonald’s executives have spent countless hours developing trustworthy protocols (procedures) to produce dependable products.
Steve uses MaintainX to write, digitize, and assign McDonald’s recommended equipment maintenance procedures. Steve also uses a corporate distribution system to train new employees and assign procedures to workers.
This way, his store supervisors and maintenance technicians always know precisely how to complete assigned procedures.
Sidebar: This is a true story! Steve saves 20 to 30 management hours per week using MaintainX to automate preventive maintenance scheduling, parts management, and more.
Now that you understand the difference between processes and procedures, you may wonder how workflow maps fit into process improvement.
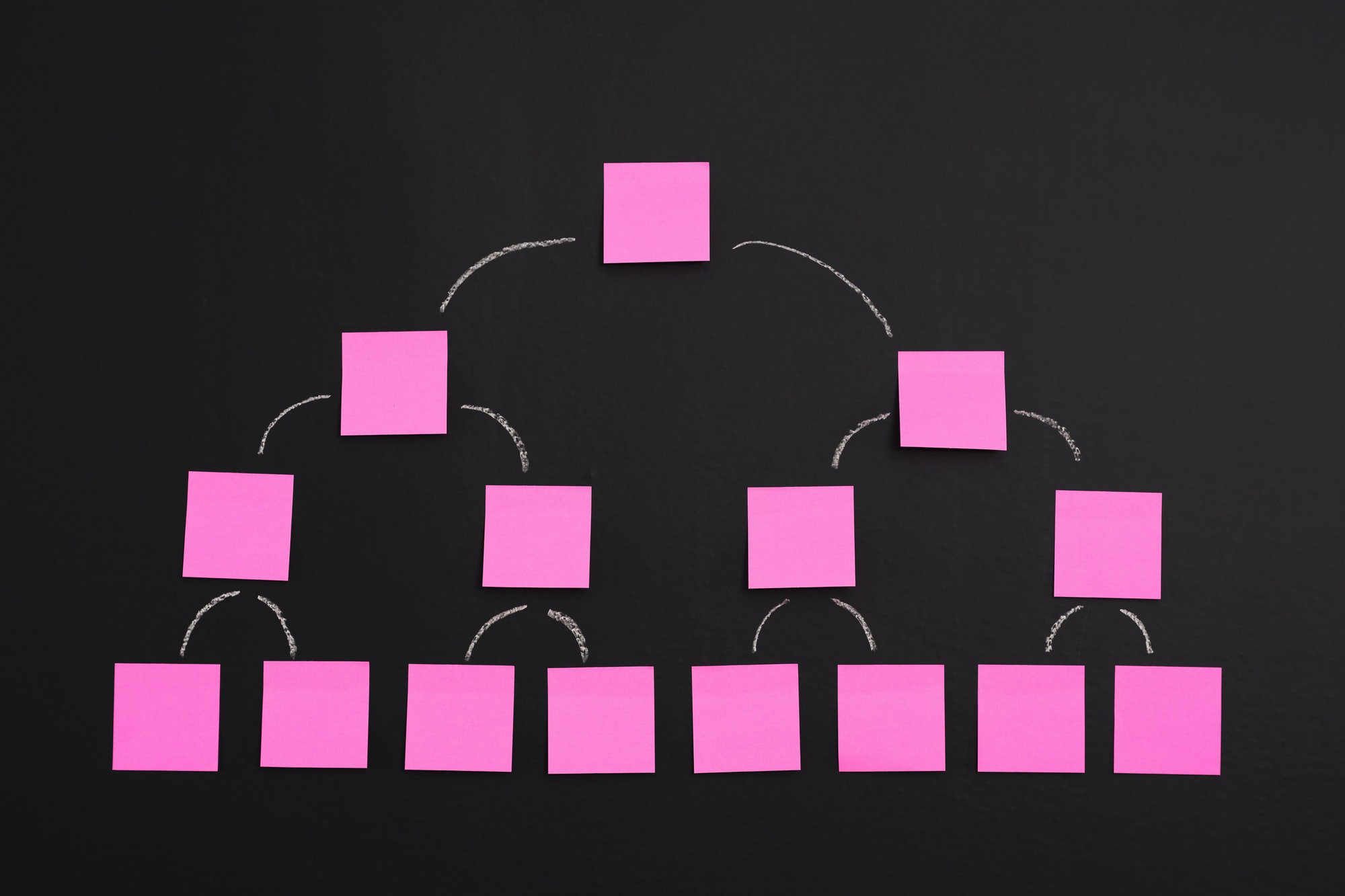
Advantages of Mapping Workflows
Workflow maps are illustrative tools created to better understand the sequence of events within a given task. Managers sketch flowcharts—also referred to as “process maps” or “process diagrams”—to visualize the steps involved in completing processes and procedures.
The advantages of mapping your workflows include the following:
Uncovering Hidden Bottlenecks
Successful companies aim to eliminate waste and improve their processes. But it’s sometimes difficult to identify which aspects need improvement without a visual aid. Workflow mapping helps identify, isolate, and resolve problem areas so management can trim unnecessary process waste.
Enhancing Compliance
No matter how small a business, complex industry regulations and audit requirements can make even the most straightforward processes more difficult. Again, mapping workflows can provide a visual representation of overlooked regulatory procedural checks that can later result in penalty fees if left unresolved.
Simplifying Employee Onboarding
Despite even the best efforts to keep employee turnover rates low, workers move on. Workflow maps make it much easier to explain complex procedures to new employees. Workflow maps also can help redistribute work orders to employees.
Enhancing Teamwork
Workflow mapping helps a company maintain a unified vision of the big picture and smaller goals. In addition, mapping helps connect SOPs to workers, thus making them feel part of the team. We like to say that “teamwork makes the dream work.
Other benefits of workflow mapping include helping enforce best practices, reducing the need for management troubleshooting, and decreasing the likelihood of human error.
Processes and Procedures in a CMMS
MaintainX provides operational and maintenance professionals with a CMMS (computerized maintenance management system).
A CMMS software platform automates maintenance scheduling, organizes historical asset data, and supports cost-effective O&M decision-making.
Our mobile and desktop applications allow users to assign technicians digital work orders (aka processes) with attached digital checklists (aka procedures).
Once technicians receive a notice of an assignment, they can open the work order for a quick overview of what needs to be done. The work order generally includes a general description, the location of the asset needing maintenance, the procedure for the work and a list of parts needed, among other components.
When the technician is ready to begin the project, the work order’s procedure will provide detailed guidance on what to do first, second, and so on.
Use Process Management Software for Work Instructions
As we’ve shown, processes and procedures go hand-in-hand. The former provides businesses with structure, efficiency, and quality-control safeguards. While the latter details step-by-step instructions that employees can follow to produce reliable results.
Understanding the difference between business process vs. procedure is the first step. The next step is to implement continuous improvement strategies like Lean Six Sigma.
Are you ready to document processes, streamline your business improvement efforts, enhance equipment reliability, and increase profitability? If so, we invite you to download MaintainX CMMS.
In addition to work order automation, our mobile-friendly business process management software allows you to customize procedural templates and communicate with team members via in-app messaging. You’ll love having a high-level view of operational activities alongside detailed reporting metrics at your fingertips.
Process vs. Procedure FAQs
Can Processes and Procedures Change over Time?
Yes, both processes and procedures can change. Processes tend to have a longer-term perspective and may change less frequently. Procedures, on the other hand, are more subject to updates and changes to adapt to evolving circumstances, technology, or regulations.
Can One Process Encompass Multiple Procedures?
Yes, a single process can encompass multiple procedures. For example, the "Quality Control" process in manufacturing can include procedures for product inspection, defect reporting, and corrective action. These procedures collectively contribute to achieving quality control within the broader process.
Can You Change a Procedure Without Affecting the Underlying Process?
Yes, you can update or change a procedure within a process without altering the entire process. This flexibility allows organizations to adapt to new technologies, best practices, or regulatory requirements while keeping the broader process intact.
FAQs
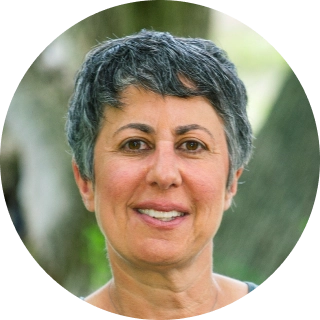
Caroline Eisner is a writer and editor with experience across the profit and nonprofit sectors, government, education, and financial organizations. She has held leadership positions in K16 institutions and has led large-scale digital projects, interactive websites, and a business writing consultancy.