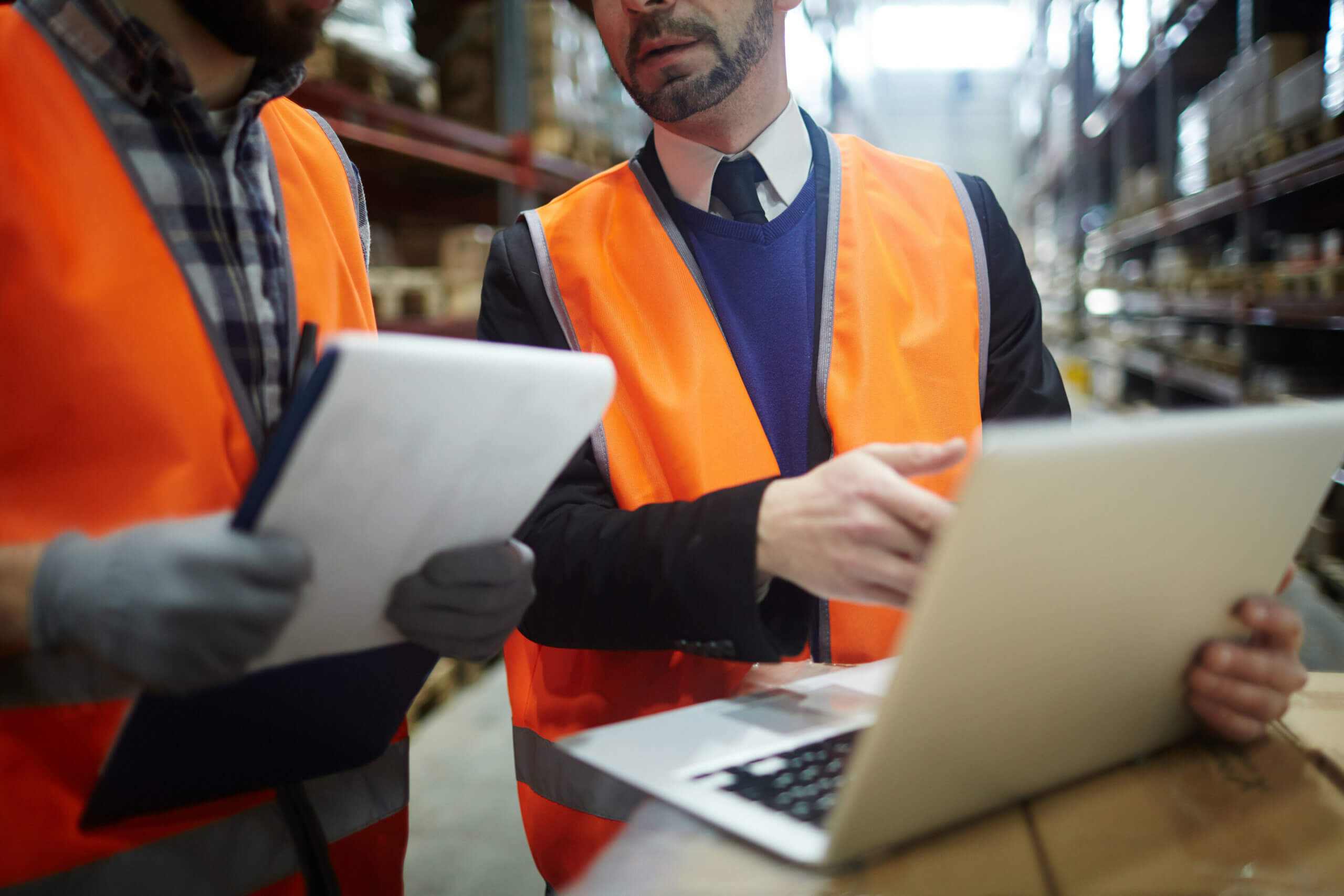
These days, integrating a CMMS with an ERP will cut downtime, increase efficiencies company-wide, and increase profit margins.
Organizations using ERP (Enterprise Resource Planning) software applications to optimize operations often run into obstacles managing maintenance operations. ERPs— like Microsoft Dynamics and NetSuite—are valuable tools for finance and human resource departments but do not offer all of the functionality and reporting advantages that maintenance departments need.
Integrating Your Existing ERP with a CMMS
The best modern computerized maintenance management software (CMMS) can access and make smart use of the real-time maintenance data both on the factory floor and in the corporate office. MaintainX provides REST APIs and integrations that pull real-time data directly into ERPs. And, the best part is that maintenance departments and teams are able to use the best CMMS systems available to them.
To be clear, CMMS software won’t replace your ERP. Nor should it. Rather, a computerized maintenance management system offers specific and unique functionality necessary to run an efficient and productive maintenance program. APIs and integrations with your ERP will make the addition of a CMMS maintenance software seamless.
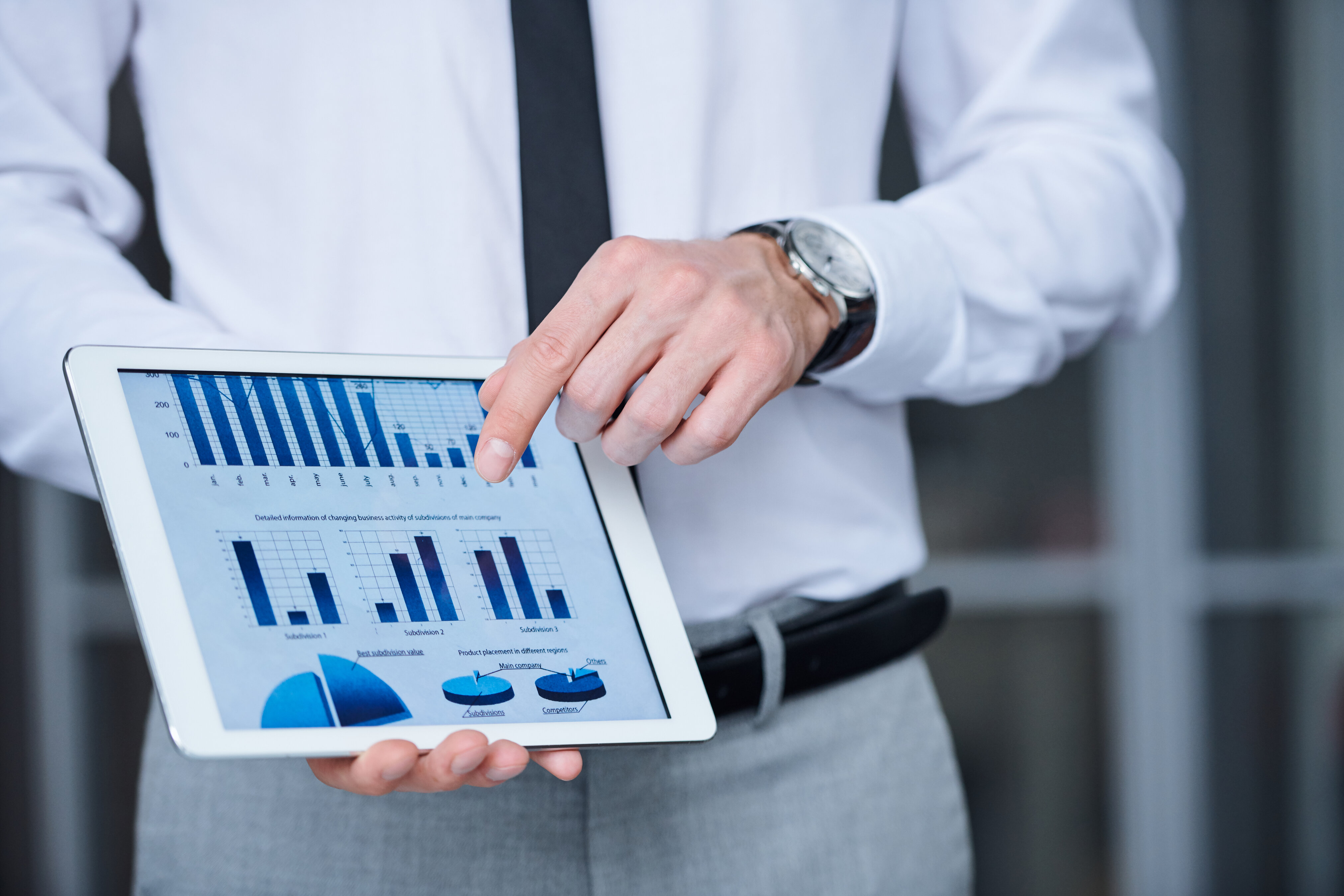
The Role of ERP Systems in Systems Integration
As Plant Engineering recently posted, “Not all ERP modules are created equal. When it comes to maintenance management, ERP may fall short in ease of use and quick implementation. Expensive customization can be required to fit the ERP’s enterprise asset management (EAM) system to the maintenance organization’s workflow, including routine preventive maintenance (PM), work orders (WOs), and detailed asset-maintenance analysis.”
In case you don’t know, ERP integrates business software applications and business processes into one platform. Previously, we needed one software for accounting, another for Human Resources, and still another for project management or contracts or sales. ERPs, such as Microsoft Dynamics 365 or Sage X3, now compile and link these software systems all into one product. Using ERP as an integrated business management tool, organizations can manage and centralize core business functions from a single tool, increasing efficiency, connecting databases, and saving costs.
However, while managing and automating many of the functions relating to systems of record—finances, accounting, benefits, procurement, contracts, and sales—work seamlessly, it often performs poorly for systems of engagement, such as maintenance management.
Is a CMMS Part of an ERP?
A system of record is one way to think of a company’s single data repository, used simultaneously across an organization, by accounting, HR, sales, and procurement. Enterprise Resource Planning software is such a system of record.
A system of engagement, on the other hand, is the system used to collect the data at the fingertips of, for example, the employees doing specific maintenance tasks: faster data entry, data exchange, streamlined frontline workflows, and real-time communication, to name only a few of the CMMS-specific functions available to maintenance managers and their maintenance teams. Knowing this, it makes sense that a CMMS created specifically for maintenance works better and more efficiently, especially if it syncs easily via API and integrations with the ERP, or system of record. Even better, it is designed to meet maintenance management needs via its platform and interface—both desktop and mobile—given that the deskless workforce needs particular information available in real-time at its fingertips.
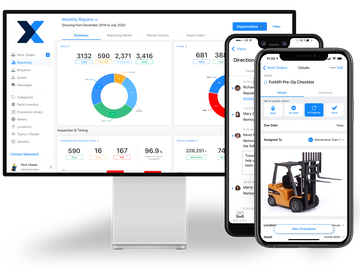
Most companies are already familiar with ERP. So here, let’s review why a CMMS-ERP integration may be an essential addition as a necessary system of engagement.
Most operations and maintenance (O&M) leaders are familiar with the idea of a CMMS. However, as with many technologies over the past 20 years, a lot has changed. A computerized maintenance management system, or CMMS, centralizes maintenance information and facilitates maintenance operations. The core of the best modern CMMS—and this is important—is its real-time database at workers’ fingertips.
Don’t Abandon Your ERP
We are not suggesting that you abandon your current ERP software. We are simply pointing out that seamlessly integrating a CMMS into your ERP will enhance your maintenance teams’ ability to increase efficiency and productivity.
A CMMS with the right combination of features will streamline maintenance work processes for increased productivity.
In this new era of mobile and cloud technologies, modern CMMS automates the logistic operations performed by maintenance management and their teams and replaces the often tedious and conventional manual maintenance tracking process. We recommend conducting a thorough CMMS software review to learn more about CMMS-ERP integration capabilities.
Just Look at What Your CMMS Can Do
Modern CMMS, like MaintainX, can provide stakeholders with the following capabilities from the spot of maintenance:
- Generate and prioritize preventive maintenance work orders.
- Communicate in real-time across teams and managers.
- Track equipment and other assets by QR or barcode.
- Monitor scheduled and unscheduled maintenance activities.
- Track work orders by asset, location, user, and category.
- Create real-time reports of ongoing job activities.
- Track resource, budget, and labor costs for every asset.
- Record time spent completing work orders.
- Provide up-to-date standard operating procedures.
- Automatically trigger corrective work orders.
- Support automated inventory management control.
- Increase asset life cycles and asset return on investment.
- Streamline spare parts ordering and purchase order.
- Allow for real-time photos of work-in-progress.
A CMMS, as the system of engagement, is not meant to replace an ERP. However, at this time, there is no ERP that has the right combination of these features. In fact, a recent PWC 4.0 Industry study noted that “Companies need to think about how they can connect their workers with the equipment, information, and processes they handle on a daily basis.”
Luckily, the best CMMS provides the exact tools and functionality that maintenance departments require for productivity, efficiency, optimization, and effectiveness. And, at the same time, it can sync with a company’s ERP, system of record, such as Oracle, Microsoft Dynamics ERP, or SAP. MaintainX offers the ability to integrate with any open REST API and offers integrations with 3,000+ software tools. Contact us today to learn how MaintainX can help your organization reach true digital transformation.
Check out MaintainX integrations and API information.
FAQs
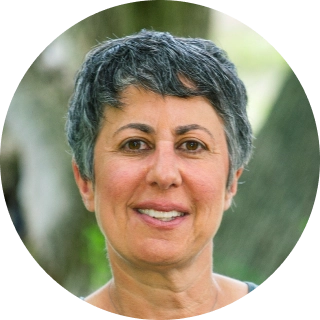
Caroline Eisner is a writer and editor with experience across the profit and nonprofit sectors, government, education, and financial organizations. She has held leadership positions in K16 institutions and has led large-scale digital projects, interactive websites, and a business writing consultancy.