We often use the terms “quality control” and “quality assurance” interchangeably, but they have different meanings and strategies.
The quality of products or services is key to business success. Quality products and services aren’t just critical to earning repeat business from customers. They’re also essential to a firm’s bottom line and profitability. For firms to measure and improve their quality and minimize defects, processes and procedures need to be in place. Modern CMMS allows companies to digitize, automate, and move these processes and procedures into the cloud.
Quality Control Defined
Quality control (QC) focuses on the overall quality of a firm’s output. It’s a strategy that systematically identifies the processes and procedures used to ensure that a firm’s products or services meet its standards and any regulatory controls. Along with quality assurance, quality control is part of a firm’s overall quality management.
“Establishing a QC program is essential to maintaining a successful business. A quick fix or Band-Aid approach to your procedures won’t provide lasting results.”
Forbes
Quality Assurance Defined
The other part of a firm’s quality management strategy, quality assurance (QA), is defined as planned activities within the manufacturing process that help to ensure the overall quality and safety of the product. QA tends to be more preventive and proactive, as the strategy aims to reduce defects and issues by assessing the process rather than the output.
“Good QA practices and culture are not an accident; they are intentionally built and monitored. . . . QA is much more likely to be effective and intentional when it is prioritized at all levels of the organization.”
Forbes
Quality Control vs. Quality Assurance: Key Differences
Proactive vs. Reactive
QA tends to be more proactive and QC more reactive. This is mainly because a comprehensive QA strategy minimizes and prevents defects. Conversely, a QC plan usually takes place following quality assurance to assess more than just the processes used in creating the end product and the product itself.
Together, QC and QA can help determine where improvements should be made and uncover new competitive advantages.
Processes Quality Control Checklist
The strategies behind QA and QC tend to differ as well. As noted, QA is a strategy to prevent defects. Hence, QA processes can include following Standard Operating Procedures (SOPs), managing suppliers, auditing projects using quality audit templates or quality audit checklists, and creating process checklists.
On the other hand, QC is more concerned with the end product and involves post-production processes such as testing and inspection, product sampling, quality control checklist apps, and product peer review.
For example, a quality control checklist assesses product packaging, product color, UPCs, potential defects, and functions, to name a few more popular controls.
Long-Term vs. Short-Term
QA is a long-term process, while QC is more short-term. Think of QA as spanning an entire product development operation, while QC focuses only on the final stages of product creation.
Benefits of Quality Control and Quality Assurance
Rigorous QC and QA strategies do more than simply improve the overall product and meet and/or exceed regulatory standards. They also promote a better overall workplace environment, make regulatory inspections less stressful, and improve your firm’s reputation.
Here’s a closer look at some key benefits of taking QC and QA seriously:
- Streamline regulatory audits: If your firm operates in an industry with stringent standards, you’re likely to be audited on occasion to ensure you’re meeting them. Quality assurance confirms that the facility proactively avoids poor-quality issues by pinpointing processes and learning where improvements can be made.
- Build a culture of continuous improvement: A complacent firm is often a struggling firm. A robust quality management strategy will always ensure that your firm seeks to avoid complacency through learning and improvement cycles. Integrate a preventive maintenance plan so that your firm won’t only regularly assess its processes but will also be preventing downtime and inefficiencies. QA and QC can influence how your firm addresses needed changes to establish new competitive advantages.
- Nurture a more engaged workforce: Strong quality improvement plans increase worker engagement. A more engaged workforce tends to be happier overall and works well with management, undergoes continuous training, and ensures the long-term success of the overall operation.
Frequently Asked Questions
What Is Quality Improvement?
Part of a firm’s overall quality management strategy, quality improvement is a framework created to help systematically improve a product or service offering. Quality improvement can extend beyond production processes and encompass everything from product design to preventative maintenance to worker training.
A good quality improvement strategy can boost a firm’s reputation, increase revenue, enhance safety, and lead to happier workers.
Who Is Responsible for Quality Assurance and Quality Control?
Quality assurance requires that everyone participate to be successful, while quality assurance is something that a more specific team is tasked with. Remember, QA tends to be more big-picture and longer-term than QC.
What Industries Use QA and QC?
Regardless of industry, every organization should have a quality management system to ensure a high-quality overall product or service and a satisfied end-user or customer. However, QA and QC are specifically important in highly regulated industries. For example, the healthcare and pharmaceutical fields are industries subject to a host of consumer, safety, and government regulations.
Likewise, the aerospace and automotive markets come to mind due to the need for highly accurate and precise parts. In industries that aren’t highly regulated, the customer or end-user is the judge.
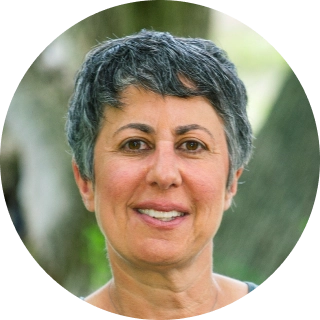
Caroline Eisner
Caroline Eisner is a writer and editor with experience across the profit and nonprofit sectors, government, education, and financial organizations. She has held leadership positions in K16 institutions and has led large-scale digital projects, interactive websites, and a business writing consultancy.
See MaintainX in action