Equipment maintenance involves using maintenance methods and procedures to keep organizational equipment running in good working condition. It includes both regular inspections and corrective repairs of assets. The practice is performed in several settings, including food service establishments, industrial plants, manufacturing facilities, hotels, and more.
What is Equipment Maintenance?
Equipment maintenance includes the upkeep of various equipment types, such as heavy machinery, computer systems, vehicles, and tools. It aims to prevent equipment breakdown and failure, which can lead to significant losses in business profits.
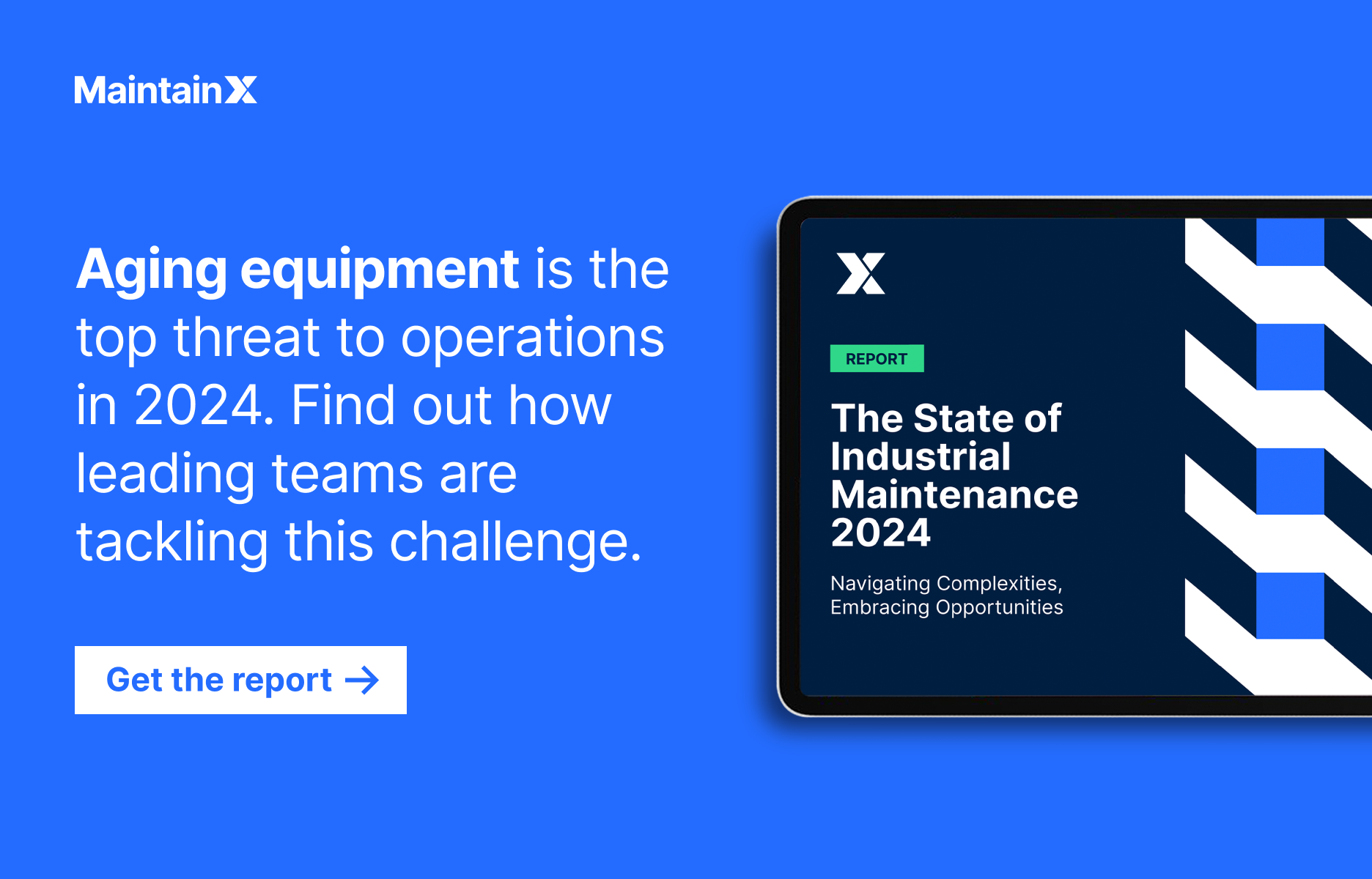
Why Is Equipment Maintenance Important?
No matter the industry, equipment downtime inconveniences workers, supervisors, and customers. However, equipment breakdown is shockingly more expensive for some than others.
According to Industry Week and Emerson, unplanned downtime costs manufacturers $50 billion annually. Equipment failure is the root cause of downtime 42 percent of the time. In the automotive industry, a single minute of downtime costs $22,000 on average! Within this context, it’s easy to see why the regular maintenance of critical assets is crucial to maximizing O&M budgets.
“Instead of being satisfied with old technologies and old ways of doing things that bring only incremental improvements, manufacturers seeking Top Quartile performance need to look at their projects and plant performance with dramatically higher expectations. . . . In many instances, by replacing older, accepted work practices and outmoded technologies, industrial manufacturers are able to achieve significant gains.”
Wall Street Journal
Goals of Equipment Maintenance Management
In addition to reducing downtime, equipment maintenance has three primary goals:
- Decreasing unnecessary O&M costs
- Increasing asset useful life cycles
- Guaranteeing facility safety
The equipment maintenance program you chose for a particular piece of equipment varies by asset type, criticality, and associated costs. In some instances, preventive maintenance (PM) of critical equipment costs significantly less than deferred maintenance.
Alternatively, non-critical assets that are inexpensive, structural, or easy to replace may not need routine maintenance before they break down.
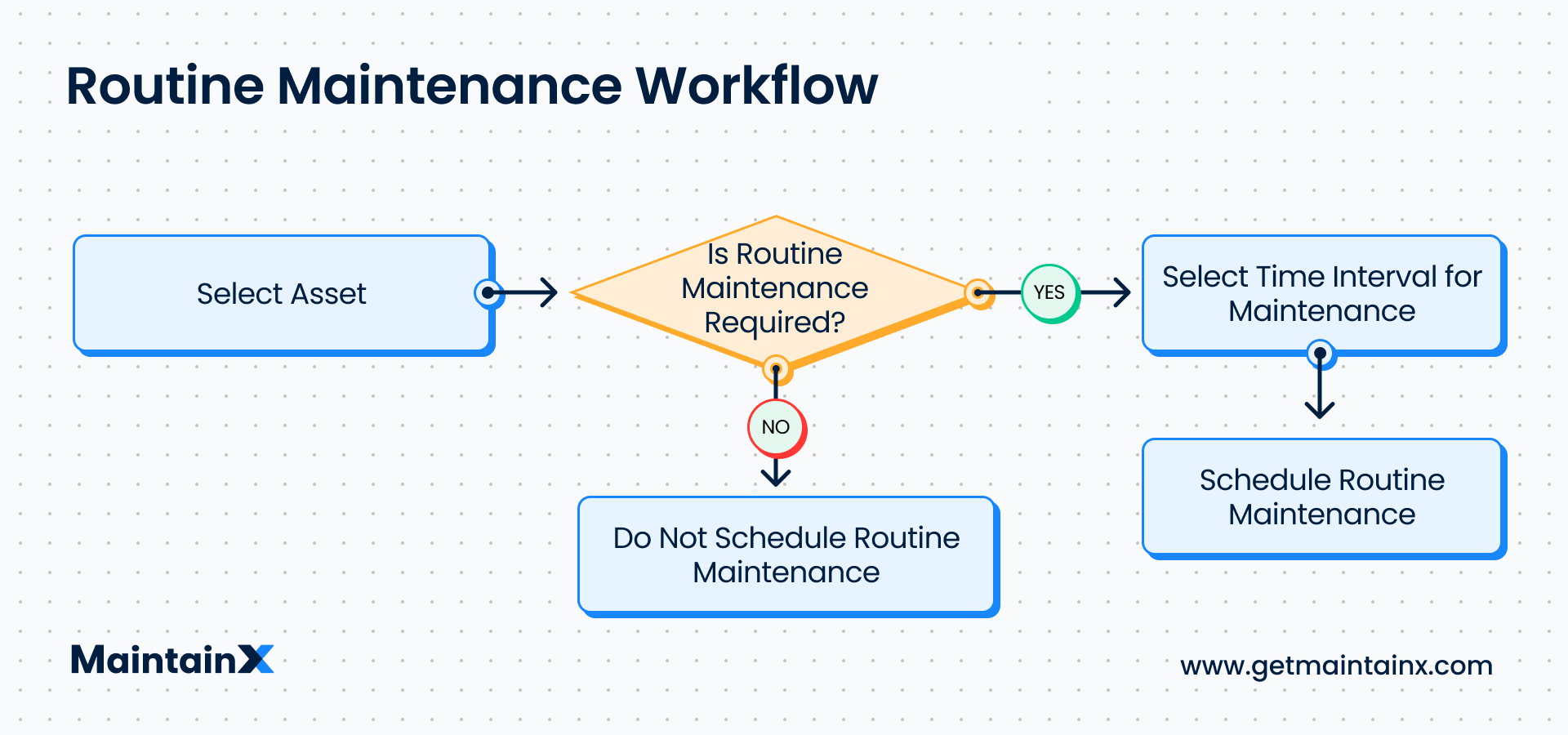
HVAC systems, air handling units, and fans are good candidates for deferred maintenance. On the other hand, facilities may invest in preventive maintenance activities for roofs, facades, parking lots, and other expensive assets subject to deterioration.
Equipment Maintenance Examples
The ratio of preventive maintenance to deferred maintenance varies substantially by facility type. Take the mining industry, for example—the timely detection of equipment problems is critical to meeting everyday production goals.
For this reason, Barrick Gold, the largest producer of gold in the Caribbean, launched a predictive maintenance program, relying on machine learning algorithms and sensors to investigate the cause of truck failures.
Since 2018, the organization has avoided several major equipment failures that would have otherwise cost $500,000. As reported by MINING.COM, Barrick Gold reduced its total number of failures from engine, brake, or suspension issues by 30 percent.
Other equipment maintenance examples include the regular lubrication of machines with rotating parts and inspection for rust or contaminants. The regular draining and replacement of oils are essential to optimal equipment functionality.
Industries That Practice Equipment Maintenance Management
A large number of industries and facilities rely on equipment maintenance management systems to ensure equipment reliability and reduce downtime. These include, among others:
- Food Industry: Food production and processing plants
- Aerospace and Automobile: Manufacturing facilities and assembly plants
- Construction and Infrastructure: Construction equipment and buildings
- Electric Power Industry: Nuclear, hydroelectric, coal-fired, geothermal, and other types of power plants
- Manufacturing: Facilities producing consumer goods
- Hospitality Industry: Hotels, serviced apartments, restaurants, and bars
All these industries use equipment that needs to be serviced to function correctly and keep operational and maintenance costs under control
Equipment Maintenance and Preventive Maintenance Best Practices
Companies that fail to invest time and effort into adequately maintaining their assets risk significant losses. Below are our recommended best practices for optimized equipment maintenance:
1. Correct Use
The first step in caring for your equipment is using it correctly. As Tony Pottinger from Tornado Industries told CleanLink, attempting to use your equipment for things it wasn’t designed for will result in premature wear and tear and may lead to equipment failure.
Train your machine operators to use the equipment according to the manufacturer’s recommendations and prioritize not overworking machinery. Though it may be tempting to increase production beyond capacity, especially during busy periods, doing so places strain on equipment parts that could cause massive failures down the line.
2. Cleaning and Storage
Clean and store your equipment correctly to extend its lifespan. Maintaining an operating environment that is free of contaminants is a principle of precision maintenance. It guarantees that your equipment, tools, and materials will work as intended and that motors won’t be subject to additional strain.
Additionally, some equipment parts are sensitive to dust and other pollutants, making cleaning even more critical. Dirt can lead to overheating and premature equipment failure.
3. Proper Lubrication
Another example of equipment maintenance in most manufacturing facilities is the regular lubrication of machines that have rotating parts. Lubricants reduce friction and excessive wear, protect surfaces, and help dissipate excessive heat. Lubricants can be petroleum-based, or synthetic oils and their quality can vary. Proper lubrication techniques—applying the right amount and type of oil at the right time—are essential for equipment performance and reliability.
4. Regular Inspections
Inspect your equipment regularly for wear and tear and address minor issues before they become problems. Check your equipment for the following signs of damage:
- Rust and contamination
- Water and excessive moisture where there shouldn’t be any
- Chips, scratches, and cracks in metal parts
- Unusual engine sounds
- Excessive vibration
- Exposed wires
CMMS software allows you to schedule preventive maintenance (PM) tasks at regular intervals, either based on calendar time (e.g., every 2 weeks) or usage time (e.g., every 100 hours of run time).
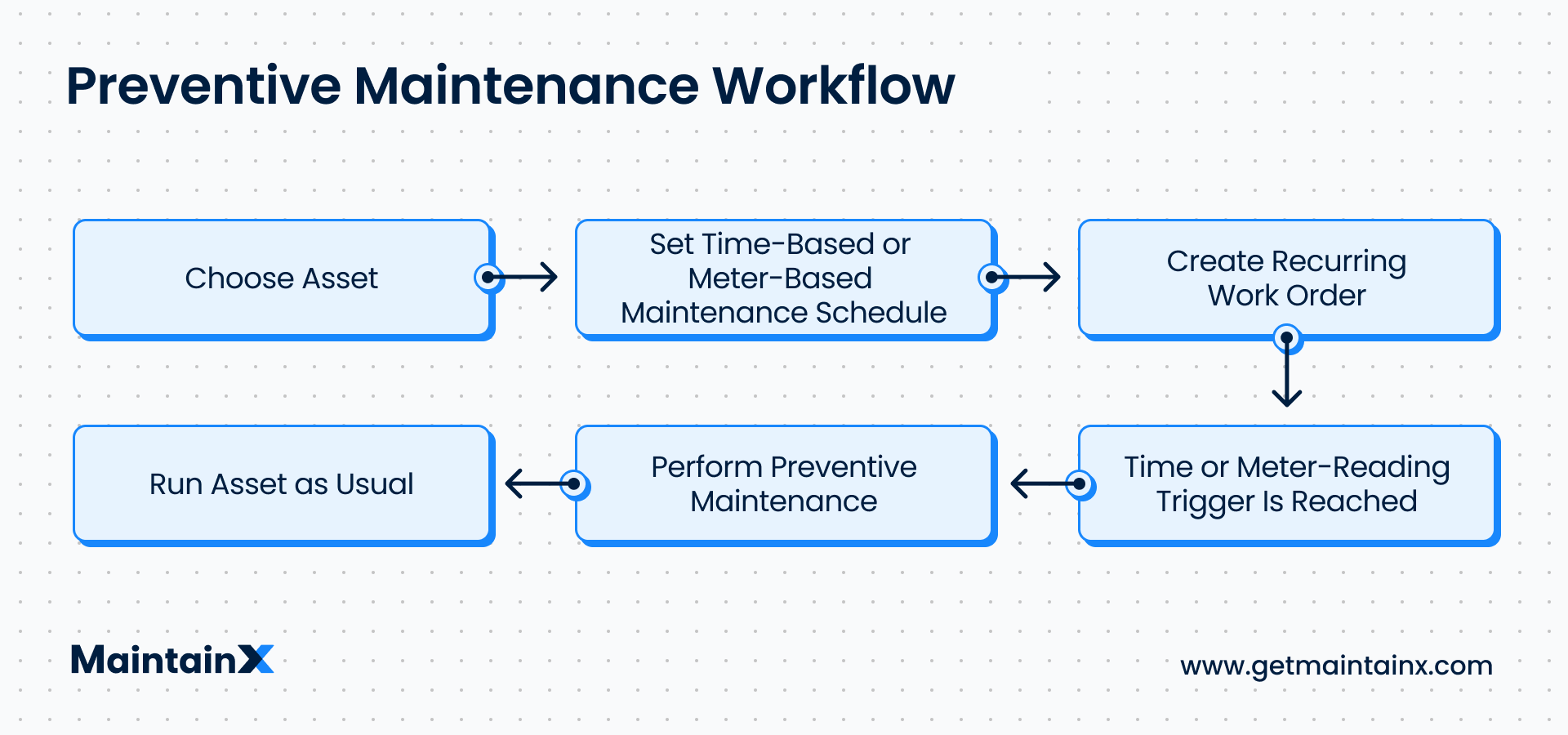
5. Timely Repairs
Follow the manufacturer’s guidelines for the repair and replacement of faulty parts, and do not delay servicing equipment that shows signs of wear and tear. Consider switching your most critical equipment from a corrective maintenance plan to a preventive maintenance one. With this, you’re extending its lifespan and ensuring that it won’t break down unexpectedly and cost you thousands in lost profits and rushed asset pricing. Timely repairs also rely on facility managers employing real-time inventory management practices.
Equipment Maintenance Roles
There are different types of equipment maintenance positions, and in some cases, there may be overlap between them.
Maintenance Technicians: Maintenance technicians perform all kinds of maintenance tasks, including the inspection, servicing, and repair of assets.
Maintenance Mechanics: Maintenance mechanics are responsible for the servicing of different types of machinery and mechanical equipment. They are more specialized than maintenance technicians.
Maintenance Managers: Managers supervise the maintenance team’s work and schedule and plan maintenance tasks. They also ensure that the maintenance team has sufficient resources to do its job and report to the organization’s managers.
Maintenance Engineers: Maintenance engineers plan, analyze, and optimize the maintenance department’s work. Their background in engineering allows them to identify potential weak points and address systemic issues.
Equipment Maintenance Certifications and Training
Different equipment maintenance certification and training programs exist.
The Association of Equipment Management Professionals (AEMP) proposes three certification programs for maintenance staff working with heavy equipment:
- Equipment Management Specialist (EMS).
- Certified Equipment Manager (CEM).
- Certified Equipment Support Professional (CESP).
On the other hand, the Society for Maintenance & Reliability Professionals (SMRP) offers a Certified Maintenance & Reliability Professional (CMRP) certification program. It is intended for maintenance professionals working across roles and facilities and covers the principles of equipment maintenance.
Let a CMMS Guide Your Equipment Maintenance
Equipment maintenance is used across industries and is essential to maintain your equipment in top condition. The timely maintenance of your assets helps improve performance, guarantees continuous uptime and availability, and keeps operational costs predictable. For this reason, you should consider equipment maintenance as an investment rather than an expense. Look into different ways to optimize it by using a CMMS, shifting to a proactive maintenance program, and training your maintenance staff.
Equipment Maintenance FAQs
What Is the Easiest Way to Schedule Maintenance Tasks?
Maintenance tasks are best scheduled in advance, according to a plan that the maintenance manager creates and updates as necessary. The easiest way to schedule maintenance tasks is by using a CMMS software, or maintenance software program, that supports the easy creation of work order templates for assigning work orders. Alternatively, some facilities still use pen and paper or whiteboard planning systems, which are less reliable and hard to find in a pinch.
How Do I Make a Maintenance Checklist?
A maintenance checklist is a list of each maintenance task that needs to be carried out to service your equipment. You can organize maintenance checklists either by asset type, asset criticality, servicing intervals, priority, resources needed, or other criteria. Create a list of the equipment pieces that need servicing, check if you have all the necessary tools and materials, and schedule the maintenance work. Standard operating procedures (SOPs) are an essential part of equipment maintenance strategies and should be included in your maintenance checklists.
What Are Maintenance Procedures?
Maintenance procedures are written instructions for maintenance tasks. Maintenance procedures need to be up-to-date and easy to consult so that maintenance staff can follow them with a high level of precision. This, in turn, ensures equipment reliability and performance.
What Is a Safety Checklist?
Safety checklists are used across industries to guarantee the safety of staff and visitors. They contain a list of steps machine operators and maintenance technicians must carry out. Safety checklists usually include details on the necessary protective gear as well.
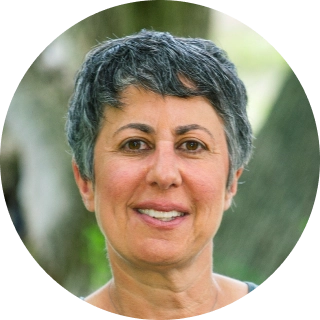
Caroline Eisner
Caroline Eisner is a writer and editor with experience across the profit and nonprofit sectors, government, education, and financial organizations. She has held leadership positions in K16 institutions and has led large-scale digital projects, interactive websites, and a business writing consultancy.
See MaintainX in action