An asset is a physical item used to achieve organizational goals. Examples include buildings, land, tools, pieces of equipment, and IT infrastructure. Ideally, such items contribute to company profitability.
Any resource that holds economic value and benefits an organization is an asset. Such things can either be tangible or intangible, so long as they help generate cash flow, improve sales, and/or reduce expenses.
Maintenance workers typically deal with fixed assets. These are physical resources used in long-term business operations. Accountants and operational leaders also refer to such items as Property, Plant, and Equipment (PP&E). The category includes expensive items that companies can’t quickly convert to cash, such as a conveyer belt. Except for land and buildings, PP&E has diminishing value and depreciates over time.
Well-run organizations track an asset’s “Useful Life” to make robust maintenance, purchase, and tax decisions. For example, an O&M manager might run a piece of equipment to failure instead of practicing preventive maintenance (PM). This is a wise strategy to pursue when the cost of repairs is higher than an asset’s current depreciated value.
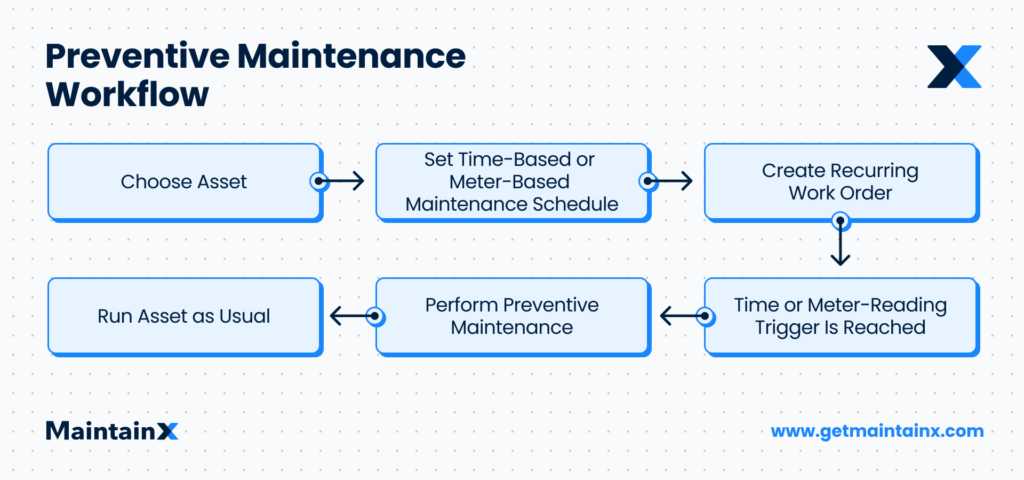
What Are Examples of Assets?
There are four types of assets: fixed, current, financial, and intangible. As previously mentioned, maintenance works on fixed assets. These items fall into the following categories:
- Tools: These include wrenches, hammers, screwdrivers, and power tools used to carry out maintenance work.
- Equipment: These are physical resources organizations use in their day-to-day operations. Equipment includes heavy vehicles such as dump trucks, excavators, forklifts, tractors, and other off-road vehicles.
- Machinery: Complex machinery may be critical to production and put under a high level of proactive maintenance. Examples include conveyor systems, boilers, fans, presses, rollers, lifts, and other automated equipment pieces.
- Furniture: This includes desks, work tables, tables, shelving, and chairs.
- Buildings and Plants: Buildings and facilities are fixed assets that require regular maintenance. These include apartment complexes and manufacturing plants. Maintenance activities often performed on these include HVAC system maintenance, snow removal, plumbing, electrical repairs, and cleaning.
- Land: Organizations also can include land as an asset. These include manufacturing, real estate, and mining companies, among others. Government institutions and municipalities also own public lands, such as city infrastructure, roads, and parks.
Profit-driven organizations should maintain every type of asset within their facilities to improve reliability and production.
Managing and Maintaining Assets
Maintenance managers and planners often use insightful metrics to develop maintenance plans for each piece of equipment in their operations. Such information is critical to maintenance decision-making and informs when and how technicians make repairs. It also determines when organizations should ideally decommission and replace equipment.
The maintenance approach depends on the likelihood of different types of failures occurring, their impact on critical operations, and the associated costs of maintenance repairs. Metrics to track machine condition can include meter readings, inventory of purchased replacement parts, equipment warranties, depreciation, downtime, and the type of maintenance performed.
The Difference between Asset Management and Maintenance
Many people use the terms asset management and asset maintenance interchangeably. Though similar in scope, the practices have distinct differences. Most notably, asset maintenance is a component of the broader responsibility of asset management.
The goal of equipment management is to maximize equipment value and performance while reducing risk. Achieving this aim often includes involving engineering, production, maintenance, and accounting departments.
Alternatively, machine maintenance solely focuses on ensuring items are in good working condition to achieve reliability. In this instance, maintenance departments coordinate maintenance resources, including sourcing replacement parts, hiring maintenance personnel, and managing the maintenance budget. And depending on an organization’s size, there may be significant overlap in responsibilities.
“Advanced analytics help manufacturers solve previously impenetrable problems and reveal those that they never knew about, such as hidden bottlenecks or unprofitable production lines.”
McKinsey
Components of Asset Management
Asset management includes the following components:
- Identification: This includes identifying what equipment an organization has in its portfolio. It helps to ensure that the organization doesn’t emphasize critical equipment while ignoring non-critical ones.
- Location: Organizations also have to know the location of each asset. Some organizations rely on technology such as Graphic Information System (GIS) mapping and Global Positioning System (GPS) to quickly locate their equipment.
- Condition: It’s essential to track an asset’s condition for maintenance and decommissioning planning purposes. Sensor devices and monitoring systems such as SCADA can monitor equipment conditions. SCADA, or Supervisory Control and Data Acquisition, is a computer system companies use to gather and analyze equipment data in real time. Industries such as transportation, oil and gas, energy, waste control, water, and telecommunications use SCADA systems to monitor and control complex machinery. According to Allied Market Research, the global SCADA market will grow 6 percent by 2023. Translation: SCADA has become a crucial component of managing complex industrial processes.
- Specification: Understanding an asset’s specifications and design helps organizations operate at maximum efficiency. Understanding how a piece of equipment should perform under optimal conditions allows maintenance technicians to better identify the causes of failures.
- Maintenance: Maintenance programs ensure equipment stays in good working condition throughout its useful life cycles.
- Costs: The goal of asset management is to maximize an asset’s useful life cycle at a minimal cost. Organizations monitor equipment performance to identify ways of saving costs on the equipment. Older assets are more expensive to operate and maintain.
The typical asset life cycle includes four stages: acquisition, operation, maintenance, and disposal/ renewal.
Let a CMMS Run Your Asset Management
In maintenance terms, an asset refers to any physical resource beneficial to the organization’s bottom line. Assets include tools, IT infrastructure, machinery, land, buildings, facilities, and equipment. It’s essential to put effective management and maintenance strategies in place to maximize an asset’s value. Tools such as computerized maintenance management systems (CMMS) can track key equipment performance metrics to maximize an asset’s useful life cycle at a minimal cost.
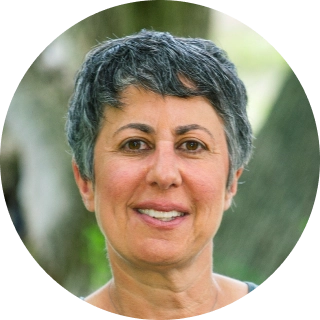
Caroline Eisner
Caroline Eisner is a writer and editor with experience across the profit and nonprofit sectors, government, education, and financial organizations. She has held leadership positions in K16 institutions and has led large-scale digital projects, interactive websites, and a business writing consultancy.
See MaintainX in action