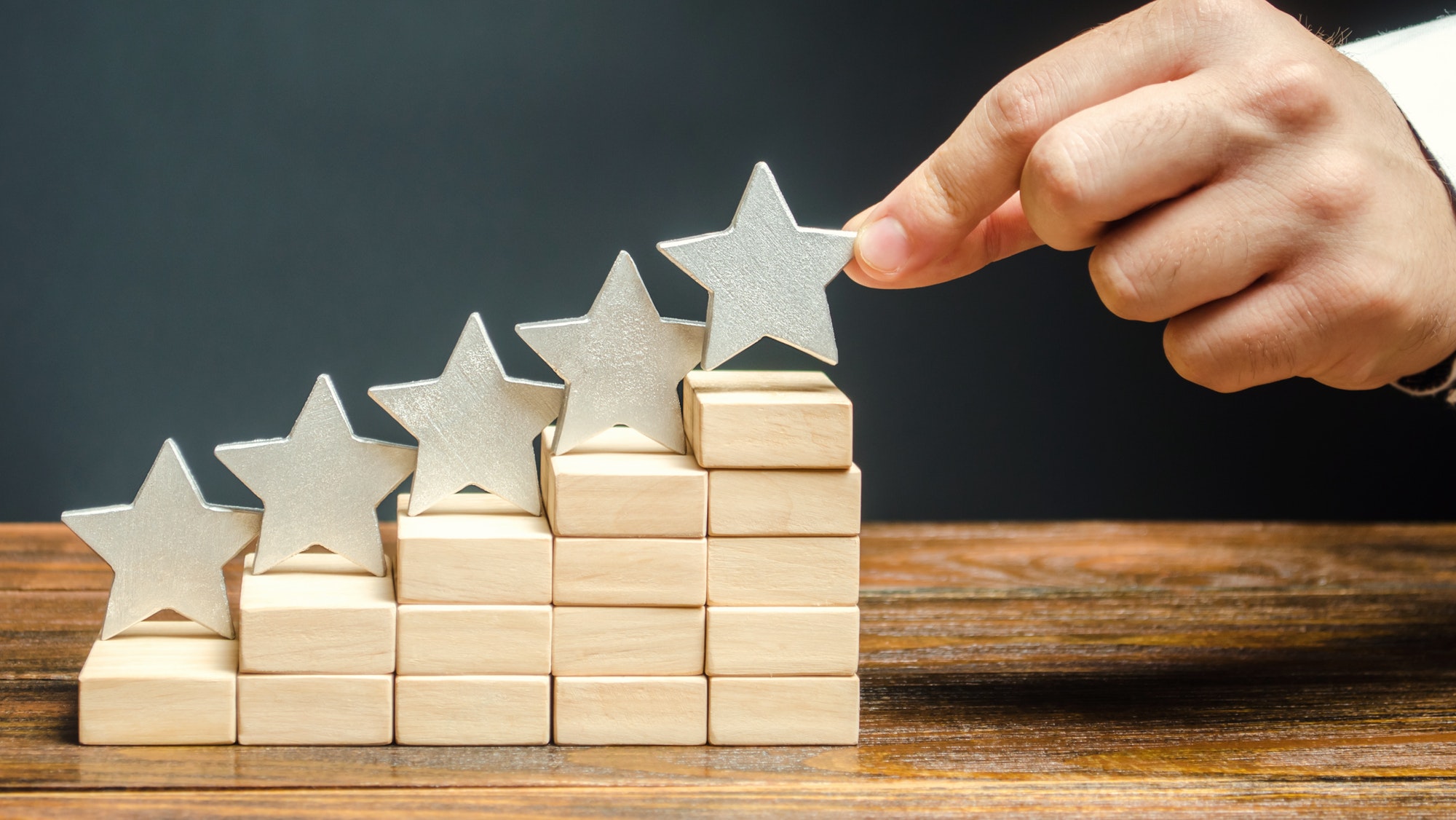
Sometimes “good enough” really is good enough. Businesses with zero threat of competition needn’t worry about enhancing the quality of their products and services.
As for the United States of America’s 33.2 million small businesses, however, quality improvement programs are essential to long-term success.
According to the Small Business Administration, only 33 percent of organizations make it past a decade.
The key to maintaining loyal customers is the standardization of quality control measures. Of course, the road to developing models for improvement isn’t without unexpected turns.
In this article, we’ll outline the essential elements of quality control plans, how to build a culture of continuous quality improvement, and how to sidestep common barriers to success. After reading, you’ll be poised to implement improvement methods designed to catapult deliverables from “good enough” to “best in class.”
What Is Quality Improvement? A Beginner’s Guide to Success
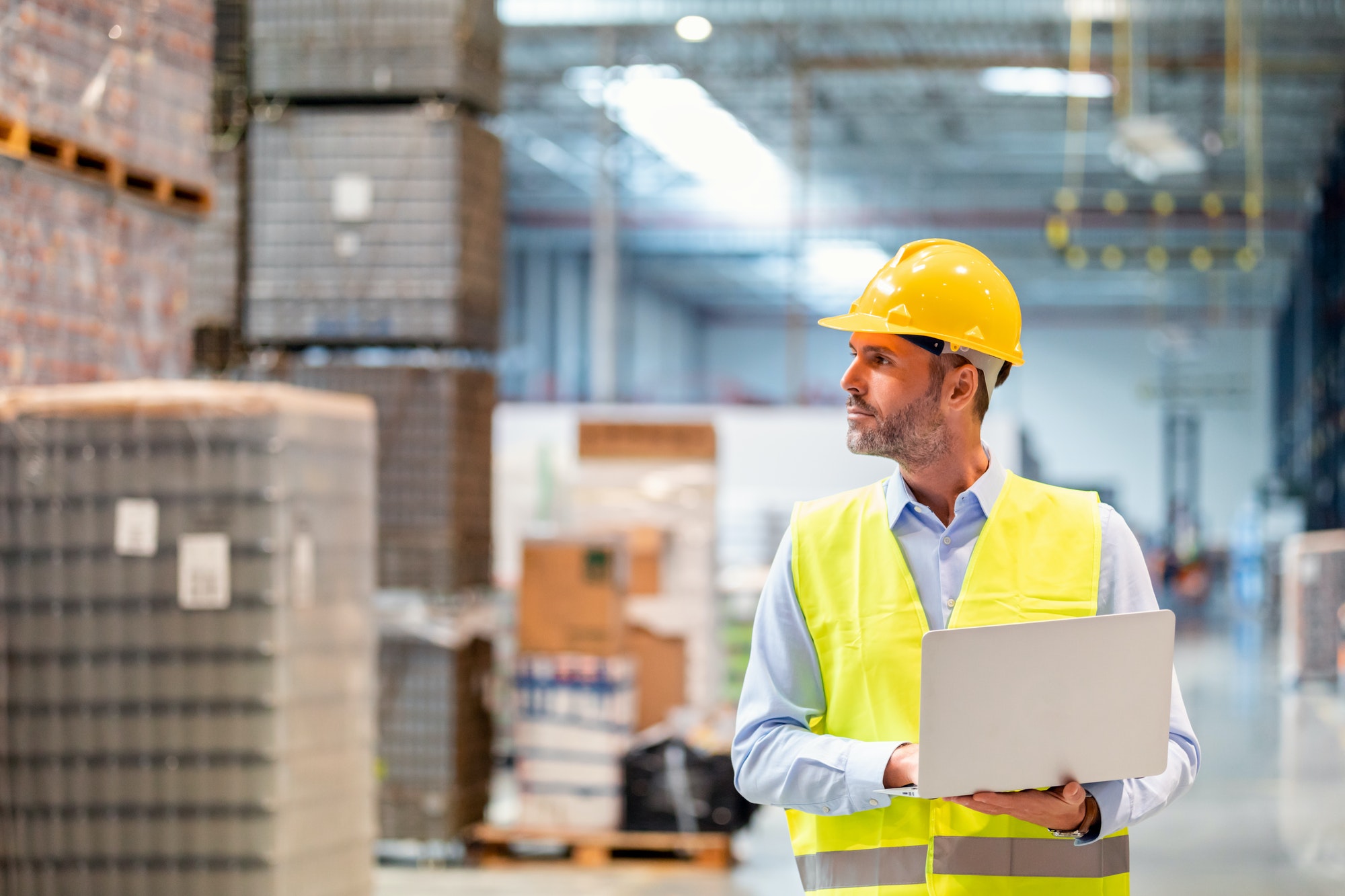
Businesses of all sizes and industries face challenges when attempting to eliminate productivity bottlenecks, control spending, and exceed customer expectations.
Before implementing quality improvements, it’s essential to recognize one fact: your team members will determine whether initiatives become wildly successful or stall out.
Fostering a company culture committed to operational excellence is a prerequisite to quality improvement.
In other words, employees within all departments should:
- Recognize the correlation between quality improvement and job security.
- Understand how standardization increases profitability.
- Embrace the organization’s core values.
It’s a common misconception that quality improvement only relates to production-related processes. On the contrary, the practice can extend to product design, preventive maintenance (PM) procedures, employee training, and more.
Help team members see “the big picture” before launching new initiatives, and you’ll increase your chances of success. Let’s take a deeper look at what quality improvement entails.
Technical Definition of Quality Improvement
Quality improvement refers to a strategic approach to evaluating organizational performance systems, procedures, and processes. The objective of implementing a quality improvement program is to identify and correct subpar operational practices.
What Is the Difference Between Quality Improvement and Quality Assurance?
It’s not unusual for managers to experience confusion around the difference between the terms quality improvement and quality assurance.
Though the phrases go hand in hand, there is a slight difference in their meaning: quality assurance measures compliance against various industry standards.
Quality assurance focuses on ensuring that your current production standards are acceptable. In addition, it aims to optimize the relationship between employee contributions and profitability.
Alternatively, quality improvement fosters organizational change in response to routine work practices that negatively impact the quality of deliverables. Let’s take a closer look at why top companies prioritize quality improvement.
Purpose of Quality Improvement
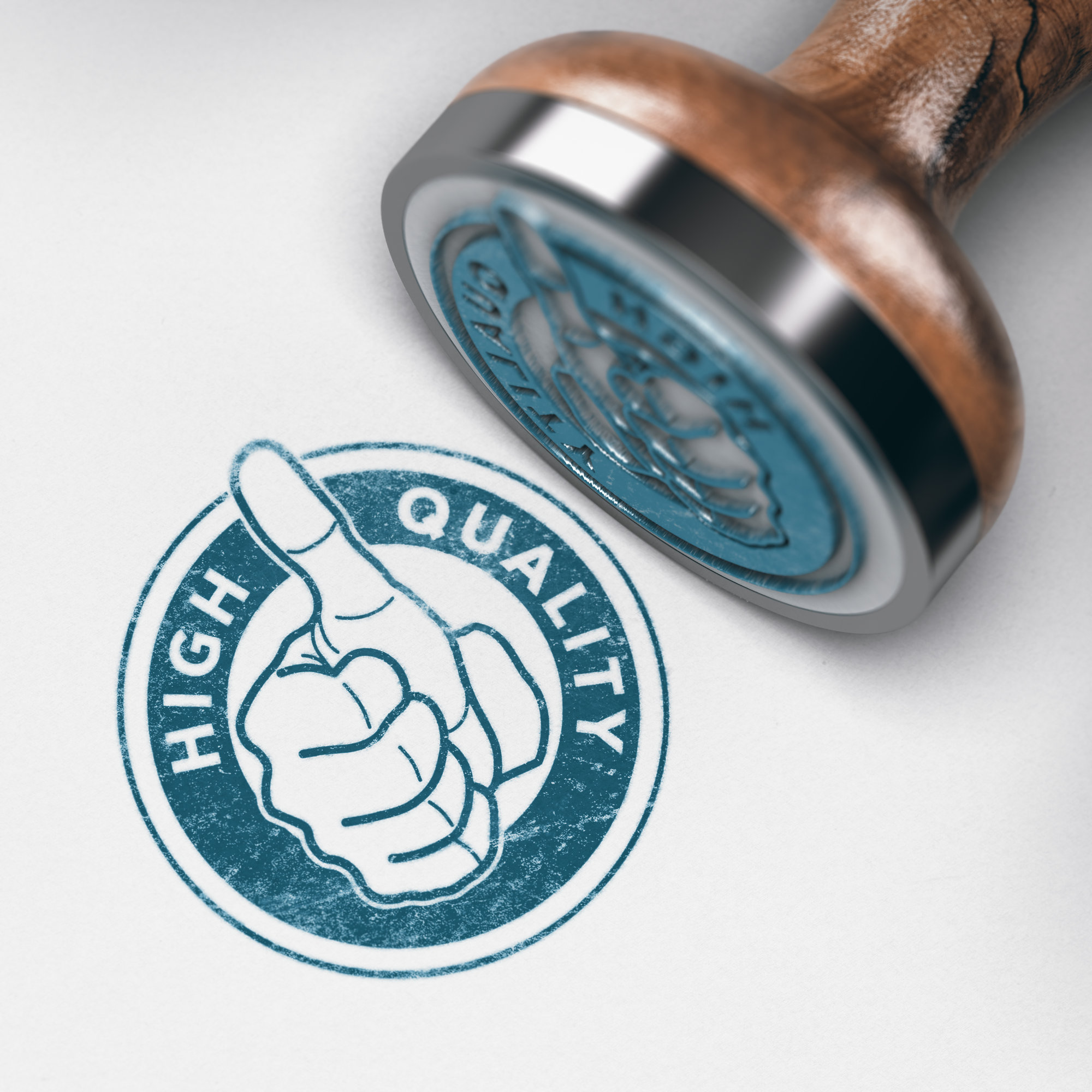
The primary purpose of a quality improvement program is to ensure that organizations produce deliverables according to high standards of efficiency, cost optimization, and quality control.
Standardization should deliver win-win outcomes for both companies and customers. Ultimately, quality improvement is a continuous process that looks to change the various components of processes and systems.
Some companies choose to improve one process at a time, while others focus on making several changes at once. Regardless, effective quality improvement plans share several traits—they are:
- Data-Driven: Management commits to continuous data collection to inform their recommendations for changes. Having access to the “right data” at the “right time” is essential for maintaining forward momentum in the “right direction.” Modern, cloud-based CMMS software platforms like MaintainX streamline the process by storing, cataloging, and converting data into meaningful insights.
- Process-Focused: Management focuses on optimizing processes, not proficiencies. Instead of focusing on how Jane might increase her skill sets, management focuses on streamlining her workflow to produce higher-quality deliverables in less time.
- Co-Created: With that said, Management seeks feedback from workers like Jane to better understand her unique challenges in completing specific tasks. Collaborative process design leads to realistic changes that tend to stick better than vacuum-generated ones.
Benefits of Quality Improvement Programs
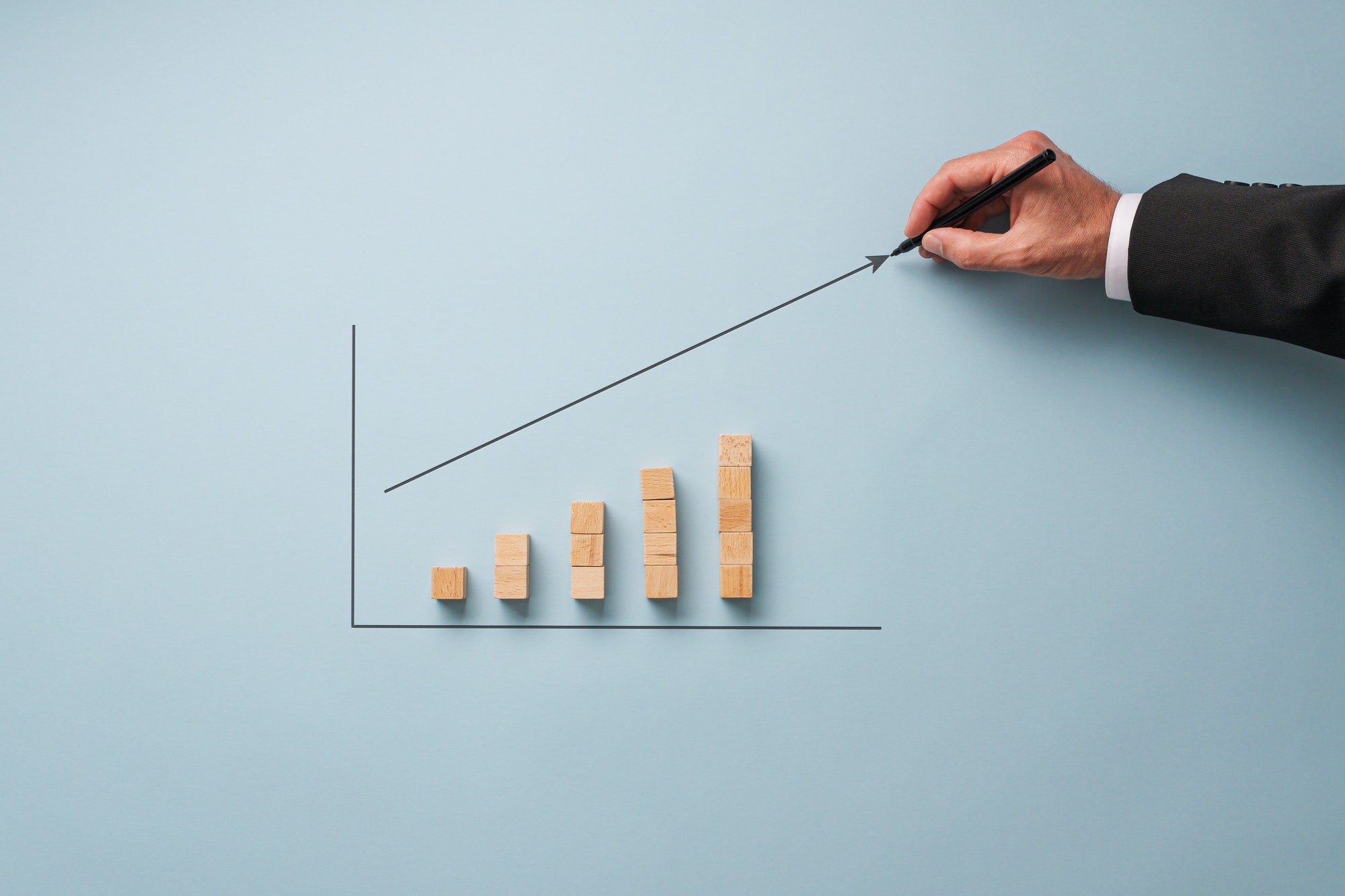
Comprehensive quality improvement programs increase workflow efficiency, eliminate wasted resources, and enhance stakeholder safety. When approached strategically, they deliver the following benefits to most types of organizations:
- Support Consistent Gains: The transition to making objective decisions based on data rather than subjective decisions based on opinions often translates to more trustworthy, long-term solutions. Translation: no more reinventing the wheel or second-guessing.
- Enhance Reputation: Process improvements made with the customer in mind lead to more satisfied customers. More satisfied customers lead to more high-rated online reviews and word-of-mouth referrals.
- Increase Revenues: In addition to public recognition, enhanced brand reputations often lead to increased sales. The more trustworthy your products and services appear to others, the easier it will be to generate new and repeat customers.
- Improve Morale: Quality improvement enables organizations to drive real change by focusing on processes, not people. Managers strive to find solutions to failures within routine procedures instead of nit-picking about perceived flaws within employees.
- Reduce Risk: Quality improvement principles advocate for structured, gradual improvements over time. This less risky approach yields a higher chance of success compared to “on-the-fly” management styles. Additionally, carefully constructed quality improvement measures have been shown to improve customer safety.
- Improve Peace of Mind: Consistent data collection supports managers in maintaining accurate perceptions of ongoing initiatives. Leadership can enjoy the peace of mind that comes with knowing exactly what is going on within each department.
The scope of process improvement outcomes can vary dramatically from business to business. An organization’s size, budget, and ability to invest in incremental improvements will influence the speed of its results. Let’s look at some examples of quality improvement in action.
Industries That Prioritize Quality Improvement
While businesses of all types can benefit from quality improvement programs, some industries take the practice more seriously than others. Below are three sectors known for taking a more regimented approach than others:
Healthcare
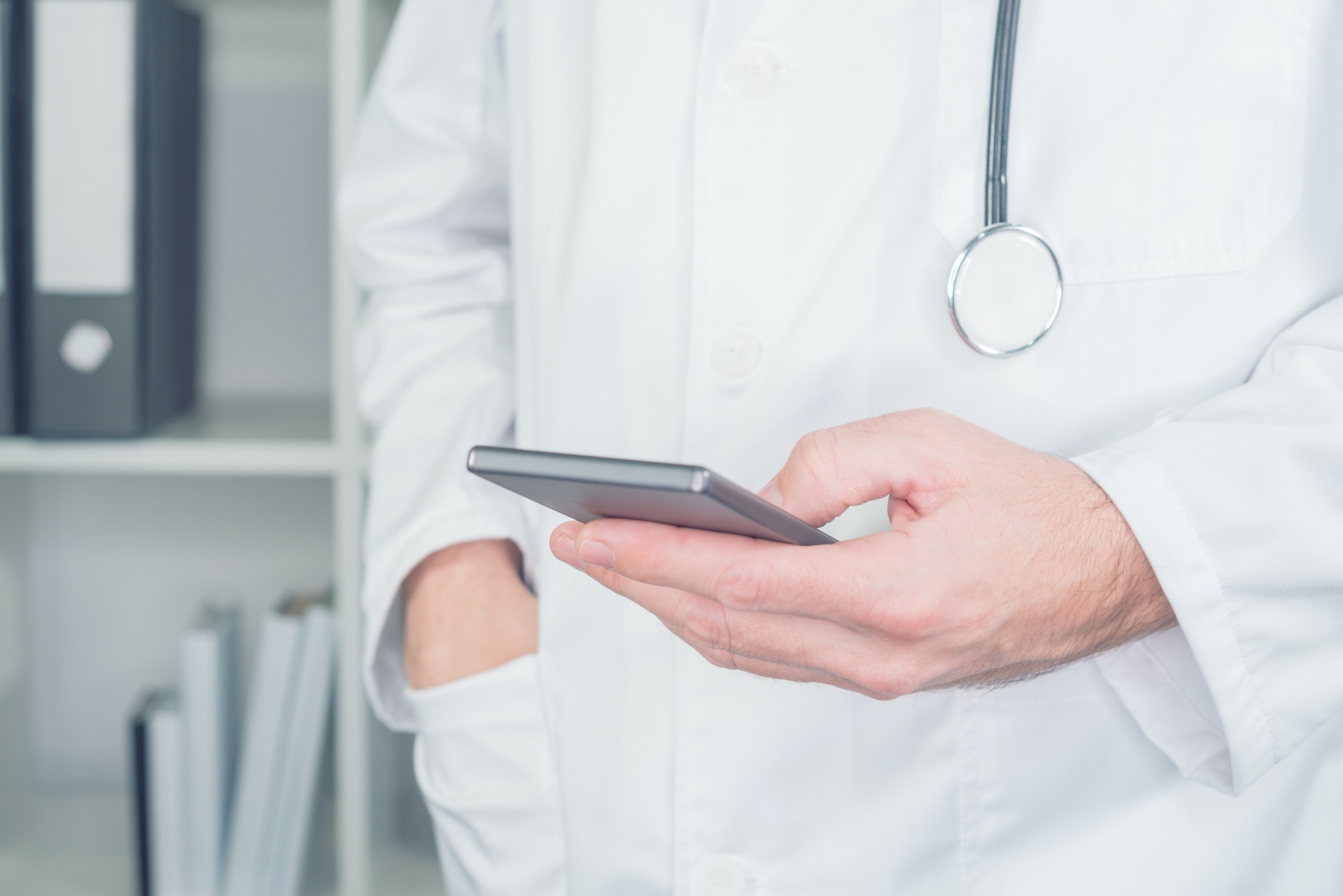
Healthcare quality is something everyone cares about. However, several challenges, including declining cash flows, unwarranted variation, and avoidable medical mistakes, routinely impact the healthcare system. Consequently, healthcare providers use quality improvement programs to monitor patient outcomes, devise new care processes, and enhance existing quality of care.
According to the Health Resources and Services Administration (HRSA), quality improvement is “structured and sustained actions intended to bring about measurable advancements in the industry and upgrade the health status of patients.” Of course, patient safety programs aren’t limited to hospitals—primary care physicians, healthcare organizations, clinicians, and labs may also redesign improvement efforts to enhance their healthcare services.
The most well-known model for improvement used by healthcare professionals is STEEEP: Safety, Timeliness, Effectiveness, Efficiency, Equitability, and Patient-Centeredness. Similar to Failure Mode and Effects Analysis (FMEA), the Institute of Medicine, now known as the National Academy of Medicine, developed the systematic approach to advocate for optimal patient care delivery.
Manufacturing
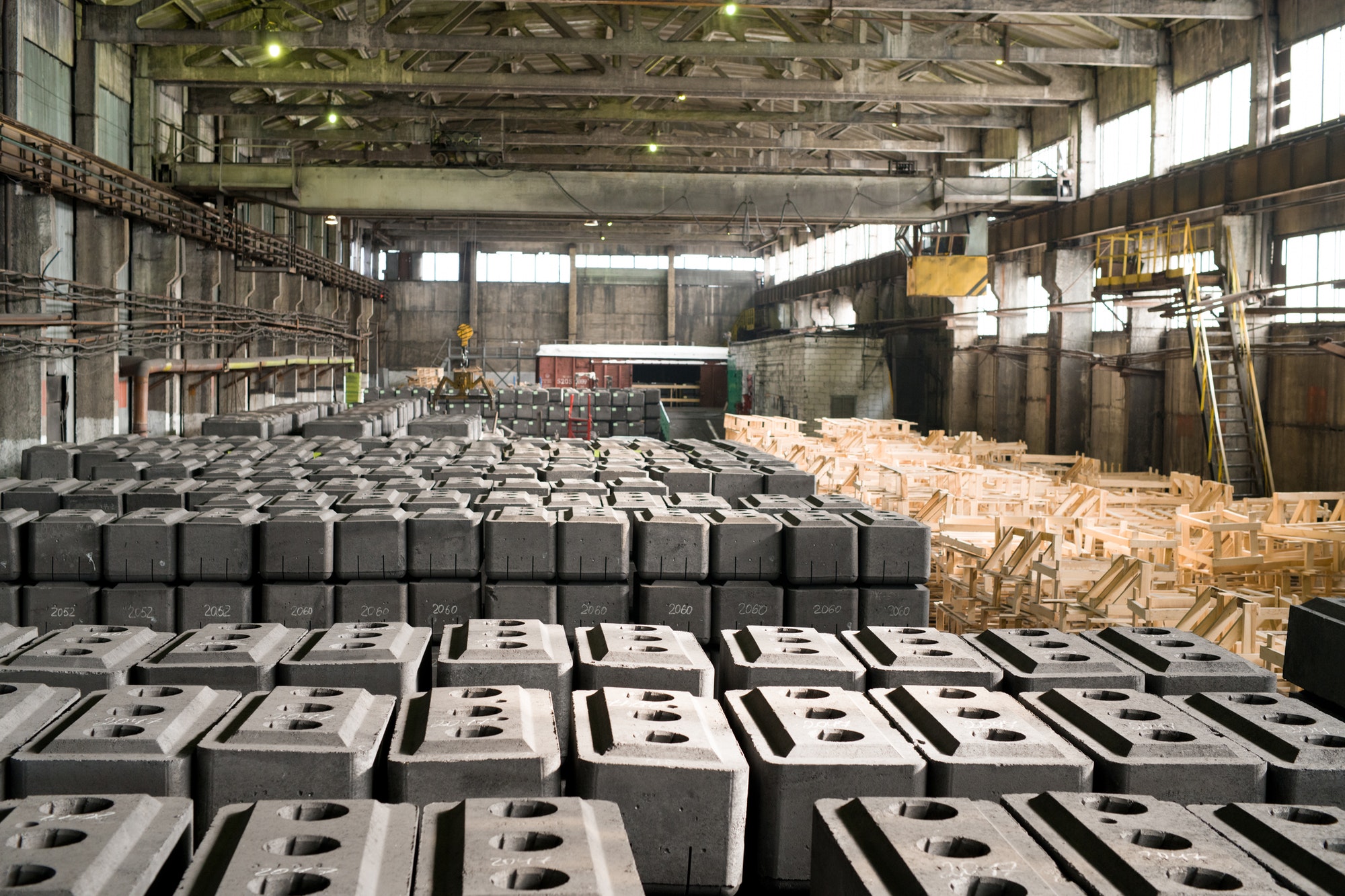
Manufacturers understand the importance of shipping high-quality products. Production defects are unacceptable because they cause rework, unusable scraps, and delayed shipment of products.
Every element in this sequence of events translates to reduced profits! Additionally, customers who repeatedly receive delayed and/or low-quality products lose trust over time. For these reasons, most manufacturing facilities run organized quality improvement initiatives, in addition to standard preventive maintenance (PM) programs.
It’s not enough for management to ensure critical equipment never breaks down unexpectedly. Operational leaders must seek opportunities to reduce supplier delays, raw material variations, capacity mismatches, design flaws, and specification miscommunications. The manufacturing industry’s most famous quality management systems include Lean Six Sigma, Total Productive Maintenance (TPM), and statistical process control.
Education
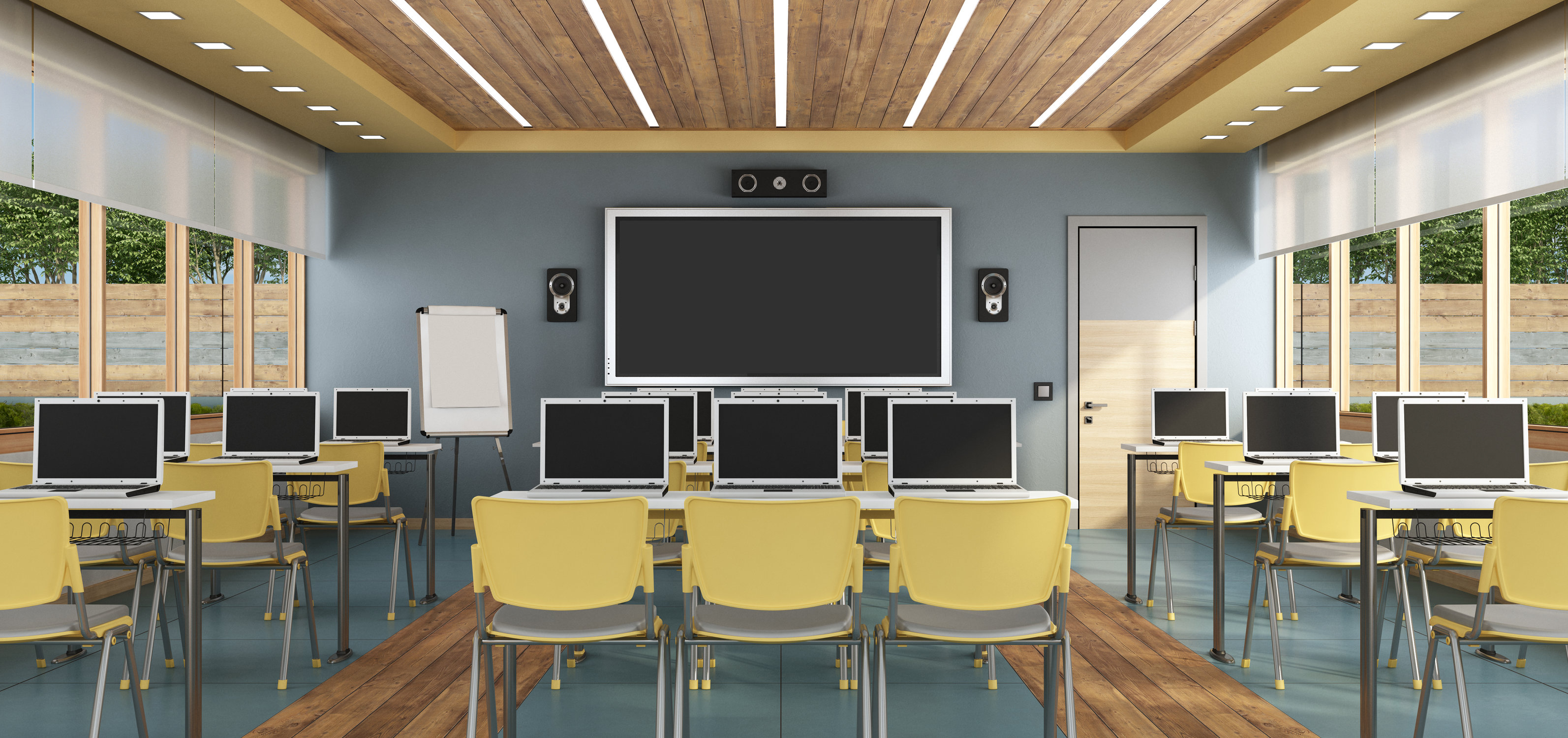
Administrators in both K-12 schools and institutions of higher learning are increasingly relying on process improvement tools like Lean Six Sigma, Plan-Do-Check-Act (PDCA), and Plan-Do-Study-Act (PDSA) to optimize operational systems.
Healthcare, manufacturing, and education are the industries most likely to run consistent quality improvement programs. But, as mentioned before, most business models can benefit from improving some of their standard operating procedures.
Whether you run a franchise chain of restaurants, an e-commerce shop, or an energy power outlet, your customers deserve your very best. Are you interested in creating a quality improvement plan? Keep reading for some quick tips!
Essential Elements of Quality Improvement Plans
A quality improvement plan is a document that outlines an organization’s long-term commitment to implement operational improvement activities. It should clearly define what your organization wants to improve, how you will do it, and the outcome you expect.
Your quality improvement plan should also detail how your team will test changes made over time. Essentially, it should also function as a monitoring and evaluation tool. The best ones begin by outlining small-scale initiatives that lead to more considerable improvements.
- Leadership: The plan clearly defines the leadership structure for the program. Who is responsible for initiating what changes? How will they be held accountable?
- Collaborative Team Members: Since quality improvement is a company-wide endeavor, leadership should assemble a team of stakeholders. Choose individuals from each department to help organize recommended process adaptations.
- Aspirational Benchmarks: Identify comparable organizations and brainstorm how your team can apply their processes within your workflows. Caveat: only employ operational systems with proven track records of success.
- Key Performance Indicators (KPIs): Specify the type of data to be collected from each department. Which metrics will illustrate success or lack thereof? Schedule periodic reviews of key performance indicators (KPIs) to assess results and course-correct, as needed.
- Quality Improvement Tools: As mentioned before, several methodologies are available to organizations wanting to strategize quality improvement initiatives. Popular tools include cause-and-effect diagrams, control charts, and stratification. Some tools include performance benchmarking,
- Data Management Software: Quality improvement programs usually involve the restructuring of routine procedures. The easiest way to ensure compliance is to invest in work order software that allows management to assign procedural checklists to team members digitally. Check out MaintainX—the world’s first work order software with team messaging—for an affordable, scalable, and user-friendly option.
Note: In the healthcare industry, it’s necessary to align your brand’s unique quality improvement plan with those developed by regulatory bodies such as Health Resources and Services Administration (HRSA) and Medicaid.
Now that you’re familiar with the basic components of quality improvement plans, let’s take a closer look at the step-by-step process of creating a program.
How to Start a Quality Improvement Program
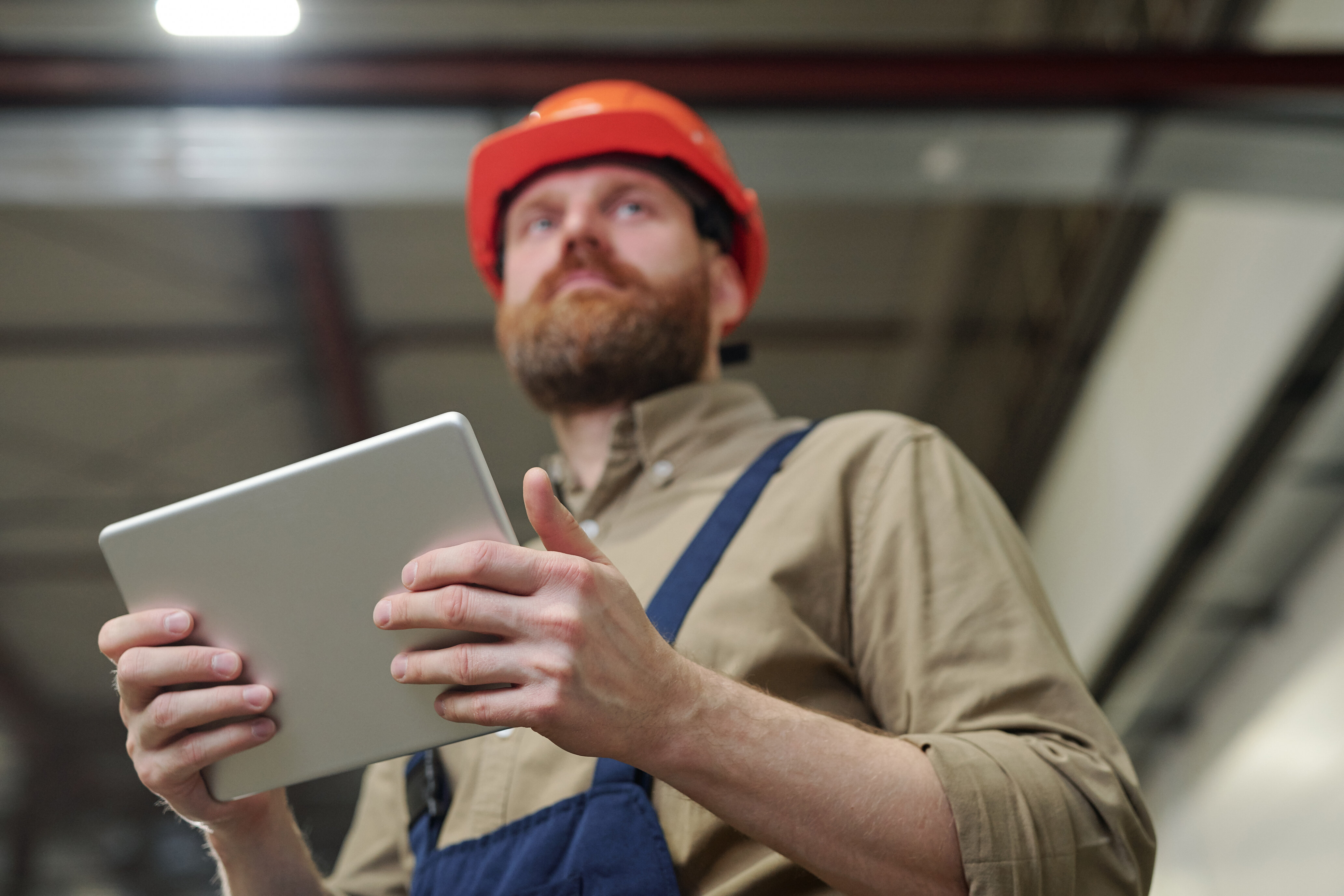
Regardless of industry, you can use the following steps as a starting point for forming your quality improvement program:
1. Articulate Your Mission Statement
Write a mission statement to serve as a north star for the program. You may want to use the commonly referenced SMART—Specific, Measurable, Achievable, Realistic, and Timely—framework to organize your thoughts. It’s essential to develop quantitative indicators of progress.
2. Recruit Your Task Force
As mentioned above, quality improvement is a collaborative effort. As such, you’ll need to recruit individuals from each department that will be affected by updated processes and procedures.
In addition, you may want to outsource experts to fill in any missing skill sets, knowledge points, and background experiences. Share your mission statement with all potential task force members and explain how the quality improvement project aligns with overall organizational objectives.
3. Organize and Distribute Background Information
Meet to identify organizational challenges and brainstorm potential solutions. Depending on the data available, you may be able to develop several clear plans of action immediately. For example, healthcare organizations have copious amounts of data on record.
They should, therefore, make clinical audits, patient registries, documented incidents, and other relevant pieces of information available to all task force members before the meeting. If you don’t have much data on record, simply share any background information you think would be helpful.
4. Match Problems with Solutions
Once everyone on the task force has reviewed the data, work together to articulate additional contextual factors—culture, inefficient systems, miscommunications—that may be contributing to organizational challenges. Once your group has analyzed the issues from all angles, work together to develop potential solutions. At this point, you should:
- Document recommended changes to processes, procedures, and systems.
- Plan to test your assumptions within small groups before assigning sweeping changes.
- Determine who will be responsible for documenting, assigning, and monitoring new SOPs.
Though it may be tempting to fix everything and the kitchen sink, resist the urge to take on too much. As the saying goes, “Rome wasn’t built in a day”—neither are world-class organizations.
5. Plan KPI Collection, Analysis, and Regrouping
Once again, data is a crucial aspect of practical quality improvement projects. Consistent data collection helps measure input, processes, and outcomes. On the other hand, inconsistent data retrieval leads to wasted time, energy, and resources on ineffective process adaptations.
For this reason, don’t leave your meeting without putting together a data management strategy! Ideally, you want to match every objective to a quantifiable measurement of progress.
For example, the maintenance department in a cement plant may measure schedule compliance, planned maintenance percentage (PMP), and mean-time-to-repair (MTTR) to evaluate asset reliability. Relevant KPIs will depend on the initiatives at hand. Develop a schedule for regularly reviewing your agreed-upon KPIs to determine what’s working and what isn’t.
6. Set Team Members up for Success
Finally, hold a presentation to introduce relevant stakeholders to your new quality improvement program. Studies show that most individuals strongly resist change—even when it’s for their benefit.
Why? Because change doesn’t only involve doing something new; it requires thinking about something new.
It’s not unusual for seasoned employees to work on autopilot, jumping from one task to the next with little thought involved. Depending on the complexity of your new policies, team members may have to extend significant mental energy to learn new ways of doing things.
For this reason, it’s crucial that management fully explain the reasons behind the changes. When employees agree upon the benefits, they’re more likely to comply.
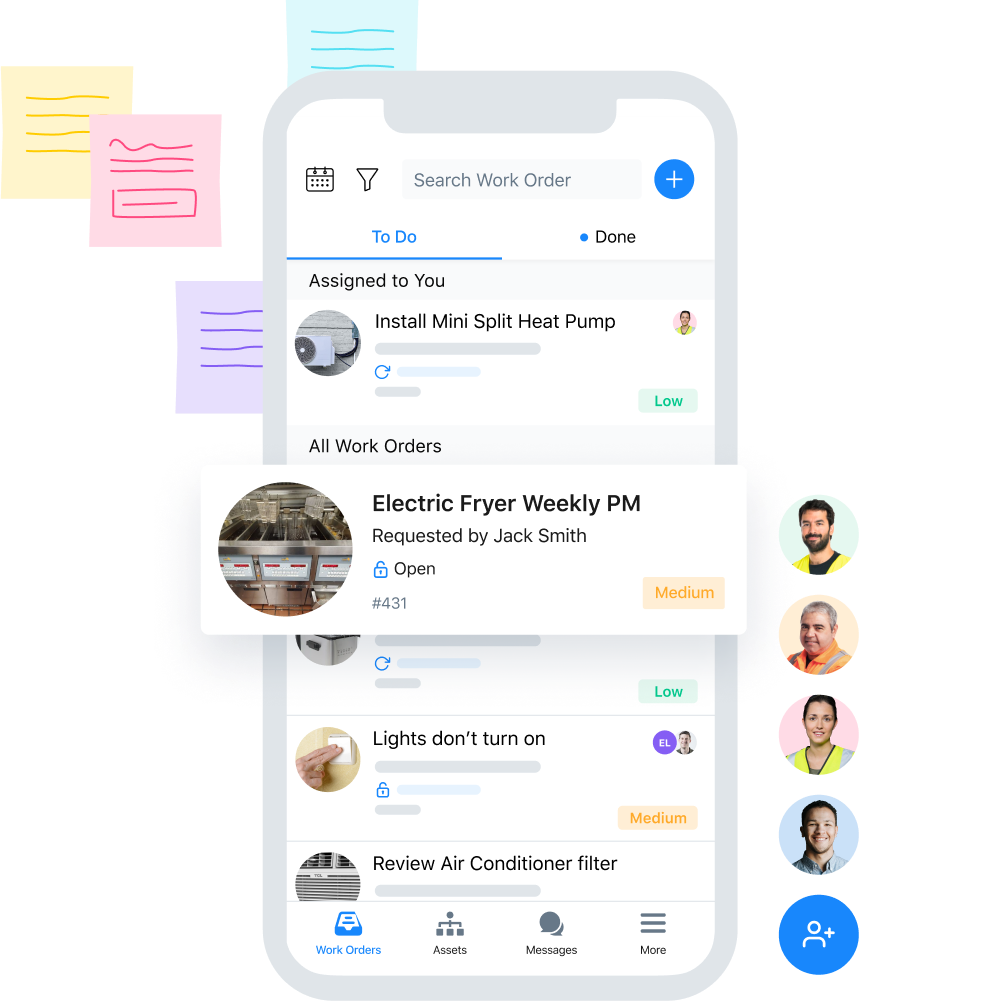
In addition, ensure your new quality improvement processes, workflows, and policies are easily accessible. Use a mobile app like MaintainX to assign digital checklists that workers can follow from the convenience of their smartphones. As a bonus, digital work order systems provide managers with real-time updates on task completion.
Common Roadblocks
Regardless of the time spent crossing every “t” and dotting every “i,” even the best plans overlook some aspect of quality control. Familiarizing yourself with the following most common quality improvement mishaps can decrease your time spent on course-correcting.
According to research conducted by the Health Foundation, quality control teams often encounter the following issues:
- The Hawthorne Effect: employees only appear to change their old habits.
- Poor communication between departments, supervisors, and employees.
- Employees don’t understand “the why” behind altered process steps.
- Disorganized progress measurement procedures.
- Unrealistic goals that demotivate employees.
- Poor budgeting and resource allocation.
- Unclearly written procedures.
- Inaccessible procedures.
- Disengaged leadership.
Consider what measures you can put in place to safeguard against these unnecessary setbacks and develop managerial standard operating procedures for them.
Improve Quality Control with MaintainX
Want to save yourself hours per week in quality improvement management? Enlist the support of work order software to assign digital work orders, provide employees with user-friendly checklists, and oversee compliance in real time.
MaintainX provides users with a flexible platform to better organize their quality improvement efforts, track KPIs, and glean insights that lead to measurable progress.
Businesses of all types—from restaurants to manufacturing facilities—use our mobile-friendly app to save time, money, and energy that could be better directed elsewhere!
Try MaintainX CMMS today for free.
FAQs
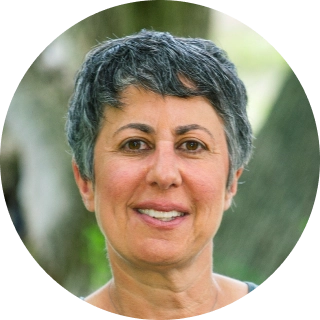
Caroline Eisner is a writer and editor with experience across the profit and nonprofit sectors, government, education, and financial organizations. She has held leadership positions in K16 institutions and has led large-scale digital projects, interactive websites, and a business writing consultancy.