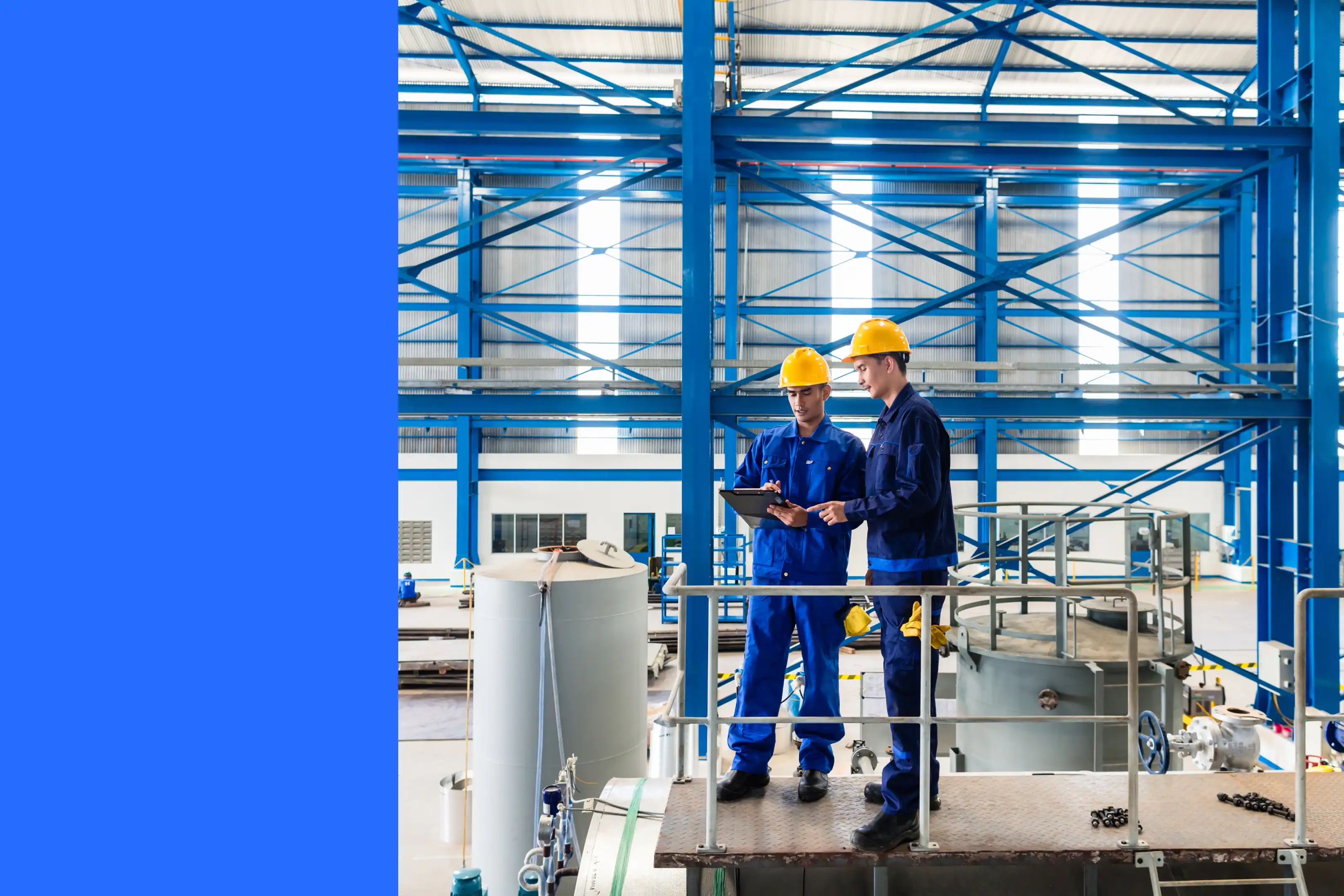
Most facilities contain more assets than their managers realize. The obvious ones, like printers, HVAC systems, and power tools, usually come with a purchase order and a paper trail. But plenty of others fly under the radar. Employee-owned property like mobile devices and laptops still count as assets for financial reporting purposes, along with digital assets like software subscriptions.
Effective facility asset management is about knowing what you have, where it is, how it’s performing, and whether it needs repairs. Failure to do so can lead to inflated maintenance costs and even potential legal consequences. Regulators like the SEC mandate accurate asset reporting, and if they find any errors during an inspection, the organization can be subject to fines and other penalties.
In this guide, we’ll explain how the right blend of software systems and processes can help you keep track of all the assets under your purview.
Key takeaways
- Facility asset management gives facility managers the visibility and control they need to make sure every item is performing the way it should.
- Common facility-related assets include HVAC equipment, electrical systems, IT-related assets, tools, software licenses, and mobile devices. Often-overlooked items also include break room appliances, uniforms, and badges.
- Done right, facility asset management leads to a number of benefits, including fewer unplanned breakdowns, reduced costs, extended asset lifespans, and better use of your existing equipment.
- Modern asset management software makes it far easier for facility managers to keep track of all asset-related considerations.
What is facility asset management?
Facility asset management is the practice of tracking, maintaining, and optimizing every physical and digital asset under your roof. A solid facility asset management program makes it easier to keep your equipment running smoothly and stay compliant with financial reporting regulations.
If you look around the shop floor, just about everything you see is an asset that needs to be tracked. It even includes things you don't see, including IT-related assets like software licenses and cloud-based systems.
You can think of this process as having two distinct parts. First and foremost, you need to make sure every item in your building has been accounted for. Then, you can focus on making sure it's working as intended, and if it isn't, determine whether it needs to be repaired or replaced.
Benefits of facility asset management
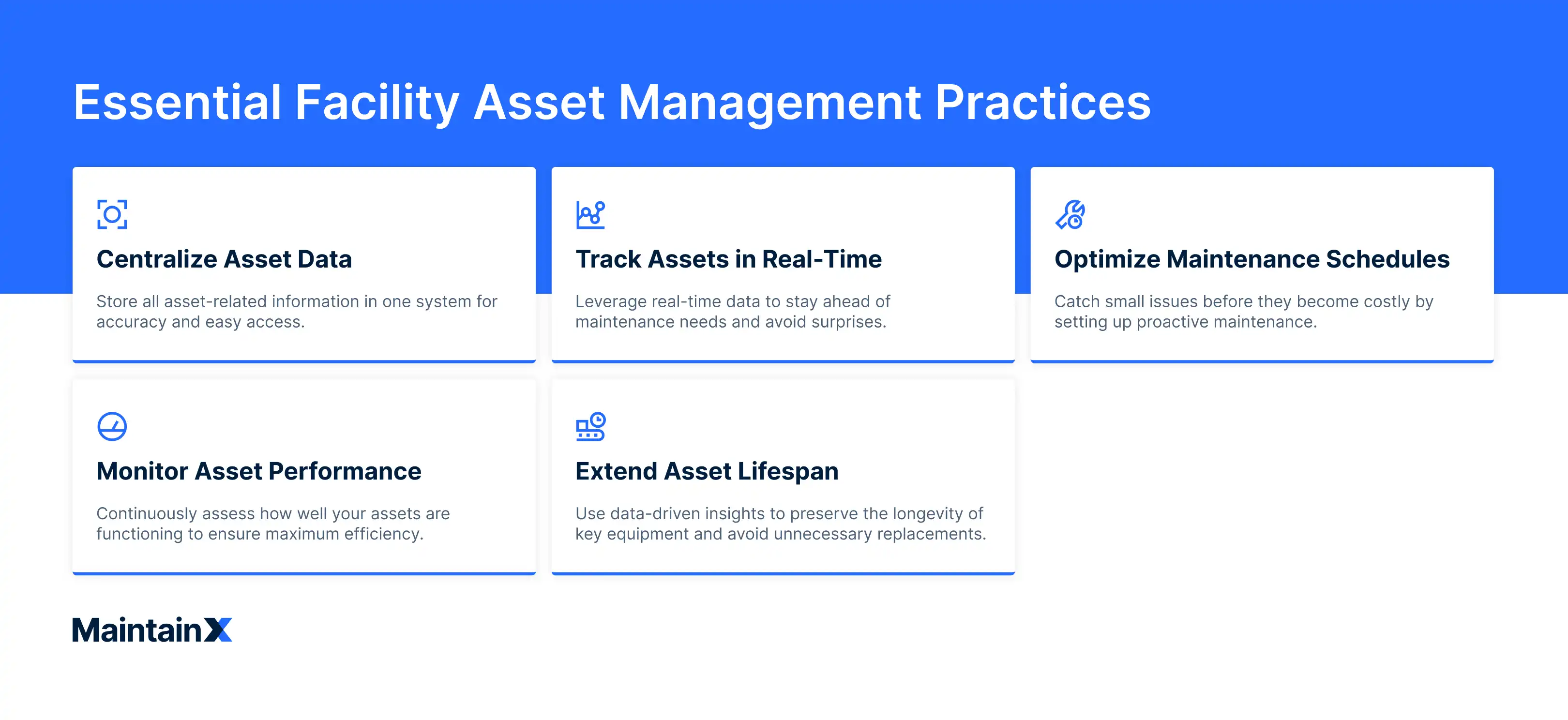
Dialing in your facility asset management plan benefits your organization in all sorts of ways. Costs drop across the board while everything from uptime to audit prep becomes much more manageable.
Here's what that looks like in practice:
Improve asset visibility
Visibility is the foundation of effective facility asset management. The more you know about the equipment in your facility, the better decisions you can make around repairs or replacement. But trying to keep tabs on every asset within your building manually is an impossible proposition. Even in smaller facilities, paper checklists and spreadsheets just aren't up to the task.
Facility asset management software makes this process a much easier lift for facility teams. These systems centralize all asset data in one place: serial numbers, repair logs, warranty info, location, and more. You know what you have, where it is, how it’s performing, and whether it’s overdue for a checkup.
Extend equipment lifespan
Assets like HVAC systems, electrical systems, forklifts, and IT equipment are major capital investments. It's imperative that they remain functional for as long as possible. Every asset has a projected useful life, but how long it actually lasts depends heavily on how well it's maintained.
With the right maintenance schedule and tracking in place, you can catch small issues before they snowball, helping your most important assets deliver maximum value over their useful life.
Reduce unplanned downtime
Just a single key component breaking down during the workday can grind an entire operation to a halt. This is known as unplanned downtime, and it's something managers try to avoid at all costs.
When you’ve got eyes on your assets and a plan in place to keep them healthy, you can prevent most of those surprises by correcting issues before they turn into major failures.
Control costs and streamline compliance
Maintenance costs go beyond big ticket repairs. Smaller issues, like over-servicing low-risk assets or forgetting to restock a part, add up fast. They can end up costing even more in the long run.
Effective facility asset management helps managers strike the right balance: enough preventative maintenance to preserve uptime but not so much that it drives up costs unnecessarily. The right level of maintenance also helps on the compliance front, making it easier to prepare for an audit or something like a fire extinguisher inspection.
What does facility asset management involve?
Facility asset management covers a wide range of asset types, processes, and responsibilities.
Here’s a breakdown of what it typically includes:
Facility-related assets
When most people think about asset tracking, these are the items that come to mind first: HVAC systems, electrical panels, printers, and other physical assets. This equipment is critical to keeping a facility up and running, as well as keeping employees and clients satisfied.
Here’s a list of the most common facility-related assets worth tracking:
- HVAC equipment
- Common room appliances
- Floors
- Signs
- Paint
- Desks
- Lighting
- Carpet
- Printers
- Computers
- Copiers/MFD fleet
- IT equipment
- Software licenses
Something worth emphasizing: don’t forget to include IT equipment and software licenses within your asset databases. Always set reminders for license renewal dates to ensure there are no interruptions in digital communication and organization.
Employee personal equipment
This second category tends to be overlooked but still needs to be tracked: employee personal equipment. This includes personal gear like radios, badges, keys, and uniforms. Both employee- and company-owned property are included here. They might seem insignificant on their own, but the cost of these items can add up quickly.
It's important to know where these assets are, who's responsible for them, and when they need to be repaired, updated, or replaced. That's especially true in industries like healthcare, where operational safety and compliance are top priorities.
Here are a few commonly tracked assets in this category:
- Safety equipment
- Mobile devices
- Uniforms
- Radios
- Vehicles
- Badges
- Keys
How to streamline asset tracking
Without the right systems in place, asset tracking can feel like a constant scramble. Here’s how to streamline the process so you can work smarter, not harder.
Centralize your asset data in one system
Asset data scattered across spreadsheets or email threads provides an incomplete view of your facility’s operations. It's nearly impossible to know what’s working, what needs fixing, and what needs to be restocked.
Facility asset management software brings order to this chaos by housing everything in one place. You can access everything you need, from asset inventory to maintenance history, from a single system. Plus, with a single source of truth, it’s easier to create reports (and harder to make errors).
Track assets in real time
When you track assets by hand, just about every report you see is already outdated. A machine, for instance, may have started malfunctioning after the last time someone checked it.
The best facility asset management programs are supported by real-time data. It's the only way to be sure that you're catching signs of failure early and replacing inventory as soon as it runs out. Accessing this real-time data requires a mix of machine sensors and facility management software like Computerized Maintenance Management Systems (CMMS).
Automate work orders linked to specific assets
Work orders tied to individual assets tell the full story of that equipment, such as when it was last serviced and what repairs were done. But logging all this detail by hand can be tedious and error-prone.
A CMMS simplifies this by automatically capturing each work order as it happens. The result is a centralized, running record for each asset including service history, checkups, license renewals, and any other relevant details.
The more data you collect, the smarter your planning becomes. Over time, patterns emerge, like certain assets needing repairs more often or how long certain parts typically last. This knowledge helps you prioritize capital investments and schedule replacements based on real usage and asset lifespan.
Sync asset records across departments and tools
Facility managers aren’t the only ones keeping track of assets. Maintenance might handle HVAC systems, while IT manages software licenses and human resources orders uniforms. If those teams aren’t sharing data, they’re going to miss things.
Software like CMMS syncs asset records across departments, helping you avoid data gaps and miscommunications.
Key metrics to track around facility asset management
Here are a few of the most impactful KPIs to keep an eye on to make sure your equipment is performing at peak capacity.
Asset utilization
How often and how effectively are your assets being used? Low utilization rates might suggest that a piece of equipment is sitting idle, driving up operating costs without delivering value. High utilization, on the other hand, can signal the need for preventive maintenance or even a backup investment to avoid burnout.
To make sure you stay in the sweet spot, define appropriate utilization ranges for each piece of equipment. Then, if possible, add sensors that automatically notify teams when utilization falls outside this range.
Total cost of ownership (TCO)
When you buy a car, you should expect to pay more than just the sticker price. You also need to account for gas, insurance, and regular repairs.
The same goes for equipment. On top of the purchase price, you should account for maintenance costs and opportunity costs like downtime losses when calculating TCO for a given asset. When you understand the true cost of an individual asset over its full lifespan, you can make smarter choices about when to repair or replace it.
Maintenance costs per asset
Maintenance costs can be tricky to track. Oftentimes, they’re spread across departments or lumped into bulk invoices, making it hard to pinpoint exactly where your maintenance budget is going.
Segmenting those costs by individual assets or asset categories (like HVAC systems, electrical systems, or leased assets) gives you a clearer picture. If a single rooftop unit is accounting for half your HVAC repair bills, for instance, you know that it probably warrants replacement.
Start building a smarter asset management program
Asset management is at its best when part of a broader facility maintenance plan. When it falls to the bottom of your to-do list, you put your facility at risk of breakdowns that bring operations to a screeching halt.
Fortunately, modern software can handle much of the heavy lifting. Learn more in our comprehensive guide.
Frequently Asked Questions
What are the challenges in facility asset management?
Facility asset management comes with several challenges, including tracking a large volume of assets, maintaining accurate records, ensuring compliance with regulations, and managing maintenance schedules efficiently. Overcoming these challenges requires the right combination of software systems, processes, and proactive decision-making to ensure optimal asset performance and cost control.
What is the difference between asset management and facility management?
Facility management is the broader discipline of managing the entire physical environment of a building. Asset management focuses specifically on tracking, maintaining, and optimizing physical assets within that environment.
What role does technology play in facility asset management?
Technology helps facility managers gain visibility, automate tasks, and make informed decisions. Real-time asset data and mobile access allow for proactive maintenance and better compliance tracking across the entire facility.
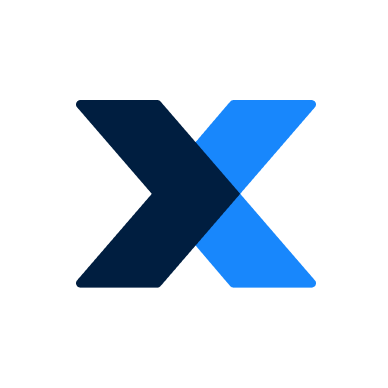
The MaintainX team is made up of maintenance and manufacturing experts. They’re here to share industry knowledge, explain product features, and help workers get more done with MaintainX!