FRACAS stands for Failure Reporting Analysis and Corrective Action System.
Unplanned downtime costs manufacturers nearly $1 trillion in lost productivity, unsatisfied customers, and revenue each year, underscoring the importance of identifying maintenance issues early so technicians can make reactive fixes fast.
But reactive maintenance and identifying problems shouldn’t be a crapshoot. We know that maintenance should be systematically organized so that corrective action, and better yet, preventive maintenance, can be planned. In addition, firms can learn from issues and adjust for potential future problems by implementing failure reporting, KPI analysis, and a corrective action system, otherwise known as FRACAS.
FRACAS Defined
FRACAS is a process to help companies report, correctly classify, and thoroughly analyze failures or bottlenecks in their maintenance processes.
FRACAS is a systematic process for managing problems and avoiding unplanned downtime.
The FRACAS standard originated in military circles before crossing over to commercial and manufacturing industries. A successful FRACAS program works as a closed-loop system, in which problems are defined, contained, identified, and corrected.
“New digital tools . . . help to accelerate and standardize the cost-benefit analyses and decision-making that underpin maintenance and reliability activities.”
McKinsey
In this post, we’ll discuss why a FRACAS process is essential, detail the steps of the process, and describe best practices to implement FRACAS at your company.
Three Primary Steps of FRACAS
FRACAS programs have three primary steps: reporting, analysis, and corrective action. Here’s an overview of each.
Step 1: Failure Reporting
The most important part of the FRACAS process, Failure Reporting, involves collecting any information and failure data about the problem and what’s needed to resolve it. The more information you’re able to collect, the more data you can use in the following steps.
FRACAS example: A piece of equipment goes offline, or a processing line operates inefficiently in a manufacturing environment. In the reporting step, you’ll want to document when the problem was first identified, the individual who noticed the issue, and any warning signs, among other details. The more information you have, the more likely you’ll be able to figure out the problem and prevent it from happening again.
Step 2: Analysis
Now that you have your reporting data, determine how to fix the problem by identifying the cause. While there is a significant amount of flexibility in this phase, the goal is to perform a complete evaluation to determine an appropriate resolution. Conducting a root cause analysis will identify the cause of the failure.
CMMS software comes in very handy during the analysis step of the FRACAS process, as techs can learn about repair histories to identify trends and relationships that can lead to more streamlined solutions.
Step 3: Corrective Action
FRACAS is designed as a closed-loop system, and this final corrective action step should close the loop. After that, it’s time to resolve the issue. This final corrective step should bring the process full circle. Always document the complete process and avoid a similar issue in the future.
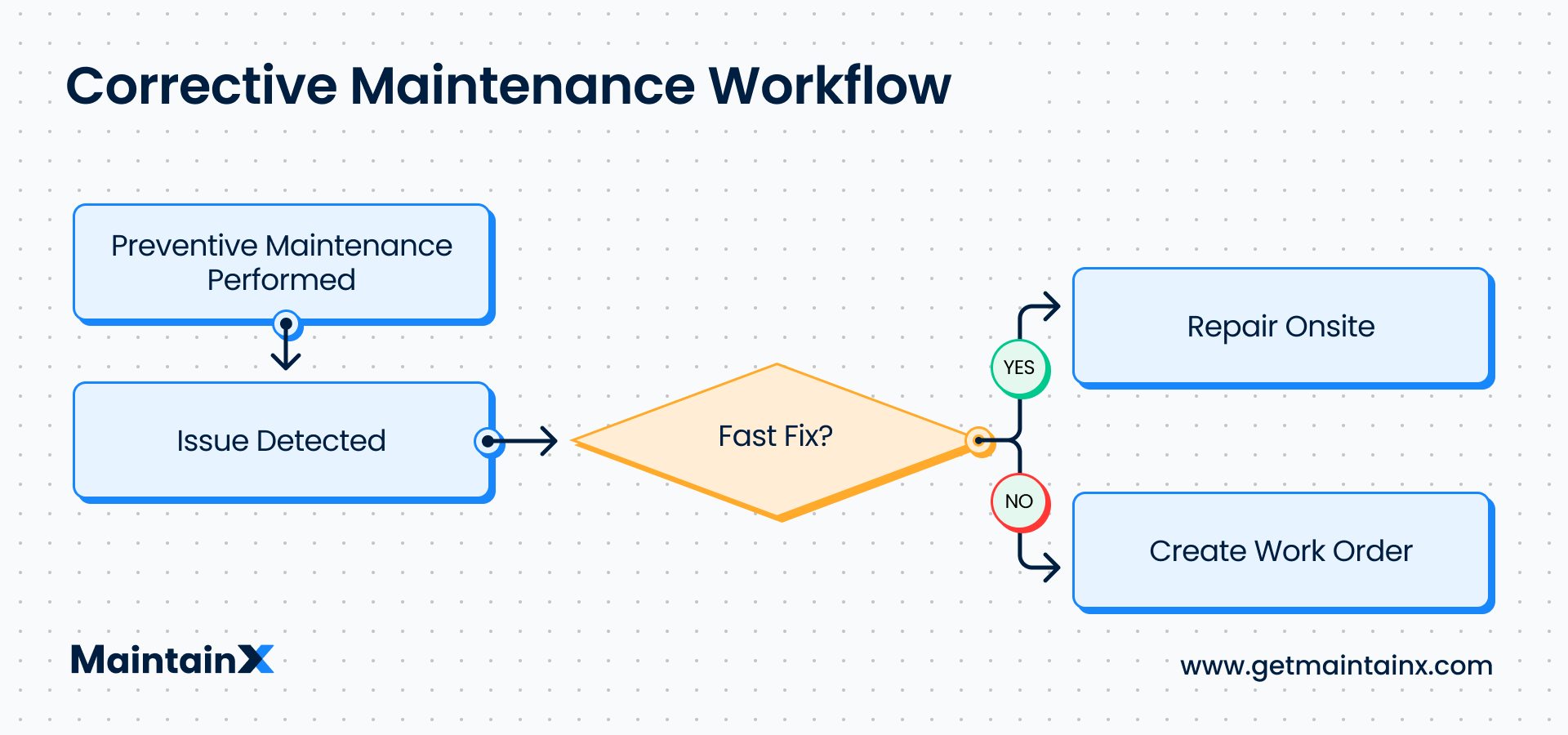
Key Benefits of FRACAS
So what are the key benefits of FRACAS? The overriding benefit is to enable an organization to quickly and effectively correct failures, learn from its mistakes, and avoid unplanned downtime.
Additional key benefits include:
- Documenting problems and mistakes so the same issue doesn’t happen again
- Reducing rework, scrap, and customer dissatisfaction
- Establishing a continuous improvement cycle with a robust, efficient maintenance plan to reduce overhead costs and keep equipment running effectively for its useful life cycle
- Determining corrective action for failures to implement quickly if there’s a next time
- Meeting ISO requirements
- Minimizing safety risks
- Creating a database based on problems in the past to reference easily
CAPA and FRACAS
CAPA stands for Corrective and Preventive Action (or Corrective Action/Preventive Action). While it’s not the same as FRACAS, it’s another closed-loop system designed to identify specific actions to mitigate failures. While both CAPA and FRACAS work to track problems and quickly streamline solutions, the strategy implemented usually depends on organizational preferences.
Implementing FRACAS
Ideally, an organization implements FRACAS in three phases: discovery, design, and enactment.
Discovery
The discovery phase establishes the guidelines of the process, such as who takes ownership of tasks, process flow, and establishing procedures.
Design
In the design phase, a company standardizes the FRACAS process. Robust CMMS software, like MaintainX, helps document information and assign tasks to specific teams or employees. MaintainX creates reports for easy analysis and assigns work orders.
Enactment
Finally, in the enactment phase, the company implements and executes the tasks established in the design phase based on the process established in the discovery phase. It’s a great maintenance cycle, with each phase depending on the one before it.
The Value of a CMMS
A CMMS doesn’t just come in handy during the design implementation phase but throughout the FRACAS process. MaintainX helps companies organize data, streamline data in real time, and make it available to anyone on the team to assess and analyze.
The best CMMS will document instructions, checklists, parts and materials, and manuals.
Check out MaintainX for free.
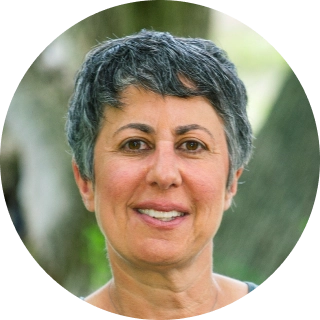
Caroline Eisner
Caroline Eisner is a writer and editor with experience across the profit and nonprofit sectors, government, education, and financial organizations. She has held leadership positions in K16 institutions and has led large-scale digital projects, interactive websites, and a business writing consultancy.
See MaintainX in action