Faced with the choice between preventive and reactive maintenance, the answer seems obvious. Preventive maintenance will save you money and time while prolonging your asset life. But can you optimize your maintenance work even further?
Instead of simply performing maintenance on a schedule, condition-based maintenance (CBM) can help you fine-tune your approach. It involves using visual inspections, scheduled tests, and sensor devices to monitor equipment performance, streamline asset management, and determine the most cost-efficient time to perform maintenance.
This guide reviews condition-based maintenance, how it differs from predictive maintenance, and how to leverage it to increase maintenance efficiency and reduce costs.
What is condition-based maintenance?
Condition-Based Maintenance (CBM) is a proactive maintenance strategy that involves performing maintenance based on the specific conditions of equipment or assets.
The goal of CBM is to perform maintenance activities only when necessary based on the actual condition of the equipment rather than on a fixed schedule or after a failure occurs. CBM involves regularly or continuously monitoring equipment conditions, identifying anomalies that could indicate imminent failure, and then performing maintenance.
This approach aims to maximize the efficiency of maintenance efforts, minimize downtime, and reduce overall maintenance costs.
Examples of condition-based maintenance
Common CBM diagnostic methods include vibration analysis, ultrasonic testing, oil analysis, infrared thermography, and pressure analysis. CBM devices collect data while the equipment operates and then, through analysis, help teams determine when to perform maintenance. Examples of this in practice include:
Example #1: Pressure analysis on piping systems
One common application of condition-based maintenance is using pressure readings on piping systems. When levels are closely monitored, maintenance staff can proactively identify when possible leaks may occur. For example, manufacturers who rely on pipe or liquid systems, such as food and beverage producers, use CBM to track pressure and diagnose problems.
Example #2: Oil analysis
If you manage a fleet of vehicles, such as in the transport or construction industry, you may be used to scheduling an oil change based on a calendar schedule (such as every three months) or mileage (such as every 5,000 miles driven). But if you use CBM, your maintenance schedule may be informed by reading a gauge that monitors oil particles. This may mean changing the oil every 8,000 miles instead of 5,000 miles or after four months instead of three months. The advanced monitoring would save costs on engine oil.
How condition-based maintenance works
CBM workflows range from simple to complex. However, most industries follow a similar model emphasizing data collection, equipment forecasting, and corrective action. Depending on the resources available to you, you can automate many of these processes. A Computerized Maintenance Management System (CMMS), for example, can help with data collection, automatically triggering work orders based on equipment conditions, and scheduling maintenance tasks.
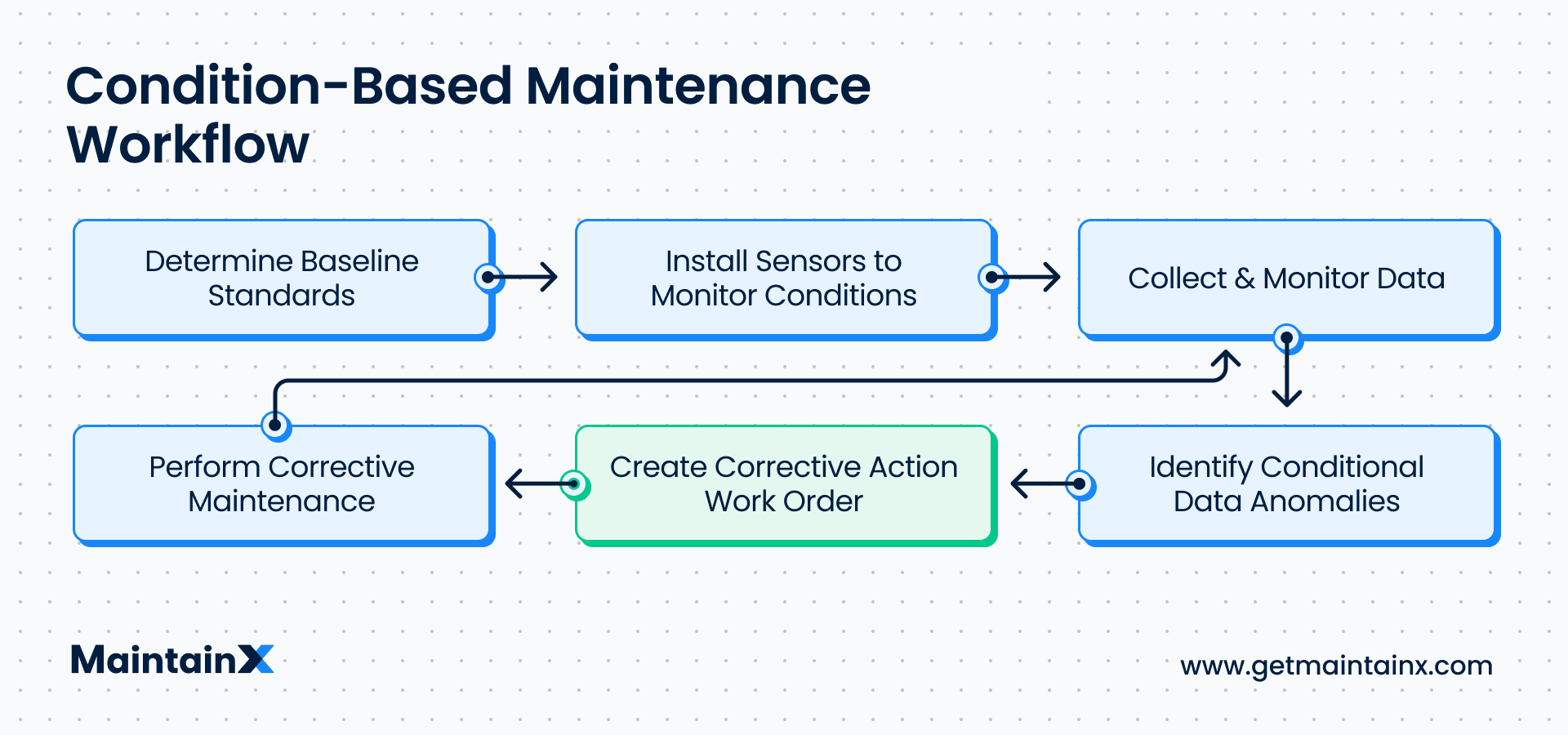
As the illustration shows, condition-based maintenance is a multi-step process. Let’s explore what those steps involve.
Determine baseline standards
The first step is to define the parameters or standards for your assets’ optimal performance. This could mean, for example, knowing that a machine performs best at temperatures within a 25 to 30-degree celsius range. With that information, your team knows that any temperatures above that range would indicate that the equipment is overheating.
Install sensors to monitor conditions
Monitoring asset conditions requires sensors that pay close attention to properties like temperature and pressure. These sensors could include pressure monitors, thermometers, thermal imagers, and more.
Collect and monitor data
The installed sensors regularly collect and analyze data from the equipment. Monitoring techniques here include:
- Vibration analysis: This type of condition-based monitoring system measures the vibration frequencies and levels of machinery. Maintenance teams then use this information to analyze the health of equipment and its components to detect problems, such as bent shafts, resonance, looseness, bearing failure, and imbalance. For example, a damaged fan will produce more vibration signals than a fan in good working condition.
- Infrared thermography: Infrared thermography is a condition-based monitoring system that uses thermal imagers to detect radiation from an object. The imagers convert the radiation to temperature and display its distribution in real time. This helps detect when a piece of equipment is overheating. Examples of infrared tools include infrared thermal imaging cameras, infrared scanning systems, and infrared thermographers. They are mostly used to check the levels of gas, liquids, and sludge; inspect bearings; examine refractory insulation; and monitor mechanical and electrical conditions of motors.
- Ultrasonic analysis: Ultrasonic analysis detects and converts high-frequency sounds into audio and digital data to help identify potentially failing assets. This condition-based monitoring system uses contact and non-contact data collection methods to determine different types of detectable failure. Contact (structure-borne) methods are generally used for faults that generate high-frequency noise, such as lubrication problems, bearing faults, broken rotor bars, and gear damage. Non-contact (airborne) methods, on the other hand, help detect pressure and vacuum leaks on compressed gas systems in addition to various electrical applications.
- Oil analysis: Maintenance teams analyze oil health, contamination, and machine wear. They can determine whether the additives are active or depleted and whether the viscosity is right, among other oil fluid properties. An oil analysis program will help confirm if a piece of equipment is operating as it should.
- Electrical analysis: Here, the focus is on the incoming power quality of assets. Circuit current is measured using motor current readings from clamp-on ammeters. Electrical analysis helps determine if an asset has an abnormal electricity supply.
- Pressure analysis: It’s important for equipment that carries air, gas, or fluid to maintain the correct pressure. Maintenance teams use pressure analysis to continuously monitor pressure levels in real time. They get alerts of sudden drops or spikes and can respond before the problem becomes more serious.
Identify conditional data anomalies
This step involves identifying any deviations from the optimal standards established in step one. Teams can achieve this via regular conditional testing or by using Internet of Things (IoT) devices to automate the process. Any deviations can then trigger the required maintenance work.
Create work order
While many teams still prefer spreadsheets and pen-and-paper work orders, work order software really does make a difference. A computerized maintenance management system (CMMS) allows you to manage multiple work orders simultaneously, assign priorities, add work instructions, comment directly in work orders, and communicate via instant chat. In addition, you can monitor work orders from start to finish, sharing and receiving real-time information from the shop floor.
Perform corrective maintenance
Work order management systems allow managers to create digital work instructions, checklists, and templates that can guide the maintenance process. This system helps ensure that your maintenance technicians know exactly how to approach corrective maintenance. With chat features, your team members can collaborate and seek or offer any necessary support. Also, as in the case of MaintainX, the global procedures library contains standard operating procedures from various industries that users can access at any time.
When to use CBM
Is CBM right for your company? Like every strategy, it has its advantages and disadvantages. While routine maintenance offers many benefits over reactive maintenance, it also puts teams at risk of over-maintenance and increased costs. You could end up spending time and resources maintaining assets that are fine.
Condition-based maintenance, on the other hand, helps teams eliminate redundant maintenance tasks by focusing on the assets that need attention. However, despite helping to save money in the long run, CBM can be costly to implement due to the necessary technology. As such, before implementing CBM, weigh the implementation costs against the potential savings.
Another factor to consider is the nature of the work environment: CBM may be less effective in working conditions that leave sensors vulnerable to damage. In addition, CBM works best with assets that have well-defined failure modes and experience gradual degradation. For assets without these well-documented failure modes, CBM may not be the best choice. Here are some other pros and cons to consider when deciding whether or not to implement CBM.
In summary, successfully implementing CBM can help companies significantly reduce maintenance costs in the long run. But, the initial stages of implementation require high upfront costs that aren’t always achievable for small businesses that are still growing. Consider pursuing a planned maintenance strategy if your company falls into this category.
Alternatively, CBM is best suited for large companies with vast resources. However, different maintenance scenarios call for different maintenance strategies—even for large companies.
How to run a condition-based maintenance program
Establishing a CBM program doesn’t have to be difficult. Here’s how to develop your CBM program in six simple steps:
- Step 1: Select the equipment you want to monitor. Give priority to the equipment that is key to business success, is high value, or has a longer lifespan. To do this, perform a criticality analysis.
If you’ve been recording your asset data with a CMMS, you’ll find this step easier. Look at historical asset data such as equipment failure records, spare parts consumption, mean time between failure (MTBF), and more. MaintainX CMMS can generate these reports with just a few clicks, providing you with greater insight into your asset performance and allowing to you rank them properly.
- Step 2: Identify the equipment’s failure modes, including all the known failure modes and probable ones. An RCM analysis can help with this. Always focus on the failure modes to manage CBM strategies.
- Step 3: Select the right condition-based monitoring system. Ensure the CBM system you choose can handle the failure modes identified in the previous step.
- Step 4: Define your asset baseline limits in the system. For the system to warn you when the equipment starts failing, you need to define the acceptable condition limits. To ensure your entire team has this information on hand, use a CMMS to store the data, allowing technicians an easy way to cross-reference readings and identify anomalies.
- Step 5: Establish your CBM program. At this point, you should define tasks and assign responsibilities to your maintenance team. The focus should be on data collection and recording.
- Step 6: Analyze the data and act as needed. The data from your inspections and sensors should help you plot trends and schedule maintenance work whenever necessary.
MaintainX makes condition-based maintenance easy
MaintainX can make condition-based maintenance simple to get up and running. Take advantage of features like:
- Sensor integration: Condition monitoring is crucial to condition-based maintenance. MaintainX provides seamless integration with third-party sensors that monitor your asset conditions and automatically collect data. This way, all your data will be automatically stored in MaintainX, and you can record it manually if necessary.
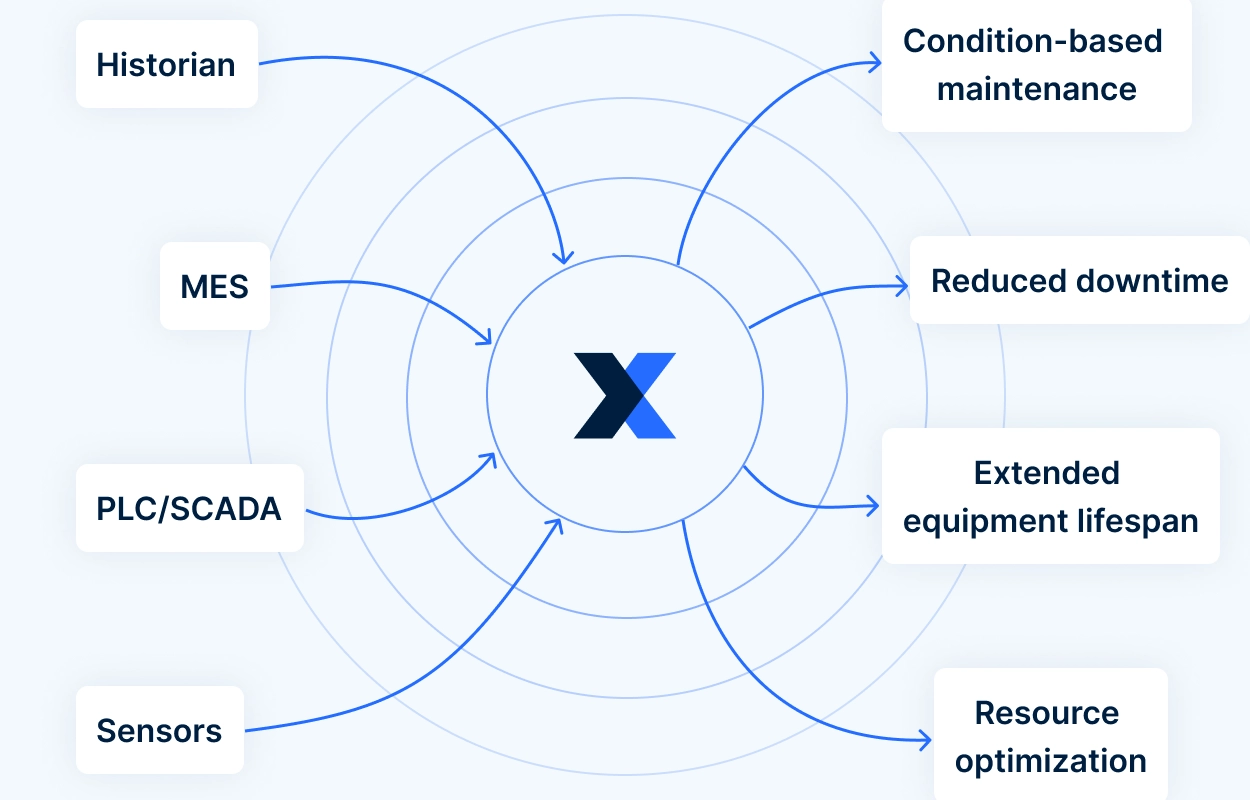
- Work order management: With MaintainX, you can trigger work orders and schedule maintenance in response to equipment conditions such as temperature, pressure, vibration, and more. MaintainX’s integration allows you to monitor assets remotely, all on a single dashboard.
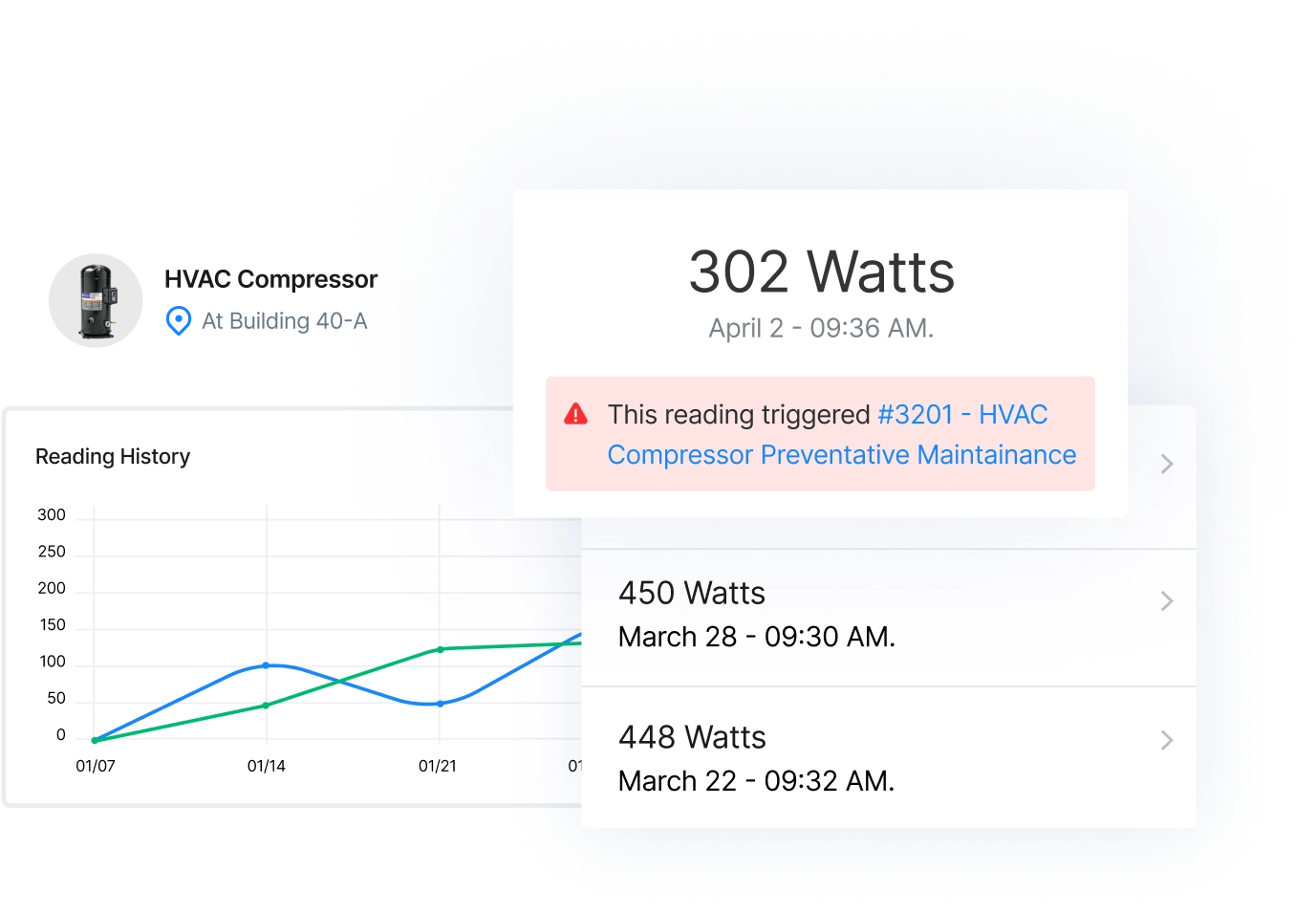
- Digital SOPs and checklists: When asset conditions necessitate a work order, you want technicians to be empowered to complete the required maintenance work as quickly and thoroughly as possible. With MaintainX, you can easily create digital checklists and attach them to work orders, providing your technicians with a step-by-step guide to completing their tasks.
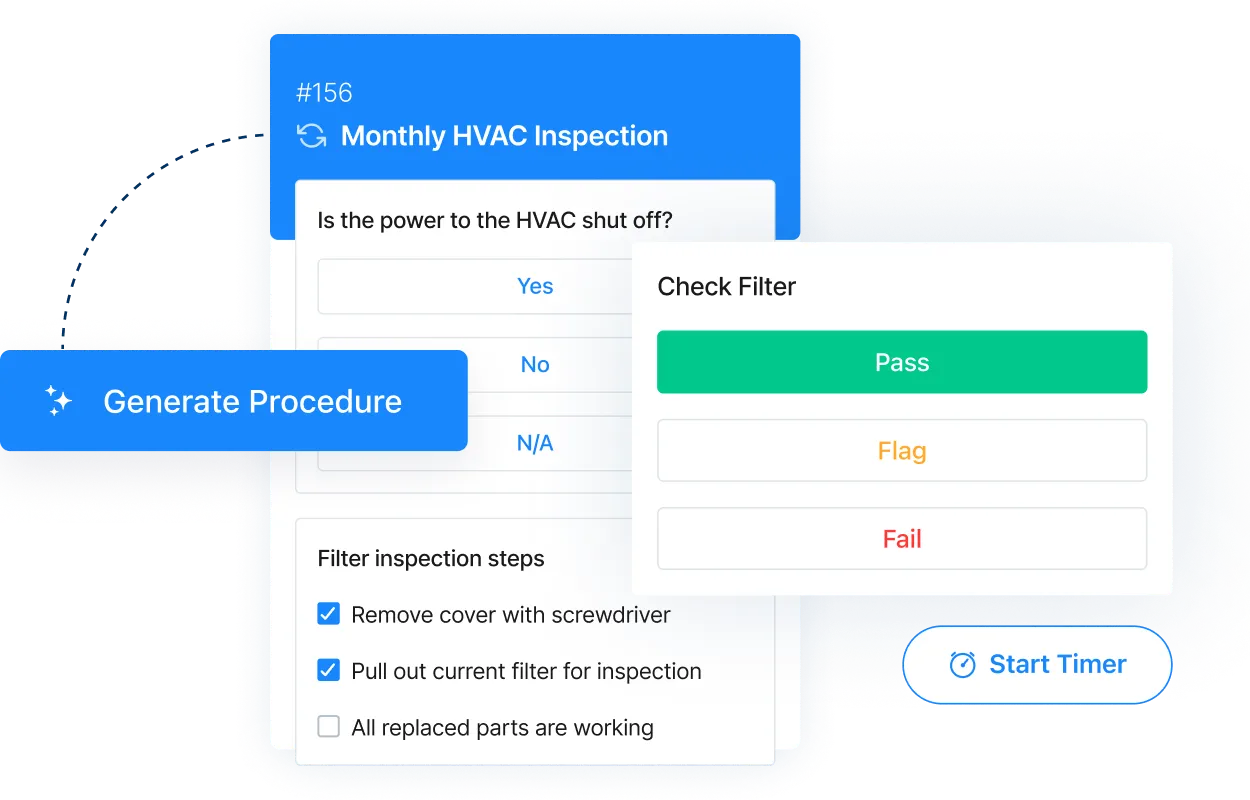
Condition-based maintenance is more than just a strategy; it’s about fostering a maximizing your resources and equipment availability. Equip your operations with the right tools to elevate your CBM practices and empower your team to drive success every step of the way. MaintainX puts condition-based maintenance at your fingertips. Try MaintainX. It’s free!
Condition-based maintenance FAQs
The terms condition-based maintenance and predictive maintenance (PdM) are often used interchangeably and for good reason.
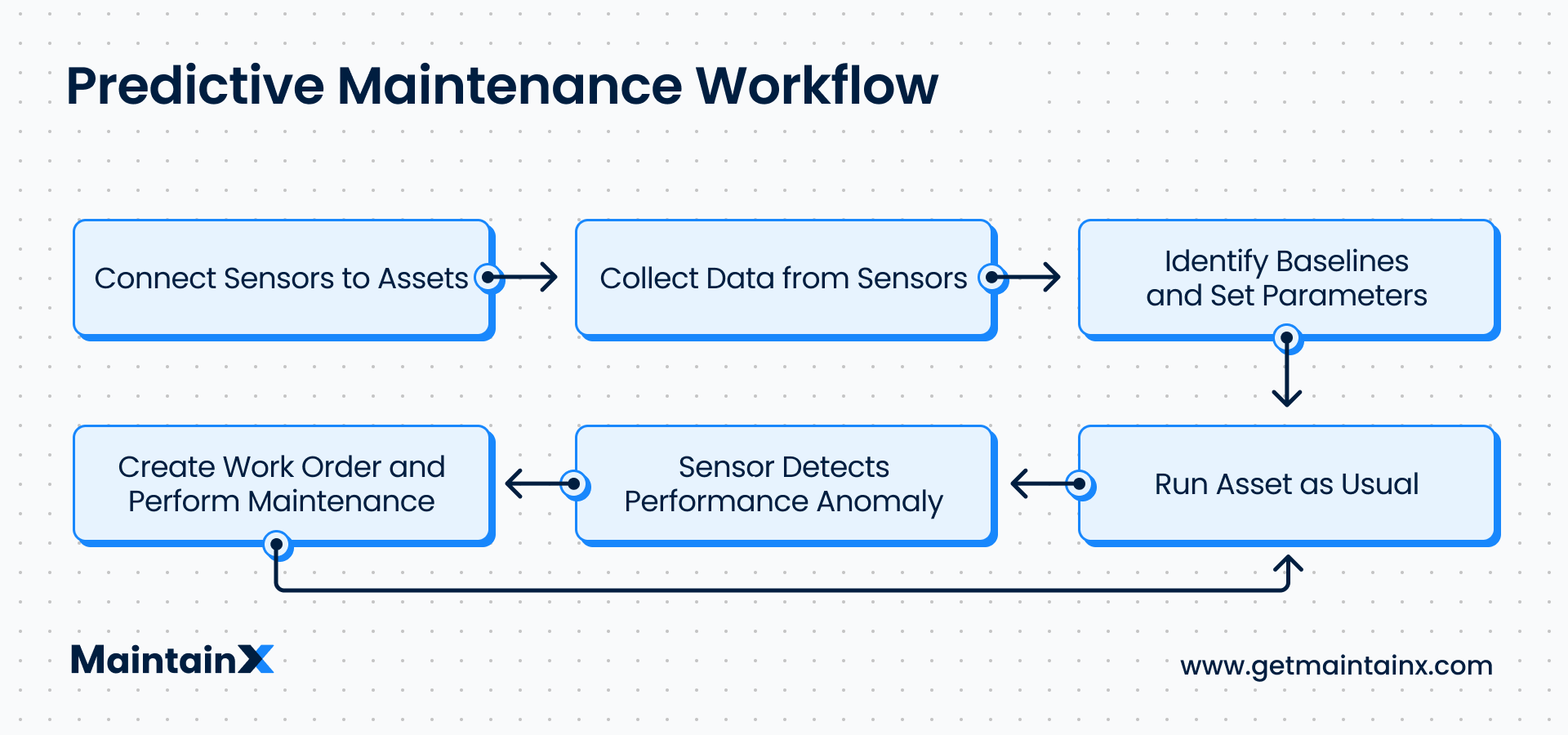
Both strategies encompass the same maintenance best practices:
a) Relying upon data to determine whether or not upkeep is necessary and
b) preventing unplanned downtime with proactive maintenance.
However, that’s where the similarities end. Here are the differences between CBM and PdM:
Predictive maintenance is a more advanced, accurate, and dependable version of condition-based maintenance. However, the technology is so new that it’s not financially feasible for most organizations at this time.
As previously mentioned, the usefulness of CBM varies depending on organizational needs, budget size, and industry. Use the information outlined in this article as a starting point to investigate if a condition-based maintenance strategy will benefit your company.
See MaintainX in action