Did you know that downtime can cost facilities an average of $25,000 an hour? That’s why it’s important that organizations prioritize preventive maintenance.
However, unexpected breakdowns are inevitable. Whether you have a preventive maintenance program or not, things will still break. That’s where breakdown maintenance comes in.
For some, it feels easier to wait for equipment to fail before fixing it. While this approach isn’t perfect, it can still work—if you have the right plan in place. In this article, we’ll look at how breakdown maintenance works and how to implement it effectively to keep operations running smoothly.
What is breakdown maintenance?
Breakdown maintenance is maintenance that a technician or team performs on broken-down, malfunctioning, or faulty equipment. It is a type of maintenance strategy where equipment or machinery is run until it fails. Technicians make repairs and replacements to the equipment at the time of failure. This approach is characterized by a lack of planned preventive maintenance activities. It’s often referred to as reactive maintenance or corrective maintenance.
Key components of breakdown maintenance include;
- No scheduled interventions
- Cost considerations
- Limited planning
- Shorter equipment lifespan
- Unplanned downtime
- Risk of safety incidents
Because teams cannot schedule breakdown maintenance in advance, companies need to be able to redirect resources toward repairs every time a piece of equipment fails. Ideally, whenever breakdown maintenance is necessary, company maintenance systems should be able to remedy the situation without coming to a complete halt.
Examples of breakdown maintenance
Of course, there is never a convenient time for downtime. This type of maintenance can and should be minimized through strategic planning.
However, there are instances where breakdown maintenance makes sense:
- Non-critical equipment that is easily replaceable.
- Parts that are either disposable, cheap, or easily available.
- Assets with shorter life cycles.
Examples that fall into these categories include:
Light bulbs: Facilities will use light bulbs until they burn out, at which point teams will replace them. This is because the inconvenience of a single bulb burning out is minor, and replacing bulbs preemptively would be more labor-intensive and costly.
HVAC filters: Monitoring and trying to extend the useful life of a filter in an HVAC system isn’t always a good use of time, so it makes more sense to use them until they reach the end of their life.
Low-cost equipment: Tools and equipment that are inexpensive and easy to replace, such as small electric motors, fans, or hand tools, are often run to failure. The cost and effort to replace them is lower than implementing a preventive maintenance program.
Non-critical redundant systems: In some systems with redundancy, where there are backup units available, teams may allow non-critical components to fail before replacing them. For example, in data centers, non-critical servers might be run to failure because other servers can take over their workload.
Personal devices: Cell phones, laptops, and other personal electronic devices are also typically used until they no longer function properly rather than maintained preventively.
Types of breakdown maintenance
Breakdown maintenance comes in two forms: run-to-failure and emergency maintenance. Both play a crucial role in how companies manage equipment failures, but each approach has its place. Knowing when to apply them can help teams manage costs, minimize downtime, and maintain control during unexpected failures.
1. Run-to-failure maintenance
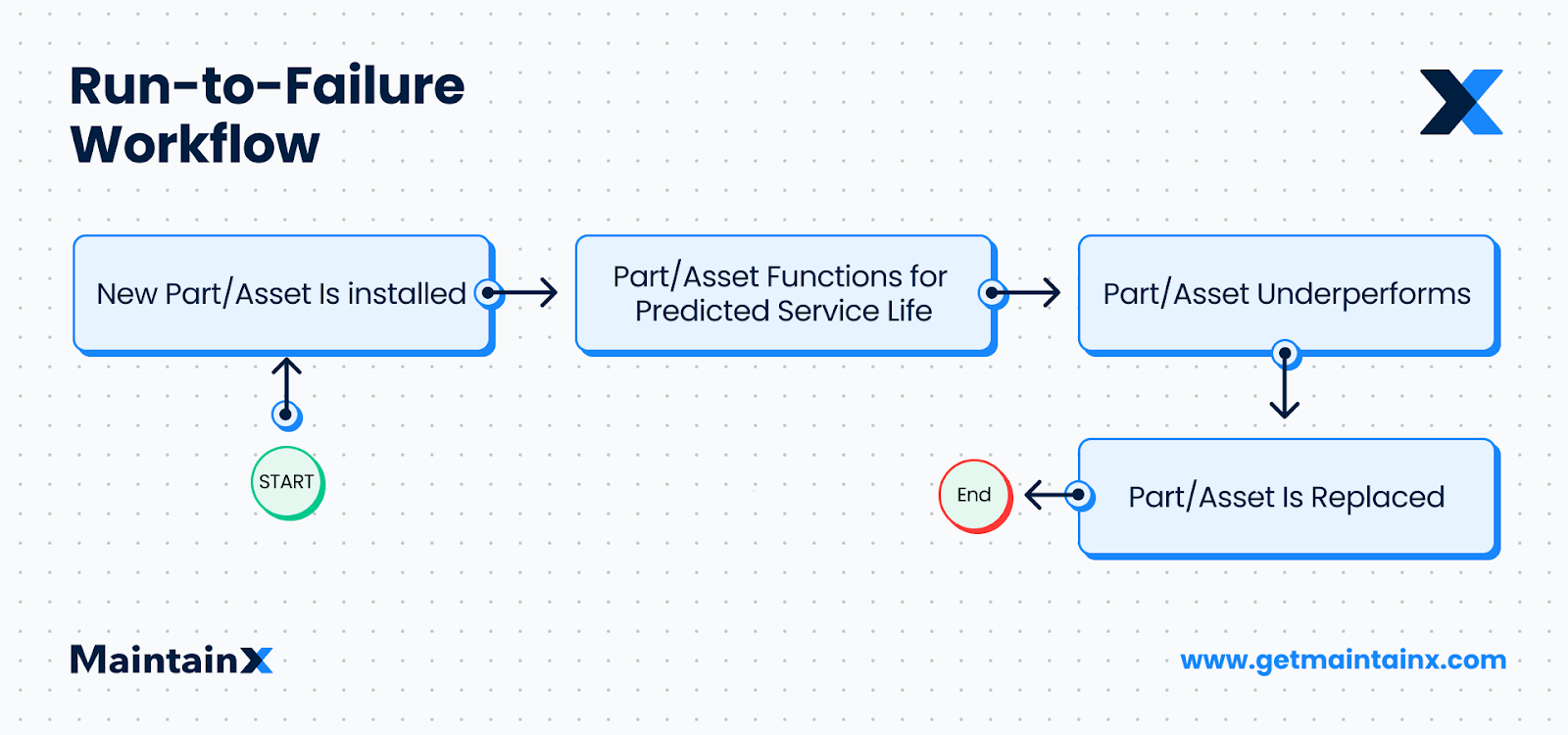
Run-to-failure maintenance means the organization is prepared for a machine to stop working at some point in the near future. Under this system, teams allow equipment to operate until it breaks down, and only carry out repairs or replacements after the failure. For example, a company might use run-to-failure maintenance on non-critical machinery, such as a backup conveyor belt or a secondary fan, knowing that if these components fail, they won’t disrupt overall operations. Ideal candidates for run-to-failure maintenance include assets that:
- Are easy to replace.
- Won’t jeopardize operational systems or personal safety when they break.
In such instances, the cost of repairing the asset “on the fly” is less than the associated preventive maintenance costs. Run-to-failure maintenance should be reserved for inexpensive or unimportant parts and machinery.
2. Emergency maintenance
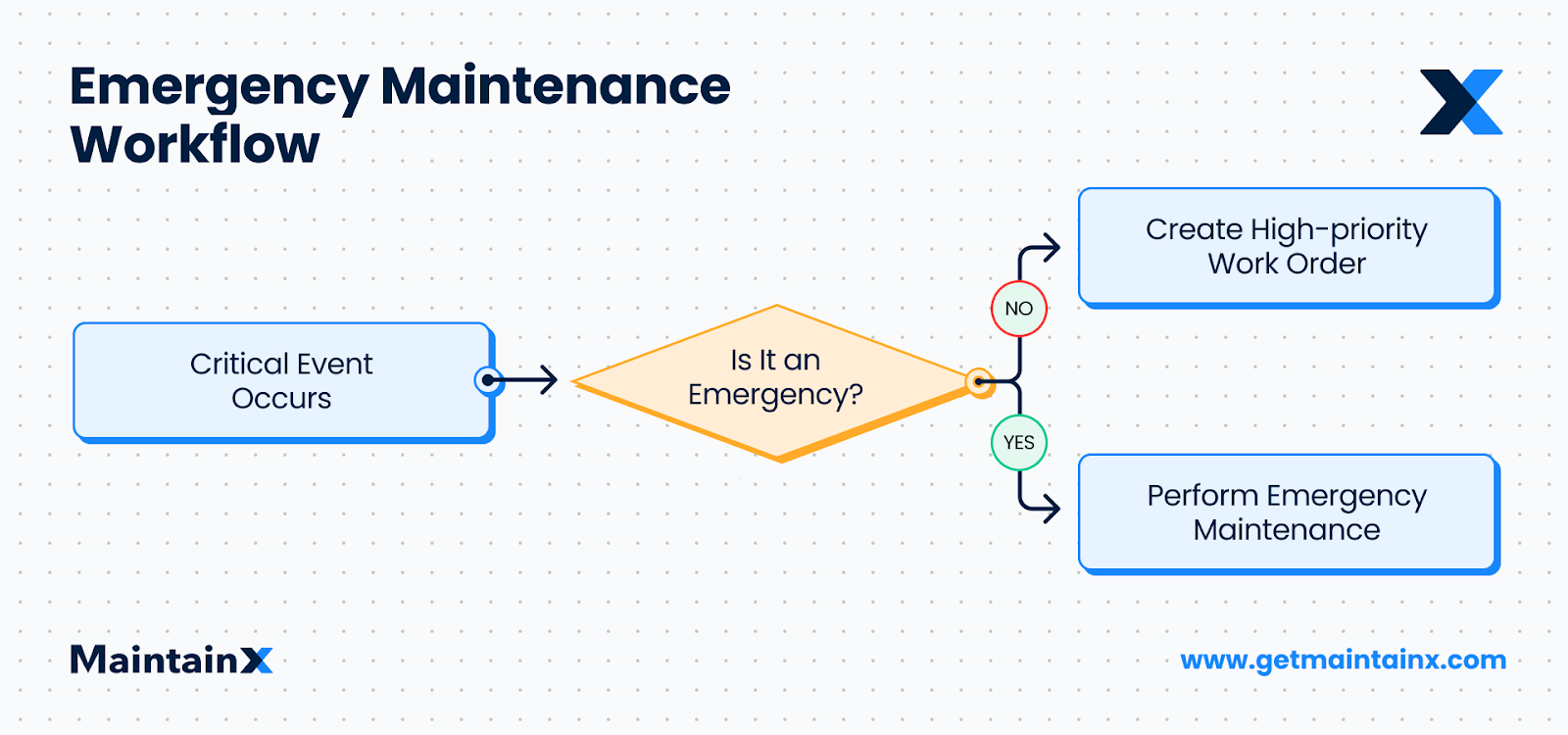
Emergency maintenance is maintenance work a team conducts when an important piece of equipment stops working unexpectedly and needs replacing immediately. In other words, this is the kind of maintenance no team wants to deal with!
Emergency breakdowns lead to costly repairs, financial losses, and even safety risks. For instance, imagine a manufacturing plant where a critical conveyor belt fails. As the failure is unexpected, the company isn’t prepared with spare parts. Because production grinds to a halt, the company has no choice but to expedite the shipping of replacement parts. Depending on staff capacity, they might even have to call in an outside technician and pay overtime to get everything back on track as quickly as possible. These urgent measures drive up costs, adding unnecessary strain to the company’s budget.
Breakdown maintenance procedures
Whether the maintenance is run-to-failure or an emergency, most breakdown situations follow a similar workflow:
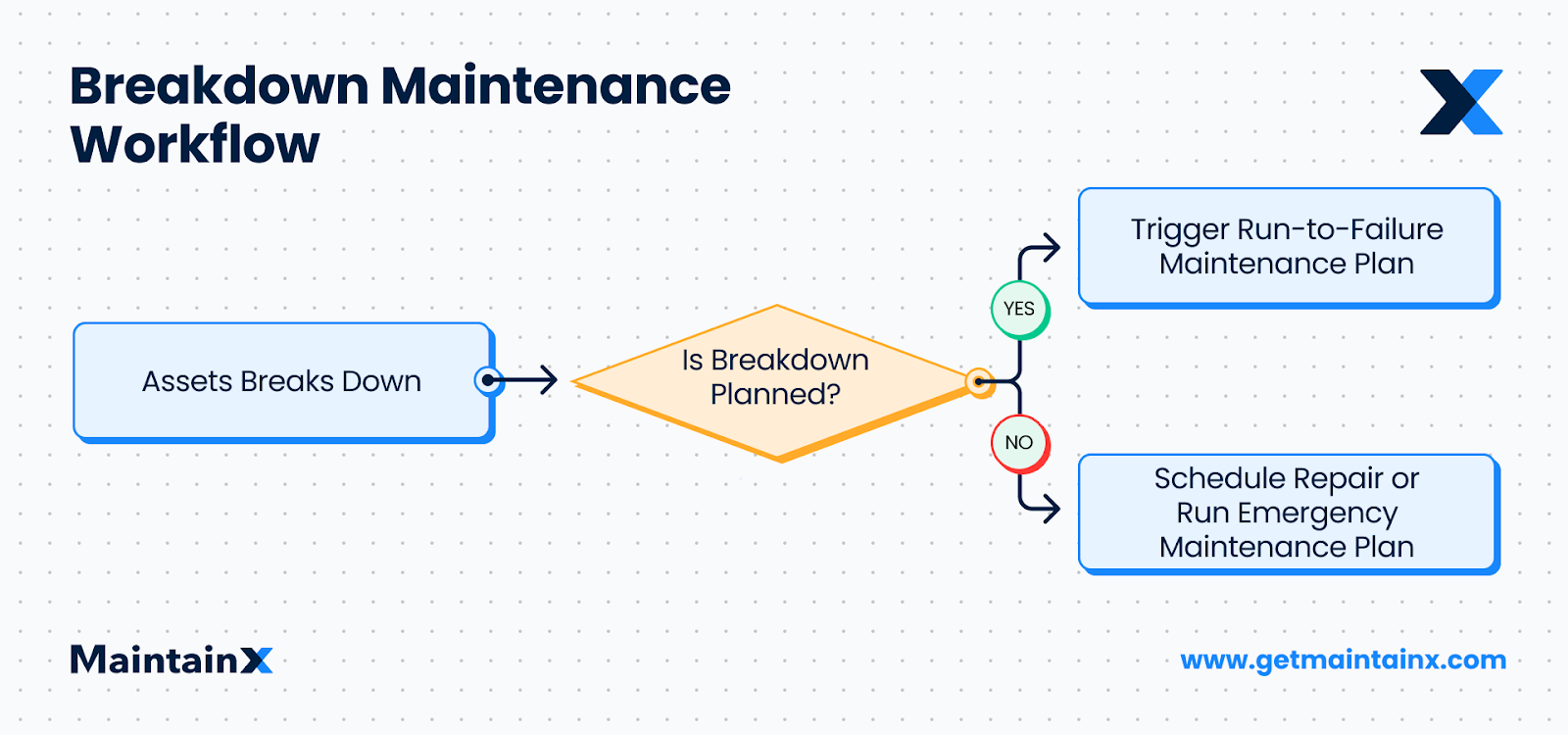
- A maintenance operator detects an equipment issue and then alerts management by phone, email, or CMMS software.
- Management creates and assigns a work order for asset inspection.
- The assigned technician analyzes the problem and provides feedback on the expected time, parts, and costs associated with repair or replacement. If the equipment malfunction being evaluated cannot be replicated, this may lead to a significant waste of resources.
- If possible, the assigned maintenance worker fixes the issue.
- The worker restarts the machine to verify the correct performance.
- The issue is “closed” within a CMMS, spreadsheet, or paperwork order.
After maintenance is complete, the maintenance team may use the newly acquired information to track and prevent similar failures in the future as part of a preventive maintenance program. Additional parts or devices may be ordered and stocked to reduce the length of any future equipment downtime.
Breakdown maintenance best practices
One advantage of breakdown maintenance is that it requires less advance work compared to preventive maintenance. However, it still requires some deliberate actions to ensure you execute it properly. Here are five key steps to take when committing to a reactive maintenance strategy.
1. Identify suitable assets
Breakdown maintenance is best suited for assets that are cheap, easy to replace, and non-critical for production and safety. Weigh the cost of an asset going into downtime against the cost of implementing a preventive strategy. The losses due to the potential equipment failure must be less than the potential cost of a preventive maintenance approach.
2. Monitor performance
Even if you’re going to run an asset until it fails, it helps to be able to anticipate when that failure will occur. To accomplish this, pay close attention to the piece of equipment’s performance over time so you can better understand its failure modes. Take advantage of software tools like a CMMS with robust reporting features. This way, when a failure does happen, you’re prepared to get the asset back up and running.
3. Document failures
Keeping detailed failure records helps you determine how well a breakdown maintenance strategy is working for you. If you notice that certain failures are recurring despite repeated repairs, it might signal that you need to consider a change in your maintenance strategy. Accomplishing this is easiest with software that allows you to track and store your maintenance data over time.
4. Stock spare parts
When a breakdown does occur, you want to ensure that your team can carry out the necessary repairs as quickly as possible. Delays due to missing or unavailable spare parts will only extend your downtime and result in greater losses. Implement a robust inventory strategy to ensure that you always have the parts you need.
5. Empower staff
Ensure that your team is equipped to carry out swift and robust repairs in the face of a breakdown. Use standard operating procedures to provide detailed, step-by-step guides to executing breakdown maintenance tasks. This way, you’ll eliminate any time wasted trying to figure out how to approach a repair, and your team can hit the ground running when a failure happens.
What are the pros and cons of breakdown maintenance?
This type of maintenance has its merits when part of a comprehensive maintenance strategy. These potential advantages include:
Pros
- Extended component life cycles: If an asset component is beginning to show signs of wear without negatively impacting system performance, it may be fiscally prudent to use the part until breakdown.
- Lowered preventive maintenance costs: In some cases, when a component can be easily replaced, preventive maintenance can be more expensive than a breakdown maintenance strategy. Additionally, breakdown maintenance has no initial setup costs.
Nevertheless, a complete breakdown maintenance approach is considered to be a “high-risk” strategy. Major equipment breakdowns can have catastrophic effects on productivity, unnecessary costs, and customer dissatisfaction. The disadvantages of the strategy are:
Cons
- Low long-term cost-efficiency: Using faulty equipment until it completely breaks down may increase energy costs in the long term. Addressing an issue on an urgent basis typically costs more than scheduled downtime. Additionally, the financial losses associated with a breakdown, and with failing to meet output targets, can be considerable.
- Threatens production: If implemented across an entire facility, breakdown maintenance leaves critical or essential assets at risk of malfunction. This could impede production schedules and negatively affect your business reputation.
- Decreased asset lifespan: Using asset components until failure may create a domino effect leading to decreased performance and total system failure.
- Decreased safety: Poorly maintained assets run the risk of unexpected failures, which can threaten production and compromise safety. Performing procedures under pressure, technicians may take shortcuts when it comes to safety measures.
Can preventive maintenance eliminate all breakdowns?
In a perfect world, yes. In real life, no. Both preventive and predictive maintenance reduce the risk of equipment breakdown. Nevertheless, unexpected equipment failures will happen, machines will need breakdown maintenance at some point. However, busy maintenance teams can reduce stress by following standard operating procedures and maintenance best practices.
Balance reactive and proactive maintenance with MaintainX
No matter your maintenance strategy, MaintainX can simplify the process and streamline your workflows. Take advantage of the undisputed #1 CMMS on the market to take your maintenance to the next level with features like:
Work order management
Schedule preventive maintenance tasks in advance and manage emergency work requests all in one place. You’ll be able to assign, prioritize, and track real-time progress right from the shop floor. In addition, enable your technicians to capture the right data at all times using pre-filled templates, time tracking, signatures, and required fields.
Parts inventory management
Whether reactive or preventive, MaintainX ensures you have the necessary parts on hand to carry out maintenance tasks. Automated low-quantity alerts and purchase orders will help you automatically restock parts once they fall below a certain level, guaranteeing you’ll never run out of parts again. You’ll spend less on costly emergency orders and reduce carrying costs by stocking only what you need.
Data-driven insights
MaintainX’s reporting and resource management modules help you generate data-driven insights to make the best decisions for your team. Labor insights give you an instant glance into how work is distributed across your team. You can assess each technician’s workload against their capacity to ensure the best results. Also, take advantage of reporting into critical metrics like Mean Time Between Failure (MTBF) and Mean Time To Repair (MTTR) to determine how well your maintenance program is working.
Breakdown Maintenance FAQs
Consider factors like budgets, the criticality of the equipment, its value, potential safety risks, and historical failure patterns. Conduct a cost-benefit analysis comparing breakdown maintenance to other maintenance strategies to determine how much a breakdown maintenance strategy will affect your bottom line. A common rule of thumb is to implement breakdown maintenance for equipment that would cost more to maintain regularly than to fix upon failure.
Breakdown maintenance is generally more suitable for simple or low-value equipment than critical assets. Critical or high-value equipment may require more preventive maintenance strategies to prevent costly asset failures.
If you leverage a breakdown maintenance program, consider implementing robust safety procedures, keeping spare parts readily available, and having contingency plans in case of unexpected failures to reduce the risks. You can also consider implementing maintenance management software to streamline breakdown maintenance tasks.
As Computerized Maintenance Management Systems (CMMS) become more affordable, maintenance teams are increasingly adopting preventive maintenance (PM) programs to reduce downtime. Studies show that realistic PM strategies can save companies 12 to 18 percent in costs.
Breakdown maintenance may always be necessary due to the unpredictable nature of man-made machinery. However, the maintenance industry continues to shift toward preventive and predictive maintenance plans. Preventive maintenance (PM) dictates that potential asset vulnerabilities are addressed before they ever pose a problem. It involves using the manufacturer’s guidelines and asset history to schedule routine maintenance procedures.
Conversely, breakdown maintenance waits to resolve issues until they have become apparent. Predictive maintenance utilizes special tools that evaluate specific equipment usage to schedule maintenance procedures at cost-effective time frames prior to breakdown. Both predictive and preventive maintenance are proactive in nature, while breakdown maintenance is reactive.
See MaintainX in action