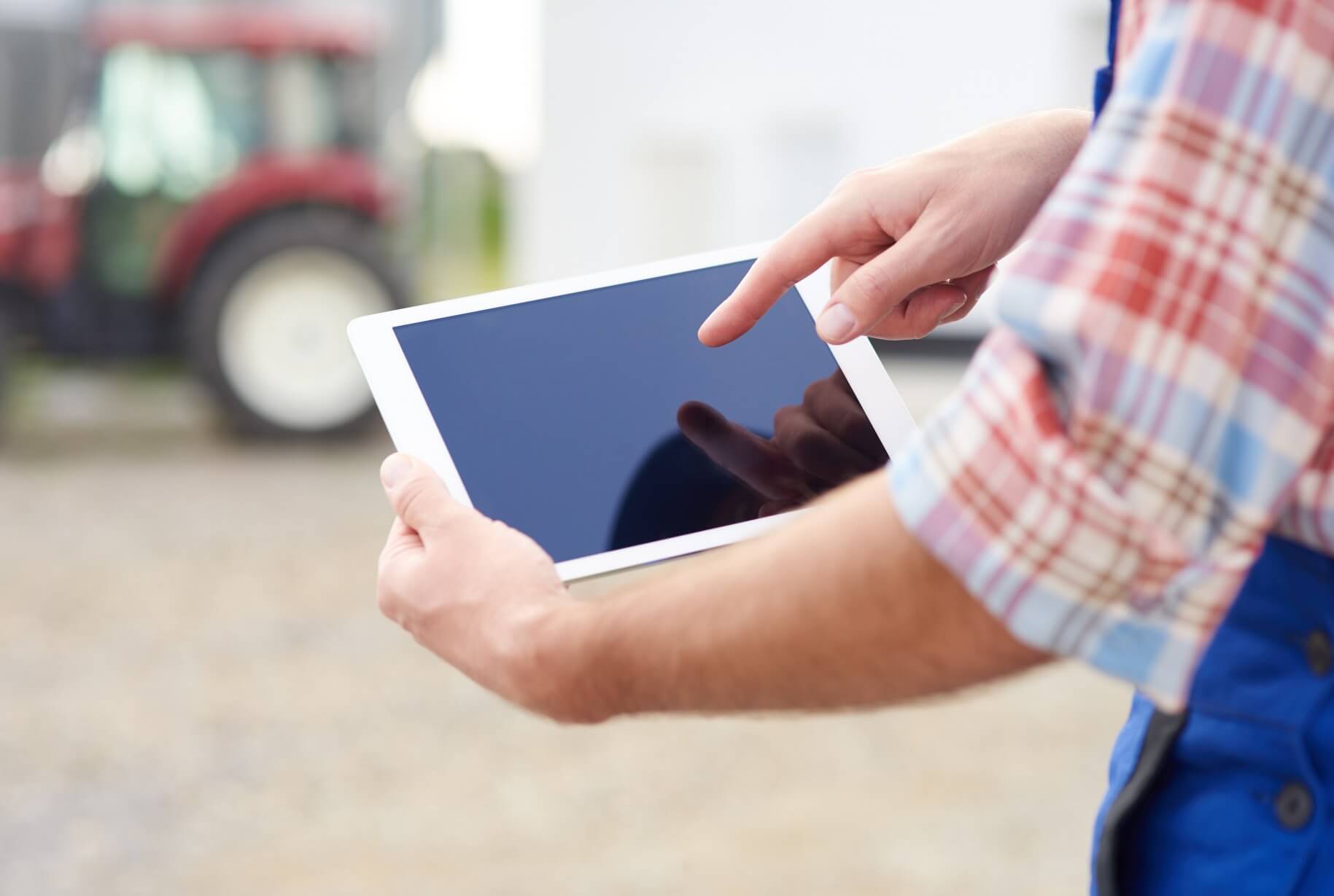
Company-wide standard operating procedures (SOPs) keep everyone on the same page at all times to continuously improve operational efficiency.
Digitized standard operating procedures across industries support connected workforces by coordinating work, proving safety compliance, and ensuring quality control.
In this post, we’ll take a closer look at how several industries are using MaintainX’s computerized maintenance management system (CMMS) software to simplify the process of creating, assigning, and monitoring routine O&M processes. Let’s get started:
5 Industries Using Standard Operating Procedures
1. Manufacturing
Manufacturers deal with many areas of compliance, including laws and regulations, product safety, and health and environmental regulations. Across a company, facility management, operations managers, maintenance teams, and management teams use SOPs to meet state and federal laws and regulations.
Manufacturers can manage maintenance and demonstrate compliance regulations with manufacturing SOPs that promote quality control and continuous improvement.
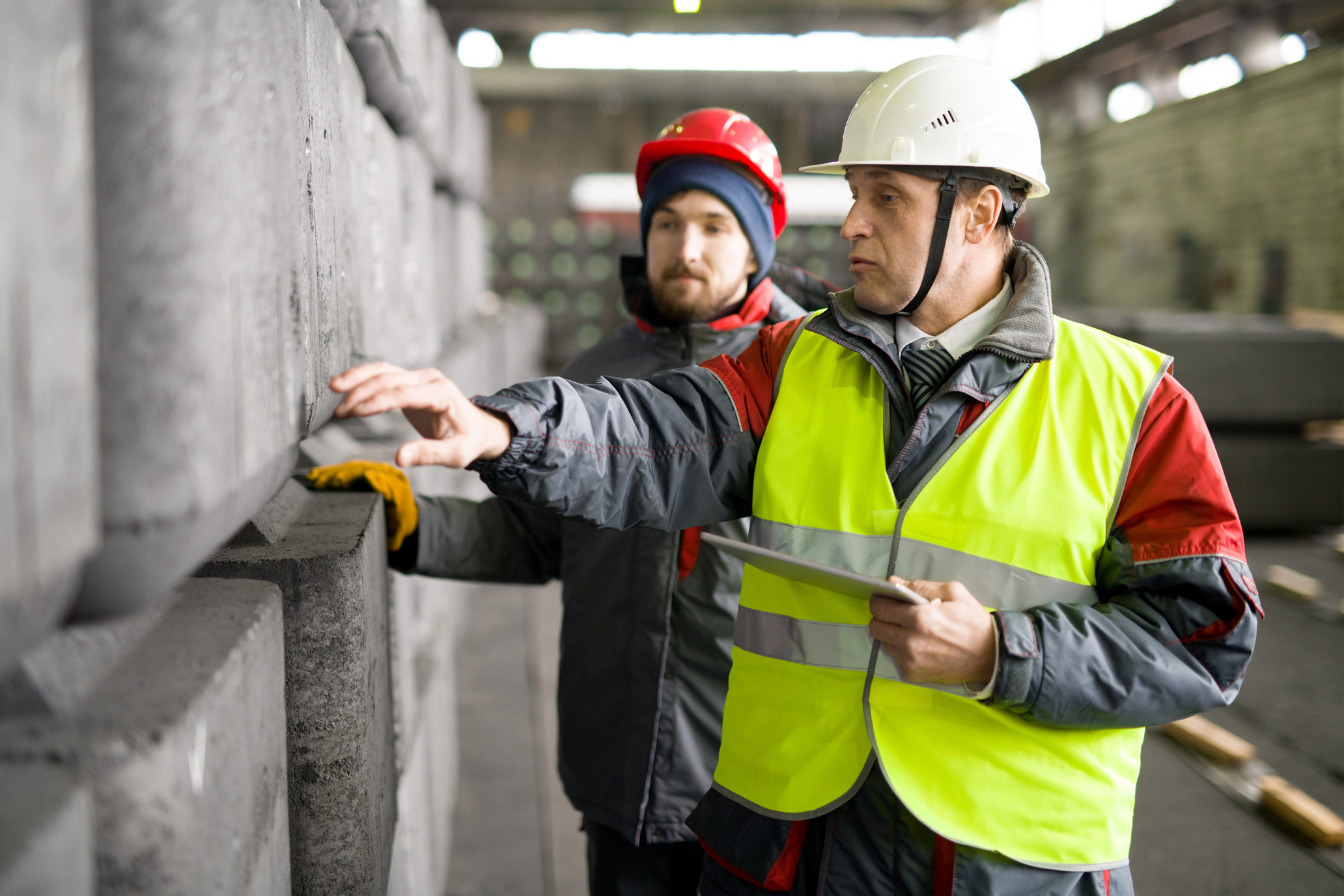
Standard operating procedures enhance a company’s ability to produce and market final products at an extraordinary rate, especially with competition from international markets.
Quality management plans and standard operating procedure documentation provide opportunities to locate inefficiency and downtime in the manufacturing process. Also, SOPs provide evidence of regulatory compliance on the factory and warehouse floor. Online SOP templates can help build an organizational culture of excellence.
2. Warehousing
A warehouse management system (WMS) or plan provides inventory control and supply chain management. An automated WMS combines supply chain processes with technology to increase efficiency and productivity. WMS delivers real-time information about warehouse operations. Warehouse managers can then create standard operating procedures to automatically trigger cycle counts with detailed instructions.
An efficient warehouse management plan needs to be accurate and fast. Warehouse best practices produce lean warehouse operations, avoid downtime, achieve rapid growth, and satisfy customers. The best WMS creates more efficient warehouse processes by managing real-time inventory and storage information throughout operations.
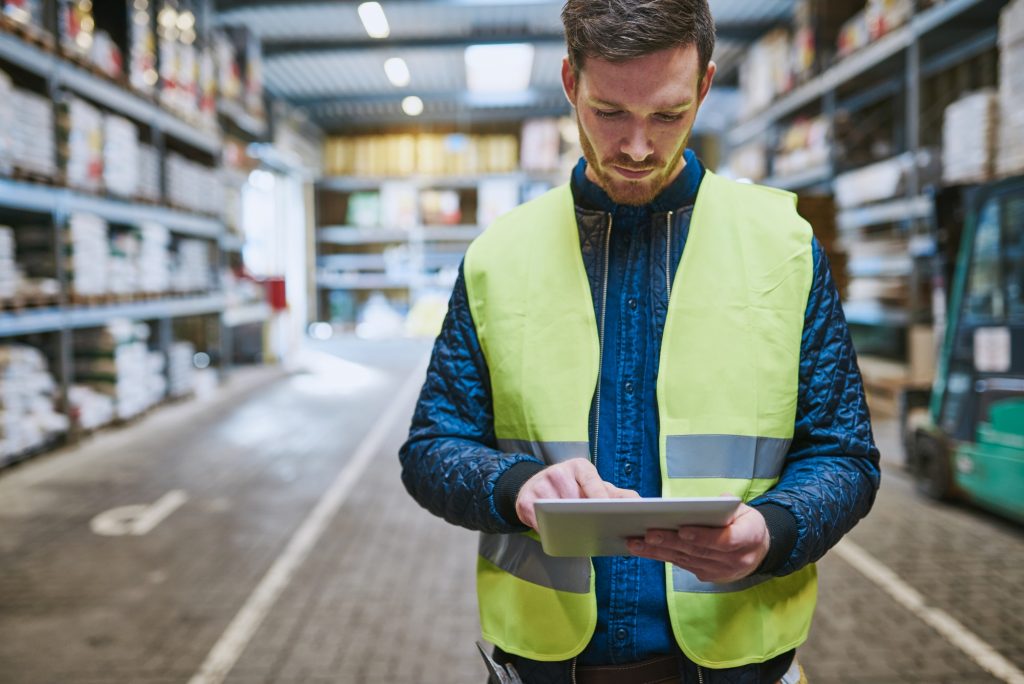
Not surprisingly, digital SOPs provide accurate, current information to managers, warehouse workers, and operations personnel for on-the-spot decision-making and supply chain management. Dashboards and checklists produce real-time supply chain data, accurate inventory counts, increased processing volume, and on-the-spot decision-making.
More than anything, online standard operating procedures in the warehouse and on the factory floor eliminate paper-based workflows and alert failures to comply. Thus, warehouse best practices, such as receiving and cross-docking, work best with standard operating procedures.
Warehouses that use online SOP are more likely to:
- Manage supply chain demands easily
- Build pinpoint accuracy
- Grow more efficient
- Maintain flexibility
- Transform operations
With digital checklists and dashboards, standard operating procedures help monitor warehouse quality assurance plans, warehouse safety rules, and industry compliance regulations.
3. Restaurants
Restaurant owners, chefs, kitchen staff, and front-of-house waiters execute SOPs daily. Quality and up-to-date SOPs keep restaurants running safely and efficiently. Online restaurant SOPs can provide easy-to-follow preventive maintenance plans, quality assurance guidelines, regulatory inspection checklists, equipment tracking, and food safety rules.
Indeed, we recommend streamlining standard operating procedures for both the front-of-house and the back-of-the-house. Train new staff, communicate in seconds with all employees, and keep guests happy and coming back for more long term. The FDA’s Hazard Analysis and Critical Control Point (HACCP) Training and Monitoring includes food safety training, quality improvement, record keeping, and employee training.
However, written SOPs are useless without great communication, training, documentation, and implementation. In many restaurants, SOPs aren’t well-documented. Instead, staff members are trained to do things a certain way, and it’s assumed that everybody knows “this is how we do things here.”
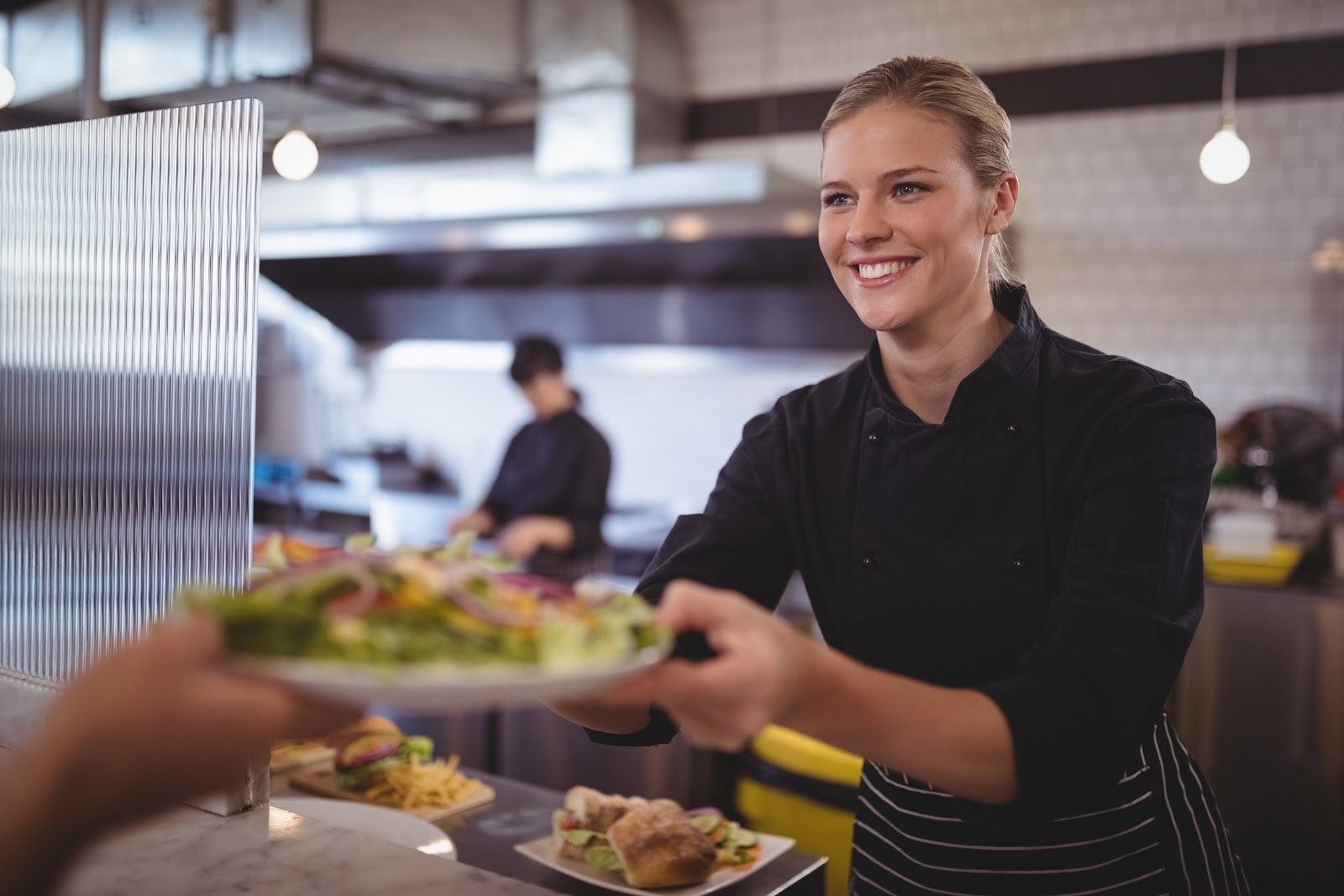
Not surprisingly, miscommunications can happen in a fast-paced restaurant, especially when dealing with the high turnover in the restaurant industry right now. Well-documented SOPs built into online employee manuals and available for easy access provide managers with compliance checklists.
Therefore, to stay in business, owners and managers need to write SOPs for both the front and back of the house that include restaurant rules and regulations. Write SOPs to put your restaurant on firm footing to pass inspections, receive rave restaurant reviews, and win restaurant awards for quality and service.
Indeed, the fast pace of restaurant operations leaves no time to find SOPs thumbtacked on walls or in hardcopy staff manuals in back offices. In fact, we recommend that SOPs be digitized and available for staff at their fingertips, wherever and whenever they need them.
Write standard operating procedures for restaurants to include:
- Staff and personal hygiene
- Cleaning and disinfecting facility and equipment
- Food flow
- Menu production
- Communications
Keep kitchens running smoothly and efficiently with clear communication between management, staff, and vendors.
4. Hotels
Undeniably, the quality and comfort of hotel guest rooms are a hotel’s highest priority. As a result, maintenance managers should focus on the hotel areas where spot-on preventive maintenance builds customer satisfaction and positive guest experiences.
Without a doubt, hotels operate in regulated environments. Therefore, front desks and managers need to assess quality issues to proactively prevent problems and react to them quickly when they arise.
As a result, SOPs that include preventive maintenance and regulatory standards ensure quality and safety for both customers and employees. They increase customer satisfaction and re-bookings and meet industry compliance.
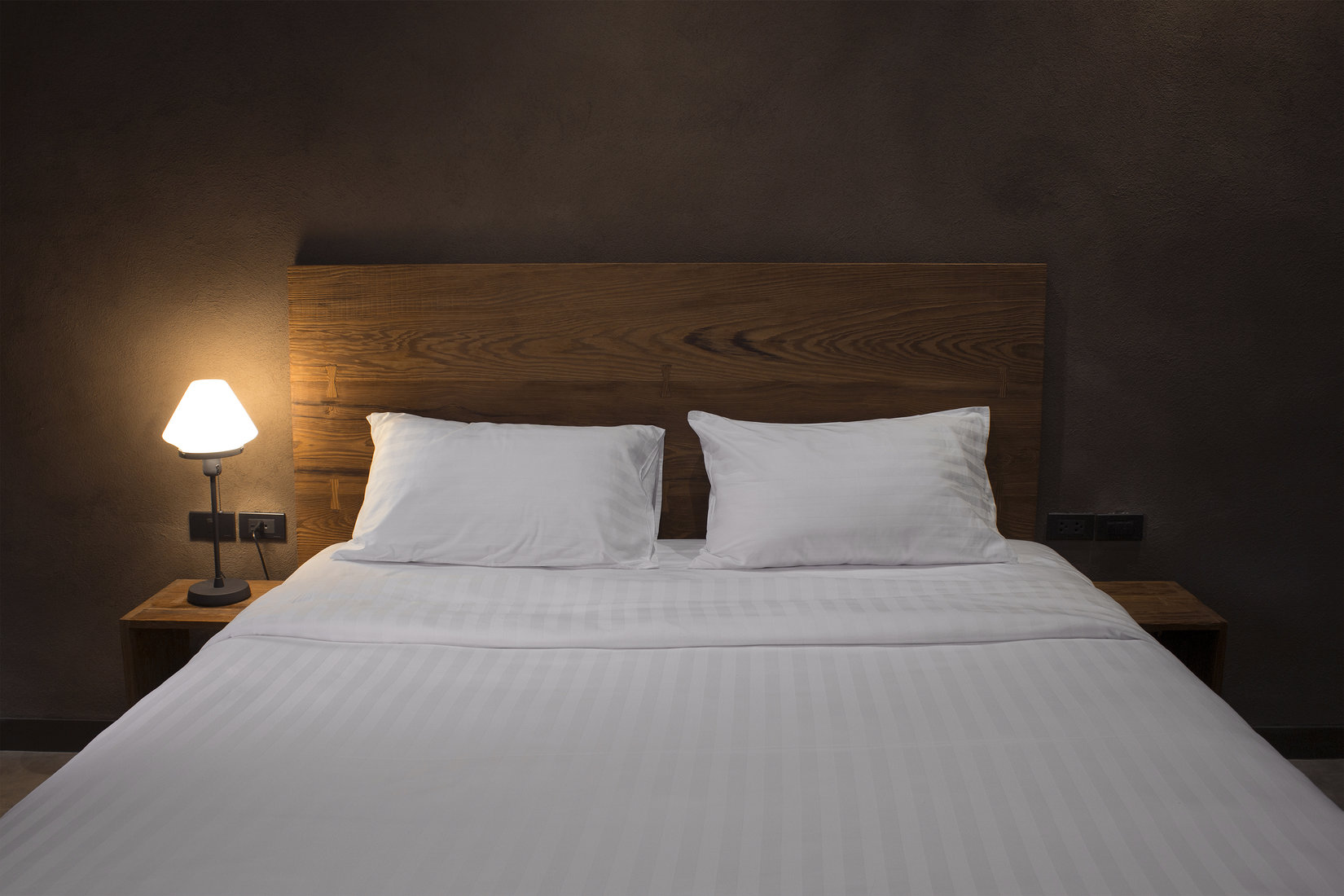
Hotel maintenance operations include:
- Heating and Cooling Systems
- Plumbing and Water Supply
- Electrical
- Lighting
- Guest Safety
- Sanitation Services and Replenishment
- Furniture
- Facility Exterior
- Equipment and Supplies
- Meeting Spaces
Interestingly, the Occupational Health and Safety Administration (OSHA) has no specific rules governing the hospitality industry. However, hotels need to comply with OSHA’s General Duty Clause that enforces worker safety.
Hotel standard operating procedures with regulatory compliance checklists should include:
- Emergency Evacuations and Lock-Down Procedures
- Housekeeping and Cleaning Operations
- Laundry Operations and Facilities
- Food and Beverage Services and Kitchen Operations
- Guest Room and Floor Safety
Subsequently, these operations are regulated at federal, state, and local levels. Furthermore, industry-specific organizations, such as those for electricians and plumbing, heating, and cooling contractors, also provide their own standards and required training and certifications. Fire safety is a major concern in the hotel industry. Employees who know and understand hospitality laws keep more accurate records online and on the spot.
5. Education
A well-designed education facility management system built with SOPs includes facility maintenance, reactive maintenance, routine maintenance, preventive maintenance, and predictive maintenance.
Subsequently, school facility maintenance plans need to focus on campus day-to-day operations and on long-range school management priorities.
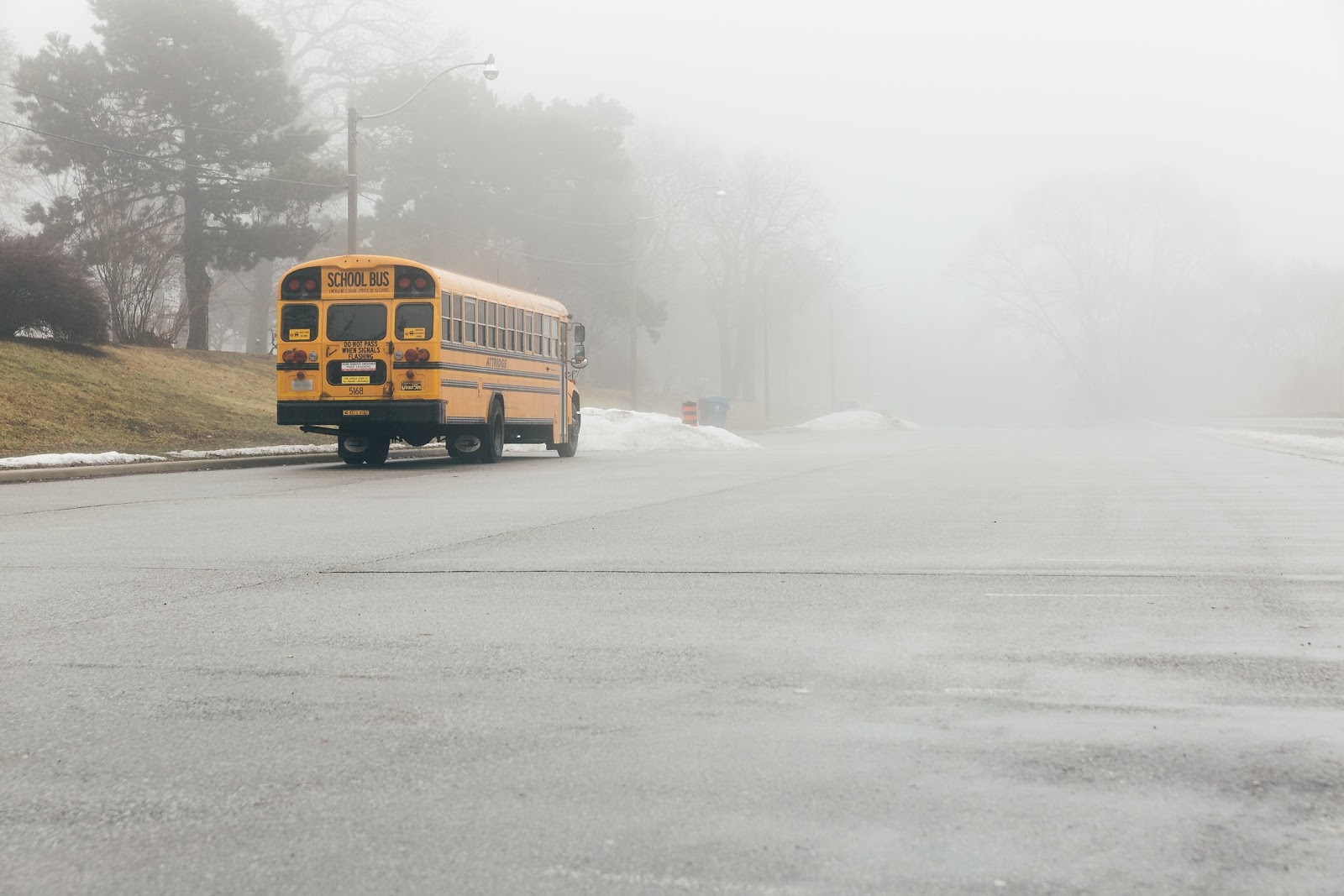
Because there are always routine and unexpected maintenance and repair demands, education organizations should proactively develop and implement plans.
Once online, completed SOP can be used to create forms and checklists for locations, assets, inspections, and routine safety checks. Time-stamped facility maintenance standard operating procedures create easy audit trails.
To be clear, building maintenance includes school buildings and athletic facilities, tool sheds, garages, and other remote sites. Grounds maintenance includes unpaved surfaces, like the athletic fields, and paved surfaces, like the parking lots. Also, It includes walkways, sidewalks, and driveways. In addition, grounds maintenance includes landscape, water flow, energy use, and even personal safety. In the winter, campus SOPs cover snow plowing for safety and access.
Equipment maintenance includes all vehicle fleets, from lawnmowers to school buses to golf carts. The National Center for Education Statistics (NCES) publishes the Planning Guide for Maintaining School Facilities.
School facility’s standard operating procedures should include:
- Fleet management, including school buses
- Building and grounds
- HVAC systems
- Indoor air quality
- Water systems, including safe drinking water
- Foodservice
- Safety and emergency preparedness
- Fire safety
- Recycling
- Sanitation
- Hazardous materials, including asbestos and lead paint
Facility maintenance teams need to adhere to rigorous education SOPs set by districts, county, and state authorities.
Campus standard operating procedures should:
- Document processes that are easily followed, accessible, and not “one size fits all” solutions
- Promote best practices and quality assurance guidelines
- Facilitate audits of daily, monthly, and preventive maintenance schedules
- Provide safe environments for teaching and learning
- Manage facility staff and contractors
- Evaluate facility maintenance efforts, implementation, compliance, and completion
MaintainX: Streamlining Standard Operating Procedures across Industries
To conclude, standard operating procedures across industries enhance safety, implement quality control, and streamline O&M tasks. If you would like to simplify SOP implementation in your organization, we invite you to download MaintainX—the world’s first industrial task-management app with chat.
FAQs
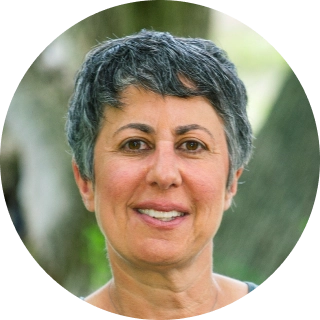
Caroline Eisner is a writer and editor with experience across the profit and nonprofit sectors, government, education, and financial organizations. She has held leadership positions in K16 institutions and has led large-scale digital projects, interactive websites, and a business writing consultancy.