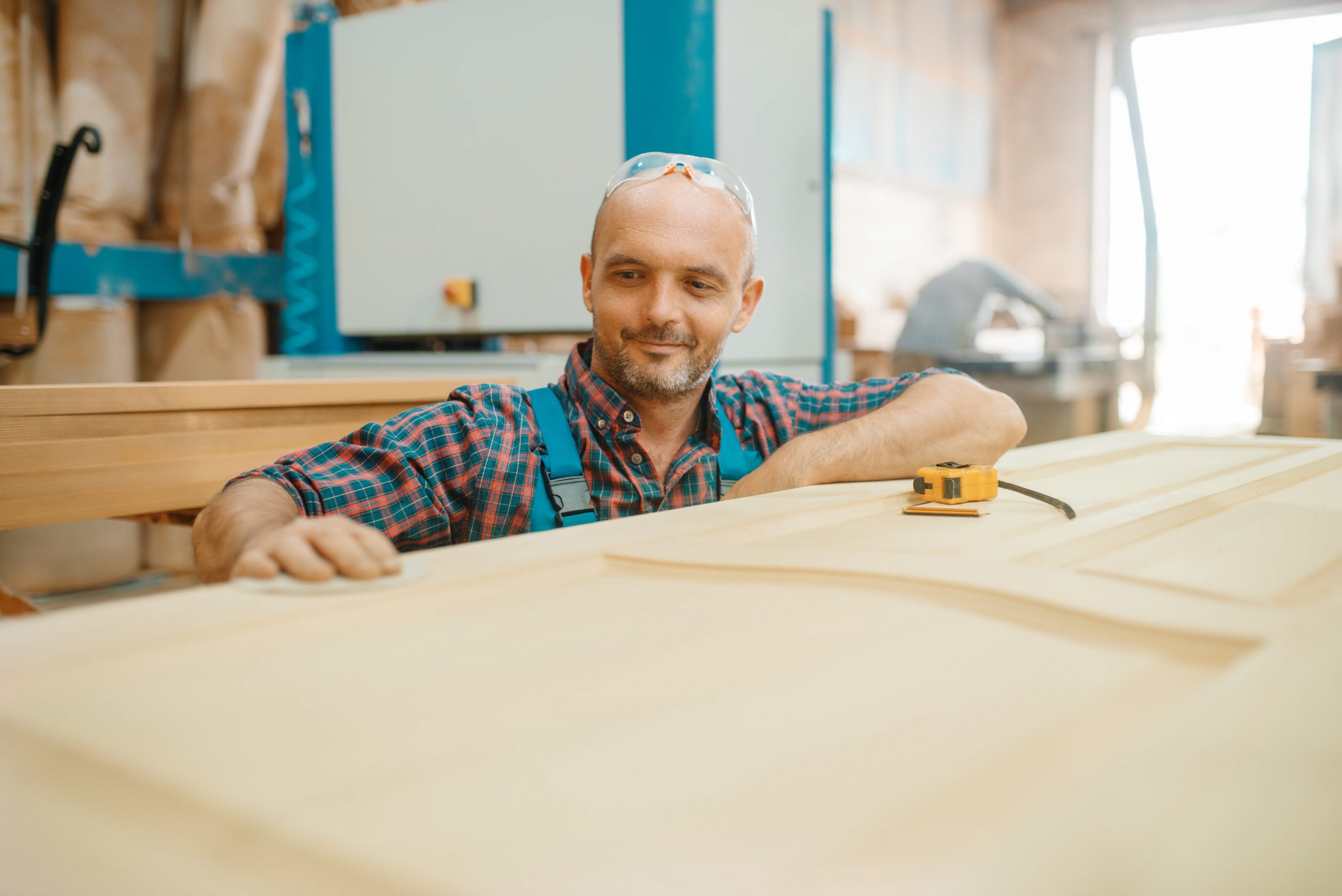
Manufacturing approaches are as many as the field of manufacturing itself is wide. Discrete manufacturing refers to the production of distinct items that can easily be counted or seen. Most items you find in stores fall into the category of distinct products.
Manufacturing companies will often adopt different methods based on their manufacturing industry, the nature of their specific business, and their unique goals. In addition, if companies are looking to reduce waste and improve productivity, they’ll likely integrate lean principles into their manufacturing operations. In other words, there is no one-size-fits-all approach to maintenance. We know that preventive maintenance to reduce unplanned downtime is always a wise approach.
That said, maintenance teams often vary their maintenance workflows based on the company’s manufacturing process. One such manufacturing process requiring a specific maintenance approach is maintenance is Discrete Manufacturing.
“Discrete manufacturing is among the top-three industries expected to invest most heavily in AI, primarily in quality management and automated preventive maintenance use cases.”
Deloitte
What is Discrete Manufacturing?
In general discrete manufacturing products can be differentiated from end products of process manufacturing like pharmaceuticals, paper, and gas, which are all undifferentiated.
Here’s another way to look at it. Individual discrete items often consist of different parts and systems. In addition to unit items, we assemble them with nuts, bolts, brackets, and similar items and systems. We can also recycle these finished products back to their original components at the end of their lifecycle. For example, toy planes, actual aircraft, furniture, and automobiles are all examples of discrete manufacturing.
Products of process manufacturing, on the other hand, are the result of a continuous production process. This continuous process usually involves refining raw material into the final product. As a result, we cannot break down these processed items into individual parts the way we can discrete items.
“. . . the discrete manufacturing industry is on the cusp of a new era that certainly favors best-run midsize players. The opportunities are vast in variety and remarkable in revenue potential. More importantly, growing brands can innovate a product and service mix that delivers valued experiences that sustain customer relationships for years to come.”
Forbes
Maintenance in Discrete Manufacturing
Discrete manufacturing depends on customer orders. This manufacturing process applies to a make-to-order (as opposed to a make-to-stock) approach. As a result, individual unit production often requires a bill of materials (an inventory of necessary raw materials) and an assembly line approach. The aerospace and automotive industries rely on discrete manufacturing processes.
Discrete manufacturing generally reduces waste, a fundamental lean principle. That said, it also has significant challenges, particularly on the maintenance side. Let’s consider these now.
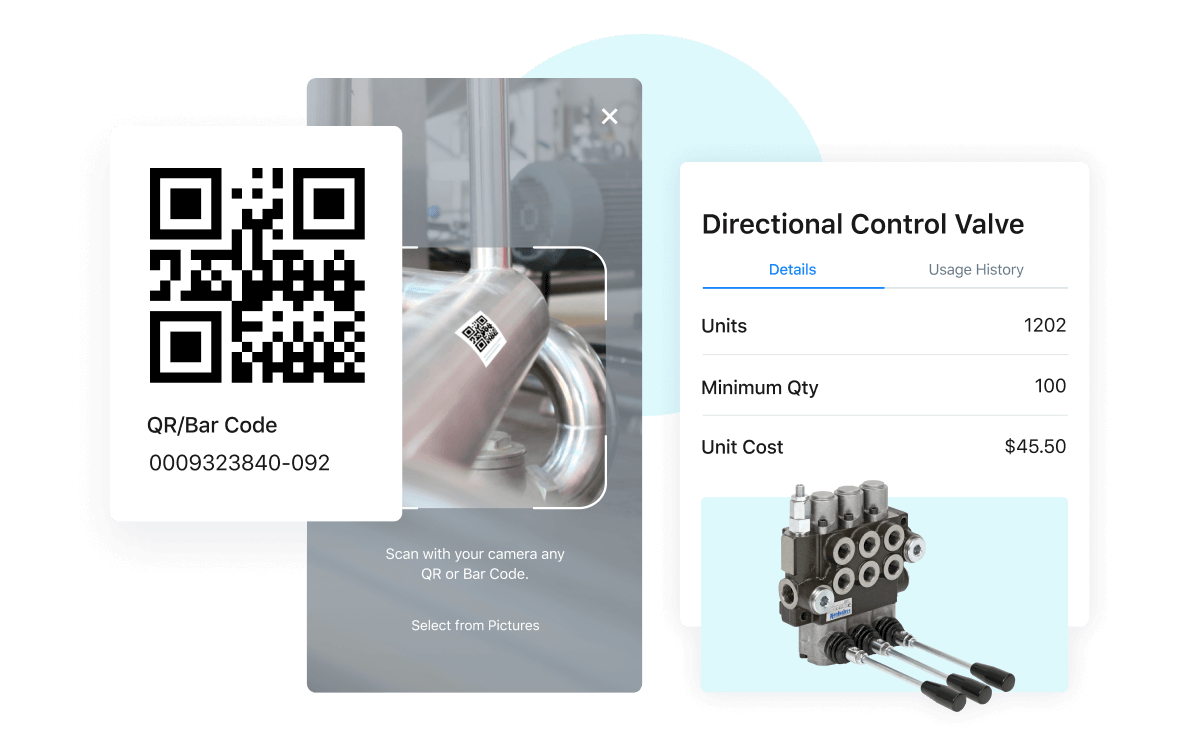
Inventory Management
As stated, discrete manufacturing operations follow a bill of materials (BOM). The BOM is unique to each product, resulting in maintaining large inventories for factories that manufacture multiple products. This becomes even more challenging depending on the specific production style.
We can organize discrete manufacturing into high-volume productions with low complexity and low-volume productions of high complexity. High-volume productions can result in more challenging inventory management. Poor inventory management, by extension, can complicate both manufacturing and maintenance processes. The last thing you want is prolonged downtime because technicians are stuck on the shop floor because the necessary spare parts for assets are not available.
Production Capacity
Maintenance planning in discrete plants is challenging because production planning is difficult. And production planning is difficult because the production capacity of discrete factories is often hard to calculate. When different products are made in different amounts based on customer orders, there is no standard daily or monthly production count. This makes it difficult for you to estimate the assets that production requires and, by extension, what maintenance activities you need to assign.
Process Standardization
Because the products made in a discrete factory can be so different, the assembly line and routing processes also can be quite different. Different assets and parts of the plant require different maintenance activities at different times. Obviously, a challenge when writing standard operating procedures for your teams.
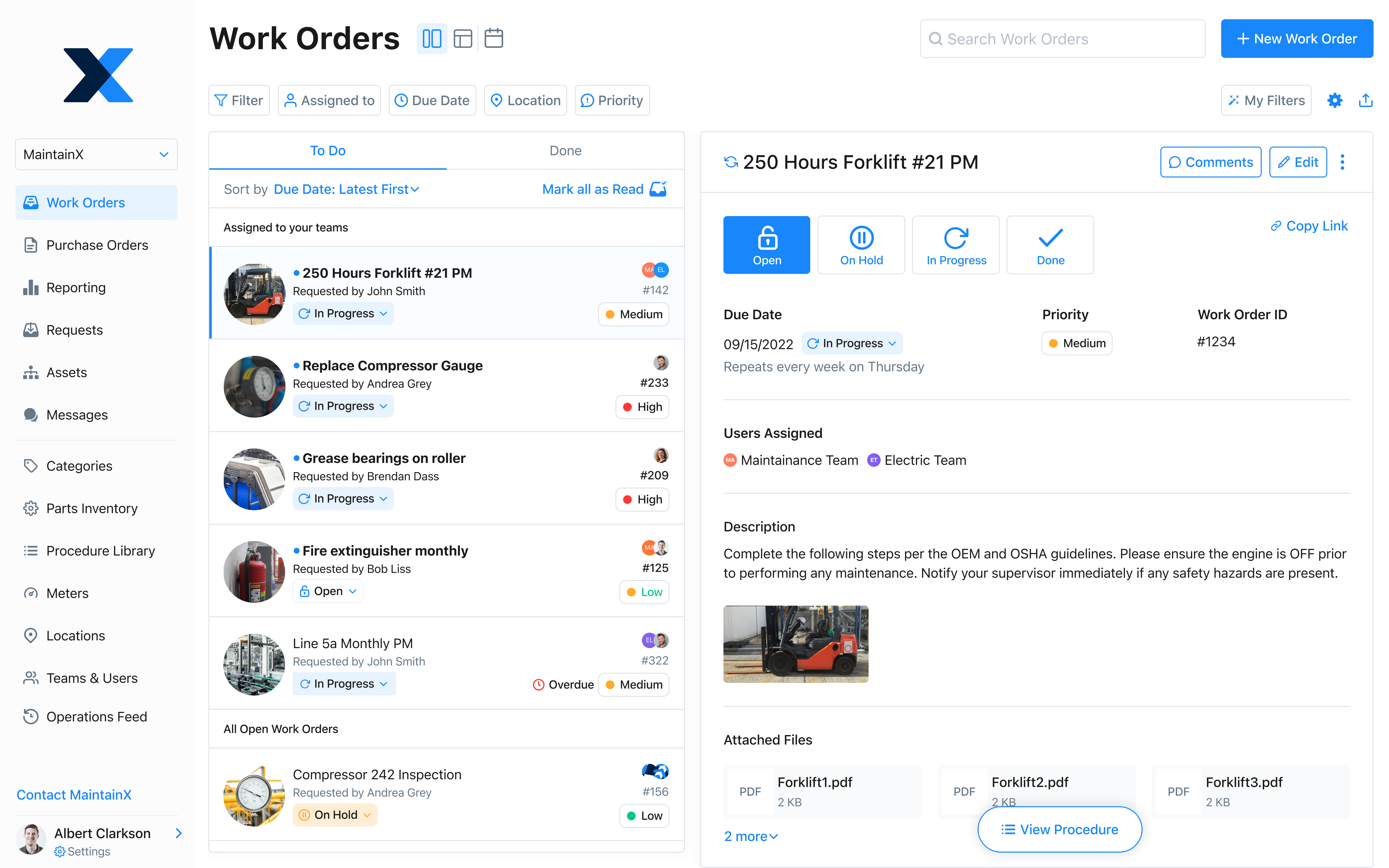
CMMS in Discrete Manufacturing Maintenance
If you’re looking to overcome these challenges, we recommend integrating a Computerized Maintenance Management System (CMMS) into your processes. A robust CMMS for manufacturing will help you streamline your maintenance operations and oversee everything from work orders to quality management directly from both your mobile device and desktop. MaintainX, for example, integrated with a discrete manufacturing workflow typically includes these functions: inventory and management, supply chain management, and KPI reporting.
But let’s look at the additional benefits of implementing a CMMS to help with your discrete manufacturing.
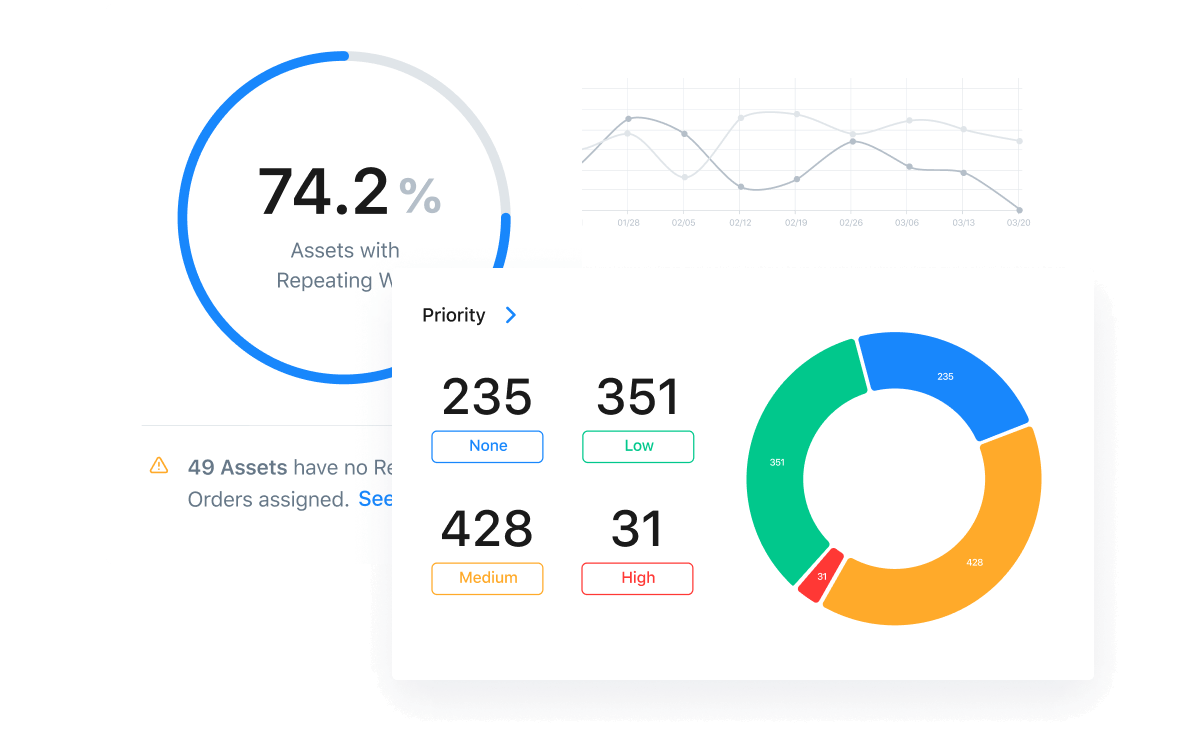
Gather Data
While managing maintenance in a discrete plant will always be a balancing act, a CMMS that collects and stores your data in the cloud can go a long way. On a day-to-day basis, you may find it difficult to capture trends or patterns in customer orders. However, a CMMS with robust reporting features can provide you with key performance indicators and other insights. You will see in real time the assets your teams most use and be able to plan maintenance more accurately going forward. Likewise, MaintainX offers a range of integrations with CRMs (customer relationship management software) as well as with other industry-specific software solutions.
For example, MaintainX can connect your assets to service providers as well as vendors to your parts inventory.
Execute Predictive Maintenance
In discrete manufacturing companies, regular preventive maintenance might not be the most efficient way to go. If orders are irregular, asset use will also be irregular. In turn, this will determine your maintenance activities. Knowing this, predictive maintenance is often a good bet. Condition-based maintenance based on the actual state of assets results in less wasted effort and resources.
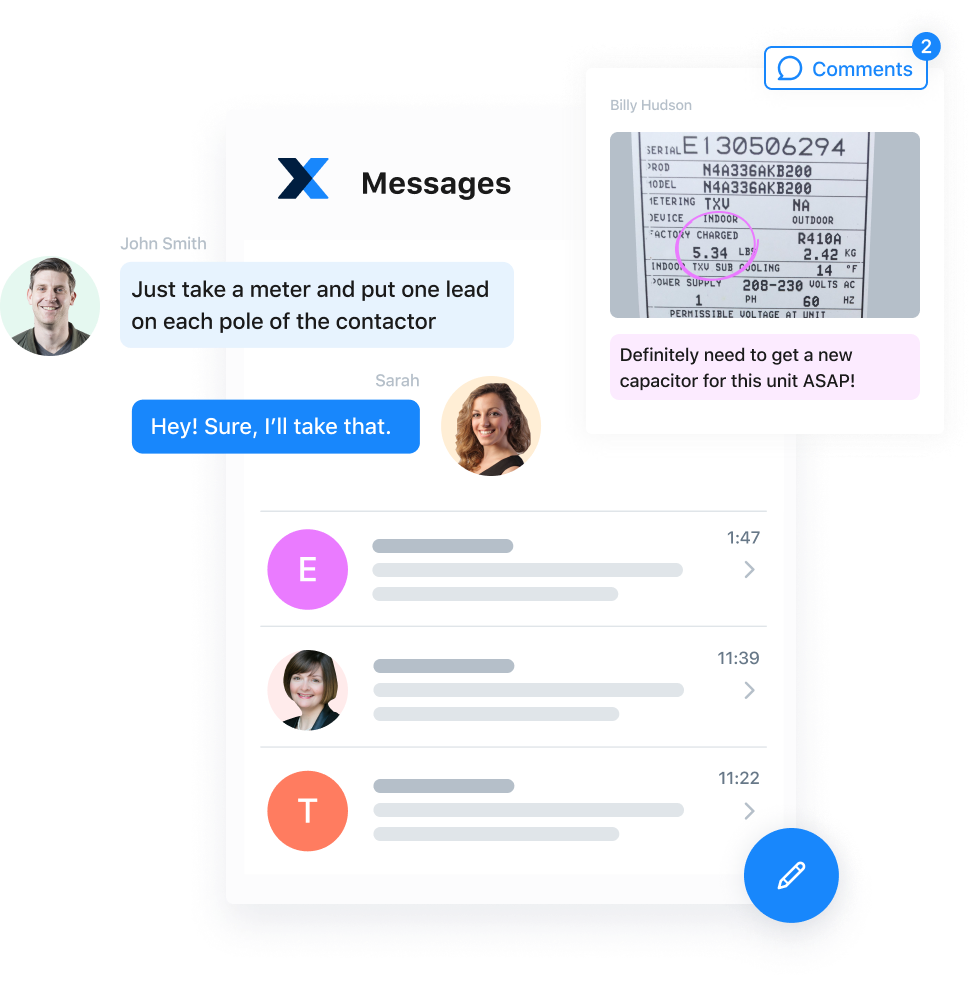
Connect Your Workers
There are many benefits to connecting your manufacturing and maintenance processes to a CMMS. Apart from work order automation and the ability to see real-time updates from the shop floor, you can set notifications regarding procurement, low inventory levels, equipment useful life, and unplanned downtime (among other KPIs).
Use MaintainX to Automate Your Discrete Manufacturing
MaintainX, for example, offers powerful ERP software integration, pulling real-time data from the production line directly into your accounting ERP sys and PO systems. In addition to a range of integrations, MaintainX will help you standardize procedures, increase cross-team collaborations, manage safety and regulatory compliance, and oversee inventory and supply chain management.
If you find yourself asking what is CMMS in manufacturing, we invite you to give MaintainX a try.
FAQs
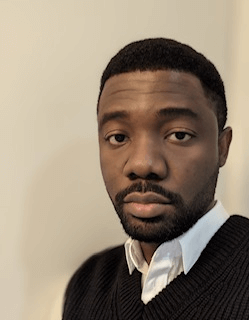
Lekan Olanrewaju is a content writer with years of experience in media and content creation. He has held positions at various media organizations, working with and leading teams at print magazines, digital publications, and television productions.