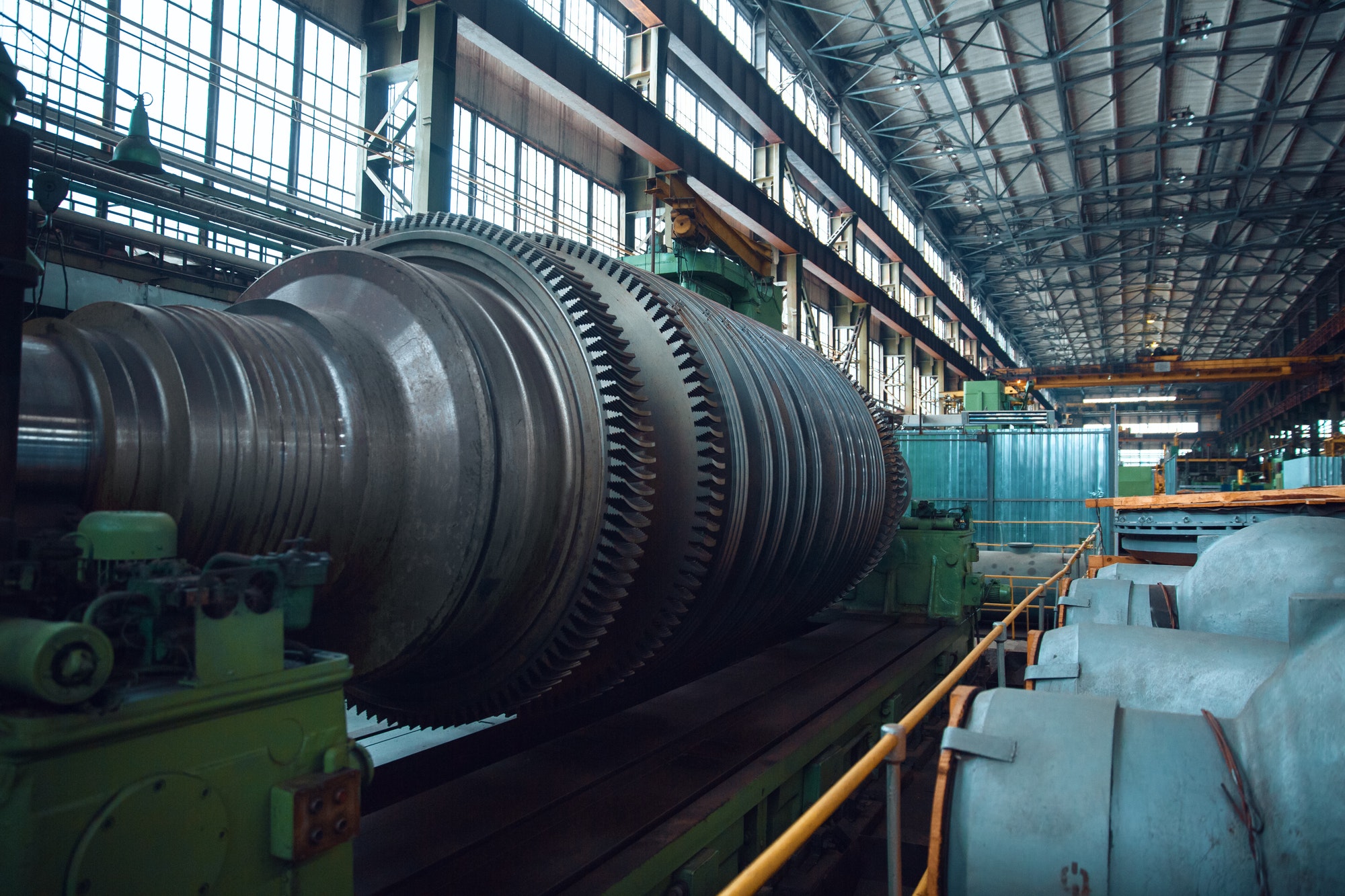
Have you ever wondered what happens in a manufacturing plant? In this post, we pull back the curtain on plant operations. We’ll cover the duties of plant operators, best practices of plant maintenance, and some surprising facts about the manufacturing industry. After reading, you’ll have a greater appreciation for that beloved smartphone, tablet, or car you depend on every day.
Most of us are clueless about what goes into producing the items we use daily.
We know the basics—heavy machinery, assembly lines, OSHA safety standards—but without accessibility, everything else may seem a bit mysterious. Yet plant operations are the backbone of organizations that produce some of our favorite goods and services.
Ensuring that complex equipment, systems, and facilities run smoothly isn’t easy. One mechanical disruption can result in hundreds of thousands of dollars in revenue loss!
The Beginner’s Guide to Plant Operations
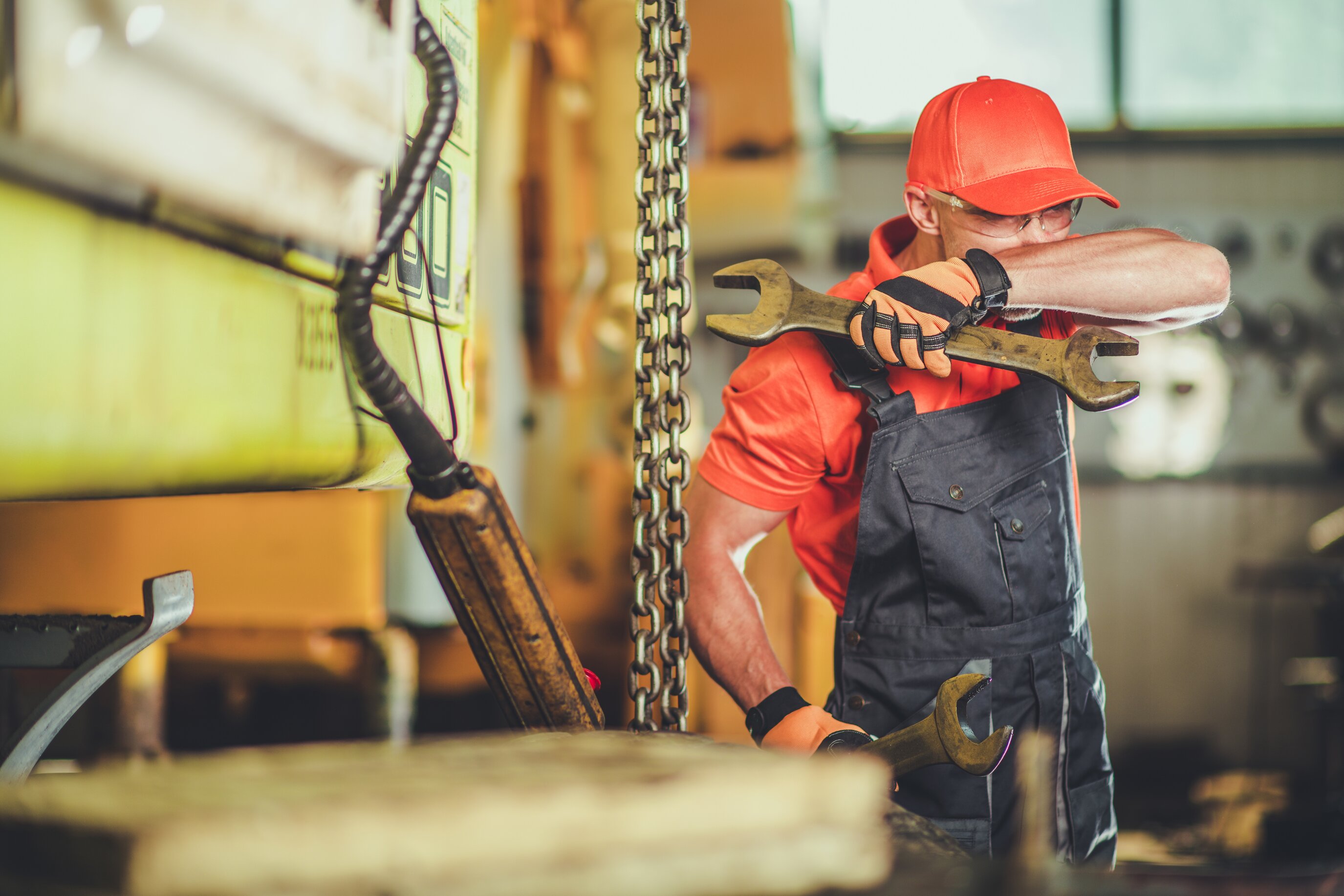
At MaintainX, we’ve been fortunate to have conversations with many experienced plant operators and managers. Most of the time, we walk away with feelings of surprise, intrigue, and admiration for what it takes to keep extensive facilities running!
No matter the materials handled, plant supervisors have an immense responsibility to ensure businesses stay profitable and workers remain safe.
In recent years, the manufacturing sector has evolved to incorporate workflow automation and sensor-based technologies that have opened up new strategies for streamlining routine processes (more on that in a moment).
Whether you’re considering a career in manufacturing or are simply wanting to gain a deeper understanding of an unfamiliar industry, keep reading to learn little-known facts about plant operations.
5 Surprising Facts about Plant Operations
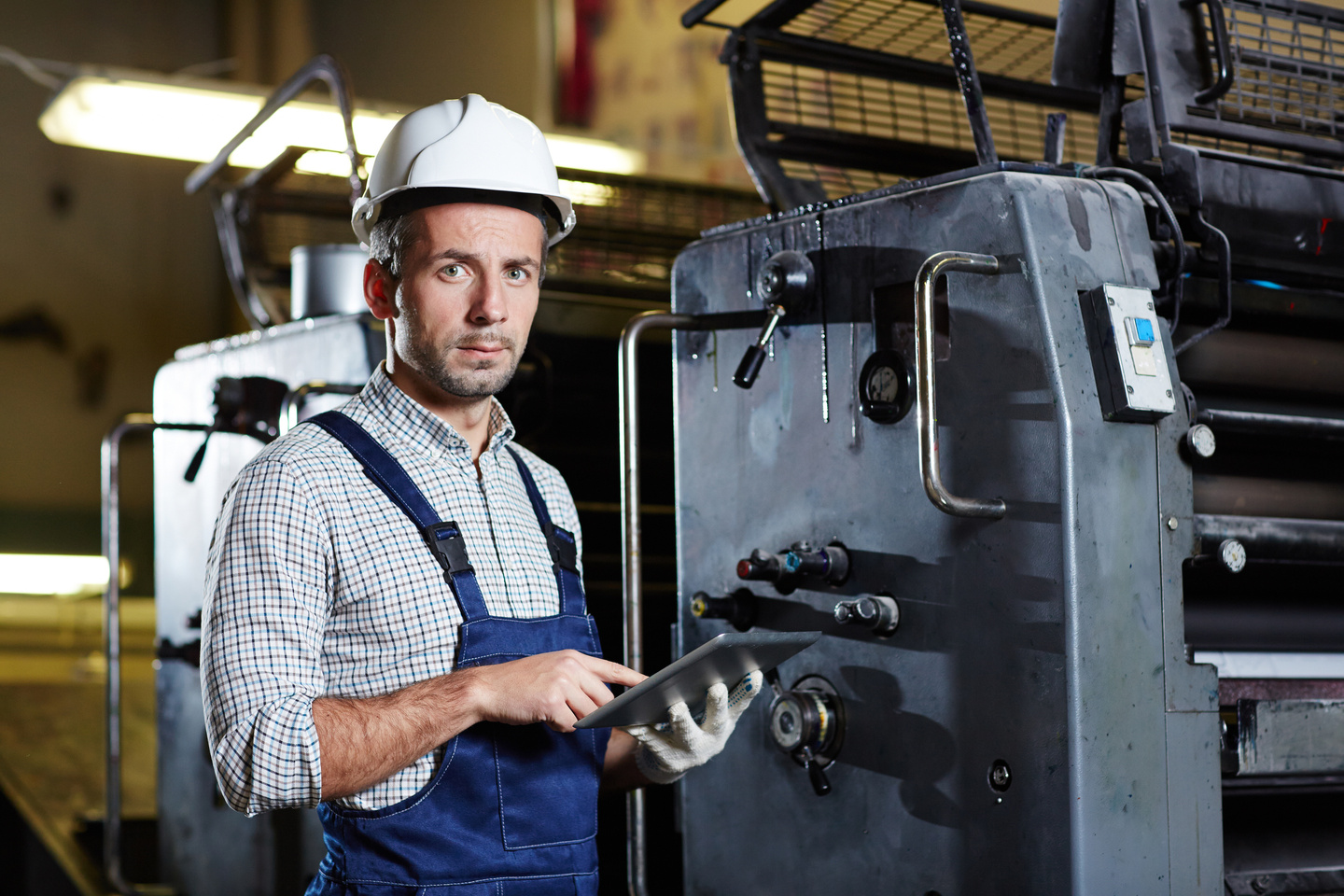
1. Manufacturing is a lucrative industry
Misperception surrounds the manufacturing industry. Only 49 percent of American parents would encourage their children to pursue a career in manufacturing, according to Kronos’s 2018 Manufacturing Day Survey. Why?
Many folks incorrectly associate plant operations with exceptionally long hours, unfavorable working conditions, and undesirable pay. Yet, research shows that manufacturing workers earn 13 percent more on average than their comparable colleagues in other sectors!
According to the U.S. Bureau of Labor Statistics, power plant operators, distributors, and dispatchers earned a median salary of $94,790 in May 2021. Though there is talk of manufacturing wages declining in recent years, the Economic Policy Institute says that:
“Manufacturing workers have an advantage in benefits, primarily in insurance and retirement benefits, and this advantage grew between 1986 and 2017.”
U.S. Bureau of Labor Statistics
These benefits seem to offset any pay erosion. Thus, it should come as no surprise that the manufacturing sector contributes 10.8 percent of the U.S. economy’s Gross Domestic Product (GDP). Only government, professional services, financial, and real estate sectors pull more. The manufacturing sector employs more than 12 million individuals, which is 8.5 percent of the non-farm workforce. Experts predict the job outlook for manufacturers will continue to grow.
2. A British citizen built the first American factory in 1790.
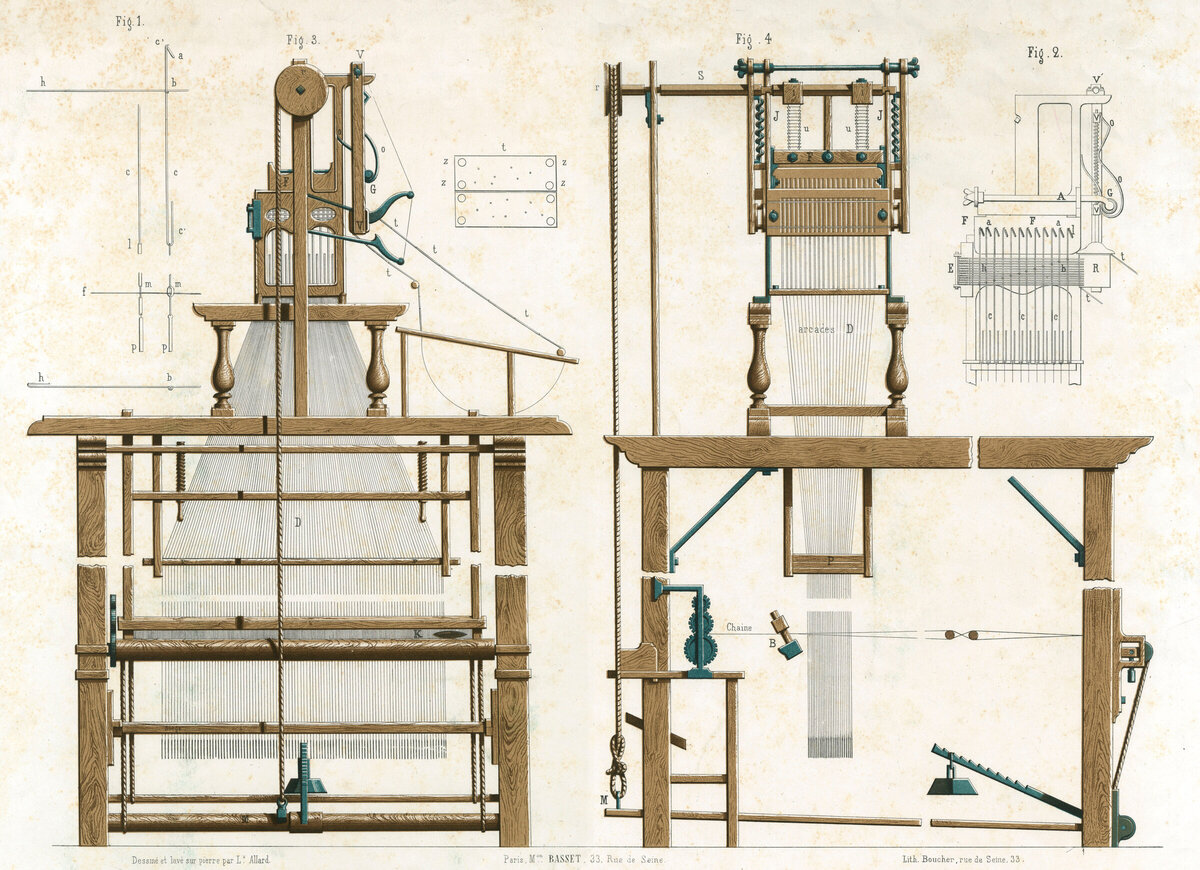
We’ve come a long way since the late 1700s—that’s when Samuel Slater paved the way for U.S. manufacturing by opening the country’s first facility.
The British mogul built a yarn factory run with foot petals, spindles, and water. His adaptation of English textile technology for American usage earned him the nickname “Slater the Traitor” back home. But in the states, he is very much considered the “father of the American industrial revolution.” The original yarn factory still stands today.
3. Industry 4.0 is changing everything.
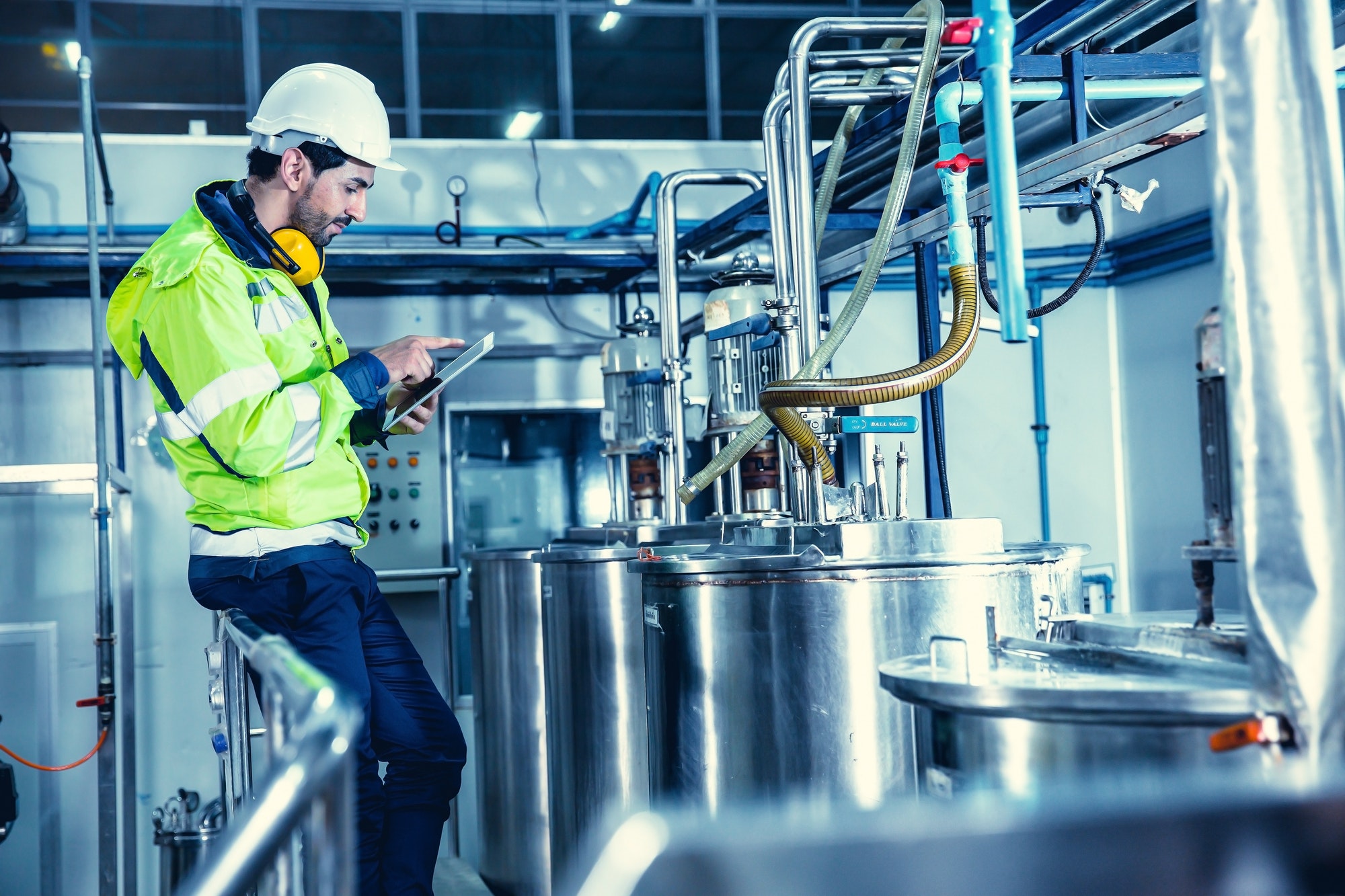
Fast forward 230 years and an increasing number of facilities are now integrating Industrial Internet of Things (IIoT) technologies into their O&M processes. The foundation of IIoT-driven operational programs is computerized maintenance management systems (CMMS) that collect, catalog, and analyze data from sensor-based technologies.
The result? Plant operators can predict equipment failures with unparalleled accuracy. The U.S. Department of Energy reported that predictive maintenance programs could increase ROI by up to ten times and reduce asset breakdowns by a whopping 75 percent.
4. It took world leaders a while to get organized.
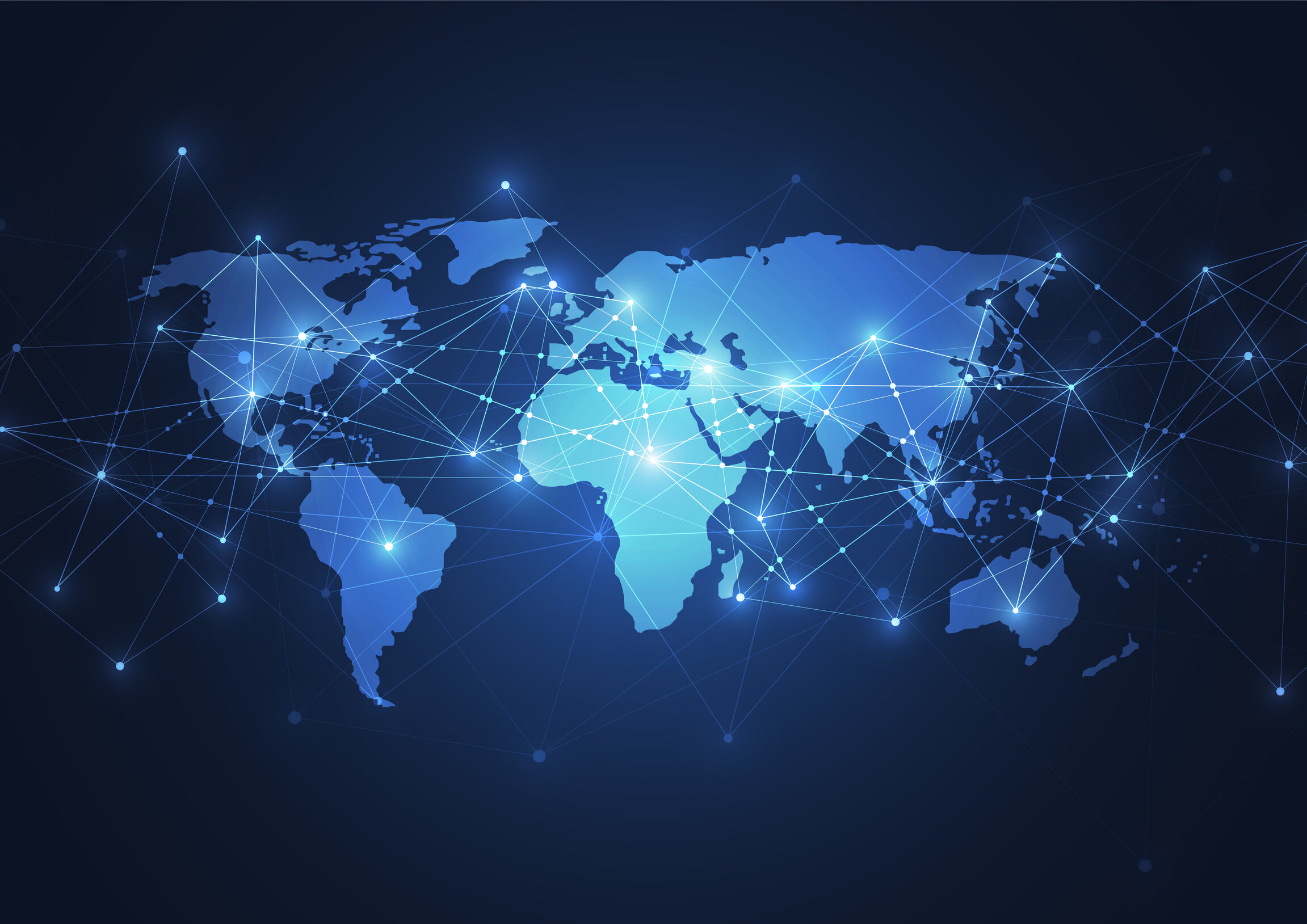
Despite the longevity of the industry, global leaders took their time establishing worldwide manufacturing standards. They didn’t find the International Organization for Standardization (ISO) until 1947. The United States is represented in the ISO through the American National Standards Institute (ANSI), established in 1918 to represent the United States in the ISO.
Another fun fact about the ISO: the acronym doesn’t stand for what you think it does. Most people assume the initials stand for the organization’s name, but it represents something you would probably never guess: the Greek word isos for “equal.” The neutral initials serve to eliminate confusion that can result from translating the name into different languages.
In addition, industry leaders didn’t develop overall equipment effectiveness (OEE) standards until the 1960s! OEE measures the productivity of plants, equipment, and processes.
5. The government didn’t prioritize worker safety until 1970.

Today, every American worker has the right to safe work conditions. This is largely because the government introduced the Occupational Safety and Health Act in 1970, and the subsequent creation of the Occupational Safety and Health Administration (OSHA).
So, how were American workers protected before OSHA? According to a speech by Dr. David Michaels, they weren’t. Michaels said many companies failed to conduct investigations after worker fatalities, injuries, and accidents.
If you felt unsafe at work, your only option was to look for another job! With that said, some states maintained better worker protection laws than others.
Today, plant operators must follow strict regulatory requirements to minimize risks and keep employees comfortable, healthy, and safe. This brings us to our next section.
What Are the Duties of a Plant Operator?
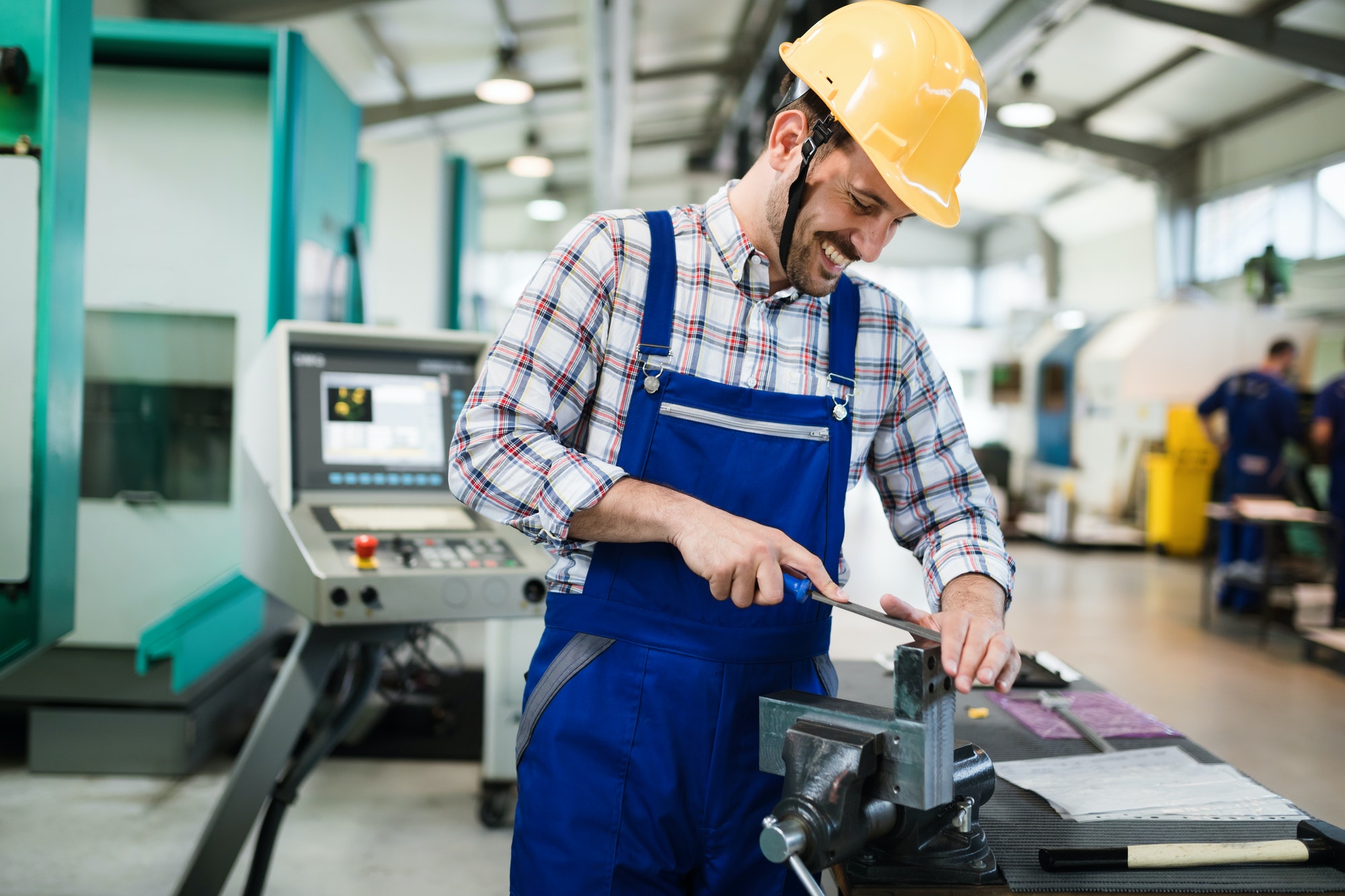
Does the term “plant operator” invoke the image of someone walking around an industrial facility, clipboard in hand, hardhat on head?
Does the backdrop include concrete floors, heavy machinery, and pipes? If so, you’ve got the right idea! However, there is more to running a manufacturing facility than handling heavy equipment.
Plant operators have many responsibilities. They often need to:
- Negotiate purchase order requisitions and collaborate with third-party contractors.
- Perform root cause analyses to solve complex production problems efficiently.
- Foster communication between company management and plant workers.
- Maintain records of historical asset data to inform maintenance strategies.
- Document, distribute, and oversee safety standard operating procedures.
- Create, assign, and monitor work orders for maintenance technicians.
- Perform preventive maintenance on critical equipment.
- Train new employees on standard operating procedures.
- Minimize production waste to improve profitability.
- Troubleshoot emergency issues quickly and safely.
- Oversee the installation of new equipment.
To perform this full-time role effectively, a plant operator should have basic engineering knowledge, adaptable machine operating skills, and excellent communication skills. Most plants require workers to have a high school diploma (or equivalent), specialized training, and 3+ years of experience in a managerial role.
In addition, they should be able to stay calm under pressure. Put simply, one never knows what sort of equipment malfunctions can arise. For this reason, some organizations require applicants to take special aptitude tests via the Edison Electrical Institute to determine suitability. The exams assess the understanding of mechanical concepts, mathematical ability, and spatial ability, in addition to reading comprehension.
Generally, years of onsite training and experience are necessary for a worker to become fully qualified to serve as a director of plant operations. Unsurprisingly, most plant operations workers start their careers in entry-level roles in plant operations departments before working their way up.
What Is Plant Operations Maintenance?
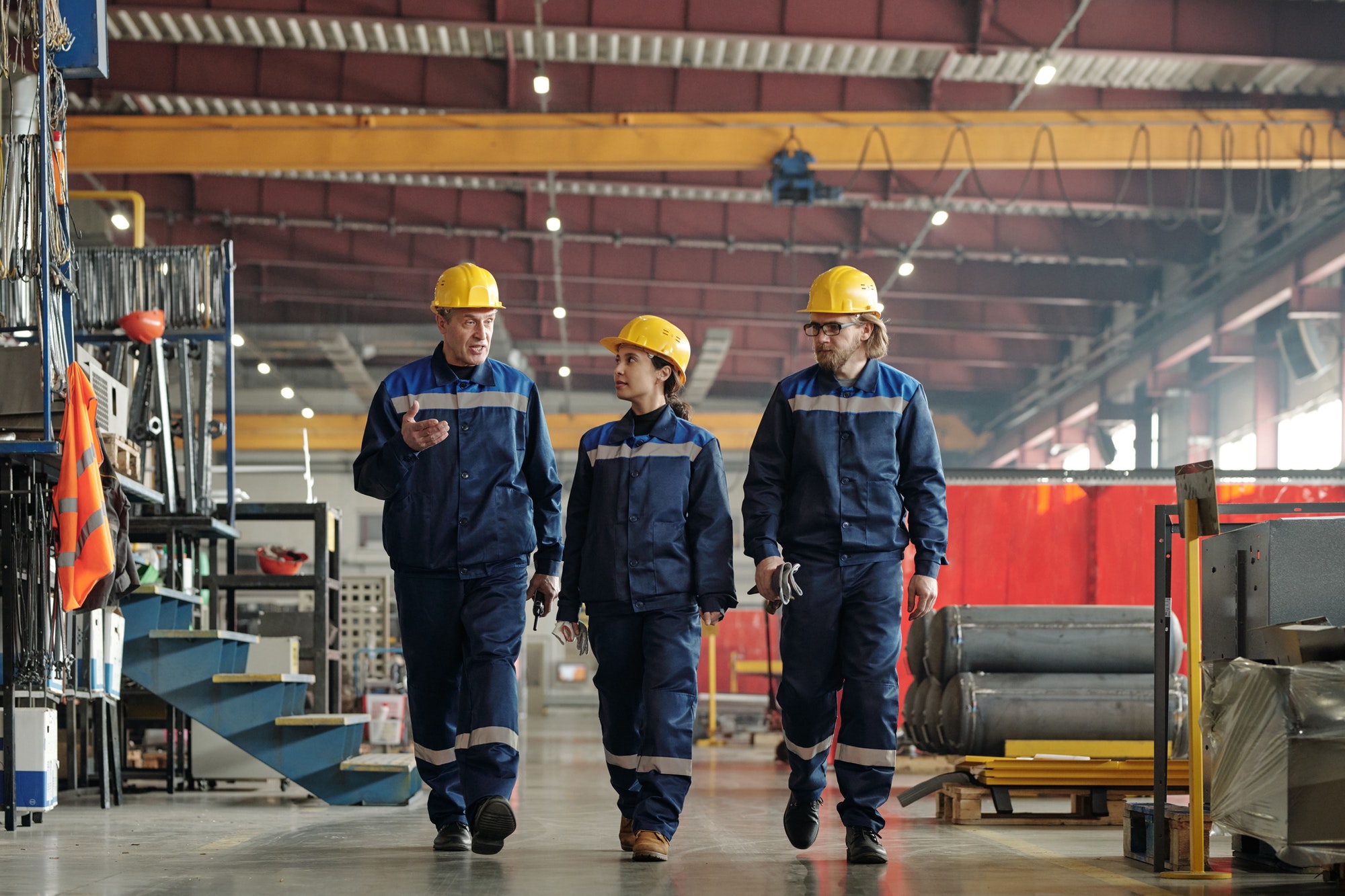
While unplanned breakdowns are inevitable, plant operators must do everything they can to minimize equipment failure. And that means conducting plant operations maintenance!
Plant operations maintenance refers to maintenance activities intended to keep facilities in good working order. Power plants, chemical plants, and manufacturing operations must work to ensure all systems work as intended.
This requires performing criticality analyses to establish equipment maintenance hierarchies of importance, running Failure Mode and Effects Analysis (FMEA) to mitigate unnecessary breakdowns, and reviewing historical maintenance data to fine-tune PM strategies.
Translation: it requires going beyond an “if it ain’t broke, don’t fix it” mentality. Benefits of plant operations maintenance include:
- Minimal unplanned downtime
- Increased asset uptime and availability
- Lower operational and production costs
- Streamlined operations management
- Improved employee engagement and morale
The proactive maintenance of plant equipment and systems is the cornerstone of plant maintenance. It improves both worker productivity and production capacity.
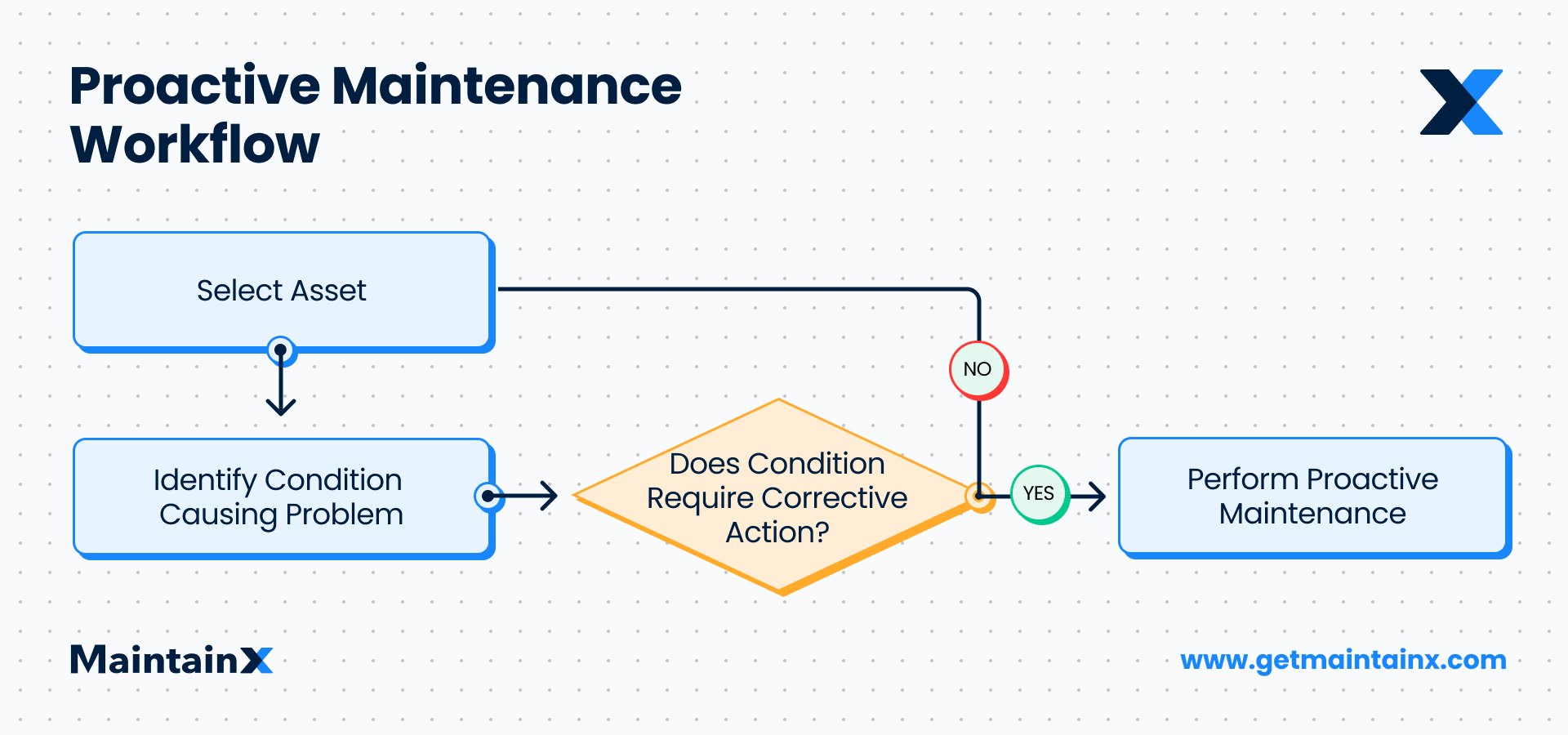
Difference between Production Plants and Manufacturing Plants
Finally, you may be wondering: what’s the difference between production plants and manufacturing plants? People often use these two terms interchangeably.
While both involve creating finished products, they focus on different processes. Distinct differences between production plants and manufacturing plants include:
- Types of Input: Manufacturing facilities outsource raw materials before processing them into final products. Alternatively, a production facility owns its raw materials.
- Nature of Products: Manufacturing facilities only produce tangible products (e.g., canned green beans, televisions, dishwashers). On the other hand, production facilities can produce both tangible and intangible products (e.g., wholesale, insurance, hospitality).
- Resources Needed: Manufacturing facilities require a labor force, machines, and materials to meet their outcomes. Comparatively, production facilities may only require labor.
- Production Scope: Manufacturing plants often have more limited scopes of production, while plants can focus on broader outcomes.
In a nutshell, every manufacturing plant is a production plant but not all production plants are manufacturing plants. Manufacturing plants lack intangible aspects of output. With that said, both types of plants require robust preventive maintenance programs to ensure smooth operations.
Simplify Plant Operations with MaintainX
The directors of plant operations we know enjoy the field’s versatility, reliability, and fast-paced nature. Case in point: MaintainX user Chris Wilcox has taken some type of educational course nearly every year of his 30-year career! He said there is always something new worth learning.
With that said, workflow automation, process improvement, and computerized maintenance management systems (CMMS) will continue to play an integral role in plant operations for years to come. If you haven’t already, we invite you to try MaintainX!
The world’s first CMMS with chat features everything you need to track inventory, oversee PM completion, analyze meter readings, and improve compliance. Find out why MaintainX is the top-rated work order software in the Apple App and Google Play stores!
FAQs
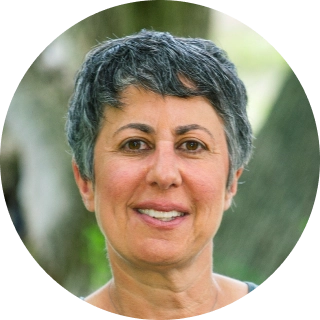
Caroline Eisner is a writer and editor with experience across the profit and nonprofit sectors, government, education, and financial organizations. She has held leadership positions in K16 institutions and has led large-scale digital projects, interactive websites, and a business writing consultancy.