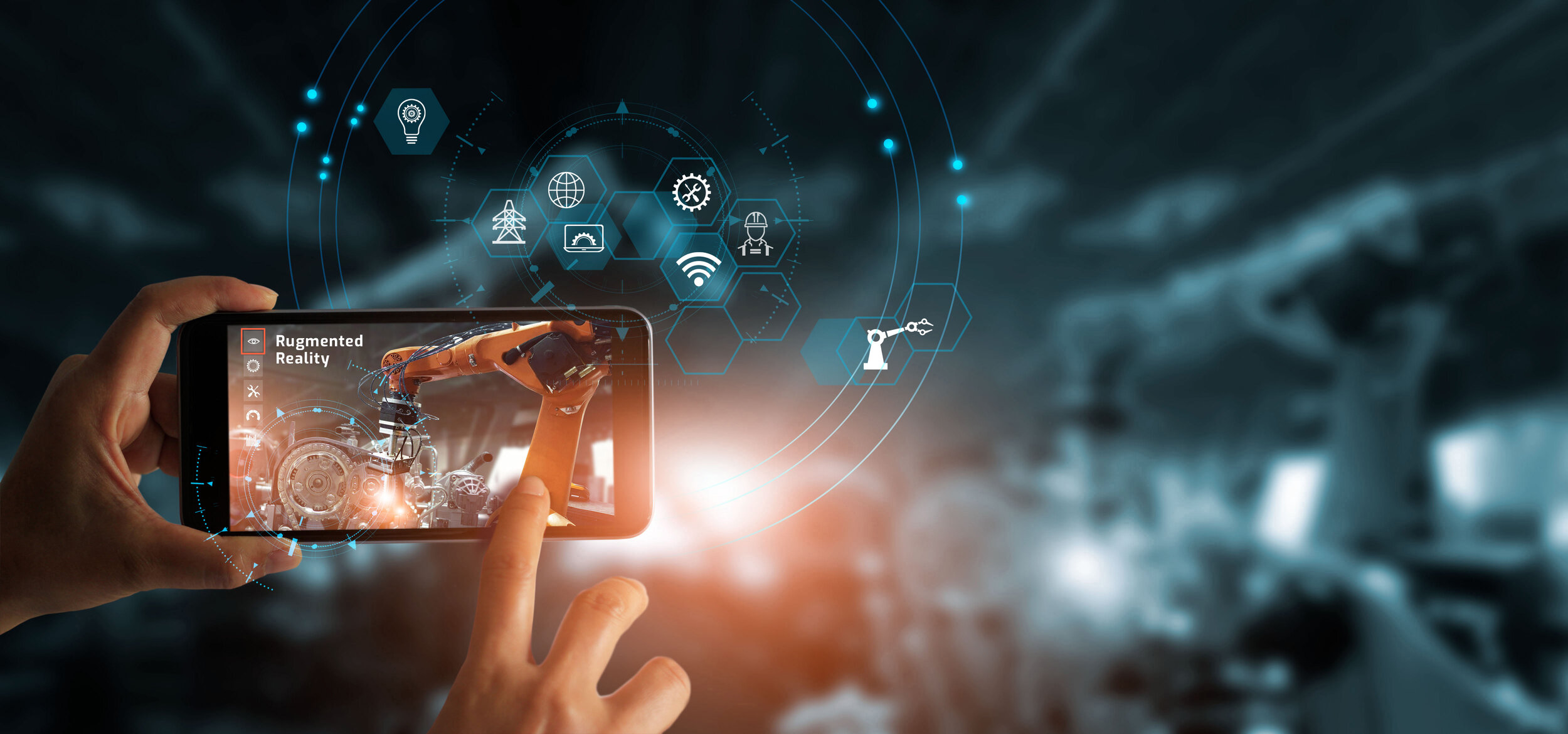
If you’ve heard of Computerized Maintenance Management Systems (CMMS) and Enterprise Asset Management (EAM) software, you might assume they perform the same role. And you wouldn’t be 100% wrong. However, there are several differences between the two.
Neither solution is universally superior. Each serves different organizational needs and contexts. The key is selecting the system that aligns with your company's operational requirements, scale, and long-term asset management strategy. Here are some factors to consider when deciding between the two:
In this article, we'll explore key considerations to help you evaluate and choose between CMMS and EAM software solutions.
Key takeaways
- CMMS and EAM have several common capabilities, but they differ in scope. CMMS is built for maintenance operations, while EAM covers the whole asset lifecycle.
- CMMS platforms are typically easier to deploy and learn, so frontline teams adopt them faster than traditional EAM software. Unless you manage complex asset portfolios across multiple locations, EAM's additional complexity may be unnecessary overhead.
- Choosing between the two comes down to your goals. Choose a CMMS for streamlined maintenance scalability. Choose an EAM for strategic asset planning across departments.
Finding the right software: EAM vs. CMMS
Enterprise Asset Management (EAM) software snapshot
What is EAM?
Enterprise asset management (EAM) software collects, houses, and analyzes data from early asset procurement to end-of-life asset disposal.
EAM apps help large organizations manage all stages of the asset lifecycle. These include buying new equipment, monitoring current asset activity and useful life, and decommissioning expired, obsolete, and unusable assets.
Who uses EAM?
Here are EAM’s use cases for various industries:
- Manufacturing: To maintain machinery and production lines efficiently
- Energy and utilities: To monitor power plants, grids, and pipelines
- Transportation and logistics: To manage fleet vehicles and infrastructure
- Healthcare: To track medical equipment and facility maintenance
- Government and municipalities: To maintain public infrastructure and buildings
How it works
Here’s a quick breakdown of how EAM works:
- EAM imports asset data: EAM imports data from other systems and databases. You need extensive data, such as purchase date, usage history, location, warranty info, and current condition. If this data is unavailable, you’ll need to start from scratch and manually enter data into your EAM.
- Each asset gets a unique ID: The EAM typically auto-assigns IDs to assets as you add them. This ID is often linked to a barcode, RFID, or IoT scanner, which feeds live data, such as temperature or pressure, to the EAM system.
- Teams monitor and maintain assets: If you have a preventive maintenance program, the EAM system tracks preventive maintenance tasks. Advanced EAM systems can also monitor data from sensors and trigger a work order when the reading breaches a defined threshold.
- Managers use dashboards and reports to visualize data: EAM systems compile data and often present it visually on dashboards and auto-generated reports. The compiled data can help managers spot trends, plan budgets, forecast failures, and make smarter asset-related decisions.
Key features
Most EAM systems offer the following features:
- Asset lifecycle management: Tracks assets across the lifecycle and monitors usage, condition, and total cost of ownership
- Maintenance management: Supports preventive and predictive maintenance, automates work orders, tracks service history, and enables mobile access for field technicians
- Inventory and parts control: Tracks inventory of spare parts, tools, and consumables to help you prevent stockouts and overstocking
- Data and integrations: Integrates with IoT devices, ERP, and financial systems and centralizes data from multiple systems and locations
- Compliance and reporting: Maintains audit trails and documentation for inspections and offers dashboards, KPIs, and reports for performance analysis
Pros of EAM
Like a robust CMMS, EAM software:
- Helps you understand the total cost of ownership of each of your assets
- Integrates with other business functions, including accounting/finance and Human Resources
- Gives you detailed and accurate lifecycle cost data to inform future procurement of physical assets
- Provides multi-site support for asset tracking across different locations
Cons of EAM
The downsides of using EAM software include the following:
- Can be costly and requires additional setup for integrations and ongoing support
- Typically requires cross-department buy-in to implement
- May be unnecessarily complex for small to mid-sized businesses
Computerized Maintenance Management System (CMMS) software snapshot
What is a CMMS?
A CMMS is a centralized digital platform focused on your company’s maintenance operations.
CMMS is less concerned with procurement and disposal, so it can do the heavy lifting for your maintenance crews and managers, who are busy operating, repairing, and fixing your assets.
As with EAM, you can integrate your CMMS software with many other SaaS and ERP systems. These integrations provide the missing link between your office-based teams that order spare parts and manufacturing and maintenance departments on the factory floor or in the field.
That said, not all CMMS platforms are equal, with some offering better functionality than others. For example, a robust CMMS like MaintainX can provide you with a real-time 360-degree view across your business. From asset uptime and downtime to planned predictive maintenance, standard operating procedures, audits and inspections, and on-the-spot inventory data, the right CMMS will help streamline the range of your manufacturing maintenance activities.
Who uses CMMS?
Technicians, maintenance teams, plant managers, and business owners all use CMMS. One of the most essential attributes of a CMMS like MaintainX is that it helps make organizational documents, systems, and apps accessible to remote team members.
A CMMS can enhance employee communication by connecting your business ecosystem, including data, computing devices, apps, enterprise solutions, and stakeholders.
Here are some examples of how various industries use a CMMS:
- Manufacturing: To keep production equipment running with preventive maintenance, minimize unplanned downtime, and avoid production delays
- Logistics and transportation: To maintain fleets, conveyors, and warehouse equipment and track maintenance by vehicle or equipment type
- Oil and gas: To maintain rigs, pipelines, compressors, and drilling equipment and perform preventive and condition-based maintenance
- Utilities and energy: To monitor infrastructure like substations, pipelines, and meters and automate inspections and regulatory maintenance
- Facilities management: To manage HVAC, lighting, elevators, and other building systems and comply with building codes and safety regulations
- Healthcare: To maintain critical equipment (MRI machines, sterilizers, etc.) and comply with health and safety standards
- Hospitality: To maintain guest-facing systems like plumbing, HVAC, and elevators and increase asset life while ensuring a safe, comfortable experience for guests
- Public sector and government: To manage municipal assets like parks, public buildings, and utilities, and track work orders and asset histories
How it works
A CMMS is easier to use than an EAM system. Here’s what the process looks like:
- Add asset information and create a maintenance schedule: You add assets to the CMMS with details like location and service history, set up preventive maintenance schedules, and the CMMS takes care of triggering your preventive maintenance work orders as they become due.
- Monitor work orders: Technicians receive a notification when the CMMS assigns them a task. While performing maintenance, the technician can access checklists, notes, and equipment information and ask questions from within the app, provided your CMMS has a built-in chat feature. You can view each work order’s status in real time and intervene when necessary.
- Track parts and inventory: The CMMS tracks parts used during repairs and deducts them from inventory. It alerts your team when stock is low. You can also set up the CMMS to automatically reorder parts when the inventory level breaches a defined threshold.
- View reports: The CMMS logs all maintenance activity. The system automatically generates various reports to help you track asset performance, team productivity, and maintenance costs.
Key features
Here’s an overview of the main features you’ll find in top CMMS platforms:
- Preventive maintenance management: Helps create, assign, prioritize, and track maintenance tasks and automate recurring maintenance schedules
- Asset and inventory management: Maintains a digital asset database with service history, tracks parts usage, manages stock levels, and automates reordering
- Mobile access: Allows technicians to receive, update, and close work orders on mobile devices and upload photos, scan tags, and communicate in real time
- Reporting: Generates reports on maintenance KPIs, downtime, and costs and produces audit-ready documentation for regulatory compliance
- IoT and sensor integration: Connects equipment sensors for real-time condition monitoring and automates maintenance triggers based on temperatures, vibration, and other types of readings
- AI-powered insights: Predicts failures using historical data and machine learning and optimizes maintenance schedules to reduce downtime and maintenance costs
Pros of CMMS
CMMS software:
- Allows you to create, assign, monitor, and complete work orders and inspection checklists all in one place
- Provides accurate compliance tracking via digital sign-off on completed asset maintenance tasks
- Enables both high-level and granular MRO inventory management
- Provides excellent communication ability for your manufacturing and maintenance operations crews, encouraging strong user adoption
- Is simple to use at all levels of your organization (check out MaintainX’s G2 Awards)
Cons of CMMS
The downsides of using a CMMS:
- May lack additional features, such as high-level accounting and HR features
- Might not automatically provide cost tracking for early design/procurement stages or decommissioning
CMMS vs. EAM software: Key differences
Now that we’ve looked at each type of software separately, let’s consolidate that information to highlight their differences.
Ideal applications
The choice between a CMMS and EAM is less about picking a “better” system and more about aligning the tool with your current operational maturity, asset portfolio size, and budget.
CMMS is best for you if your goal is to streamline maintenance operations without overcomplicating things. CMMS platforms like MaintainX are user-friendly and faster to implement. It’s also an excellent choice if you’re growing and want a scalable option without enterprise-level complexity from day one.
EAM is a better fit for asset-intensive, highly regulated, or operationally complex companies. If you’re already operating at a high level of enterprise maturity and need to manage thousands of assets across multiple locations, an EAM might be the right option. EAM is generally more expensive and takes longer to implement, so make sure you’re carefully evaluating your needs before settling on EAM.
Scalability and growth
CMMS platforms are no longer entry-level tools suitable only for small teams. Modern CMMS tools like MaintainX are scalable, in terms of both users and functionality. They support multiple locations, departments (maintenance, quality, operations, etc.), and complex workflows, all while remaining user-friendly for frontline adoption.
The bottom line is that CMMS tools have closed much of the historical functionality gap, especially for maintenance-centric operations. A scalable CMMS like MaintainX offers a lot of the capabilities of an EAM at a fraction of the cost and complexity. However, a small fraction of companies may still find more value in implementing an EAM, for example, companies that already use a full-blown ERP system and want asset management tightly woven into that fabric.
Key functions
CMMS primarily focuses on streamlining maintenance operations. Key features include work order management, preventive maintenance scheduling, asset management, parts and inventory tracking, checklists, inspections, and audits. CMMS platforms offer enough functions and capabilities for most companies.
EAM platforms offer additional features to cover the entire lifecycle of assets. Additional features include capital planning, capital budgeting, and advanced business intelligence.
Summary of differences
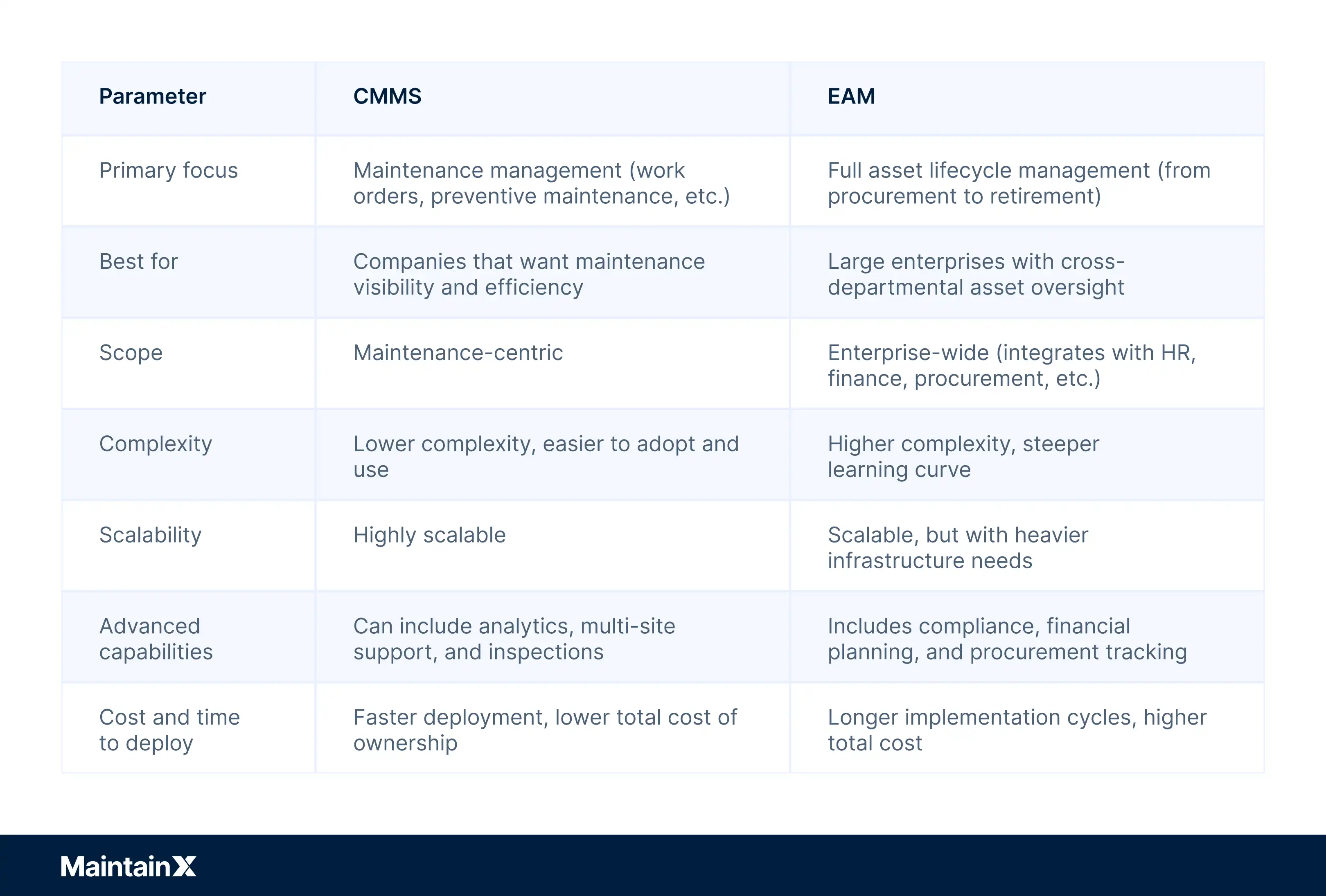
Which maintenance management software is best for your business?
When considering your options, you’ll want to start by taking stock of your current business position and overall needs. For example, how many assets do you manage? How do you presently manage your assets? What are your pain points?
Take advantage of free subscriptions, join webinars, read use cases and case studies from different providers, and, of course, consider the requirements of each area of your business, from maintenance personnel to machine operators to supervisors and, ultimately, your customers.
While both help automate workflows and encourage improved asset performance, the right software solution will meet your organization’s future needs. If you’d like to see if MaintainX is right for you, book a live tour.
FAQs on CMMS and EAM
When is a CMMS the best choice?
A CMMS like MaintainX is ideal for businesses that want to switch from paper-based maintenance management (or siloed digital systems like spreadsheets) to a more transparent, streamlined, and efficient manufacturing and maintenance tool.
“As technology has improved, CMMS capabilities have expanded to blur the lines between enterprise asset management systems (EAM) and enterprise resource planning (ERP) software. They are IIoT-ready and contain native integration capabilities for commonly used software. . . . CMMS developers have the system knowledge to create integration hubs and ensure that the incoming data structure and naming conventions align correctly with their CMMS’s required meta-data elements.”
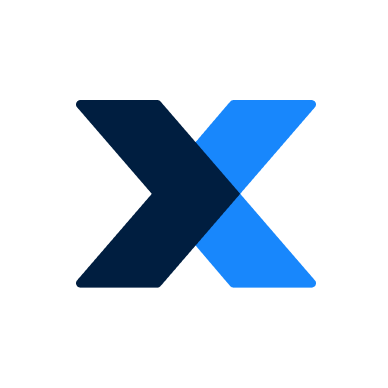
The MaintainX team is made up of maintenance and manufacturing experts. They’re here to share industry knowledge, explain product features, and help workers get more done with MaintainX!