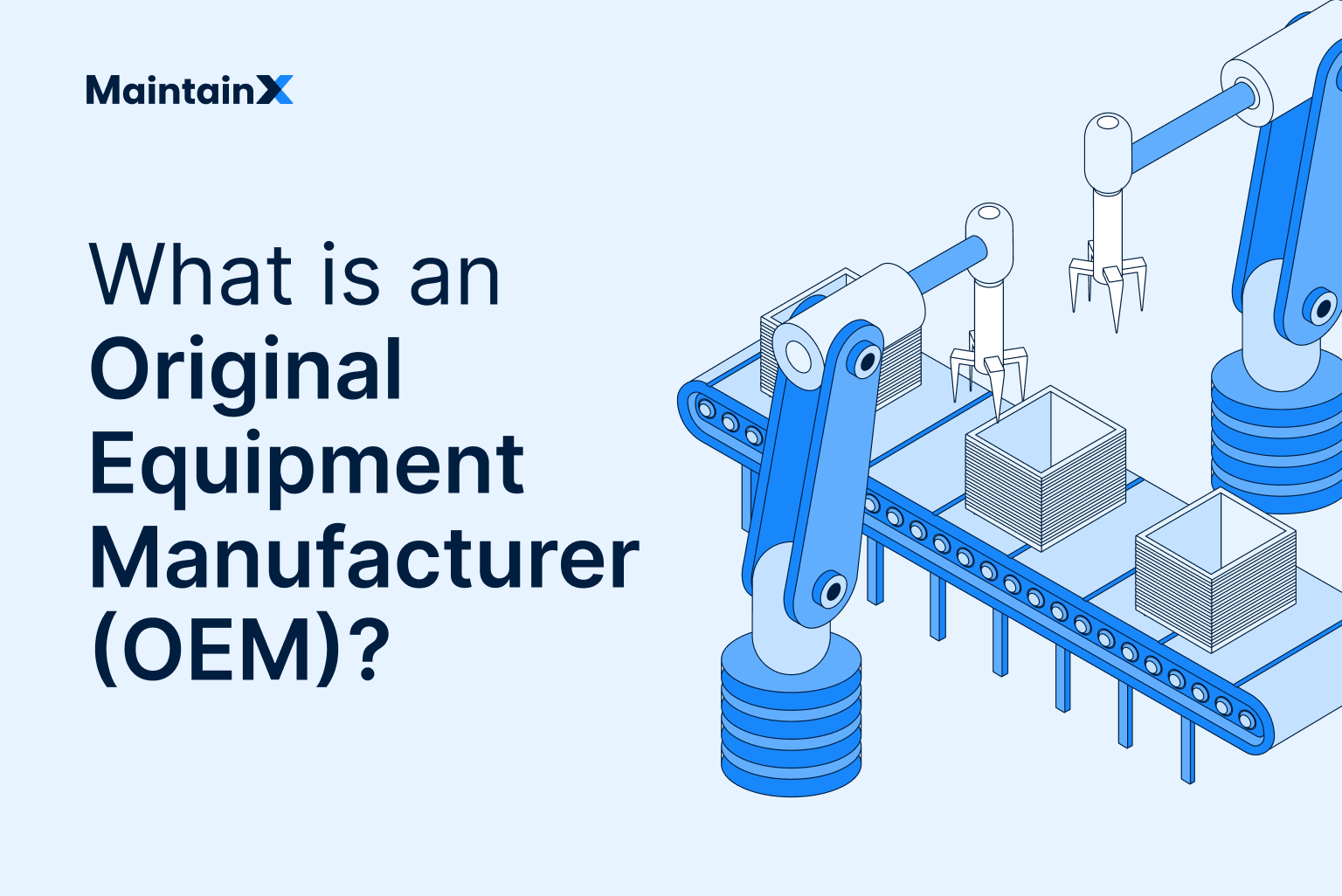
Balancing complex equipment maintenance, peak performance, and resource efficiency can be challenging. Between trying to meet customer demand, managing labor optimally, and keeping equipment in good working order, it can be easy to lose sight of seemingly minor issues like finding the right equipment parts.
Many kinds of parts exist in the market, and maintenance managers who do not pay close enough attention to their choices must be ready to face incompatibility issues, increased downtime, and compromised safety. Working with the right original equipment manufacturers (OEMs) to source the parts that you need is critical to reducing maintenance costs, improving asset performance, and reducing unplanned downtime.
Original equipment manufacturers play a crucial role in the maintenance of equipment and machinery. OEMs produce the components or equipment used in another company's end product, making them essential partners for maintenance managers. In this post, we'll explain what OEMs are, how they work, and the benefits they provide to manufacturers.
What is an OEM?
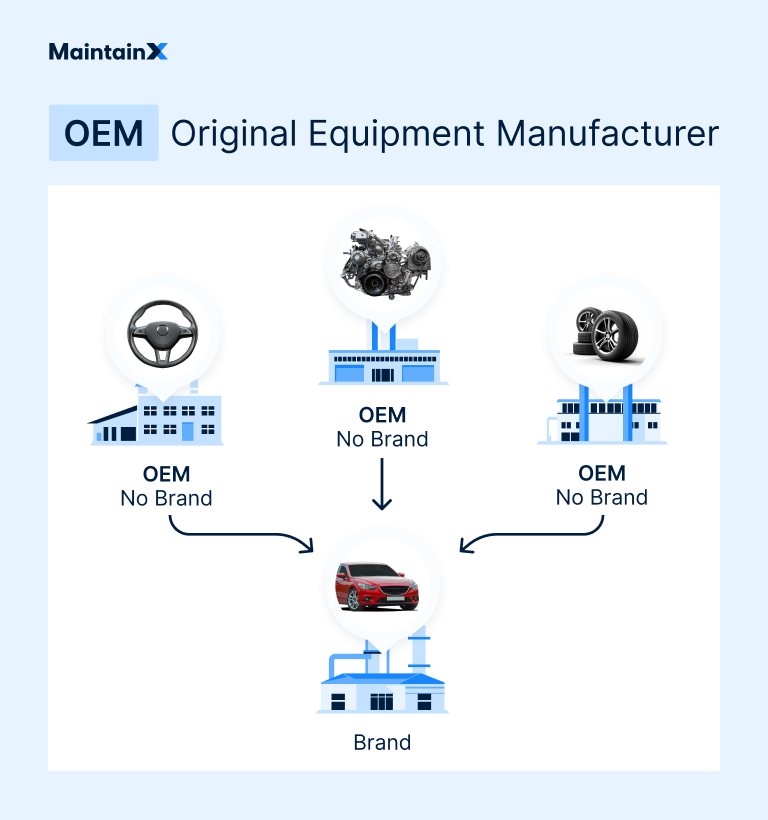
An original equipment manufacturer (OEM) specializes in producing components or equipment used in another company's end product. For example, automotive companies like BMW, Ford, and Mercedes-Benz buy components from OEMs like Bosch and Continental and integrate the components into the final cars under their brand name. Instead of selling directly to consumers, OEMs work closely with these companies, known as a value-added resellers (VAR), to create customized components or equipment based on their needs and specifications.
Key characteristics of OEMs include:
- Expertise in specific components: OEMs often possess expertise in manufacturing specific parts. For example, they might produce automobile engines, computer processors, or smartphone display screens.
- Collaboration with other companies: OEMs typically collaborate closely with the companies that use their parts. This collaboration is crucial for ensuring the components are compatible and function effectively in the final product.
- Invisibility in the consumer market: Generally, consumers are unaware that the product or equipment they use is a sum of parts from OEMs. The final product is typically marketed under the VAR brand that puts the parts together.
Examples of original equipment manufacturer
Industrial Equipment OEMs
A company can purchase a Caterpillar skid steer loader in its entirety from Caterpillar, the original equipment manufacturer. And when it's time to replace the air filter, the company can source the genuine part directly from the OEM or purchase a different brand of filters from other companies.
Technology OEMs
PCs enter the market under a brand name, such as Lenovo or Dell. However, the computer manufacturer uses many other OEM products to build the computer. For example, a Lenovo PC may include an operating system from Microsoft, a processor from Intel, and computer software from Adobe.
Automotive OEMs
The auto industry is perhaps the simplest example of an end product built from a network of original equipment manufacturer relationships. Your average Ford pickup may have hundreds of OEM auto parts that come together to form the final product. Everything from the GPS to the air conditioning compressor likely comes from individual original equipment manufacturers.
Why are OEMs important?
OEMs offer companies specialized components at lower costs and with higher reliability. Because they specialize in producing specific components, they develop expertise and technological capabilities in manufacturing that product.
Innovation lies at the heart of OEMs. They consistently push their boundaries with investments in research and technology to improve their current components and create new solutions. These innovations can often reshape the trajectory of an entire industry. Many of the solutions we currently use result from an OEM’s pursuits—GPS navigation, anti-lock braking systems (ABS), and autonomous vehicles are great examples.
Companies also work with OEMs because they can achieve greater cost efficiency. Because they work with multiple companies, they can produce specialized parts at scale. And economies of scale allow OEMs to produce parts at a cost much lower than if done in-house.
You might have varying component needs—factors like seasonality and macroeconomic factors can drive your demand. Working with OEMs allows you to scale back or scale up orders as needed. OEMs can typically support this since they serve a diversified clientele.
Benefits of partnering with OEMs
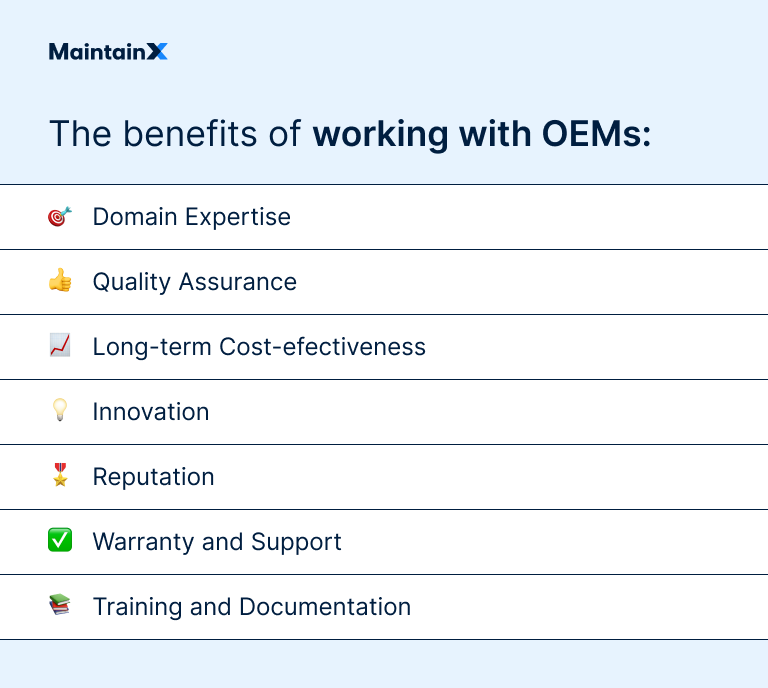
Some of the largest companies in the world rely on OEMs to source components for their products—and remember, these are companies with big pockets. Wonder why? Here are a few reasons:
- Domain expertise: OEMs specialize in specific components and parts. This niche approach allows them to build expertise and technological capabilities that translate to high-quality production.
- Quality assurance: OEMs manufacture parts to match the specifications and performance standards of the original product. This approach guarantees a high level of quality, ensuring that the parts fit perfectly and function as intended, which is crucial for maintaining the integrity and longevity of the product.
- Long-term cost-effectiveness: While OEM parts might sometimes have a higher upfront cost than aftermarket parts, their longer lifespan, reliability, and the minimization of downtime can lead to greater cost-effectiveness in the long run. The reduced risk of damage to other product components contributes to overall cost savings.
- Innovation: OEMs typically make efforts to innovate in multiple ways. They invest in R&D, partner with clients to achieve more effective and functional designs, and experiment with raw materials and manufacturing techniques that can improve the quality of manufactured components.
- Reputation: Many companies partner with OEMs to add credibility. If you’re a small or medium-sized computer manufacturer, partnering with OEMs like Foxconn or Intel can earn your brand credibility because people know and trust these OEMs.
- Warranty and support: OEM parts often come with a manufacturer's warranty. Additionally, using OEM parts usually doesn't void any existing warranties on the product. This aspect, combined with the support provided by the manufacturer for their specific parts, offers peace of mind and valuable assistance in case of issues.
- Training and documentation: OEMs usually provide comprehensive training and documentation for their parts and services. This system ensures that the users or technicians are well-informed about the proper installation, maintenance, and use of the parts, leading to more efficient and effective operation and troubleshooting. Using a CMMS, you can attach the OEM manuals directly to work orders and procedures.
OEMs and the future of manufacturing
Rapid advancements in technology has revolutionized production processes and redefined the very essence of modern manufacturing. OEMs stand poised on the cusp of a new era as innovation drive improvements in efficiency, productivity, and sustainability. Here are some ways OEMs are taking advantage of technology to transform their business:
- Artificial intelligence (AI): AI deserves a top spot on this list because it will reshape how OEMs run business. AI will improve efficiency, predictive maintenance capabilities, product design optimization, customer behavior analysis, and after-sales support. This list is far from exhaustive—these are just a few areas AI will impact.
- IoT (Internet of Things) devices: IoT devices collect real-time data from equipment. You can use this data to monitor assets and predict potential failure events. Feeding this data into analytics software can help implement prescriptive maintenance, an excellent way to reduce downtime and improve profitability. For example, GE uses IoT in the wind turbines to monitor real-time performance and create a predictive maintenance schedule. This method has reduced downtime by 20% and increased annual energy production by 15%.
- Edge computing: Edge computing enables faster data processing, which helps realize the potential of your IoT devices by providing quick and localized insights. Another benefit of edge computing is reduced latency. Lower latency supports real-time responsiveness, providing immediate insights into asset performance. It also improves the ability of your autonomous systems to react to safety hazards or changing conditions.
- Augmented reality (AR) and virtual reality (VR): Manufacturers are already deploying AR and VR technologies to deliver innovative and improved customer experiences. For example, Mercedez-Benz provides virtual remote support using AR. By leveraging Microsoft HoloLens 2 and Dynamic 365 remote collaborative conferencing platform, Mercedes-Benz created an AR-enabled repair solution that allows local technicians to connect directly with specialists without needing to travel nationwide.
- Blockchain: Blockchain technology improves traceability, transparency, and security. It reduces the possibility of fraud and solidifies your relationship with OEMs through smart contracts. A smart contract automatically executes the contract terms—when the OEM delivers the product, you can mark delivery as complete, and the system will automatically execute the payment based on the agreed terms.
- Advanced materials and nanotechnology: OEMs will be able to produce stronger and lighter parts in the future to improve product performance. For example, composite materials like carbon fiber-reinforced polymers (CFRP) have gained popularity in multiple industries, including automotive and construction. CFRP offers excellent strength, is lighter than metals, and improves efficiency and performance. Similarly, nanocomposite materials with nanoplastics dispersed in a matrix improve strength and conductivity.
Partnering with future-ready OEMs is vital to your success. Look for OEMs prepared to invest in or have already invested in innovative technologies. They’ll help you build better products faster through their innovative offering.
Key considerations when partnering with OEMs
There are four things you should consider before placing your first order with an OEM:
Capacity and scalability
For growing manufacturers, partnering with OEMs—particularly those with the capacity to meet your needs—can significantly speed up operations by saving you time, effort, and resources that would otherwise go into manufacturing parts from scratch. However, partnering with an OEM lacking the capacity to upscale can hinder your attempts to grow, leaving you stuck and potentially needing a new partner at crucial times. Pay attention to their capacity and ability to upscale production to meet your future needs when evaluating OEM.
Technical expertise
Not all OEMs function equally. Despite the cost and operational benefits of partnering with an OEM, working with the wrong one can mean you risk products poorly suited to your needs. Devote time to assessing the technical expertise of potential OEM partners—inspect their products and facilities, seek customer feedback, and work with your engineering team to ensure the OEM’s outputs meet your technical standards.
Intellectual property (IP) rights and licensing agreements
Work out who will retain ownership before collaborating with an OEM on developing a new IP. Being upfront about this helps to prevent future legal conflicts and ensure a smooth and beneficial collaboration.
Consider signing non-disclosure agreements (NDAs) to prevent the OEM from disclosing proprietary data to third parties. License terms are also critical—sign an agreement to establish the scope, duration, restrictions, and royalty payments for the licensed IP.
It’s also important to factor in the local regulator’s interpretation of the IP laws. For example, most Chinese courts agreed that OEM-related products bearing identical or similar trademarks constituted infringements. But between 2010 and 2015, the SPC made various retrial judgments that held that simply affixing trademarks to OEM-related products doesn’t translate to infringement. Things changed again with the Honda case in 2019.
“After the 'Honda' case in 2019, Chinese courts adopted the judgment that affixing trade marks on OEM-related products constitutes trademark use, and thus expressed cautious optimism about the defense of noninfringement by OEM activities.”
Communication
Establish clear communication channels and protocols when working with an OEM. Doing this helps to ensure clarity when sharing technical details like specifications, requirements, or standards, especially when starting your contract with the OEM.
OEMs in maintenance
Original Equipment Manufacturers (OEMs) play a crucial role in industrial maintenance, contributing to the efficiency, reliability, and longevity of equipment and machinery.
- Equipment design and reliability: The domain expertise of OEMs results in high-quality products that, by extension, are assembled into high-quality equipment. Because the parts fit particular specifications and designs, they work together to reduce the risk of damage and improve equipment reliability and availability. This minimizes the occurrence of downtime and the need for reactive maintenance.
- Documentation and manuals: Especially compared to aftermarket parts, OEMs are more likely to provide robust documentation and equipment manuals. This approach ensures teams assemble and use equipment as needed and don’t spend extra time searching for instructions when issues arise.
- Asset lifecycle support: Instead of selling parts and sending customers on their way, many OEMs offer robust after-sales support—from warranties to reliable replacement parts and technical assistance—that facilitates your asset lifecycle management.
- Remote diagnostics: Some OEMs use remote monitoring and diagnostics systems to recognize malfunctions in equipment and parts located at various sites. Through telematics technology, OEMs can monitor some parts they supply you, identify any issues, and communicate them to you. Also, with OEMs that offer after-sales support, technicians can use remote diagnostics to get a more robust picture of a malfunction before arriving on-site.
OEMs and VARs
Value-added resellers (VARs) manufacture finished products from parts produced by OEMs. As the name suggests, VARs offer additional benefits to consumers, such as extra features integrated into the product, after-sales services and support, or value in the form of a trusted brand name. In practice, an OEM can make several parts that different VARs purchase and assemble into other products under their brand names. The OEM will often create according to the VAR’s requirements.
VARs also sell OEM products directly to consumers. For example, BMW (a VAR) procures fuel injection systems from Bosch (an OEM) and uses them in its car assembly. However, a customer who needs a replacement fuel injection system needn’t go to Bosch and can purchase one directly from BMW or the aftermarket (more on this shortly).
OEM and ODM
In the case of original design manufacturing (ODM), one company or customer selects an existing product design from a manufacturer, makes slight changes or customizations, and sells it under their brand name.
For example, suppose an original design manufacturer has a catalog with phone charger designs. Two companies can choose to have the ODM produce the charger in different colors. The products retain the same general design, but branding, packaging, and other aesthetic factors follow each buyer’s specifications.
ODM reduces the amount of work the seller has to perform in manufacturing. Instead of investing time and resources in product development, they can focus their attention and energies on branding and marketing strategies.
ODM also benefits the manufacturer, as producing the same design in large quantities reduces the unit cost of each product.
However, one significant risk of ODM is that sellers can struggle to stand out from competitors as, despite the small changes and customizations, the products are still the same.
OEM vs. Aftermarket
The aftermarket is the market for third-party manufacturer parts that perform the same function as OEM parts. Aftermarket parts are often compatible with products from a wide range of manufacturers, unlike OEM parts, which are typically optimized to work with specific products from specific manufacturers.
Aftermarket products can be cost-effective in the short term, but it’s wise not to be tempted by their cheapness. One reason for this is that they aren’t always of the same quality as OEM parts, and while they may work as well at first, their reduced durability and quality lifespan may diminish their lifespans.
In addition, performance issues may arise as aftermarket parts exist to serve a wide range of equipment, meaning they often lack the level of customization OEM parts have for your particular machines. You can be sure OEM parts will fit and work right.
Also, with OEM parts, you’ll likely have a more robust warranty and customer support system if issues arise.
Read more about how to choose between OEM or Aftermarket parts.
OEMs vs. Resellers vs. Distributors
In addition to the aftermarket and ODMs, you can also source components from resellers and distributors. Here’s a quick overview of how they’re different that shows OEMs are your best bet:
OEM in the automotive industry
One of the most common applications of original equipment manufacturing is in the automotive industry. The average car comprises thousands of parts—brake pads, exhaust systems, windshield glass, window switches, chair springs, nuts, bolts, etc. However, producing all of these components on a car-by-car basis would be an arduous endeavor for even the most accomplished vehicle manufacturing division.
Manufacturers like BMW, for example, design, create, and sell their products made up of countless sub-assembly parts. These parts come from OEMs like Bosch, while BMW functions as a VAR, assembling the parts to its own specifications and offering added value in the form of unique designs, extra features, the BMW brand name, support services, and much more.
Another example is the relationship between the Ford Motor Company and Motorcraft. Motorcraft is an OEM that supplies parts to Ford—in fact, Ford owns Motorcraft. Despite this relationship, Motorcraft functions autonomously and supplies parts to other car manufacturers such as Mazda. In addition, not all Ford parts come from Motorcraft, and the company sources components from other OEMs. Like BMW, Ford acts as a VAR here, assembling a car out of parts from its affiliated OEM (Motorcraft) and other OEMs like Bosch.
OEMs and CMMS work together to enhance equipment maintenance
An OEM partnership and CMMS are vital to a successful maintenance strategy. OEMs offer expertise, technical knowledge, and access to high-quality parts, and CMMS software helps manage maintenance tasks and parts inventory, collaborate with technicians, and analyze maintenance data. Here’s why you also need a CMMS:
- Data integration: CMMS platforms centralize maintenance data. It stores maintenance history, work orders, parts, and standard operating procedures (SOP). Similarly, it can integrate with OEM data sources like manuals, catalogs, and service bulletins.
- Preventive maintenance schedules: CMMS can automatically assign work orders based on the OEM’s recommended preventive maintenance schedule. To put preventive maintenance on autopilot, create a template that outlines the entire process, maintenance frequency, and required resources.
- Predictive maintenance insights: Some OEMs offer predictive maintenance insights based on years of data collected while manufacturing and using their equipment. These insights can guide various decisions and predict failure events, protecting you against unplanned downtime.
- Spare parts management: Once you integrate the OEM catalog within the CMMS, they can view images, specifications, and compatibility. At the same time, technicians can view current spare parts inventory. This streamlines spare parts management, but you can even automate it entirely by setting a trigger for ordering inventory. When the inventory reaches a certain level, the CMMS can automatically place an order with the OEM.
- Warranty management: You can track warranty information for each asset using your CMMS. You can store details like the start and end dates, coverage, and T&C. You can even configure the CMMS to alert you when the warranty for a specific asset ends.
- Performance analytics and reporting: CMMS generates reports using data collected over a specific time frame. For example, it can create reports that provide insights into quarterly performance, maintenance activities, and OEM spare parts consumption. This data offers valuable information for decision-making.
Partnering with the right OEM is key
Sure, OEM partnerships can contribute to your success. But there are various things to consider before selecting an OEM: product quality, reliability, technical capabilities, and facility standards are a few examples. Reliability is essential because a lack of parts can translate to downtime.
In addition to a reliable OEM partner, you also need dependable assets. Keeping up with maintenance schedules is critical to ensuring asset reliability. MaintainX helps streamline and automate critical parts of your maintenance schedule. If you’re interested in learning how MaintainX can transform your maintenance process, book a demo today.
Original Equipment Manufacturer FAQs
What is an example of an Original Equipment Manufacturer (OEM)?
Foxconn Technology Group is a popular OEM in the hardware space. The company produces a range of electronic components, including printed circuit boards (PCBs), displays, and connectors. Foxconn sells these components to companies like Apple, Dell, and Sony.
What does it mean when a product is OEM?
OEMs manufacture components for other businesses. The purchasing company integrates the components into their finished product. These components often adhere to the purchasing company’s specifications and designs.
What are the different types of OEMs in the automotive industry?
OEMs in the automotive industry produce components and systems used in manufacturing vehicles. Automotive OEMs fall into categories—Tier 1, 2, and 3. Tier 1 OEMs produce entire systems or major components like engines, braking systems, and steering assemblies. Tier 2 and 3 OEMs produce smaller components and subsystems like seats and specialized materials.
Note that some manufacturers also sell components that compete with OEM parts. These components are called aftermarket replacement parts. Customers will typically use an aftermarket part when the original product or part fails and needs replacing. This is exactly why your mechanic doesn’t ask you to get a replacement from the OEM when you repair your car.
What is the difference between an OEM and a manufacturer?
OEMs produce specialized components that manufacturers use to produce a finished product. Manufacturers are buyers of these OEM components. They use OEM components to create finished products. For example, Bosch (an OEM) supplies fuel injection systems to BMW (a manufacturer).
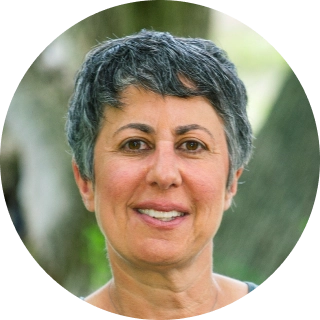
Caroline Eisner
Caroline Eisner is a writer and editor with experience across the profit and nonprofit sectors, government, education, and financial organizations. She has held leadership positions in K16 institutions and has led large-scale digital projects, interactive websites, and a business writing consultancy.
See MaintainX in action