Look under the hood of any organization, and the primary goal of its preventive maintenance program is the same:
Reduce Asset Deterioration → Reduce Equipment Downtime → Reduce Costs.
Preventive maintenance (PM) is planned maintenance that increases the longevity of company assets, equipment, and infrastructure. Also known as preventative maintenance, PM includes regular maintenance tasks like adjustments, cleaning, lubrication, repairs, and parts replacements.
Put simply, any kind of maintenance that isn’t a reaction to “Oh crap, when (or how) did that happen?” is preventive maintenance.
To effectively prevent those "oh crap" moments, it's crucial to understand that preventive maintenance is not a one-size-fits-all approach. There are various types of PM, each with its own strengths and ideal applications. Let’s explore the four main types in this guide.
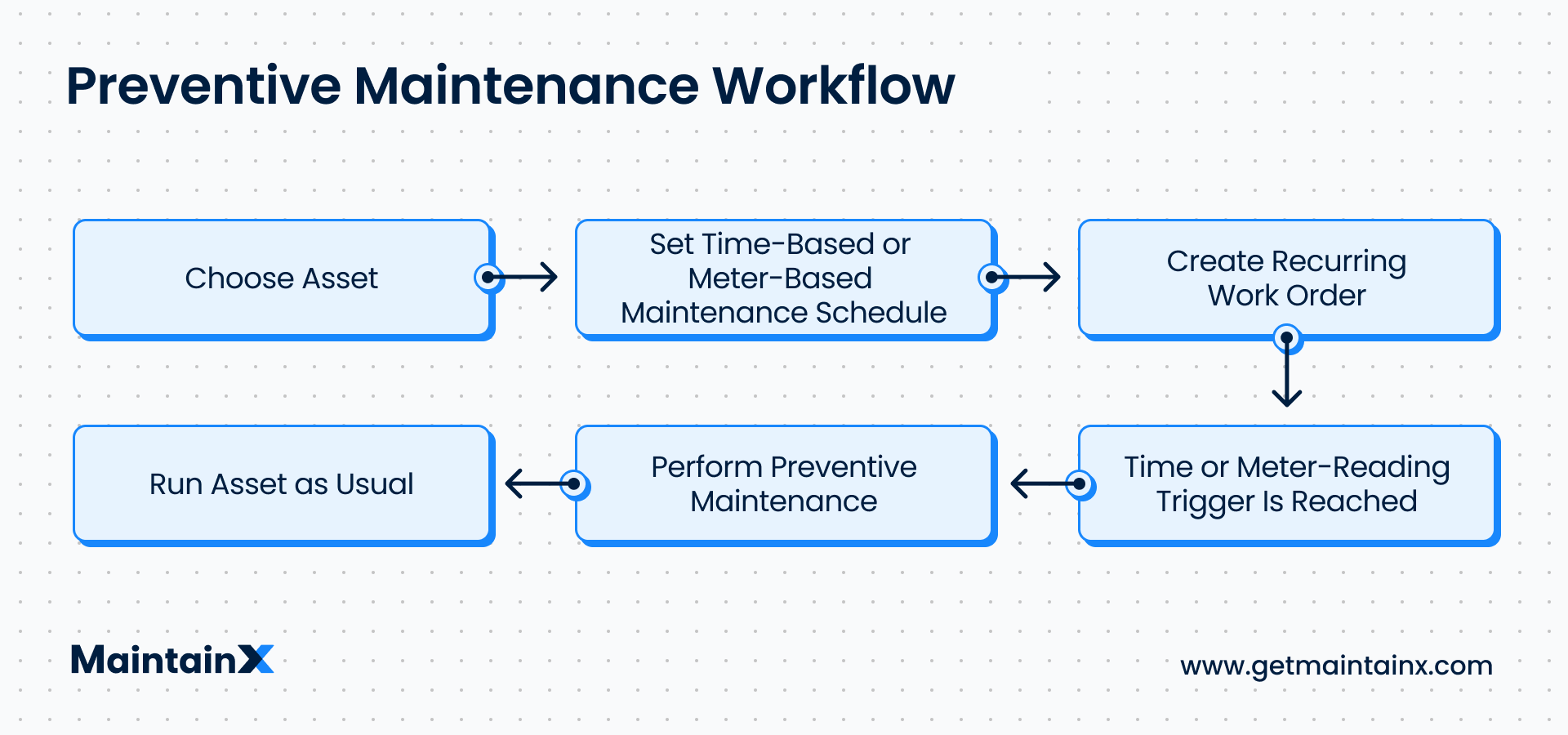
The 4 types of preventive maintenance
Although there is no universal consensus on exactly how many different types of preventive maintenance exist, most of them fall into four general categories:
- Periodic (Calendar-based) maintenance
- Meter-based maintenance
- Predictive maintenance
- Prescriptive maintenance
1. Periodic maintenance
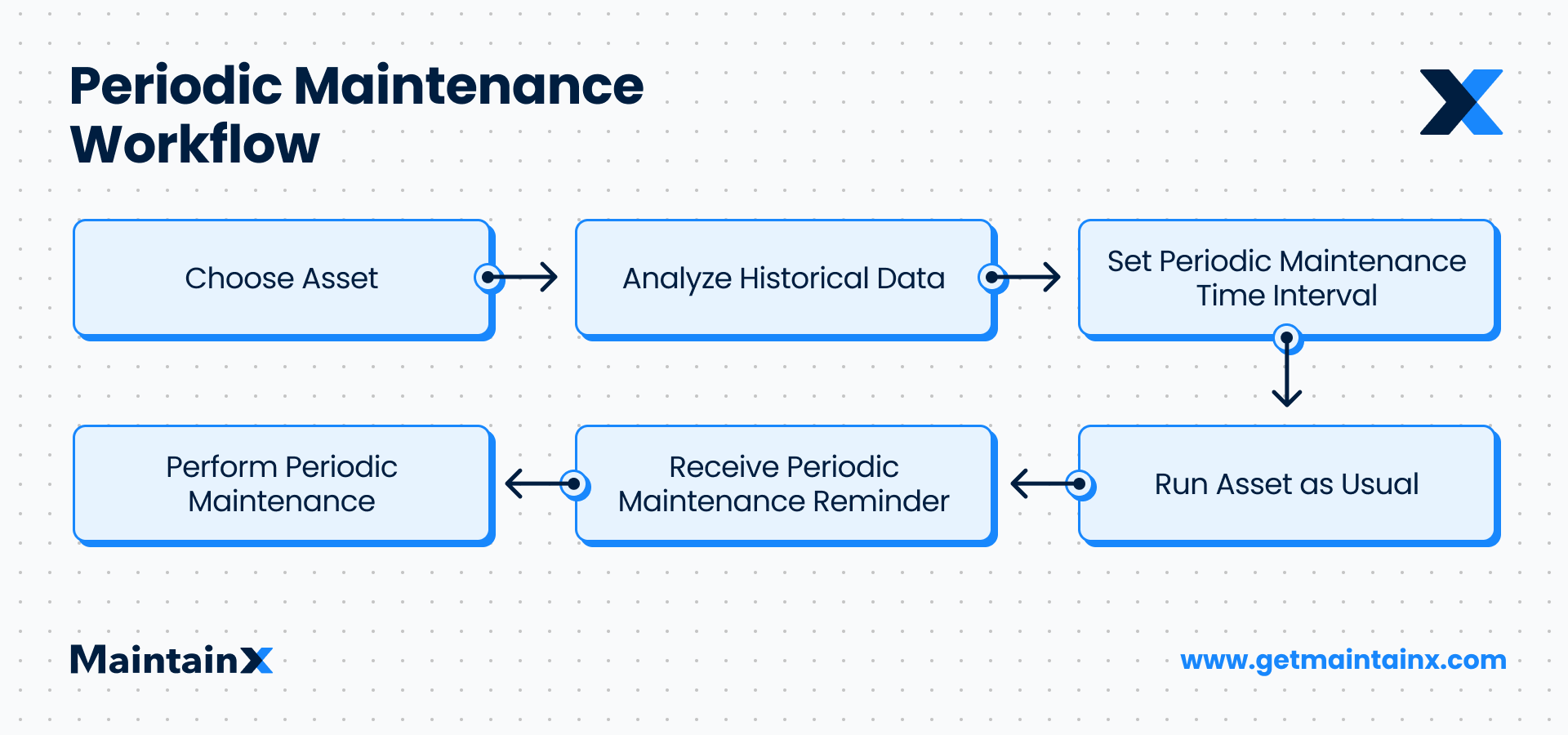
Periodic maintenance, or time-based maintenance, is performed on assets at scheduled time intervals throughout the calendar year. While it can be done annually, quarterly, monthly, or weekly, the best way to know how often to do it is by following a combination of manufacturer guidelines and your own observations.
Each piece of equipment comes with specific maintenance recommendations designed to extend lifespans. These guidelines are based on the manufacturer’s Mean Time Between Failure (MTBF), or the average time a machine is operating between stops. If similar models worked efficiently for X amount of time before maintenance task A was needed, we can conclude your machine will follow a similar pattern.
That said, by tracking your own MTBF, you can finetune your own periodic maintenance schedules with even higher levels of accuracy. It’s also important to note that while periodic maintenance works great for regularly used equipment, it’s ineffective on machines that are only used once in a while.
Additionally, periodic maintenance can include the subcategories of failure-finding maintenance (FFM) and risk-based maintenance (RBM). FTM is the process of checking for malfunctioning “hidden parts” that exist as safety mechanisms.
For example, pressure valves function to prevent machines from overheating. Regularly servicing such unseen parts can provide some peace of mind that assets are safeguarded from larger failures.
Alternatively, RBM represents the philosophy of prioritizing high-risk PM tasks over low-risk PM tasks in the face of limited resources. All of these routine maintenance scheduling methods are useful measures for reducing the likelihood of age-related equipment failure and can be used simultaneously.
Examples of periodic maintenance
- Cleaning corrosion
- Checking bearing grease
- Changing lubricating oils
- Replacing filter components
- Checking pressure/temperature gauges
Pros: Minimal costs to begin, no additional equipment required.
Cons: Risk of performing unnecessary maintenance activities.
2. Meter-based maintenance
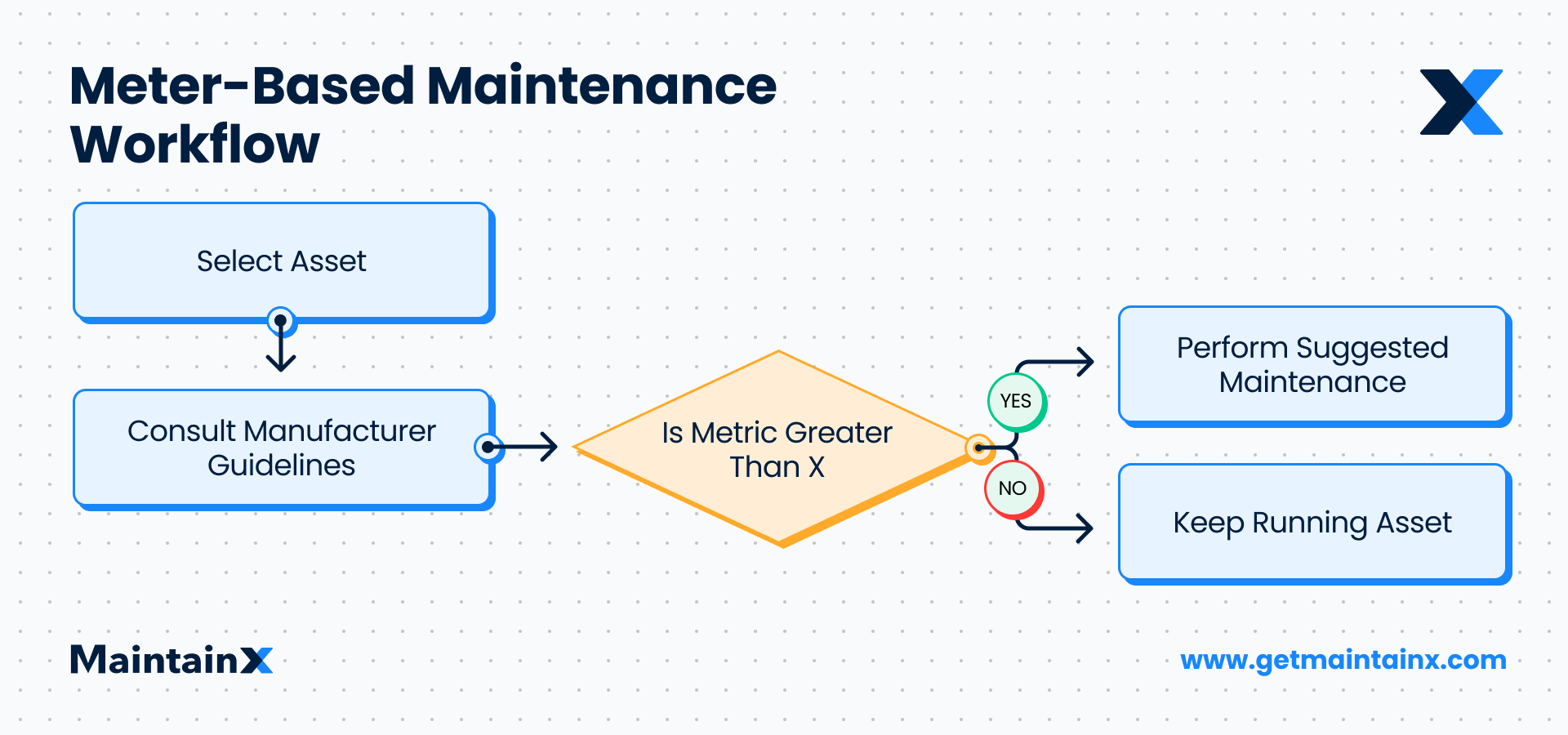
Meter-based maintenance, also known as performance-based maintenance, is slightly more complex than periodic maintenance. This preventive maintenance method task is performed when a meter reading indicates that an asset should be serviced. Common measurement variables include but are not limited to, hours used, miles driven, parts produced, and pressure generated.
Essentially, all meter readings are based on time-based triggers. Consequently, you need to monitor meters regularly to ensure you keep your equipment maintained. Sometimes the asset will have a built-in meter, while, other times, the machine will require separate components for measurement.
Examples of meter-based maintenance:
- Conveyor belt machines with maximum run times
- Checking the chlorine level in a pool
- Changing the oil of a motor every 15,000 miles
- Reading a gauge to ensure it is within a safe range
Pros: Minimal costs to begin, dependably consistent, highly accurate.
Cons: Fairly challenging to maintain compliance with regulations.
3. Predictive maintenance
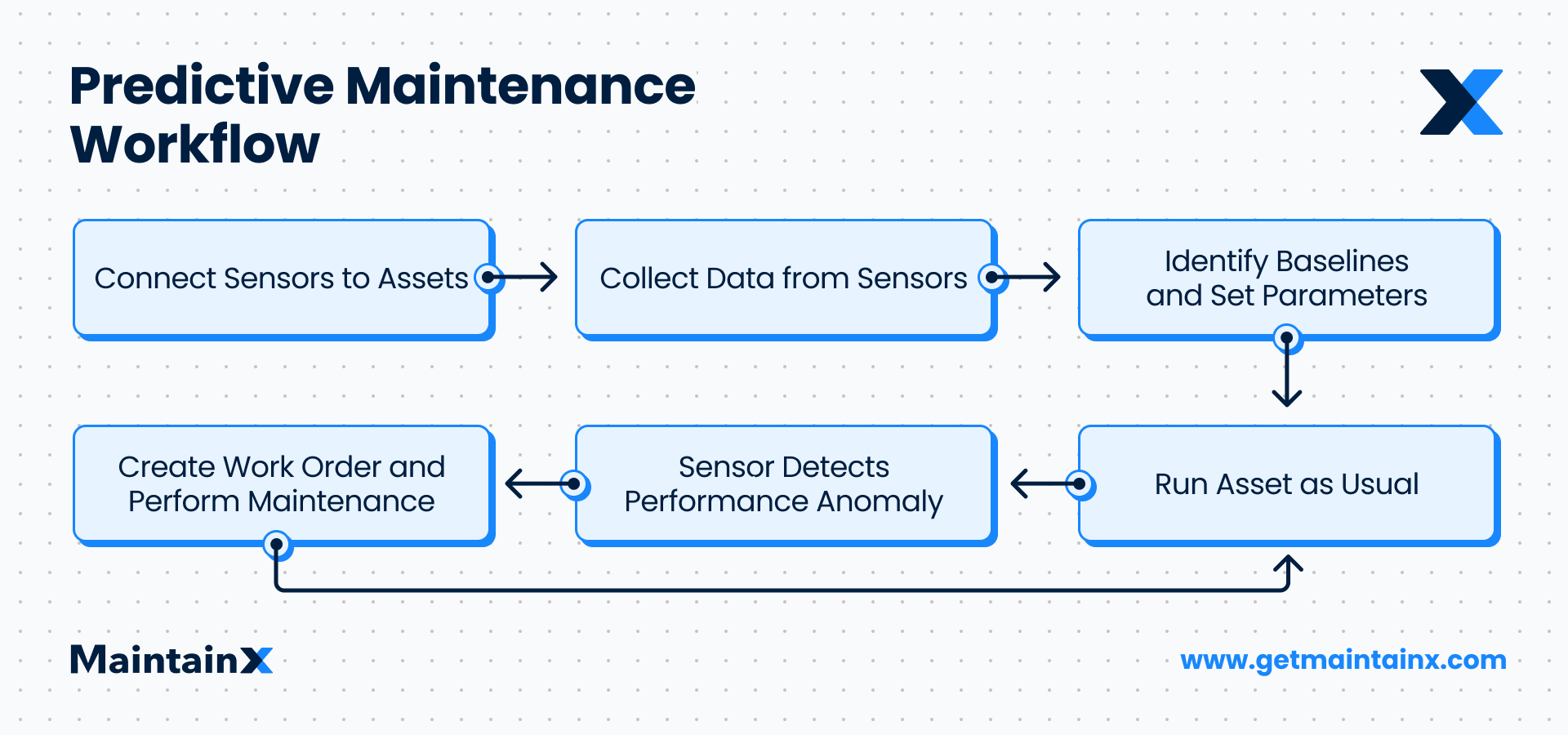
According to IBM’s Using the IoT for Preventive Maintenance report, 30 percent of preventive maintenance procedures are performed too frequently. Yet numerous studies show companies waste even more money by not practicing proactive maintenance at all and simply reacting to unexpected equipment failures.
Predictive maintenance (PdM) is the Goldilocks of the maintenance world—it’s the “just right” solution for not overdoing it or underdoing it with PM. This advanced maintenance method monitors the condition of assets using sensor devices. Once a sensor detects an abnormality, a work order is automatically generated within a Computerized Maintenance Management System (CMMS) and assigned to a maintenance technician.
Predictive maintenance programs can save your organization lots of time, manpower, and money in the long run. However, this emerging technology isn’t a good fit for most teams. If you already have a high level of PM organization in place to set up initial PdM baselines, then you’re an ideal fit. If your team is still in run-to-failure or reactive maintenance mode most of the time or isn’t willing to make a sizable investment, a better bet might be sticking with time-based and meter-based PM.
Examples of predictive maintenance
- Thermal sensors installed on equipment in server facilities provide automated alerts when technology vents are in danger of overheating.
- Vibration meters attached to centrifugal pump motors in coal plants to identify abnormal spikes in acceleration based on historical data.
- Using historical asset data from your CMMS to perform a PM work order one month early on a wrapper machine to prevent unplanned downtime.
Pros: More accurately increase active uptime, streamline maintenance costs
Cons: Expensive initial investment, large organizational commitment
4. Prescriptive maintenance
Similar to predictive maintenance, prescriptive maintenance (RxM) makes decisions based on data. However, this cutting-edge method of equipment monitoring takes efficiency even further with machine learning software. The smart software analyzes equipment condition monitoring over time, assesses operational risks, and makes specialized recommendations that outperform generic manufacturer guidelines.
While predictive maintenance can provide an estimated duration until failure, RxM allows maintenance teams to track variable operating conditions up to the time of failure. The technology behind the advancement is called “prescriptive analytics,” and was created to hypothesize potential outcomes that could lead to equipment stops. The coolest part about prescriptive maintenance?
The more familiar Artificial Intelligence (AI) becomes with your machine’s inner workings, the more cost-efficient your organization becomes. In other words, you almost never perform unnecessary preventive maintenance or emergency reactive maintenance.
As with most early technology, RxM isn’t affordable for most companies at this time and is still in its infancy. However, we expect to see incredible advancements that lower the barrier to entry for organizations of all sizes in the decades to come.
Examples of prescriptive maintenance
- If the weather conditions suggest thunderstorms, which would raise the barometric pressure, the AI might assign you a work order to adjust the pressure in a processing tank to avoid issues.
- If your production line gearbox is due for a monthly PM, but it requires the line to be shut down for 15 minutes during a busy production cycle, the AI might determine there is only a 2% increased likelihood of failure if this month is skipped and will help meet order demand by keeping the line running.
Pros: Highest possible degree of accuracy, streamlined costs, cutting-edge
Cons: Must be customized to individual facilities, very expensive
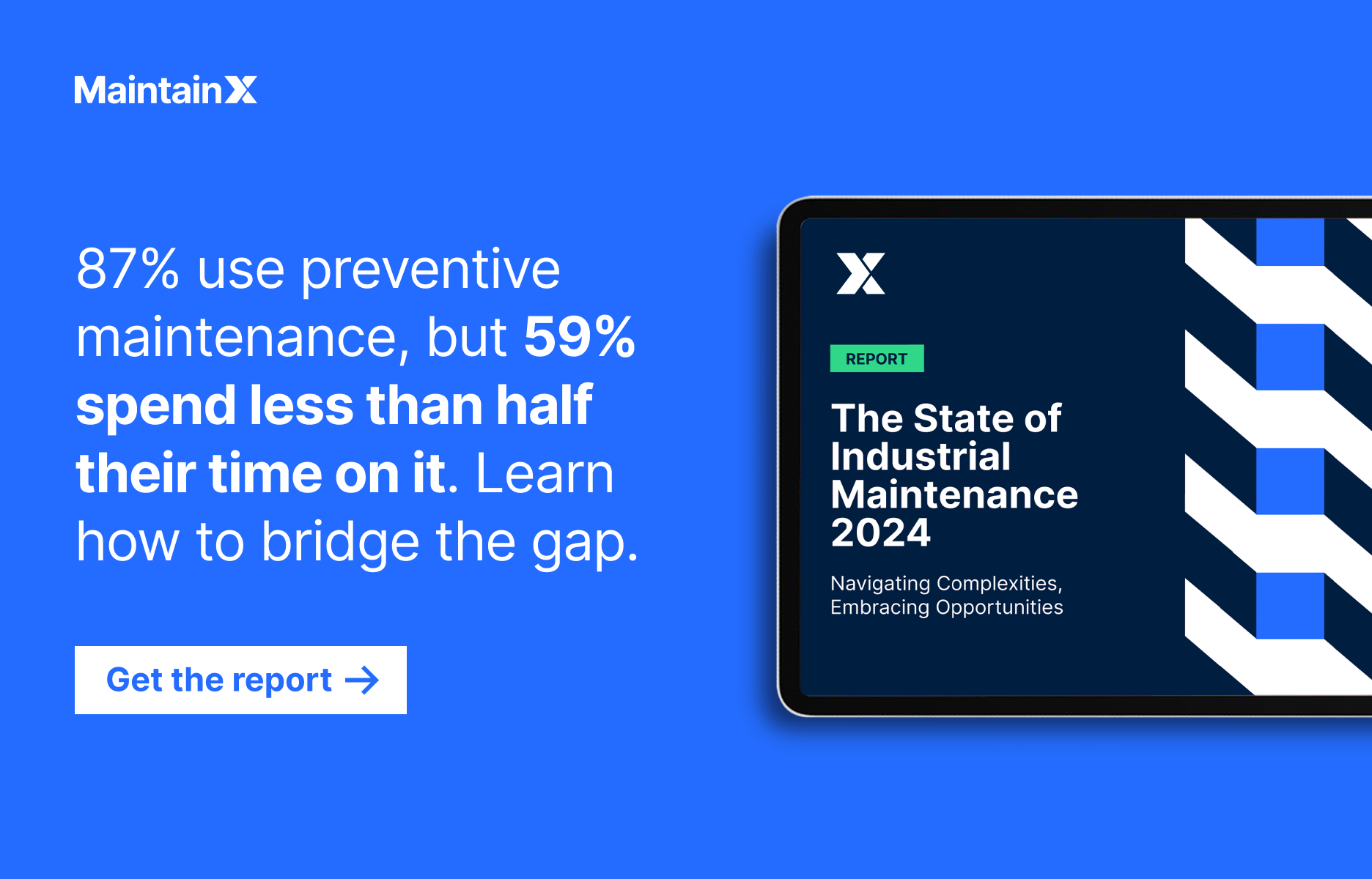
Three examples of preventive maintenance in action
Let’s dive some common examples of preventive maintenance in action:
Condition-based maintenance in manufacturing
An excellent example of preventive maintenance in action is proactively replacing parts after a certain usage threshold, even before they fail completely. This approach is often based on the expected lifespan of the part, as determined by the manufacturer or historical data. For instance, manufacturers often replace conveyor belt rollers after a certain number of rotations to prevent unexpected equipment breakdowns during production that could cause significant downtime and financial losses.
A robust CMMS software like MaintainX can be set up to create work orders based on usage data to ensure regular proactive asset maintenance.
HVAC system maintenance in commercial buildings
Regular inspection and cleaning of filters, coils, and ductwork in heating, ventilation, and air conditioning (HVAC) systems can prevent breakdowns, improve energy efficiency, and ensure a comfortable and healthy indoor environment. This proactive maintenance approach can also extend the lifecycle of the equipment and significantly reduce the risk of costly emergency repairs.
With a CMMS software like MaintainX, you can create repeatable work orders and create a regular inspection schedule for your HVAC system. You can bolster your work orders by including step-by-step procedures and checklists for the technicians.
Regular lubrication of industrial machinery
Lubricating parts like bearings, gears, and chains regularly is crucial to prolonging the lifespan of critical equipment. This simple yet important practice reduces friction and wear, prevents overheating, and improves asset performance. OEMs often include recommended lubrication schedules in equipment manuals.
Simplify preventive maintenance with MaintainX
MaintainX is the top-rated preventive maintenance software that empowers your maintenance team to effortlessly streamline maintenance and safeguard critical assets. Here's how MaintainX can transform your PM program:
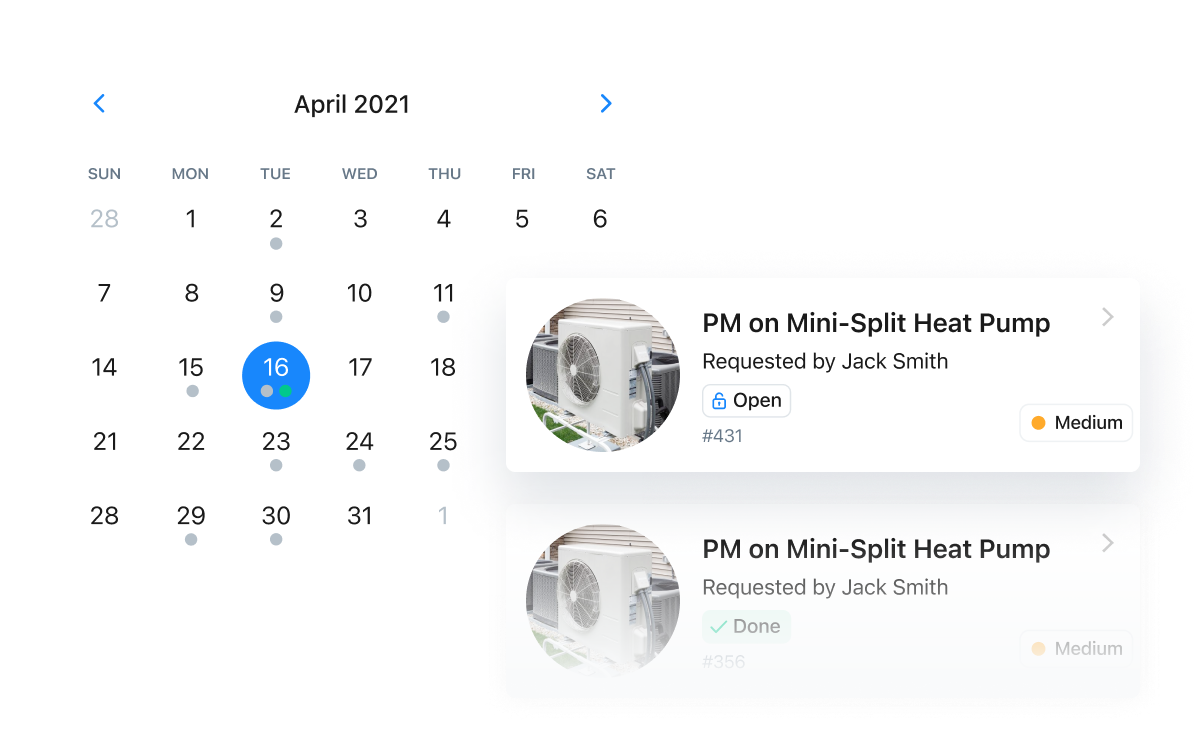
- Automated scheduling: Easily create and schedule recurring work orders and inspections, ensuring consistent and timely maintenance of critical assets.
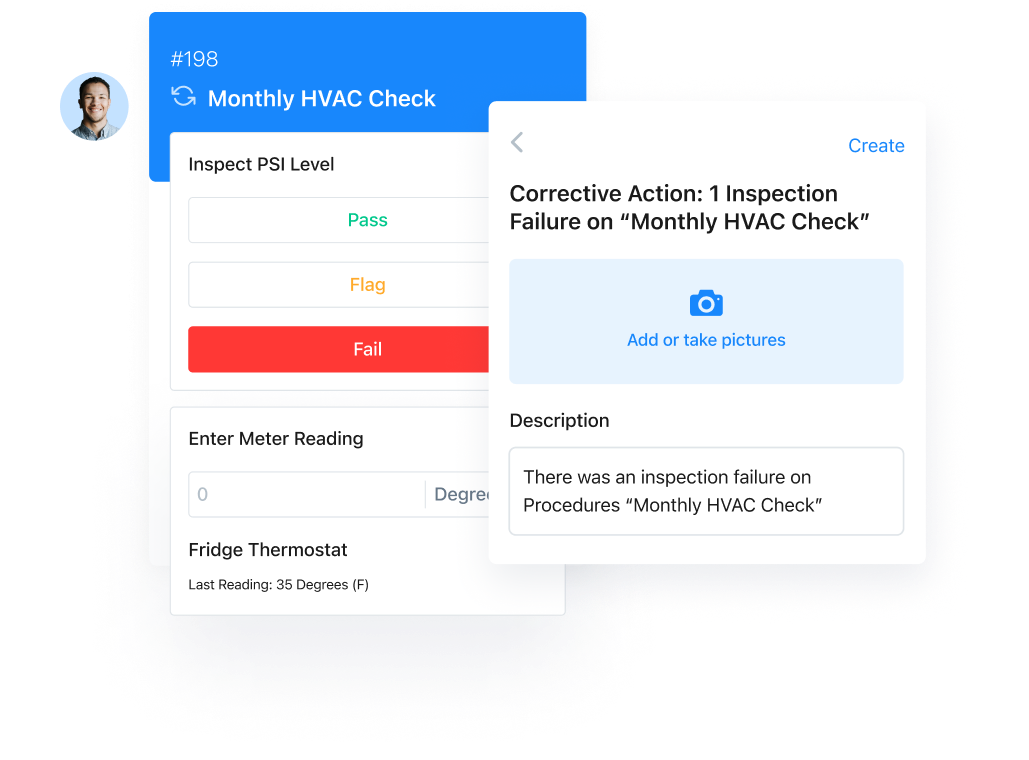
- Swift issue resolution: Respond rapidly to failed inspections with automated corrective maintenance workflows and facilitate timely repairs, refurbishment, and regulatory compliance.
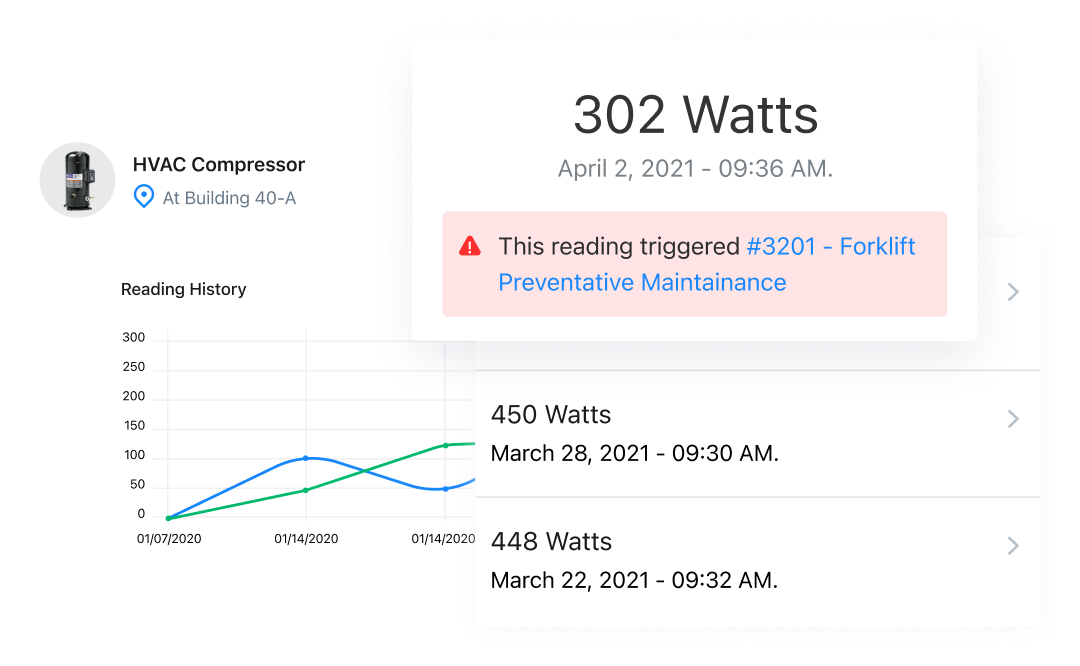
- Condition-based maintenance: Trigger preventive maintenance tasks based on real-time meter readings, such as time used, mileage, temperature, or pressure, ensuring proactive interventions before issues arise.
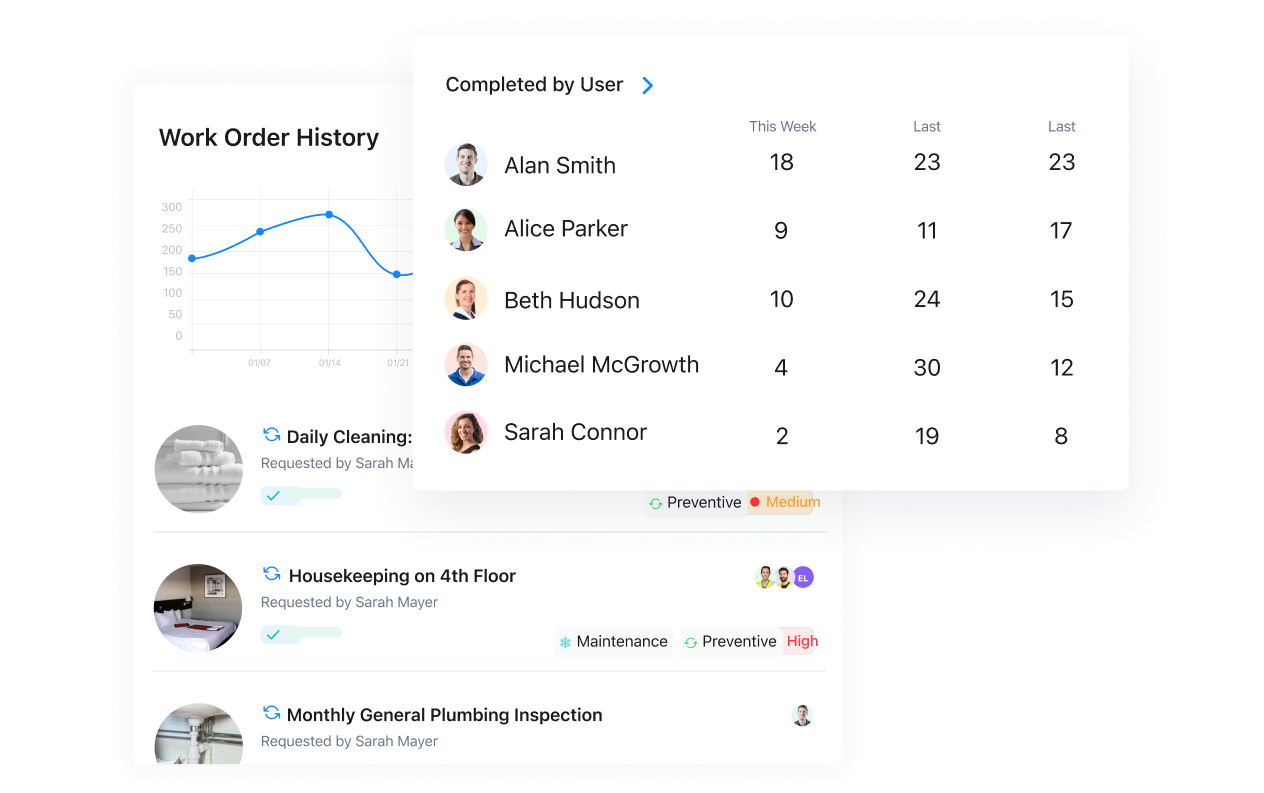
- Data-driven insights: Gain actionable insights into key performance indicators like PM compliance and Mean Time Between Failures (MTBF), enabling data-driven decisions to reduce downtime, optimize staffing, and prioritize high-impact tasks.
MaintainX equips your team with the tools and insights needed to proactively manage preventive maintenance, minimize unplanned downtime, and maximize the lifespan and productivity of your critical assets. Ready to supercharge your maintenance program? Get started with MaintainX today!
Types of preventive maintenance FAQs
What is preventive maintenance (PM)?
Preventive maintenance (PM) is a proactive approach to regular maintenance that involves scheduled tasks and regular inspections aimed at costly repairs, preventing equipment failures and maintaining optimal performance.
Which type of preventive maintenance is best for my equipment?
The best type of preventive maintenance plan depends on factors such as the type of equipment, usage patterns, manufacturer recommendations, and industry standards. In practice, a combination of Time-Based maintenance, Usage-Based maintenance, and Condition-Based maintenance approaches may be used to create a comprehensive maintenance strategy.
How do I implement a preventive maintenance program?
Implementing a preventive maintenance management program involves:
- Identifying equipment that requires maintenance.
- Determining the appropriate type of PM for each piece of equipment.
- Creating a preventive maintenance schedule and assigning responsibilities.
- Documenting tasks, procedures, and results.
- Implementing a system for tracking and analyzing maintenance data.
See MaintainX in action