Preventive maintenance (PM) and breakdown maintenance are the cornerstones of any professional maintenance program. One might even say they are the most commonly used maintenance strategies on the planet. There’s a common misconception that facilities either practice one option or the other (i.e., preventive maintenance vs. breakdown maintenance). However, the reality is most maintenance teams rely upon a mixture of preventive and breakdown maintenance to achieve their goals.
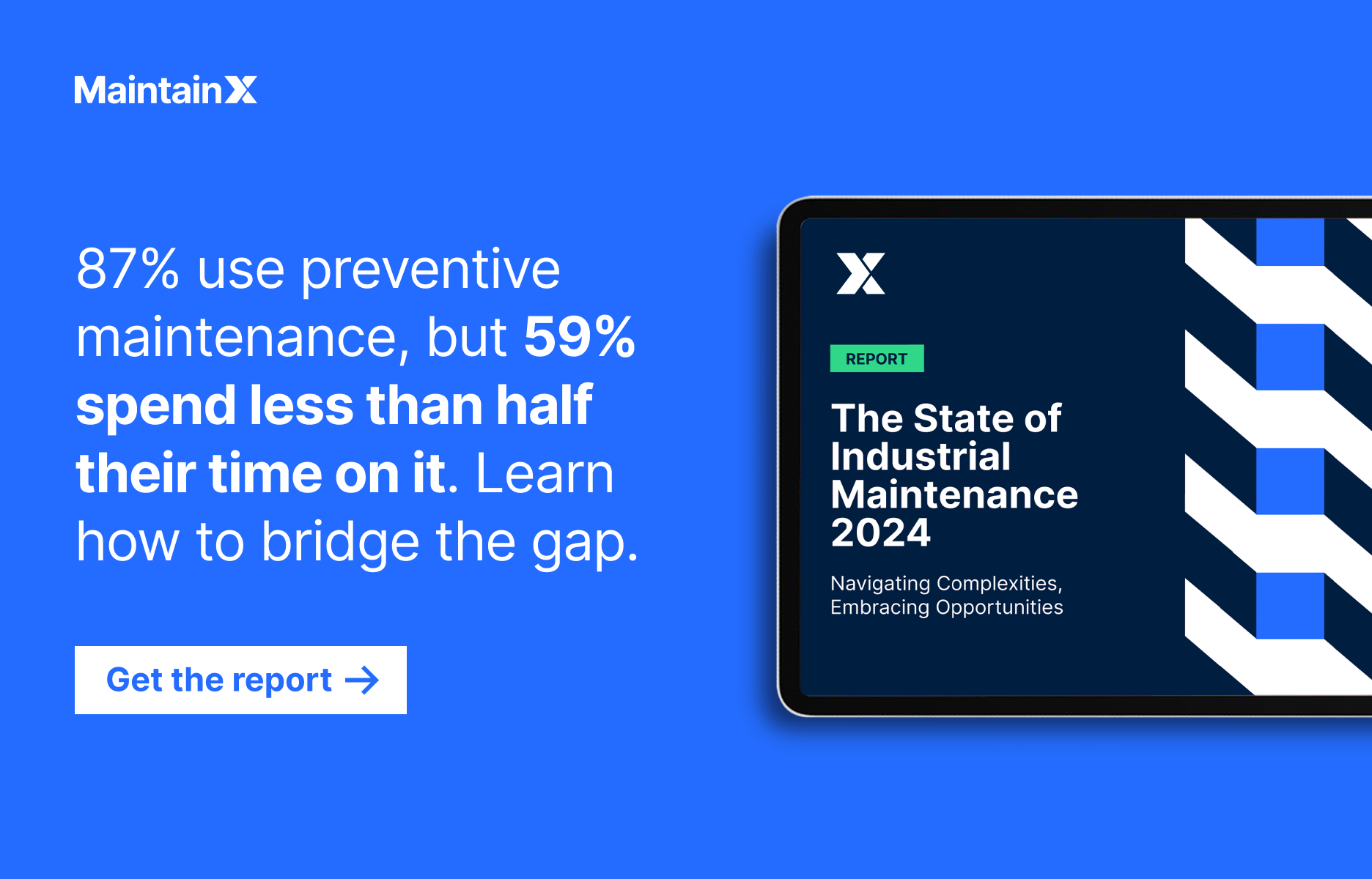
Preventive Maintenance vs. Breakdown Maintenance
Preventive maintenance refers to maintenance tasks that are performed on a repeated schedule to prevent failures. These tasks include conducting regular inspections, reporting identified equipment issues, and replacing parts before failure. The primary goal of preventive maintenance is to detect and take care of small issues before they become big problems.
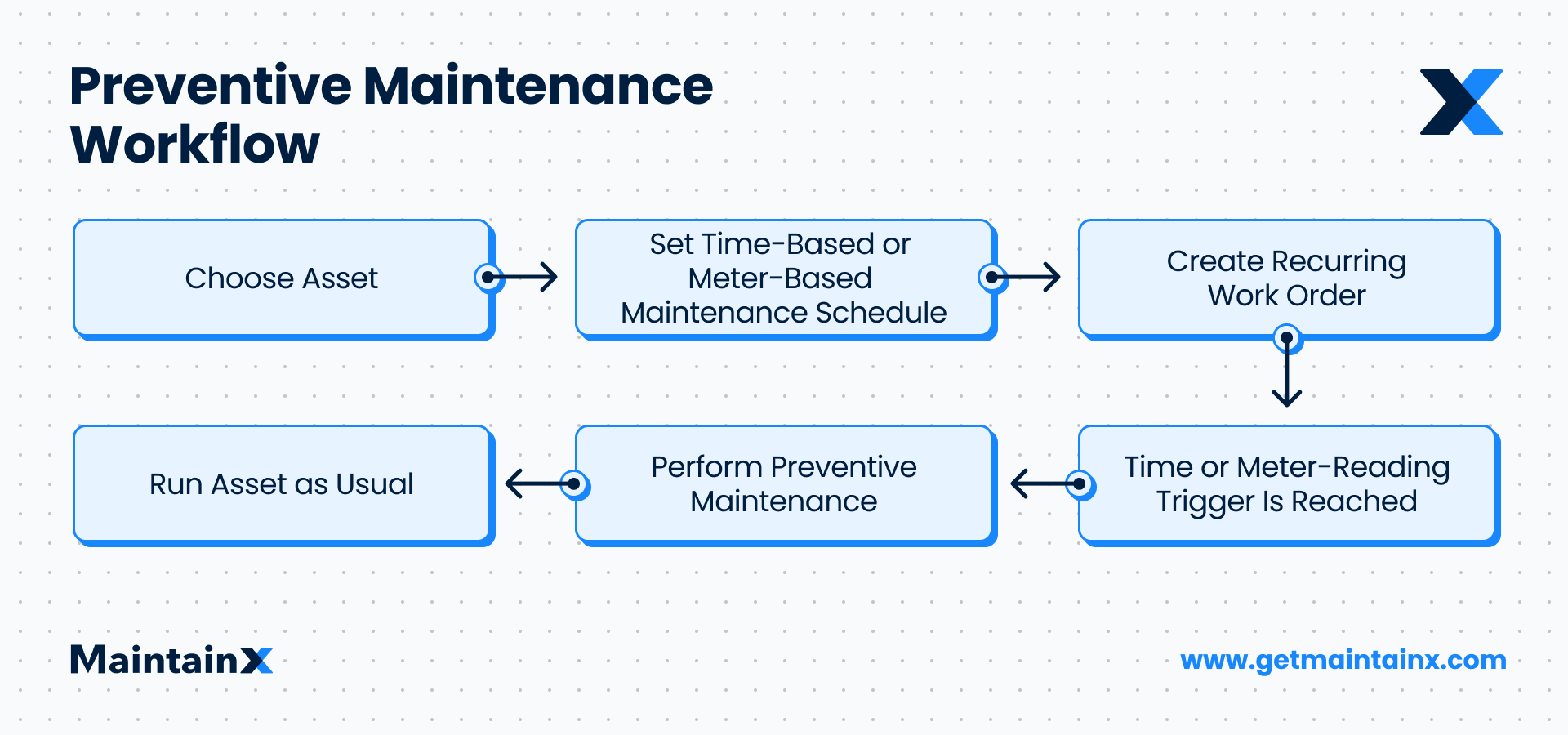
Breakdown maintenance, also referred to as corrective maintenance, is a strategy that performs maintenance tasks only after an asset fails. Maintenance tasks are only performed when they become urgent. For example, repairing or replacing a water heater after it has broken down.
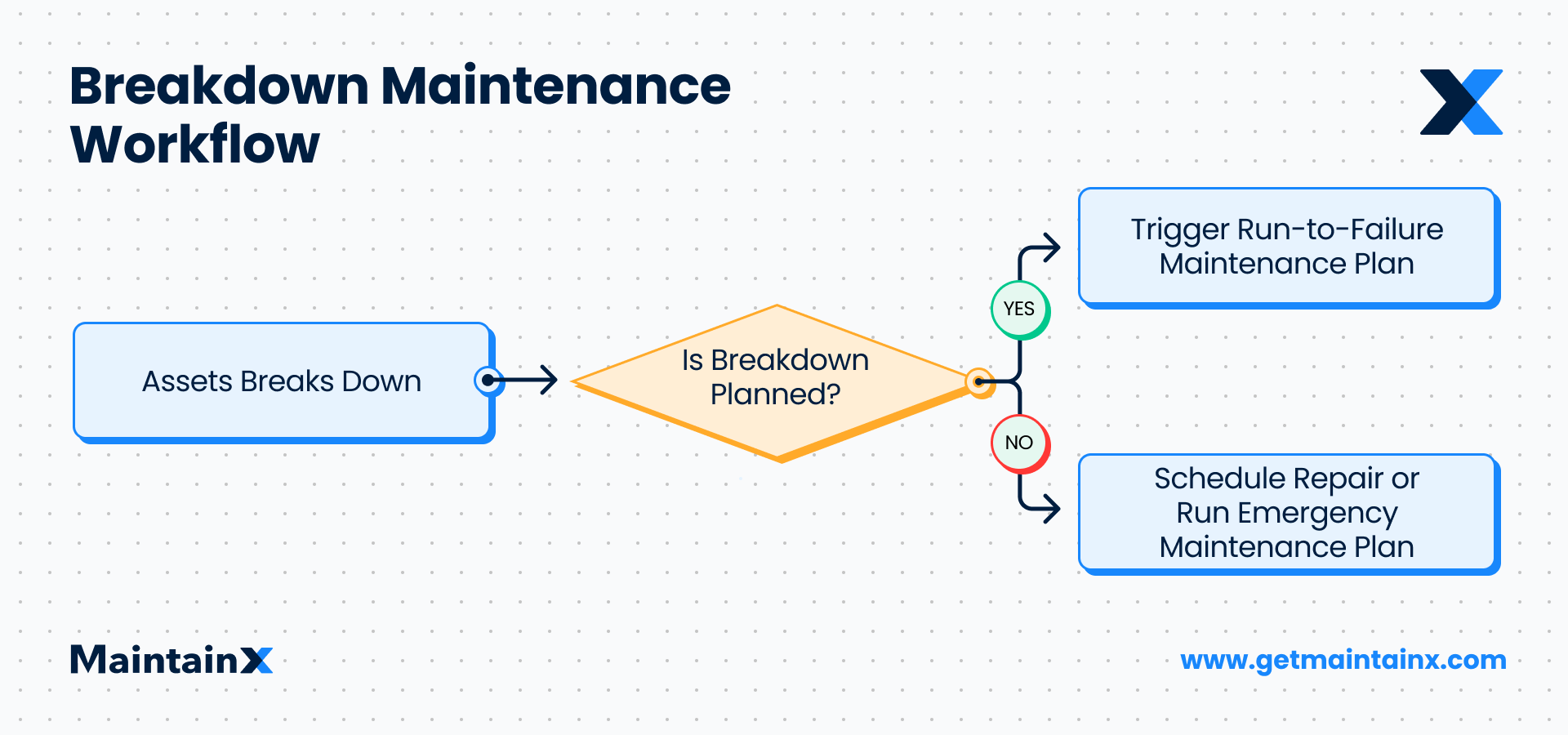
Types of Preventive Maintenance
Preventive maintenance involves identifying triggers that indicate potential equipment failure. There are five different types of preventive maintenance, which include:
Risk-Based Maintenance (RBM)
RBM refers to maintenance tasks that are performed depending on the level of risk an asset poses in the event of failure. The higher the risk, the more maintenance efforts should be directed toward that asset. Risk is calculated by looking at the likelihood of failure and the consequences of said failures. Crucial assets are given high priority when it comes to maintenance.
Failure-Finding Maintenance
This type of preventive maintenance focuses on detecting potential hidden failures of assets that perform protective functions. Take trip transmitters and safety valves, for example. Since these mechanisms only function when another asset has failed, it’s difficult to know whether they are still functional under normal conditions. Organizations typically conduct failure-finding maintenance at fixed intervals.
Time-Based Maintenance (TBM)
TBM refers to maintenance tasks that are performed at fixed intervals regardless of the asset’s condition. Also called scheduled maintenance, the principle argues that failure is usually age-related and you can determine a clear service life. The purpose of TBM is to protect business operations against the failure of an asset’s wearing parts. However, research studies conducted by the airline industry indicate that 70 to 90 percent of failure modes are not age-related. Alternatively, the occurrence of most failure modes is “random.” Later research by the United States Navy and others found very similar results.
Condition-Based Maintenance (CBM)
CBM focuses on a piece of equipment that is in the process of failing or indicating an impending failure. The goal is to prevent complete failure and avoid consequences. The strategy requires early detection of problems so that there’s enough time to perform maintenance before functional failure occurs. This allows teams time to organize resources needed for maintenance tasks.
Predictive Maintenance (PdM)
PdM is a more advanced form of CBM that uses process parameters to determine whether an asset is headed towards failure. PdM relies heavily on sensors and the Internet of Things (IoT) to monitor the performance of an asset and indicates declining performance. PdM allows technicians to undertake maintenance tasks early enough to restore an asset to optimal performance.
The different types of preventive maintenance strategies all hold the same goal: perform maintenance tasks before failure occurs.
Types of Breakdown Maintenance
Breakdown maintenance is also referred to as run-to-failure maintenance. As the name suggests, it involves performing maintenance tasks after an asset has failed. It’s most often used when preventing failure is impossible or not economically feasible. There are two types of breakdown maintenance:
Planned Breakdown Maintenance
In this instance, an organization anticipates a specific type of equipment malfunction in the near future. However, since the issue will neither disrupt productivity nor pose a safety threat, management decides to run the equipment to failure.
Unplanned Breakdown Maintenance
Every facility on the planet is familiar with unplanned downtime. Unfortunately, equipment sometimes fails at inconvenient, unexpected, and costly times. Most facilities budget for unexpected maintenance expenses since all machinery is fallible.
It’s worth mentioning that breakdown maintenance is often confused with corrective maintenance. Though the terms appear similar, they aren’t the same.
Types of Corrective Maintenance
Corrective maintenance is the result of unexpectedly finding a part/equipment issue while fulfilling an unrelated work order. For example, say a technician identifies a failing blower motor on an HVAC unit while changing an air filter. He or she would schedule corrective maintenance on the motor for a future date. Additionally, corrective maintenance can be divided into two categories: Deferred corrective maintenance and emergency maintenance.
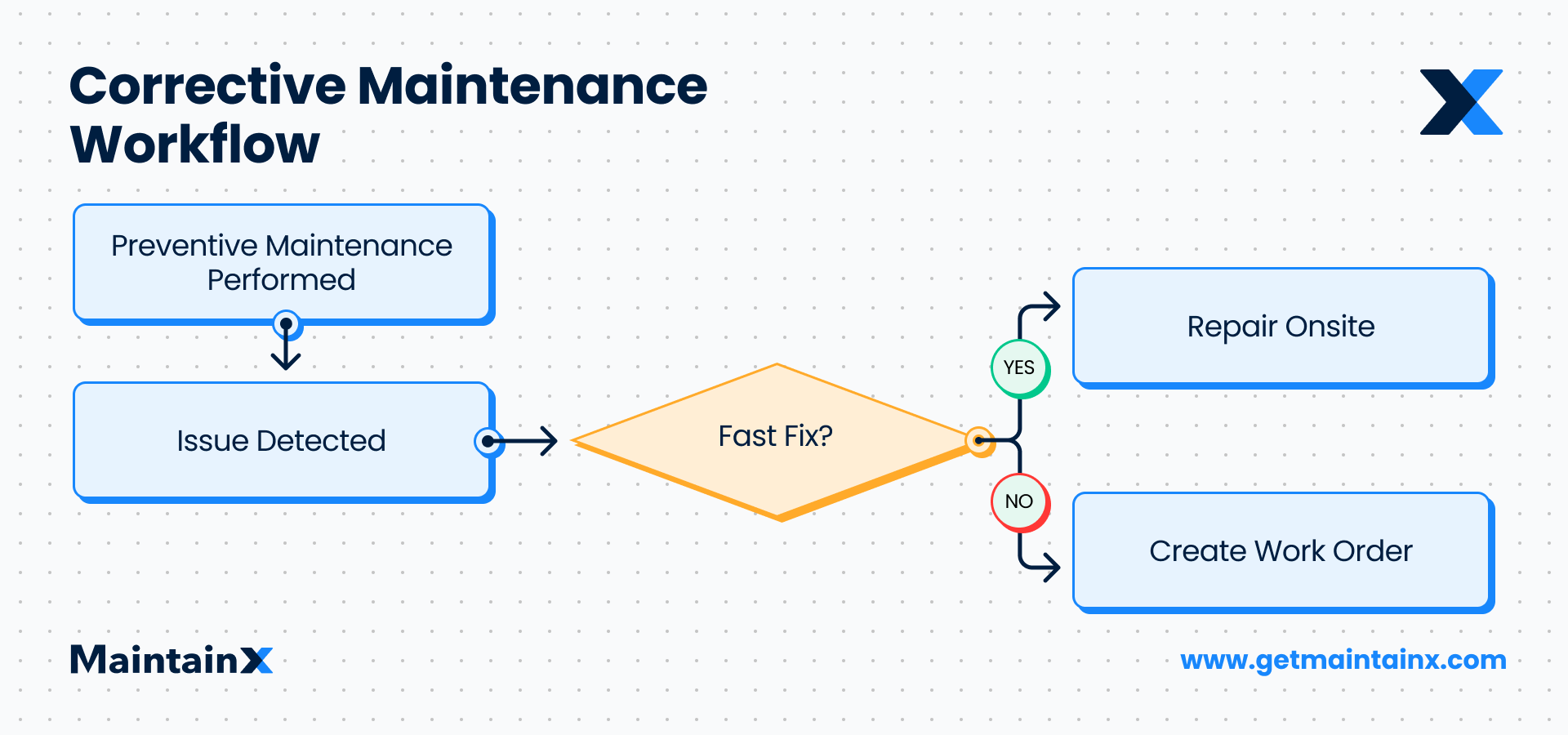
Deferred Corrective Maintenance
When resources aren’t immediately available to fix breakdowns tasks are often deferred to a later date when manpower, supplies, and finances are readily available. Thus, deferred maintenance tasks are planned and scheduled after failure has occurred.
Emergency Maintenance (EM)
Emergency maintenance refers to urgent maintenance tasks that cannot be scheduled for later. For example, fixing a broken water valve. The longer an asset is unattended is left unattended, the more r business operations are affected.
Corrective maintenance is best suited to assets that are not critical to business operations and should be used minimally. As reported by Buildings, corrective maintenance could cost an organization 10 times more than it would spend on preventive maintenance.
Now, back to preventive maintenance vs breakdown maintenance:
Preventive Maintenance Example
Here’s an example of preventive maintenance:
The aviation industry has, over the years, improved its preventive maintenance systems. There are maintenance requirements that have to be met before an aircraft is licensed to fly. Aircraft can be grounded for faulty systems. For instance, the Boeing 737 has been grounded for over a year for its defective safety system.
Because air accidents are always fatal, maintenance tasks cannot wait until an aircraft breaks down. Equipment failure must be avoided. The industry’s robust preventive maintenance strategy has drastically reduced the number of accidents over the years.
Breakdown Maintenance Examples
Planned breakdown maintenance is most often used on inexpensive and nonessential equipment parts. As long as breakdowns don’t compromise health and safety, organizations are free to consciously choose run-to-failure.
The following situations are ideal for breakdown maintenance:
- Short-Life Assets (e.g. batteries, high-flow pumps)
- Non-Critical Equipment (e.g. hand tools)
- Unrepairable Machinery (i.e. not designed for repairs)
- Inexpensive/Disposable Items (e.g. light bulbs)
Here’s a common breakdown maintenance scenario that takes place outside of maintenance facilities. Cyclists in the Tour de France replace flat tires mid-ride or switch to replacement bikes, as needed. They’ve perfected their breakdown maintenance routines to 20 seconds flat (no pun intended). In other words, flat tires are random occurrences that require emergency maintenance; preventive maintenance would be a waste of time.
Preventive Maintenance vs. Breakdown Maintenance Comparison Chart
Understanding Maintenance Workflows
Both preventive maintenance and breakdown maintenance strategies are useful for different reasons. For this reason, organizations should never choose between preventive maintenance vs. breakdown maintenance. Critical assets require a systematic PM approach to extend their lifespans and maintain optimal performance levels.
Alternatively, breakdown maintenance is handy for noncritical assets that don’t majorly impact production quality, worker safety, and extraneous costs. Maintenance management teams should strive to find the ideal balance between the two approaches. What works best for one organization may not be ideal for another.
MaintainX: Reenvisioning How Maintenance Works
MaintainX is a cloud-based CMMS system designed with convenience, affordability, and security in mind. Users can sign-up, log in, and begin creating worfklows and WOs immediately from their desktop or mobile devices.
See MaintainX in action