What is Fault Tree Analysis?
Fault tree analysis (FTA) is a systematic, graphical approach that identifies the primary causes of operational and maintenance (O&M) issues. It’s a deductive analysis tool that begins with a general conclusion before working backward to identify potential causes. Maintenance leaders complete this problem-solving exercise using visual representations of cause and effect known as fault tree diagrams.
In FTA, the undesired event, also known as the "top event," is placed at the top of the fault tree diagram. The top event represents the specific outcome or failure that is of concern. The event is then analyzed by breaking it down into its contributing causes, which are represented top-down as branches in the tree structure.
Operational managers, maintenance directors, and reliability engineers use fault tree analysis to identify potential causes of equipment failures before actual breakdowns occur. FTA improves system reliability, enhances system safety, and reduces extraneous costs associated with equipment downtime.
Bell Laboratories first developed the deductive process during the 1960s. The company wanted a reliable method for visually identifying human errors that resulted in equipment failure. Since then, maintenance teams worldwide have embraced FTA to uncover the real causes of asset and system failures.
Components of Fault Tree Analysis
Fault trees help organizational leaders determine the root causes of equipment failure events. The process enhances asset reliability, improves safety, and increases customer satisfaction. The three components of FTA include:
1. Fault Tree Diagram
This flowchart provides a visual framework of events proceeding equipment breakdowns. Organizations draw a series of logical deductions starting with the asset failure and then trace back to the root cause.
2. The Events
Events can refer to the common causes of failure, contributors, or failure itself. They include everything that could have or has happened in the chain of actions leading to the breakdown. Events can either be input (i.e., lead to other occurrences) or output (i.e., result from other circumstances).
3. Logic Gates
Logic gates use a Boolean “and/ or” sequence to connect related events. Two input events that lead to an output event are connected using an “and” gate, while single input events that lead to an output event connect using an “or” gate. For instance, a flawed wiring system and a burnt-out light bulb connect with an “and” gate. Alternatively, if only the bulb was bad, an “or” gate is appropriate.
Fault Tree Analysis Example
While FTA follows a standard process, it can range from simple to complex depending on its circumstances. Here’s a simple example:
A mixer at a production facility stops working; the maintenance team initiates FTA to identify the cause of potential failure. A fault tree diagram reveals the issue could be the result of either mechanical or electrical failure. Further investigations reveal the cause was an electrical failure because of a high current draw caused by an overload.
Below is an example of a blank fault tree diagram:
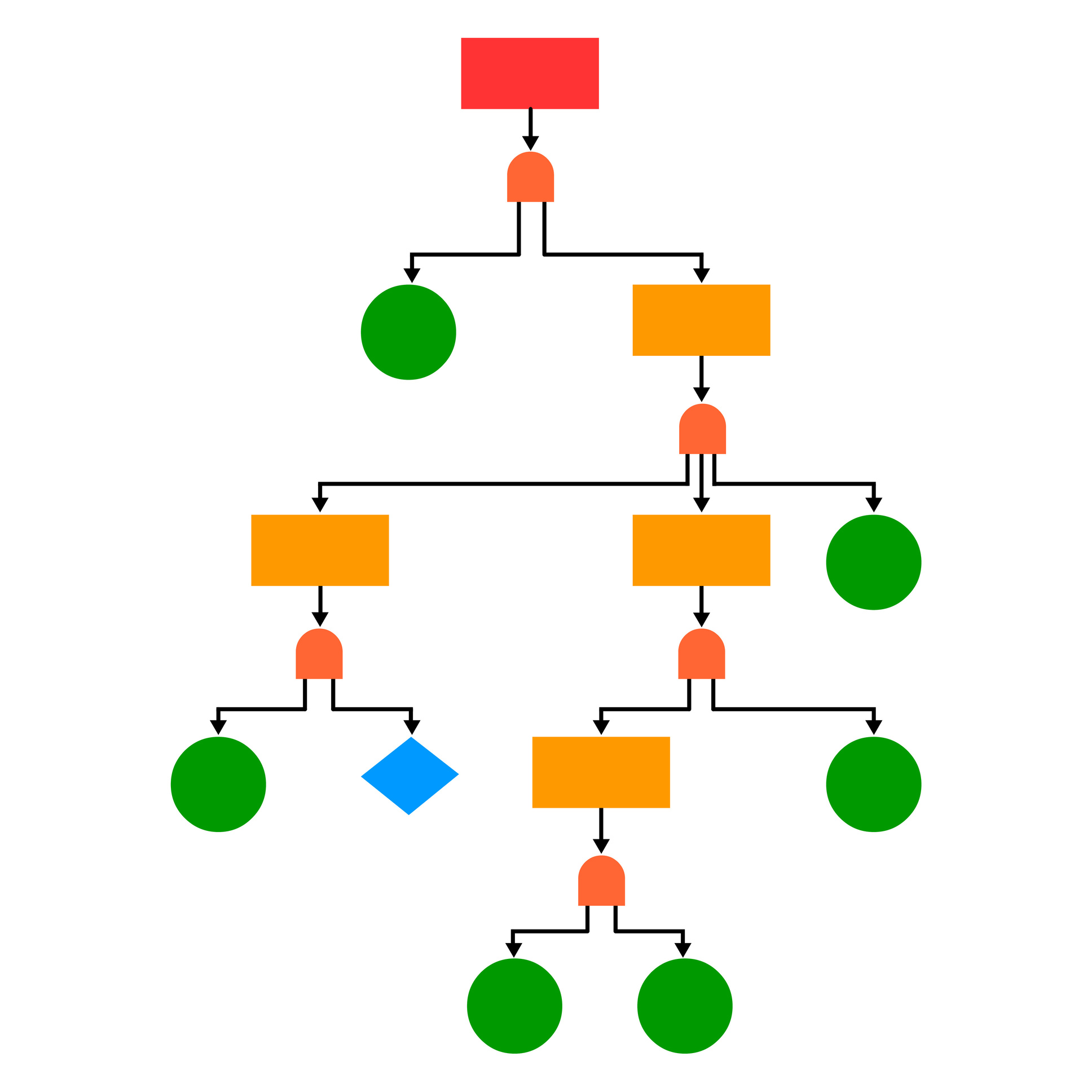
To begin, write the initial problem in the top rectangle before working through the various events that could have led to it in the subsequent boxes.
Situations for Fault Tree Analysis
Maintenance leaders use fault tree analysis in a variety of situations, including:
- Analyzing safety concerns in a facility
- Designing and installing new systems
- Making modifications to existing systems
- Implementing existing system designs in a new environment
- Investigating regulatory concerns, such as compliance with Americans with Disabilities Act (ADA) regulations
- Optimizing maintenance costs within an organization
The industries that most commonly use FTA include aviation, transportation, mining, nuclear, software, manufacturing, and chemical production.
The Benefits of FTA
Key benefits that organizations stand to gain from using FTA include:
- Considers human errors: Unlike other failure-analysis tools, fault tree analysis factors in human error. This inclusion sheds light on an often overlooked downtime component: standard operating procedures (SOPs) that are not followed.
- Analyzes each fault independently: FTA focuses on one weakness at a time. This strategy helps to solve problems in a much more organized manner.
- Highlights essential elements that contribute to system failures: Most approaches look to solve the problem and get the systems back up as soon as possible. FTA, on the other hand, looks to go deeper to investigate how each element contributed to the failure.
Despite the advantages of fault tree analysis, the problem-solving methodology isn’t ideal for every team or situation. Situations that are either caused by several corresponding events or related to time delays may not be conducive to fault tree diagramming. Additionally, some organizations may not have team members who have received training in using logic gates and events.
How to do Fault Tree Analysis
Fault tree analysis follows six steps:
- Identify the Failure: Identifying the exact failure is the first task in FTA. To do so, organizations need a precise definition of the problem to narrow down their investigations.
- Understand the System: After identifying the problem, it’s essential to collect as much information as possible. This process includes understanding how the system and its components work; whether the failure is mechanical, electrical, or software-related; requirements for changing the system; and system engineers’ input. This helps to determine how the system was functioning before the failure occurred.
- List Potential Causes of the Failure: At this stage, all potential causes of the failure should be listed, and the probability of each causing the failure estimated.
- Draw the Fault Tree Diagram: Starting with the failure identified in step 1, organizations should create a fault tree diagram unique to the problem. They can then map out the potential causes of the failure and use the logic gates to connect them until they reach their root cause.
- Perform Risk Assessment: Managers should assign each event an individual risk and probability level. Data collection and projection can make this step less complicated. It’s also vital to involve system engineers and operators in this step as they know the systems best.
- Mitigate the Risk: After the root cause of the failure is identified, sustainable steps should be taken to mitigate the risk of future occurrences.
Use a CMMS With FTA
FTA provides organizations with easy, scalable, and sustainable ways to deal with asset and system failures. When used effectively, it’s a powerful tool that can help an organization optimize its maintenance costs.
However, FTA will only be effective if the organization can collect accurate data and make smart predictions on a failure’s potential causes. This objective requires organizations to invest adequate resources in implementing fault tree analysis. A user-friendly Computerized Maintenance Management System (CMMS) can streamline the data collection process part of Fault-Tree Analysis.
Ready to digitize your maintenance program with MaintainX? It’s free.
Fault Tree Analysis FAQs
When is Fault Tree Analysis Used?
Fault Tree Analysis is widely used in various industries, including engineering, aerospace, nuclear power, chemical processing, and healthcare, to assess and mitigate risks associated with complex systems. It helps in identifying critical failure modes, prioritizing risk management efforts, and ensuring the safety and reliability of system analysis and processes. This helps to reduce failure rates and increase maintainability.
There are also certain scenarios in which businesses may choose to use failure mode and effects analysis instead. Fault Tree Analysis (FTA) and Failure Modes and Effects Analysis (FMEA) are both powerful tools used for system level risk assessment and management in different contexts. The choice between FTA and FMEA depends on the specific needs, goals, and characteristics of the system or process being analyzed.
What Are The Basic Elements of a Fault Tree?
The basic elements (or gate symbols) of a Fault Tree analysis method include:
1. Top event (undesired event).
Symbol: • (Dot in a circle)
2. Logic gates (AND gates, OR gates, and NOT gates)
Symbol: + (Plus sign)
3. Basic events (individual events or failures contributing to the top event)
Symbol: ¬ (Negation symbol)
These elements work together to visually represent the potential causes and relationships leading to the undesired event (top event) in a systematic and structured manner. It uses Boolean logic to combine a series of lower-level events. By analyzing the FTA diagram, one can identify the critical paths and combinations of intermediate events that can lead to the top event, allowing for targeted risk assessment and mitigation.
What Are The Limitations of Fault Tree Analysis?
Some limitations of FTA event tree analysis include:
Requires accurate data for event or failure probabilities, which may not always be available. The trickiest part of the whole thing is getting the sequence of failure dependencies worked out in the first place.
FTA often assumes events are independent, which may not always be the case in complex systems.
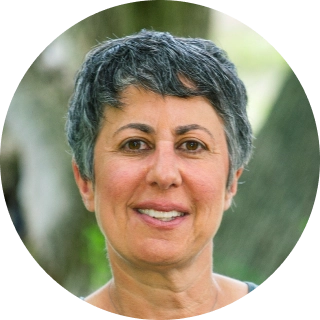
Caroline Eisner
Caroline Eisner is a writer and editor with experience across the profit and nonprofit sectors, government, education, and financial organizations. She has held leadership positions in K16 institutions and has led large-scale digital projects, interactive websites, and a business writing consultancy.
See MaintainX in action