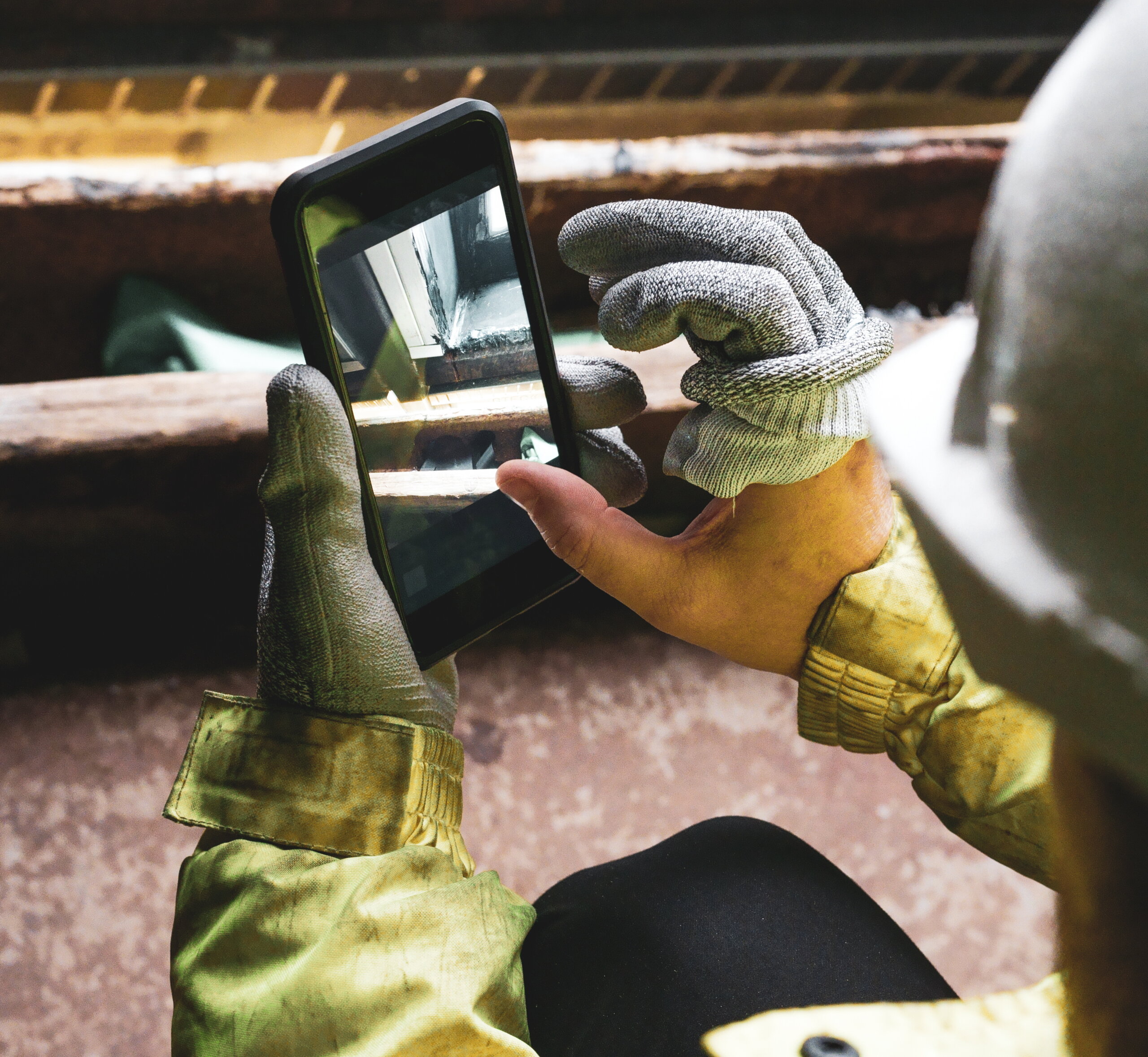
Field maintenance is an essential component of maintenance and repair that is performed on-site. Statistics show that there are more than 20 million field technicians worldwide.
This article covers different ways to improve field maintenance that will help you improve efficiency, performance, and asset life.
5 Ways to Improve Your Field Maintenance
1. Standardize Maintenance Workflows
Standardization is the best way to improve field maintenance. Developing common maintenance workflows and processes will make your technicians efficient, and it will help them save time.
Standardizing has several benefits:
- Improves productivity
- Increases clarity
- Improves quality
- Increases employee satisfaction
- Decreases guesswork and mistakes
Organizing maintenance around workflows and Standard Operating Procedures will make it easier for employees and technicians to optimize their tasks. They will know exactly when a technician or equipment will reach the site and what route it will take. They will know the next step they have to take once the equipment and technician reach the site. And so on.
“If managed properly, standardized work establishes a relationship between people and work processes which can enhance ownership and pride in the quality of work performance. The result is high morale and productivity.”
Walter McIntyre
So what you need to do is standardize recurring and routine workflows and processes by defining clear rules. This is the first step towards field maintenance improvement. Think about what type of planned maintenance will work for your equipment: preventive maintenance, predictive maintenance, etc.
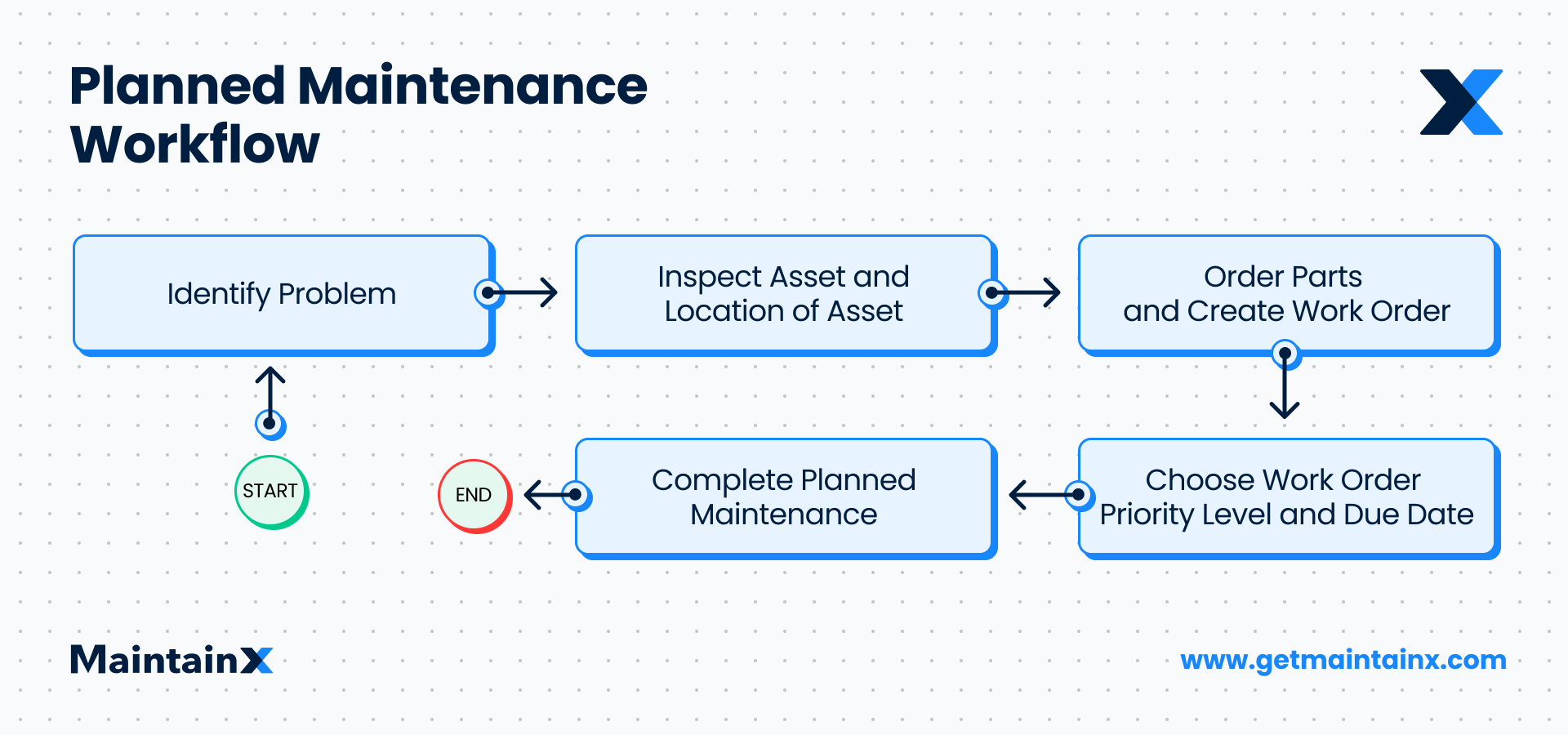
2. Add Manufacturer’s Manuals
Field workers deal with different equipment and tools. To make your technician’s life easier in the field and to improve field maintenance, provide them with manufacturer’s manuals.
Statistics show that manuals are available to field workers less than 50% of the time, and it is one of the top challenges that technicians face in the field.
Whether manufacturing turbines or toys, the core function of the maintenance team stays the same: keep the plant, its systems and its assets running smoothly, all the while minimizing and correcting any issues that arise….As plants being increasingly digitized and connected, software solutions certainly have a role to play. Consider how a dedicated workflow solution or knowledge transfer system can reduce workflow disruptions, giving back critical time to the maintenance team.
Industry Today
Manufacturer and service manuals are something that technicians should have access to all the time. They should be able to access any manual 24/7 digitally. This means you need to link or upload the manuals to your CMMS to make sure they are accessible to workers all the time. Even if it’s not a digital copy, you should still upload the paper version (as an image or PDF) to the field maintenance tool.
Use a CMMS software like MaintainX that lets you attach and share manuals to standard operating procedures. This way, your technicians will be able to access manuals when they’re in the field.
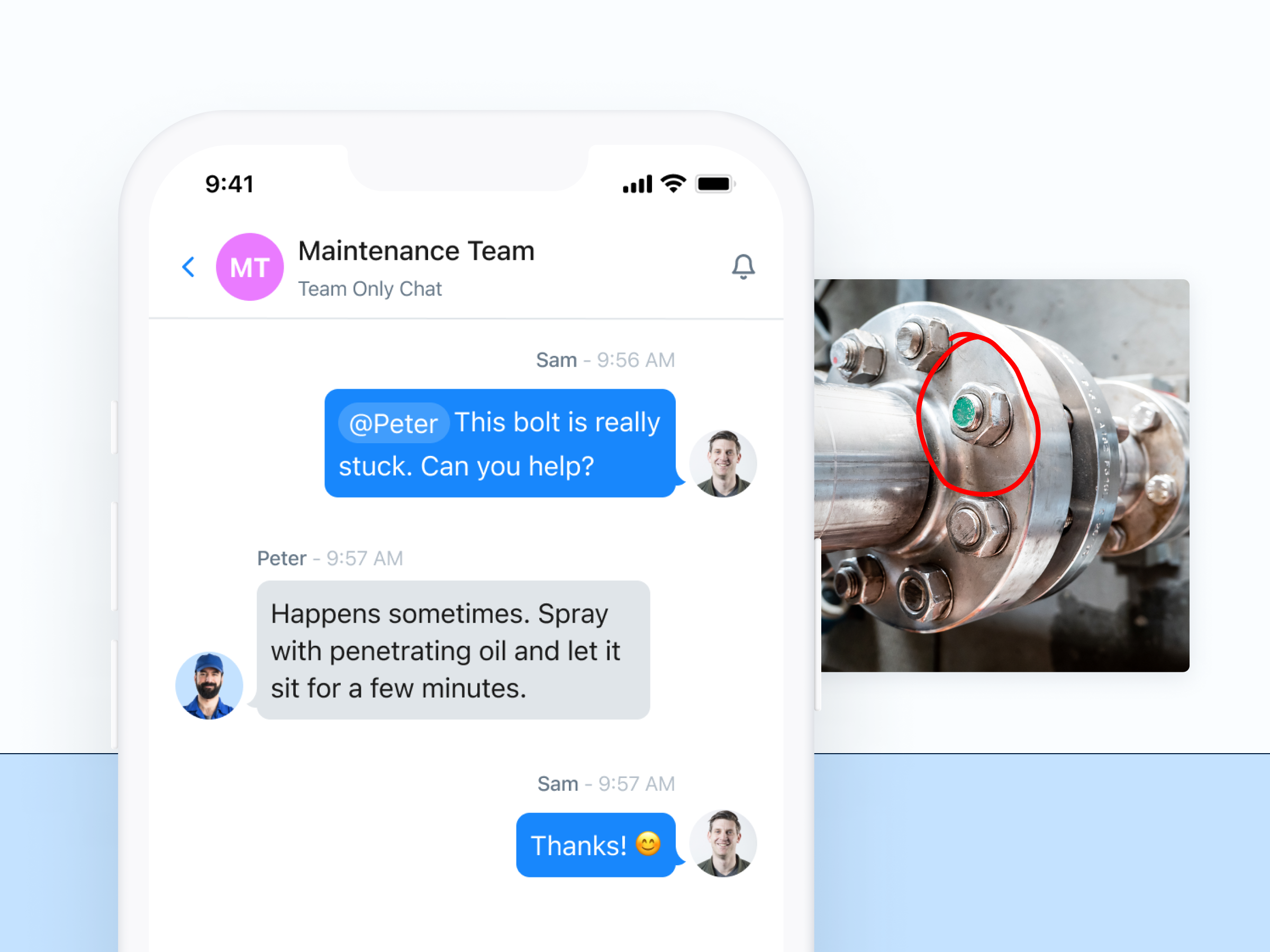
3. Communicate and Collaborate
Collaboration improves field maintenance. Teamwork gets the work done. Technicians in the field should be able to communicate on the go with their peers back in the office and other technicians out in the field as well.
MaintainX, for example, offers powerful collaboration and communication features that lets your workers send unlimited messages and photos to collaborate on the go. The CMMS organizes messages by teams and users to make finding and sorting conversations easy.
Let’s admit it, your technicians don’t just need to communicate. They need access to files, data, photos, and other material. The truth is you never know what they need in the field. Therefore, a communication tool with cloud storage is a must. Merely having a smartphone with traditional messaging apps just isn’t enough anymore.
The use of a sophisticated collaboration tool lets your workforce access the history of previous maintenance projects. Equipment history helps solve similar issues without wasting time.
4. Improve Response Time
Let’s admit it, nothing hurts field maintenance more than poor response time. If you’re interested in improving field maintenance, response time should be your top priority.
If you’re using field maintenance software, reducing response time will get easier. You can dispatch technicians based on their current location, skillset, availability, and expertise. This can only be done if you’re using sophisticated software that has all the information about your workers.
If the data isn’t updated in real-time, you won’t have information on the current status of a worker. And this is what hurts response time. When a worker finishes a job in the field, his status should be immediately updated in the software so the manager can assign him a new project accordingly.
The status of the workers should be automatically updated as soon as they mark a task complete in the software. With a robust CMMS, you will be able to monitor key performance indicators in real time. MTTR and Equipment Downtime statistics will improve with the right maintenance plan automated via your CMMS.
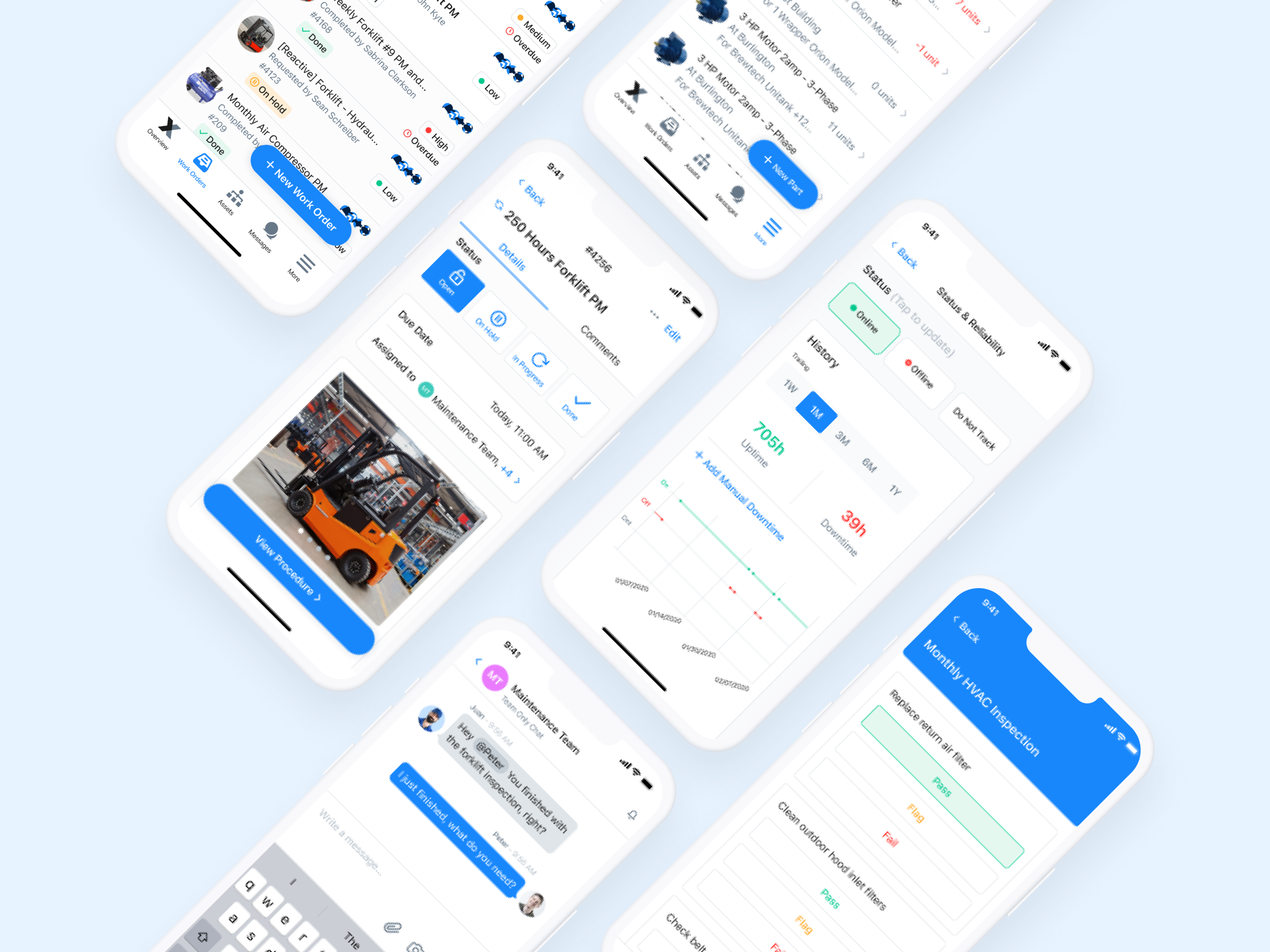
5. Use a CMMS
So, where should you begin?
Let’s start with your field maintenance software. MaintainX is based on real-time communication and enables you to organize work orders from one screen.
Maybe you’re already using field maintenance software. If your tool doesn’t offer you advanced features like communication and collaboration, workflow management, checklists, manual sharing, etc., you should think of changing it.
Once you’re using the right CMMS software, implement the approaches discussed in this post to see what works best for your workers.
FAQs
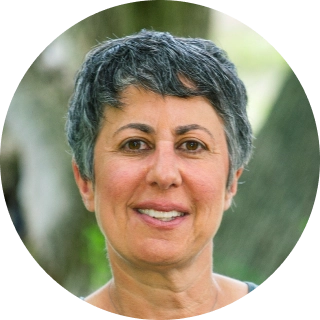
Caroline Eisner is a writer and editor with experience across the profit and nonprofit sectors, government, education, and financial organizations. She has held leadership positions in K16 institutions and has led large-scale digital projects, interactive websites, and a business writing consultancy.