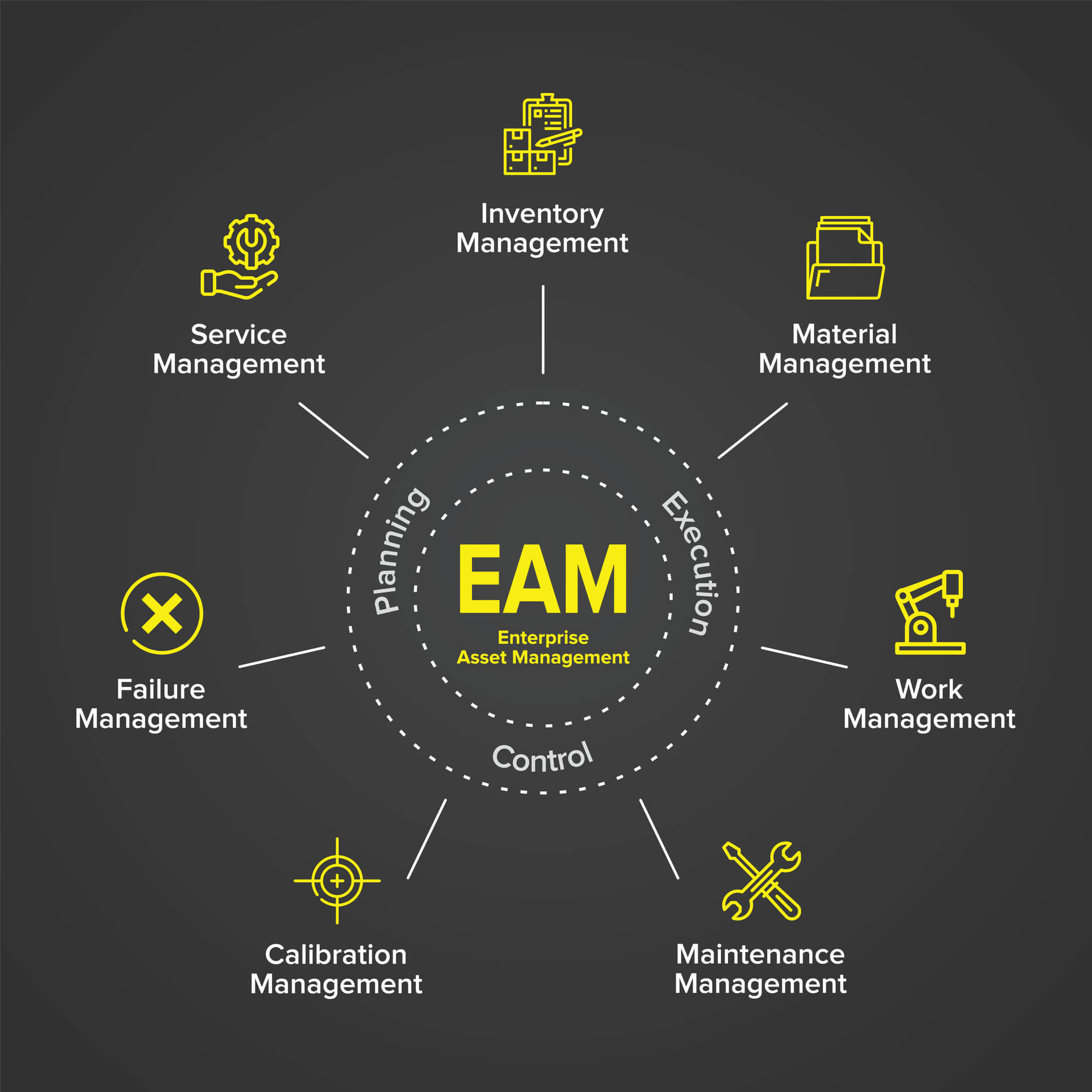
Enterprise asset management (EAM) is a suite of tools, software, processes, and services that provide businesses with an end-to-end view of their assets.
Offering far more than just asset performance monitoring, EAM draws on data from multiple areas of the organization. As such, owners and managers get a deeper understanding into:
- Operational costs through the entire asset lifecycle
- Equipment downtime and uptime trends
- Aggregated metrics from equipment telemetry and sensors
- Asset performance and productivity
- Purchasing, disposal, and other supply chain insights
- Spare parts usage and inventory management
- Planned production data vs. equipment utilization
- Upcoming preventive maintenance requirements
- Integrations with assets and other business units, such as HR and finance
An enterprise asset management system is a powerful tool. It collects information and data from many disparate sources and creates a centralized dashboard for all asset-related information.
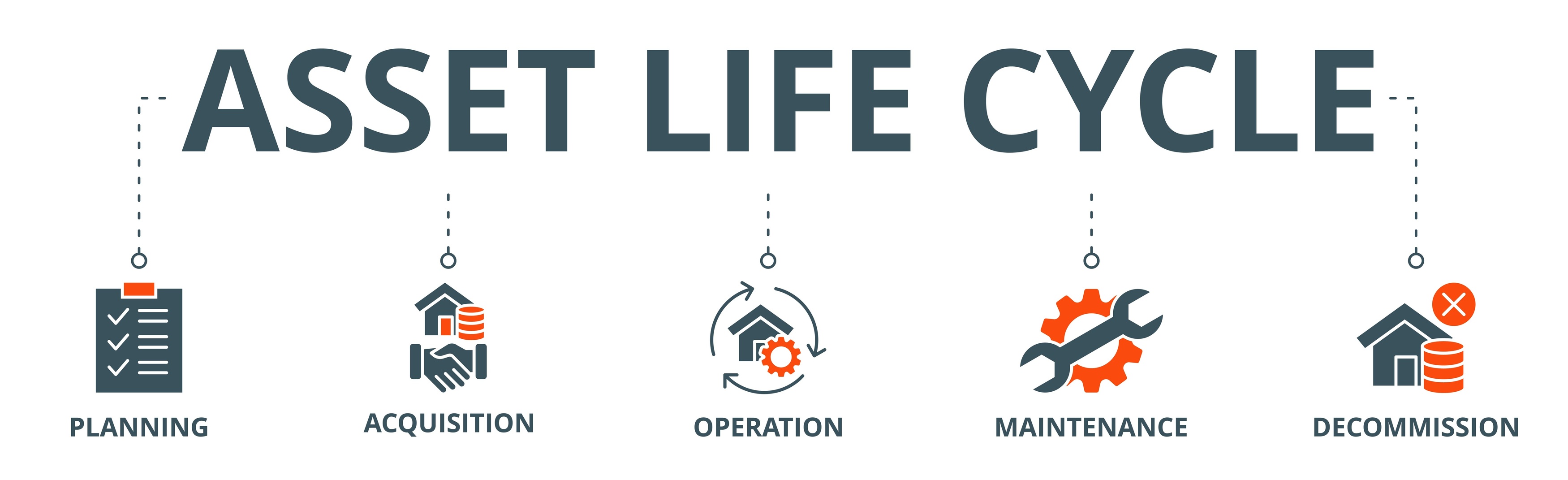
When businesses use EAM systems in conjunction with other software (such as ERP systems), they can strategically optimize their lean manufacturing operations for better productivity.
Where EAM Fits in Your Lean Manufacturing Business
Larger organizations typically use EAM systems with hundreds of different assets spread across large facilities, multiple factories, the country, or the world. In addition, businesses using EAM are generally at a level of maturity where productivity and efficiency are under the microscope. Running a large and complex company requires robust systems where disruptions, oversights, and production stoppages are never left to chance.
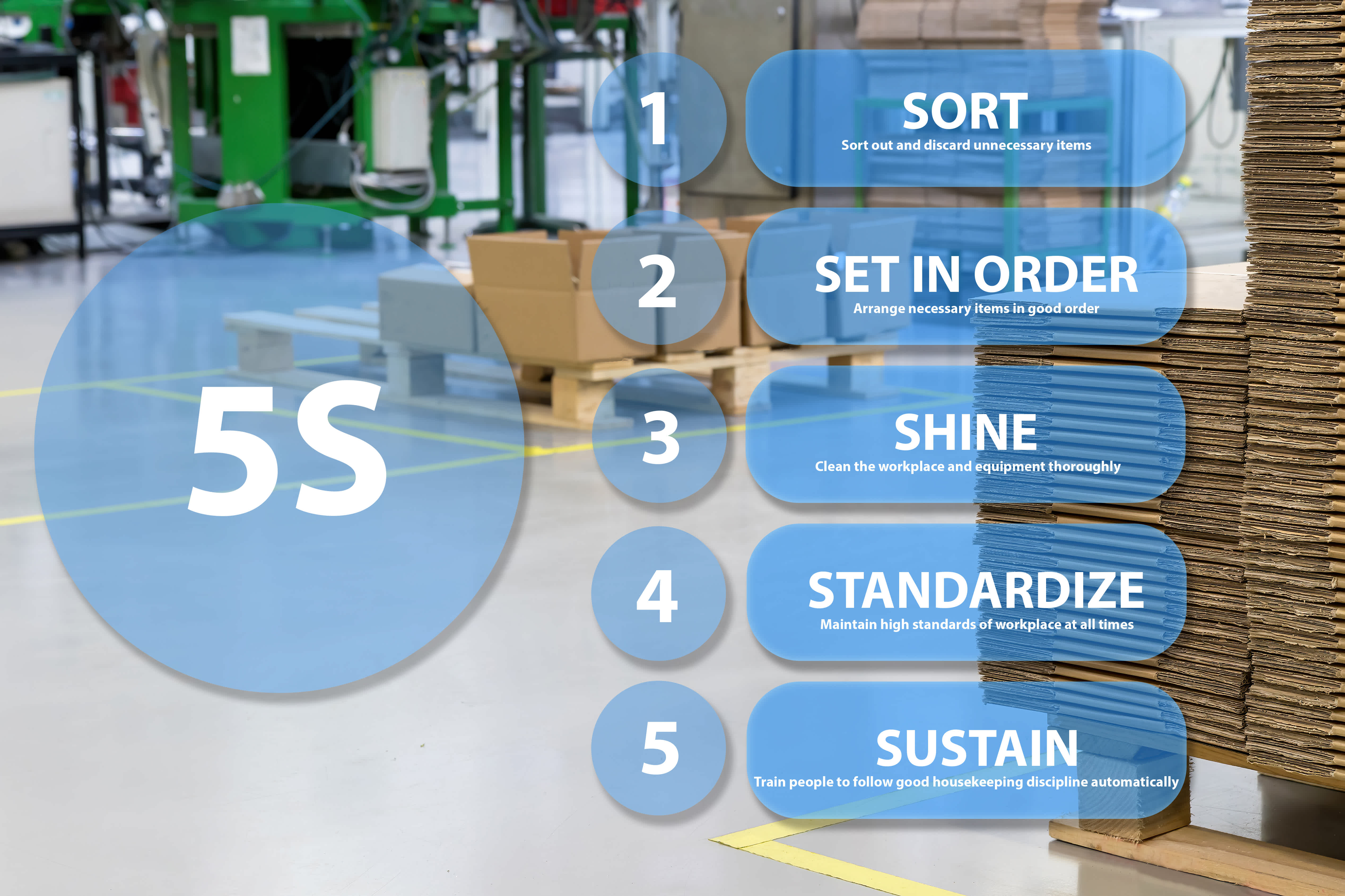
This focus on extracting the most value from each manufacturing process or asset–with the least possible waste–is also a core tenet of lean manufacturing methodology. There is a substantial overlap between the emphasis on continuous improvement encouraged by lean methodology and the emphasis on optimizing assets via holistic EAM.
“The possibility of achieving zero downtime increases by using lean manufacturing principles in conjunction with technologies that automate the management of assets, service, and equipment performance. Enterprise asset management (EAM) systems maximize the availability of and service performed on the physical or capital assets on which lean manufacturers depend.”
Reliable Plant
Established businesses need high-level visibility, comprehensive data, and consistent feedback loops to help them act on critical issues, such as:
- reducing maintenance costs
- keeping stocks of raw materials under control
- ensuring breakdowns have minimal impact on production targets
Weaving together real-time information from all areas of your organization is where EAM software can really shine, helping you progress in your lean journey.
The Benefits of EAM Software
Provides Visibility across Entire Asset Lifecycle
EAM software assists with managing each stage of the asset lifecycle, from planning to acquisition, utilization, and disposal. In addition, the software makes full use of the Industrial Internet of Things (IIoT). It can connect onboard sensors (such as a control module on a compressor) with expanded views of how that asset works with the other moving parts of the business. Predictive maintenance, for example, makes good sense here.
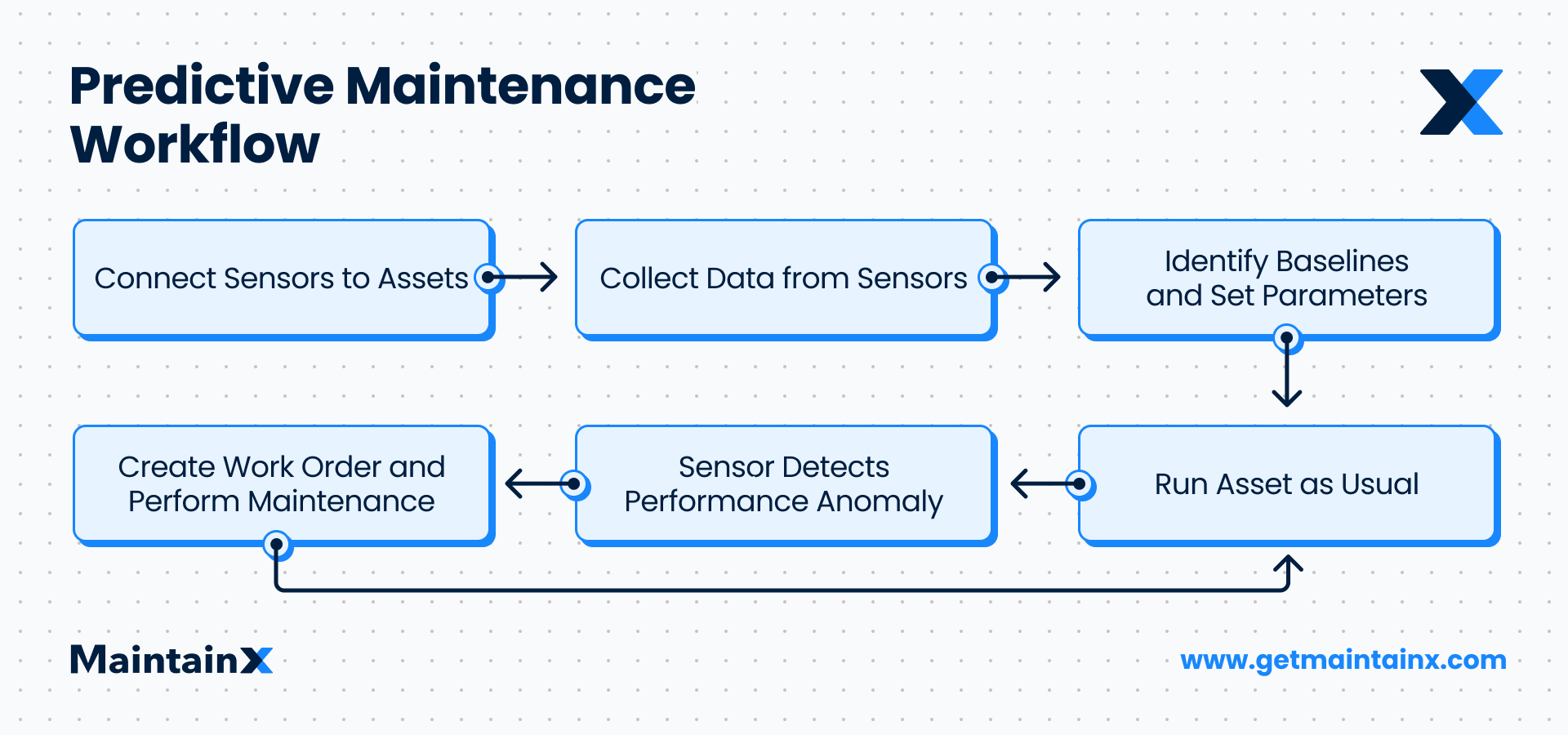
Helps Manage Overall Equipment Effectiveness (OEE)
Most maintenance strategies aim to maximize OEE by measuring and analyzing the productivity of assets. This ensures predictive maintenance processes keep machines and equipment working at full capacity. Total Productive Maintenance (TPM) takes this concept further, working to eliminate unplanned breakdowns.
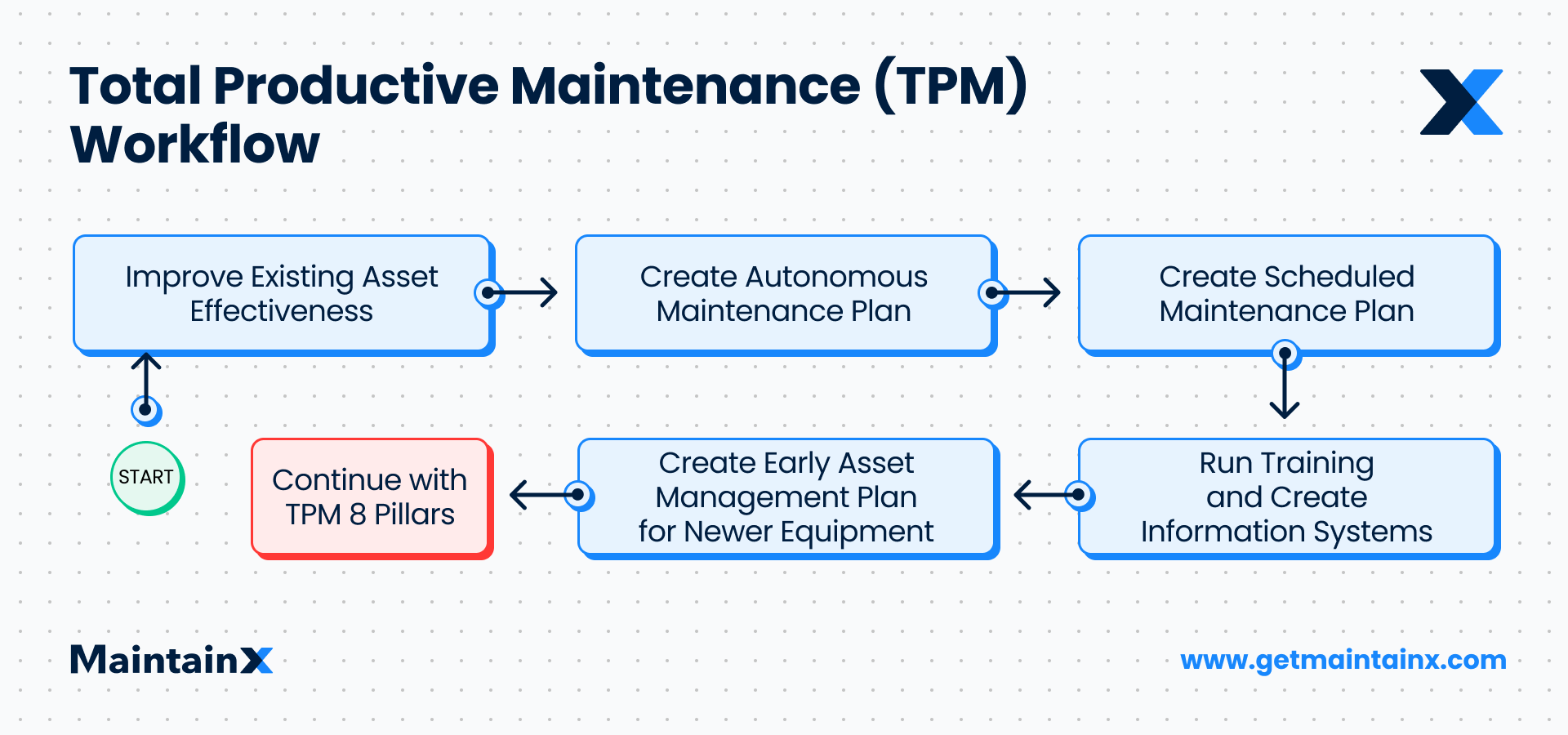
Ultimately, the goal of TPM is to bring OEE to 100%, meaning 100% equipment uptime and system availability. This goal becomes easier to achieve with real-time data, comprehensive reporting, and manufacturing analytics via a robust EAM like MaintainX.
Brings Together Many Data Sources
Integration with ERP systems like SAP or Microsoft Dynamics allows even deeper insights to be gleaned from your EAM. In addition, enterprise software providers typically provide detailed support and advice when you’re looking to integrate and automate several different systems. Individual tools are customized to function as one smooth asset management system.
“While lean principles have long been used in manufacturing to drive efficiency and reduce waste, adding digital technologies to lean can take an enterprise to a whole new frontier.”
Deloitte
Helps Identify Process Waste
Like the Lean Six Sigma approach, EAM clarifies areas where companies aren’t using assets to their full potential, thereby creating unnecessary waste. Not only does waste impact production efficiency, but it also negatively impacts sustainability and environmental goals, creates complexities in supply chain management, and can lead to poor team performance and missed productivity goals.
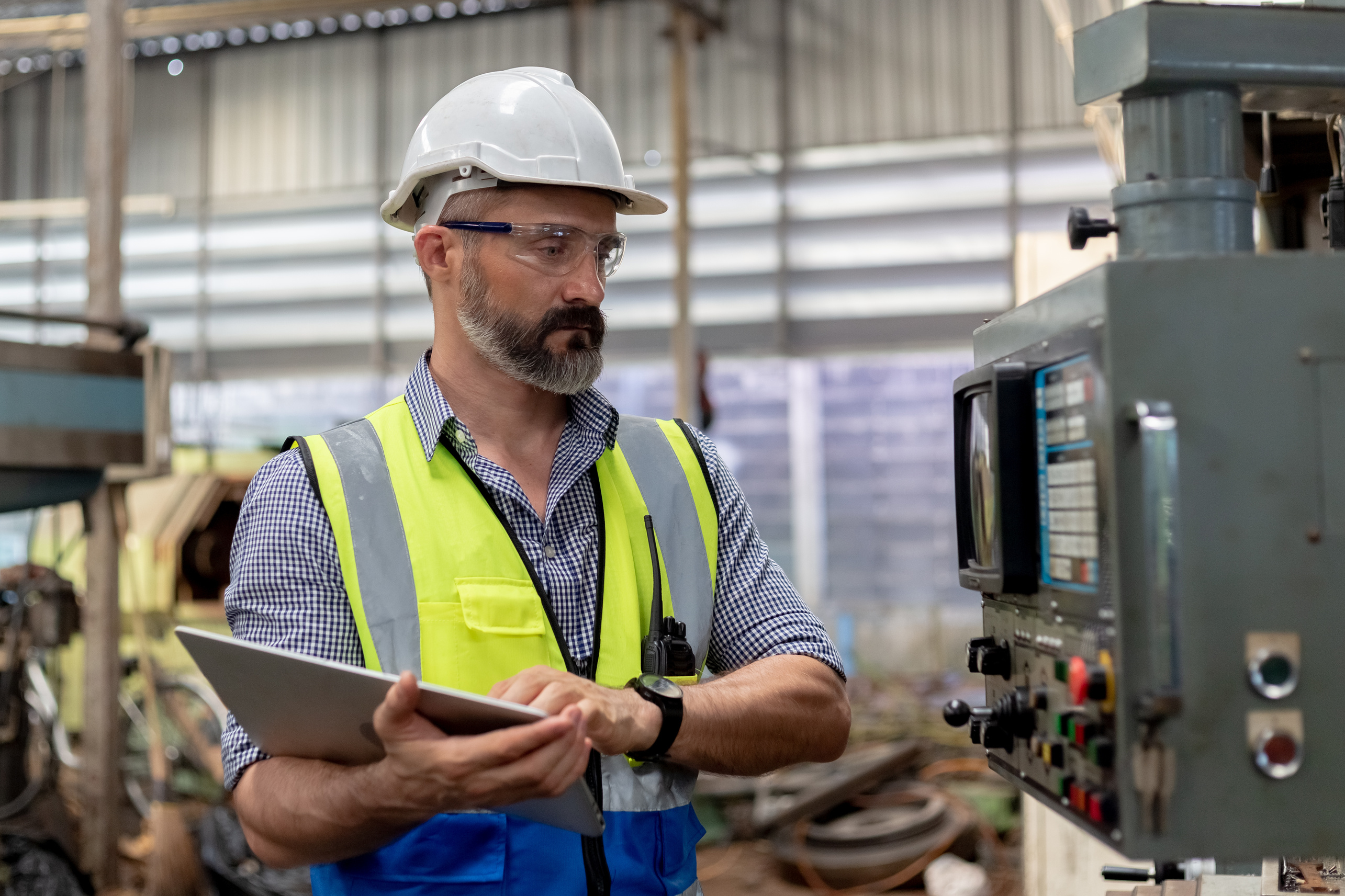
EAM and Lean Manufacturing: Two Approaches, One Goal
Both lean manufacturing methodologies and EAM platforms give businesses a better understanding of where waste and downtime exist in their current workflows.
And once you know where the waste is, you can get to work eliminating it!
An EAM/CMMS like MaintainX provides all the features–work order automation, real-time parts inventory management, QR and barcode scanning, global procedures library, checklists and filters for audits, in-app communication, and robust KPI and metrics reporting–to scale with your company as it grows and expands.
Ultimately, the tool that will give you greater visibility into the entire asset lifecycle is the one that you can best adapt to your business needs. Want to see how MaintainX can become part of your enterprise asset management toolbox? Book a live tour to find out more.
FAQs
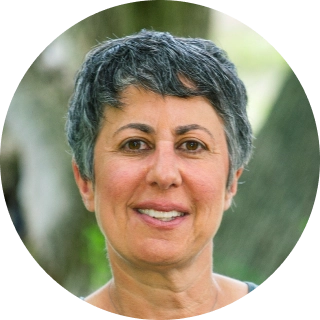
Caroline Eisner is a writer and editor with experience across the profit and nonprofit sectors, government, education, and financial organizations. She has held leadership positions in K16 institutions and has led large-scale digital projects, interactive websites, and a business writing consultancy.