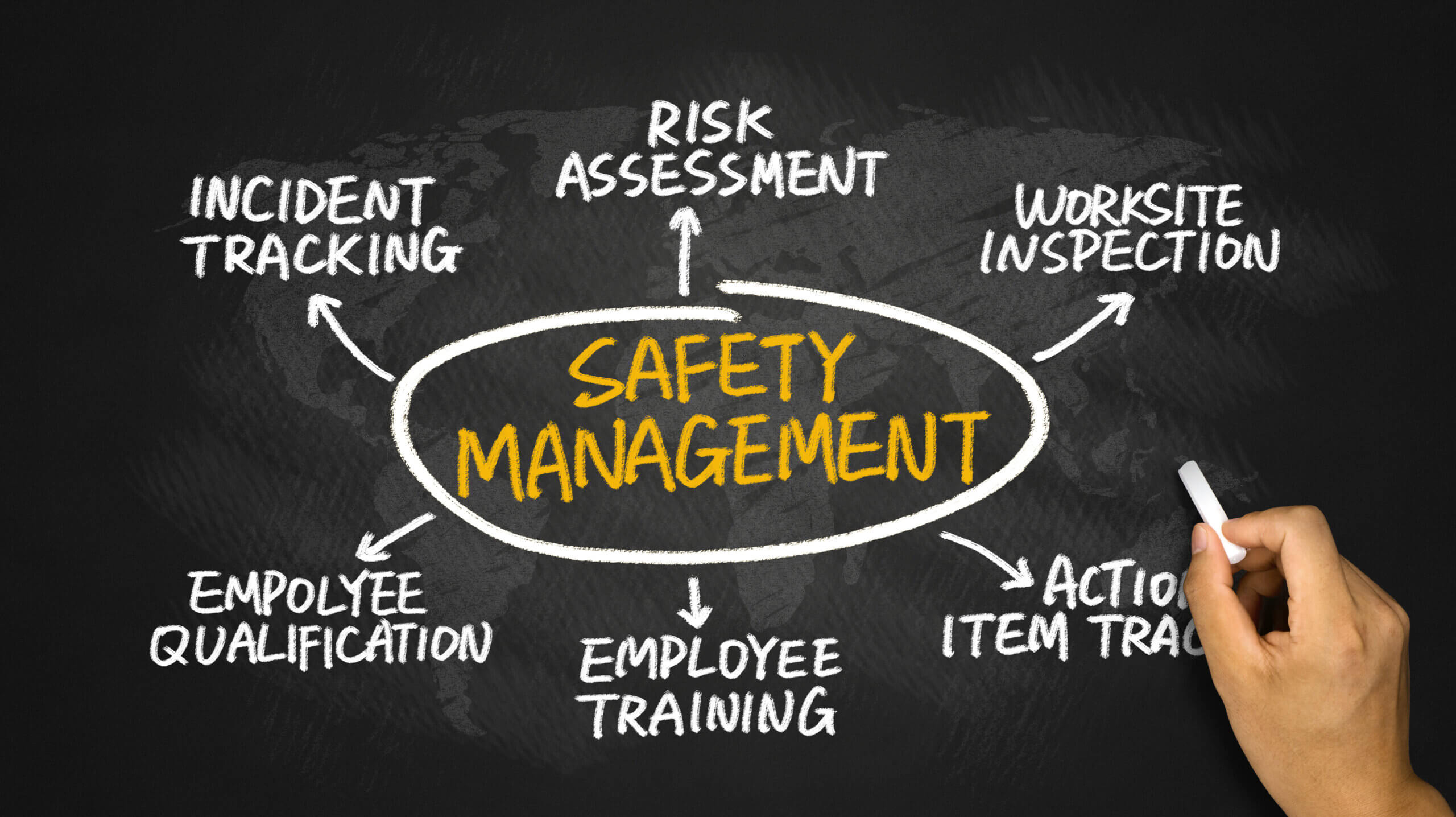
Keeping a maintenance team running smoothly means making adjustments. You may have set routines and standard operating procedures. But, you may notice something your team can do better. Continuous improvement is a key principle of a successful team. So, if there are any changes you’ve been mulling over or preparing for, today is an excellent time to implement them.
Plans to do better next time can often seem surface-level and pointless. But, if you are thinking of ways to get your team excited, optimistic, and eager to jump into new work, you could do much worse than creating a safety culture that engages your maintenance team.
To be sure, safety in maintenance is nothing new. Most teams will have their own safety programs in place, although in different ways. The key word here is “culture,” from emergency safety procedures to safety training for individual staff handling crucial assets.
How can you take things a step further with safety management? How do you make safety practices part of day-to-day work life? How do you ensure your team sees their safety not just as a matter of following rules, taking surveys, and ticking boxes but as part of what it means to do a good job?
“Someone who skips steps in a Lockout-Tagout procedure raises the likelihood of experiencing an injury. And workers who don’t support safety policies and procedures and even feel those steps get in the way of their work are less likely to follow them.”
Professional Safety Journal
Why Create a Culture of Safety?
Of course, you always want your employees to be safe. But outside of that, why make any effort to create a safety mindset for employees? After all, you could just hand out a list of safety rules and regulations to follow.
To understand why it’s essential, here are reasons to consider creating an effective safety culture in your team.
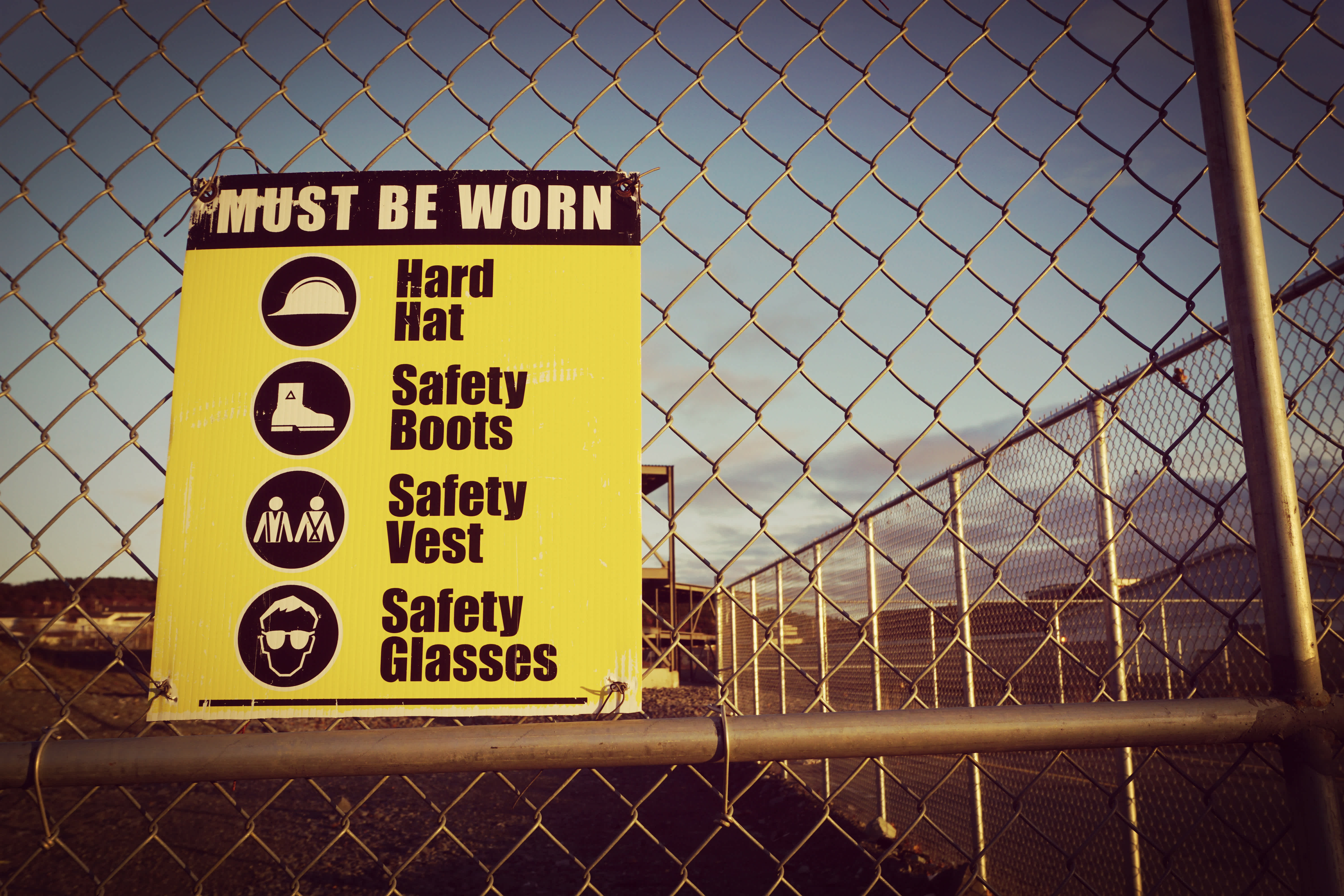
Defines What You Stand For
Contrary to the idea that safety is one of many company goals, your safety culture says a lot about the company as a whole. When you have a strong safety culture, you’re telling your employees that you care more than just the financial bottom line. You’re signaling to your workers that leadership cares about their well-being. You’re also telling customers that you are a workplace with serious values.
“Providing for employee safety and reasonable working conditions impacts market performance.”
Market Maven
Supports Regulatory Compliance
Whatever kind of teams you run, you likely need to comply with regulatory bodies. For example, the Occupational Safety and Health Administration (OSHA) has strong guidelines regarding workplace safety. Workers have a right to a safe work environment. A positive, proactive safety culture contributes to this. You’re more likely to reach your safety goals when employees think of safety policies as part of the culture of their work as a whole.
Increases Employee Engagement
A 2020 Gallup poll indicated that only 36% of U.S. employees considered themselves actively engaged in their work, and close to 14% reported being actively disengaged.
Members of your team probably have no problem following rules. But what you want is a truly engaged team, one that takes full ownership of their work. Safety initiatives can be integral to work practices to help workers focus on what’s necessary. When safety is second nature, employees know there’s no need to panic in an emergency. There’s no confusing rush for instructions. Instead, people will know what to do, who to call, and where to look to get what they need.
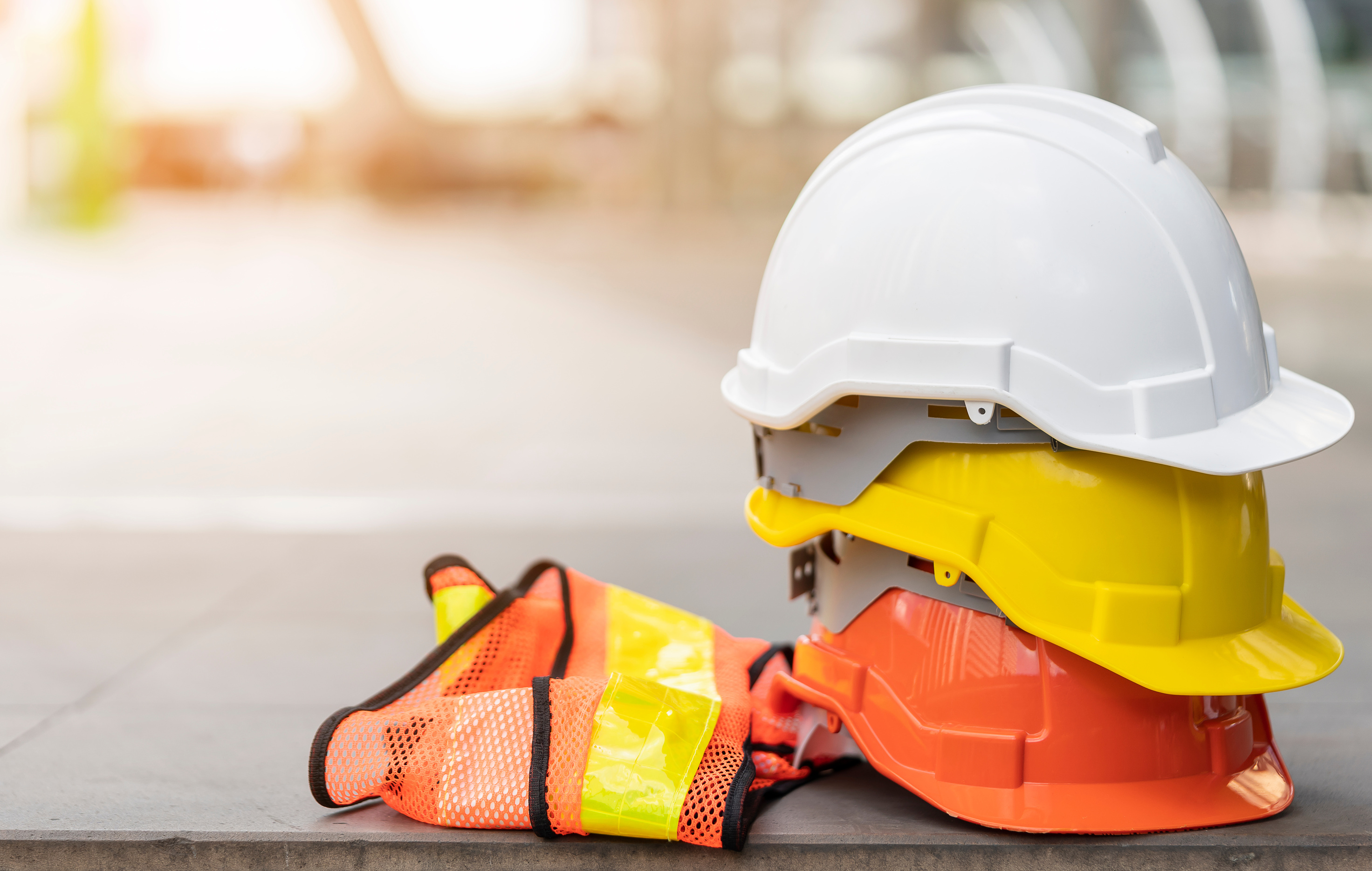
How to Create a Culture of Safety
The National Academies of Sciences, Engineering, and Medicine (NASEM) conducted a study on the cultures of the offshore oil and gas industry. And in 2016, NASEM published a report with recommendations for improving the safety culture across the industry. One of the recommendations was to share information, experiences, research, tools, and other resources related to safety to improve overall safety in the industry.
Make Your Values Clear
When defining what matters to a team or an organization, establish the importance of safety as a fundamental principle. Let team members understand that safety is paramount to the organization’s overall success. Just as essential, in fact, to reducing downtime and improving key performance indicators (KPIs), like Mean Time Between Failure and Overall Equipment Effectiveness. In other words, hitting KPIs is only as good as keeping workers safe as they do their work. In the same way that team members understand the importance of a robust preventive maintenance plan, they should understand why it’s necessary to keep the workplace safe for everyone.
Model Good Behavior
It all starts with leadership. Management can dole out SOPs that people have no choice but to follow. If you’re looking for a dedicated workforce, create a management system that teaches how to teach. The best way to get buy-in from everyone on the team is to see safety principles followed from the top down.
“Getting a certification indicates to potential employers that you’re accountable and that you can maintain high standards in maintenance work.”
Career Builder
Support Employee Learning and Accountability
Create concrete safety goals for employees to aim for. One way to do this is by outlining safety metrics and KPIs that teams should try to reach. Also, create checklists for them to follow and have access to at all times.
Also, consider encouraging employees to seek additional training and certifications. OSHA, for example, offers safety certification. While the program and the OSHA card granted at completion is still voluntary in much of the country, employers should consider the training for their workers.
Every worker has a right to a workplace that is safe and healthy. They should be fully aware of all job hazards and what they can do to protect themselves from them.
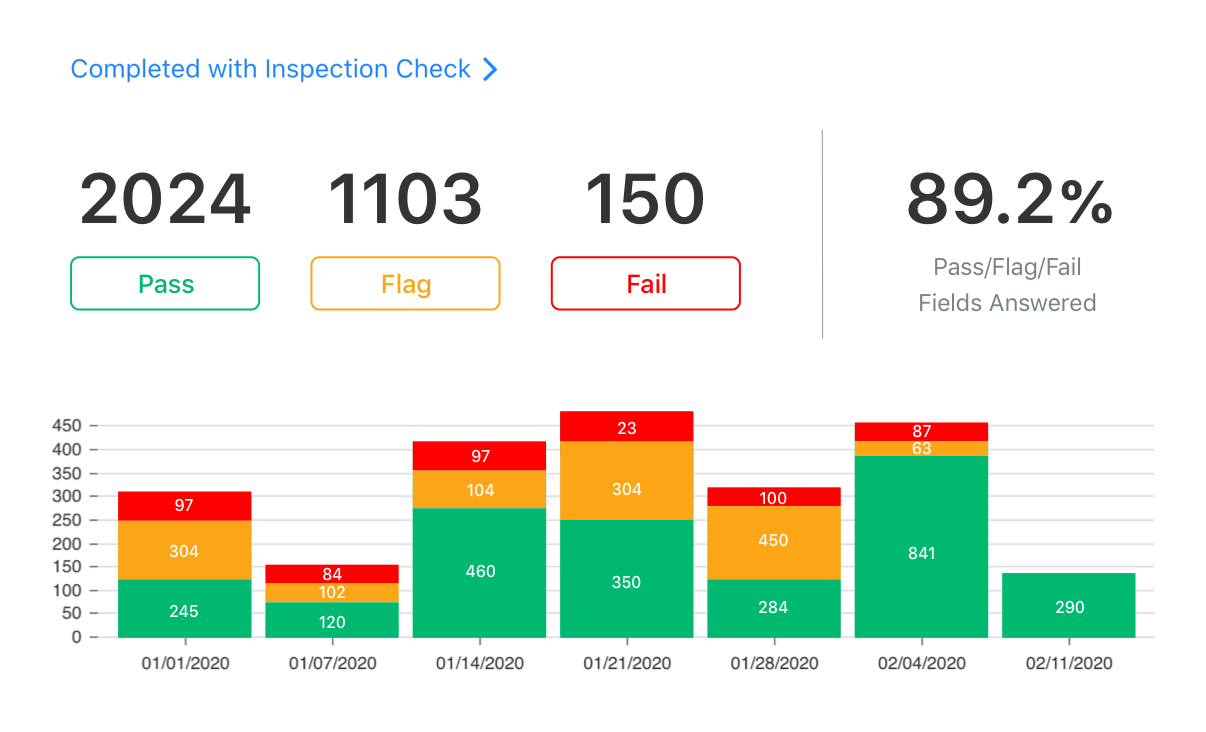
Track Performance
Measure safety performance so that employees know how they’re doing. For example, you could conduct regular safety performance audits to get a handle on what employees and teams are doing right and what they may need to improve.
Using a CMMS to Create a Culture of Safety
We recommend using a CMMS ( Computerized Maintenance Management System) to create safe and effective maintenance conditions. Sure, replacing pen and paper is no small feat, but you can use technology to facilitate standardized and safe operating procedures with your team.
Use MaintainX to help you:
- Communicate and reiterate company values, approved processes, and teamwork.
- Connect your workers. A CMMS like MaintainX with instant messaging capability allows workers to easily seek clarification whenever issues arise, point out safety hazards, highlight safety concerns, and report incidents and near-misses. In addition, employees can also access remote safety meetings and training sessions.
- Access crucial information: In addition to easy incident reporting, MaintainX stores data in real time. You’ll be able to give your team instant on-the-go access to your SOPs, inventory, and global safety procedures.
- Track safety milestones with inspection KPIs at your fingertips.
FAQs
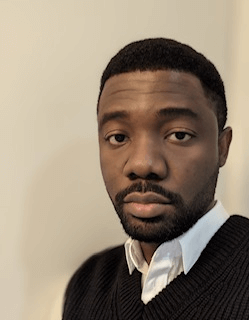
Lekan Olanrewaju is a content writer with years of experience in media and content creation. He has held positions at various media organizations, working with and leading teams at print magazines, digital publications, and television productions.