PREVENTIVE MAINTENANCE
Minimize downtime with preventive maintenance
Plan and schedule recurring maintenance tasks to resolve issues before they result in downtime.
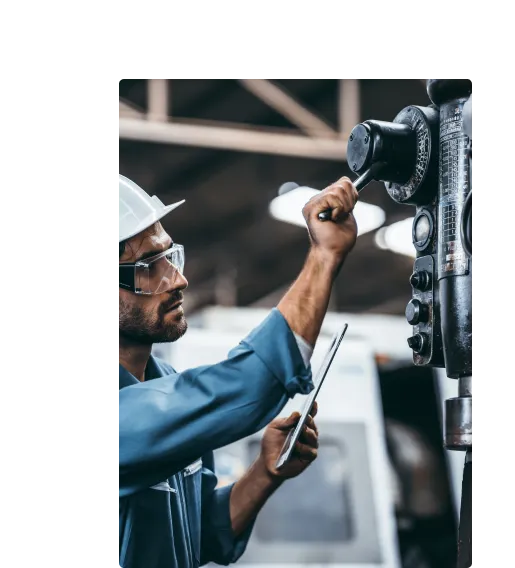
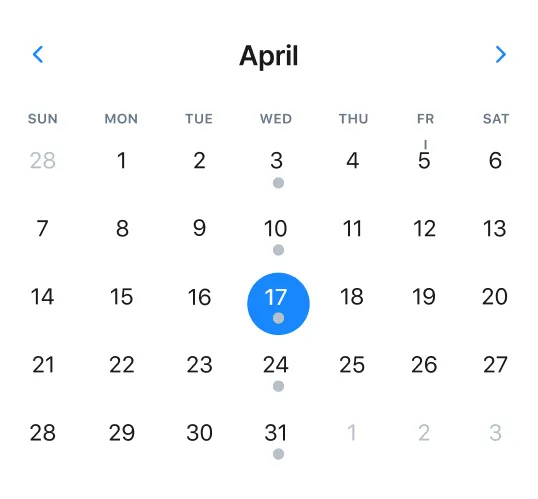
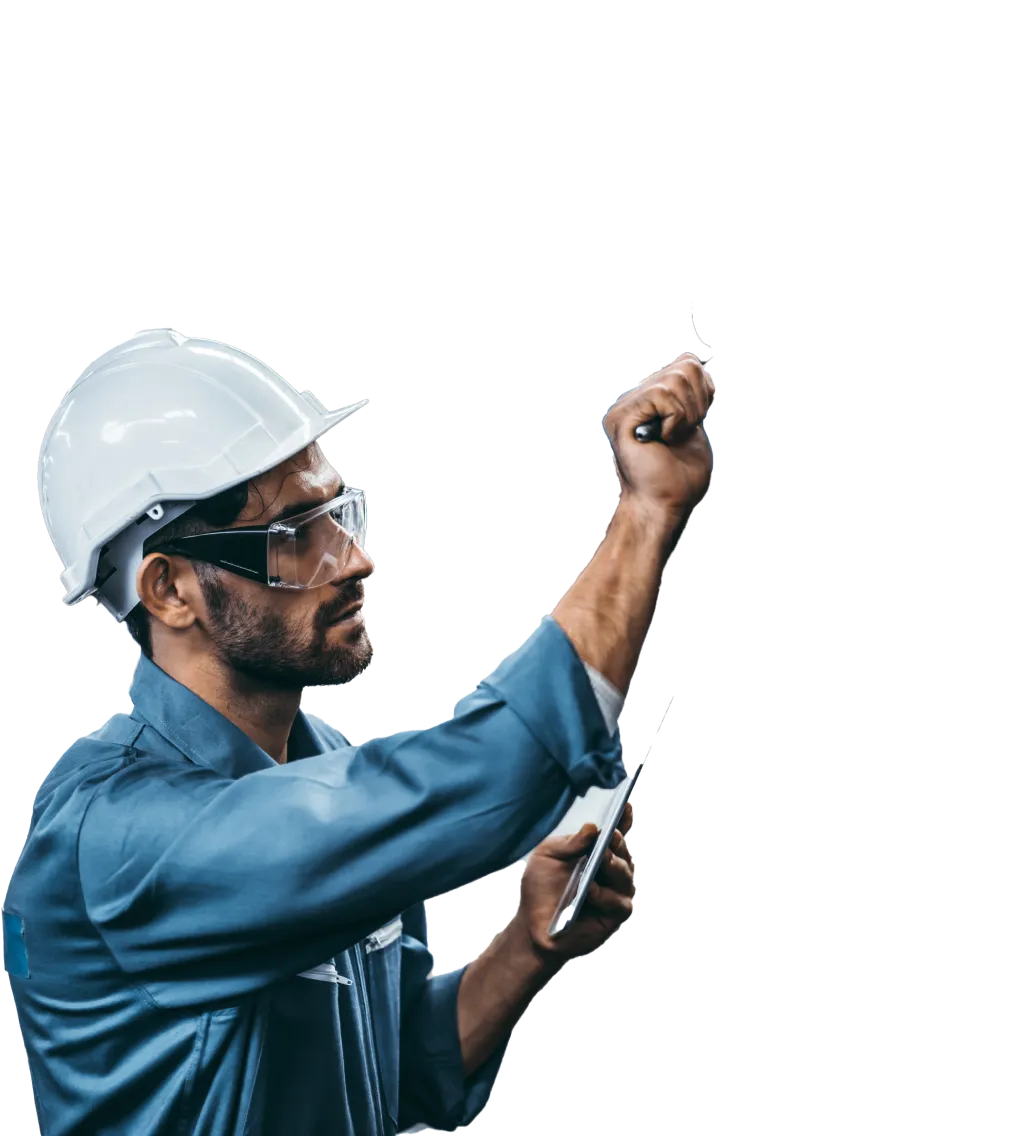
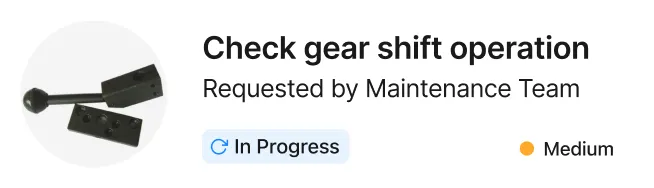
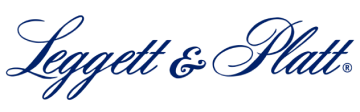
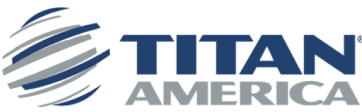
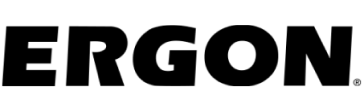

Our clients using MaintainX report
Prevent downtime before it halts production
Streamline preventive maintenance to reduce asset downtime and increase production capacity. Schedule inspections on your calendar and trigger condition-based maintenance to keep your equipment online.
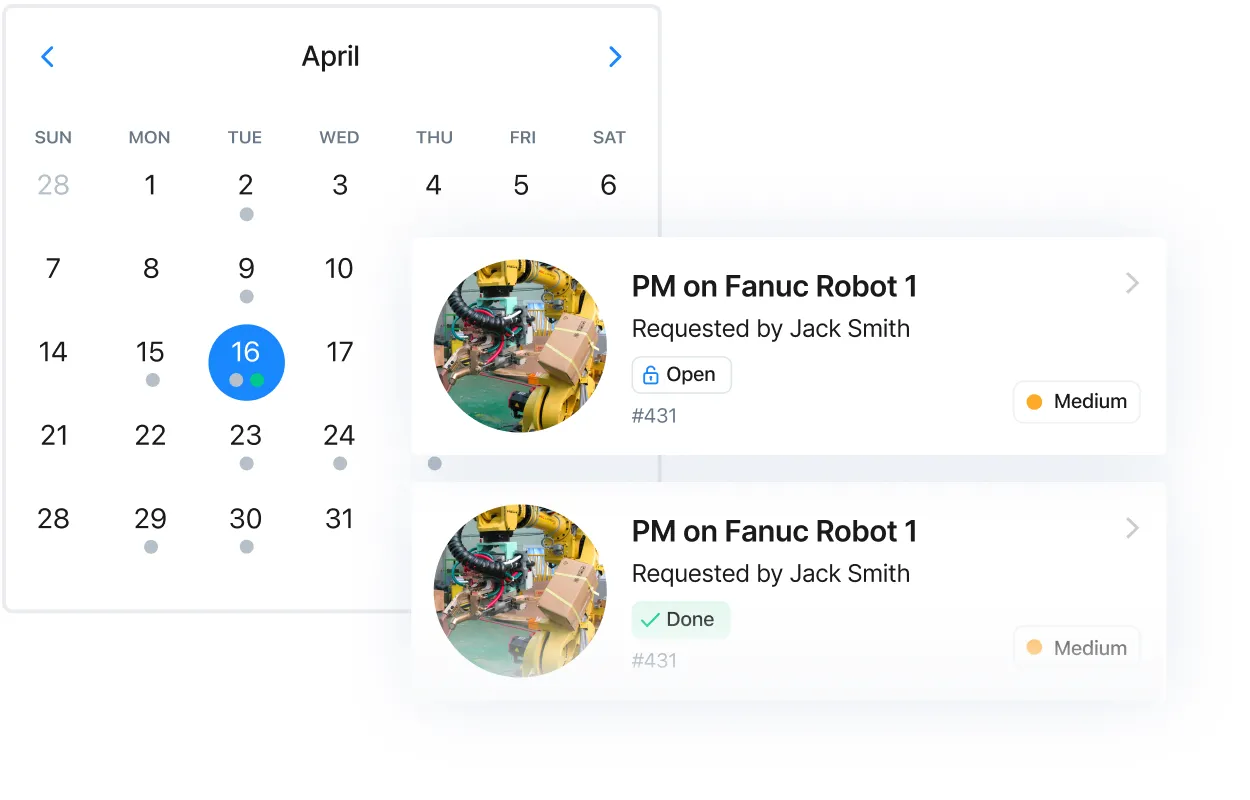
Respond quickly to failed inspections
Track all your preventive maintenance in one place, and quickly see what passes and what fails. Automate corrective actions for repairs, refurbishment, and regulatory compliance as issues come up.
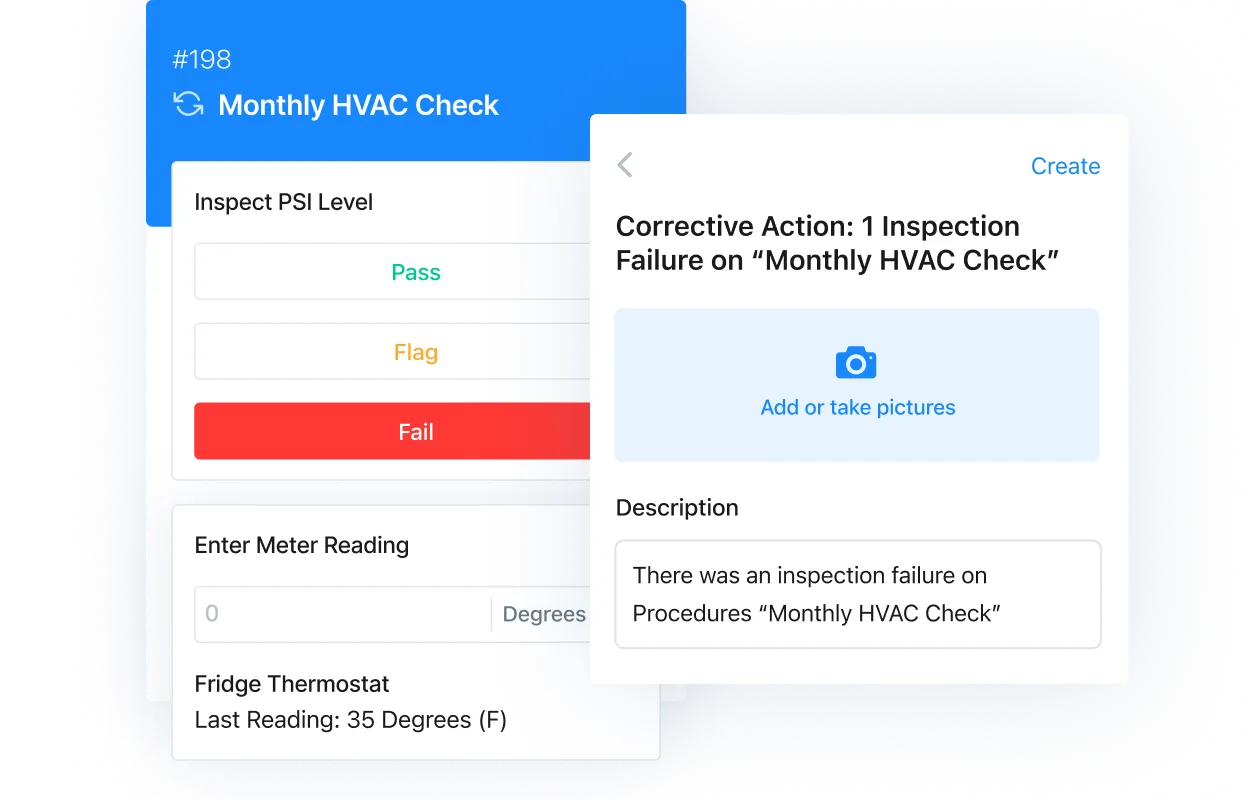
Schedule maintenance based on meter readings
Trigger PM tasks based on meter readings, so that you can inspect or service equipment after time used, mileage, temperature, pressure, and more.
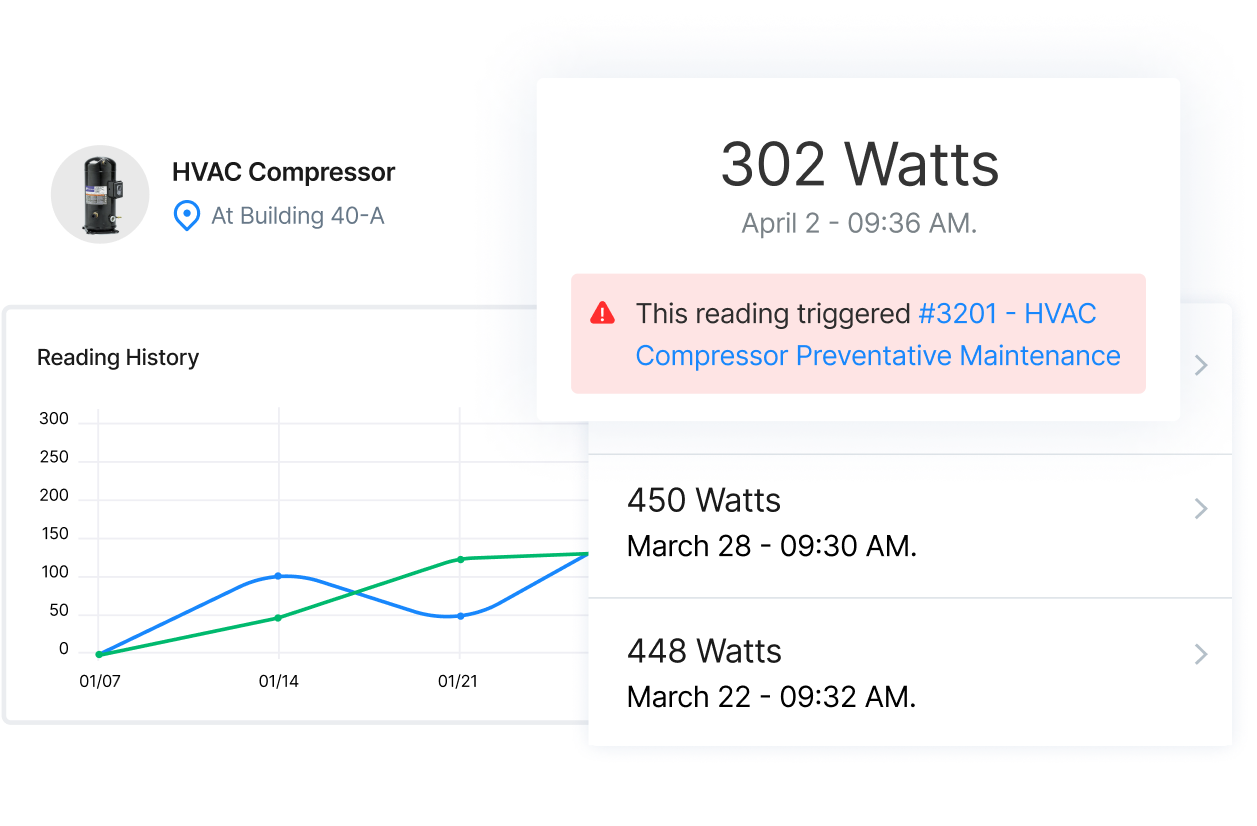
Measure and improve your PM program
Robust reporting allows you to measure the performance of all your preventive maintenance tasks. Get insights on key KPIs like PM compliance and MTBF so you can reduce downtime, optimize staffing, and ensure high priority work gets done.
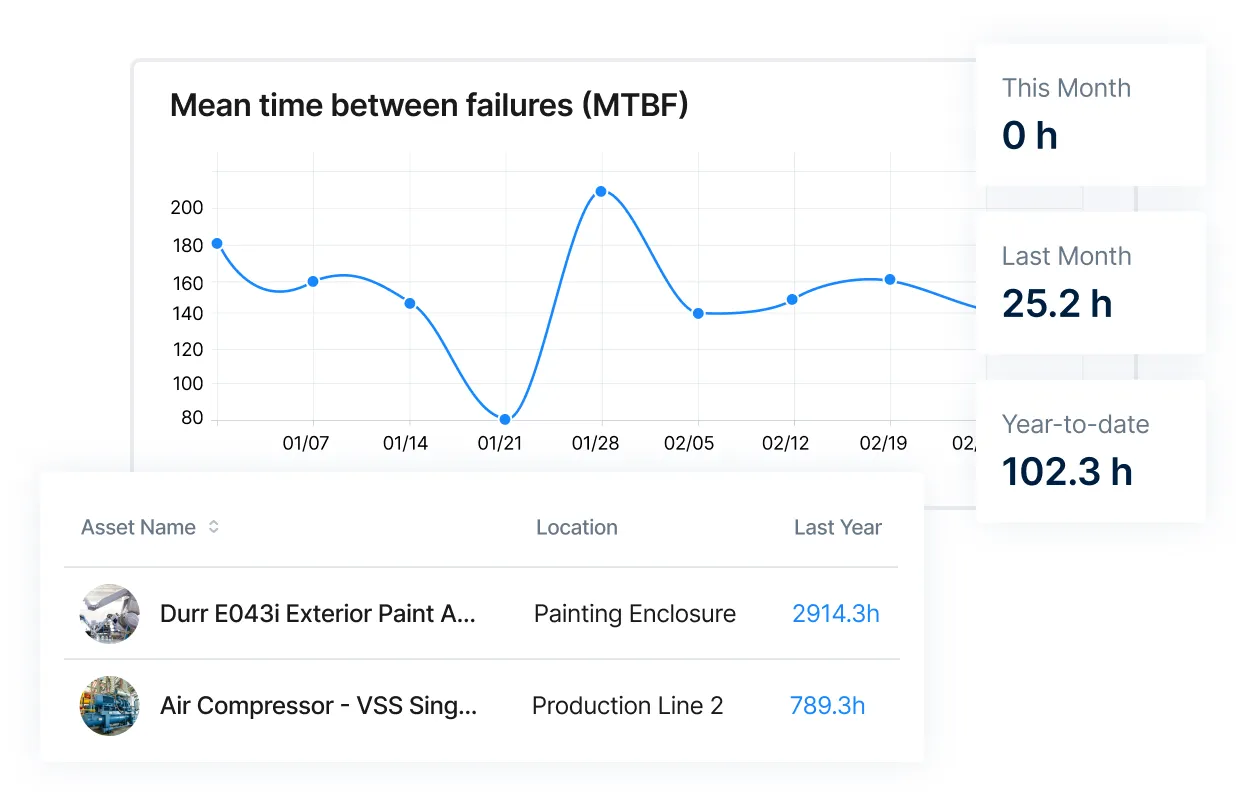
Capture inspection data more easily
Make it ridiculously easy for technicians to log work on their mobile devices. Capture the right data every time using pre-filled templates, time tracking, signatures, and required fields.
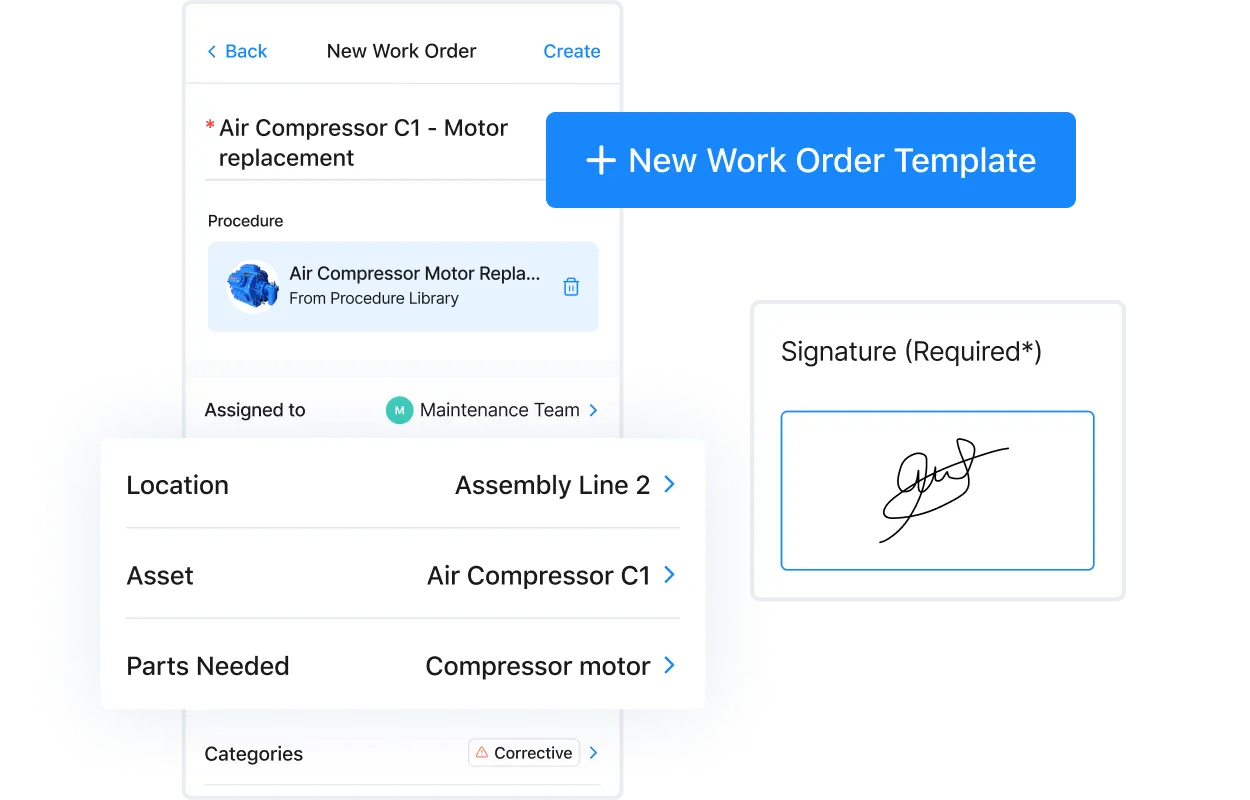
Streamline audit management with digital work history
Comply with OSHA, EPA, FDA and more regulations by mandating certain instructions and gathering a comprehensive digital audit trail automatically.
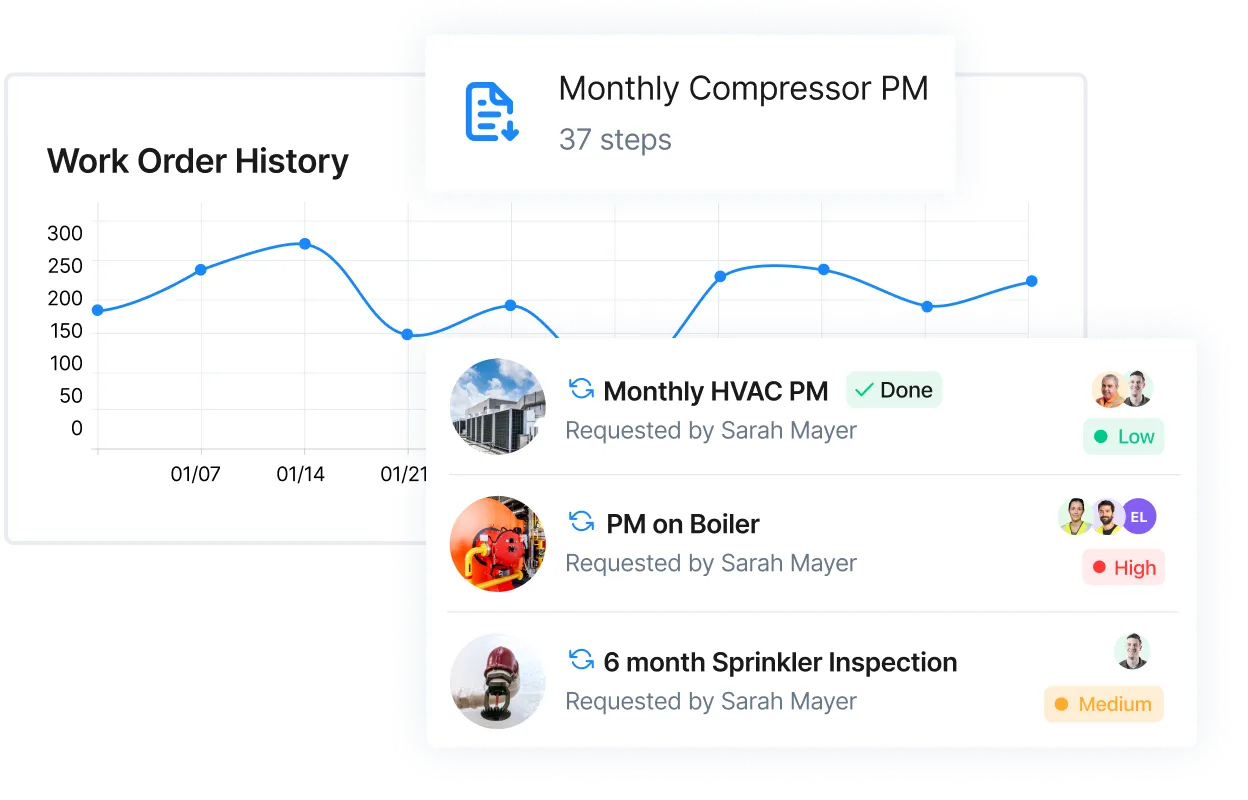
See asset and work history instantly
Access a full maintenance log for each asset, including what work was performed, who did the work, and which parts were used. Run reports on asset availability, costs, and failure causes to get data-driven insights.
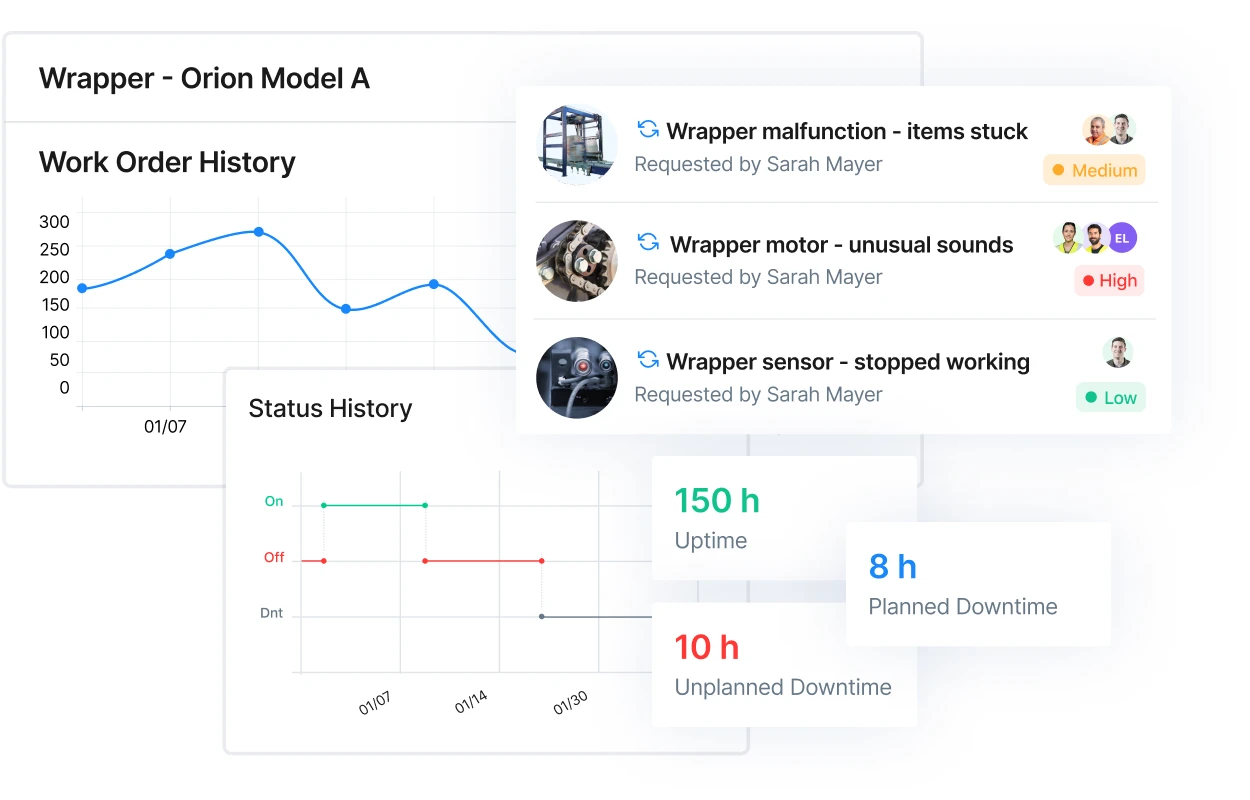
MaintainX is the best software for maintenance and operations across third-party review sites
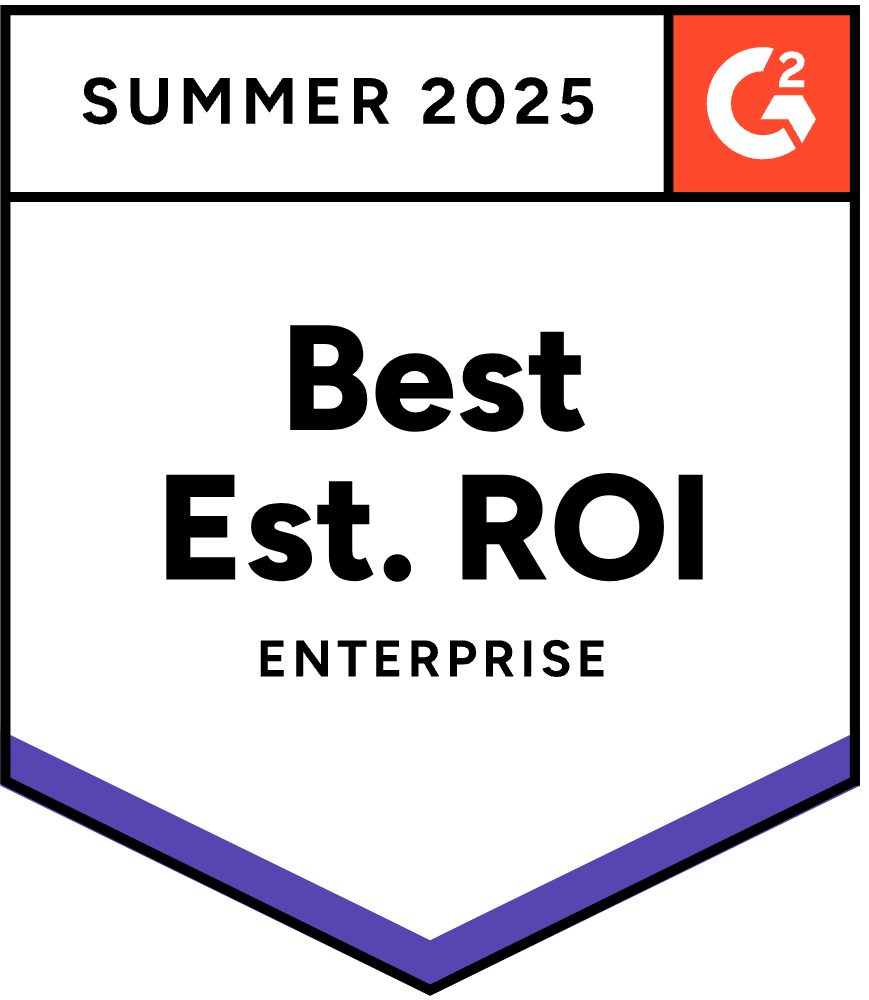
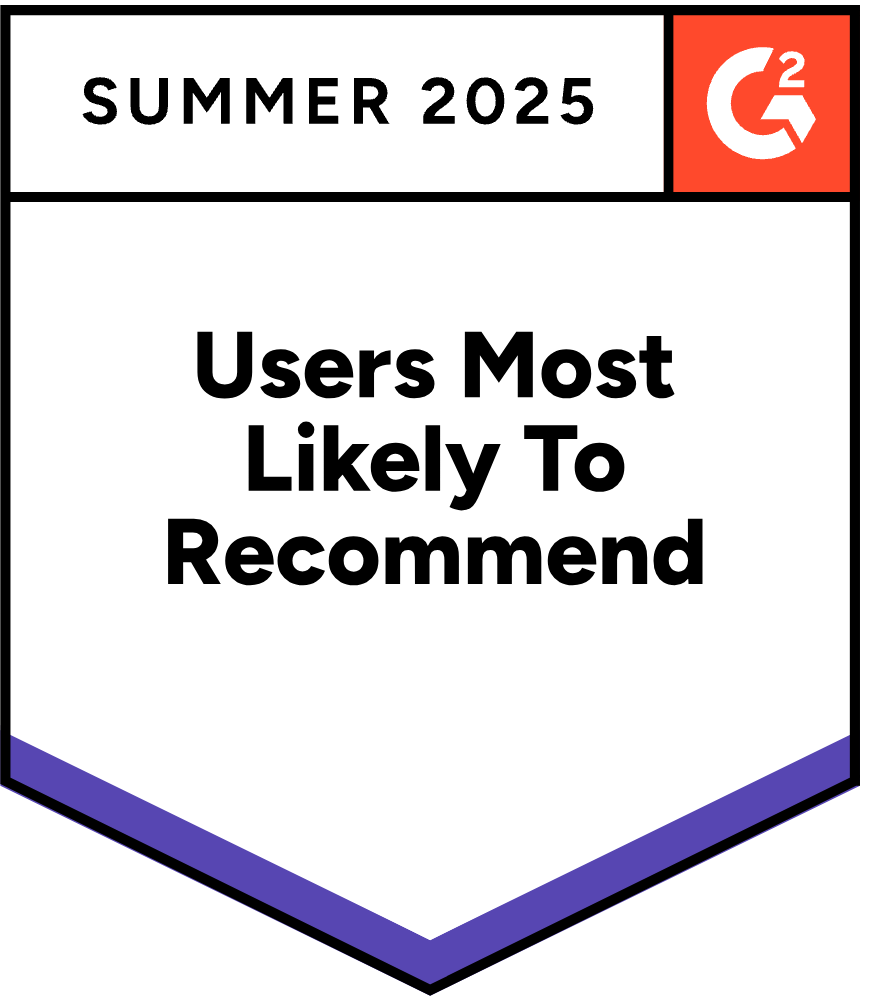
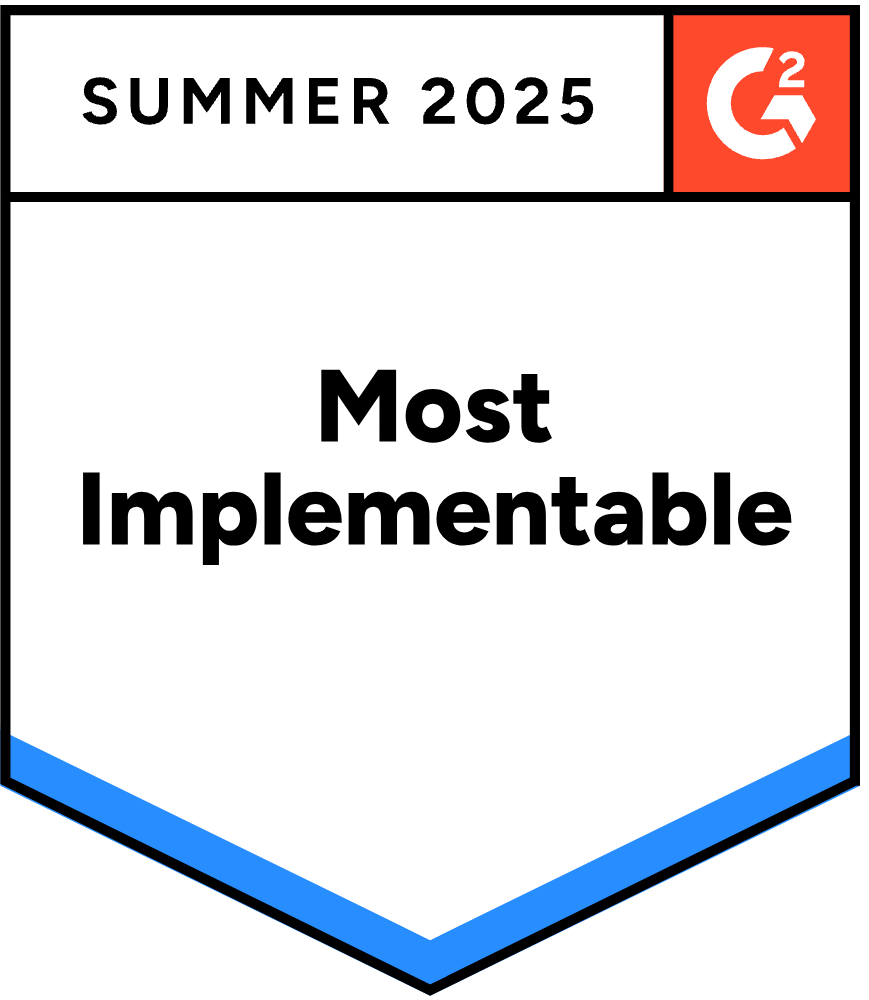
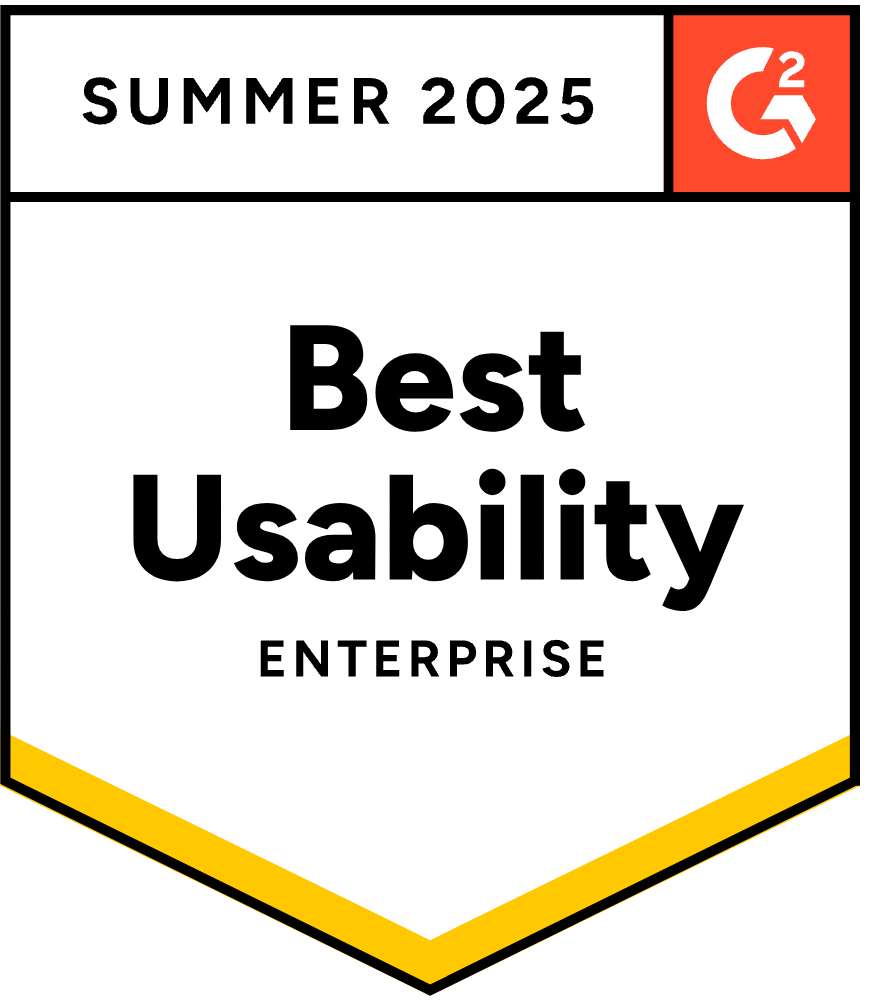
See what customers have to say
Get more done with MaintainX
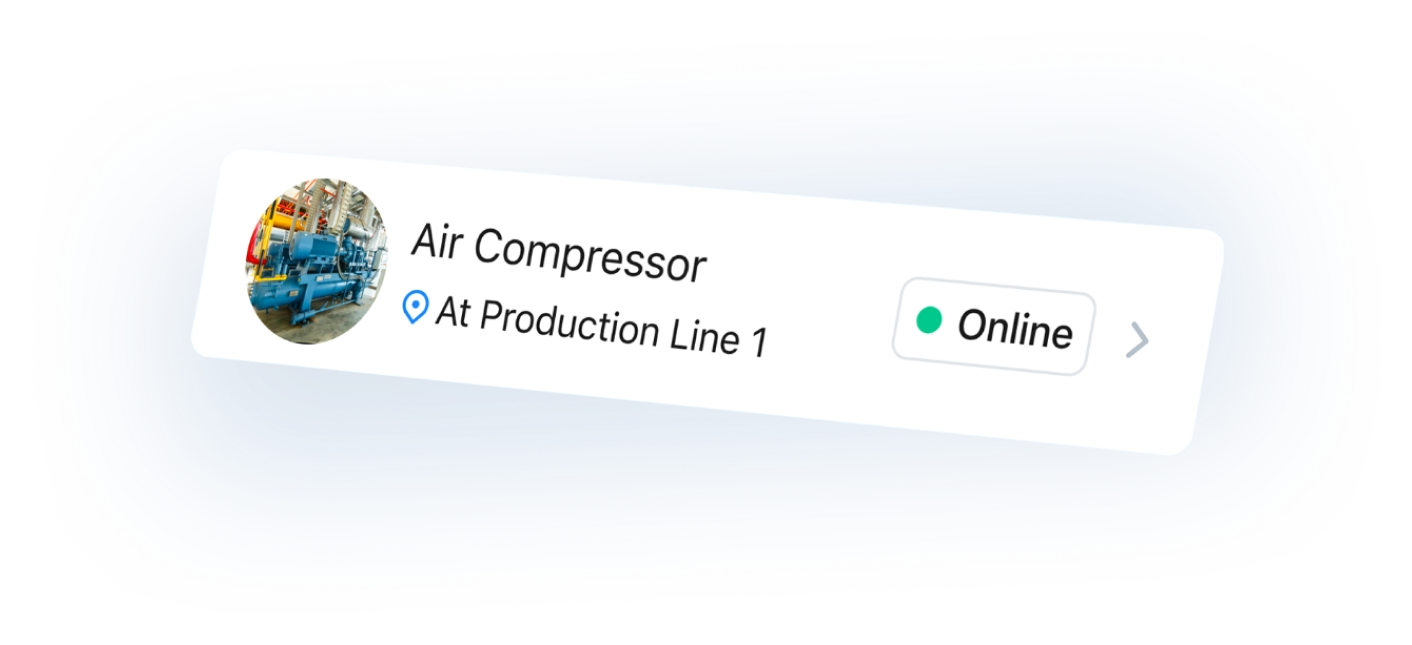
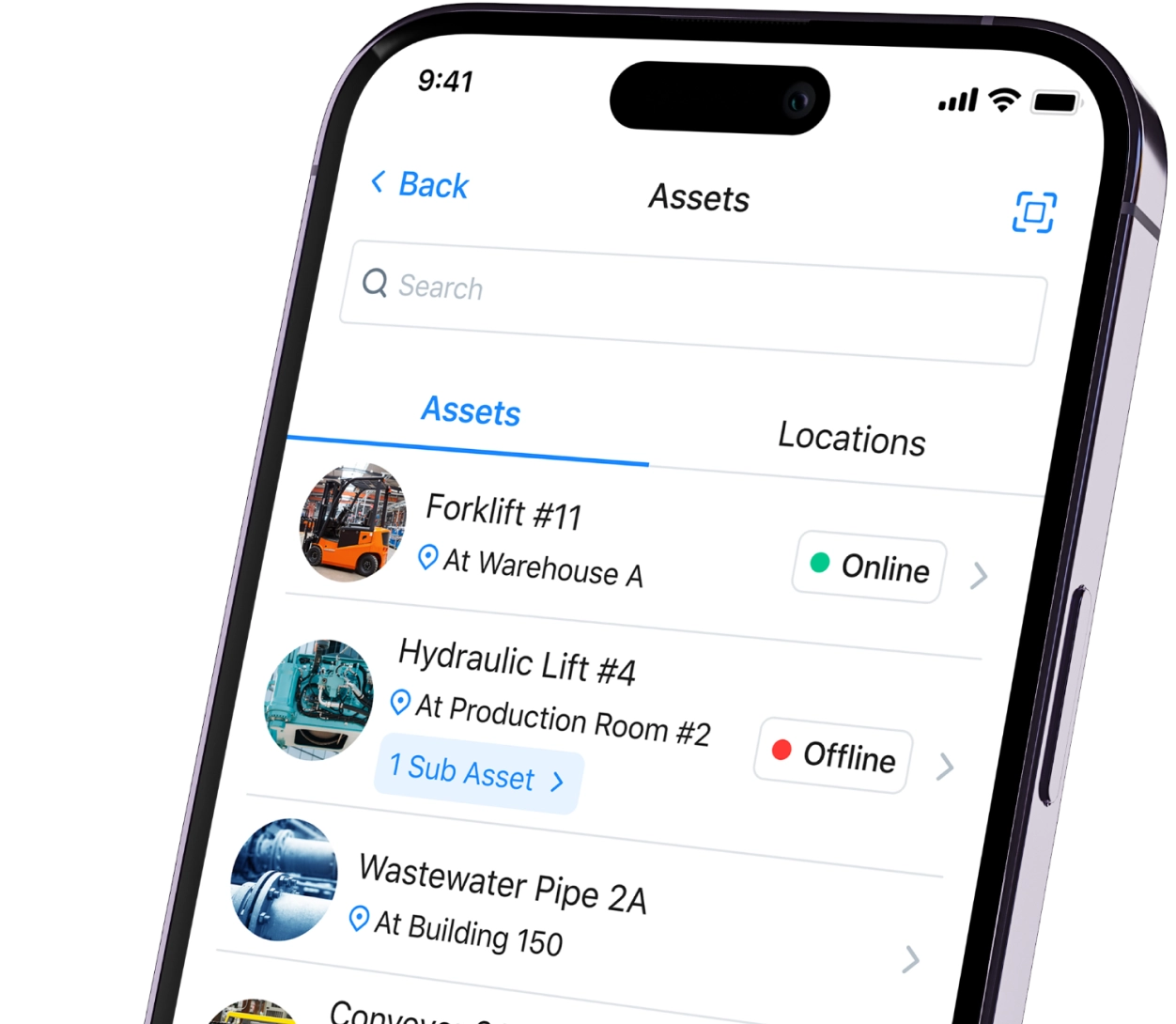