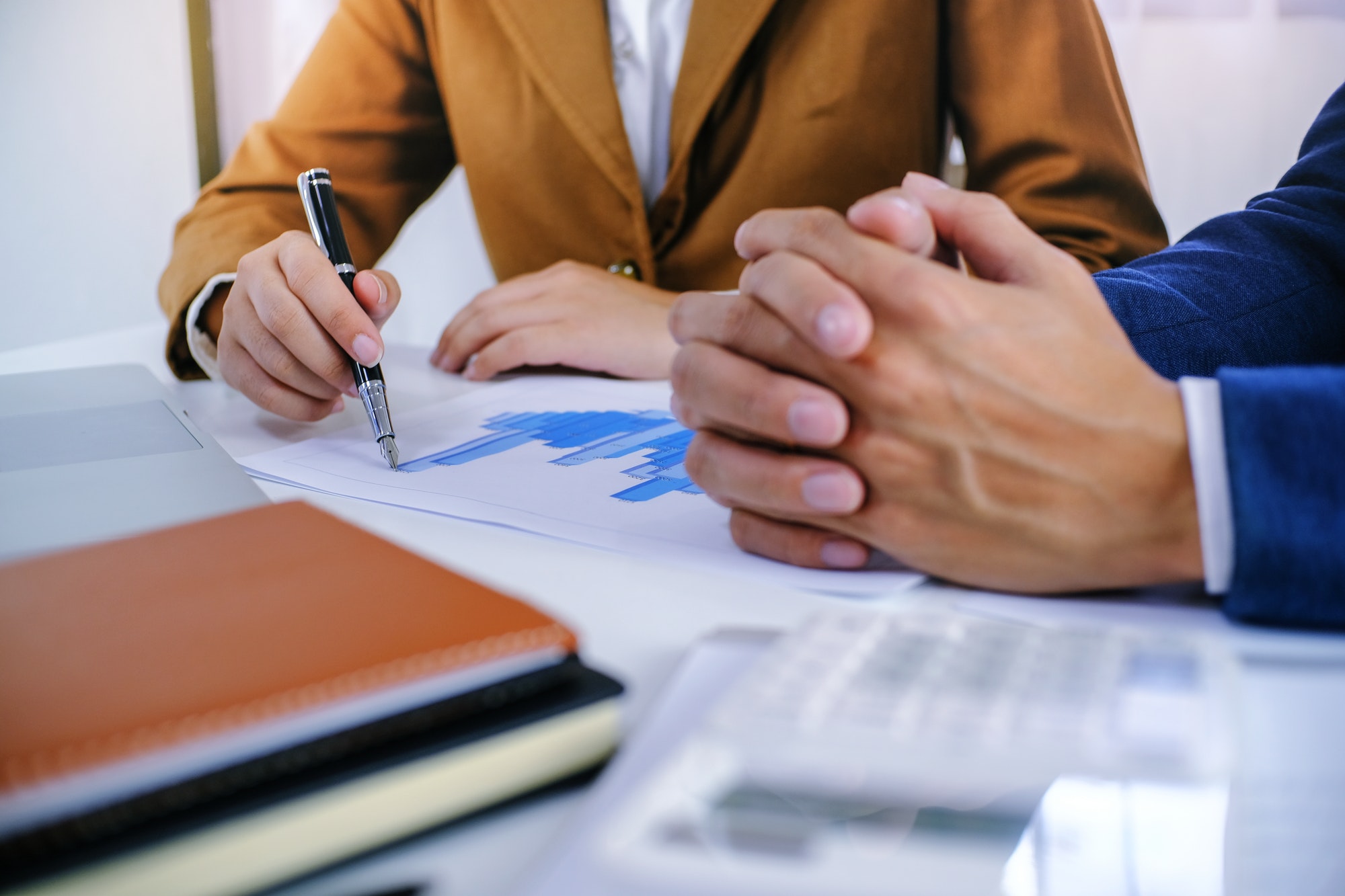
Ensuring regulatory compliance has never been more crucial.
Business organizations of every type must comply with federal, state, and local legislation mandated to keep stakeholders safe.
According to a study by Ponemon Institute, businesses worldwide lose an average of $14.8 million annually due to compliance failures.
Want to know a secret? The bulk of costs aren’t because of fines—they are a byproduct of business disruptions. Facilities found in violation of compliance regulations are often forced to shut down while making required regulatory changes.
Common causes of non-compliance include lack of leadership, operational systems, and accountability. The key to fulfilling ever-evolving regulatory requirements is developing and implementing effective standard operating procedures (SOPs).
This article will highlight the most common types of regulatory compliance, how to simplify compliance efforts with SOPs, and the advantages of process digitization. Let’s dive in.
How to Improve Regulatory Compliance with SOP Programs

Standard operating procedures (SOPs) help establish proper business processes, improve accountability, and strengthen corporate compliance programs.
Generally speaking, compliance means conforming to a specific rule, law, standard, or policy. Regulatory compliance refers to organizations taking steps to abide by given policies, regulations, and ordinances. The practice is also known as business compliance.
Accessible SOPs leave no room for wondering what should be done or how to do it. Documenting SOPs is especially crucial because, depending on the industry, an organization may be required to follow dozens—if not hundreds—of specific regulations.
1. Understand the Types of Regulations
Government institutions, both at the federal and state level, are the most recognized regulators of compliance. Municipalities mandate how organizations should conduct business, interact with customers, and treat employees, among other operational details.
In addition, some companies must adhere to industry-specific guidelines regarding licensing, permits, accreditation, certificates, client contracts, and industry standards and codes. The sheer volume of regulations is enough to make even the most organized manager’s head spin!
For this reason, it’s essential to periodically review the different types of regulatory compliance within your sector. Proactive compliance management will safeguard your team against surprise compliance issues, penalties, and inconveniences during audits.
Regulatory Compliance Laws by Industry
Examples of industry-specific regulations in the United States include:
Financial Industry
- The Dodd-Frank Act: Developed in 2010 after the 2008 financial crisis, the Dodd-Frank Act promotes transparency and accountability in the insurance and banking sector. It protects the economy and consumers from risky behavior by financial institutions.
- Payment Card Industry Data Security Standard (PCI DSS): The PCI DSS regulates how organizations handle, process, store, and transmit credit card information. The goal of the regulation is to increase the security of credit and debit card transactions.
- Sarbanes-Oxley Act (SOX): It protects investors from fraudulent financial reporting by corporations. The Act provides auditing and financial regulations for publicly traded companies. It’s also known as the Corporate Responsibility Act of 2002 or the SOX Act of 2002.
- Gramm–Leach–Bliley Act (GLBA): Also known as the Financial Services Modernization Act of 1999, the GLBA governs the consolidation of financial institutions, such as insurance firms, securities companies, investment banks, and commercial banks.
- Fair Credit Reporting Act of 1970: The Fair Credit Reporting Act (FCRA) regulates how credit reporting agencies access and collect personal credit reports and credit information.
- Sherman Act of 1890: This regulation aims to prevent the creation of monopolies by prohibiting anti-competitive agreements between companies. It is an antitrust law that prescribes the rule of free competition.
Other popular financial industry regulations include the Securities Exchange Act of 1934, which established the Securities and Exchange Commission (SEC); the Securities Act of 1933, which aimed to increase transparency in financial statements to minimize fraud; and the Bank Secrecy Act (BSA) that assists the government in detecting and preventing money laundering.
Technology and Data Security Industry
- Federal Information Security Modernization Act (FISMA): FISMA was signed into law in 2014 to prevent data breaches and other outside intrusions on federal information technology systems. It aims to ensure the confidentiality, integrity, and availability of system-related information.
- EU General Data Protection Regulation (GDPR) of 2016: It regulates how organizations process an individual’s data. Any company that markets its products to European citizens, regardless of its location, has to comply with the GDPR.
- California Senate Bill 1386: It requires companies operating in California to notify residents about data breaches if they are likely to expose personal information.
Healthcare
- Health Insurance Portability and Accountability Act (HIPAA): HIPAA regulates how organizations use and disclose individual’s health information. It also protects workers’ health insurance coverage.
- The Medicare Access & CHIP (Children’s Health Insurance Program) Reauthorization Act (MACRA) of 2015: This regulation addresses payment for doctors and Medicare Part B cost controls.
- The Health Information Technology for Economic and Clinical Health (HITECH) Act: The act promotes the adoption and meaningful use of health information technology.
Federal Laws
- Civil Rights Act of 1964: The act bans forms of discrimination, such as racial, gender, sexual orientation, and religious intolerance.
- Americans with Disabilities Act: It outlaws discrimination based on an individual’s disability.
Employment/Workplace
- Fair Labor Standards Act (FLSA): The act establishes the minimum wage, record keeping, overtime pay, and other standards for government and private-sector employees in the U.S.
- Family and Medical Leave Act (FMLA): It establishes the grounds for which employees are entitled to unpaid leave for medical and family reasons.
- Worker Adjustment and Retraining Notification (WARN) Act of 2003: The act requires employers to give employees advance notice in the case of plant closures and mass layoffs.
- Equal Pay Act of 1963: The act addresses gender-based wage discrimination.
- Federal Workers’ Compensation Act (FECA): This act establishes compensation for federal workers who get injured on the job.
- Uniformed Services Employment and Reemployment Rights Act (USERRA): It protects military officers’ civilian job rights while on military duty.
There are also other standard regulations, such as Hazard Analysis and Critical Control Points (HACCP), the Employee Retirement Income Security Act (ERISA), and the Social Security Act of 1935, that organizations should know. If you are in the restaurant and hotel sector, you can find notable regulations for the industry here.
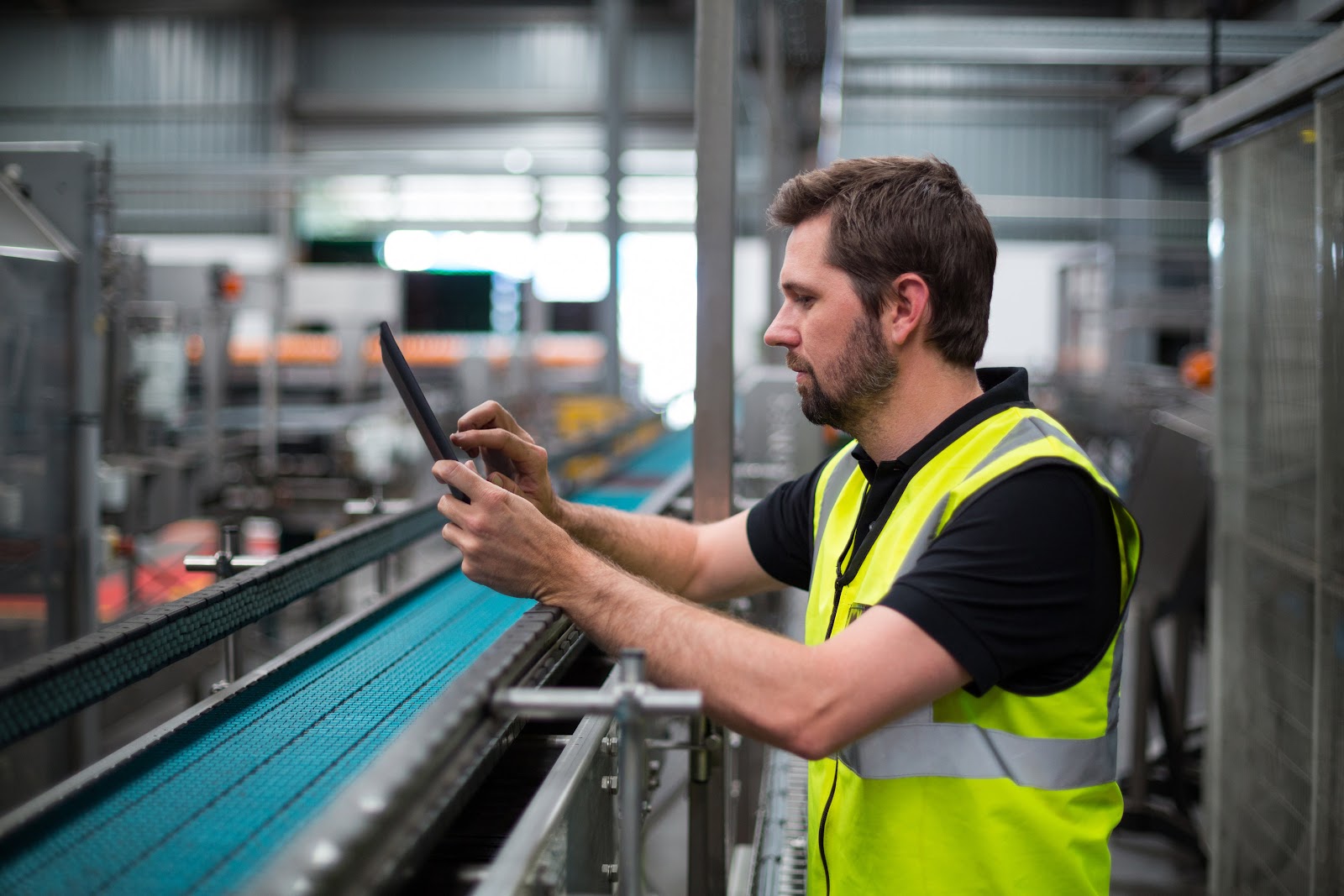
2. Adopt SOP Best Practices
Financial services, healthcare, cybersecurity, and manufacturing are among the most regulated industries within the United States. Depending on your industry, you may have several regulatory bodies to track. Your unique requirements will vary depending on business type, sector, location, and risk management factors. Regardless, follow these tips to strengthen regulatory compliance efforts:
- Assess Your Organization’s Exposure to Regulations: Determine if you’re in a highly regulated industry and note your mandatory requirements. An excellent place to start is the Occupational Safety and Health Administration (OSHA), Equal Employment Opportunity Commission (EEOC), and Environmental Protection Agency (EPA).
- Develop Standard Operating Procedures (SOPs): Document compliance processes to establish consistent follow-through. Employees should receive step-by-step work instructions that detail how to appropriately complete tasks. The easiest way to distribute SOPs is via compliance software like MaintainX.
- Adopt a “Single Source of Truth”: Centralized resources keep everyone on the same page, which is crucial for effective compliance solutions. Again, compliance software is the easiest way to streamline data collection, workflows, and policies. This minimizes the potential of errors instead of siloed teams that increase the risk of misinformation.
- Streamline Cross-Department Communication: Standardize communication across company lines with business messaging apps. Not only does encrypted instant messaging allow for quick troubleshooting between management and staff, but it also discourages information from getting into the wrong hands.
- Update Compliance Policies Regularly: As a company grows, expands, or merges, so will its compliance needs. As previously mentioned, regulators are introducing new regulations with increasing frequency. Schedule compliance management reviews to update policies in accordance with new mandates to prevent legal penalties.
- Hire Experienced Compliance Attorneys: Finally, enlist the support of an experienced legal advisor to ensure compliance with local and federal regulations. Always hire advisors who have experience dealing with rules specific to your industry.
Lastly, consider ditching the paper stacks, binders, and spreadsheets for digital compliance software solutions.
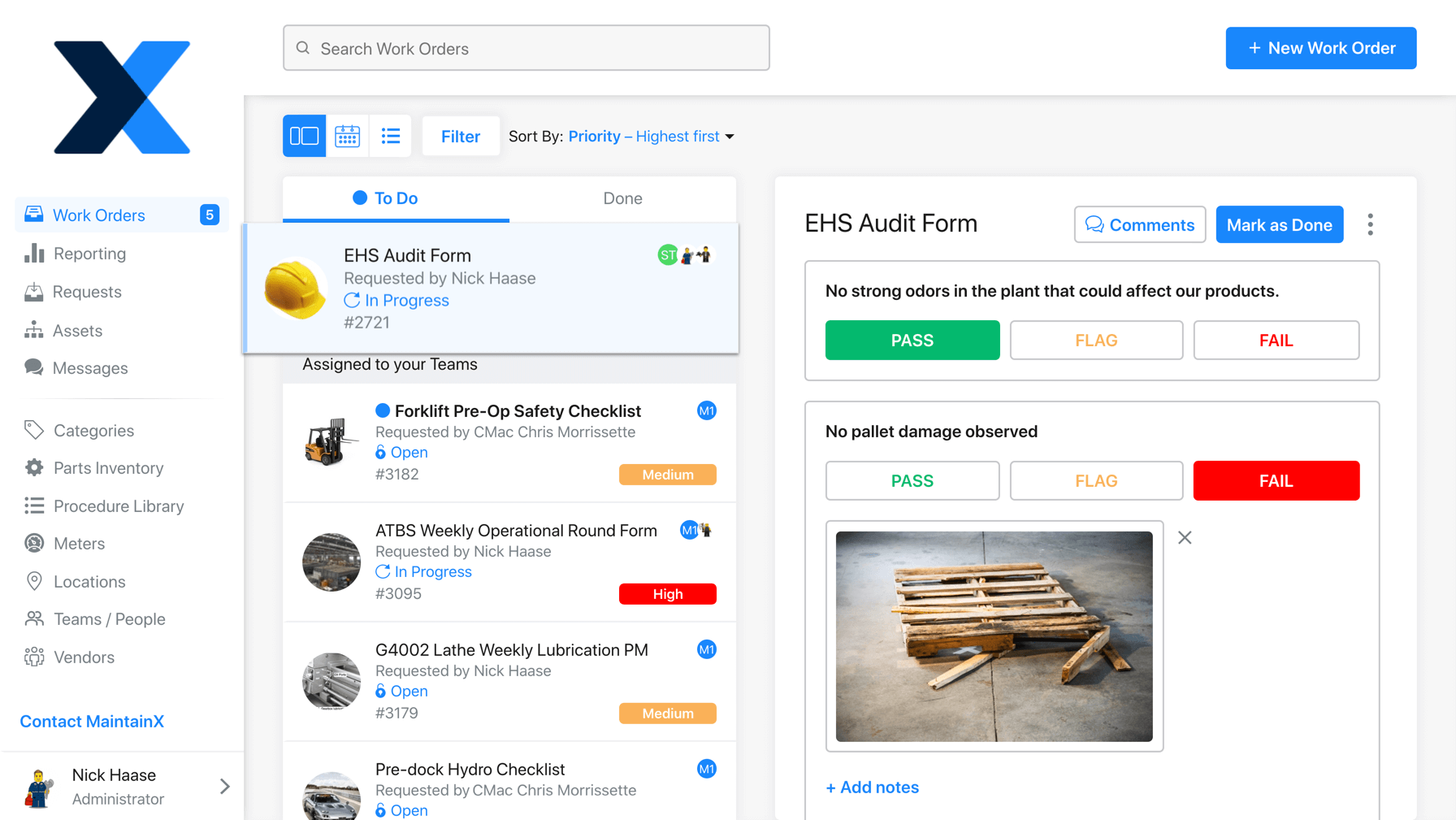
3. Digitize SOPs to Improve Regulatory Compliance
Document management is, potentially, the biggest hurdle to regulatory compliance. As regulations change, it becomes difficult to edit, print, and redistribute new compliance SOPs to employees. It’s also challenging to effectively keep track of paper checklists over the course of years!
Several software solutions exist for managing SOPs, such as compliance management software, enterprise asset management (EAM) software, and computerized maintenance management systems (CMMS).
These programs enable managers to track, monitor, and audit business operations. SOP fulfillment automation removes the stress of checking whether departments are following applicable laws, organizational policies, and consumer standards. If you are using a CMMS like MaintainX, simply enter the dates of compliance in question and generate a report from digital audit trails.
Benefits of Digitizing SOPs
- Streamlined employee shift changes (decreased downtime)
- Improved availability, accuracy, and accessibility of compliance data
- Increased bottom lines (with better organization)
- Decreased training time for new employees
- Reduced incidences of non-compliance
- Enhanced employee accountability
- Improved quality assurance
- Enhanced agility of SOP editing
It’s worth mentioning that OSHA now requires organizations to submit injury and illness records digitally. In addition, the Food and Drug Administration (FDA) promotes Good Manufacturing Practices (GMPs), which require companies to distribute new or revised SOPs to modernize food GMPs promptly. Digital SOP systems improve stakeholder compliance in all areas.
Improve Regulatory Compliance with MaintainX
Regulatory compliance requirements help protect businesses, customers, and environments. The highest cost of noncompliance is having your business shut down temporarily or permanently. Improve regulatory compliance by developing and distributing effective SOPs.
One of the best software solutions you can use to automate regulatory compliance is MaintainX. It allows managers to assign digital SOPs, streamline compliance training programs, access equipment historical records, and generate compliance reports within seconds.
Ready to improve regulatory compliance?
FAQs
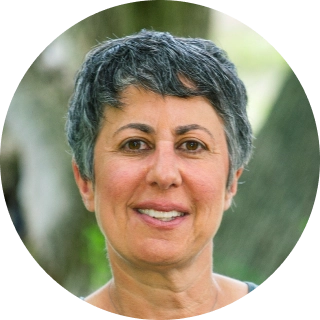
Caroline Eisner is a writer and editor with experience across the profit and nonprofit sectors, government, education, and financial organizations. She has held leadership positions in K16 institutions and has led large-scale digital projects, interactive websites, and a business writing consultancy.