High-level organizations often practice preventive maintenance (PM) within a reliability-centered maintenance (RCM) framework to increase equipment lifespans, enhance reliability, and optimize savings. Though both terms include scheduling work orders in advance—based on usage, time, or performance triggers—they are not the same. Preventive maintenance is a general type of proactive maintenance, while RCM is a maintenance strategy that combines various types of maintenance intending to optimize efficiency.
What Is Preventive Maintenance (PM)?
Preventive maintenance refers to scheduled maintenance activities completed to keep assets in optimal condition, prevent unplanned downtimes, and maintain safety. Common PM tasks include inspecting, cleaning, lubricating, adjusting, replacing, and repairing equipment parts. These tasks are always performed before asset failure may occur.
PM work orders are scheduled based on time, usage, or behavioral triggers. Operational managers schedule, assign, and track recurring tasks via Excel spreadsheets, whiteboards, paper clipboards, or Computerized Maintenance Management System (CMMS) software. According to the Plant Engineering Maintenance Survey, a whopping 80 percent of manufacturing plants prefer using preventive maintenance over other strategies. Why? Because PM enables organizations to save up to 18 percent in maintenance costs.
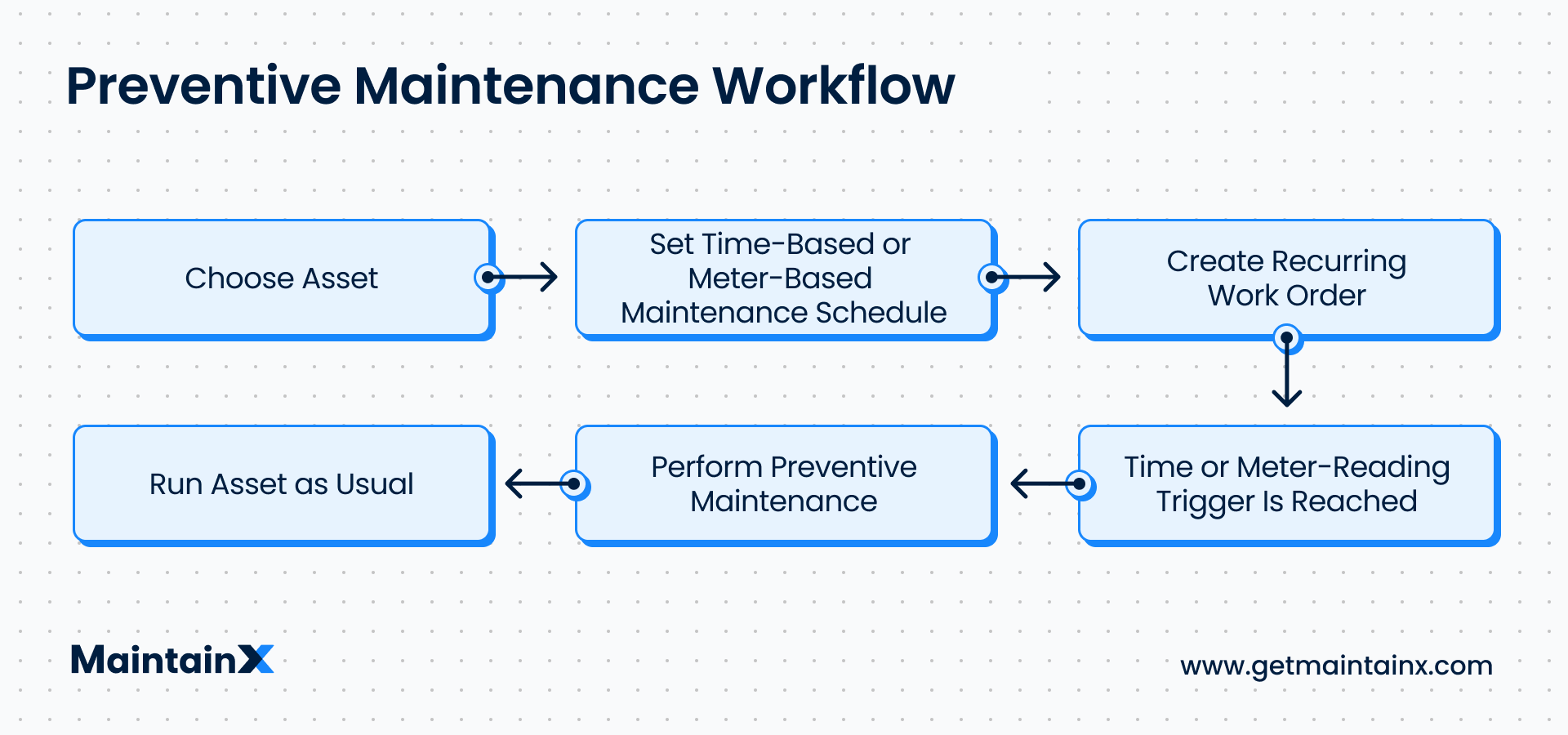
Examples of Preventive Maintenance
The easiest way to understand preventive maintenance is to consider the responsibilities of vehicle ownership. For example, you may choose to service your car every three months or every 3000 miles, according to manufacturer recommendations. Oil changes are a form of scheduled maintenance aimed at keeping your vehicle’s engine in reliable working condition. Furthermore, drive too long without changing your vehicle’s oil, and you may find yourself stalled out on the shoulder of a highway during rush hour.
Similarly, professional facilities are responsible for maintaining hundreds of assets for safety, financial, and productivity reasons. The effort involved in preventive maintenance varies according to industry. Take airlines, for example.
The D Check, often called the “heavy maintenance visit,” involves taking apart entire planes for parts inspection, repair, and replacement every 6 to 10 years. The standard operating procedure (SOP) generally takes 50,000 man-hours over 2 months. The complex process is just one of several PMs conducted on aircraft after a specified amount of time or usage to prevent accidents, breakdowns, and premature decline. It’s worth mentioning that preventive maintenance in the form of RCM was pioneered by the aviation industry, but is widely practiced by other industries today.
“Reliability-Centered Maintenance (RCM) is the process that is used to determine the most effective approach to maintenance. It involves identifying actions that, when taken, will reduce the probability of failure and which are the most cost effective.”
NASA
What Is Reliability-Centered Maintenance (RCM)?
Reliability-Centered Maintenance (RCM) is a structured maintenance strategy designed to increase productivity while optimizing maintenance costs. The goal of RCM is to identify the maintenance methods best suited to different pieces of equipment to optimize reliability, productivity, and costs.
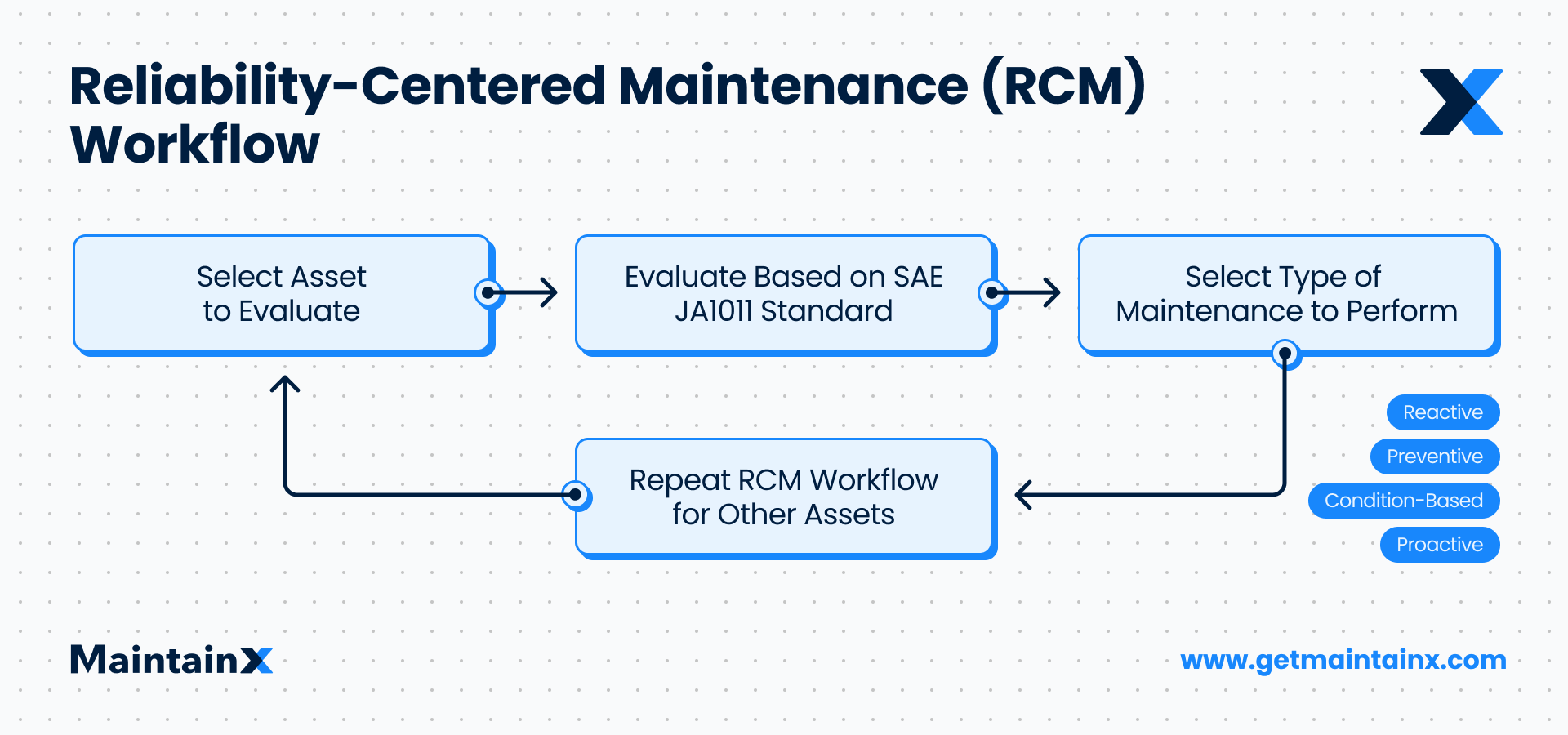
The core of the maintenance framework is RCM Analysis, which includes a step-by-step process to match individual assets with ideal maintenance strategies**.** Operational managers assess assets individually, evaluating their functional purposes, possible failure modes, and potential impact on production in the event of failure. The Society of Automotive Engineers (SAE) outlines seven questions in the SAE JA1011 standards that inform the criteria for RCM processes, regardless of industry:
- What is the equipment’s primary function and its performance standards?
- What are the possible ways in which it can fail to perform the main function?
- What are the causes of each failure?
- What happens when each failure occurs?
- What are the impacts of each failure on the system?
- How can you prevent or minimize the impact of each failure?
- What actions should you take if failure cannot be prevented?
As previously mentioned, RCM analysis reveals the most suitable maintenance approach—preventive maintenance, predictive maintenance, reactive maintenance—for each piece of equipment. In some instances, more than one approach is suitable and can be used on a particular asset.
“Reliability-Centered Maintenance (RCM) is a process to establish the safe minimum levels of maintenance while ensuring equipment continues to perform to its design function within the current operating context. It achieves this by providing a means for determining optimal maintenance and operational strategies based on the probability and consequence of the analyzed failure modes.”
General Electric
9 Principles of Reliability-Centered Maintenance
Nine principles of modern maintenance guide RCM:
- Failures should be accepted.
- Most failures are not a result of aging.
- Some failures have a bigger impact than others.
- Parts wear out while equipment breaks down.
- You have to identify hidden failures.
- Identical equipment may not require identical maintenance.
- Maintenance only preserves a piece of equipment’s inherent design reliability and performance.
- Effective maintenance programs shouldn’t waste resources.
- Good maintenance programs improve and become better over time.
Examples of Reliability-Centered Maintenance
Did you know that NASA has saved more than $300,000 in maintenance costs since it began practicing RCM at its Marshall Flight Center facilities? NASA’s RCM plan, mostly used for its pressurized systems, has enabled the institution to reduce energy consumption, improve workplace safety, minimize environmental impact, and extend the lifespan of aging pieces of equipment.
Additionally, The National Ignition Facility has saved $2 million in maintenance costs by using RCM. The RCM approach has enabled it to cut out routine maintenance tasks that were unproductive. Instead, it focused on identifying potential problems and how to effectively take care of them.
The Difference between Preventive and Reliability-Centered Maintenance
The main difference between preventive vs reliability-centered maintenance is the structure of each maintenance schedule. While PM tends to be generalized across several assets, RCM looks at each asset and matches it with a unique maintenance strategy. In terms of cost, preventive maintenance is expensive due to its extensive scheduling needs. RCM, on the other hand, only has high upfront costs that decrease as equipment-specific maintenance procedures reduce inefficiencies.
The table below provides a summary of the differences between the two approaches.
Get a CMMS for Your Preventive and Reliability-Centered Maintenance
People often confuse preventive maintenance with reliability-centered maintenance. Preventive maintenance isn’t as selective as RCM and, therefore, lacks the level of efficiency that RCM offers. RCM looks to assign unique maintenance activities to individual assets after carefully analyzing each asset’s failure mode and how best to take care of it.
With CMMS software like MaintainX, manufacturers can easily track and record all information related to the maintenance activities of their assets. This, in turn, helps identify situations that could lead to equipment failure or downtime. In addition, by using RCM as part of their overall maintenance strategy, manufacturers can ensure that all necessary preventive measures are taken to minimize the risk of mechanical breakdowns or downtime.
Overall, RCM, combined with the convenience of CMMS software, provides an effective preventative maintenance strategy for reducing unplanned downtime, improving reliability, and ensuring that all machinery runs at peak efficiency. With an effective preventative plan in place, manufacturers can achieve maximum production rates while keeping operational costs low. As a result, businesses can increase their competitive advantage by eliminating or minimizing mechanical failures. This reduces long-term repair costs associated with emergency maintenance activities.
See MaintainX in action